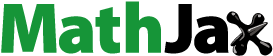
Abstract
Al2O3–TiB2 composites were synthesized using high-energy ball milling from starting powders containing Al, TiO2, and B2O3. To explore the effect of the addition of another ductile metallic phase during milling, 15 wt.% Ni was added to a sample of the starting powders. The phase transformations and microstructure of the milled powder mixtures were investigated using X-ray diffraction and electron microscopy. The results showed that the Ni addition facilitated the mechanochemical reaction between the Al, TiO2, and B2O3. Before the appearance of the Al2O3–TiB2 composite, the intermediate product NiAl was formed by a gradual exothermic reaction. With continued milling, the final phases of Al2O3–TiB2 and Ni were obtained.
Keywords:
1 Introduction
In recent years, a great deal of effort has been devoted to the development of ceramic–matrix composites. In particular, alumina, a ceramic material commonly used in high-temperature structural and wear resistant components, has been subjected to intense scrutiny. Much of this research focuses on incorporating one or more reinforcing phase(s) into an alumina matrix because the applications for monolithic alumina are limited by its low fracture toughness, brittle fracture behavior, and poor sinterability [Citation1]. Various types of relatively soft metallic particles such as Ni, Fe, Al, Cu, Mo, and Nb have been added to alumina to improve its ductility [Citation2–Citation7]; on the other hand, alumina-based ceramic composites can be reinforced with hard secondary phases such as carbides, borides, and nitrides to produce novel ceramic materials with high strength and toughness for use in cutting tools [Citation1,Citation8–Citation11].
Titanium diboride is a potential candidate for a secondary reinforcing phase because of its high melting point, low specific weight, high hardness, high strength to density ratio, good wear resistance, and excellent thermal and chemical stability up to 1973 K [Citation12]. It also has good structural and thermodynamic compatibility with alumina. In a previous study, Sharifi et al. [Citation13] synthesized Al2O3–TiB2 nanocomposites from Al, B2O3 and Ti using a mechanochemical synthesis technique. To lower the cost of the raw materials, Sharifi et al. [Citation14] and Khaghani-Dehahani et al. [Citation15] developed techniques to fabricate Al2O3–TiB2 composites using mechanical alloying (MA) from Al, TiO2, B2O3 and Al, TiO2, H3BO3, respectively. The aluminothermic reduction reaction accelerated the formation of the Al2O3–TiB2 composite, and in the final product the two phases were homogeneously distributed. Taken together, these studies conclusively demonstrated that MA is an effective method to synthesize Al2O3–TiB2 ceramic composites.
MA is a solid-state powder processing technique involving the repeated welding, fracturing, and re-welding of powder particles in a high-energy ball mill. Lü et al. [Citation16] proposed that the raw materials used in MA should include at least one ductile metal to act as a host or binder to hold together the other ingredients. The powders deform plastically under high-energy collision. With new clean surfaces exposed by the mechanical treatment, the powders weld to each other to form new, aggregate particles with different compositions. These welding and fracturing processes are repeated until a fully alloyed powder is formed. Efficient cold-welding of the powders is essential to ensure complete mechanical alloying.
In view of these successful applications of MA to the preparation of Al2O3–TiB2 composites and the determination of the essential conditions required, the authors have ever added the ductile metal Ni to the raw Al, TiO2, and B2O3 powders to prepare the Al2O3–TiB2 composite powders [Citation17]. Based on the study, in this paper, a control group without Ni was milled under the same condition and the results showed that the Ni addition facilitated the mechanochemical reaction between the Al, TiO2, and B2O3. Additionally, the formation mechanism of Al2O3–TiB2 composite and the effect of Ni on the MA process were investigated.
2 Experimental procedure
Al (99% purity), TiO2 (99% purity), B2O3 (99% purity), and Ni (99% purity) powders were used as raw materials. The mixture of Al, TiO2, and B2O3 accounted for 85% of the total powder weight, and was prepared in accordance with the stoichiometry of the reaction:(1)
(1) An addition of 15 wt.% Ni was added to this mixture to make the “Group #1” powders. For comparison purposes, raw powders without any Ni addition were also made (“Group #2”).
Ball milling of the powder mixtures was carried out in a planetary ball mill with a stainless steel vial (150 mL) and balls at room temperature under an Ar atmosphere. Since the highest collision energy can be obtained if balls with different diameters are used [Citation18], two different sizes of balls (∅8 mm and ∅6 mm) were employed in a weight ratio of 1:1. The ball-to-powder weight ratio and the rotational speed of the vial were 10:1 and 500 rpm, respectively. The milling was interrupted after predetermined intervals, and small amounts of powder were removed for characterization.
Phase transformations in the powder mixture were analyzed using X-ray diffractometry (XRD). The morphology and microstructure of the milled powder particles were examined using transmission electron microscopy (TEM). The TEM sample was prepared by suspending the powder sample in ethanol and subjecting it to ultrasonic vibration. A drop of the suspension was then placed on a carbon-coated copper grid and dried.
