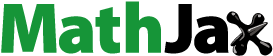
Abstract
Mesoporous alumina was synthesized by hydrothermal method at 150 °C for 6–24 h using tetramethyl urea followed by their calcination at 500–1100 °C. The samples were characterized by XRD, FTIR, N2 adsorption–desorption, FESEM and TEM. The γ-Al2O3 was found to be stable up to 1000 °C for the samples prepared at 150 °C/6 h, and up to 900 °C for the samples prepared at 150 °C/12–24 h. The BET surface area values of 500 °C treated samples were 428 m2 g−1, 393 m2 g−1, and 366 m2 g−1 for the reaction time of 6 h, 12 h and 24 h, respectively. FESEM and TEM showed the formation of alumina nanoparticles at 150 °C/6 h, which ripened to flake-shaped alumina comprising of alumina nanoflakes (70–100 nm) at 150 °C/12–24 h. To understand the role of tetramethyl urea, a tentative formation mechanism was illustrated.
1 Introduction
Because of high surface area and thermal stability, alumina is becoming an important functional material to be used widely as catalyst, catalyst supports, adsorbents, membranes, ceramics, etc. The performance of alumina as adsorbents, catalysts and catalyst supports is affected by its textural and morphological characteristics. Therefore, synthesis of mesoporous alumina (MA) with high surface area and nanostructured morphology has attracted a great deal of attention in recent times. For the synthesis of MA, different methods like sol–gel [Citation1], evaporation induced self-assembly (EISA) [Citation2,Citation3], spray pyrolysis method [Citation4], hard templating route using carbon [Citation5] have already been reported. Wu et al. [Citation6] synthesized MA by reverse precipitation method. Recently, we have synthesized MA with nanofiber [Citation7] and nanorod-like [Citation8] morphology.
In this communication, we have studied the role of tetramethyl urea (TMU) on the formation of mesoporous alumina. The time effect in changing alumina nanoparticles to flake-shaped alumina from 150 °C/6 h to 150 °C/12–24 h has also been reported in this study. To the best of our knowledge, the synthesis of mesoporous alumina using TMU via an aqueous based simple hydrothermal process has been reported for the first time.
2 Experimental
In a typical experiment, 5 mmol Al(NO3)3·9H2O (G.R. Merck, India, purity > 99%) was dissolved in 5 mL of deionized (DI) water under stirring for 10 min at room temperature. 100 mmol tetramethyl urea (99%, Sigma–Aldrich, USA) was added dropwise into the former solution. The mix solution was allowed to stir for 2 h to obtain a homogeneous solution. The above solution was transferred into a 50 mL Teflon-lined autoclave followed by hydrothermal reaction at 150 °C for 6 h, 12 h, and 24 h. After the reaction, the particles were collected by centrifugation and washed with acetone and DI water followed by drying at 60 °C over night. The dried samples were calcined at 500 °C for 1 h with a heating rate of 1 °C min−1, and at 700, 900, 1000, 1100 °C with a heating rate of 1 °C min−1 up to 500 °C/1 h followed by heating rate of 5 °C min−1 up to those temperatures with 1 h dwell time each.
The samples were characterized by powder X-ray diffraction (PXRD) (Philips X’Pert Pro PW 3050/60) with Ni-filtered CuKα radiation (λ = 0.15418 nm), operating at 40 kV and 30 mA. The crystallite size (d) of γ-Al2O3 was determined by XRD peak analysis based on Scherer's equation: d = 0.9λ/B cos θ, where λ is the wavelength of CuKα, B is the full width at half maximum intensity peak (FWHM) in radian and θ is the angle of largest peak. The low-angle XRD measurements of the calcined samples (500 °C) were recorded by Rigaku Smartlab (9 kW) using CuKα radiation, operating at 45 kV and 200 mA. The characteristic vibration bands of the particles were confirmed by FTIR (Nicolet 5PC, Nicolet Analytical Instruments, Madison, WI) with KBr pellet at a resolution of 4 cm−1. Nitrogen adsorption–desorption measurements were conducted at 77 K with a Quantachrome (ASIQ MP) instrument. The powders were outgassed in vacuum at 250 °C for 4 h prior to the measurement. The surface area was obtained using Brunauer–Emmet–Teller (BET) method within the relative pressure (P/P0) range of 0.05–0.20 and the pore size distribution was calculated by Barret–Joyner–Halenda (BJH) method. The nitrogen adsorption volume at the relative pressure (P/P0) of 0.99 was used to determine the pore volume. The morphology of the particles was examined by field emission scanning electron microscopy, FESEM with Zeiss, Supra™ 35VP instrument operating with an accelerating voltage of 10 kV, and transmission electron microscopy, TEM using a Tecnai G2 30ST (FEI) instrument operating at 300 kV.
