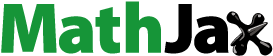
Abstract
Two 5 vol% Ni/Al2O3 composites with the difference in Al2O3 grain size were fabricated by pulsed electric current sintering technique to investigate the influence of Al2O3 grain size on oxidation behavior of the composites. Average Al2O3 grain sizes of two fabricated composites were 1.1 μm and 0.5 μm after sintering. Oxidation tests were conducted at temperatures ranging from 1100 to 1350 °C for 1–48 h in air. A thin NiAl2O4 layer was observed in exposed surface of samples after oxidation. An oxidized zone that consisted of Al2O3 matrix and NiAl2O4 grains was defined. Growth of the oxidized zone obeyed the parabolic law. Influences of Al2O3 grain size on high-temperature oxidation of the composites were discussed.
1 Introduction
Alumina (Al2O3) has been well-known as a high-performance structural material and widely applied in industries because of its advantages such as excellent heat resistance, high mechanical strength and wear resistance. However, similar to other ceramics, Al2O3 materials have inherently strong covalent and ionic bonds that prohibit substantial dislocation motion or plastic deformation. They fail to alleviate stress concentrations that occur in front of crack tips. Hence, Al2O3 materials are easily fractured as a consequence of crack propagation resulting from a slight surface flaw or internal flaw. Al2O3 materials thus exhibit poor toughness that restricts their application. In order to increase their toughness, dispersion of non-oxide phases such as Ni, NiAl, Co and SiC in Al2O3 matrix were proposed [Citation1–Citation4]. On the other hand, the presence of the non-oxide phases gives the materials the self-healing function that occurs at high temperatures in the air [Citation2,Citation5–Citation7].
Ando and his co-workers reported self-healing function that can be achieved on ceramic-based composites such as SiC/mullite, SiC/Al2O3 [Citation7–Citation11]. When non-oxide dispersoids in the matrix were oxidized at high temperatures, the oxidation product filled up the cracks and involved the reduction of stress concentrations at crack tips. As a result, the mechanical strength was recovered up to the level of as-polished samples. Furthermore, this mechanism improves their performance with longer lifetime and more reliability at high temperatures.
Similarly, nano-Ni dispersed Al2O3 composites also have the self-healing function at high temperatures in the air [Citation12–Citation14]. Maruoka et al. reported the recovery of mechanical strength for nano-Ni/Al2O3 that was able to achieve when the fraction of surface crack disappearance is over 50% [Citation14]. The study indicated that the crack disappearance effectiveness depended on the formation of NiAl2O4-oxidation product that mostly referred to the diffusion of Ni2+ along grain boundaries of the Al2O3 matrix. The conclusion implies that finer grain size of the matrix could give a positive effect on the crack-healing function.
While self-healing effectiveness mostly depends on the diffusion of Ni2+ and Al3+ cations, the oxidation resistance of materials depends on diffusion of O2− ions along grain boundaries. At high temperatures, oxygen can penetrate the oxide matrix that causes the oxidation of dispersed Ni particles within the matrix. The region consisting of oxidized nickel particles develops as increasing oxidation temperature and duration. Nanko et al. reported the oxidation behavior of Ni/Al2O3 composites at temperatures ranging from 1200 to 1300 °C [Citation15], in which the growth of oxidized region was attributed to obedience of the parabolic law. It implied that the mass transport in the oxidized region was the rate-controlling process, which was the diffusions of cations and oxide ions along grain boundaries of the Al2O3 matrix. Maruoka et al. reported the influence of Si-doping of nano-Ni dispersed Al2O3 composites on high-temperature oxidation [Citation16]. The study concluded that the growth rate of the oxidized zone was decreased effectively at 1200 °C by doping 0.1 mol% Si in Ni/Al2O3. Doping of Si was attributed to the change to grain boundary diffusion in polycrystalline Al2O3. The grain boundary diffusion in polycrystalline Al2O3 could be also decreased by either dopant of Y, SrO, LuO1.5 or ZrO2 [Citation17,Citation18]. Since the grain boundary diffusion is an important factor responsible for the oxidation resistance of the composite, influences of Al2O3 grain size on oxidation resistance of Ni/Al2O3 are in need of investigation for high-temperature applications.
