Abstract
Processing of mullite and alumina based refractory ceramic by unidirectional dry pressing, from two mixtures that include silica sand, pure alumina (PA) and recycled alumina (RA) is described. The samples were sintered up to 1600 °C to study the refractory properties. The fired properties of materials (firing shrinkage, water absorption, density, flexural strength, refractoriness, and SEM microstructure) were evaluated. Promising refractories materials based on mullite and alumina were obtained.
Keywords:
1 Introduction
Dense alumina ceramics are widely used for structural applications, such as armor systems, wear resistance applications and some other fields where there are situations of severe mechanical stresses often coupled with corrosive and thermal actions. On the other hand, mullite is having not only good to high temperature properties but also excellent electrical insulating ability making it potentially useful in applications ranging from refractories to electronic substrates. Mullite and corundum are known to have excellent thermal stability and have a high level of mechanical properties; for example, some materials can be successfully used in abrasion and erosion environments; armor systems based on some kinds of alumina ceramics can support high-velocity projectiles with steel, lead and even tungsten carbide cores [Citation1–Citation13].
A presence of the mullite phase in alumina ceramics may have a positive effect on ceramic properties. Alumina ceramics with an Al2O3 content of 72–76 wt.% containing mullite demonstrated remarkable technological and mechanical properties, e.g. flexural strength up to 350 MPa, and the sample shows a low density [Citation14].
In previous studies by present authors [Citation15–Citation17], different compositions of Moroccan geomaterials (kaolin clay, red clay, marl, silica sand, perlite, etc.) allowed obtaining a good quality of refractory between 1400 and 1600 °C. The present work aims to develop mullite and alumina-based ceramic refractories, shaped by unidirectional pressing of dried powder mixtures made of pure alumina (PA), recycled alumina (RA) with a remarkable content of mullite, and common natural raw materials, such as silica sand. These products should present high thermal stability, electrical insulating properties, and strong mechanical strength. A detailed description about the processing and evaluation of the ultimate materials properties is given.
2 Materials and experimental procedure
2.1 Raw materials
Silica sand used in this study comes from an artisanal quarry, located at 3 km SE of the Mechraa Hammadi Dam (Morocco). The sands appear as a thin layer of a white-pink and friable rock, belonging to the series of limestone of the upper Jurassic [Citation16] ().
The fine alumina powders (PA) commercialized by Super Cerame (Morocco) have characteristics and specific functions in terms of rheology, mechanical strength and refractoriness (density: 0.7 g/cm3; specific surface areas BET: 0.6 m2/g; loss at 100 °C: <0.5%). Our choice was mainly guided by its high purity of alumina (Al2O3: 99.4%; Na2O < 0.5%; CaO < 0.05%; Fe2O3 < 0.04%; SiO2 < 0.04%). The different size classes of this alumina are given in . The mineralogical composition of recycled and pure alumina was analyzed using X ray diffractometer (XPERT DATA COLLECTER software) operating at 40 kV and 40 mA and using CuKα radiation. The analysis showed the presence of alumina (a). The contamination level of silica–alumina refractory materials used as coatings in kilns in the ceramics industry is low. It is for this reason that firebrick having undergone three years of use as a coating in a kiln was finely milled to obtain a white aluminous powder noted ‘RA’ (Al2O3: 71.14%; Na2O: 0.63%; CaO: 0.18%; Fe2O3: 0.93%; K2O: 1.05%; SiO2: 25.12%). Mineralogical analysis of this powder shows that it consists mainly of mullite (b). The spectra show the presence of cristobalite at 2θ = 22°, 44° and 56° ().
Table 1 Different granulometric fraction percent of pure alumina (PA).
2.2 Experimental techniques
Two different mixtures (named M1 [mullite-based] and M2 [alumina-based]) were prepared, combining the started materials in the proportions given in . The procedure used to prepare and evaluate the materials is schematically shown in [Citation16,Citation17]. For each formulation, three bricks were tested and the average value was taken.
Table 2 Tested batch formulations (wt.%).
The fired properties of the samples were evaluated and are given in and and respectively. The apparent density, water absorption and open porosity were measured according to ASTM C373-88 [Citation18–Citation20]. Fired products were characterized for mechanical properties such as flexural strengths with three-point bending. This test was carried out at an ambient temperature. The loading procedure consisted of applying a preliminary load (0.05 kN) at a rate of 0.5 mm/min to eliminate positioning defects of the specimens. The distance between bottom supports was 80 mm.
Table 3 Room temperature properties of M1 and M2 samples sintered at 1600 °C.
The samples microstructures were evaluated using scanning electron (SEM) and binocular microscopy. The observation of refractory sample under a binocular microscope identifies some traces related to the manufacturing technique, the characteristics of the briquette, and the size and color of inclusions and pores. The observation of the samples was performed using a binocular microscope OLYMPUS-SZX9 with a camera (DS Camera Head DS-5M). The cyclic thermal shock tests were performed according to DIN 51 068 [Citation21,Citation22]. The sample was heated for 15 min at 950 °C, and immediately immersed in the cooling water at 25 °C for 3 min.
