ABSTRACT
For maintenance and repair of offshore structures, such as wind turbines, onsite assembly is essential. Currently, secondary elements such as sensors, safety conductor supports, and cathodic protection are welded or screwed to the primary offshore structure, which itself is coated to be protected against maritime stressors such as corrosion induced by sea water. Because of the welding or screwing processes, complex and costly post-treatments are unavoidable for safe operation during the lifetime of the offshore structures. Thus, welding operations for example require the coating to be removed and recoated to provide full corrosion protection. In this study the disadvantages resulting from the state-of-the-art joining processes were addressed in order to be avoided by application of adhesive bonding technology. For this purpose, thermal and mechanical characterisation of two structural two-component (2K) adhesive systems under influence of maritime conditions were carried out. For this purpose, an epoxy adhesive and a methacrylate ester adhesive were analysed. In addition to water absorption and glass transition temperatures, tensile properties as a function of curing were also analysed, as these properties are essential to ensure the reliability and long-term stability of the bond. The adhesive bonds were tested at tensile shear level. Inductive curing of the adhesive was investigated to ensure both adhesive application and removal in a single 30-minute immersion in marine environment. The present work highlights the fundamental challenges of bonding under water in combination with inductive rapid curing of adhesive systems.
1. Introduction
1.1. Bonding of offshore structures
Offshore wind turbines consist of a primary structure that includes the tower, nacelle as well as the rotor blades. Other secondary structures, such as jetties, platforms, cables, and lightning mounts complete the wind turbine and make it operational. For the secondary elements, welding, or mechanical joining techniques such as screwing represent the current state of the art. Regarding the structure’s integrity, it is important to note that the joints are subjected to environmental influences of varying degree.[Citation1,Citation2] As a consequence, offshore structures are divided into different zones, which are defined in the international standard ISO 129,442.[Citation3] In detail, three zones can be distinguished: splash water, water change, as well as submerged zone, with corrosion protection representing the most important challenge in each of them. Maritime coatings[Citation4] as well as cathodic corrosion protection[Citation5] on bare structural steel provide protection against corrosive effects. If secondary elements are welded to the primary structure, component distortion as well as severe coating damages are unavoidable due to the high heat input resulting from the welding process.[Citation6] In addition to the high repair costs, geometric and metallurgical notches may develop, which can weaken the structures fatigue strength.[Citation7,Citation8] To overcome these limitations, adhesive bonding technology appears to be promising as it does not damage the maritime coatings or substrates by excessive temperature development and thus maintains the structures notch class. After studying the realistic environmental conditions in the maritime field, the following criteria are considered for the selection of fully cured adhesives. The service life of typical offshore wind farms is 25 years.[Citation9] An adhesive bond should be able to withstand a 25-year service life. Small reductions in bond strength of the bonded joints are acceptable. These are unavoidable due to the expected environmental influences, such as harsh climatic conditions. Other environmental influences are temperature fluctuations, which can be as much as 10°C or even 30 °C[Citation10] depending on the season. In the last 10 years, maximum temperatures of 60°C have been recorded at the Fino 1 measuring station in the North Sea.[Citation11] Salty air and saltwater pose further challenges to the bonds. Saltwater resistance ranging from 29 PSU (Practical Salinity Units) to 33 PSU[Citation12] and resistance to biological fouling such as algae, mussels and barnacles are required.[Citation13] The UV stability of the adhesives can be neglected due to the untransparent components. Initial creep resistance should be high. The weight of the secondary component must be supported by the adhesive without significant decrease in creep resistance of the bond.
1.2. Underwater bonding
The test standard ISO 9001[Citation14] defines adhesive bonding as a special process, which is very sensitive to environmental influences and therefore must be carried out in a well-controlled environment to guarantee a strong bond according to its specific requirements, i.e. short- and long-term quality of the joint. In addition, both chemical cure of the adhesives[Citation15] and adhesion buildup represent complex, water sensitive processes, which is why outsourcing them near to or below the sea surface represents a major challenge.[Citation16] If underwater bonding is performed, common risks are an adhesive surface with adsorptive bound water molecules as the cornerstone of the bond. The wettability of the adhesive surface by the water layer is severely limited.[Citation16] To increase the wettability of the adhesive surface, usually a steel surface, there are approaches to remove the water from the adhesive surface by process engineering. In such a process step, the water can be removed using the principle of a mussel, suction cups or compressed air.[Citation16] After cleaning, the adhesive can be applied by means of an injection process.[Citation17] Underwater bonding of secondary elements, such as fasteners with a small diameter of 60 mm, is possible. Information on long-term use is limited.[Citation18,Citation19] A multi-stage application of special adhesives is also possible. The adhesives can absorb the water, cure and do not lose their adhesive strength.[Citation20] The study by Li et al. investigated underwater adhesives. Their function is to remove interfacial water and achieve improved cohesion in direct underwater applications. The adhesives use physicochemical properties or functional groups to achieve improved cohesion in direct underwater applications[Citation21] Water displacement by specific hydrophobic coatings or by specific adhesives with reduced surface energy can contribute to this.[Citation22,Citation23] For the marine sector, there are some initial scientific studies on the application of adhesive bonding for repair work in the offshore and marine industries.[Citation24–26] Furthermore, adhesive systems have been synthetised based on the adhesiveness of barnacles, mussels, and supramolecular Velcro to overcome challenges of joining adhesive bonds under water. Nevertheless, these bionic-based systems are still not used commercially in the offshore industry due to high costs.[Citation27,Citation28]
1.3. Rapid curing of adhesives
To reduce the duration of diving operations in underwater bonding, the joints should achieve handling strength quickly. Adhesive systems with a short cure time or the use of rapid curing methods to accelerate the curing reaction of the adhesives are therefore desired. Various rapid curing methods such as microwave, infrared, oven, hot air, UV, and induction curing[Citation29] allow direct or indirect heating of adhesives. In addition to 1-part adhesives, 2-part adhesives can also be accelerated in this way.[Citation30] A UV-curing epoxy resin adhesive has been formulated by the Vienna University of Technology for use in water. When the adhesive is used, a thin layer of water vapor is formed during the curing process due to the heat generated. There is a lack of knowledge about the adhesion of the adhesive to substrate materials.[Citation31] Induction can be used for indirect heating, e.g. of a metallic substrate, or for direct heating of the adhesive, e.g. of metallic fillers in the adhesive.[Citation32,Citation33] Induction for accelerated curing of adhesives in air has been studied extensively and could show shorter process times with at least the same mechanical performance (for construction applications).[Citation34,Citation35]
In Germany, inductive heating of adhesives has been investigated in joint projects such as “NanoMobil” and “Induflex”. These projects are funded by the Federal Ministry of Education and Research BMBF.[Citation36] Until today, however, inductively cured adhesive bonds have hardly been investigated.[Citation37] If insulated inductors can be used under water, this method appears promising for the manufacturing of adhesive bonds in marine environment.
1.4. Scope
Based on the state of the art, the investigation within publication will focus on manufacturing of adhesively bonded joints in artificial seawater environment. For this purpose, the main challenges of bonding in marine environment will be addressed. Firstly, appropriate adhesives must be identified by testing their thermomechanical performance after aging in artificial seawater in a cured state and for curing under marine conditions. Secondly, the curing process in artificial seawater itself will be addressed by investigation of accelerated curing via induction heating. If this process is feasible, it will be possible to produce durable bonded joints regardless of the surrounding water and temperatures. This type of heating will enable rapid and complete curing of adhesives in artificial seawater.
