Figures & data
Mean ± 1 standard deviation; n = 4 for 6.35-mm and 2-mm formats; n = 3 for pellet meal due to a problem with high-performance liquid chromatography injection volume in one replicate.
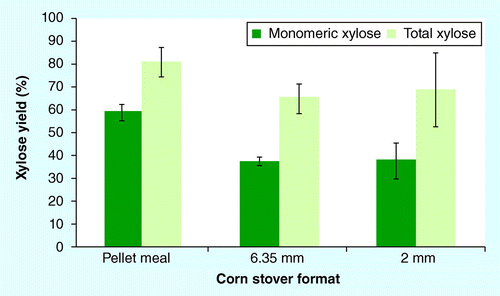
Mean ± 1 standard deviation; n = 4 for 6.35-mm and 2-mm formats; n = 3 for pellet meal due to problem with high-performance liquid chromatography injection volume in one replicate.
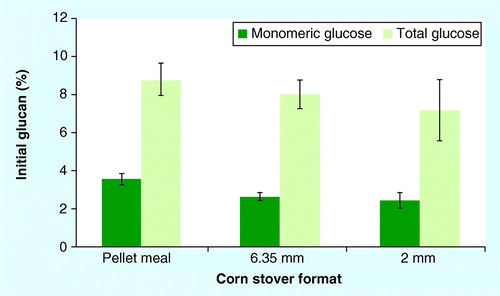
Mean ± 1 standard deviation; n = 4.
TEY: Theoretical maximum ethanol yield.
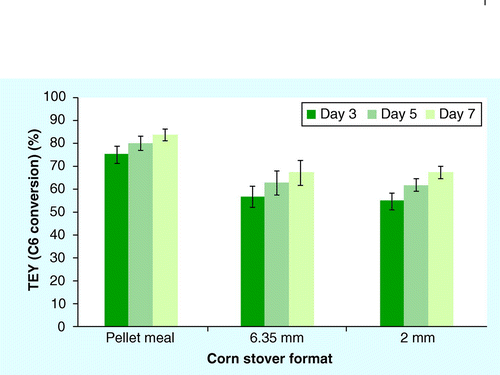
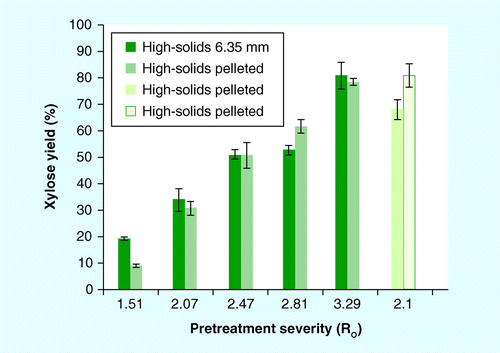
Mean ± 1 standard deviation; n = 3.
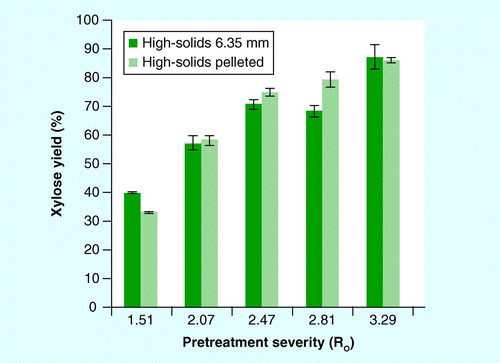
Mean ± 1 standard deviation; n = 3.
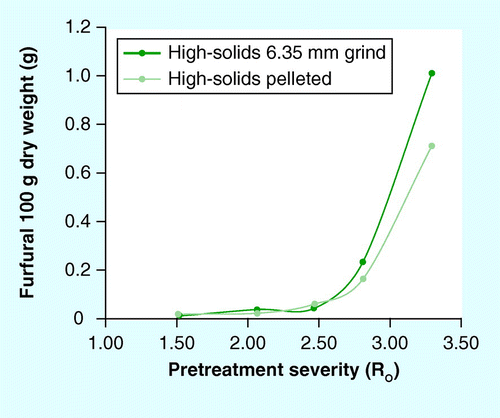
Mean ± 1 standard deviation; n = 3.
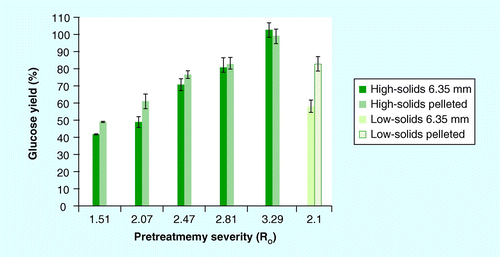
Reactivity is defined as the fraction of the glucose and xylose released from pretreatment and enzymatic hydrolysis, divided by the initial mass of glucose and xylose in the native feedstock.
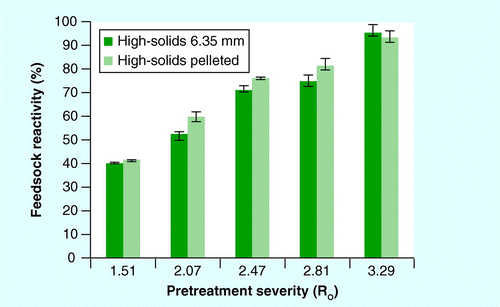
(A) Native corn stover at 700× magnification and (B) native corn stover at 100× magnification; (C) pelleted corn stover at 700× magnification and (D) pelleted corn stover at 440× magnification.
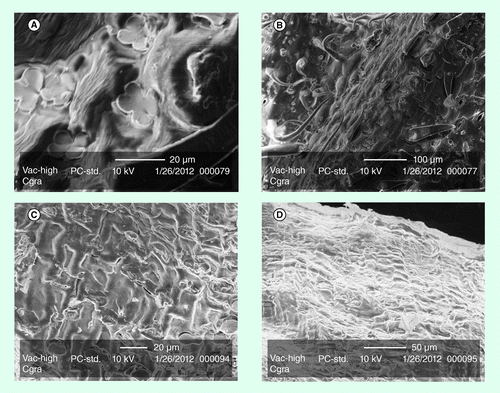
There is a significant difference between treatments (p ≤ 0.05) if the letters above the bars are different (Bonferroni post-hoc adjustments).
BET: Brunauer–Emmett–Teller.
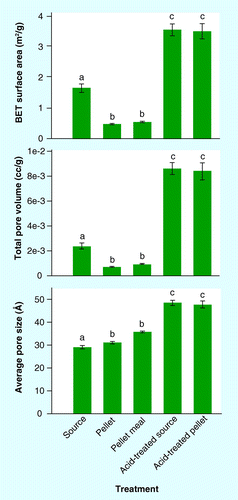
Table 1. Pretreatment conditions for high-solids pretreatment experiments using the ZipperClave®.
Table 2. Particle size distribution parameters (mean ± 1 standard deviation; n = 3) of corn stover formats†.
Table 3. Degrees of freedom, F-values and p-values from a one-way analysis of variance for Brunauer–Emmett–Teller surface area, total pore volume and average pore size.