3 Results and discussion
shows the XRD patterns of alumina synthesized at 150 °C for (A) 6 h, (B) 12 h and (C) 24 h, each calcined at (a) 500 °C, (b) 700 °C, (c) 900 °C, (d) 1000 °C and (e) 1100 °C. It was observed that at shorter reaction time (6 h), the crystallization of alumina was lower specially, at 500–700 °C. However, with increase in calcination temperature at 900 °C, γ-Al2O3 (JCPDS File No. 10-425) phase appeared, and persisted up to 1000 °C. At 1100 °C, partial conversion to θ-Al2O3 (JCPDS File No. 35-121) occurred. Interestingly, for 12–24 h reaction time, the γ-Al2O3 phase was observed at 500 °C and became stable up to 900 °C followed by its transformation to θ-Al2O3 at 1000–1100 °C. The crystallite sizes for 6 h, 12 h and 24 h treated samples after calcination at 900 °C each were found to be 4 nm, 7 nm and 10 nm, respectively. With increasing synthesis time, crystal growth of the particles took place rendering larger crystallite size.
Fig. 1 XRD patterns of alumina synthesized at 150 °C for (A) 6 h, (B) 12 h and (C) 24 h, each calcined at (a) 500 °C, (b) 700 °C, (c) 900 °C, (d) 1000 °C and (e) 1100 °C. (▴): γ-Al2O3; (•): θ-Al2O3.
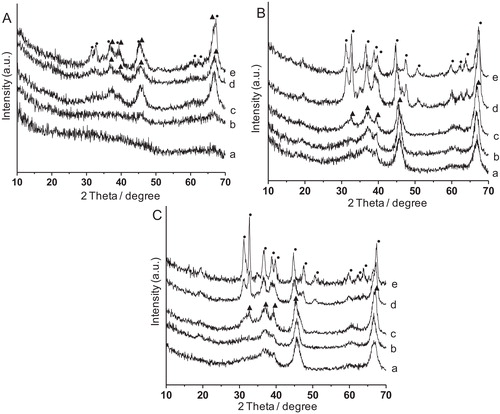
shows the FTIR spectra of the samples synthesized at 150 °C for (A) 6 h, (B) 12 h and (C) 24 h, each calcined at (a) 500 °C, (b) 700 °C, (c) 900 °C, (d) 1000 °C and (e) 1100 °C. For 6 h reaction time up to the calcination temperature of 1000 °C, and for 12–24 h reaction time up to the calcination temperature of 900 °C, the appearance of broad absorption bands in the region at around 560–850 cm−1 resulted which were due to Al–O vibrations of γ-Al2O3. In this case aluminum ions were in both tetrahedral and octahedral sites [Citation9]. The absorption bands at around 565, 760 and 845 cm−1 for the samples prepared with the reaction time of 6 h after heat treatment at 1100 °C, and those of 565, 630, 705, 760, 840 and 925 cm−1 for the samples synthesized with the reaction time of 12–24 h after calcination at 1000–1100 °C were due to Al–O vibration of θ-Al2O3.
Fig. 2 FTIR spectra of the samples synthesized at 150 °C for (A) 6 h, (B) 12 h and (C) 24 h, each calcined at (a) 500 °C, (b) 700 °C, (c) 900 °C, (d) 1000 °C and (e) 1100 °C.
