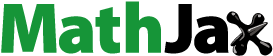
Highlights
• | Nanosecond pulse electric field-induced assembles of TNTs agglomerates. |
• | Controlled fabrication of linear dense assembles of TNTs (LATNTs) in polymer matrix. |
• | The noticeable decrease of electric resistivity by the LATNTs. |
• | Electron transfer routes in polymeric nanocomposites by reduced amounts of TNTs. |
Abstract
A facile technique has been introduced for incorporating TiO2 nanotubes (TNTs) in amorphous polysiloxane-based nanocomposite films and for linear and dense assembling of these TNTs (LATNTs) under application of nanosecond pulse electric field. The use of a nanosecond electrical pulse enables the application of high electric power without causing dielectric breakdown, which occurs when DC/AC electric field is used, and the formation of LATNTs which anchor the resulting composite film planes. The properties of the nanocomposites were investigated using X-ray micro CT scanning, digital micrographs, UV–vis spectroscopy and electrical resistivity measurements. More than 5.5-fold UV–vis transmittance improvement was obtained by the polymer composite containing LATNTs (TNT 5.0 wt%). Such a composite exhibited a decreased electric resistivity of 3.08 × 107 Ω m compared to the case for randomly distributed TNTs (3.25 × 108 Ω m).
1 Introduction
Titanium oxide (TiO2) is used extensively in industry as an additive in plastics and cosmetics, as a catalyst and catalyst support, and for photochemical degradation of toxic chemicals [Citation1]. Incorporation of TiO2 in polymeric nanocomposites is anticipated to have a wide range of applications, particularly in dye-sensitized solar cells, fire retardant composites, and photocatalysts [Citation2,Citation3]. In addition, the existence of TiO2 nanoparticles enhances the shear strength, thermal stability, flexural strength and other mechanical and thermal properties of neat epoxy in composite materials [Citation4,Citation5]. However, TiO2 nanoparticles have limited specific surface area compared with TiO2 nanotubes (TNTs) thereby limiting their extended applications involving adsorption as photocatalysts. TNTs have surface area 4–5 times that of pristine TiO2 nanoparticles [Citation6].
Self-organized TNTs were synthesized using the chemical synthesis method by Kasuga et al. in 1998 when it was first established, and have subsequently attracted a lot of attentions [Citation6,Citation7]. The hydrothermal method enables the self-assembled TNTs under one-step batch reaction with high purity and uniform outside diameter of about 10 nm without a special template [Citation6]. The TNTs have attractive characteristics, such as the longer lifetime of photogenerated carriers of light excitation [Citation8] and larger surface area compared with those of TiO2 nanoparticles [Citation7]. Furthermore, high density hydroxyl groups covering the surfaces of TNTs facilitate easier adsorption of other organic molecules [Citation9]. Due to their semiconducting properties with a band gap of about 3.2 eV and their chemical stability, TNTs are widely applied as catalysts for highly effective photocatalysis [Citation10], dye-sensitized solar cells [Citation11,Citation12], optoelectronic devices [Citation13], gas sensors [Citation14] and electrochemical displays [Citation15].
Recently, studies on the fabrication of organic-inorganic nanocomposites have been actively carried out because controlling the orientation and assembly of inorganic fillers with high thermal, electrical and optical properties in an organic polymer matrix can lead to a composite with superior physical properties [Citation16–Citation18]. However, there have been few reports on polymer-based nanocomposite films incorporating TNTs with controlled assembles using reduced filler amount. This is our major motivation for the present study. In our work, we chose to incorporate TNTs in amorphous polysiloxane-based nanocomposite films and then facilitated the formation of linear assembles of the TNTs by applying a nanosecond pulse electric field. The method for generation of nanosecond pulse electric field was first introduced by our group and demonstrated the generation of high power without causing electrical breakdown [Citation19]. This technology can thus be used for the synthesis of a controlled organic-inorganic nanocomposite structure with oriented alignment of inorganic filler in a polymer matrix through a variety of ways [Citation20].
