Figures & data
(A) Emphirical design method, (B) Theoretical design method, (C) Laboratory method and (D) Pilot plant technique method.
Modified with permission from Citation[20].
![Figure 2. Design procedure of CO2 absorber. (A) Emphirical design method, (B) Theoretical design method, (C) Laboratory method and (D) Pilot plant technique method.Modified with permission from Citation[20].](/cms/asset/f5b6d836-6db6-426a-9b02-9b012432bd13/tcmt_a_10816195_f0002.gif)
CB: Concentration; G: Gas; L: Liquid; PA: Partial pressure.
Modified with permission from Citation[20].
![Figure 4. Small cell used for laboratory method.CB: Concentration; G: Gas; L: Liquid; PA: Partial pressure.Modified with permission from Citation[20].](/cms/asset/730fbbe9-a76f-4f23-928c-65e954cd2112/tcmt_a_10816195_f0004.gif)
γ: Unit volume of liquid; av: Interfacial area; CB: Concentration; G: Gas; KG; Overall gas mass transfer coeffiecient; KL; Overall liquid mass transfer coeffiecient; L: Liquid; PA: Partial pressure; Z: Height.
![Figure 5. String-of-sphere column Citation[45].γ: Unit volume of liquid; av: Interfacial area; CB: Concentration; G: Gas; KG; Overall gas mass transfer coeffiecient; KL; Overall liquid mass transfer coeffiecient; L: Liquid; PA: Partial pressure; Z: Height.](/cms/asset/3881253e-4dc1-4f20-891c-98826cced528/tcmt_a_10816195_f0005.gif)
