Abstract
The use of industrial waste (by-products) as raw materials in the ceramic industry has been under study for decades due to the economical, energy, tax and environmental advantages. The specificity of the waste requires a basic characterization and technology thereof.
The applicability of rice husk ash (RHA), as silica (SiO2) source, in refractory and porous materials withpotential structural, insulating and/or filtering applications was carried out by characterizing the ceramicbehavior of stoichiometric mixtures of calcined alumina (Al2O3) and RHA. A reaction-sintering frameworkcan be defined in the (Al2O3–SiO2) system. The sinterability and conversion during the reaction sinteringprocesses were studied in order to obtain mullite (3Al2O3·2SiO2) ceramics. Also some microstructural fea-tures of the developed materials were studied in the 1100–1600ºC range. The mullitization was studiedquantitatively.
Partial densification was achieved (30%) and highly converted materials were obtained. The developedmicrostructure consisted in a dense ceramic matrix with homogenous interconnected porosity, with anarrow pore size distribution below 20 μm. The developed material gives enough information for design-ing mullite ceramics materials with either porous or dense microstructures with structural, insulating orfiltering applications employing RHA as silica source and calcined alumina as the only other raw material.
1 Introduction
Attributable to the economical, energy, tax and environmental advantages the use of industrial waste (by-products) as raw materials in the ceramic industry has been under study for decades. The specificity of the waste requires a basic characterization [Citation1–Citation7].
The rice processing companies use the husk as fuel for drying, parboiling the cereal and heating for of storage silos. These are generally small businesses and these companies neither have processes for the use nor proper disposal of ash generated by burning. They either deposit these ashes in vacant lots or simply dump those into rivers and streams, causing pollution and aggression to the health of the population, by contaminating the air and eventually causing silicosis [Citation8–Citation13]. On the other hand, recycling of rice husk ash is an excellent alternative to minimize the environmental impact caused by the improper disposal of this material and reducing disposal costs in controlled landfills. The ashes have shown to be great raw material silica, creating a fine material and high reactivity. Accordingly, the silica obtained from rice bran has been used with great success as an alternative raw material for the production of various ceramic materials. Mainly in cement industry [Citation14–Citation16], as inorganic filler of polymer composite [Citation17] and for processing silicon carbide ceramics [Citation18], showing its high technological potential. The combustion of rice husk results in the production of rice husk ash (RHA), around 20% of ash is produced. This RHA presents a significant amount of silicon oxide (SiO2) (≥90%) and is different from the ash resulting from the combustion of rice straw. In particular, as observed in the results that rice hull ash has a high SiO2 content even higher than reported from other species of rice. Particularly the predominant polymorph observed in this RHA is cristobalite. This might be related to the relatively high temperature of the particular combustion chamber.
Mullite (3Al2O3·2SiO2), the only stable crystalline phase in the Al2O3–SiO2 system presents a great importance in both traditional and advanced ceramics. This is mainly due to its properties such as high thermal stability and favorable properties as conductivity and low thermal expansion, high resistance to creep and corrosion stability, along with good mechanical strength and fracture toughness [Citation19–Citation25]. Mullite is the crystalline phase resulting from the thermal treatment of clay minerals [Citation19].
Mullite and mullite ceramics display a large variety of appearances, reaching from Czochralski-grown single crystals to polycrystalline and polyphase ceramics, and from very large refractory products to very tiny engineering components with high purity and homogeneity [Citation20].
Porous mullite ceramic meet insulating material functions at high temperatures, also as materials for membrane filters of gases and liquids at elevated temperatures, as catalyst supports insulating or as insulating material. Porous mullite materials can be elaborated by different routes and different alumina and silica sources [Citation26–Citation35]. Moreover other by-products have been proposed as starting powders for mullite based materials [Citation36–Citation41].
The adequacy of this material (RHA) for this reutilization strategy was evidenced in a recent work [Citation36] that presents the possibility of processing mullite and mullite-based ceramics and ceramic composites from Al metal wastes and waste by-products of mining tin ores with high kaolinite content. Another recent work [Citation42] obtained porous mullite ceramic employing RHA as silica source. In that case, another alumina source (aluminum acetate) was proposed. This source resulted more expensive and difficult for large scale ceramic production. The resulting ceramics presented higher porosities with filtering applications [Citation42].
In another recent work, mullite based materials with a filter application were proposed: obtaining a porous ceramic material processed from a kaolinitic clay and Rice husk (hull) (not directly the ash like in this work). The calorific power of the husk is a noticeable advantage besides the particular pore distribution that was correlated with the husk properties [Citation43]. The cost effectiveness was assessed [Citation44].
