ABSTRACT
The mechanical properties of polyurethane compounds were experimentally investigated by changing the composition of their components. Polyol components (polyoxypropylene glycol: PPG, polyoxytetramethylene glycol: PTMG, and polycarbonatediol: PCD) were mixed with monomeric methylene diphenyl diisocyanate to synthesize polyurethane pre-polymer, mixed with chain extenders (1,4’-butanediol: 1,4’-BD or dimethylthiotoluene diamine: DMTDA), and cured, to prepare four types of polyurethane resins. Tensile tests were conducted using a mechanical testing machine with a strain rate of approximately 0.3 s−1 and a hydraulic high-speed tensile testing machine with a strain rate of approximately 500 s−1. The temperature was controlled to be −40°C, −10°C, or 25°C. When PTMG was used as the polyol, the stress-strain relationship was less sensitive to temperatures and loading rates, and the material properties exhibited a relatively good balance between elongation and strength. Additionally, the use of 1,4’-BD as a chain extender resulted in higher elongation and lower strength than the use of DMTDA. Conversely, the stress-strain relationship was dramatically altered by the test conditions when PPG and PCD were used as the polyol and embrittlement under a combination of low temperature and high strain rate was confirmed. Furthermore, there were certain compositional combinations that exhibit necking at low temperatures.
1. Introduction
Adhesive bonding technology is used in a wide range of engineering fields, including the electrical, transportation, and aerospace industries.[Citation1,Citation2] The automotive industry has traditionally used adhesive bonding, but the demand for applying adhesives has increased dramatically based on requirements for lighter vehicle bodies with recent moves to tighten global regulations aimed at reducing CO2 emissions.[Citation3] A promising method for reducing the weight of automobile bodies is to replace conventional materials such as steel with lightweight materials, including aluminum alloys and carbon-fiber-reinforced plastics (CFRPs). However, CFRPs in particular face significant difficulty in welding.[Citation4] Additionally, it is important to use lightweight materials in the correct locations. Therefore, hybrid structures combining steel and CFRPs or CFRP mounted on aluminum alloys have appeared,[Citation5] which are typically referred to as multi-material structures. In such structures, joining methods are critical. Adhesive bonding is one of the suitable methods for joining dissimilar materials and is attracting attention in the automotive industry.[Citation6,Citation7]
Automotive manufacturing generally uses epoxy adhesives for structural applications that require high strength and polyurethane adhesives for semi-structural applications that require less strength. A practical application of polyurethane adhesives is the bonding of windshields, which is called direct glazing.[Citation8] Considering potential future changes in car body materials and the shift to multi-material structures, the importance of composite materials and plastics is expected to increase and the use of adhesives that do not require heat-curing and provide elongation capabilities will be necessary. Therefore, polyurethane adhesives are also expected to find use in structural applications.
High reliability is essential from a safety perspective when applying polyurethane adhesives as structural adhesives for industrial usage. Adhesives are polymeric materials and become brittle under high-speed and low-temperature conditions, the combination of which causes further embrittlement. However, high-impact resistance is particularly important in the case of a collision. Additionally, automobiles are used under a wide range of temperatures. Therefore, the combination of these two conditions is extremely important when considering the adhesives used for vehicles, and the temperature effect on the impact shear strength of adhesives for the automotive industry has been widely investigated.[Citation9–13]
Various studies have been conducted on the impact loading of adhesive joints in terms of strength and toughness.[Citation14] To apply impact load, Izod or Charpy test machine, drop weight testing machine, or split Hopkinson bars (SHPBs) are widely used. SHPBs facilitate experiments with the highest strain rates, but limited displacement. With the advent of the digital image correlation (DIC) technique, it became possible to measure strain in the high-speed range accurately. With the evolution of testing equipment and analysis technology, the phenomena associated with high-speed deformation are gradually becoming clearer.
In general, strength increases and elongation decreases with an increasing loading rate or decreasing temperature because materials become more brittle. However, the effects of impact loading and/or low temperatures on strength and toughness are complicated and analysis is required for each material. In the case of fracture tests, the transition from stable to unstable fractures under high-speed or low-temperature conditions has been reported in wedge-peel or double-cantilever-beam tests.[Citation15–17] Conversely, the fracture toughness under stable fracture is less sensitive to loading rates or temperatures, except for creep or temperatures above the glass transition temperature (Tg), in many adhesives. Under creep or high-temperature conditions, fracture toughness drops dramatically.[Citation18,Citation19] Regarding strength, an increase in joint strength with a higher loading rate or lower temperature has been reported in many cases.[Citation20–25] Kadioglu and Adams reported that the shear strength of a flexible epoxy/acrylate hybrid adhesive for automotive applications increased by approximately two times under impact loading when using a pendulum impactor and single-lap-joint specimen.[Citation20] Yokoyama et al. also reported an increase in joint strength with an increasing loading rate when using modified SHPBs for a two-component structural thermosetting epoxy adhesive.[Citation21] Challita et al. conducted double-lap shear tests under a wide strain rate range from 10−4 s−1 to 104 s−1 and found that strength increases and then decreases with an increasing strain rate for a toughened epoxy film adhesive.[Citation22] A decrease above the critical strain rate at approximately 103 s−1 was attributed to adiabatic heat.
