Figures & data
Table 1. Chemical composition (wt.%) of the base materials.
Figure 4. Pictures of furnace samples before carburizing by three different processes. (a) Process 1; (b) process 2 and (c) process 3.
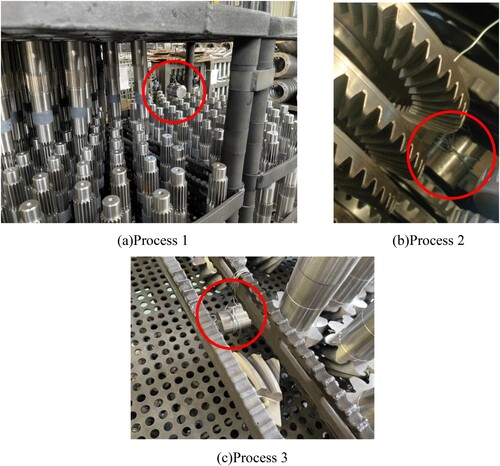
Table 2. Carburizing and quenching process.
Figure 5. Pictures of furnace samples after carburizing by three different processes. (a) Process 1; (b) process 2 and (c) process 3.
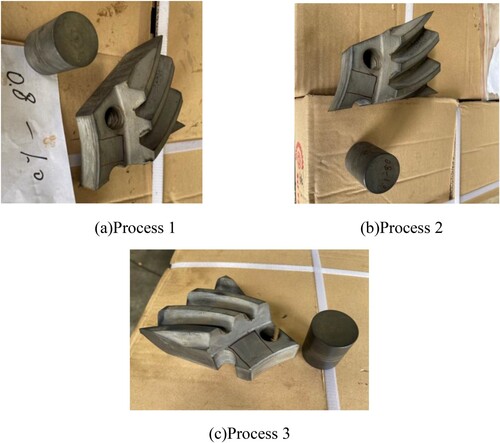
Figure 7. Three different process carbon concentration test positions. (a) Test positions and (b) the schematic diagram of the testing area.
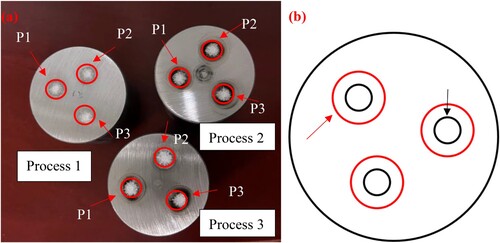
Figure 8. Comparison of experimental values and simulation values. (a) Simulation result point positions; (b) process 1; (c) process 2 and (d) process 3.
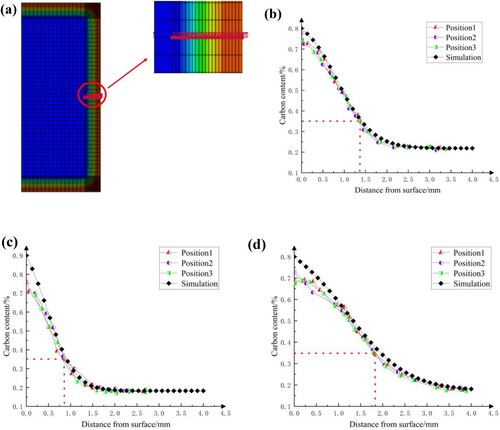
Figure 9. Microstructure after atmosphere carburizing. (a) Cylindrical sample; (b) sketch map; (c) surface; (d) sub-surface and (e) center.
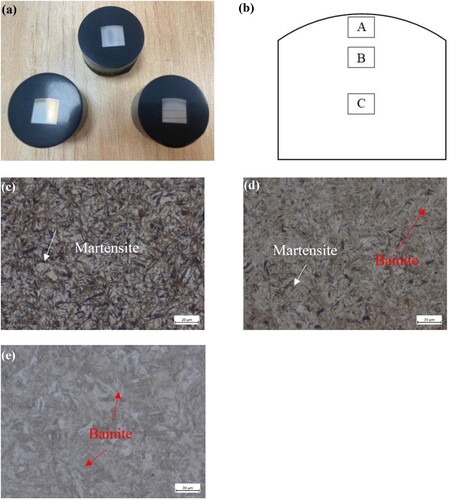
Figure 10. Microhardness profile of the carburized layer. (a) Indentation diagram and (b) three different process hardness gradients.
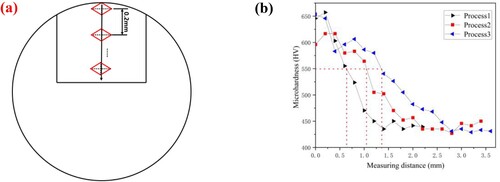
Table 3. Simulation generates a training set scheme list.
Table 4. Six sets of carburizing process parameters.
Table 5. Simulation generates a training set scheme list.
Table 6. Three sets of carburizing process parameters.
Table 7. Comparison of prediction time and simulation calculation time.