Finally a waste alumina source (with some calcination pretreatment) was employed in a similar work that proposed the elaboration of a mullite based ceramic with alumina and RHA starting powders [Citation45]. In that work the RHA employed was also chemically pre-treated (HCl) to increase the SiO2 content. They obtained dense materials at 1700 °C thermal cycles. The conversion was studied qualitatively. No acid pre-treatment is assessed in this study.
The principal objective of this article is to study the applicability of this by-product in refractory and porous ceramic materials with potential structural, insulating and/or filtering applications by characterizing the ceramic behavior of stoichiometric mixtures of calcined alumina and RHA without any chemical pretreatment. Particularly to establish sinterability and conversion during the reaction sintering processes in order to obtain mullite ceramic (3Al2O3·2SiO2). Previously a characterization of the non-conventional silica source was carried out. Finally we intend to describe some microstructural features of the developed materials.
2 Experimental procedure
2.1 Starting materials
The employed alumina source is a typical fine grained calcined alumina usually used for the refractory manufacture ((α-Al2O3), A-2G, Alcoa Inc., USA). The rice husk ash employed (RHA) is produced in grill type biomass boiler only fed by rice husk. This produces 10 tons/day of ash. After firing this alternative fuel produces approximately 20% of ashes [Citation8,Citation13]. The XRD pattern is shown in , the results of the Rietveld–LeBail quantification as well [Citation46–Citation49].
The main properties are shown in . It can be seen that the important amount of cristobalite is remarkable, probably a consequence of the high firing temperature. The expected amount of amorphous phase was also detected and pondered. The particle size distribution can be observed in , is coarse and makes necessary the proposed milling pre-treatment: in this case we propose a simple ball milling.
Table 1 Chemical composition of the as received rice husk ash.
Table 2 Particle size distribution of the studied RHA.
2.2 Processing
Ceramic materials were processed in lab scale employing the RHA as SiO2 source. Stoichiometric (3Al2O3:2SiO2) mixtures were wet ball milled (1000 cm3 for 24 h) in order to make those adequate the particle size and at the same time to achieve an adequate mixture. The resulting powder was then dry pressed with a pressure of 200 MPa. Two grams (2.0 g) disc shaped samples were conformed to 15.0 mm diameter. These samples were fired in electric kiln, with a 60 min dwelling time, and 5 °C/min heating rate at the following final temperatures (1100, 1200, 1300, 1400, 1500 and 1600 °C). The resulting materials were labeled M11, M12, M13, M14, M15 and M16 respectively.
2.3 Characterization
Previously, in order to understand the thermal behavior of the mixture, the differential thermal analysis (DTA) together with the thermogravimetric analysis (TG) was carried out simultaneously for the unfired mixture with the same heating rate (Rigaku Evo II, Japan). Alumina crucibles and standard were employed with 200 mg load in air atmosphere. Particle size distribution was performed by laser scattering (Malver-Mastersiezer 2000) with a dispersion unit (HYDRO 2000G) at 8000 rpm stirring and ultrasound. In order to study the sinterability, the shrinkage and textural properties were evaluated to the M11–M16 materials (Archimedes immersion method).
Developed crystalline phases were analyzed by XRD (Philips 3020 equipment with Cu Kα radiation in Ni filter at 40 kV to 20 mA, with 2θ between 3° and 70°, 2 s steps of 0.04°). The XRD patterns were analyzed with the program FullProf (version 4.90, July 2010) which is a multipurpose profile-fitting program, including Rietveld refinement to perform phase quantification. Formerly the phases were identified using phase analysis software (X’Pert HighScore, version 2.1.2). Microstructure of polished samples was observed with a scanning electron microscope (JCM-6000 NeoScope Benchtop SEM), the complementary energy-dispersive X-ray spectroscopy (EDS) was carried out, and both global and punctual identification quantifications were performed.
3 Results and discussion
3.1 Rice husk ash (RHA) characterizations
shows a digital image of the as received ash, the grid size is 5 mm. This is similar to the one reported in literature [Citation8–Citation13]. A dark gray color is observed. The presence of some longitudinal angled coarse particles can be observed at this enlargement. shows SEM images of the same RHA, the dimension bar is 50 μm. The presence of micron size particle is observed together with some other larger particles. The angles are also observed in these images.