Two structural two-component adhesives were investigated with respect to suitability for the underwater bonding process, as well as for accelerated curing via induction heating. Two different types of adhesives were investigated: firstly, an epoxy-based adhesive (2K-EP) and secondly a methyl methacrylate-based adhesive (2K-MMA). As a representative comparison reference specimens in ambient laboratory conditions with and without inductive accelerated curing were investigated. The terms “under ambient conditions” implied a dry environment. Tests carried out in a humid environment are labelled “in artificial seawater”.
The following tests were used to gain an understanding of adhesives in saltwater environments. In addition to possible changes of thermo-mechanical properties during and after curing in seawater, the application potential of the adhesives was tested on tensile shear tests using mild steel S355 and two epoxy based coated steel surfaces (C1 and C2). In addition, inductively curing of adhesive bonds in a marine environment will be investigated for the first time. The adhesives were inductively cured to determine an economical time window for the immersion work to achieve a handling strength of 1 MPa. The following tests were carried out to investigate the feasibility, also shown in :
- The determination of water absorption of ambient cured and inductively cured adhesive systems (two adhesives) was performed to extend the available data and to identify potential risks for property changes. Water absorption was determined over a defined period according to ISO 62.
- The thermomechanical properties of two adhesive systems were analysed using dynamic mechanical testing (DMA) in accordance with ISO 6721-1. Prior to this, the specimens were partially inductively cured at ambient conditions and in artificial seawater. The glass transition temperatures were analysed and evaluated for different curing and aging scenarios in artificial seawater.
- The strength and ductility of the two adhesives were measured to assess the quality of the adhesives. This was followed by tensile tests on adhesive volume specimens (based on ISO 527). The dog-bone specimens were analysed and evaluated for different curing and aging scenarios in artificial seawater.
- Differential scanning calorimetry (DSC), based on ISO 11,357-2, was added to the tests to determine the progress or degree of cure. These are important for understanding and interpreting the tensile results and are therefore presented after the tensile tests.
- In addition to the substrate specimens, the adhesive bond was also analysed. The tensile shear tests in accordance with ISO 1465 were carried out on blasted steel substrates and coated steel. The aim of the tests was to identify the application potential of the bond. Tensile shear strengths and fracture patterns were recorded and analysed. In addition, the handling strength of the bond was tested by inductively curing at ambient conditions and in artificial seawater for two adhesives.
2. Materials and methods
2.1. Adhesives
The adhesives were selected to comply with different requirements during the curing process and after curing.
The adhesives in the uncured state were subject to the manufacturing requirement of low viscosity to be suitable for an injection process. The adhesives must completely fill the cavity during injection without leaking into the surrounding water. The injection time must be considered due to the limited immersion time of 30 minutes for the whole process. The 30 minute process window is derived from the accident prevention regulation BGV C23.[Citation38]
A thick layer of adhesive is required due to the curved geometry of the primary structure of offshore structures. In practice, the curvature of primary structures varies.[Citation39] A transition piece of an offshore structure can have a diameter of 7 m. For the study, a minimum thick film adhesive[Citation22,Citation40,Citation41] with a minimum 1 mm gap is defined. A bond must be able to compensate such a curvature. Ambient curing temperatures must be considered in offshore applications. Temperatures during the bonding process can range from 10°C to 30°C. At low temperatures the curing times were longer, according to the theory of Arrhenius.[Citation22] The adhesives can be accelerated and cured safely using heat. However, the process must not exceed temperatures of 100°C, being the boiling point of water. When cured, water absorption must be considered. The most important requirement is low water absorption of the adhesive systems. This minimises the risk of property change and ageing.
Based on the state-of-the-art of maritime requirements, the chosen adhesives and their properties are shown in . SikaPower®-1200 (2K-EP) is a structural two-component epoxy resin. The pot life given in the technical data sheet is 45 min at room temperature (RT). The second adhesive is the two-part methacrylate acid ester, Araldite 2051 (2K-MMA). It cures relatively quick with a pot life of 4 to 6 minutes at RT. Both adhesive systems were promising in terms of their ability to absorb water without significantly changing their properties. Adhesive manufacturer Huntsman promotes the use of the system for bonding in water.[Citation42]
Table 1. Overview with basic properties after RT curing from data sheets.[Citation43,Citation44].
2.2. Seawater
All underwater tests were carried out in artificial seawater in accordance with ISO 15,711. The components are listed in the below.
Table 2. Composition of artificial seawater according to ISO 15,711.
2.3. Steel and coatings
The primary structure of an offshore structure is usually made of steel. In most cases, the steel needs to be protected against corrosion by means of protective coatings. Adhesion of the adhesives to the structural steel S355 and the protective coatings must be ensured. The following coatings were considered within this study.
Firstly, Hempadur 35,620 (C1) manufactured by Hempel. Secondly, SikaCor® SW501 (C2) from Sika Deutschland GmbH was selected. Both coatings were double layer epoxy-based systems. gives further information on the layer thickness.
Table 3. Overview of coating systems for S355 steel specimens.
For coating, the steel sheets were cleaned with solvent to remove impurities. After deburring, the steel sheets were cleaned again with methyl ethyl ketone solvent. The steel sheets were blasted. The residues of the blasting material were removed by cleaning the surface. The first coat was applied. After the first coat had dried, a second coat was applied.
The coated sheets are shown in .
2.4. Development of induction parameters for specimens
Two coils were used to achieve uniform inductive heating of the specimens. The air coil for use at ambient conditions has one winding and was located at a greater distance from the tensile shear specimens than the insulated inductor for use in artificial seawater. shows the induction set-up for tensile shear test specimens. For use in water, a powerful coil was required to achieve the desired temperature in the adhesive layer (). This was due to the volume of water and the saltwater medium surrounding the inductor and the specimens. A copper coil with a double winding and a smaller distance to the bonded tensile shear specimens was suitable. The inductors were operated by a TruHeat HF 5010 induction unit manufactured by Trumpf.
Figure 3. Inductors for inductive rapid curing of tensile shear specimens at ambient conditions and in artificial seawater.
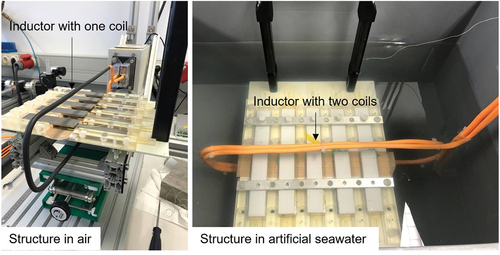
shows the validated induction parameters from the preliminary tests. The induction system used is controlled by Fraunhofer IFAM software. The software contains the slope controller, which allows the time, the desired temperature, and the heating rate to be set. On the other hand, the software also contains a k/α controller, with which the k and α values can be set. The k value determines how smooth the slope of the heating curve should be. The α value specifies the accuracy of the temperature curve through the system. The temperature sensors are also controlled. In the tests a “hottest sensor” was selected to set the maximum temperature. Pmax is the power output of the inductors. The resonant frequency was 129.177 kHz with a total reactive power of 112 kW and an inductor voltage at the resonant frequency of 457 V. At a heating rate of 1 K/s to a defined temperature, the maximum temperature of the adhesive systems, the tensile shear specimens were inductively heated at different holding times. The maximum heating temperature was 80°C for the 2K-EP adhesive and 40°C for the 2K-MMA adhesive. A holding time of 800 seconds for 2K-EP and 120 seconds for 2K-MMA, respectively, represents the induction time to maintain the respective temperatures at ambient conditions and in artificial seawater. In consultation with a diving company, a repair dive should not exceed 30 minutes. During this time the parts to be bonded must be prepared and the adhesive applied. A maximum of 15 minutes was allowed for this. A rapid cure method can then be used. The 800 seconds chosen for the 2K-EP was the maximum time window before the fasteners were removed and the diver emerges. Holding times of less than 800 seconds do not demonstrate the handling strength of the bond and do not allow for safe removal of the fasteners. The situation was different with 2K-MMA. Longer cure times do not provide any benefit in terms of tensile shear strength. As the aim was to keep the bonding process as short and efficient as possible, the tests were set at 120 seconds. Under these conditions, the tensile shear specimens were inductively cured at ambient conditions and in artificial seawater, safely.
