Figures & data
Table 1. Chemical composition in mass% of modified C55 (EN ISO 683-1, Citation2018) and 3Dprint AM 80 HD (Voestalpine Böhler Welding Austria GmbH, Citation2023) nominal according to datasheet.
Figure 2. Double elliptical Goldak heat source model (Rubio-Ramirez, Giarollo, Mazzaferro, & Mazzaferro, Citation2021).
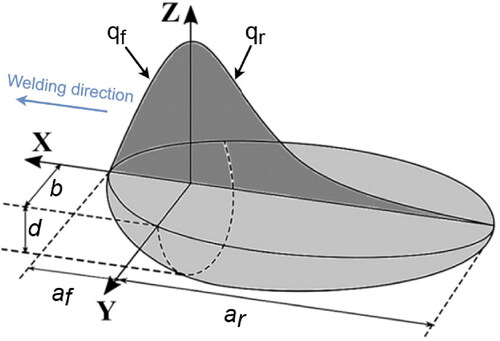
Table 2. Welding parameters for experiment.
Figure 5. Deviation of the simulation from the experimentally determined melt pool geometry (double elliptical heat source).
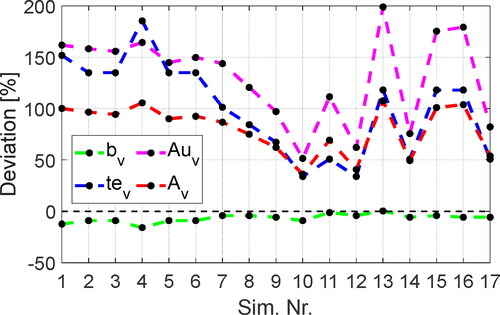
Figure 6. Deviation of the simulation from the experimentally determined melt pool geometry (Gaussian heat source).
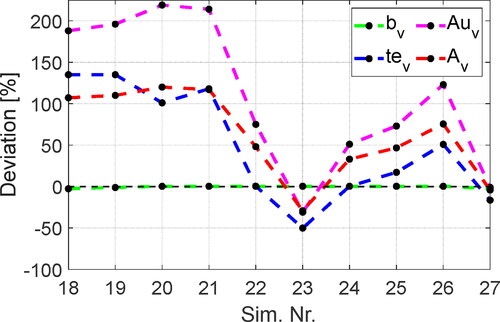
Table 3. Heat source parameters.