ABSTRACT
Composites of aligned (K,Na,Li)NbO3 (KNLN) piezoceramic particles in a PDMS polymer matrix are presented as promising materials for flexible sensors and energy harvesters. Their ease of processing is matched with a relatively high damage tolerance and piezoelectric performance at low dielectric loss. To maximize piezoelectric performance, the effective poling conditions for dielectrophoretically structured KNLN-PDMS composites are studied, and compared with random composites. Effective poling is identified at 7.5 kV/mm, for 6 min at 150°C in structured composites. The structured composites demonstrate improved piezoelectric performance, with respect to random composites, while retaining the low stiffness of the PDMS polymer matrix.
Introduction
Composites of piezoceramic particles in a polymer matrix are promising materials for flexible energy harvesting and sensing applications due to their ease of processing matched with favorable mechanical properties and low dielectric loss [Citation1,2]. Existing piezoelectric materials, based on lead zirconium titanate (PZT) ceramics, raise ecological concerns and demonstrate poor mechanical properties with typically high stiffness (∼60 GPa) and low strain at break, limiting their application within curved devices [Citation1]. PVDF polymer based piezoelectrics demonstrate favorable piezoelectric performance at stiffnesses of ∼1 GPa, yet continue to exhibit high dielectric losses above 5% [Citation2]. In piezoceramic-polymer composites the electrical and mechanical performance can be tailored by adjusting the composition, internal structure and volume fraction of the two phases [Citation3]. Composites with perfect particle connectivity, or a “1–3” structure, have been shown to attain significantly increased performance, yet require complex processing, in the form of ceramic fiber spinning and sintering, to produce and sacrifice mechanical performance. Random piezoceramic-polymer composites, or “0–3” composites, the simplest type of composite to process and mold into predesigned shapes, tend to demonstrate significantly reduced piezoelectric performance due to the greater distance between particles, or inter-particle distance. Structuring the ceramic particles within the polymer matrix by application of dielectrophoresis (DEP) has been shown to significantly decrease the inter-particle distance in composites, improving the piezoelectric and dielectric performance with respect to random composites, preserving their relative ease of processing [Citation4]. A further concern influencing the piezoelectric performance of these composites is the degree of poling of the ceramic phase. Piezoelectric particulate-polymer composites require high poling fields (on the order of 10 - 15 kV/mm at temperatures above the polymer Tg) to achieve sufficient poling. The poling electric field acting on each particle is influenced both by the ratio of the conductivity and the ratio of the dielectric constant of the two phases [Citation5]. The effective electric field the ceramic phase experiences tends to be only a fraction of the applied electric field, due to the low dielectric constant of the polymer matrix. Though, in composites based on lead free piezoceramics this limitation can be relatively overcome due to the reduced dielectric constant of lead free ceramics compared to lead based ceramics. At poling times longer than the relaxation time of the composite, the distribution of the electric field will be dominated by the ratio of the conductivities of the two phases instead of the dielectric constants [Citation6]. To attain an effectively poled piezoceramic-polymer composite, it has been demonstrated that the poling time should be longer than the relaxation time of the composite [Citation6]. Yet, fine-tuning of the exact poling conditions of a particular piezoceramic-polymer composite should still be investigated empirically. Recent work has demonstrated that composites based on (K,Na)NbO3 fillers doped with Li (KNLN) have increased piezoelectric performance when compared to similar lead containing composites [Citation7]. In this work, the effective poling conditions to come to optimal performance in a flexible, lead free KNLN – polydimethylsiloxane (PDMS) piezoelectric structured composite [Citation8] are investigated and compared with random composites.