Modified from with permission from Citation[20].
CB: Concentration; G: Gas; L: Liquid; PA: Partial pressure; Zm: Height.
![Figure 6. Pilot plant technique.Modified from with permission from Citation[20].CB: Concentration; G: Gas; L: Liquid; PA: Partial pressure; Zm: Height.](/cms/asset/bad5aa69-f32b-4d22-b996-9a156f8677eb/tcmt_a_10816195_f0006.gif)
HEX: Heat exchanger; L: Liquid; P: Pump; V: Vapour.
Reproduced with permission from Citation[15].
![Figure 7. Pilot plant schematic process flow diagram for (A) ITC, Esbjerg CASTOR and ITT (B) SINTEF/NTNU.HEX: Heat exchanger; L: Liquid; P: Pump; V: Vapour.Reproduced with permission from Citation[15].](/cms/asset/8dfd4f88-0384-4272-beb4-9567610ed241/tcmt_a_10816195_f0007.gif)
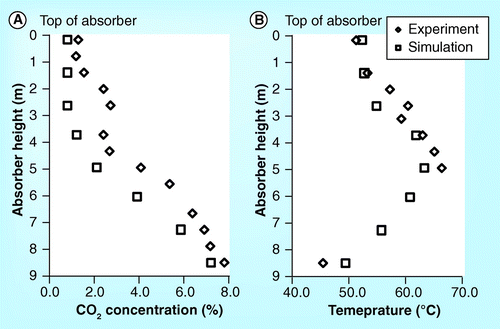
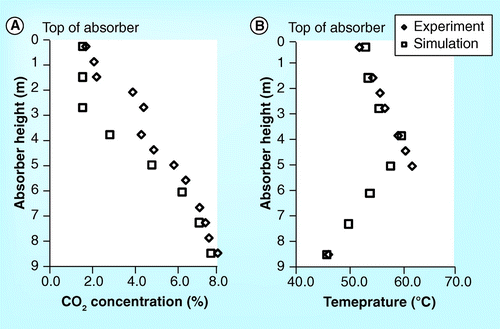
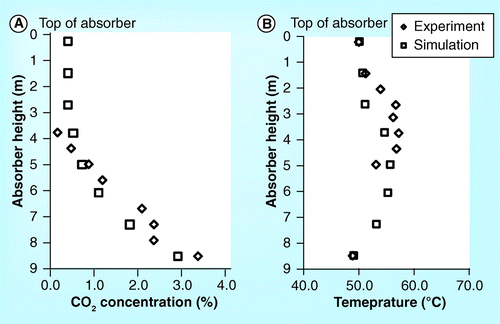
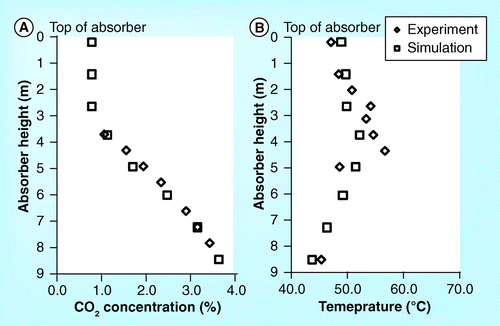
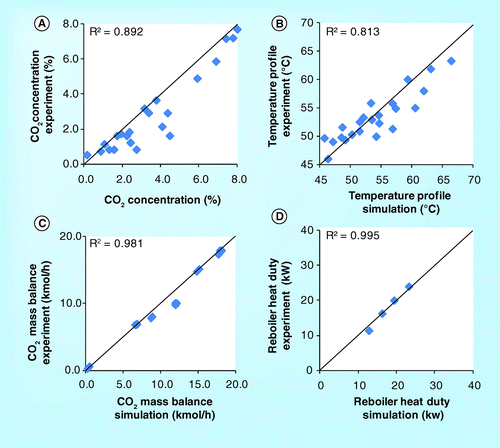
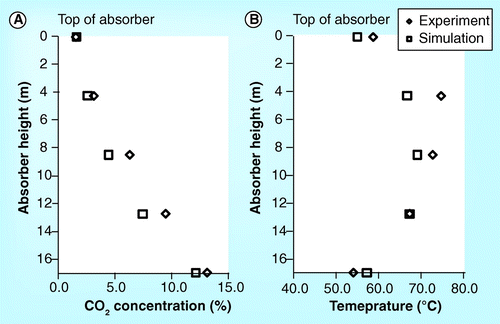
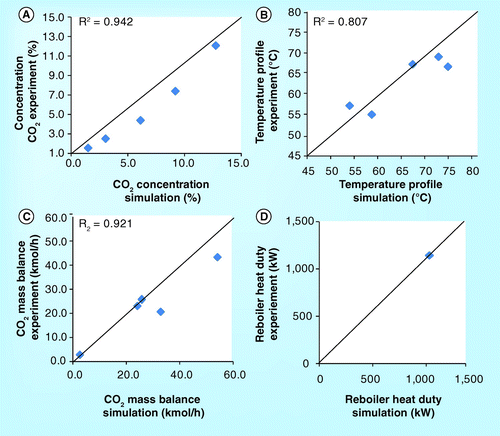
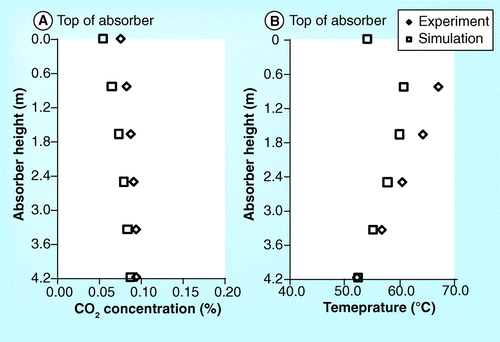
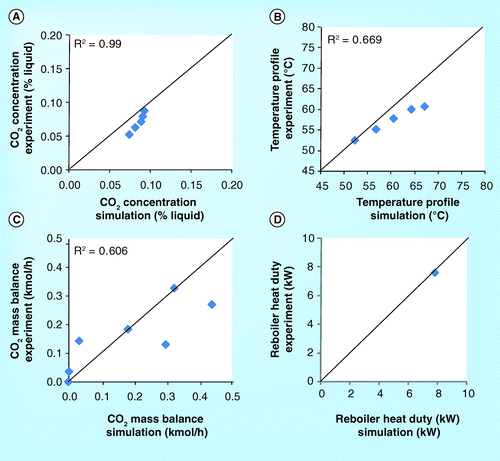
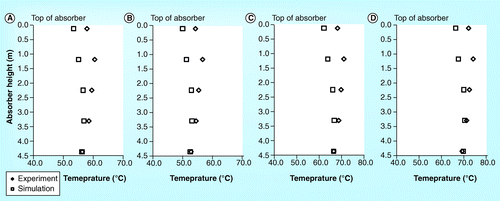
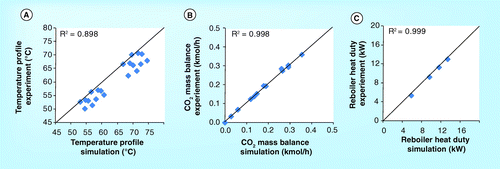
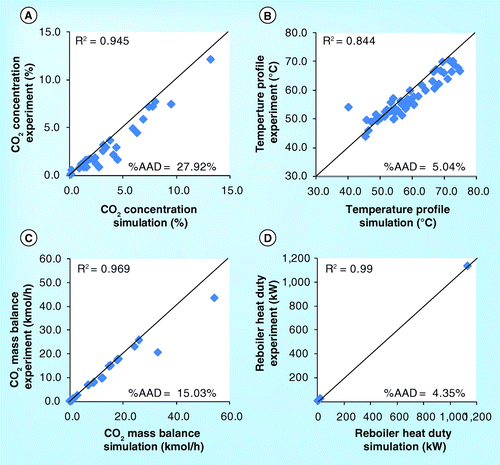
G: Generator; HX: Heat exchanger; PM: Particulate matter; RH: Reheater; SH: Superheater.