The brittle behavior of the RHA can be interpreted from the images; this fact is concordant with the amount of glassy amorphous phase detected by XRD. Moreover during the manipulation of the RHA some breakage is observed, evidencing the easiness (and adequacy) of the posterior milling treatment.
The particular textures can also be observed. This texture is a consequence of the husk morphology. The RHA presents complex structures: canal, pores and striations can be observed. These are typical forms from the plant ash source.
3.2 Grains size distribution of the ball milled RHA–alumina mixtures
shows the grain size distribution (and the cumulative) of the milled alumina–RHA mixtures. These showed a relatively fine mean diameter (D50: 5 μm); this is higher than the alumina size (2.5 μm). But smaller than the coarse grain size distribution presented by the as received RHA, shown in .
3.3 Thermal behavior of the RHA–alumina mixtures (TG–DTA)
The simultaneous differential thermal analysis (DTA) and thermogravimetric analysis (TG) were carried out. These allow to identify the different thermal processes during the firing cycle. shows the TG and the DTG (the graphical derivative of the TG), the residual carbon (and other organic material) combustion occurs between 400 and 500 °C. The mass loss evaluated (≈3% wt.) is concordant with the performed chemical analysis (). No other important processes were observed.
3.4 Sinterability
The sintering parameters (density, porosity and shrinkage) of the materials are shown as a function of the maximum thermal treatment temperature in . The evaluated density is slightly over 3.15 g/cm3, this below the alumina (3.95–4.05 g/cm3) and over the silica specific gravity (between 2.2 g/cm3 and 2.4 g/cm3 depending on the crystalline structure). The achieved values are near the theoretical mullite density (3.17 g/cm3). Because of this, no important change would be observed by this property, as a consequence of the possible existence of close porosity (not evaluated by the immersion method) and the different crystallinity of the silica reagents studied that might evolve during the thermal processing.
The achieved porosity is ≈30% in M14, M15 and M16 materials. This fact was expectable, based in the high refractoriness, the coarse grain size and low moderate compaction grade usually achieved by the uniaxial pressing (55–65%). This in many applications is an advantage [Citation26]. The not-so rounded morphology of the RHA might also be explained by these facts.
The shrinkage behavior is particularly strange. While gradual shrinkage is observed between 1100 and 1300 °C, an abrupt decrease of the sample diameters was observed after the 1400 °C treatment (M14) achieving an 8% shrinkage. At temperatures over 1300 °C the viscosity of the viscous silica phase is low enough for a viscous flux resulting in a sinterization. As mentioned, the density of the reagents and products is different. Finally M15 and M16 present a relative expansion in comparison with M14, but observed contractions are 6% and 5% respectively. This is an evidence of the mullite formation, with lower density than the reagents. The crystalline phase evolution was followed by XRD and is shown in the next section.
3.5 Crystalline phases evolution as a function of the sintering temperature
The XRD allowed qualitatively weighting conversion, and the Rietveld refinement permitted to assess the conversion quantitatively. shows the diffraction patterns of the M13, M14, M15 and M16 materials. The detected peaks corresponded with alumina (corundum) and mullite accompanied by the crystalline phases present in the ash () only for M13 material. These were also present in the materials processed at lower temperatures. Mullite is not detected in M13, neither was it in M11 and M12 as well. It may be noted that the formation of mullite occurs is almost complete, after 1500 and 1600 °C treatments and incipient treatments after 1400 °C. This is consistent with the literature for other silica sources [Citation41] and the shrinkage behavior is shown in . The presence of unreacted alumina was detected in M15 and M16. Silica glass might form the binder phase together with ash impurities (see ) that would explain the lack of silica peak detection. Finally we can say that at 1400 °C, with the employed dwell (60 min), the reaction is incipient and incomplete. However in some industrial processing route the dwelling times are ten times the one employed in this article a conversion could be completed. The mullitization can be optimized, taking into account the kinetics of mullite formations. This can be carried out by performing longer thermal cycles which can ensure the complete formation, especially introducing longer dwelling times. Other strategies might include the introduction of fluxing additives like clay, alkaline or earth alkaline oxides or by performing a milling pretreatment [Citation41].
Finally the Rietveld structural refinement allowed to evaluate quantitatively the evolution of the phases, results are shown in . Finally no quartz was detected, evidencing the Silica thermal path from cristobalite to mentioned binding glassy phase, into mullite. No Quartz diffraction peaks were detected in these materials. The cell parameters obtained for the mullite corresponded to the 3:2 stoichiometry [Citation24]. The Rwp parameter resulting values were in all cases below 30 sustaining the goodness of the refinements, specially taking into account the low crystalline characteristic of the RHA and its fired products [Citation8,Citation13].