Many of the adhesives used in the aforementioned studies were epoxy adhesives. Because the Tg of epoxy adhesives is generally much higher than room temperature (RT), the effects of different loading rates and temperatures were similar. However, there are many types of adhesives available. Therefore, differences depending on adhesive type have also been reported.[Citation26–28] Polyurethane adhesives in particular exhibit varying tendencies. Fracture toughness increases with an increasing loading rate for a polyurethane adhesive, whereas an epoxy adhesive is less sensitive to the loading rate.[Citation27,Citation29] Because the Tg of the polyurethane adhesive was lower than RT, an increase in the loss factor tan δ with increasing test speed was thought to be the main factor. When the Tg of a polyurethane adhesive was slightly higher than RT, the fracture toughness dramatically decreased while maintaining stable fracture at lower temperatures and high loading rates.[Citation30] The same adhesive has also been used for thick-adherend shear tests under low temperature and high-strain-rate conditions.[Citation31] When increasing the loading speed while maintaining the testing temperature, the shear strength increased. Conversely, the shear strength decreased with a decreasing temperature for a given loading speed. Therefore, the strength was higher with a higher temperature and loading rate, and the relationship between the temperature and loading rate was inconsistent with viscoelastic behavior.
The best way to understand such complex phenomena is to investigate the material behavior of the adhesive itself. Changes in the mechanical properties of adhesives caused by temperature have been widely investigated using standard mechanical tensile testing machines with environmental chambers to obtain stress-strain (SS) curves .[Citation32] Tension behaviors under high-strain-rate conditions have been investigated using SHPBs for polyurethane and polyurea materials.[Citation33–35] However, for soft and stretchable materials, testing using SHPBs faces difficulty due to the limitation of maximum displacement under tension. Therefore, other types of high-speed tensile testing instruments are essential to analyze materials with significant elongation.[Citation36–38] Additionally, the combination of high strain rates and low temperatures is expected to change material properties dramatically if the Tg of a materials is near or lower than RT.[Citation33,Citation34]
Polyurethane adhesives can significantly change their material properties by changing components. Specifically, the chemical structure, type, and number of functional groups, as well as molecular weight, can be varied by combining isocyanate, polyol, and chain extenders, and various mechanical properties can be obtained.[Citation39] The transparency and Tg can also be varied.[Citation40,Citation41] Although the strain rate dependence of tensile or compressive properties with different compositions of polyurethane resins has been reported,[Citation42,Citation43] there should also be temperature dependence. Therefore, understanding the changes in SS relationships under both temperature and loading rate variations is important.
In this study, we focused on the compounds that serve as the main ingredients of polyurethane adhesives and similar adhesives, and considered the types and compositions of isocyanates, polyols, and chain extenders. The effects of composition on tensile properties were experimentally investigated to explore polyurethane resins that have sufficient strength and elongation at RT and are not easily embrittled at low temperatures and high strain rates. Four polyurethane resins with typical compositions were considered in our experiments and each material was evaluated at different tensile rates and temperatures.
The remainder of this paper is organized as follows. Section 2 presents the details of all materials used in this study. Section 3 describes our experimental procedures. Section 4 presents and discusses the results of our experiments. Finally, Section 5 summarizes our main conclusions.
2. Materials
2.1. Composition of polyurethane resin
Polyurethane compounds are composed of isocyanates, polyols, and chain extenders. gives the formulations used to prepare four types of polyurethane samples by varying the combination of polyols and chain extenders, which are denoted as polyurethane compounds (PUCs) 1, 2, 3, and 4. Industrial-grade monomeric methylene diphenyl diisocyanate (MDI) which consists of mainly 4,4’-diphenylmethane diisocyanate, was used as the isocyanate.
Table 1. Composition and appearance of polyurethane compounds.
In the case of PUC1, polyoxypropylene glycol (PPG) with a molecular weight of 2000 and monomeric MDI were synthesized under the condition of NCO/OH Index as 2.5 at the temperature of 80°C for 4 h into a urethane pre-polymer using a bismuth-based catalyst, followed by curing with 1,4’-butanediol (1,4’-BD) under the condition of NCO/OH Index as 1.2 at room temperature.
The polyol was changed to polyoxytetramethylene glycol (PTMG) with a molecular weight of 2000 for PUC2 and polycarbonatediol (PCD) with a molecular weight of 2000 for PUC3. These polyols are diol-type polyols and the other conditions, such as synthesis Index and temperature, were the same as those for PUC1.
In the case of PUC4, the chain extender was changed from 1,4’-BD to an amine compound called dimethylthiotoluene diamine (DMTDA) while keeping the other conditions the same as PUC2 to investigate the effects of differences in chemical bonding on physical properties. PUC1, PUC2, and PUC3 are largely composed of urethane bonds, whereas PUC4 is composed of both urethane and urea bonds.