Table 4. Validated induction parameters for 2K-EP and 2K-MMA specimens for inductively curing at ambient conditions and in artificial seawater (ISO 15,711) for all methods.
2.5. Water absorption
The reference specimens were cured at ambient conditions. In comparison, a further set of specimens was inductively cured at the target temperatures of 800 seconds at 80°C for the 2K-EP specimens and 120 seconds at 40°C for the 2K-MMA specimens at ambient conditions. Using the heating rates, dwell temperatures, and dwell times determined from the . For water absorption, series of three specimens of 60 × 60× 1 mm3 were fully cured and then aged in artificial seawater for 16 days, shown in .
All specimens were aged in seawater for defined periods. In a first step, the specimens cured without inductive heating were weighed as a benchmark for water absorption. This was followed by measurements at hourly intervals of 2, 6, 24, 96, 192, 216, 384, 720, 1584, 3864, 14808 hours and a final weighing after 19,992 hours. From the results it was possible to determine the hourly weighing cycles up to 384 hours for the water saturation of the adhesive systems. For a representative buffer, the last measurement of the induction cured specimens took place after 720 hours. The time intervals remained constant at 0, 2, 6, 24, 96, 192, 216, 384 and 720 hours. At specified times, the specimens were removed from the water tank, dried, and weighed on a precision balance (±0.01 mg). The specimens were wiped dry once on all sides with a cellulose precision wipe. The specimens were visually dry. The same procedure was followed for each specimen. Specimens preparation and measurements were performed according to ISO 62.[Citation45] A total of n = 3 specimens was under investigation per adhesive.
2.6. Dynamic mechanical analysis
The reference specimens were cured at ambient conditions and in artificial seawater. In comparison, a further set of specimens was inductively cured at the target temperatures of 800 seconds at 80°C for the 2K-EP specimens and 120 seconds at 40°C for the 2K-MMA specimens at ambient conditions and in artificial seawater. Using the heating rates, dwell temperatures, and dwell times determined from the . The induction process was stopped, followed by a cooling period of 30 minutes to room temperature, and then the test was performed. DMA specimens of 18 × 15× 1 mm3 were prepared in silicone moulds at ambient conditions. For specimen preparation in artificial seawater, the adhesive was fixed between two S355 steel sheets lined with Teflon and spaced by 1 mm spacers. For the underwater specimens the water displaced by the adhesives. The cured adhesive was then cut to size. Measurements were conducted according to ISO 6721–1 using a TA Instruments DMA2980 instrument in the single arm bending test. Each measurement was tempered to an initial temperature of −20°C, after a cooling phase at a rate of 5 °C/min. The specimens were then subjected to a sinusoidal stress at a frequency of 1 Hz and an amplitude of 25 µm. After a holding time of 10 minutes, a second heating cycle was performed at a rate of 2 °C/min to a temperature of 200°C. From the resulting storage (G’) and loss moduli (G’’), the glass transition temperature (Tg) was determined at the maximum of the loss factor tan δ (= G’’/G’).
Aged specimens were produced at ambient conditions, partly by inductively curing. After complete curing, they are stored in water, analogous to the water absorption in Chapter 2.5. Aged specimens (Chapter 2.5) were measured in the DMA and compared. The specimens were completely saturated with water due to the long storage in water. The specimens were not redried. A total of n = 1 specimen was under investigation.
2.7. Adhesive bulk specimens
Tensile tests at room temperature were carried out in accordance with ISO 527–1.[Citation46] The test specimens, both at ambient conditions and in artificial seawater, were fixed between two S355 steel sheets lined with Teflon and spaced by 1 mm spacers. In addition to curing at room temperature, the specimens were inductively cured. As in the overall study, the 2K-EP adhesive was inductively cured at 80°C for 800 seconds and the 2K-MMA adhesive was inductively cured at 40°C for 120 seconds. Using the heating rates, dwell temperatures, and dwell times determined from the . All inductively cured specimens were cooled to room temperature for 30 minutes at ambient conditions and then destructively tested. The cured adhesive was then punched out. A lever punch with a cutting die was used to punch out the adhesive. shows the punched specimens. The geometry of tensile test specimens according to 5A from ISO 527–1. To correlate the results with the adhesive thickness of the other specimens, a specimen thickness of 1 mm was used, which deviates from the standard.
A Zwick Z050/TH3A with a 10 kN load cell was used for the tensile tests. The specimens were tested at a rate of 5 mm/min. The gripping length was 50 mm. In addition, the strain of the specimens was recorded using an extensometer. The measuring length of the extensometer was 20 mm. The specimens were tested to failure. The modulus of elasticity was determined at an elongation between 0.05% and 0.25%. A total of n = 5 specimens was under investigation.
2.8. Differential scanning calorimetry
The reference specimens were cured at ambient conditions. In comparison, a further set of specimens was inductively cured at the target temperatures of 800 seconds at 80°C for the 2K-EP specimens and 120 seconds at 40°C for the 2K-MMA specimens at ambient conditions and in artificial seawater. Using the heating rates, dwell temperatures, and dwell times determined from the . All inductively cured specimens were tested at ambient conditions after 30 minutes. The adhesive cooled to room temperature after 30 minutes. Differential scanning calorimetry (DSC) measurements are performed according to DIN EN ISO 11,357–2. The instrument used is a TA Instruments Discovery DSC. The aim of the measurement is to determine the change in reaction enthalpy of the adhesives.
DSC specimens of 18 × 15 * 1 mm3 are prepared in silicone moulds at ambient conditions. For the preparation of specimens in artificial seawater, the adhesive is fixed between two Teflon-coated S355 steel sheets separated by 1 mm thick spacers (analogous to the applied adhesive shown on the left in ). The weight of the specimens is between 1 mg and 5 mg.
The specimens were subjected to two heating cycles. The first heating cycle started at 20 °C/min and finished at 150 °C/min. In the second heating cycle the measurements started at 0 °C/min and finished at 200 °C/min. A total of n = 1 specimen was under investigation.
2.9. Tensile shear specimens
The reference specimens were manufactured for the tensile shear tests without inductively curing at ambient conditions and in artificial seawater. Specimens were manufactured in accordance with DIN EN 1465. Uncoated S355 steel specimens and epoxy coated S355 steel specimens were used as the joining part materials. The joining part combinations must be surface treated prior to joining. The uncoated S355 steel was wiped with MEK and allowed to flash off for 10 minutes. The next step was to sandblast the uncoated steel with corundum F54, cleaned it again with MEK and allowed it to air out. For the epoxy-based coatings C1 and C2, a more neutral surface pre-treatment with the solvent isopropanol follows. The wiped surface was allowed to flash off for 10 minutes. The coating was not roughened prior to bonding. Uncoated steel S355 was bonded to S355, as well as Coating C1 to Coating C1 and Coating C2 to Coating C2.
For fabrication at ambient conditions, the specimens were bonded together in a bonding jig. Two tensile shear test specimens, each with a geometry of 100 × 24.8 * 4 mm3, were bonded with an adhesive thickness of 1 mm. The overlap length was 12.5 mm. Five specimens were produced per combination to allow statistical comparison between specimens.
For artificial seawater curing, the parts to be bonded were cleaned, then manually immersed in artificial seawater. The adhesive was then applied. The second mating part was also immersed in artificial seawater, removed, and adherend to the first mating part using stainless steel spacers after the adhesive layer thickness of one millimetre (1 mm) has been adjusted. The tensile shear test specimens were prepared for storage in artificial seawater as shown in the . An overlap length was set to 12.5 mm.
