ABSTRACT
In this paper, a new method is developed for tool path planning on triangular mesh surfaces with consideration of the scallop height restriction and the path smoothness. This method first maps the triangular mesh surface into a unit disk region by using a harmonic map algorithm, and then the shortest boundary path graph (SBPG) is constructed on the unit disk region to describe the shortest geodesic distance from each mesh vertex to the surface boundary. The tool path is then obtained by inversely mapping the contours of SBPG from the harmonic mapped region to the physical space of mesh surface. During this process, a subdivision method is used to boost the computing efficiency and a smoothing treatment is conducted on the SBPG to improve the path smoothness. The tool path planning is performed starting from the surface boundary in an iteration process. Taking the level difference of SBPG contours as the initial path interval and being supplemented by a correction process, the maximal step distance between any two paths, which meets the requirement of scallop height restriction, can be determined efficiently. Typical simulation cases and experiments are carried out to illustrate the effectiveness of the proposed method.
Acknowledgements
The authors would like to thank for the financial support from the Science Foundation Ireland (SFI) (No. 15/RP/B3208) and ‘111’ project by the State Administration of Foreign Experts Affairs and the Ministry of Education of China (No. B07014).
Disclosure statement
No potential conflict of interest was reported by the authors.
Additional information
Funding
Notes on contributors

Fusheng Liang
Fusheng Liang is a postdoctoral researcher in the Centre of Micro/Nano Manufacturing Technology (MNMT-Dublin) situated in the Engineering and Materials Science Centre, at University College Dublin. He holds a PhD (2018) in Mechanical Engineering, from Jilin University. His current research centres on CNC machining and digital manufacturing of freeform surfaces with high precision.
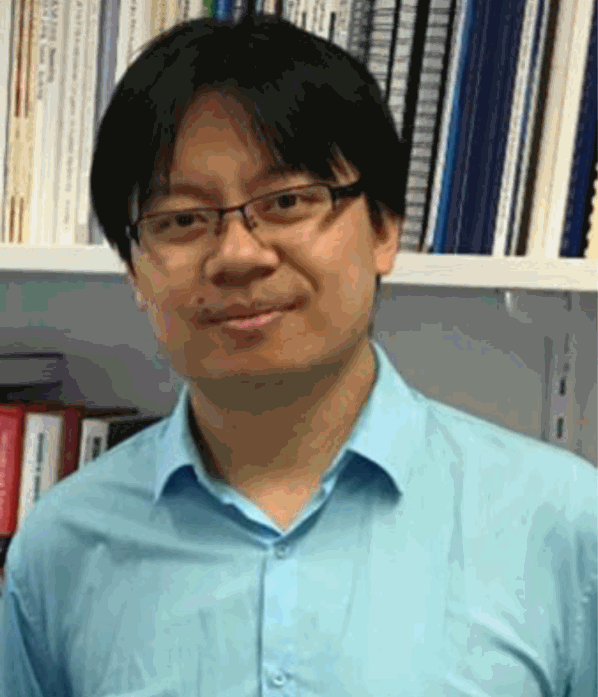
Chengwei Kang
Chengwei Kang is a Senior Research Engineer of the Centre of Micro/Nano Manufacturing Technology (MNMT-Dublin) at University College Dublin. He received his Ph.D. degree in Mechanical Engineering from the University of Queensland (UQ) in 2016. His research interests are micro/nano machining of difficult-to-machine materials and surface finishing of next-generation bio-implants.
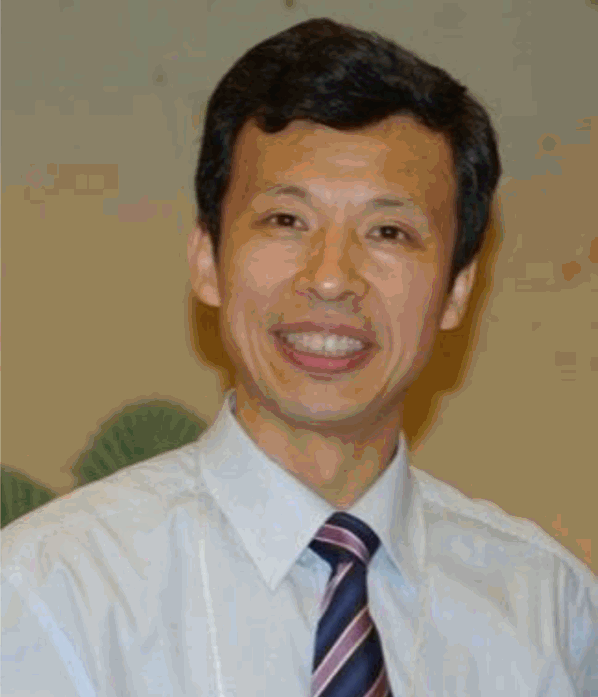
Fengzhou Fang
Fengzhou Fang is a joint Professor of Centre of the Micro/Nano Manufacturing Technology (MNMT) at Tianjin University and University College Dublin. He has been working in the field of manufacturing since 1982 when he became a faculty member at university. He has conducted both fundamental studies and application development in the areas of optical freeform design and manufacturing, micro/nano machining, and ultra-precision machining and measurement benefiting a variety of industries in medical devices, bio-implants, optics and mould sectors.