Abstract
This work concentrates on the preparation of AA6061/(0, 2, 4, 6, 8 wt.%) rice husk ash (RHA) aluminum matrix composites (AMCs) using compocasting and investigation of the dry sliding wear behavior by means of pin-on-disc apparatus at room temperature. The microstructures of the composites were studied using scanning electron microscopy and electron back scattered diffraction. The micrographs confirmed successful incorporation of RHA particles into the aluminum matrix. A proper distribution of RHA particles without segregation was achieved. RHA particles refined the grains of the aluminum matrix and improved the wear resistance of the composite. The influence of RHA particulate content and applied load on the worn surface and wear debris was further reported. RHA particles improved the wear resistance of the composites and reduced the damage on the worn surface. The wear mode changed with increase in the content of RHA particles and the applied load.
1 Introduction
Owing to lightweight and moderate strength, aluminum alloys are extensively used in numerous industries [Citation1,Citation2]. In spite of several advantages, the tribological properties of aluminum alloys remain poor. They cannot be used as material for components which make sliding motion [Citation3 Citation2013;Citation5]. The wear rate becomes excessive during the course of service leading to premature failure of components. Therefore, hard ceramic particles are commonly reinforced with aluminum alloys to improve the wear resistance. Such materials are called as aluminum matrix composites (AMCs). AMCs are increasingly used in the place of aluminum alloys due to several excellent properties which are not exclusively limited to improved wear resistance [Citation6 Citation2013;Citation8].
The production cost of AMCs is high comparing with conventional monolithic alloys owing to multiple factors. The cost of AMCs can be brought down if industrial waste and natural minerals are utilized as reinforcement particles [Citation9,Citation10]. Rice hush ask (RHA) is considered as one of the economic as well as promising reinforcement particle for AMCs. RHA is an agricultural waste which is available in surplus quantities across the globe. The constituents of a typical milled paddy are rice, bran and husk. Rice mills make use of this husk as fuel to produce steam for the parboiling process. The volatile matter in the husk evaporates during the process of burning and the residual husk is transformed into ash which is named as RHA [Citation11 Citation2013;Citation13].
There are number of methods used to produce AMCs. Among them, stir casting is very popular due to its applicability for mass production and low production cost [Citation14,Citation15]. A mechanical stirrer is used to create a vortex in the molten aluminum and reinforcement particles are added at the periphery. Though this method appears simple in principle, reinforcement rejection is commonly reported due to deprived wettability between ceramic particles and liquid aluminum. Wettability can be improved if stirring is carried out within the freezing range of the aluminum alloy by keeping it in semi-solid state. This technique, called as compocasting enhances the wettability and admission of particles into the aluminum alloy [Citation16,Citation17].
The wear behavior of AMCs reinforced with ceramic particles was studied widely in literature. However, reports on the wear behavior of AMCs reinforced with industrial waste and natural minerals are limited [Citation18 Citation2013;Citation27]. Sudarshan and Surappa [Citation18] explored the wear mechanisms in A356/fly ash AMCs developed using stir casting. Kaur and Pandey [Citation19] synthesized Al–Si/Zircon sand AMCs using spray forming and analyzed the role of applied load on wear behavior. Aigbodion and Hassan [Citation20] correlated the wear parameters and wear rate of Al–Cu–Mg/bagasse ash AMCs developed using double stir casting method. Kumar et al. [Citation21] reported the effect of temperature on sliding wear behavior of AA6061/fly ash AMCs consolidated using powder metallurgy. Prasad and Krishna [Citation22] studied the influence of applied load on dry sliding wear behavior of A356.2/RHA AMCs fabricated using stir casting. Rao et al. [Citation23] created AA2024/fly ash AMCs using stir casting. They examined the effect of sliding distance on wear rate. Kumar et al. [Citation24] assessed the effect of particle size on wear behavior of LM13/Zircon sand AMCs developed using stir casting. Senthilkumar et al. [Citation25] produced Al–Si–Mg/RHA AMC using stir casting and investigated the effect of applied load, sliding speed and volume fraction of RHA on the dry sliding wear. Selvam et al. [Citation26] provided an insight into the wear mechanisms of AA6061/fly ash AMCs synthesized using compocasting. Dinaharan et al. [Citation27] analyzed the role of fly ash particle on wear behavior of AA6061/fly ash AMCs formed using friction stir processing.