Experimental procedure
Composite preparation
First, the K0.485Na0.485Li0.03NbO3 particulate powder was prepared by combining stoichiometric proportions of the >99% pure oxides NaCO3, K2CO3, Li2CO3, and Nb2O5 (obtained from Sigma Aldrich). Before calcination, the oxides were milled in a glass jar with 5 mm yttria-stabilized ZrO2 balls in cyclohexane. A two-step calcination scheme was employed to obtain cubical particles by first calcining at 1050°C for 3 hours, milling for 5 hours, and then calcining again at 950°C for 20 hours [Citation7]. Rather than employing a third milling step to break apart remaining agglomerates, the powders were sieved through a 63 μm size mesh and ultrasonicated for 1 hour, to mitigate agglomeration while retaining the cuboid particle shape. Composite disks were prepared by mixing the KNLN particulate powder in the optically clear two-component polydimethylsiloxane (PDMS) polymer, Sylgard 184 (Dow Corning Corp., Midland MI, USA), with a particle volume of 10. The PDMS, cured at 100°C in 30 min with a working time of 90 min, has a dielectric constant, ϵ33 [−], of 3.9 at room temperature, and a glass transition temperature of −120°C, as measured by dynamic mechanical analysis, at 1 Hz. The KNLN particulate powder, first dried overnight at 150°C, was mixed for 5 min at 2500 rpm with the silicone elastomer in a planetary mixer (Speed mixer DAC 150 FVZ, Hauschild, Germany). After addition of the silicone curing agent, the composite slurry was mixed again for 5 min at 2500 rpm. Next, the mixture was degassed in a vacuum chamber for 15 min, mixed again for 5 min at 2500 rpm, to ensure homogeneity of the slurry, and poured into a prepared Teflon mold. The Teflon mold consists of 1 mm thick, 14 mm diameter circular cutouts, with Al electrodes applied on either side. After pouring the composite slurry in the mold, the mold is clamped between two steel plates. To achieve structured composites, a dielectrophoretic structuring electric field of 1 kV/mm was applied at an optimal frequency of 200 Hz with a resulting phase angle of 85°. The electric field was applied at room temperature for 90 min, after which the mold was heated to 100°C for 1 hour, to allow the composites to cure while in the presence of the structuring electric field. To prepare random composites, the same procedure was followed, without application of the electric field. Gold electrodes were applied on both sides of the disk shaped samples with a sputter coater (Quorum Q300T, East Sussex, UK). Effective poling conditions for the cured KNLN-PDMS composites are studied by poling and repoling the same structured and random samples, over and over again for each poling parameter (electric field, poling time and temperature) under investigation. All composites were poled in a silicone oil bath at temperatures varying from 25 to 150°C, for times varying from 2 to 30 min, and electric fields varying from 5 to 20 kV/mm. The composite samples were cooled to room temperature in the presence of the electric field, and aged for at least 24 hours before piezoelectric and dielectric measurements took place.
Measurement techniques
X-ray diffraction (XRD) (Rigaku MiniFlex600 X-ray diffractometer using Cu-Kα, AddspeX, Abcoude, the Netherlands) was used to confirm the crystal structure of the KNLN particulate powder, via the PDXL2 software. The spatial distribution of the KNLN particles within the random and structured composites was recorded with a field-emission scanning electron microscope (SEM) (JEOL (Europe) BV, JSM-7500F, Nieuw Vennep, the Netherlands). The piezoelectric charge constant, d33 [pC/N], was measured with a Berlincourt type piezometer (PM300, Piezotest, London, UK). The capacitance, C [pF], and dielectric loss, tan δ, were measured at 1 kHz and 1 V with an Agilent 4263B LCR (Santa Clara, CA, USA). The ϵ33 was derived from the capacitance. A tensile tester (Instron 3365, Darmstadt, Germany) was used to measure the Young's modulus, E33 [GPa], of structured composites by uniaxial tensile testing of five samples.
Results and discussion
The X-ray diffraction pattern of the KNLN particulate powder () confirms the development of a single phase perovskite structure, with sharp crystalline peaks. The achievement of DEP structuring in the 10 vol.% filled KNLN-PDMS composites is established through scanning electron micrographs of the cross-sections, in . The effects of DEP structuring can be clearly seen, as the KNLN particles in the structured composite have assembled themselves into chains, spanning the thickness of the composite. The moderately agglomerated powder is observed to be homogeneously distributed.
Figure 2. Scanning electron micrographs of the cross-section of an (a) random and (b) structured 10 vol.% KNLN-PDMS composite at 200× magnification.