3.6 Developed mullite based ceramic microstructure, SEM analysis
SEM images with 200 and 1000 enlargements of M15 and M16 materials are shown in . shows detailed microstructure of the M15 material, from which an EDX analysis was performed. The results of the quantifications are shown in . The global quantification gave the expected contents of Al2O3 and SiO2 equivalent to the proposed stoichiometric relation. Punctual analyses were also carried out. For example, the results of two particular points were also transcript to , while the evaluated contents correspond to stoichiometric composition in point A, the silica excess is evident in the B point.
Table 3 Aluminum and silicon oxide percentile weight proportions of the M15 material.
Fig. 10 SEM image of the M15 material. Points A and B correspond with the punctual EDX analysis reported in .
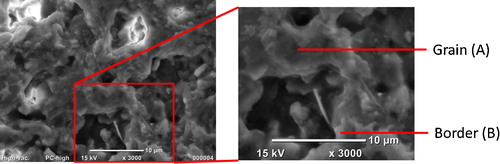
The developed microstructure can be observed in the SEM images; no important difference can be found. A homogenously distributed porous matrix can be witnessed in both materials. These interconnected pore diameters are of several microns. The ceramic matrix in which the porous items are imbibed presents a dense microstructure. No typical acicular mullite could be generally observed. Only in some places it could be devised. The developed microstructure corroborates the possible application of these ceramic materials in structural, insulating and filtering applications. More processing fine optimization would be necessary for the particular application, but the present results encourage the usage of this sustainable starting material.
Larger pore size distribution can be designed from these materials by the incorporation of a pore forming combustion agent. This strategy has been explored for similar mullite materials [Citation19] and is usually employed by insulating Al2O3–SiO2 materials manufacturers. All these support the hypothesis of employing this silica for mullite based materials source with the listed advantages.
On the other hand lower porosity size or even dense mullite based materials could be designed from these materials by improving the milling pretreatment and/or with sintering aid incorporation like clay or feldspar. Both strategies present advantages and disadvantages described in the literature [Citation19].
4 Conclusions
An industrially obtained rice husk ash (RHA) was characterized; the ash source is stable and big enough to sustain the hypothesis of employing the by-product as a silica source for materials processing. The characterization comprised the chemical and physical characteristics, SEM images were also obtained. These showed the particular morphology of the ash, the expected amorphous silica structure and high cristoballite content. Milled stoichiometric alumina–RHA mixtures were chosen to study the ceramic behavior of the RHA. The thermal behavior showed that the residual carbon content (3% wt.) was burned at around 400 °C. Subsequently both mullitization and sinterization occurred during heating treatments; these were studied and correlated with the processing variable (temperature). Mullitization started after 1400 °C and was complete after 1600 °C treatments. Only a partial sinterization was achieved (≈30%). This was explained in terms of the characteristics of the mixture. The developed microstructure consisted in a dense ceramic matrix with a homogenous interconnected porosity with a narrow pore size distribution below 20 μm.
The developed material gives enough information for further designing mullite materials with either porous or dense microstructures with structural, insulating and filtering applications employing RHA as silica source and calcined alumina as the only other raw material.
Notes
Peer review under responsibility of The Ceramic Society of Japan and the Korean Ceramic Society.