The objective of the present investigation is to report the dry sliding wear behavior of AA6061/RHA AMCs prepared using compocasting process. A detailed microstructural and wear characterization were carried out.
2 Experimental procedure
Aluminum alloy AA6061 reinforced RHA particulate composite was fabricated by compocasting at 630 °C. The chemical composition of AA6061 is provided in . The SEM micrograph of the RHA particles and the composition are respectively given in and . Most of the RHA particles exhibit solid spherical shape. The average size was estimated to be 2–3 μm. Castings were obtained with various content (0, 2, 4, 6 and 8 wt.%) of RHA. A detailed fabrication procedure was reported elsewhere [Citation28]. Specimens were prepared from the castings to carry out microstructural characterization. All the specimens were polished using standard metallographic technique and etched with Keller’s reagent. The etched specimens were observed using a scanning electron microscope (JEOL-JSM-6390) and electron back scattered diagram (EBSD).
Table 1 Chemical composition of AA6061 aluminum alloy.
Table 2 Chemical composition of rice husk ash.
Specimens of size 10 mm × 10 mm × 30 mm were obtained from the castings having various content of RHA. The wear rate was measured using a pin-on-disc wear apparatus (DUCOM TR20-LE) at room temperature according to ASTM G99-05 standard. The polished surface of the pin was slid on a hardened chromium steel disc. The tests were carried out at various applied loads (10, 20, 30, 40 and 50 N) at a sliding velocity of 2 m/s and sliding distance of 2000 m. A computer-aided data acquisition system was used to monitor the loss of height. The volumetric loss was computed by multiplying the cross section of the test pin with its loss of height. Worn surfaces and wear debris of selected specimens were observed using scanning electron microscope.
3 Results and discussion
3.1 Microstructure of AA6061/RHA AMCs
The representative SEM micrographs of the produced AA6061/RHA AMCs are presented in . The distribution of RHA particles indicates that the preparation of the composite using compocasting was successful. a is the microstructure of the cast aluminum matrix. The micrograph displays a characteristic dendritic structure caused by fast solidification. This structure is characterized with highly elongated arms. The spaces between the arms are observed to be filled with coarsened Mg2Si phase. Because, the concentration of the major alloying elements Mg and Si is above the solubility limit. The micrographs are continuous without any presence of macro level defects such as porosity, voids and cracks. The semisolid slurry absorbs less air compared to fully melted aluminum in case of stir casting. Hence, the chances for macro level voids are remote. The dendritic structure is totally absent in the micrographs of the composites (b–e). The reinforcement of RHA particles lead to refinement of microstructure. The presence of RHA particles altered the solidification pattern and formed a well-defined grain structure. RHA particles are spread across the micrographs. There is no segregation of particles along the grain boundaries. Hence, the distribution can be counted as fairly homogenous. Few clusters of particles are also observed. A homogenous distribution is essential to improve the properties and increase the service life of AMC components. There are number of factors which influence the distribution of reinforcement particle. The final distribution is the result of initial distribution in the slurry; change in distribution during pouring and solidification [Citation29]. In case of stir casting, the particle movement is high due to the presence of fully molten aluminum alloy. The density difference causes considerable displacement of particles after incorporation. Since, the viscosity of semi-solid slurry is very high compared to aluminum melt; the movement of reinforcement particles is retarded. The tendency to float or sink due to density difference is restricted. Further, the change in the distribution of particles during pouring and solidification in compocasting is insignificant due to shorter period of time. Hence, a desirable distribution is obtained. It is well known that the wettability of molten aluminum and RHA particles is poor [Citation30]. The successful incorporation of the RHA particle suggests that the semi-solid slurry alleviated the issues with wettability. It is interesting to observe the nature of distribution in the SEM micrographs. Many grain boundaries are clearly visible in the figure. Most of the RHA particles are spotted inside the grain boundaries. This kind of distribution is known as intragranular distribution. The properties and performance of AMCs will enhance with intragranular distribution. The velocity and movement of the solidification front influences the nature of distribution. Since casting was carried out in semi-solid state, the solidification front does not have enough momentum to push the particles towards the grain boundaries. Simultaneously, nucleation and grain grown takes place which tend to retain the particles within the grain boundaries.