The specimens with inductively curing were bonded after the reference specimens, see . In comparison, a further set of specimens was inductively cured at the target temperatures of 800 seconds at 80°C for the 2K-EP specimens and 120 seconds at 40°C for the 2K-MMA specimens at ambient conditions and in artificial seawater. Using the heating rates, dwell temperatures, and dwell times determined from the . All inductively cured specimens were tested at ambient conditions after 30 minutes. The adhesive cooled to room temperature after 30 minutes.
Tensile shear specimens were tested under laboratory conditions using a Zwick UTM. This machine can apply a maximum load of 20 kN. The gripping length was 100 mm, and the test speed was 5 mm/min. For tensile shear tests, the artificial seawater and inductively cured specimens were be cooled to RT for 35 minutes prior to destructive testing under laboratory conditions. Each series was tested in a fivefold determination. The fracture pattern was analysed according to ISO 10,365. At the same time, the tensile shear strength of the bonded joint was analysed according to DIN EN 1465. A total of n = 5 specimens was under investigation. The overview of the different tested specimens is shown in .
Table 5. Overview of the different tested specimens.
3. Results
3.1. Development of induction parameters for specimens
The temperature was monitored using type K thermocouples, which were inserted into the adhesive layer and attached to the joining material. The software transmits the temperature program to the induction unit and controls the output of the induction unit. After validation of the induction coils with appropriate tested induction parameters, constant temperature curves were determined for induction at ambient conditions and in artificial seawater. The shows representative temperature curves for two adhesives. The red curves are the measured temperature in the adhesive layer. The blue curves represent the induction power during the heating, holding and cooling phases. The results are plotted against time in seconds. 80°C was successfully maintained for 800 seconds for the 2K-EP and 40°C for 120 seconds for the 2K-MMA. According to the technical data sheets, the adhesive manufacturers and heat tests at higher temperatures resulting in blistering, the temperatures have been identified as the maximum temperatures for the application.
3.2. Water absorption
The relative water content as a function of ageing time in artificial seawater for both adhesives with respective sigmoidal growth fitting function is shown in .
Figure 7. Water content in mass percent for 2K-EP and 2K-MMA, partly inductively cured specimens (abbreviation: ind.).
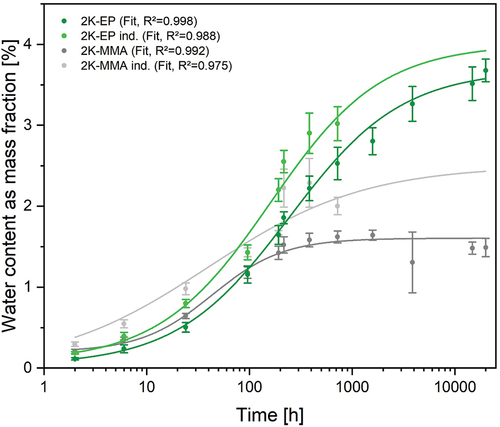
Within the first 16 days of water immersion (384 hours), the 2K-EP cured at ambient conditions absorbed 2.22 ± 0.15 M%. After 19,992 hours (equivalent to 2.3 years) a water absorption of 3.68 ± 0.14 M% was determined. The water absorption of the inductively cured 2K-EP specimens was 2.90 ± 0.25 M% after 384 hours (reference 2.22 ± 0.15 M%) and 3.02 ± 0.21 M% after 720 hours, while the regularly cured reference showed 2.53 ± 0.2 M% after the same period of aging.
For the 2K-MMA specimens cured at ambient conditions, a plateau was reached at around 1.58 ± 0.08 M% (after 384 hours) and the specimens appear to be saturated. Despite continued water storage, the weight decreases. An odour can be detected in the liquid. Analysis of the relative water absorption of the induction cured specimens shown a similar trend to that of the 2K-MMA cured at ambient conditions. After 384 hours there was a plateau in water absorption at 2.22 ± 0.23 M%. After 720 hours, the average value dropped to 2.00 ± 0.1 M%, which was like the water absorption measured after 384 hours.
There was similar water absorption by the adhesives during the first 300 hours. In the first few hours the specimens absorb significantly more water. There is no significant water absorption when comparing 384 hours to 720 hours. Measurement of the inductively cured specimens was therefore discontinued. The fits were used to predict further low water absorption.
3.3. Dynamic mechanical analysis
3.3.1. Non-aged adhesives
In , the results of the DMA tests are shown focussing the elastic and viscous fractions, storage (G’) and loss modulus (G’’), as well as the glass transition temperature (Tg) of both adhesives using dissipation factor tan δ with increasing temperature. The maximum of the dissipation factor (green) indicated the Tg.
Figure 8. DMA results of 2K-EP (a-b) and 2K-MMA adhesive (c-d). Each plot showing both air (solid line) and water (dashed line) as surrounding medium during adhesive cure under the respective curing conditions.
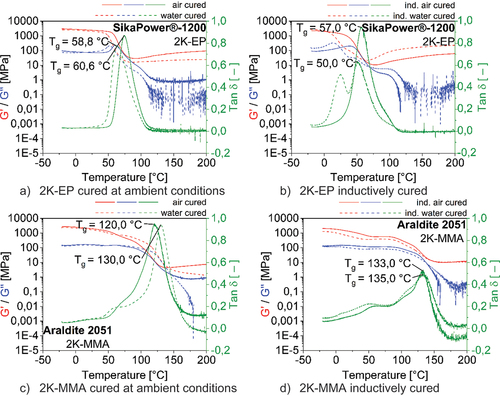
The glass transition temperatures Tg of 2K-EP specimens () cured at ambient conditions were between 58.8°C and 60.7°C. The 2K-EP specimens showed the lowest glass transition temperature after curing in artificial seawater. For the 2K-EP specimens applies: the loss factor curve for induction in water had two prominent points, a loss factor of about 0.5 at 25°C and 0.6 at 54°C. Inductively cured at ambient conditions specimen had a prominent point at 57°C with a dissipation factor of 0.9. The storage modulus showed a high value of 1413.5 MPa in air, the modulus decreases to 281.9 MPa after induction of the specimens in water. The loss modulus decreased only slightly from 160.4 MPa to 145.4 MPa. Induction in artificial seawater reduced the Tg from 57°C to 50°C. The curve around the dissipation factor tan δ has two peaks. The higher peak is assumed to be Tg 50°C. Compared to the references, the glass transition temperatures decreased by 3°C for specimens measured in air and by 8°C for specimens manufactured in artificial seawater. The glass transition temperatures Tg for the inductively cured 2K-MMA specimens at ambient conditions and inductively cured in artificial seawater are highlighted in . The reference measurements were 120.0°C for cured specimens at ambient conditions and 130.0°C cured specimens in artificial seawater. After inductively heating in artificial seawater, the Tg for the 2K-MMA increased by 2°C. For the 2K-MMA, the peak was observed at 133°C with a loss factor of about 0.5 for induction in air and at 135°C with a loss factor of about 0.45 for induction under water. The maximum values of the storage moduli G′ (red) and the loss moduli G′′ (blue) were recorded at a temperature of 25°C. The G′ shows a lower value of 548.5 MPa under water to 1185.1 MPa in air. The G′′ decreases from a value of 138.7 MPa in air to 91.6 MPa inductively cured in artificial seawater.
3.3.2. In artificial seawater aged adhesives
The 2K-EP and 2K-MMA air cured, and inductively cured specimens are shown in the after the DMA. The colour coding and measurements are the same as the test results in the Chapter 3.3. 2K-EP cured at ambient conditions and aged in water (analogue to the water absorption specimens from the Chapter 3.2). At low temperatures of −20°C the storage modulus was 2490 MPa. The loss modulus reached its maximum at 64.27°C with 59.84 MPa (storage modulus here was 2016 MPa). The Tg was 96°C.