3 Results and discussion
3.1 Technological characteristics
Technological characteristics results of the two samples fired at 1600 °C are given in . The substitution of pure alumina by recycled alumina has allowed improving the mechanical properties. The flexural strength is increased from 41.82 to 55.87 MPa. The relatively high mechanical properties of ceramic products are essentially due to their structure which is mainly composed of mullite and alumina [Citation15]. The presence of a crystalline phase in the ceramic matrix provides the piece with a high fired mechanical strength.
shows the influence of firing temperature on the bulk density and apparent porosity of the two mixtures. The bulk density increased as firing temperature increased from 1200 to 1600 °C. The bulk densities increased sharply from 1200 to 1400 °C due to the formation of high viscosity siliceous phase which facilitates precipitation of mullite [Citation23]. The fraction of this liquid phase depends on batch composition (amount of impurity) and firing temperature. Within the temperature range investigated, M1 with the highest impurity content (recycled alumina) recorded the highest bulk density. Above 1400 °C most of the Al2O3/SiO2 have transformed into mullite; therefore, slight change in densities was observed. The samples attained highest densities at 1600 °C, where complete mullitization has occurred. The M1 samples recorded the highest bulk density (2.23 g/cm3) followed by M2 (2.13 g/cm3). The formation of a glassy phase caused by the presence of fluxing agents and alkali oxides (CaO, MgO, Na2O, K2O) helped improve densification of the fired bricks.
The apparent porosity decreased for two mixtures over the firing temperature range. Between 1200 and 1600 °C, the apparent porosity decreased sharply. This is mainly attributed to the expansion that accompanies the quartz to cristobalite polymorphic transformations that occur on firing at such high temperatures closing the pores respectively [Citation24,Citation25]. The decrease in porosity reduces the volume of the bricks whilst improving the mechanical properties [Citation9].
shows the effect of firing temperature on the flexural strength of the two mixtures. The results indicate that absolute flexural strength values increased strongly with increasing firing temperatures. The flexural strength of the fired bricks is influenced by their phase composition. The increase of the highly refractory phases (cristobalite, alumina and mullite) and the densification of the bricks due to the presence of flux agents improved the flexural strength of the bricks.
Refractoriness of a material is strongly dependent on microstructural parameters such as grain size and shape, the relative volume of solid and vitreous phases, the viscosity of the vitreous phase and porosity [Citation16]. Refractoriness can be evaluated by examining the evolution of the morphology of test samples with increasing temperature under their own weight (without any other load). Refractoriness in this paper is defined as the temperature corresponding to the moment when a material begins to lose its shape (melting point). The samples tested here maintained their shape without undergoing any deformation up to 1600 °C (). They retain their original characteristics: no cracks, no deformation, no or low shrinkage and especially no color change at the end of the thermal cycle.
Fig. 7 Aspect of samples M1 and M2 fired at 1600 °C (other samples correspond to elaborate refractory from Moroccan geomaterials).
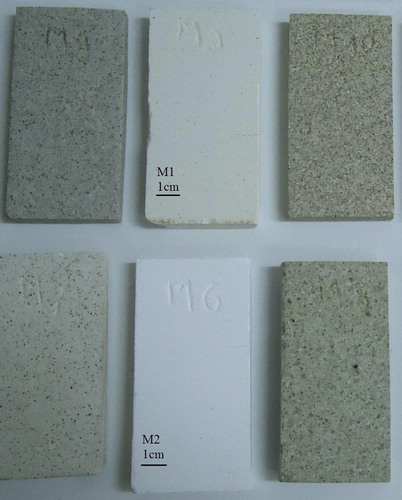
On the other hand, thermal shock resistance shows the ability of a structure to withstand rapid changes in temperature. The image of , illustrates the homogeneous character of the samples, subjected to 200 cycles of thermal shock with a temperature difference of 925 °C. No mass loss was observed. No cracks, no deformation, no color change, but more importantly no observed degradation show the refractory character of our developed samples.
Fig. 8 Aspect of samples fired at 1600 °C and having undergone 200 cycles of thermal shock with a temperature difference of 925 °C (after mechanical test).
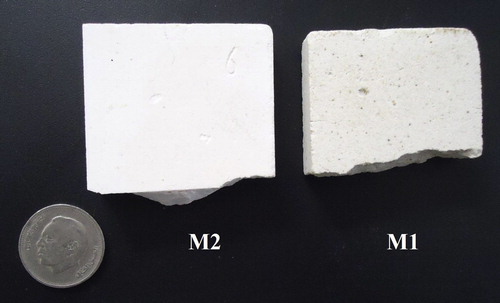
The chemical resistance to hydrochloric acid (pH 1.5) and NaOH (basic solution, pH 13) was studied. The refractory samples were placed in these solutions for 7 days to monitor the mass loss after chemical reaction. The results show that the developed refractory exhibits good chemical resistance since no mass loss was observed after reaction.