2.2. Specimen preparation
The four types of polyurethane compounds described above were cured at a temperature of 23°C and humidity of 55% Rh. The polyurethane compounds were poured into a mold. When they solidified to some extent, they were removed from the mold, cured on release paper, and left at RT for one to three weeks to harden before punching with a dumbbell shape die cutter. The specimens were then left for several more months to allow the reaction to reach full completion and the material properties to remain constant. The viscoelastic characteristics of the polyurethane resins were investigated prior to the tensile tests. shows the results of dynamic mechanical analysis (DMA) under a temperature sweep of 3°C/min at a constant frequency of 10 Hz using a DMA machine (Rheogel-E4000, UBM Corp., Kyoto, Japan). Each Tg value was obtained from the peak of the loss factor tan δ as −16.0°C for PUC1, −35.9°C for PUC2, 8.2°C for PUC3, and −59.6°C for PUC4, respectively.
Figure 1. Viscoelastic characteristics of polyurethane compounds with respect to temperature: (a) storage modulus E’, (b) loss modulus E”, and (c) loss factor tan δ.
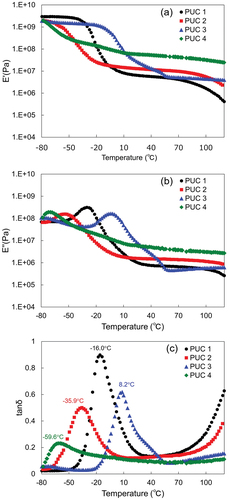
The cured compound sheets were punched into the final specimen shapes. The thickness and width of each specimen were measured using a micrometer prior to our tests. The specimen geometry is shown in . The length of the gripping area was different between the static test and impact test based on differences in the gripping jig for each testing machine (see ). The DIC method has been widely used to measure strain optically, but the prepared materials elongated too much to use DIC. Therefore, the parallel parts of the specimens were marked laterally with six black lines spaced 1 mm apart and the marks were tracked using a camera to measure strain. Because the resolution of this method was too low to calculate the Young’s moduli obtained from the results in the small-strain range in the early stages of the tests, only the material behavior in the largely deformed section is discussed.
3. Experiments
3.1. Static tests
A mechanical material testing machine (AG-XDplus 50 kN, Shimadzu Corp., Kyoto, Japan) with a thermostatic chamber (TCR2W, Shimadzu Corp., Kyoto, Japan) was used for the static tensile tests. presents an overview of the equipment setup. A load cell with the capacity of 5 kN and pantograph-type gripper were used. Three tests were performed for each condition. The crosshead speed was set to 300 mm/min. The temperature was set to −40°C, −10°C, or RT (approximately 25°C). The RT tests were performed without using the thermostatic chamber. In the −10°C and −40°C tests, the specimens were set in the gripper, the heat controller for the thermostatic chamber was switched on, and the test was performed 30 min after the temperature in the chamber reached the target temperature. A digital camera (Lumix DMC-GH2, Panasonic Corp., Osaka, Japan) was placed outside the chamber to record elongation through the window. Although a double-glazed window with a heater was installed in the door, the frost prevented observation of the −40°C tests. Therefore, dry air was blown into the space between the inside and outside glass panels to prevent ice buildup on the window, as shown in . The movement of the target marks was automatically tracked using image analysis software (Photron FASTCAM Analysis, Photron Inc., Tokyo, Japan) and the strain was obtained from the displacement of the two outermost targets.
3.2. High-speed tests
A hydraulic high-speed tensile tester (HITS-TX, Shimadzu Corp., Kyoto, Japan) with a thermostatic chamber was used for our high-speed tests. presents an overview of the equipment setup. A load cell with a capacity of 10 kN was used. Three tests were performed for each condition. The crosshead speed was set to 5 m/s. The temperature was set to −40°C, −10°C, or RT. The waiting time before the tests at −40°C and −10°C was the same as that in the static tests. A high-speed camera (MEMRECAM HX-7S, NAC Imaging Technology, Inc., Tokyo, Japan) was placed outside the chamber to record elongation through the window. The frame rate was set to 20,000 fps or 100,000 fps. The movement of the target marks was manually tracked using image analysis software (ImageJ, National Institute of Health, Maryland, USA) and the strain was obtained based on the displacement of the two outermost targets.
3.3. Nuclear magnetic resonance (NMR) analysis
Pulse NMR (JNM-MU25, JEOL Ltd., Tokyo, Japan) was used to analyze the structures of the polyurethane resins. Pulse NMR allows the relaxation time of organic compounds to be measured, from which differences in the degree of cross-linked structures can be detected. The solid echo method, which is one of the available pulse-NMR-based analysis methods, was adopted.
4. Results and discussion
4.1. Static test results
The SS curves derived from the static tensile tests are presented in , and the maximum stress and maximum strain values are presented in . The strain rates are in the range of 0.1 to 1 s−1 (average 3.2 ± 0.4 × 10−1 s−1). The mechanical properties and material behavior of each polyurethane resin are very different. At RT, PUC1 exhibits the greatest elongation, but the lowest stress (i.e., it is the most flexible). The shapes of the SS curves for PUC2, PUC3, and PUC4 at RT are similar and representative of typical rubber-elastic behavior. The elongation is in the order of PUC3 < PUC4 < PUC2, but even for PUC3, the maximum strain is over 350%. The maximum stress follows the opposite order as elongation.
Figure 5. Typical SS curves of each polyurethane compound under static loading conditions: (a) RT, (b) −10°C, and (c) −40°C.