Figure 9. DMA results of 2K-EP (a-b) and 2K-MMA adhesive (c-d). Each plot shows air as the surrounding medium during curing of the adhesive under the respective curing conditions and after immersion in artificial seawater until the specimens were saturated with water.
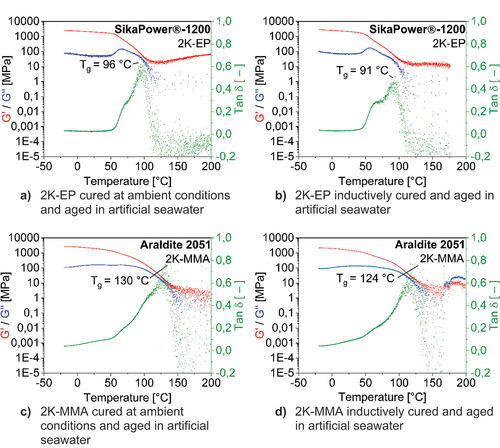
2K-EP specimens inductively cured and ambient conditions cured and aged analogous to the water absorption of the inductively cured specimens had a high storage modulus of 2174 MPa at RT. The peak loss modulus was 177.8 MPa at 57.62°C (storage modulus was 753.3 MPa). The Tg was 91°C. With the highest Tg of 130°C, the specimens cured in air and aged in water showed lower storage moduli. At 28.14°C the storage modulus was 1950 MPa and the loss modulus was 166.9 MPa. Thereafter the loss modulus decreased to 162 MPa at 64.47°C (storage modulus was 917.2 MPa).
The inductively cured and ambient conditions cured 2K-MMA specimens after water saturation showed lower moduli. At 30.29°C the storage modulus was 1454 MPa and the loss modulus was 138 MPa. The loss modulus decreased to 135.5 MPa up to 53.68°C (storage modulus was 860.4 MPa, after which it continued to decrease). The Tg was 124°C.
The large scatter of the dissipation factors in are measurement signal errors in the system. They were therefore not considered in the evaluation.
3.4. Adhesive bulk specimens
3.4.1. 2K-EP
Tensile test results are shown in for specimens cured at ambient conditions without inductive heating (green bar), cured in artificial seawater (blue bar), cured at ambient conditions, and aged in water for 10 days (yellow bar) and the 2K-EP adhesive specimens inductively cured at ambient conditions (light green bar and orange background). The specimens were tested according to the specified procedure and analysed as follows. For the 2K-EP specimens cured at ambient conditions, the maximum tensile strength was 39.6 ± 2.6 MPa when cured at ambient conditions. The modulus of elasticity was 2466 ± 136 MPa for cured specimens at ambient conditions, like that of the specimens aged in artificial seawater (blue bar) at 2422 ± 238 MPa. The elongation at break was reduced by approximately 50% for specimens that have been in contact with water.
Figure 10. Tensile strengths in MPa, modulus of elasticity in MPa and elongation at fracture for the 2K-EP, the inductively cured specimens have an orange background.
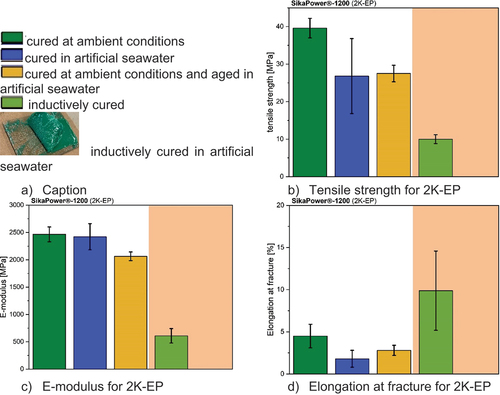
The tensile strength of the specimens inductively cured at ambient conditions was 10.0 ± 1.2 MPa. The Young’s modulus was 608.9 ± 133 MPa and the elongation at break was 9.9 ± 5.7%. No results could be obtained for the specimens inductively cured in artificial seawater because the curing process did not result in a handling strength that would allow the specimens to be demoulded and clamped.
The set temperature can be maintained in artificial seawater with the developed induction setup. This is shown as an example in . Due to the structure of the large adhesive carrier plates from which the dog-bone specimens were fabricated, in combination with a slow curing 2K-EP adhesive system, no handling strength can be achieved for the dog-bone specimen geometry. The specimens are sticky, as shown in the caption of , and cannot be tested. The 2K-EP specimens failed brittle for each curing condition.
3.4.2. 2K-MMA
shows the tensile strengths without and with induction at ambient conditions and in artificial seawater. The colours of the bars correspond to the legend in . Ambient cured specimens are separated from inductively cured specimens by the orange background. The specimens of the 2K-MMA adhesive cured under ambient conditions had a tensile strength (see of approximately 30 ± 2 MPa. shows the Young’s modulus of the 2K-MMA. The modulus was similar at 2028 ± 81 MPa in air and 2025 ± 96 MPa in artificial seawater cured specimens. The elongation at break is shown in . The elongation at break of the air cured specimens and the water aged specimens was 1/3 lower without water storage. Induction under water resulted in a reduction in strength from 11.8 ± 2.6 MPa (shown in air with light green bars) to 5.9 ± 0.5 MPa. The Young’s modulus decreased from 575.9 ± 203 MPa for specimens inductively cured at ambient conditions to 133.1 ± 17 MPa for specimens inductively cured in artificial seawater. Number 5 (inductively cured at ambient conditions) had the lowest modulus of elasticity at 263.7 MPa. The elongation of the specimens inductively cured in artificial seawater was higher. When inductively cured at ambient conditions the elongation was 44.0 ± 46.0% and when inductively cured in artificial seawater this value increased to 107 ± 50%.
Figure 11. Tensile strengths in MPa, modulus of elasticity in MPa and elongation at fracture for the 2K-MMA, the inductively cured specimens have an orange background.
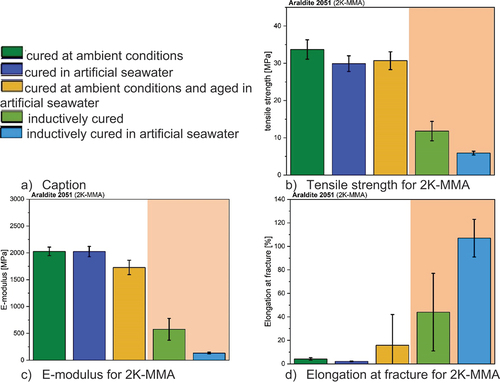
The specimens cured at room temperature proved to be ductile. The ambient cured 2K-MMA specimens failed brittle and ductile in combination with water. The specimens inductively cured at ambient conditions showed a ductile fracture percentage of 40%, a necking fracture percentage of 20% and a shear fracture percentage of the remaining 20%; for the 2K-MMA, the induction showed a brittle fracture percentage of 20%. For the underwater induction, the remaining 80% were ductile fractures.
3.5. Differential scanning calorimetry
3.5.1. 2K-EP
The Differential scanning calorimetry (DSC) results form the basis for the comparison with the fast-curing specimens at ambient conditions and in artificial seawater for the 2K-EP (). The cooling phase, marked in green in the diagram, shows a curve with a peak at 0.7 W/g at a temperature of around 140°C. The first heating phase (green line) shows a trough at −0.9 W/g and a temperature of around 60°C. The black curve shows the second heating phase after cooling. The curve is smooth and has a step. Measurements for specimens with water were not performed.
Figure 12. DSC of 2K-EP specimens after cured at ambient conditions, inductively cured at ambient conditions and in artificial seawater.