References
- C.M.F.VieiraS.N.MonteiroRev. Mater.1432009881905
- M.SutcuS.AkkurtCeram. Int.357200926252631
- N.QuarantaM.UnsenH.LópezC.GiansiracusaJ.A.RoetherA.R.BoccacciniCeram. Int.3712011377385
- R.R.MenezesH.S.FerreiraG.A.NevesH.d.L.LiraH.C.FerreiraJ. Eur. Ceram. Soc.257200511491158
- F.Raupp-PereiraD.HotzaA.M.SegadãesJ.A.LabrinchaCeram. Int.3222006173179
- P.KumarA.SrivastavaV.KumarM.MajhiV.SinghJ. Asian Ceram. Soc.222014169175
- M.SultanaA.AhmedM.ZamanM.RahmanP.BiswasP.NandyJ. Asian Ceram. Soc.3120152226
- N.SoltaniA.BahramiM.I.Pech-CanulL.A.GonzálezChem. Eng. J.2642015899935
- Y.NakataM.SuzukiT.OkutaniM.KikuchiT.AkiyamaJ. Ceram. Soc. Jpn.9781989842849
- N.YalcinV.SevincCeram. Int.2722001219224
- N.H.BateniM.N.HamidonK.A.MatoriJ. Ceram. Soc. Jpn.1222014161165
- K.G.MansarayA.E.GhalyEnergy Sources19919979891004
- V.P.DellaI.KühnD.HotzaMater. Lett.5742002818821
- L.SunK.GongInd. Eng. Chem. Res.4025200158615877
- K.GanesanK.RajagopalK.ThangavelConstr. Build. Mater.228200816751683
- G.Rodríguez de SensaleCem. Concr. Compos.2822006158160
- Z.A.M.IshakA.A.BakarEur. Polym. J.3131995259269
- S.K.SinghB.C.MohantyS.BasuBull. Mater. Sci.2562002561563
- H.SchneiderS.KomarneniMullite1st ed.2006John Wiley & Sons
- H.SchneiderJ.SchreuerB.HildmannJ. Eur. Ceram. Soc.2822008329344
- J.AnggonoJurnal Teknik Mesin712005110
- C.SadikI.E.El AmraniA.AlbizaneJ. Asian Ceram. Soc.2220148396
- C.SadikI.E.El AmraniA.AlbizaneJ. Asian Ceram. Soc.242014310316
- K.OkadaN.OtsukaS.SomiyaAm. Ceram. Soc. Bull.7010199116331640
- L.S.CividanesT.M.CamposL.A.RodriguesD.D.BrunelliG.P.ThimJ. Sol-Gel Sci. Technol.5512010111125
- J.H.SheT.OhjiMater. Chem. Phys.8032003610614
- R.BareaM.I.OsendiJ.M.F.FerreiraP.MiranzoActa Mater.5311200533133318
- R.BareaM.I.OsendiP.MiranzoJ.M.F.FerreiraJ. Am. Ceram. Soc.8832005777779
- B.A.LatellaL.HenkelE.G.MehrtensJ. Mater. Sci.4122006423430
- A.EsharghawiC.PenotF.NardouCeram. Int.3612010231239
- H.AbeH.SekiA.FukunagaH.TsuzukiM.EgashiraJ. Ceram. Soc. Jpn.9841990339347
- A.YaoB.YuK.YangR.WangRare Met. Mater. Eng.3412005257258
- J.YinJ.LiuA.GuoD.SongW.WangKey Eng. Mater.4342010682683
- B.-R.ChoD.-H.HeoKey Eng. Mater.317–3182006105110
- A.Ruíz-CondeJ.Pascual CospE.Garzón GarzónL.MoralesM.Raigón PichardoP.J.Sánchez-SotoProc. 1st Spanish National Conference on Advances in Materials Recycling and Eco-EnergyMadrid, Spain, November 12–132009 pp. S04–15
- Y.-Z.RuanY.YuR.-P.WuChin. J. Struct. Chem.2582006965970
- Z.-Y.LiangG.-Y.YanL.P.ZhengX.-H.ZhengY.-Z.RuanAdv. Mater. Res.233201110671072
- R.WuY.YuY.RuanJ. Chin. Ceram. Soc.358200710921096
- Y.DongX.FengX.FengY.DingX.LiuG.MengJ. Alloys Compd.4601–22008599606
- S.C.VieiraA.S.RamosM.T.VieiraCeram. Int.33120075966
- R.R.MenezesE.Fagury-NetoM.C.FernandesP.M.SoutoR.H.G.A.KiminamiCeramica543302008245252
- R.P.A.SouzaF.V.MottaR.G.CarvalhoW.AccharE.HarimaR.MaribondoC.A.PaskocimasMater. Sci. Forum8022014232238
- P.G.ZhangJ.D.LiangK.Y.WangS.M.GuoProc. Materials Science and Technology Conference and Exhibition 2011, MS and T’11,Columbus, OH, USA, October 16–2020118794
- K.SaiintawongS.WadaA.JaroenworaluckCeram. Eng. Sci. Proc.2532004141146
- H.M.RietveldJ. Appl. Crystallogr.219696571
- R.A.YoungCryst. Res. Technol.3041993138
- D.L.BishJ.E.PostAm. Mineral.789–101993932940
- M.S.ConconiM.R.GaunaM.F.SerraG.SuarezE.F.AgliettiN.M.RendtorffCeramica603562014524531
- Y.NurishiJ.A.PaskCeram. Int.8219825759