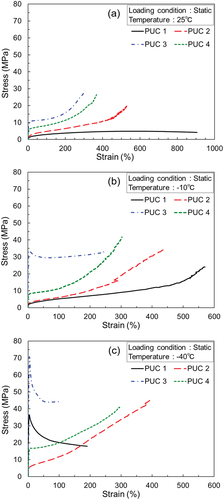
Figure 6. (a) Tensile strength and (b) elongation of each polyurethane compound under static loading conditions.
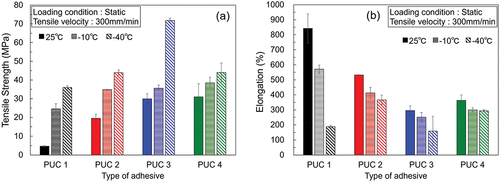
When reducing the temperature, the strength increases and the elongation decreases, regardless of the resin type. Additionally, the material behavior changes in some cases. In the case of PUC1, rubber-elastic behavior is observed at −10°C and elastoplastic behavior with a stress peak in the middle is observed at −40°C. Therefore, it can be concluded that PUC1 is a resin susceptible to temperature effects. This elastoplastic behavior is also observed in the case of PUC3 at −10°C and −40°C. Particularly at −40°C, the maximum stress dramatically increases. This demonstrates that PUC3 is also temperature sensitive. In contrast, PUC2 and PUC4 maintain their rubber-elastic behavior and elongate by over 250%. This demonstrates that PUC2 and PUC4 are less temperature-sensitive resins, which can be correlated to the Tg of the two compounds being much lower than the others.
4.2. High-speed test results
The SS curves derived from the high-speed tests are presented in , and the maximum stress and strain values are presented in . The strain rates are in the range between 100 to 1000 s−1 (average 4.8 ± 1.0 × 102 s−1). In most cases, the maximum stress increases and the elongation decreases with decreasing temperature, which is a similar trend compared to the static tests, but the strength is higher and the elongation is smaller compared to the static test results. In the case of PUC1, a significant change in behavior is observed between −10°C and −40°C. Above −10°C, the elongation is over 500%, but at −40°C, it is only 12.3% and the resin becomes extremely brittle, i.e., it is considered that a transition to a glassy state occurred. presents the images captured during the high-speed tests at RT and −40°C for PUC1. An entirely different behavior is observed, revealing that the combination of low temperature and high strain rate resulted in the material exhibiting glass-like behavior. PUC3 exhibits a similar change in the SS curve compared to the static tests. However, localized necking is observed under the combination of low temperature and a high strain rate, as shown in . A portion of the parallel section is constricted at −10°C and large local elongation occurs. This partial necking is more pronounced at −40°C. Therefore, the local strain at the constriction (ε2) was compared to the total strain (ε1) in terms of stress−strain relationship in and time variation of strain in . The numbers in correspond to the photograph numbers in . Although the global average strain (ε1) decreases to 130%, the local strain (ε2) is approximately 400% at −40°C. This indicates that elongation does not decrease with decreasing temperature, but constriction makes it appear as if elongation decreases. Three phases were confirmed from the strain variation over time; the initial stage with slow elongation until reaching the maximum stress, the second stage with localized necking, and the third stage with fast elongation to fracture. After necking occurred, the local strain rate was several times larger than the global strain rate. Compared to PUC1 and PUC3, PUC2 and PUC4 have a lower Tg, making them less sensitive to temperature even under high-strain-rate conditions.
Figure 7. Typical SS curves of each polyurethane compound under high-strain-rate loading conditions: (a) RT, (b) −10°C, and (c) −40°C.
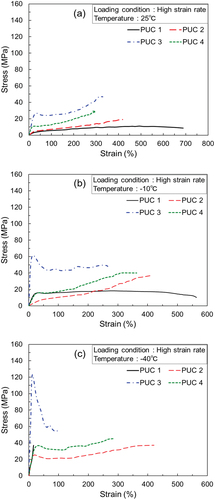
Figure 8. (a) Tensile strength and (b) elongation of polyurethane compounds under high-strain-rate loading conditions.
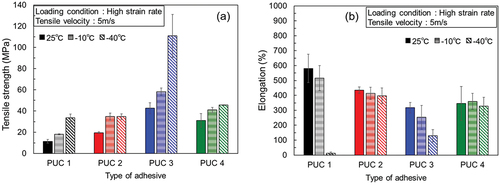
4.3. Analysis of polyurethane compounds based on pulse NMR and DMA results
presents the results of pulse NMR analysis. The S phase is the hard segment and the L phase is the soft segment. The M phase represents a segment with hardness between those of the S and L phases. PUC1, PUC2, and PUC4 contain a large amount of the L phase with little of the S and M phases. Unlike the other three resins, PUC3 is dominated by the S and M phases and contains little L phase. From the perspective of composition, PUC1, PUC2, and PUC4 are relatively soft materials, whereas PUC3 is relatively hard.
Figure 13. (a) Phase ratios and (b) relaxation times of polyurethane compounds evaluated by pulse NMR.