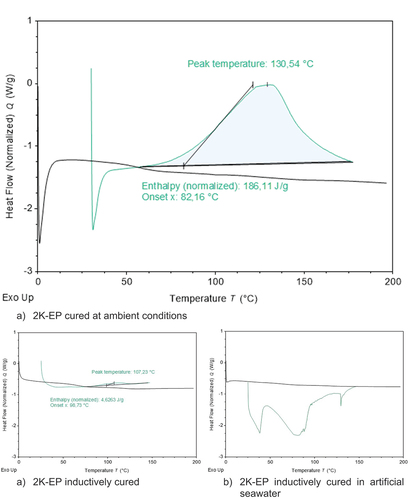
The 2K-EP specimens were inductively cured. The cooling phase showed a peak at 150°C with a value of about 1.25 W/g. The heating phase up to 150°C had its maximum at about 30°C with −0.75 W/g.
shows the heat flow curves for the specimens inductively cured in artificial seawater. The curve represents the normalised heat flow in W/g during the DSC analysis. The first heating phase up to 150°C indicated irregularities. Another characteristic point is at −2.25 W/g at a temperature of 75°C. There is also a deflection at around 35°C with a value of −2.20 W/g. The second heating phase shows a regular curve for both types of inductively cured specimens.
3.5.2. 2K-MMA
For the 2K-MMA adhesive in , the DSC measurement demonstrated a different behaviour. The first heating phase up to 150°C, shown as a blue curve, shows a flattened curve with a low point at about 67°C with a heat flow of about −0.6 W/g. The subsequent cooling phase is shown as a green curve. It peaked at around 136°C. The heat flow was 0.6 W/g. The red curve shows the second heating phase. The red curve represents the second heating phase up to 200°C and shows a regular progression with one step.
Figure 13. DSC of 2K-MMA specimens after cured at ambient conditions, inductively cured at ambient conditions and in artificial seawater.
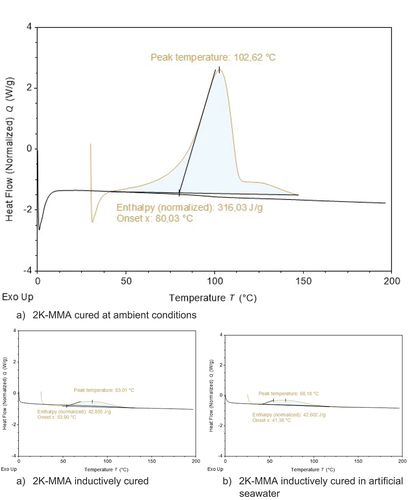
Reference specimens with water were not performed. For the 2K-MMA specimens inductively cured, the maximum heat flow was measured in the cooling phase at 140°C with a value of about 1.4 W/g. No other anomalies were observed. 2K-MMA inductively cured in artificial seawater show a dilution of the water in the specimens (blue line, which is very inconsistent).
3.6. Tensile shear strengths and analysis of fracture surfaces
3.6.1. 2K-EP
The results of the tensile shear tests of the 2K-EP are shown in . The maximum tensile shear strength for the 2K-EP on the steel S355 was 27.5 ± 2,1 MPa for specimens cured. The specimens of this combination failed cohesively. A tensile shear strength of 1 ± 1.2 MPa was achieved after two days of curing the structural steel S1 in artificial seawater. The strength for this specimen correlated with 80% adhesive and 20% cohesive failure. Strengths of approximately 14 MPa to 22 MPa were obtained on coatings C1 and C2 with 20% to 90% coating failure. Depending on the combination, the specimens failed 20% to 80% cohesively. The tensile shear strengths for coating C2 of the reference and induction hardened specimens were in a similar range of 15 MPa to 18 MPa. In addition to the 20% to 35% coating failure, a smaller proportion of 5% to 15% adhesive failure occurs. The remainder failed cohesively. The tensile shear strength of the combination of bare steel inductively hardened in artificial seawater was 10 MPa. 90% of the fracture surface fractions pointed cohesive failure and 10% adhesive failure.
3.6.2. 2K-MMA
The 2K-MMA adhesive references were cured and left at ambient conditions for 24 hours. The inductively cured specimens were heated up to 40°C at a rate of 1 K/s. The temperature of 40°C was maintained for an additional 120 seconds. The results are shown in .The tensile shear strengths for the 2K-MMA reference on bare steel in artificial seawater as well as induction cured have low strengths ranging from 0.5 MPa to 2.5 MPa. The highest tensile shear strength of over 30 MPa was given by the combination references on uncoated steel. 70% of the specimens failed cohesively. The adhesive bond with coating C2 has comparable strengths of 7 MPa to 15 MPa both at RT and induction cured. Coating C2 failure was observed in the specimens cured in artificial seawater without induction. Shown in coating C1 broken at strengths of 18 MPa to 20 MPa.
Figure 16. Tensile shear strengths of specimens prepared at ambient conditions and in artificial seawater for the 2K-MMA specimens, the inductively cured specimens have an orange background.
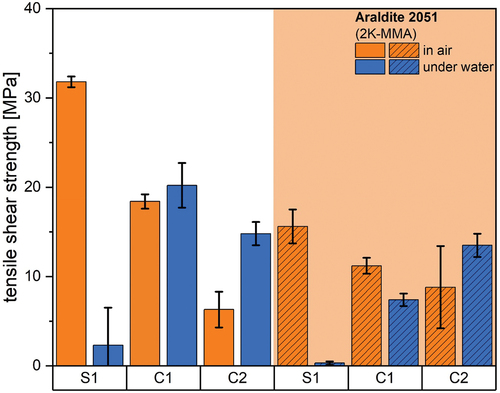
4. Discussion
4.1. Development of induction parameters for specimens
Induction programs of 80°C for 800 seconds for the 2K-EP adhesive and 40°C for 120 seconds for the 2K-MMA adhesive have been successfully validated by many preliminary tests not shown in the publication. There is a strong dependency between the inductor, both the geometry of the inductor and induction performance, and the part material, the part geometry, the adhesive system and the medium (curing under dry conditions and curing in artificial seawater). The indirect inductive heating of the adhesives has been developed and can be used for all the methods, see Chapter 2.5 to 2.9. The authors concluded that the inductively induced temperatures in the adhesive could be developed and maintained continuously, as a constant adhesive layer thickness of 1 mm was set. The phenomenon during the 30 minutes cooling of the adhesive layer up to the destructive tests confirmed the same temperature performance at the position of the thermoelements in the adhesive layer.
4.2. Water absorption
The results for both adhesives, the ambient cured specimens, showed low water absorption of less than 1.5 M% within the first two weeks. The ambient cured 2K-EP specimens reached a saturation of approximately 3.68 M% water after 200 days. The inductively cured 2K-EP specimens absorbed approximately 0.25 M% more water at an early stage of the observed period. However, the water saturation of the inductively cured specimens reached approximately 3 M% between 384 hours and 720 hours. The level of water saturation was considered low by the authors.
The saltwater saturation of 2K-MMA in the environment of the cured specimens was 1.7 M%. After 12 days in artificial seawater, the adhesives no longer appeared to be absorbing the surrounding medium. Even after a long period of 19,992 hours, approximately 2 years, the water content of the test specimens remained almost constant. After this time, a saltwater odour was detected. The adhesive appeared to have released substances into the surrounding water. The adhesive should not be freely accessible in seawater to avoid contamination of the environment. The trend of low water saturation was also evident with an initially higher water absorption of approximately 0.25 M% for the inductive 2K-MMA specimens. Water saturation was reached at 2.22 M% after 384 hours. Although the water absorption of the specimens has increased, it is still within the uncritical range for the application.