3 Results and discussion
The Ni-free Al2O3–TiB2 nanocomposites were synthesized according to Reaction Equation(1)(1)
(1) by high-energy ball milling with a self-propagating combustion mode [Citation14]. For the specimen with the 15 wt.% Ni addition, the reaction became more complex. Since the Gibbs free energy of NiO is higher than that of both B2O3 and TiO2 (), neither the Ni/B2O3 nor the Ni/TiO2 reactions occur. This suggests that Ni would only react with Al to form an Al–Ni intermetallic compound before aluminothermic Reaction Equation(1)
(1)
(1) took place during the mechanical milling. In addition, studies on the preparation of Al–Ni alloys by MA of elemental powders had been reported [Citation19Citation[20]–Citation21]. Mashreghi and Moshksar [Citation20] reported that a NiAl intermetallic compound was formed during MA of Al50Ni50 according to the gradual exothermic reaction:
(2)
(2)
Fig. 1 Standard Gibbs free energy of formation as a function of temperature for Al2O3, B2O3, TiO2 and NiO.
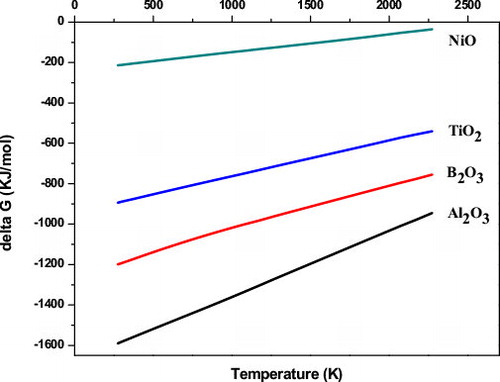
shows the XRD patterns of the samples with the 15 wt.% Ni addition after milling for 0, 4, 8, 12, and 16 h. The diffraction pattern of the un-milled powder shows peaks associated with the raw materials: Al, Ni, TiO2, and B2O3. B2O3 was represented in only one sharp peak at around 2θ = 28° due to the overall lower intensity of B2O3 peaks compared to other components. After 4 h of milling, the peaks corresponding to the raw powders decreased in intensity and broadened; this is caused by the reduction of the crystallite size and the microstrain induced in the powders. Simultaneously, a small amount of the NiAl phase was detected. As the amount of Ni added into the raw mixture was small and only a small fraction of the Ni participated in the gradual exothermic Reaction Equation(2)(2)
(2) , the peak related to NiAl phase was not remarkable. With continued milling to 12 h, the lattice parameter of NiAl decreased from 2.877 to 2.867 Å. shows the variation in the lattice parameter of the NiAl phase during mechanical alloying. It is believed that, due to the high Al content of the raw powders, Al dissolves in the NiAl phase during MA so that the lattice parameter decreases [Citation21].
Table 1 Lattice parameter (a) of NiAl for different milling times.
Fig. 2 XRD patterns of the Ni-containing powders after different milling times. The inset picture shows corresponding local amplification.

Peaks associated with the Al2O3 and TiB2 phases were detected after 16 h of milling. Meanwhile, the peak associated with the raw materials (Al, TiO2, B2O3, Ni) and the intermediate product (NiAl) disappeared almost entirely. This suggested that, in spite of the presence of the dilutant Ni, Reaction Equation(1)(1)
(1) still took place with a combustion mode. Additionally, the intermediate product NiAl reacted with TiO2 and B2O3 to form Al2O3–TiB2 according to
(3)
(3)
Previous studies [Citation22] determined that NiO can be reduced by NiAl to form the Al2O3/Ni in a similar reaction. No traces of Ni were observed in the XRD pattern after 16 h. This may be due to the fact that when the brittle phase Al2O3–TiB2 formed, severe plastic deformation and fragmentation during high-energy milling led to poor crystallinity in the Ni phase. The reduced intensity of the Ni peaks would result in their disappearance from the XRD pattern.
To synthesize Al2O3–TiB2, 20 h of milling time were required for the Ni-free powders (). This is an indication that, when 15 wt.% Ni was added to the starting powder mixture, the preparation of Al2O3–TiB2 by MA was accelerated. The addition of the relatively ductile Ni leads to cold welding of the ductile components (Al and Ni) during MA [Citation18]. The subsequent work hardening and fragmentation of the Al–Ni particles result in a refinement of the grain sizes. Additionally, when the brittle intermetallic phase NiAl was formed, the fragmentation of particles occurred more rapidly. The process of cold welding and fragmentation during MA was thereby expedited.
The crystallite size and lattice strain were obtained from an analysis of the XRD pattern using the Scherrer formula. The variation in the crystallite size and lattice strain of Al as a function of milling time is presented in . Under the same milling conditions, the crystallite size of Al in the Group #1 powders is smaller than that in Group #2 powders, and the lattice strain of the Al in Group #1 is higher than that in Group #2. As would be expected, the microstrain enhances the diffusivity of ingredients. Furthermore, the refined microstructural features decreases the diffusion distance [Citation18], and the heat evolved from the formation of the NiAl phase enhances diffusion. Consequently, the alloying amongst the Al, TiO2, and B2O3 via Reaction Equation(1)(1)
(1) was facilitated by the presence of Ni.