3.2 Structural characteristics
In order to identify the corresponding chemical composition, microstructural analyses were carried out at low (optic microscopy) and high magnifications (SEM and EDS) on the two samples M1 and M2 sintered at 1600 °C ( and ). The observation under an optical microscope (binocular) shows a high density. The sample M2 shows a homogeneous microstructure and especially richness in grains of alumina. This sample had a more compact structure than M1 where we can observe some pores that are often isolated and have globular shape (a and b).
Fig. 9 Optical micrographs: (a) highly dense structure of the firebrick M2 (×57) and (b) less compacted structure of the firebrick M1 (×57).
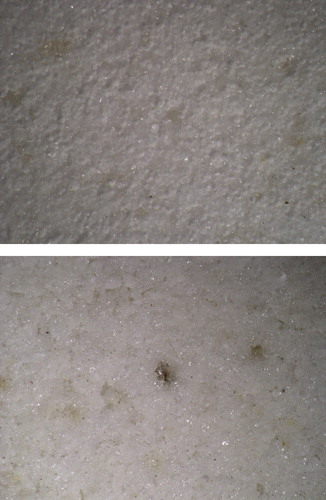
At high magnification, two different microstructures were observed. Hexagonal and facetted crystals of alumina with grain size of about 2–5 μm are observed (a). On the other hand, white–gray elongated grains of mullite are appeared in c, which is confirmed by the EDS data (d). It should be noted that the length of the synthesized mullite exceeds sometimes 10 μm (13 μm) that justifies the good mechanical properties obtained.
4 Conclusion
From the results of this study, the following conclusions were drawn:
- | Silica sand and recycled alumina prove to be efficient for elaboration of silica–alumina refractory. |
- | The substitution of pure alumina by recycled alumina has improved the flexural strength from 41.82 to 55.87 MPa. |
- | The refractory materials contain mullite and alumina. |
- | Very good dimensional stability, good mechanical characteristics and chemical resistance are obtained after firing at 1600 °C. |
Notes
Peer review under responsibility of The Ceramic Society of Japan and the Korean Ceramic Society.
References
- A.AndrewsE.Nsiah-BaafiS.K.Y.GawuP.A.OlubambiCeram. Int.40201460716075
- T.JuettnerH.MoertelV.SvinkaR.SvinkaJ. Eur. Ceram. Soc.27200714351441
- H.N.YoshimuraA.P.AbreuA.L.MolisaniA.C.de CamargoJ.C.S.PortelaN.E.NaritaCeram. Int.342008581591
- P.GehreC.WenzelC.G.AnezirisCeram. Int.37201117011704
- I.D.KatsavouM.K.KrokidaI.C.ZiomasCeram. Int.38201257475756
- C.AkselMater. Lett.572002708714
- C.AkselCeram. Int.292003183188
- A.LiH.ZhangH.YangCeram. Int.4020141258512590
- T.ShimizuK.MatsuuraH.FurueK.MatsuzakJ. Eur. Ceram. Soc.33201334293435
- B.MengJ.PengCeram. Int.39201315251531
- J.BaiCeram. Int.362010673678
- V.ViswabaskaranF.D.GnanamM.BalasubramanianAppl. Clay Sci.2520042935
- L.XuZ.XieL.GaoX.WangF.LianT.LiuW.LiCeram. Int.312005953958
- N.S.KostyukovE.Y.MedvedovskiF.Ya.KharitonovAcad. Sci., USSR1988 (in Russian)
- C.SadikI.El AmraniA.AlbizaneJ. Asian Ceram. Soc.220148396
- C.SadikI.El AmraniA.AlbizaneJ. Asian Ceram. Soc.12013351355
- C.SadikA.AlbizaneI.El AmraniJ. Mater. Environ. Sci.42013981986
- ASTM C326-03Standard Test Method for Drying and Firing Shrinkages of Ceramic Whiteware Clays, 15-02, Glass Ceramics2006
- ASTM C373-88Standard Test Method for Water Absorption, Bulk Density, Apparent Porosity, and Apparent Specific Gravity of Fired Whiteware Products, 15-02, Glass Ceramics2006
- ASTM C674-88Standard Test Methods for Flexural Properties of Ceramic White-Ware Materials, 15-02, Glass Ceramics2006
- M.KolliM.HamidoucheG.FantozziJ.ChevalierCeram. Int.33200714351443
- B.AmraneE.OuedraogoB.MamenS.DjaknounN.MesratiCeram. Int.37201132173227
- R.M.GermanLiquid Phase Sintering1985PlenumNew York
- G.RoutschkaVulkan Verlag, Essen, Germany1997
- D.A.BrosnanC.A.SchachtRefractories Handbook200479107