Thus, in this work, the fabrication of linear assembles composed of TNTs agglomerates was investigated in a polymer using nanosecond pulses with an attempt toward producing new and improved properties. Optical transmittance, electrical resistivity measurements and X-ray micro CT scanning were used to evaluate the nanocomposites.
2 Experimental procedure
Polysiloxane/TNTs nanocomposites were prepared by introducing TNTs into a polysiloxane pre-polymer mixture. The TNTs were synthesized using a modified method [Citation21], based on the method developed by Kasuga et al. [Citation6,Citation7]. Two pre-polymers with different viscosities were used to prepare the polysiloxane: YE5822(A) (viscosity: 1.2 Pa s, Mwav: 21,000) and YE5822(B) (viscosity: 0.2 Pa s, Mwav: 16,000) (Momentive Performance Materials). The electrode for applying the electric field was an indium tin oxide-coated glass slide (2.5 mm × 7.5 mm × 1.0 mm) which has a surface resistivity of 8–12 Ω/sq (Sigma–Aldrich).
Various amounts (1–5 wt.%) of TNTs were incorporated into the pre-polymer of polysiloxane. For example, 0.0333 g of the TNTs (1 wt.%) were distributed in 3 g of pre-polymer YE5822(A) by ultrasonic treatment for 10 min after mechanical stirring at 1500 rpm for 10 min. After that, 0.3 g of YE5822(B) were introduced into the mixture; which was then sonicated for 10 min to produce a homogeneous dispersion. This suspension was placed on a polyamide spacer (1.2 mm × 1.2 mm × 120 μm), which was placed between two electrodes. DC (100 V) and nanosecond pulse electric fields were applied for 16 h at room temperature to enhance the orientation and assembly by relocation of the TNTs in the pre-polymer suspensions. The experimental conditions are DC electric field of 100 V and nanosecond electric field of 3 kV in voltage, 50 Hz of repetition rate, 70 ns of pulse width. The technology of pulse generation and its application into fabrication of polymer-nanocomposites are described elsewhere [Citation22]. Finally, the prepared composites were dried for 30 min at 80 °C to complete the curing.
The surface morphology and microstructure of the samples were investigated using field emission scanning electron microscopy (FE-SEM, Japan Electronic Products, JSM-6700F), and high-resolution transmission electron microscopy (HR-TEM, Japan Electronic Products, JEM-2000FX). The orientation and linear structure of TNT fillers in the polysiloxane matrix were observed using a digital microscope (Keyence, VHX-9000) after cross-sectional cutting the films. To evaluate the structural variation of the filler, optical transmittance and reflectance of the composites were measured using a UV-VIS V-630 recording spectrophotometer (UV–vis; V630, JASCO). The electric resistivity of the composite films was measured using a multimeter (Advantest R6581) and an AC/DC power supply (Hioki, wt-8752) by employing the two-point probe method, which is capable of measuring high surface resistivity. The measured resistance R is converted into volume resistivity ρ by using the following equation [Citation23]:where S is the cross-sectional area perpendicular to the current and d the thickness of the sample between the two electrodes the value of the volume resistivity (Ω m) was used as that of electrical resistivity of the composite.
The linear distribution of TNTs in the matrix was observed by a high resolution X-ray micro CT scanner (SkyScan1172, Bruker micro CT), which was operated at 60 kV, with a 1350 ms exposure time and a 0.25° rotation step.
3 Results and discussions
((a) and (b)) shows SEM images and (c) shows a TEM image of the TNTs synthesized in this work. The TEM image clearly shows an outer and inner diameter of around 8–10 and 5–7 nm, respectively. The length of the TNTs can be varied depending upon the kind of raw TiO2 nanoparticles used [Citation1]. In addition, the TNTs are aggregated together in the range of 1–15 μm based on the diameter of entangled TNTs ((a)).
Fig. 1 SEM images of TNTs: (a) low magnification (5000×), (b) high magnification (100,000×), and (c) TEM image of TNTs.