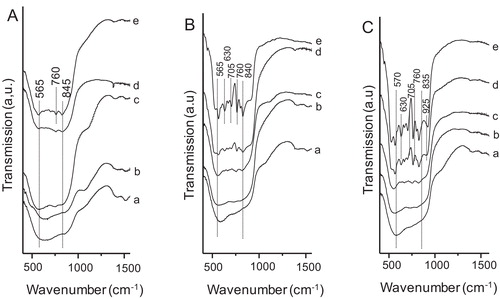
shows the nitrogen adsorption–desorption isotherms and pore size distributions (PSD) (in the insets) of the samples synthesized at 150 °C for (a) 6 h, (b) 12 h and (c) 24 h, each calcined at 500, 700, 900, and 1000 °C. All the isotherms display type IV isotherm according to IUPAC classification, which indicated mesoporous characteristic of the samples. The appearance of type H-2 hysteresis loop in the isotherms indicated ink-bottle-like mesopores [Citation10] and/or pore constrictions. This type of pores is generally formed between agglomerated primary crystallites. It is believed that intercrystallite voids were developed with randomly stacked alumina nanorods in flake-shaped alumina. The pore size distribution (PSD) curves became narrower with increase in reaction time at 12–24 h. shows the textural properties of alumina synthesized at 150 °C for 6 h, 12 h and 24 h, after calcination at 500, 700, 900 and 1000 °C each. It exhibited the BET surface area of 428 m2 g−1, 393 m2 g−1, and 366 m2 g−1 for the 500 °C-treated samples prepared for 6 h, 12 h and 24 h, respectively, while the corresponding pore volumes were 2.86 cm3 g−1, 1.11 cm3 g−1, 0.79 cm3 g−1, respectively. With increase in calcination temperature, the BET surface area and pore volume decreased. Interestingly, the pore size of the samples prepared for 6 h was about 35 nm which decreased to 3.7–3.9 nm with increase in reaction time at 12–24 h which indicated almost unique pore size. At longer reaction time (12–24 h), there occurred the closer of bigger pores. With increase in synthesis time, crystal growth of the particles occurred rendering smaller mesopores in the samples. It minimized the random arrangement of the pores resulting in narrower pore size distribution. It was also evident from the TEM study as discussed shortly. The mesoporosity of alumina was further confirmed by low-angle XRD analysis. shows the low-angle XRD patterns of the samples calcined at 500 °C. It exhibited 2θ peaks at 0.78 (d100 = 11.32 nm) and 0.67 (d100 = 13.17 nm) for 6 h and 12–24 h reaction times, respectively. It indicated the presence of mesopores in the samples [Citation3]. For the sample prepared for 6 h reaction time, a slight shifting of the low-angle peak to higher value accompanying with a lower d-spacing reflected a lesser organization of pores [Citation11]. It was supported by TEM images discussed shortly.
Table 1 Textural properties of alumina synthesized at 150 °C for 6 h, 12 h and 24 h, after calcination at 500, 700, 900 and 1000 °C each.
Fig. 3 Nitrogen adsorption–desorption isotherms and pore size distributions (PSD) (in the insets) of the samples synthesized at 150 °C for (a) 6 h, (b) 12 h and (c) 24 h, each calcined at 500, 700, 900, and 1000 °C.
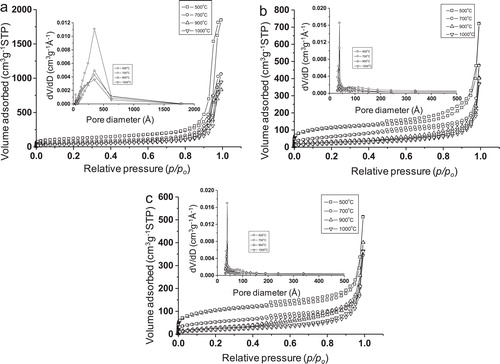
Fig. 4 Low-angle XRD patterns of alumina synthesized at 150 °C for 6 h, 12 h and 24 h, each calcined at 500 °C.