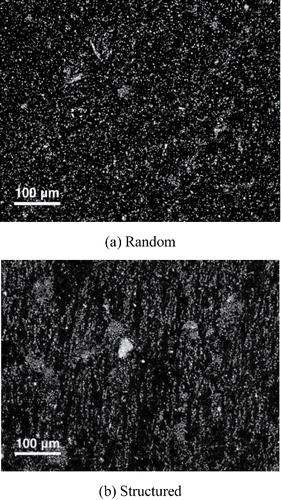
The effect of the poling electric field strength on the piezoelectric charge constant of KNLN-PDMS composites is presented in . The samples were poled at a fixed temperature and time of 150°C and 30 min. The piezoelectric charge constant of the composites increases with electric field, until 10 kV/mm after which performance degrades. We observed that the dielectric constant of all composites degrades as a consquence of the poling trial from 9.9 to 7.2 in structured, and 6.7 to 5.9 in random. The decrease in performance, more pronounced in structured composites, suggests degradation of the polymer matrix. Since the inter-particle distance in structured composites is shorter, the polymer matrix between these particles experiences a relatively high local electric field. Re-poling composites at lower fields did not recover optimal performance. The optimal poling condition for random composites lags behind that of structured composites, reaching a maximum in piezoelectric charge constant at 10 kV/mm for random, and 7.5 kV/mm for structured. The effects of poling temperature are shown in , at a fixed time of 30 min and an electric field of 7.5 kV/mm. The piezoelectric charge constant of both types of composite increases with temperature up to 150°C, after which the polymer matrix degrades. Results of the poling time versus piezoelectric charge constant are shown in . The piezoelectric charge constant of all composites increases with poling time. In structured composites, poling saturation is reached after 6 min, while in random composites improvement can be seen up to 30 min. Effective poling conditions found for structured composites are 7.5 kV/mm for 6 min at 150°C, and random: 10 kV/mm for 30 min at 150°C. Effective poling conditions are found at a lower field and time than in random composites, due to the improved inter-particle distance in the structured composites. The average dielectric constant of the optimally poled KNLN-PDMS composites was 5.9 and 8.6 for random and structured, respectively, with an average dielectric loss of 1.5% each. The low stiffness of the polymer matrix is retained in the structured KNLN-PDMS composites, as measured perpendicular to the direction of alignment, and is 8.6 MPa on average. Finally, the energy harvesting figure of merit (g33d33) of the structured composites is equivalent to 3.7 pm3/J, bringing the performance within the same order of magnitude as monolithic piezoelectric ceramics and PVDF based polymers.
Figure 3. Variation of the piezoelectric charge constant of random and structured KNLN-PDMS composites, poled at 150°C for 30 min, with the poling electric field strength.
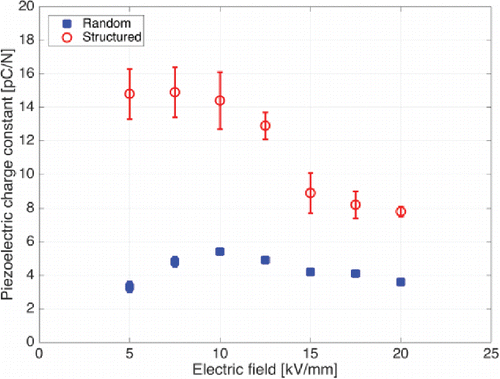
Conclusions
Flexible KNLN-PDMS composites with 10 vol.% of filler are prepared in both random and dielectrophoretically structured forms. Effective poling conditions are identified at 6 min, 150°C, and 7.5 kV/mm for structured and 10 kV/mm for random composites with improvements up to 30 min. Further increases in temperature lead to degradation of the polymer matrix. Increases in poling time have no demonstrable effect in structured composites, while increasing the electric field only reduces piezoelectric performance by degradation of the polymer matrix. Dielectrophoretic structurization leads to increased piezoelectric performance in the composites, on par with PVDF based piezoelectric polymers at a significantly lower dielectric loss.
References
- J. Rödel, K. G. Webber, R. Dittmer, W. Jo, M. Kimura, and D. Damjanovic, Transferring lead-free piezoelectric ceramics into application. J Eur Ceram Soc. 35(6), 1659–1681 (2015).
- A. Jain, J. PK, S. harma. AKr, A. Jain, R. P. N., Dielectric and piezoelectric properties of PVDF/PZT composites: A review. Polym Eng Sci. 55, 1589–1616 (2015).
- R. E. Newnham, D. P. Skinner, and L. E. Cross, Connectivity and piezoelectric-pyroelectric composites. Mater Res. 13, 525–536 (1978).
- D. A. van den Ende, B. F. Bory, W. A. Groen, and S. van der Zwaag, Improving the d33 and g33 properties of 0–3 piezoelectric composites by dielectrophoresis. J Appl Phy. 107, 024107 (2010).
- G. Sa-Gong, A. Safari, S. J. Jang, and E. Newnham, Poling flexible piezoelectric composites. Ferroelectrics Lett. 5(5), 131–142 (1986).
- C. K. Wong and F. G. Shin, Role of interfacial charge in the piezoelectric properties of ferroelectric 0–3 composites. J Appl Phy. 97, 034111 (2005).
- D. B. Deutz, N. T. Mascarenhas, S. van der Zwaag, and W. A. Groen, Enhancing energy harvesting potential of (K, Na, Li)NbO3-epoxy composites via Li substitution. J Am Ceram Soc. 100(3), 1108–1117 (2017).
- D. B. Deutz, N. T. Mascarenhas, J. B. J. Schelen, D. M. de Leeuw, S. van der Zwaag, and P. Groen, Flexible piezoelectric touch sensor by alignment of lead-free alkaline niobate microcubes in PDMS. Adv Funct Mater. 27(24), 1700728 (2017).