In this study, the influences of the different structure of Al2O3 matrix on oxidation resistance of 5 vol% Ni/Al2O3 composites are discussed. The oxidation resistance of the composites was evaluated through the growth rate of oxidized zone after heat treatment in air at temperatures ranging from 1100 to 1350 °C for 1–48 h.
2 Experimental procedures
In order to fabricate two types of 5 vol% Ni dispersed Al2O3 composites with the difference in Al2O3 grain structure, two different types of Al2O3 powder (Sumitomo Chemical Co. Ltd, AA-04, d = 0.44 μm and Taimei Chemicals Co. Ltd, TM-DAR, d = 0.14 μm) were used as starting materials. Aqueous slurries containing Ni(NO3)2·6H2O (Kojundo Chemical Laboratory Co. Ltd, purity 99.9%) and the Al2O3 powders were prepared by milling in a plastic bottle with Al2O3 balls for 24 h. The composite that was prepared from Al2O3 with average particle size of 0.44 μm is referred to as Ni/Al2O3-044, hereafter. Similarly, Ni/Al2O3-014 is referred to as the composite that was prepared from the Al2O3 with average particle size of 0.14 μm. After drying at 400 °C in a boiling flask, the powder mixtures were milled by using an alumina mortar for 15 min. These powder mixtures were heat-treated at 600 °C for 12 h in a stream of the Ar–1% H2 gas mixture to reduce NiO to Ni metallic phase. The powder mixtures were consolidated in a graphite die by pulsed electric current sintering (PECS) at 1400 °C for Ni/Al2O3-044 and 1200 °C for Ni/Al2O3-014 under 50 MPa uniaxial pressure in a vacuum for 5 min holding time. The relative density of all the consolidated samples used in this study attained at least 99% of the theoretical density. shows the fractured surfaces of the as-sintered samples. Ni particles, that could be visible as the bright contrast dots, were homogeneously dispersed in the Al2O3 matrix. The average particle size of these Ni particles was approximately 300 nm while the average Al2O3 grain size of Ni/Al2O3-044 was 1.1 μm, and that of Ni/Al2O3-014 was 0.5 μm.
Fig. 1 SEM images of fractured surface of as-sintered samples: (a) Ni/Al2O3-044 and (b) Ni/Al2O3-014.
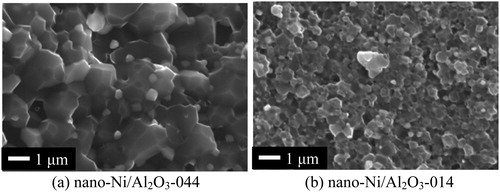
High-temperature oxidation tests were conducted at temperatures ranging from 1100 to 1350 °C for 1 h up to 48 h in the air with a heating rate of 400 °C/h. The tested samples were put on alumina balls (3 mm in diameter) in an alumina crucible and exposed in the air at the investigated conditions. Phase identification of the samples was carried out by X-ray diffraction (XRD). Oxidation evolution of heat-treated samples was evaluated via the growth rate of oxidized zone observed on cross-sectioned surface by scanning electron microscope (SEM).
3 Results
shows XRD patterns obtained from sample surface before and after oxidation tests. Before oxidation, only two dominant phases of Ni and Al2O3 are detected on the sample surface (a). After oxidation at 1200 °C for 1 h, NiAl2O4 phase was identified as shown in b. On the other hand, the intensity of signals from Ni phase was decreased. The peak intensity of NiAl2O4 phase which was formed after oxidation at 1200 °C for 24 h was significantly increased and replaced for the existence of Ni-metallic phase. In addition, nickel oxide phase could not be identified on oxidized samples. This phenomenon has been reported by Trumble et al. [Citation19] that NiO did not coexist with Al2O3. It implies that Ni particles reacted with Al2O3 matrix as the following equilibrium:(1)
(1)
Fig. 2 XRD patterns of nano-Ni/Al2O3: (a) before oxidation, (b) oxidized at 1200 °C for 1 h and (c) oxidized at 1200 °C for 24 h in air.