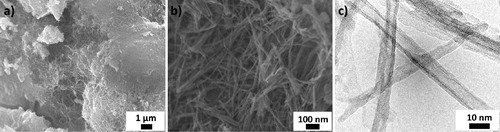
shows X-ray micro CT scanning images of the TNT aggregates, exposing the formation of a linear assembled structure in response to the applied nanosecond pulse electric field. The bright domains in the composites are TNT aggregates which are visualized by scattering of the irradiated X-ray. However, it should be noted that the TNTs aggregates, which are less than 0.8 μm in diameter, do not appear as bright domain due to the limitation of sensitivity. (a-1) showing minimum bright TNTs domains implies that TNTs are well distributed without forming assembly as shown in ((a-2) and (a-3)). It is noticed that the brightness of the TNTs agglomerates and LATNTs are getting more distinct as the TNTs content increases from ((a-1 to a-3) to (c-1 to c-3)). For example, the brightness becomes distinct as the filler amount increases from 1 wt.% to 5 wt.%. Furthermore, ((a-3) to (c-3)) shows that no pore was observed. This means that the TNTs agglomerates are formed by the denser population of TNTs. Additionally, as the added amount of TNTs increases, the population of LATNTs increases because the density of the aligned TNT chains becomes larger. ((a-1), (b-1), and (c-1)) shows that without an applied electric field, the TNTs are distributed without localization occupying the whole composite film plane. However, ((a-2), (b-2), and (c-2)) shows that, by applying nanosecond electric pulses, the TNTs anchor the film planes inside the polymer matrix like bridges. Samples of 1 and 3 wt% TNTs formed the straight line shaped LATNTs from bottom to top surfaces. On the other hand, sample of 5 wt% TNTs formed the LATNTs branched which are interconnected during electric field-inducement. The same branched structure was formed in the results of the electric field orientation of the carbon nanotube system [Citation24]. The reason for forming the branched structure is influenced by the electric field from the adjacent LATNTs. From this result, the structure of the LATNTs is influenced by the contents of TNTs. In case of the contents of TNTs below percolation threshold, the straight line shaped LATNTs were formed. In case of the contents of TNTs over percolation threshold, the branched shaped LATNTs were formed. The 3D internal structure of the polysiloxane/TNT nanocomposites was successfully observed by X-ray CT scan with high resolution. However, the contrast of images is automatically adjusted in the X-ray CT scan. Therefore, estimation of the absolute size of the LATNTs by the X-ray CT scan is very difficult. The diameter and size of LATNTs were estimated using cross-sectional micrographs.
Fig. 2 X-ray micro CT-scan images of polysiloxane/TNT nanocomposites prepared without an electric field or with different nanosecond pulse electric fields. Cross-section view of (a-1) without electric field for 1 wt.% TNTs, (a-2) nanosecond pulse electric field for 1 wt.% TNTs, (b-1) without electric field for 3 wt.% TNTs, (b-2) nanosecond pulse electric field for 3 wt.% TNTs, (c-1) without electric field for 5 wt.% TNTs, (c-2) nanosecond pulse electric field for 5 wt.% TNTs. And plane view of (a-3) nanosecond pulse electric field for 1 wt.% TNTs, (b-3) nanosecond pulse electric field for 3 wt.% TNTs, (c-3) nanosecond pulse electric field for 5 wt.% TNTs.
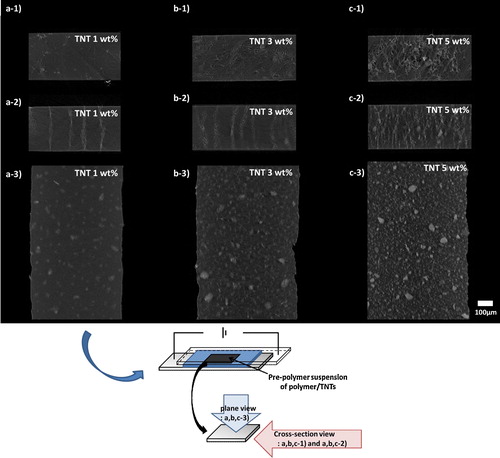
shows cross-sectional micrographs of polysiloxane/TNT nanocomposites fabricated under different electric fields. The cross-sectional micrographs in (a-1) to (a-3) reveal that many TNTs agglomerate. These agglomerates are homogeneously distributed over a smaller scale in the polymer with the application of an electric field. They form linearly aligned assembly when a nanosecond pulse field is applied, as seen in ((a-2), (b-2), and (c-2)). Comparison of the cross-sectional images in ((a-2) and (c-2)) reveals that the LATNTs fabricated under 5 wt.% of TNTs are thinner and lager in number than those fabricated under a 1 wt.% of TNTs. The diameter of the LATNTs are almost several tens micrometers in all samples. This is almost same as the size of the agglomerates of TNTs. On the other hand, the density of the LATNTs increased with the amount of TNTs.