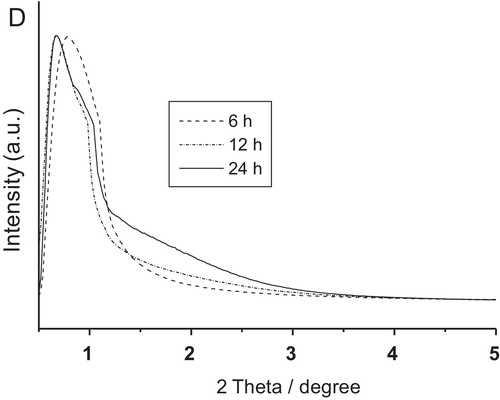
shows the FESEM micrographs of alumina particles synthesized at 150 °C for (a) 6 h, (b) 12 h and (c) 24 h followed by their calcination at 500 °C each. For 1000 °C-treated samples, the corresponding FESEM images are shown in a–c, respectively. It is clear that for 6 h reaction time, alumina nanoparticles of size 50–80 nm were formed, and some agglomerated particles were also noticed for both the calcination temperatures (a and a). With increase in reaction time at 12–24 h, flake-shaped alumina particles were formed (b and c for 500 °C treated samples, and b and c for 1000 °C treated samples). With closer inspection of flake-shaped alumina particles (insets of b and c and b and c), it revealed that each alumina flake comprised of a number of assembled nanoflakes (70–100 nm). It is interesting that the morphology remained unchanged with increase in calcination temperature from 500 to 1000 °C for each sample instead of phase transformation from γ-Al2O3 to θ-Al2O3.
Fig. 5 FESEM images of alumina particles synthesized at 150 °C for (a) 6 h (b) 12 h and (e) 24 h, each calcined at 500 °C.
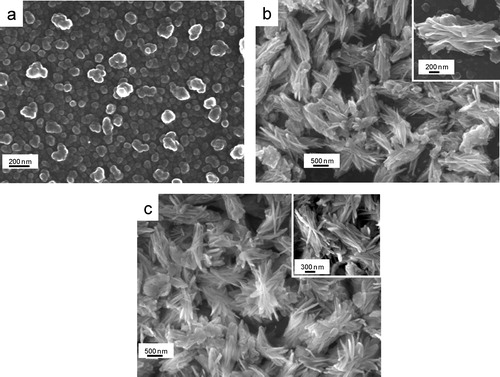
Fig. 6 FESEM images of alumina particles synthesized at 150 °C for (a) 6 h, (b) 12 h and (e) 24 h, each calcined at 1000 °C.
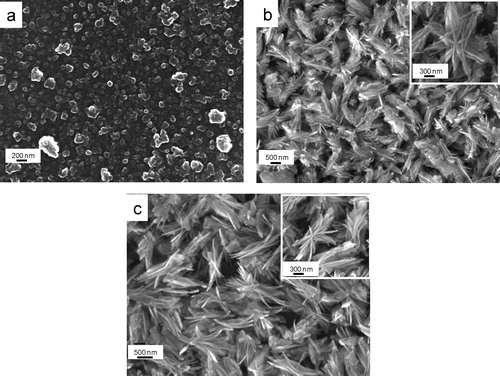
shows the TEM images of the samples prepared for the reaction times of (a) 6 h, (b) 12 h and (c) 24 h followed by their calcination at 500 °C each; the corresponding high magnified images are shown by arrow marks. From low magnified images, the formation of agglomerated nanoparticles and flake-shaped alumina was noticed for the reaction time of 6 h and 12–24 h, respectively. Interestingly, from the high magnified images, it is clear that for 6 h reaction time, the pores are relatively large with random distribution. However, for the reaction time of 12–24 h, more or less uniform distribution of the pores of smaller size was revealed. It was supported by BET and low angle XRD studies. Therefore, an optimum time is required for uniform pore size distribution of alumina.
Fig. 7 TEM images of alumina particles synthesized at 150 °C for (a) 6 h, (b) 12 h and (c) 24 h, each calcined at 500 °C.