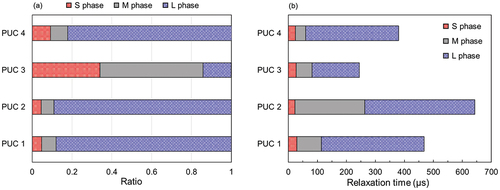
PUC1 is a polyurethane resin with a large amount of L phase and exhibited the lowest strength and highest elongation among the four resins at RT in the static test. This can be attributed to the amorphous nature of the PPG used for the polyol. However, the Tg was −16.0°C. Therefore, at −40°C, the compound behavior changed from rubber elastic to elastoplastic even at slow test speed. At high test speed, it became more brittle and the plastic region disappeared.
At RT, PUC3 exhibits elongation exceeding 300%, even at high strain rates, indicating good rubber-elasticity. However, in terms of composition, S and M phases with relatively hard segments account for large proportions and the L phase is scarce. The reason for this discrepancy can be attributed to the fact that the polyol in PUC3 is PCD. In addition to the crystalline nature of PCD, it is characterized by strong molecular interactions between carbonate groups, which increases the strength of resin materials containing this component. Therefore, PUC3 is considered to have properties similar to a soft plastic, rather than a rubber-elastic material. PUC3 had the highest Tg, but it was still slightly lower than RT. Therefore, its behavior can be transformed from rubber-elastic to elastoplastic by simply reducing the temperature or increasing the test speed. However, it did not transition to a glassy state, even under the combination of low temperature and a high strain rate. Therefore, it was revealed that the Tg can be used an index of the ease of behavior changes, but changes are not determined solely by the Tg. Furthermore, necking caused the specimen to fail early, resulting in a reduced average failure strain. Therefore, the decrease in elongation was not caused by embrittlement, but by necking. A possible cause of this necking could be a localized temperature increase in the parallel portion of the specimen. Pan et al. demonstrated that high-strain-rate conditions can cause local adiabatic heating in a specimen, leading to a local temperature rise.[Citation44] As observed through pulse NMR, PUC3 has a high content of S and M phases, similar to soft plastics, and tends to be highly exothermic. Therefore, in the high-speed test, the material was more adiabatic, which could have led to necking caused by a local temperature increase. Considering the characteristics of polyurethane resins as adhesives for automobile bodies, it is not desirable to use an adhesive that is prone to embrittlement under any conditions. Additionally, resin strength must be sufficiently high. PUC3 has sufficient strength but appears to be brittle in some cases. However, the reason for the small elongation of PUC3 was the necking of the specimen and the local strain in the vicinity of the necking was sufficiently large. Therefore, there is a possibility that this material has sufficient properties to be used as an adhesive with high crash resistance. When considering the application of materials such as PUC3 to adhesives, it is necessary to evaluate not only the material properties but also the strength and toughness of a bonded specimen in detail.
PUC2 and PUC4 contain a large amount of L phase, similar to PUC1, but their strength is much higher than that of PUC1. PUC2 and PUC4 had Tgs of −39.5°C and −59.6°C, respectively. Therefore, a behavior change is expected only under the combination of low temperature and high speed. Under the condition of −40°C in the high-speed tests, the SS curves became more elastoplastic than rubber-elastic. However, the maximum stress and maximum strain values changed little, and PUC2 and PUC4 exhibited a good combination of strength and elongation under most test conditions. Although PUC2 and PUC4 exhibited similar trends, the SS curve of PUC4 was always above that of PUC2 under the same test conditions. This result can be attributed to the difference in cross-linkers. PUC2 used 1,4’-BD, whereas PUC4 used DMTDM. Generally, 1,4’-BD produces more urethane bonds, whereas DMTDM produces urea bonds. Compared to urethane bonds, urea bonds have stronger binding strength, which may be the reason for the differences observed between PUC2 and PUC4.[Citation45] The more urea bonds, the higher the stress and the less elongation.
5. Conclusions
This study focused on the main components of polyurethane adhesives and other similar compounds. The effects of their composition on tensile properties were experimentally investigated to explore polyurethane resins that have sufficient strength and elongation at RT and are not easily embrittled under conditions with low temperatures and/or high strain rates.
Four types of polyurethane resins with distinct compositions and different properties were considered in our experiments. They were obtained by varying the combination of polyol and chain extender for the same isocyanate. Each resin was evaluated by varying the temperature (25°C, −10°C, and −40°C) and tensile speed (300 mm/min for static and 5 m/s for high-strain-rate conditions). Based on our experiments, the following conclusions were obtained.
A decrease in temperature and/or increase in test speed leads to higher strength and less elongation in general.
When the Tg of a material is lower, elongation is less sensitive to temperature and strain rate.
Even when SS curves exhibit similar rubber-elastic behaviors under static loading conditions at RT, the tensile properties at low temperatures and/or high strain rates may differ significantly.
The composition ratio of hard segments (S phase), soft segments (L phase), and intermediate segments (M phase) observed from pulse NMR are important factors affecting the material properties of polyurethane resins at RT. However, no direct relationship was found with embrittlement caused by low temperatures and/or high strain rates.
The use of PTMG as a polyol is considered to be a promising option for polyurethane materials in automotive body structures based on its moderate sensitivity to temperature and strain rate. In contrast, when PPG or PCD are used, the sensitivity to temperature and strain rate increases. Therefore, there is a strong possibility of causing rapid fracture under the combination of low-temperature and high-strain rate conditions, and their application under such conditions requires careful consideration.