Fig. 3 Digital micrographs of polysiloxane/TNT nanocomposites prepared by applying different electric fields; (a-1) without electric field for 1 wt.% TNT, (b-1) without electric field for 3 wt.% TNT, (c-1) without electric field for 5 wt.% for TiO2 NT, and (a-2) nanosecond pulse field for 1 wt.% TNT, (b-1) nanosecond pulse field for 3 wt% TNT, (c-1) nanosecond pulse field for 5 wt.% TNT.
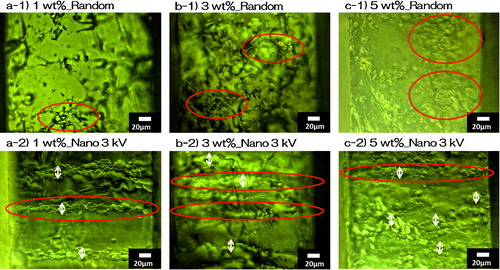
shows UV–vis transmittance spectra of the nanocomposites which were fabricated under different electric fields. The TNTs agglomerates influenced the optical properties of the composite under the light in UV–visible range. The composites prepared under the nanosecond pulse electric field contributed to the higher optical transmittance and the lower reflectance compared with those prepared under DC 100 V. Although the neat polymer showed almost 100% transmission, the addition of just 1 wt.% of the TNTs with random distribution caused the transmission to decrease to 20% ((a-1)). With incorporation of TNT 1 wt%, the composite prepared under the nanosecond pulse exhibited 70% of transmittance (at wavelength 800 nm), which is 3.5 times higher than the case with random distribution of TNTs (20%). Even though the overall transmittance was decreased by increasing TNT contents to 5 wt%, the nanosecond pulse electric field motivated 5.6-fold transmittance (2.8%) of composite comparing with the one with random distribution of TNTs (0.5%). Since the value of transmittance (%) has reversed relationship with reflectance (%), the lowest reflectance value which is influenced by the nanosecond pulse confirms the improved effect of optical transmittance.
Fig. 4 UV–vis transmittance of nanocomposites under different electric fields: (a-1) 1 wt.% TNTs, (b-1) 3 wt.% TNTs and (c-1) 5 wt.% TNTs. Diffuse reflectance of nanocomposites containing TNTs without an electric field and with nanosecond pulse field for (a-2) 1 wt.% TNTs, (b-2) 3 wt.% TNTs, and (c-2) 5 wt.% TNTs.
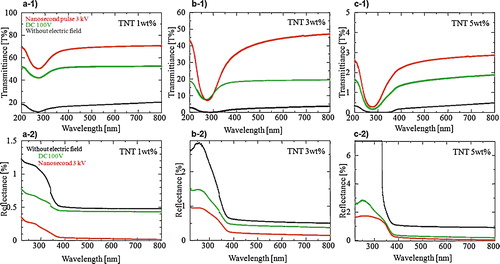
The optical band gap energy calculated from the UV–vis absorption spectra, assuming indirect transitions for TiO2 nanoparticles, is approximately 3.41–3.45 eV for chemically synthesized TNTs [Citation25]. It is considered that this is because the TNTs do not absorb visible light and because they have such a wide band gap [Citation26].