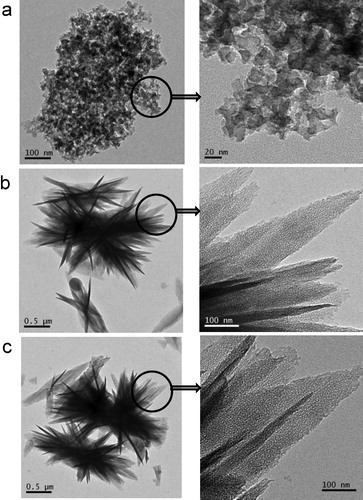
shows schematically a tentative mechanism for the formation of nanostructured mesoporous alumina. Under hydrothermal reaction at 150 °C, tetramethyl urea (TMU) undergoes hydrolysis [Citation12] forming dimethyl ammonium hydroxide ((CH3)2NH2OH) and CO2 according to the following reaction:(1)
(1)
(2)
(2) In the presence of dimethyl ammonium hydroxide, Al3+ ions in solution undergo hydrolysis forming hydrous aluminum oxide. With the progress of reaction time, nuclei of hydrous aluminum oxide are grown into smaller particles which subsequently transform into flake-shaped alumina particles by the Ostwald ripening process, minimizing the interfacial energy. For the generation of mesoporosity, and enhancement of BET surface area and pore volume, dimethyl ammonium (DMA) ions have an interesting role. They interact with hydrous alumina through hydrogen bonding and/or weak forces like van der Waals's interaction, etc. It is worth mentioning that hydrothermal synthesis of flake-shaped alumina particles in the presence of urea was reported [Citation13]. However, urea could not significantly increase the BET surface area of the synthesized alumina. The pore volume and pore size determined from urea-derived alumina were found to be 0.77 cm3 g−1 and 3.1 nm, respectively, which were also less than TMU derived alumina. Interestingly, in the present study, DMA ions having two methyl groups, derived from TMU, act as templating agents in increasing significantly the BET surface area and pore volume of alumina.
4 Conclusions
Nanostructured mesoporous alumina was synthesized under hydrothermal reaction at 150 °C for 6–24 h using tetramethyl urea. The mesoporosity of the samples was confirmed by low angle XRD, BET surface area analysis, and TEM study. The maximum BET surface area and pore volume were obtained for 500 °C-treated samples, which decreased with increasing calcination temperatures. Relatively uniform distribution of the pores of smaller size was noticed for 12–24 h treated samples. Alumina nanoparticles (50–80 nm) formed for 6 h reaction time transformed to flake-shaped alumina assembling with nanoflake-like (70–100 nm) particles with increase in reaction time of 12–24 h. Dimethyl ammonium ions generated from tetramethyl urea behaved as templating agent in increasing significantly the BET surface area and pore volume of alumina.
Acknowledgements
The authors would like to thank the Director of this Institute for his kind permission to publish this paper. The financial support from Department of Science and Technology under DST-SERB project (Grant No.: SR/S3/ME/0035/2012), Government of India (Project No. GAP0616) is thankfully acknowledged. S. Ghosh is thankful to CSIR and R. Dalapati is thankful to DST-SERB for their fellowship.
Notes
Peer review under responsibility of The Ceramic Society of Japan and the Korean Ceramic Society.
References
- V.V.VinogradovA.V.AgafonovA.V.VinogradovT.I.GulyaevaV.A.DrozdovV.A.LikholobovJ. Sol–Gel Sci. Technol.562010333339
- P.YangD.ZhaoD.I.MargoleseB.F.ChmelkaG.D.StuckyNature3961998152155
- S.GhoshM.K.NaskarJ. Am. Ceram. Soc.972014100106
- C.LiuY.LiuQ.MaH.HongChem. Eng. J.1632010133142
- Q.LiuA.WangX.WangT.ZhangChem. Mater.18200651535155
- Y.S.WuJ.MaF.HuM.C.LiJ. Mater. Sci. Technol.282012572576
- S.GhoshK.P.DeyM.K.NaskarJ. Am. Ceram. Soc.9620132831
- S.GhoshM.K.NaskarRSC Adv.3201342074222
- M.D.SacksT.-Y.TsengS.Y.LeeBull. Am. Ceram. Soc.631984301310
- C.SangwichienG.L.AranovichM.D.DonohueColloids Surf. A: Physicochem. Eng. Aspects2062002313320
- J.C.RayK.-S.YouJ.-W.AhnW.-S.AhnMicropor. Mesopor. Mater.1002007183190
- K.R.LindforsD.X.WestR.E.DominicJ. Solution Chem.51976163169
- M.K.NaskarJ. Am. Ceram. Soc.92200923922395