When isocyanate and polyol are the same, the use of 1,4’-BD as a chain extender results in greater elongation and lower strength than the use of DMTDA.
Local constriction occurs when PCD is used as a polyol under conditions with low temperature and a high strain rate. However, when analyzing local strain, little change in elongation at fracture can be observed with and without necking.
The properties of polyurethane resins under low temperatures and high strain rates vary significantly depending on the compositions of those resins. However, the effect of each component of the polyurethane resin on the mechanical behavior has not yet been perfectly elucidated. Therefore, the compositions of polyurethane adhesives must be carefully and thoroughly considered when designing such adhesives for industrial applications.
Acknowledgements
This paper was written based on results obtained in the JPNP14014 project commissioned by the New Energy and Industrial Technology Development Organization (NEDO). We would like to thank Editage (www.editage.com) for English language editing.
Disclosure statement
No potential conflict of interest was reported by the author(s).
Additional information
Funding
References
- Budzik, M. K.; Wolfahrt, M.; Reis, P.; Kozłowski, M.; Sena-Cruz, J.; Papadakis, L.; Saleh, M. N.; Machalicka, K. V.; de Freitas, S. T.; Vassilopoulos, A. P. Testing Mechanical Performance of Adhesively Bonded Composite Joints in Engineering Applications: An Overview. J. Adhes. 2022, 98(14), 2133–2209. DOI: 10.1080/00218464.2021.1953479.
- Liu, Y.; Camegie, C.; Ascroft, H.; Li, W.; Han, X.; Guo, H.; Hughes, D. J. Investigation of Adhesive Joining Strategies for the Application of a Multi-Material Light Rail Vehicle. Mater. 2021, 14(22), 6991. DOI: 10.3390/ma14226991.
- Ishikawa, T.; Amaoka, K.; Masubuchi, Y.; Yamamoto, T.; Yamanaka, A.; Arai, M.; Takahashi, J. Overview of Automotive Structural Composites Technology Developments in Japan. Compos. Sci. Technol. 2018, 155, 221–246. DOI: 10.1016/j.compscitech.2017.09.015.
- Meschut, G.; Hahn, O.; Janzen, V.; Olfermann, T. Innovative Joining Technologies for multi-material Structures. Weld. World. 2013, 58, 65–75. DOI: 10.1007/s40194-013-0098-3.
- Zinn, C.; Bobbert, M.; Dammann, C.; Wang, Z.; Tröster, T.; Mahnken, R.; Meschut, G.; Schaper, M. Shear Strength and Failure Behaviour of Laser nano-structured and Conventionally pre-treated Interfaces in Intrinsically Manufactured CFRP-steel Hybrids. Compos. B Eng. 2018, 151, 173–185. DOI: 10.1016/j.compositesb.2018.05.030.
- Banea, M. D.; Da Silva, L. F. M. Adhesively Bonded Joints in Composite Materials: An Overview. Proc. Inst. Mech. Eng. Pt. L J. Mater. Des. Appl. 2009, 223(1), 1–18. DOI: 10.1243/14644207JMDA219.
- Banea, M. D.; Rosioara, M.; Carbas, R. J. C.; da Silva, L. F. M. Multi-material Adhesive Joints for Automotive Industry. Compos. B Eng. 2018, 151, 71–77. DOI: 10.1016/j.compositesb.2018.06.009.
- Sensui, K.; Tarui, T.; Sato, C. Effect of Solvent Used for Isocyanate Primer on Interphase Formation. J. Adhes. 2021, 97(16), 1473–1485. DOI: 10.1080/00218464.2020.1789460.
- Avendaño, R.; Carbas, R. J. C.; Chaves, F. J. P.; Costa, M.; da Silva, L. F. M.; Fernandes, A. A. Impact Loading of Single Lap Joints of Dissimilar Lightweight Adherends Bonded with a crash-resistant Epoxy Adhesive. J. Eng. Mater. Technol. 2016, 138(4), 041019. DOI: 10.1115/1.4034204.
- Machado, J. J. M.; Marques, E. A. S.; da Silva, L. F. M. Influence of Low and High Temperature on Mixed Adhesive Joints under quasi-static and Impact Conditions. Compos. Struct. 2018, 194, 68–79. DOI: 10.1016/j.compstruct.2018.03.093.
- Machado, J. J. M.; Nunes, P. D. P.; Marques, E. A. S.; da Silva, L. F. M. Adhesive Joints Using Aluminium and CFRP Substrates Tested at Low and High Temperatures under quasi-static and Impact Conditions for the Automotive Industry. Compos. B Eng. 2019, 158, 102–116. DOI: 10.1016/j.compositesb.2018.09.067.
- Machado, J. J. M.; Marques, E. A. S.; da Silva, L. F. M. Mechanical Behaviour of Adhesively Bonded Composite Single Lap Joints under quasi-static and Impact Conditions with Variation of Temperature and Overlap. J. Compos. Mater. 2018, 52(26), 3621–3635. DOI: 10.1177/0021998318766641.
- Rosendo, D.; Viana, G.; Carbas, R.; Marques, E.; da Silva, L. F. M. Effect of Temperature and Moisture on the Impact Behavior of Adhesive Joints for the Automotive Industry. J. Appl. Comput. Mech. 2021, 7(3), 1488–1500. DOI: 10.22055/JACM.2021.36089.2793.