The transmittance is also increased by the electric field-induced localization of TNT aggregates in which the nanosecond pulse motivated the higher efficiency of optical transmittance than the DC. We have confirmed that the pre-polymer suspension with incorporation of TNT 5 wt.% cannot avoid electric breakdown when the applied DC/AC voltage is higher than 200 V (data are not shown here). From this point of view, the application to 3 kV of electric field by nanosecond pulse width without electric breakdown is influential technique for localization of TNTs fillers in polymer-based composites. This can be explained related with the cross-section views of composites in . In the case of composites with random distribution of TNTs, when UV–vis light is applied perpendicular to the composite planes the light will be reflected or scattered by homogeneously dispersed TNTs through the polymer matrix. However, the composites with LATNTs which are assembled perpendicular to the film planes have less domains for TNTs-to-UV-vis light contact, which results in higher optical transmittance and the lower reflectance.
shows electrical resistivities of the nanocomposites as a function of the TNT content, for samples obtained with and without electric field. The thickness of obtained composite films ranges from 220 to 230 μm. With addition of a very small amount (1 wt%) of TNTs under application of nanosecond pulse electric field, the formation of the LATNTs reduced the resistivity to 2.95 × 108 Ω m. This is comparable to the resistivity of the composite film fabricated without electric field (3.08 × 107 Ω m). Also, despite the high electrical resistance of the TiO2 nanoparticles of 108 Ω m [Citation27], the TNTs resistivity was found to be significantly low at 3.37 × 105 Ω m [Citation28]. The electrical resistance was found to decrease with increasing TNT content, suggesting the addition of TNTs yields a good electrode. As shown in , the TNTs agglomerates which anchor the film surfaces inside the polymer matrix make their population denser in the linear assembled structure making the filler-to-filler gaps narrower as increase of the filler content. Thus, the existence of a large amount of TNTs forming the LATNTs motivated the noticeable decrease of electric resistivity of the resulting composites.
Fig. 5 Electrical resistivities of nanocomposites as a function of TNT content under different electric fields.
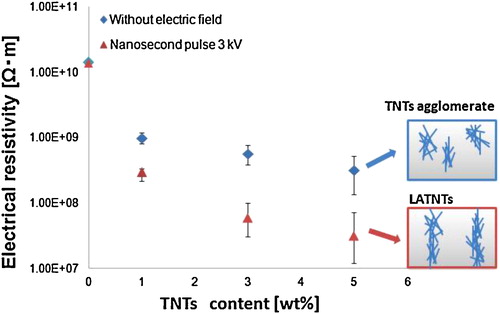
It is considered that the electron transport through the LATNTs is faster than the structure with vertically oriented TNT arrays without development to linear assemble resulting in a decrease in resistivity. We believe that the linear structure of the TNTs thus would play an important role for electron transport in dye-sensitized solar cells (DSSCs) [Citation29]. Application of TNTs rather than TiO2 nanoparticles in DSSCs contributed to the higher overall cell efficiency because the TNTs with the higher aspect ratio that can serve as routes for electron express way [Citation30], which implies that facilitating the narrower filler-to-filler gaps for the shorter route of electron transfer is one of the overwhelming factors in DSSCs. The tuning technology of nanosecond pulse-induced assembly of TNTs agglomerates in polymer-based nanocomposites, therefore, is expected to lead to improved electron transport in DSSCs.
4 Conclusions
Polysiloxane-based nanocomposite films incorporating linear dense assembles of TNTs (LATNTs) were fabricated by applying a nanosecond pulsed electric field, which caused no damage to the nanocomposites. The presence of the LATNTs enhanced the optical transmittance over 5.6 times comparing with the one with random distribution of TNTs. Also, decreased the electric resistivity to 3.25 × 108 Ω m comparing with 3.08 × 107 Ω m of the composite without the LATNTs. The LATNTs anchoring the film planes worked as electron transfer routes, which resulted in a noticeable decrease of electric resistivity. This field-induced technology of tuning TNT agglomerates into linear assembly may pave a way for polymer-based nanocomposits, such as, nanoscale semiconductor devices and dye-sensitized solar cells.