Fig. 2 SEM micrographs of AA6061/RHA AMCs containing RHA; (a) 0 wt.%, (b) 2 wt.%, (c) 4 wt.%, (d) 6 wt.% and (e) 8 wt.%.
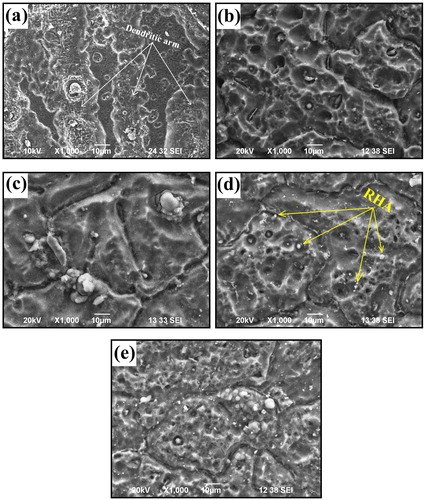
EBSD images of AA6061/RHA AMCs are presented in . EBSD images confirm a clear formation of grain boundaries in the composites. It can be ascertained from that RHA particles played a role in refining the grains. It is observed that the average grain size reduced with an increase in RHA particles. The average grain size was measured to be 102 μm at 0 wt.% and 30 μm at 8 wt.%. The reduction in grain size suggests that RHA particles acted as grain nucleating agents. The grain refinement originates from the following factors. RHA particles oppose the growth of aluminum grains. The location of RHA particles becomes nucleating sites for grains and the aluminum grains tend to grow on them. RHA particles at room temperature were added to the slurry. The temperature of the slurry around the RHA particles drops resulting in an undercooling effect. This creates more number of nucleation sites wherever RHA particles are present in the slurry. The resistance for aluminum grain growth increases with increased nucleation sites. The net result is refinement of grains in the composites. The grain refinement increases with increased content of RHA particles.
3.2 Sliding wear behavior of AA6061/RHA AMCs
3.2.1 Effect of RHA content
The effect of RHA particulate content on the wear rate of the AA6061/RHA AMCs is depicted in . It is observed from the graphs that the wear rate reduces as a function of RHA particulate content at any given load. The incorporation of RHA particles is beneficial to the enhancement of wear resistance. The microstructural changes that take place due to the presence of RHA particles leads to strengthening of the composite. The increase in hardness was reported in our earlier study [Citation28]. The improved hardness offer resistance to the cutting action of the counterface asperities. The thermal mismatch between the aluminum matrix and the RHA particles creates dislocations during solidification. Those strain fields strengthen the subsurface. The homogenous distribution of RHA particles lead to Orowan strengthening. Most of the RHA particles display spherical shape which avoids stress concentration and retards the premature detachment of particles from the aluminum matrix during sliding. Further, RHA particles endure the applied load and reduce the actual contact area of the wear specimen on the counter disc. The above discussed factors lead to a reduction in wear rate and improvement in wear resistance of the composite.
represents the SEM micrographs of the worn surface of composite specimens as a function of RHA particulate content for a constant load of 30 N. The worn surface of aluminum matrix displays severe plastic deformation. This situation occurs due to plastic flow of sliding surface induced by frictional heat evolving between the pin surface and counter face. The wear mode is identified as adhesive wear. The increase in RHA particulate content reduces the plastic deformation on the worn surface. The presence of RHA particles restricts the plastic deformation. A distinct parallel groove pattern is visible at higher volume fraction under the experimental condition. The subsurface damage reduces at higher volume fraction. The wear mode changes from adhesive to abrasive mode.
Fig. 5 SEM micrographs of worn surface of AA6061/RHA AMCs containing RHA; (a) 0 wt.%, (b) 2 wt.%, (c) 4 wt.%, (d) 6 wt.% and (e) 8 wt.% at applied load 30 N.