- Machado, J. J. M.; Marques, E. A. S.; da Silva, L. F. M. Adhesives and Adhesive Joints under Impact Loadings: An Overview. J. Adhes. 2018, 94(6), 421–452. DOI: 10.1080/00218464.2017.1282349.
- Blackman, B. R. K.; Kinloch, A. J.; Taylor, A. C.; Wang, Y. The Impact wedge-peel Performance of Structural Adhesives. J. Mater. Sci. 2000, 35, 1867–1884. DOI: 10.1023/A:1004793730352.
- Blackman, B. R. K.; Dear, J. P.; Kinloch, A. J.; Macgillivray, H.; Wang, Y.; Williams, J. G.; Yayla, P. The Failure of Fibre Composites and Adhesively Bonded Fibre Composites under High Rates of Test. J. Mater. Sci. 1995, 30, 5885–5900. DOI: 10.1007/BF01151502.
- Sekiguchi, Y.; Sato, C. Experimental Investigation of the Effects of Adhesive Thickness on the Fracture Behavior of Structural Acrylic Adhesive Joints under Various Loading Rates. Int. J. Adhes. Adhes. 2021, 105, 102782. DOI: 10.1016/j.ijadhadh.2020.102782.
- Jhin, G.; Azari, S.; Ameli, A.; Datla, N. V.; Papini, M.; Spelt, J. K. Crack Growth Rate and Crack Path in Adhesively Bonded Joints: Comparison of Creep, Fatigue and Fracture. Int. J. Adhes. Adhes. 2013, 46, 74–84. DOI: 10.1016/j.ijadhadh.2013.05.009.
- Banea, M. D.; Da Silva, L. F. M.; Campilho, R. D. S. G. Effect of Temperature on Tensile Strength and Mode I Fracture Toughness of a High Temperature Epoxy Adhesive. J. Adhes. Sci. Technol. 2012, 26, 939–953. DOI: 10.1163/156856111X593649.
- Kadioglu, F.; Adams, R. D. Flexible Adhesives for Automotive Application under Impact Loading. Int. J. Adhes. Adhes. 2015, 56, 73–78. DOI: 10.1016/j.ijadhadh.2014.08.001.
- Yokoyama, T.; Nakai, K. Determination of the Impact Tensile Strength of Structural Adhesive Butt Joints with a Modified Split Hopkinson Pressure Bar. Int. J. Adhes. Adhes. 2015, 56, 13–23. DOI: 10.1016/j.ijadhadh.2014.07.011.
- Challita, G.; Othman, R.; Casari, P.; Khalil, K. Experimental Investigation of the Shear Dynamic Behavior of double-lap Adhesively Bonded Joints on a Wide Range of Strain Rates. Int. J. Adhes. Adhes. 2011, 31(3), 146–153. DOI: 10.1016/j.ijadhadh.2010.11.014.
- Araújo, H. A. M.; Machado, J. J. M.; Marques, E. A. S.; da Silva, L. F. M. Dynamic Behavior of Composite Adhesive Joints for the Automotive Industry. Compos. Struct. 2017, 171, 549–561. DOI: 10.1016/j.compstruct.2017.03.071.
- Machado, J. J. M.; Gamarra, P. M. R.; Marques, E. A. S.; da Silva, L. F. M. Improvement in Impact Strength of Composite Joints for the Automotive Industry. Compos. B Eng. 2018, 138, 243–255. DOI: 10.1016/j.compositesb.2017.11.038.
- Dos Reis, M.; Carbas, R.; Marques, E.; da Silva, L. Functionally Graded Adhesive Joints under Impact Loads. Proc. Inst. Mech. Eng. Pt. D J. Automobile Eng. 2021, 235(13), 3270–3281. DOI: 10.1177/09544070211004505.
- Banea, M. D.; Da Silva, L. F. M. The Effect of Temperature on the Mechanical Properties of Adhesive for the Automotive Industry. Proc. Inst. Mech. Eng. Pt. L J. Mater. Des. Appl. 2010, 224(2), 51–62. DOI: 10.1243/14644207JMDA283.
- Sekiguchi, Y.; Yamagata, Y.; Sato, C. Mode I Fracture Energy of Adhesive Joints Bonded with Adhesives with Different Characteristics under quasi-static and Impact Loading. J. Adhes. Soc. Jpn. 2017, 53, 330–337. DOI: 10.11618/adhesion.53.330.
- Ernault, E.; Diani, J.; Schmid, Q. Single-lap Joint Creep Behaviour of Two Soft Adhesives. J. Adhes. Online First version. 2022. DOI: 10.1080/00218464.2022.2100254.
- Yamagata, Y.; Lu, X.; Sekiguchi, Y.; Sato, C. Experimental Investigation of Mode I Fracture Energy of Adhesively Bonded Joints under Impact Loading Conditions. Appl. Adhes. Sci. 2017, 5, 7. DOI: 10.1186/s40563-017-0087-7.