Fig. 4 The variation of crystallite size (a) and lattice strain (b) of Al in the two types of powders at different milling times.
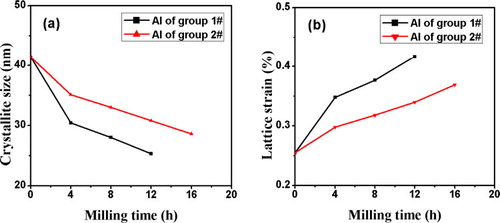
shows TEM images and the associated selected-area diffraction pattern (SADP) of the Group #1 powder milled for 16 h. The Al2O3 (1 1 3), (2 1 4); TiB2 (2 0 1); and Ni (3 1 1) phases were identified from the positions of the rings in the SADP. The only Ni-related ring (3 1 1) observed in the SADP indicated that the short-range order structure still existed in Ni phase in spite of poor crystallinity. These results were consistent with the XRD results.
4 Conclusion
Al2O3–TiB2 composites were synthesized using high-energy ball milling from a starting powder mixture of Al, TiO2, B2O3, and Ni. The addition of 15 wt.% Ni aided the preparation of the Al2O3–TiB2 composite. In the early stages of milling, before the aluminothermic reaction occurred, elemental Al reacted with Ni to form NiAl in a gradual exothermic reaction. The presence of the ductile Ni phase and brittle NiAl phase accelerated the cold-welding and fragmentation processes during milling. As a result, the crystallite size of the Al in the mixtures with Ni was smaller than that in mixtures without Ni for the same milling time. The aluminothermic reaction amongst Al, TiO2, and B2O3 began after milling for 16 h, and the heat from this reaction prompted intermediate product NiAl to react with TiO2 and B2O3 to form the Al2O3–TiB2. The final phases present after mechanical alloying were Al2O3–TiB2 and Ni, as determined by XRD and TEM.
Acknowledgments
The authors acknowledge the financial support provided for this work by the following organizations: National Natural Science Foundation of China (Grant nos. 51375150 and 51205114), Academic Leaders project of the WuHan Science and Technology Bureau (Grant no. 201271130448), and the Hubei Provincial Natural Science Foundation of China (Grant no. 2013CFB018). The authors would also like to express gratitude to the reviewers for their constructive comments on the original manuscript.
Notes
Peer review under responsibility of The Ceramic Society of Japan and the Korean Ceramic Society.
References
- J.LiL.GaoJ.GuoJ. Eur. Ceram. Soc.2320036974
- A.ChakrabortyS.V.KamatR.MitraK.K.RayJ. Mater. Sci.35200038273835
- W.G.FahrenholtzD.T.EllerbyR.E.LoehmanJ. Am. Ceram. Soc.83200012791280
- B.D.FlinnM.RühleA.G.EvansActa Metall.37198930013006
- K.H.MinS.-T.OhY.D.KimI.-H.MoonJ. Alloys Compd.3522003163167
- O.SbaizeroG.PezzottiActa Mater.482000985992
- P.A.TrustyJ.A.YeomansJ. Eur. Ceram. Soc.171997495504
- J.DengL.LiuJ.LiuJ.ZhaoX.YangInt. J. MachTool Manuf.45200513931401
- E.Mohammad SharifiF.KarimzadehM.H.EnayatiJ. Alloys Compd.4822009110113
- E.Mohammad SharifiF.KarimzadehM.H.EnayatiJ. Alloys Compd.4912010411415
- M.ZakeriM.R.RahimipourS.K.SadrnezhadR.Yazdani-radJ. Alloys Compd.4812009320325
- D.VallauriI.C.Atías AdriánA.ChrysanthouJ. Eur. Ceram. Soc.28200816971713
- E.M.SharifiF.KarimzadehM.H.EnayatiAdv. Powder Technol.222011526531
- E.M.SharifiF.KarimzadehM.H.EnayatiAlloys J. Compd.5022010508512
- M.A.Khaghani-DehaghaniR.Ebrahimi-KahrizsangiN.SetoudehB.Nasiri-TabriziInt. J. Refract. Met. Hard Mater.292011244249
- L.LüM.O.LaiS.ZhangJ. Mater. Process. Technol.521995539546
- W.YangS.J.DongA.Z.YangliZ.X.XieAppl. Mech. Mater.401–4032013734737
- C.SuryanarayanaProg. Mater. Sci.4620011184
- M.H.EnayatiZ.SadeghianM.SalehiA.SaidiMater. Sci. Eng. A375–3772004809811
- A.MashreghiM.M.MoshksarJ. Alloys Compd.4822009196198
- A.R.Shirani BidabadiM.H.EnayatiE.DastanpoorR.A.VarinM.BiglariJ. Alloys Compd.581201391100
- V.UdhayabanuK.R.RaviV.VinodB.S.MurtyIntermetallics182010353358