Figures & data
Table 1. Chemical composition of the masteralloy used (wt %).
Table 2. Composition of the mixtures used in study 1.
Table 3. Designation and composition of the mixtures used in study 2.
Figure 1. Final geometry (machined and polished) of the fatigue samples for Astaloy CrA + 0.6%C + 3%Ni sinter hardened at 1250 °C.
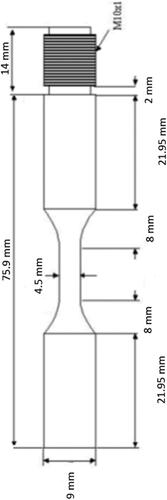
Figure 3. Hardness, impact energy and oxygen content of PM steels with 0.6% admixed carbon, compacted at 700 MPa, sintered 60 min at 1250 °C in N2-10% H2.
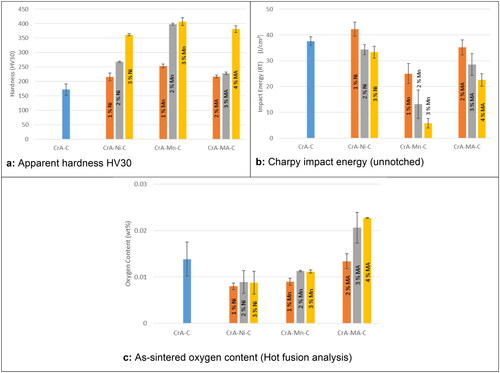
Table 4. As-sintered properties of PM steels AstaloyCrA-x-0.6%C (x = Ni, Mn, MA in varying contents). Compacted at 700 MPa, sintered 1 hr at 1250 °C in N2-10%H2.
Figure 5. Impact fracture surfaces of PM steels with 0.6% admixed carbon, compacted at 700 MPa, sintered 60 min at 1250 °C in N2-10% H2.
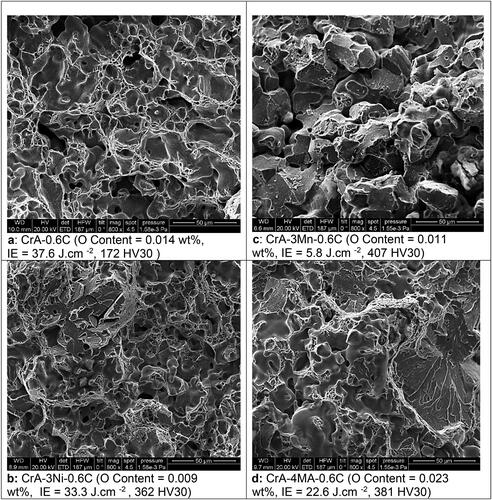
Figure 6. As-polished OM micrographs of hybrid alloyed steels; the larger pores in Mn steel compared to the two other grades are clearly visible.
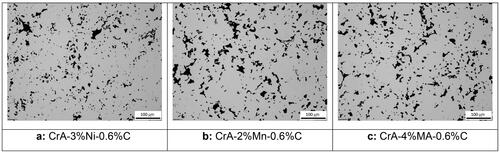
Table 5. Sintered properties of hybrid alloyed steels; compacted at 700 MPa, sintered 60 min at 1250 °C in N2-10%H2, heat treated by gas quenching and tempering
Figure 7. Nital etched OM micrographs of different steels show martensitic matrix after sinter hardening.
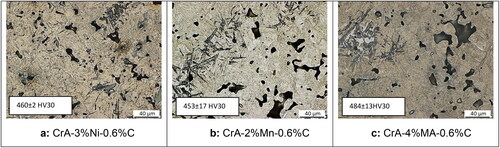