- Jia, Z.; Yuan, G.; Hui, D.; Feng, X.; Zou, Y. Effect of High Strain Rate and Low Temperature on Mode II Fracture Toughness of Ductile Adhesive. Int. J. Adhes. Adhes. 2018, 86, 105–112. DOI: 10.1016/j.ijadhadh.2018.09.003.
- Jia, Z.; Yuan, G.; Feng, X.; Zou, Y.; Yu, J. Shear Properties of Polyurethane Ductile Adhesive at Low Temperatures under High Strain Rate Conditions. Compos. B Eng. 2019, 156, 292–302. DOI: 10.1016/j.compositesb.2018.08.060.
- Kumpenza, C.; Pramreiter, M.; Nenning, T. J.; Bliem, P.; Reiterer, R.; Konnerth, J.; Müller, U. Temperature-related Tensile Modulus of polymer-based Adhesive Films. J. Adhes. 2023, 99(2), 259–276. DOI: 10.1080/00218464.2021.2011239.
- Zhang, L. H.; Yao, X. H.; Zang, S. G.; Han, Q. Temperature and Strain Rate Dependent Tensile Behavior of a Transparent Polyurethane Interlayer. Mater. Des. 2015, 65, 1181–1188. DOI: 10.1016/j.matdes.2014.08.054.
- Jia, Z.; Yuan, G.; Ma, H.; Hui, D.; Lau, K. Tensile Properties of a polymer-based Adhesive at Low Temperature with Different Strain Rates. Compos. B Eng. 2016, 87, 227–232. DOI: 10.1016/j.compositesb.2015.10.013.
- Wang, H.; Deng, X.; Wu, H.; Pi, A.; Li, J.; Huang, F. Investigating the Dynamic Mechanical Behaviors of Polyurea through Experimentation and Modeling. Defence Technol. 2019, 15(6), 875–884. DOI: 10.1016/j.dt.2019.04.016.
- Machado, J. J. M.; Hayashi, A.; Nunes, P. D. P.; Marques, E. A. S.; Carbas, R. J. C.; Sato, C.; Da Silva, L. F. M. Strain Rate Dependence of a Crash Resistant Adhesive as a Function of Temperature for the Automotive Industry. Proc. Inst. Mech. Eng. Pt. L J. Mater. Des. Appl. 2019, 233(11), 2189–2203. DOI: 10.1177/1464420719836914.
- Liao, Z.; Yao, X.; Zhang, L.; Hossain, M.; Wang, J.; Zang, S. Temperature and Strain Rate Dependent Large Tensile Deformation and Tensile Failure Behavior of Transparent Polyurethane at Intermediate Strain Rates. Int. J. Impact Eng. 2019, 129, 152–167. DOI: 10.1016/j.ijimpeng.2019.03.005.
- Roland, C. M.; Twigg, J. N.; Vu, Y.; Mott, P. H. High Strain Rate Mechanical Behavior of Polyurea. Polym. 2007, 48(2), 574–578. DOI: 10.1016/j.polymer.2006.11.051.
- Šebenik, U.; Krajnc, M. Influence of the Soft Segment Length and Content on the Synthesis and Properties of isocyanate-terminated Urethane Prepolymers. Int. J. Adhes. Adhes. 2007, 27(7), 527–535. DOI: 10.1016/j.ijadhadh.2006.10.001.
- Wongsamut, C.; Suwanpreedee, R.; Manuspiya, H. Thermoplastic polyurethane-based Polycarbonate Diol Hot Melt Adhesives: The Effect of hard-soft Segment Ratio on Adhesion Properties. Int. J. Adhes. Adhes. 2020, 102, 102677. DOI: 10.1016/j.ijadhadh.2020.102677.
- McCreath, S.; Boinard, P.; Boinard, E.; Gritter, P.; Liggat, J. J. High Clarity Poly(caprolactone Diol)-based Polyurethane Adhesives for Polycarbonate Lamination: Effect of Isocyanate and chain-extender. Int. J. Adhes. Adhes. 2018, 86, 84–97. DOI: 10.1016/j.ijadhadh.2018.08.003.
- Yi, J.; Boyce, M. C.; Lee, G. F.; Balizer, E. Large Deformation rate-dependent stress–strain Behavior of Polyurea and Polyurethanes. Polym. 2006, 47(1), 319–329. DOI: 10.1016/j.polymer.2005.10.107.
- Somarathna, H. M. C. C.; Raman, S. N.; Mohotti, D.; Mutalib, A. A.; Badri, K. H. Rate Dependent Tensile Behavior of Polyurethane under Varying Strain Rates. Constr. Build. Mater. 2020, 254, 119203. DOI: 10.1016/j.conbuildmat.2020.119203.
- Pan, Z.; Sun, B.; Shim, V. P. W.; Gu, B. Transient Heat Generation and thermo-mechanical Response of Epoxy Resin under Adiabatic Impact Compressions. Int. J. Heat Mass Transfer. 2016, 95, 874–889. DOI: 10.1016/j.ijheatmasstransfer.2015.12.072.
- Delpech, M. C.; Coutinho, F. M. B. Waterborne Anionic Polyurethanes and poly(urethane-urea)s: Influence of the Chain Extender on Mechanical and Adhesive Properties. Polym. Test. 2000, 19(8), 939–952. DOI: 10.1016/S0142-9418(99)00066-5.