shows the SEM micrographs of the wear debris of composite specimens as a function of RHA particulate content for a constant load of 30 N. The morphology of the wear debris changes with increase in RHA volume fraction. The wear debris of the aluminum matrix shows large flaky shape. The large wear debris is the result of adhesive wear where material is removed in huge chunks at high rate. The size of the wear debris of the composite specimens is less compared to aluminum matrix debris. Many equiaxed particles are generated in the composite. They are the result of abrasive wear mode. Those equiaxed particles transform two body abrasive wear into three body abrasive wear. The nature of contact changes from sliding to rolling. Hence, the size of wear debris is less at higher volume fraction and wear rate of the composite decreases.
3.2.2 Effect of applied load
The effect of applied load on the wear rate of the AA6061/RHA AMCs is depicted in . The wear rate increases with increased applied load for a constant volume fraction of RHA particles. This is in agreement with well-known Archard’s wear expression [Citation31]. Archard’s law states that the wear of the sliding metallic materials is proportional to the applied pressure. The increase in applied load increases the pressure on the sliding specimen. Both the pin surface and counterface have large number of asperities which differ in shape and height. There is no perfect smooth sliding surface. The counterface disc is harder than the composite pin. Hence, the harder asperities of the counterface begin to cut the surface of the pin and penetrate into the subsurface. The applied load determines the degree of penetration of counterface asperities into the pin surface. The penetration increases with increase in applied load which causes increased material removal. The wear rate subsequently increases. Further, the applied load dictates the intimacy of contact. The increase in applied load leads to more intimate contact between the pin and the counterface. This situation causes more accumulation of frictional heat and results in softening of the pin surface. The penetration of counterface asperities becomes easier and consequently more material is removed.
represents the SEM micrographs of the worn surface of AA6061/6 wt.% RHA AMC specimens as a function of applied load. The worn surface appears relatively smooth at a lower load of 10 N. There are no deeper grooves or plastic deformation. The subsurface remains intact. The increase in applied load increased the plastic deformation on the worn surface and the formation of pits. The subsurface is exposed at a higher load of 50 N. This confirms that the penetration of counterface asperities was more at higher load. The overall wear mode appears to be abrasive. The parallel groove pattern can be seen in all the worn surfaces. Nevertheless, the effect of applied load is well pronounced in the form of plastic deformation at the edge of grooves and existence of pits.
Fig. 8 SEM micrographs of worn surface of AA6061/6 wt.% RHA AMC at applied load; (a) 10 N, (b) 20 N, (c) 30 N, (d) 40 N and (e) 50 N.
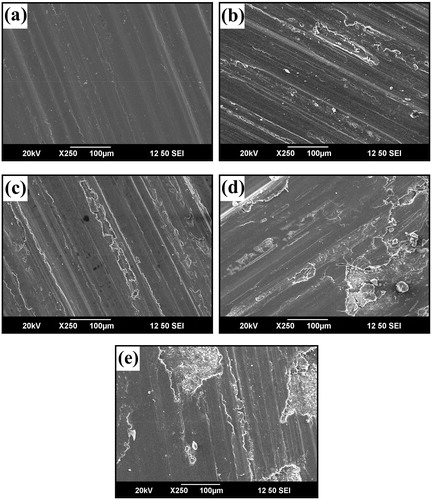
shows the SEM micrographs of the wear debris of AA6061/4 wt.% RHA AMC specimens as a function of applied load. A change in the size and morphology of the wear debris with increase in applied load is clearly visible. More equiaxed and less flaky shaped wear debris are generated at a lower load of 10 N. Fine size of debris indicates that the wear rate was less at lower load. The number of flaky shaped debris increase at higher loads. Large size debris are visible at a higher load of 50 N. This observation suggests that material was removed at higher rate which reduced wear resistance at higher load.