Modified with permission from Citation[16].
![Figure 20a. (A) An integration of CO2 capture into pulverized coal-fired power plant.G: Generator; HX: Heat exchanger; PM: Particulate matter; RH: Reheater; SH: Superheater.Modified with permission from Citation[16].](/cms/asset/7b290f64-23e7-4a7d-889e-b5845e259f69/tcmt_a_10816195_f0020a.gif)
Comp: Compressor; G: Generator; GT: Gar turbine; HP: High-pressure turbine; HX: Heat exchanger; IP: Intermediate-pressure turbine; LP: Low-pressure turbine.
Bolded numbers 1–4 indicate a connection of each stream line.
Modified with permission from Citation[50].
![Figure 20b. (B) An integration of CO2 capture into combined cycle gas turbine power plant.Comp: Compressor; G: Generator; GT: Gar turbine; HP: High-pressure turbine; HX: Heat exchanger; IP: Intermediate-pressure turbine; LP: Low-pressure turbine.Bolded numbers 1–4 indicate a connection of each stream line.Modified with permission from Citation[50].](/cms/asset/83164e02-1d98-471a-8c33-47eba105ca0b/tcmt_a_10816195_f0020b.gif)
G: Generator; IP: Intermediate-pressure turbine; LP: Low-pressure turbine.
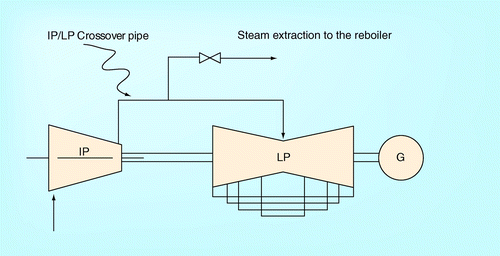
G: Generator; IP: Intermediate-pressure turbine; LP: Low-pressure turbine.
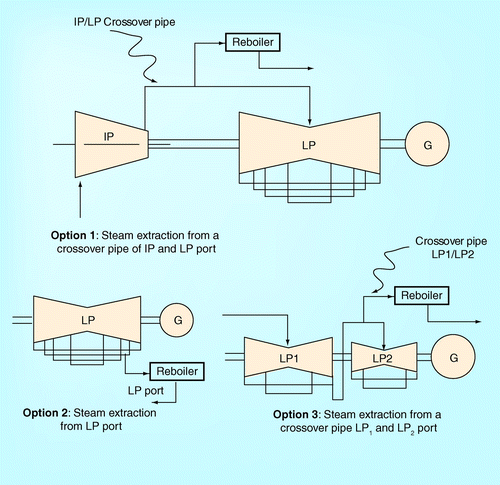
Table 1. Brief description of process parameters in four different pilot plants.