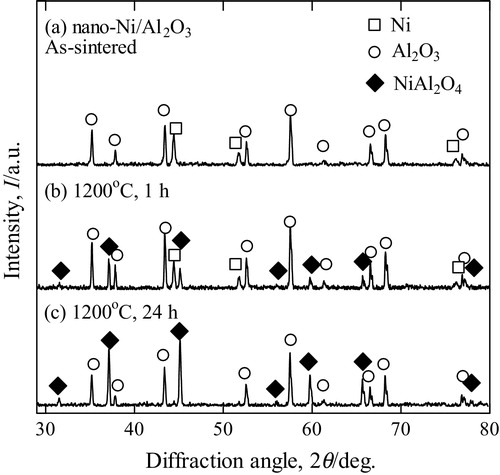
shows the SEM images of cross-section surface of Ni/Al2O3-014 and Ni/Al2O3-044 after oxidation at 1200 °C for 24 h. In the region from the surface to the depth of 35 μm, the grains that are larger than Ni particles were oxidation product-NiAl2O4 formed by oxidation test (a). Nano-Ni particles could be visible as bright dots in the region deeper 35 μm from the surface. For the reasons above, the region composed of the NiAl2O4 grains and Al2O3 was defined as the oxidized zone. b shows the thickness of oxidized zone in Ni/Al2O3-044 which is smaller than that of Ni/Al2O3-014. A thin surface layer that has the same color of NiAl2O4 was observed on both samples as shown in . From XRD results, the thin surface layer formed on the sample surface was determined as the NiAl2O4 layer. The NiAl2O4 layer formed on Ni/Al2O3-014 after oxidation at this condition was approximately 1.5 μm which was similar to that of Ni/Al2O3-044.
Fig. 3 SEM images of cross-section surface of (a) Ni/Al2O3-014 and (b) Ni/Al2O3-044 sample after oxidation at 1200 °C for 24 h in air. A thin surface layer composed of NiAl2O4 was observed on both samples.

shows the thickness of oxidized zone in Ni/Al2O3-014 and Ni/Al2O3-044 as a function of oxidation time at various temperatures. With increasing oxidation temperature, the thickness of the oxidized zone increased. The growth of oxidized zone obeyed the parabolic law:(2)
(2) where x is the thickness of oxidized zone, kp the parabolic rate constant, and t is oxidation time. The growth rate of oxidized zone in Ni/Al2O3-014 was slightly higher than that of Ni/Al2O3-044 after oxidation at 1200 °C. Nevertheless, this manner was reversed when the samples were heat-treated at 1300 °C. The growth rate of oxidized zone in Ni/Al2O3-014 was slightly lower than that of Ni/Al2O3-004 at higher temperatures.
shows the parabolic rate constant, kp, in Ni/Al2O3-014 and Ni/Al2O3-044 as a function of reciprocal oxidation temperature. The slope of the straight line representative for Ni/Al2O3-014 was similar to that of Ni/Al2O3-044. The values of apparent activation energy for the growth rate of oxidized zone in Ni/Al2O3-014 and Ni/Al2O3-044 were 400 kJ mol−1 and 414 kJ mol−1, respectively.
4 Discussion
The thickness of NiAl2O4 layer, which was formed on the sample surface after oxidation by outward diffusion of cations is much thinner than oxidized zone as mentioned in . For example, the thickness of oxidized zone formed by oxidation was 30–35 μm, while the thickness of NiAl2O4 surface layer was approximately 1.5 μm. From the kinetic point of view, diffusion of ions and cations in the oxidized zone play the major roles in oxidation behavior of the composites. The growth of NiAl2O4 layer in Ni/Al2O3-014 and Ni/Al2O3-044 was similar to each other under the investigated conditions. This fact indicates that grain size of Al2O3 does not influence significantly on the outward diffusion of cations under the investigated conditions.