Specimens subjected to accelerated curing exhibited higher water absorption compared to cold-cured ones. Although the absorption rate was not significantly higher, it remained within a comparable range. The ambient cured specimens already have natural ambient moisture in the system and therefore absorb water more slowly during aging in artificial seawater, delaying their saturation time. The initial high temperature curing removes the natural ambient moisture from the inductively cured specimens. Water absorption is favoured. This phenomenon has not been a limitation for the use of adhesives in marine applications as water absorption has remained low.
The specific properties of the adhesives have to be considered. It is important, that the water does not degrade the specimens or cause significant changes in material properties. Water absorption by adhesives results in an increase in volume.[Citation22] The more water the adhesive absorbs, the greater the risk of premature failure of the bond. The bond may become plasticised. The less water penetrates the material, the less the properties can be affected. The risk of adverse property change is reduced. Water saturation of less than 4 M% was achieved for all specimens. For marine applications, this means that the properties of the adhesives, such as elasticity, will hardly change at all due to the low level of water absorption.[Citation47] The authors concluded that there is no risk for maritime applications for either adhesive, as the adhesive specimens did not degrade during aging and there were no noticeable changes in properties due to the low water absorption.
4.3. Dynamic mechanical analysis
4.3.1. Non-aged adhesives
The adhesive specimens were analysed, evaluated, and discussed without being aged in water.
Slightly lower glass transition temperatures (Tg) of about 2°C were determined for both the ambient cured 2K-EP specimens and the inductively cured 2K-EP specimens without or with water. The storage modulus at RT of 2K-EP specimens cured at ambient conditions was about 2400 MPa and was high compared to the 2K-MMA specimens cured at ambient conditions.
When cured in artificial seawater, the water might have migrated into the polymer matrix and acted as a plasticiser.[Citation48] The plasticising could affect the glass transition temperature of the specimens manufactured in artificial seawater and lowered the Tg for the 2K-EP. The two peaks in the curve indicate that the 2K-EP has not cured after inductively curing in water. This phenomenon was also observed during the preparation of the bone specimens and is discussed later in the Chapter 4.4. Since at the usual offshore temperatures are about −7°C to + 28°C [10], the determined Tg ranges of about 50 to 61°C are not relevant for the 2K-EP adhesive, and therefore do not restrict the use of this adhesive in the marine environment. The high Tg of around 120°C to 135°C for the 2K MMA specimens, both for the ambient cured and the inductively cured specimens without and with water, was striking. Compared to the reference, the relatively high temperatures of 133°C (inductively cured) and 135°C (inductively cured in artificial seawater) could be due to post-crosslinking due to higher curing temperatures by using induction. The region of glass transition temperatures is not a disadvantage for marine use, as temperatures offshore are approximately 100°C lower than the glass transition temperature. After curing at ambient conditions, the storage modulus was 2024 MPa at RT. After curing in artificial seawater, the storage modulus was 1617 MPa at RT. After induction of the specimens, further reduction in storage modulus was observed in the specimens inductively cured in artificial seawater. The water might have diffused into some specimens during curing and thus created additional space for molecular motion.
At higher curing temperatures, molecular movement was accelerated, resulting in a decrease in storage modulus. Another notable feature was observed in the loss factor curve with a lower peak value for the inductively cured 2K-MMA specimens. The authors estimate that the inductively cured 2K-MMA specimen became more elastic due to water absorption at very high temperatures, which are not of interest for the application. In principle, to resist the effects of waves on a structure, a high degree of elasticity is appropriate.
4.3.2. In artificial seawater aged adhesives
The results after water immersion are discussed by the authors as follows: due to the water absorption of the fully saturated specimens, the adhesives[Citation22] plasticised to varying degrees and the glass transition temperatures had changed.
If specimens are redried, the original level of glass transition temperatures can be recovered. Re-drying was not considered in this work. The authors noted the trend of decreasing glass transition temperatures due to aging for an inductively cured 2K-MMA specimen. Without storage the Tg was 133°C; after aging the Tg was 124°C. The other specimens show an opposite trend. The cross-linking density for the aged specimens was not determined, the suspicion is that the decrease in Tg is due to the lower cross-linking density of the specimen. The literature shows that, depending on the adhesive system and curing scenario, there may well be an increase in the Tg. The Tg depends on the adhesive system, curing process and storage medium and may vary.[Citation49]
The other glass transition temperatures increased because of aging in water. A Tg of 96°C was determined for the 2K-EP specimens cured at ambient conditions and aged in water, and a Tg of 91°C was determined for the inductively cured 2K-EP specimens aging in artificial seawater. However, the glass transition temperatures increased by 20°C compared to the unaged specimens. The cross-linking density must have been higher.
After ambient curing and aging in water, the Tg increased to 130°C compared to the air cured 2K-MMA specimen and solidified compared to the water cured 2K-MMA specimen. The authors concluded that this also indicates a higher cross-linking density and therefore a higher glass transition temperature.
Induction influences both adhesive systems. The glass transition temperatures were still within a non-critical application temperature range. This opinion is independent of specimens cured under ambient conditions and induction cured specimens with aging. The adhesives can be used based on the DMA results.
4.4. Adhesive bulk specimens
The 2K-EP specimens were characterised by high strength and modulus with low elongation at break. The tensile strength was 40 MPa for 2K-EP cured at ambient conditions. Strength and Young’s modulus decreased both after curing and after aging in water. After inductive curing at ambient conditions the strength was 10 MPa. The ductility of the air cured specimens was higher than that of the water cured specimens. The modulus of elasticity of 600 MPa was lower than that of the reference specimens (approx. 2500 MPa). Although the ultimate strength was not reached, the elongation at break was 10%. Elongation at break characterises the deformability of a material. The material becomes more mouldable. The adhesive can have favourable properties to compensate for the stress of the wave impact after the adhesive has fully cured. All specimens failed brittle. The 2K EP specimens were not sufficiently cured by induction in salt water to achieve the handling strength for the test. Temperature measurements at the centre of the inductor showed that the temperature of 80°C was reached in the adhesive layer, as with the other specimens. Test geometry can be inductively cured, but induction/curing time must be extended. This is because 800 seconds is the maximum induction time for the application, otherwise there is not enough time to fix, bond and release the mating parts in a 30-minute immersion. Therefore, no induction was performed for longer than 800 seconds.
When testing the mechanical properties of 2K-MMA, the trend of decreasing tensile strength, modulus and increasing elongation at break after inductively cured of the specimens was also observed. The properties of the adhesive system were different to those of the 2K-EP, as they showed an 85% cure advance in behaviour (see results of DSC measurements). On average, the strengths and moduli were lower than those of 2K-EP. The elongation at break was higher despite higher standard deviations and the 2K-MMA gained in elasticity. Inductively cured specimens at ambient conditions and in artificial seawater can be produced and tested for 2K-MMA adhesive. After high plastic deformation of the specimens during the mechanical tensile test, 40% of the inductively cured specimens and 80% of the induction cured specimens in artificial seawater failed ductile. The reaction rate of the 2K-MMA was higher compared to the 2K-EP. The reaction rate during curing defines the speed of molecular movement. The molecular movement was accelerated by the 40°C. The molecular movement created gaps in the molecular chains due to water absorption, resulting in the elastic behaviour of the specimens. The gaps were not closed during curing because the temperature accelerated the curing reaction and there was not enough time to close all the gaps. This meant that the density of the cross-linking was lower. Strength was greatly reduced and elongation at break was very high.
Considering both adhesive systems for curing under ambient conditions, both at ambient conditions and in combination with artificial seawater, the results show hardly any limitations in use of the adhesive systems for sea water environment. No conclusions can be drawn regarding the use of the inductively cured 2K-EP specimens in marine applications, due to the production problems in artificial seawater.