Notes
Peer review under responsibility of The Ceramic Society of Japan and the Korean Ceramic Society.
References
- T.SekinoInorg. Metal. Nanotubular Mater.11720101732
- B.O’ReganM.GrätzelNature3531991737740
- M.GrätzelNature4142001338344
- A.ChatterjeeM.S.IslamMater. Sci. Eng. A4872008574585
- L.XiongH.B.LiangR.M.WangY.PangPolym. Plast. Technol.49201014831488
- T.B.KasugaM.HiramatsuA.HosonT.SekinoK.NiiharaAdv. Mater.11199913071311
- T.KasugaM.HiramatsuA.HosonT.SekinoK.NiiharaLangmuir14199831603163
- M.ZhangZ.JinJ.ZhangX.GuoJ.YangW.LiX.WangZ.ZhangJ. Mol. Catal. A: Chem.2172004203210
- P.UmekP.CeveA.JesihA.GloterC.P.EwelsD.ArconChem. Mater.17200559455950
- Y.JiaguoD.GaopengH.BaibiaoJ. Phys. Chem. C11320091639416401
- K.Jang-YulS.TohruT.Shun-IchiroJ. Mater. Sci.46201117491757
- O.YoshinoriM.naruhikoK.TakayukiW.YujiO.TakumiS.TourN.KohichiY.ShozoPhys. Chem. Chem. Phys.7200541574163
- Z.JianpingZ.QingH.KaiM.NicolaJ. Phys. Chem. C11420101072510729
- S.Min-HyunY.MasayoshiK.TetsuyaH.Jeung-SooS.KengoY.NoboruSens. Actuators B1372009513520
- A.GhicovP.SchmukiChem. Commun.2791–28082009
- M.B.RadoicicZ.V.SaponjicM.T.Marinovic-CincovicS.P.AhrenielN.M.BibicJ.M.NedeljkovicJ. Serb. Chem. soc.772012699714
- L.SuY.X.GanCompos. Part B432012170182
- L.MeifangH.YingC.QilinL.ChunzhongMacromol. Sci. Phys.492010419428
- T.YokooT.ImafukuN.OshimaW.JiangK.YatsuiT.GotoH.KusamaT.InamiV.TarasenkoPapers of Technical Meeting on Pulsed Power TechnologyIEEE Japan, PPT-0420043740
- H.-B.ChoM.ShojiT.FujiwaraT.NakayamaH.SuematsuT.SuzukiK.NiiharaJ. Ceram. Soc. Jpn.11820106669
- J.-W.LeeH.-B.ChoT.NakayamaT.SekionS.-I.TanakaK.MinatoT.UenoT.SuzukiH.SuematsuY.TokoiK.NiiharaJ. Ceram. Soc. Jpn.1212013123127
- H.-B.ChoN.C.TuT.FujiharaS.EndoT.SuzukiS.TanakaW.JiangH.SuematsuK.NiiharaT.NakayamaMater. Lett.65201124262428
- L.BokobzaPolymer Nanotube Nanocomposites: Synthesis, Properties, and Applications2010WileyUSA
- H.-B.ChoM.HuynhT.NakayamaS.NguyenH.SuematsuT.SuzukiW.JiangS.TanakaY.TokoiS.LeeT.SekinoK.NiiharaJ. Nano Mater.20132013110
- T.SekinoJ. Ceram. Soc. Jpn.412006261271 (in Japanese)
- H.AkiraOrganic, Inorganic, and Metallic Nanotubular Materials2008FrontierJapan
- H.TangK.PrasadR.SanjinesP.E.SchmidF.LevyJ. Appl. Phys.75199420422047
- T.SekinoT.OkamotoT.KasugaT.KusunoseT.NakayamaK.NiiharaKey Eng. Mater.317–3782006251255
- H.Shin-YuS.ChaochinK.SasipriyaL.Chung-YenL.Wen-RenThin Solid Films5292013123127
- S.YoshikazuN.SupachaiA.KeisukeY.SusumuJ. Jpn. Soc.532006202208