shows that the growth rate of oxidized zone in Ni/Al2O3-014 was higher than that of Ni/Al2O3-044 after oxidation at 1200 °C. This fact matches with the assumption that finer Al2O3 grain size accelerates the inward diffusion of oxygen ions. However, the thickness of oxidized zone in Ni/Al2O3-014 was lower than that of Ni/Al2O3-044 after oxidation at 1300 °C as mentioned in . shows SEM images observed on the fractured surface of Ni/Al2O3-044 sample after oxidation at 1300 °C for 12 h. The average Al2O3 grain size in the oxidized zone was 1.5 μm (b) while it was 1.3 μm in the non-oxidized zone (c). The existence of pores in the oxidized zone was attributed to outward diffusion of cations. Similarly, shows the differences in the microstructure of Ni/Al2O3-014 after oxidation at 1300 °C for 12 h. The average Al2O3 grain size in the oxidized zone was 1.3 μm (b) while it was 0.75 μm in the non-oxidized zone (c). Taking account of Al2O3 microstructure after sintering, the average Al2O3 grain sizes in Ni/Al2O3-044 and Ni/Al2O3-014 were 1.1 μm and 0.5 μm, respectively. Ni/Al2O3-014 was sintered at 1200 °C which was lower than that of the investigated conditions. Oxidation at temperatures higher than sintering temperature caused grain growth of the composites. On the other hand, Ni particles dispersed in Al2O3 matrix act as grain growth inhibitors. Outward diffusion of cations in oxidized zone during oxidation induced the reduction of Ni concentration. Consequently, grain growth occurred during oxidation tests especially in the oxidized zone. The similarities in microstructures of Al2O3 matrix in oxidized zone causes the similarities of oxidation behavior. In summary, nanostructure on Ni/Al2O3 is effective for mechanical behavior. However, there was no significant influence in high-temperature oxidation and its related phenomena because of grain growth in their oxidation zone.
5 Conclusions
Influences of Al2O3 grain size on oxidation behavior at temperatures ranging from 1100 to 1350 °C for 1–48 h were investigated in this study. A thin NiAl2O4 layer was observed in exposed surface of samples after oxidation. An oxidized zone that consisted of Al2O3 matrix and NiAl2O4-oxidation product was defined. The growth of oxidized zone obeyed the parabolic law. Finer Al2O3 grain size caused higher growth rate of oxidized zone at heat-treated temperatures lower than 1200 °C. At higher heat-treated temperatures such as 1300 °C, Al2O3 grain size has less influence on oxidation behavior of the composites due to the grain growth at oxidized zone.
Acknowledgements
The authors wish to express their gratitude to the Japan Science and Technology Agency (H26-354-15) for supporting this study through the Advanced Low Carbon Technology Research and Development Program. The authors also wish to acknowledge the discussion and advice of Assoc. Prof. Shigenari Hayashi, Tokyo Institute of Technology.
Notes
Peer review under responsibility of The Ceramic Society of Japan and the Korean Ceramic Society.
References
- T.SekinoT.NakajimaT.UedaK.NiiharaJ. Am. Ceram. Soc.80199711391148
- O.AbeY.OhwaY.KuranobuJ. Eur. Ceram. Soc.262005689695
- W.P.TaiT.WatanabeJ. Mater. Sci.33199857955801
- A.SawaguchiK.TodaK.NiiharaJ. Ceram. Soc. Jpn. Int. Ed.991991510513
- D.MaruokaT.ItayaT.MisakiM.NankoMater. Trans.53201218161821
- A.L.Salas-VillasenorJ.Lemus-RuizM.NankoD.MaruokaAdv. Mater. Res.6820093443
- S.K.LeeK.TakahashiM.YokouchiH.SuenagaK.AndoJ. Am. Ceram. Soc.87200412591264
- M.C.ChuS.SatoY.KobayashiK.AndoFatigue Fract. Eng. Mater. Struct.18199510191029
- K.AndoM.C.ChuK.TsujiT.HirasawaY.KobayashiS.SatoJ. Eur. Ceram. Soc.22200213131319
- K.AndoB.S.KimM.C.ChuS.SaitoK.TakahashiFatigue Fract. Eng. Mater. Struct.272004533541
- T.OsadaW.NakaoK.TakahashiK.AndoS.SaitoJ. Eur. Ceram. Soc.27200732613267
- D.MaruokaY.SatoM.NankoAdv. Mater. Res.892010365370
- D.MaruokaM.NankoMater. Sci. Forum6962011378383
- D.MaruokaM.NankoCeram. Int.39201332213229
- M.NankoM.MizunoM.WatanabeK.MatsumaruK.IshizakiAdv. Tech. Mater. Mater. Proc. J.62004240243
- D.MaruokaM.NankoMater. Trans.51201015701573
- T.NakagawaI.SakaguchiN.ShibataK.MatsunagaT.MizoguchiT.YamamotoH.HanedaY.IkuharaActa Mater.55200766276633
- H.YoshidaS.HashimotoT.YamamotoActa Mater.532005433440
- K.P.TrumbleM.RuhleActa Metall. Mater.39199119151924