ABSTRACT
Aluminium alloys play a crucial role in the aerospace industry due to their lightweight properties and strength. Achieving an acceptable level of corrosion protection of aluminium alloys without chromates remains a challenge. Ongoing research at the author’s company focuses on improving corrosion resistance by formulating epoxy systems and exploring additives without the use of Cr. The company’s best to-date Cr-free (CF) primer reached 5000 h of salt spray exposure. Additionally, IPTREAT12, a water-based pre-treatment that enhances adhesion and corrosion resistance, was investigated. IPTREAT12, which replaces chromating baths, significantly extended the lifespan of the paint system. When combining Indestructible’s surface pre-treatment IPTREAT12 with one of its Cr-free paint formulations, over 6000 h of salt spray resistance were reached.
Aluminium alloys are widely used in the aerospace industry, and they used to be protected against corrosion by chromates, containing Cr(VI), either via immersion in chromating baths or by chromate containing paints, or both. Chromates have excellent anticorrosive properties, but they are also extremely toxic and carcinogenic, with risks during manufacture and application. They are, therefore, regulated under the UK and EU REACH (Regulation on the Registration, Evaluation, Authorisation and Restriction of Chemicals). To be legally compliant, chromates may only be used in the UK and the EU if there is a REACH authorisation in place. Much work has been done and is still being done to replace chromates whilst maintaining an acceptable level of anticorrosion performance.
In order to understand the level of anticorrosion performance achieved by chromates, IP3-6362, one of Indestructible’s existing chromate containing 2-pack epoxy primers, was tested. The coating was sprayed onto aluminium panels at 25 microns dry film thickness and tested in neutral salt spray chambers (ASTM B117 standard). shows the results obtained with time spent in test (panels were scanned at various intervals).
Figure 1. Neutral salt spray resistance of Chromate primer IP3-6362 used with our standard catalyst sprayed over 2024 Aluminium alloy at 25 microns dry film thickness at t0, after 500 h of exposure, 1000, 4000, 6000, and 8620 h.
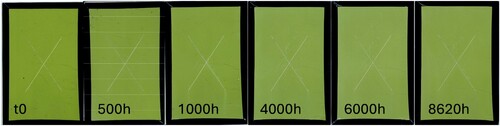
These images show that the coating remained corrosion-free even after almost one year in neutral salt spray chamber. Achieving the same level of anticorrosion protection in a primer without chromates has not yet been achieved, to the best of the author's knowledge. Only the results obtained on 2024 aluminium alloy are shown in this article, but 7075 aluminium alloy has also been tested and the results were similar.
As a comparison, shows the corrosion resistance obtained on IP3-6700, one of Indestructible’s current Cr-free primers (colour matched to the chromate-containing primer), applied on 2024 aluminium alloy at 30 microns dry film thickness. IP3-6700 primer reaches 2000 hours of salt spray resistance.
Figure 2. Neutral salt spray resistance of Cr-free primer IP3-6700 used with our standard catalyst sprayed over 2024 Aluminium alloy at 30 microns dry film thickness at t0, after 500 h of exposure, 1000 h, and 2000 hours.
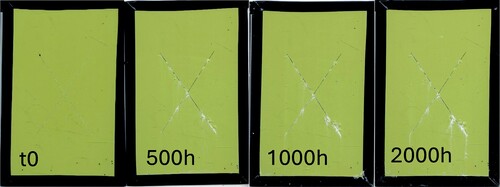
The Cr-free primer shows some signs of corrosion after 500 h of exposure and significant corrosion after 2000 hours, less than a quarter of the protection offered by the chromate primer.
In recent years researchers at Indestructible have been working extensively to increase the corrosion resistance of its 2-pack epoxy systems, with over 30 trial formulations for the base and half a dozen additives tested in the catalyst; only some of them will be shown in this article.
Whilst optimising the paint and the catalyst formulations is key, studies have also been made on the effect of the company’s water-based pre-treatment called IPTREAT12 which promotes adhesion of the paint onto the metal surface as well as enhancing the corrosion resistance of magnesium alloys, aluminium alloys and steels. This aqueous solution can be sprayed or used by immersion, and it is non-toxic. It can replace chromating baths. It adds two additional steps in the process compared to direct to metal application ().
shows CF Variant 2 with Catalyst Mod 1 sprayed over 2024 aluminium alloy. In one case the paint was applied direct to metal (no pre-treatment), and in the other, the Cr-free pre-treatment IPTREAT12 was used prior to applying the paint. The corrosion resistance of the paint alone in that case reached 3200 h in salt spray (which is already an improvement compared with IP3-6700). When IPTREAT12 was used, the same paint system lasted 5200 h in salt spray test, showing the extensive enhancement of the corrosion protection brought about by the use of IPTREAT12.
Figure 4. Neutral salt spray resistance of CF Variant 2 with Catalyst Mod 1 sprayed over 2024 Aluminium alloy (panel without pre-treatment has 35 microns dry film thickness; panel with IPTREAT12 has 30 microns dry film thickness) at t0, after 1000 h of exposure, 3200, and 5200 h.