4 Conclusions
AA6061/X vol.% RHA AMCs (X = 0, 2,4, 6 and 8) were prepared using compocasting. The effect of RHA particles and its volume fraction on the microstructural features and dry sliding wear behavior were studied. The results can be summarized as follows:
• | RHA particles were dispersed uniformly in the aluminum matrix irrespective of the volume fraction. There was no aggregation or segregation of RHA particles. The fine dispersion was ascribed to the preparation method used in this work. Most of the particles were present inside the grain boundaries. |
• | RHA particles acted as grain nucleation sites and refined the grains of the aluminum matrix. RHA particles resisted the growth of aluminum grains. |
• | RHA particles improved the wear resistance of the composites. They reduced the plastic deformation of the worn surface and size of wear debris generated. The improvement in wear resistance was attributed to increased hardness, generation of strain fields, homogenous distribution, spherical shape of RHA particles and reduction in effective contact area. The wear mode transferred from adhesive to abrasive with increase in the content of RHA particles. |
• | The applied load increased the wear rate of the composite. The increased penetration of counterface asperities and softening of pin surface cause higher material removal. The increase in load increased the plastic deformation and pit formation. The size of wear debris became larger with applied load. |
Acknowledgements
The authors are grateful to the Centre for Research in Metallurgy (CRM) at Karunya University and OIM and Texture Lab at Indian Institute of Technology Bombay for providing the facilities. The authors are also thankful to Mr. A. Raja, Mr. I. Deva Manoharan and Mr. C. John Kennedy for their assistance offered to execute the above work.
References
- T.DursunC.SoutisMater. Des.562014862871
- J.HirschTrans. Nonferrous Met. Soc. China24201419952002
- S.SureshN.S.V.MoorthiS.C.VettivelN.SelvakumarMater. Des.592014383396
- R.HashemiG.HussainWear324–32520154554
- M.WalczakD.PieniakM.ZwierzchowskiArch. Civ. Mech. Eng.152015116123
- Y.DouY.LiuY.LiuZ.XiongQ.XiaMater. Des.602014669677
- X.JiangM.GalanoF.AudebertMater. Charact.882014111118
- A.A.TofighM.O.ShabaniCeram. Int.39201374837490
- A.BahramiN.SoltaniM.I.Pech-CanulC.A.GutierrezCrit. Rev. Environ. Sci. Technol.462016143207
- S.ZahiA.R.DaudMater. Des.32201113371346
- N.SoltaniA.BahramiM.I.Pech-CanulL.A.GonzálezChem. Eng. J.2642015899935
- R.PodeRenew. Sustain. Energy Rev.53201614681485
- E.P.AyswaryaK.F.Vidya FrancisV.S.RenjuE.Thomas ThachilMater. Des.41201217
- B.S.YigezuP.K.JhaM.M.MahapatraMater. Manuf. Processes282013969979
- J.Jebeen MosesI.DinaharanS.Joseph SekharTrans. Nonferrous Met. Soc. China26201614981511
- K.M.Sree ManuK.SreerajT.P.D.RajanR.M.ShereemaB.C.PaiB.ArunMater. Des.882015294301
- A.A.TofighM.R.RahimipourM.O.ShabaniP.DavamiJ. Compos. Mater.49201516531663
- SudarshanM.K.SurappaWear2652008349360
- K.KaurO.P.PandeyTribol. Lett.382010377387
- V.S.AigbodionS.B.HassanMater. Des.31201021772180
- P.R.S.KumarS.KumaranT.S.RaoS.NatarajanMater. Sci. Eng. A527201015011509
- D. SivaPrasadA. RamaKrishnaJ. Mater. Sci. Technol.282012367372
- J.B.RaoD.V.RaoK.S.PrasadN.R.M.R.BhargavaMater. Sci.302012204211
- S.KumarV.SharmaR.S.PanwarO.P.PandeyTribol. Lett.472012231251
- M.SenthilkumarS.D.SaravananS.ShankarJ. Compos. Mater.49201522412250
- J.D.R.SelvamD.S.R.SmartI.DinaharanKovove Mater.542016175183
- I.DinaharanR.NelsonS.J.VijayE.T.AkinlabiMater. Charact.1182016149158
- J.A.K.GladstonN.M.SheriffI.DinaharanJ.D.R.SelvamTrans. Nonferrous Met. Soc. China252015683691
- J.HashimL.LooneyM.S.J.HashmiJ. Mater. Process. Technol.92–93199917
- S.D.SaravananM.SenthilkumarS.ShankarTribol. Trans.56201311561167
- J.F.ArchardJ. Appl. Phys.241953981988