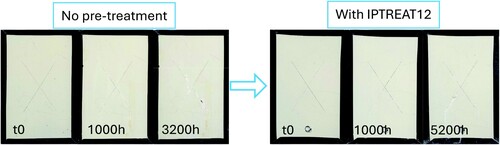
Skydrol (Tri-n-butyl phosphate) resistance has also been tested and the results are listed in . Three aspects of the coating have been looked at: blistering, 1000 g scratch test and cross hatch adhesion. If one test failed, the paint system was excluded from further consideration. The modifications to the catalyst seem to have a strong effect on the coatings performances, and Catalyst Mod 2 shows excellent results for all three bases tested (IPTREAT12 treated panels with CF Variant 1; CF Variant 19; and CF Variant 20).
Table 1. Tri-n-butyl phosphate (Skydrol) immersion for 7 days at 70°C.
Water immersion (ASTM D870-15) was also performed on the same paint systems for 7 days at 40°C (). In this case, as well, the best results were obtained when the catalyst Mod 2 was used. The system IPTREAT12 – CF Variant 1 also passed with all three catalysts.
Table 2. Water soak test for 7 days at 40°C.
Cyclic acidified salt spray corrosion (ASTM G85 standard) has also been tested and CF Variant 1 with Standard Catalyst sprayed over panels pre-treated with IPTREAT12 as well as CF Variant 19 with Standard Catalyst (no pre-treatment) both passed 2000 hours in test ().
Figure 5. Cyclic acidified salt spray resistance of CF Variant 1 with Standard Catalyst sprayed over panels pre-treated with IPTREAT12 2024 Aluminium alloy (top line 45 microns dry film thickness) and CF Variant 19 with Standard Catalyst sprayed over 2024 Aluminium alloy, no pre-treatment (bottom line 25 microns dry film thickness) at t0, after 500 h of exposure, 1000, 1500 h and 2000 hours.
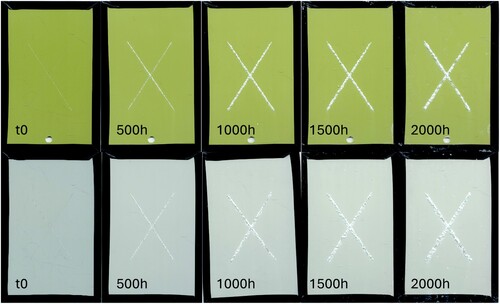
The best-to-date tested anticorrosive Cr-free primer is CF Variant 15. It passed 5000 h of neutral salt spray resistance using Catalyst Mod 1 without any surface pre-treatment of the panels ().
Figure 6. Neutral salt spray resistance of CF Variant 15 with Catalyst Mod 1 sprayed over 2024 Aluminium alloy at a dry film thickness of 35 microns at t0, after 1000 h of exposure, 2000 hours, 4000 and 5000 h.
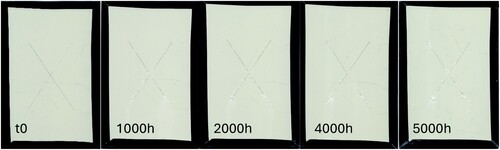
Work has since then started on testing CF Variant 15 with Catalyst Mod 2 and better results are expected from this combination. Testing is still ongoing. Thanks to a collaboration with Warwick Manufacturing Group (WMG), Warwick University (Dr. Paul Lansdell, Dr. Indrachapa Bandara, and Matthew Chant), extensive SEM-EDX studies have been performed on our coatings, pre- and post-salt spray exposure. Some images of CF Variant 15 are shown in .
The film thickness on the SEM images confirms the measurement from the Indestructible probe in-house. The elemental distribution for the main components of the formulation can also be seen. On the bottom right corner, the legend was removed for formulation commercial proprietary reasons. The particle size and distribution look satisfactory and in accordance with the raw materials used.
When combining surface pre-treatment IPTREAT12 with CF Variant 1 and Catalyst Mod 2, over 6000 h of salt spray resistance () were reached. Since then testing has started on CF Variant 15 with Catalyst Mod 2 on pre-treated panels with IPTREAT12 and good results are also expected, possibly even better than those noted here.
Figure 8. Neutral salt spray resistance of CF Variant 1 with Catalyst Mod 2 sprayed over panels pre-treated with IPTREAT12 2024 Aluminium alloy at a dry film thickness of 35 microns at t0, after 500 h of exposure, 2000 hours, 4000 and 6000 h.
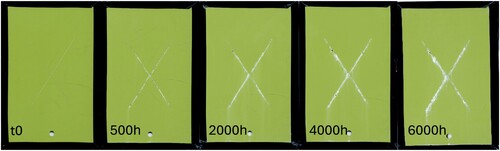
Improving the anticorrosion performance of the company’s 2-pack epoxy primer is vital to the business and the aerospace industry in general. Progress is regularly shared with all the prime customers and joint testing will hopefully result in the approval of Indestructible’s new products. The IPTREAT12 water-based surface pre-treatment is already available and approved by some primes, particularly on magnesium alloys.
Indestructible is also actively working on improving its water-based 2-pack epoxy primers in an effort to reach net zero in the near future.
Acknowledgements
The author would like to thank Matthew Chant, Dr. Paul Lansdell, and Dr. Indrachapa Bandara (WMG) for their work providing the SEM-EDS images as well as their constructive input throughout the project.
Disclosure statement
No potential conflict of interest was reported by the author(s).