4.5. Differential scanning calorimetry
The 2K-EP specimens measured without the influence of induction and artificial seawater showed a total enthalpy of reaction of 186.11 J/g. When the 2K-EP was inductively cured at 80°C for 800 seconds, the residual enthalpy of reaction was 4.62 J/g, indicating that the material had reacted almost completely. 2K-EP specimens inductively cured in artificial seawater showed strong endothermic processes during heating, which may have overlapped with the exothermic residual reaction enthalpy. The curing progress was not evident in the results. The specimen’s preparation for the bone specimens in the tensile tests for the 2K-EP after induction in artificial seawater did not allow the specimens to be handled. The specimens were not yet cured at this time.
The total enthalpy of reaction of 316.03 J/g described the 2K-MMA adhesive. After induction at ambient conditions, there was a residual enthalpy of reaction of 42.86 J/g, meaning that the material was approximately 85% fully cured. After induction in artificial seawater, a residual enthalpy of reaction of 42.60 J/g remained, indicating that approximately 85% of the material was fully reacted after induction in water. Therefore, the 2K-MMA appeared to be suitable for accelerated curing even under marine conditions.
4.6. Tensile shear
The aim of the study was to obtain handling strength after a defined period.
The time window is based on the dive duration of the professional diver who will be working in the maritime field in the future. A dive lasts approximately 30 minutes. During this time, the parts to be joined must be fixed, the adhesive applied, and the fixings released.
The holding times of the induction were matched to this. The 1 MPa handling strength was selected to the strength required for the adhesive bond, e.g., to enable the release of fasteners. Subsequent slipping or loosening of the bond must not occur.
Overall, the tensile shear strengths of the 2K-EP were characterised by high average values, regardless of the curing method, with or without the use of induction. For the joints cured in artificial sea water with uncoated S355 steel (S1), acceleration by induction heating resulted in a significant increase in tensile shear strength. The average tensile shear strength of the water cured reference was around 1 MPa and increased to 10 MPa because of inductive rapid curing. The reason for the low strength of the reference was the adsorption of artificial seawater[Citation16] on the uncoated S355 steel. Induction can contribute to the reduction of the previously adsorbed layer of water on the steel by drying at 80°C through the heat input via the metallic joining parts.
The hydrophobic coatings C1 and C2 provided good wettability[Citation22] for the adhesives. As the water only collected on the surface drop by drop, it provided space for the adhesive to bond without a completely waterlogged adhesive surface as a bonding base. As a result, the tensile shear strengths of the combinations of coated S355 steel increased compared to uncoated steel. Tensile shear strength of around 20 MPa was achieved by bonding the coating combinations C1 with C1 and C2 with C2 specimens cured in ambient and artificial seawater. The fracture surfaces correlate with the strength. In some cases, the coating failed instead of the adhesive. That means that in some cases the cohesion of the 2K-EP adhesive was higher than the adhesion of the coating. The handling strength of S1, C1 and C2 could be quickly achieved by induction. The authors concluded that the induction of 2K-EP specimens in combination with the joining partners S1, C1 and C2 can be used for the bonding process in the diving window.
The air cured 2-part MMA adhesives on S1 are suitable for marine applications due to their high tensile shear strength and fracture surface. The chemical curing reaction of the adhesive was faster than expected. The low temperature of 40°C meant that the water in the 2K-MMA adhesive did not evaporate. This situation meant that the adhesion of the 2K-MMA adhesive to the uncoated steel S1 was not improved. During the curing process, the previously adsorbed artificial seawater[Citation16] had little time to evaporate from the S355 steel surface and wet it. An adhesion barrier for the adhesive has been created. The induction temperature was not increased as it cannot be excluded that too high a temperature could damage the adhesive, as stated by the manufacturer. After accelerated curing of the uncoated steel S1 at ambient conditions in artificial seawater and by induction in artificial seawater, the target of 1 MPa for the 2K-MMA specimens was not achieved. It was not possible to achieve a sufficient level of adhesion of the adhesive to the substrate. A future application on uncoated steel cannot be recommended with the adhesive 2K-MMA.
After induction, both at ambient conditions and in artificial seawater, the tensile shear strength of coating C1 was lower than those of the reference. DSC measurements showed that there was a 15% curing gap before the 2K-MMA adhesive was fully cured. It is not surprising that the strength is lower at this point. The handling strength has been achieved. The combination can now be used. The tensile shear strength of coating C2 was at the same level as the reference specimens. During the destructive testing of coating C2, a small area of the coating was found to be cracked. In general, the fracture surfaces correlate with the tensile shear strength of the reference. Low tensile shear strengths correlated with higher rates of adhesive failure and vice versa. Coating limits led to coating failure. For example, the 2K-MMA could have chemically infiltrated the coating. It is possible that outgassing products of low molecular weight from the adhesive had time to diffuse into the coatings C1 and C2 and possibly weaken or damage them. Adhesives have not been analysed for outgassing products in this publication. Irrespective of the adhesive system, the authors estimate that a lack of coating be ruled out before bonding. The coatings did not fail at the edge or in the centre. An assumption regarding curved bonding surface of the substrates due to the geometry of the dried coatings can be ruled out. There was no visual evidence of increased coating thickness at the edge of the coated specimens. The coatings did not dry convexly. Due to the viscosity, curing and multi-layer application of the coatings, these aspects may be an unavoidable disadvantage for adhesion. Further investigation would be required to explain the failure of the coatings. The coated specimens cured in artificial seawater offered advantages for bonding due to their hydrophobic surfaces.[Citation22]
5. Conclusion
After evaluation of all data, the following important findings could be outlined from the results. In order to be able to carry out economic adhesive repair and installation work on offshore structures in splash water, water change and submerged zone[Citation3] by divers, potential adhesives and adhesive bonding to maritime construction materials of maritime use were investigated. A challenge for the adhesive bond is the contact with salt water. The water can cause mechanical and thermal property changes and/or damage the cured adhesive by infiltration, leading to adhesion problems or plasticising effects. This can affect the durability of the bonded joint.[Citation47] One aim of the investigations was to determine the applicability of the adhesives in terms of curing and property profile. In addition to salt water, the ambient temperature is a major challenge for the use of adhesives in maritime applications. The cooler the temperature of the air or seawater, the longer it takes for the adhesives to reach the handling strength of 1 MPa. The curing of the adhesive can be accelerated by high temperatures and cured to handling strength regardless of the ambient temperature. The bond can remain on the primary structure without further processing until final strength is achieved. To accelerate the indirect heating of the adhesives, inductive heating in artificial seawater was investigated for the first time. The aim was to achieve 1 MPa bond handling strength within an immersion time of 30 minutes, regardless of ambient temperature. The property profile is compared with RT cured specimens and analysed for anomalies. At the same time, the tests serve as a benchmark for testing final strength without induction and handling strength after induction. The aim was to identify any changes in the properties of the specimens, such as critical glass transition temperatures or high elasticity, which could hinder the use of the adhesives in the marine sector. For accelerated curing of adhesives to early handling strength, the adhesives have been successfully heated indirectly by induction. Induction may be an innovative rapid curing method for the marine sector in the future, and this publication is the first to investigate it for the marine sector.
Finally, two adhesive systems, 2K-EP, and 2K-MMA, were analysed for the influence of artificial seawater on the uncured and cured adhesives and the bonded joints about their use in maritime applications. Three representative surfaces commonly used in ship-building industries were bonded: uncoated structural steel S355 (S1) and two EP-based coatings C1 and C2 on structural steel S355. Investigations included thermal and mechanical analyses, including water saturation by water absorption over time, DMA, tensile tests, and DSC on ambient and inductively cured specimens at ambient conditions and in artificial seawater. The tests were carried out to determine the glass transition temperatures and the curing progress after inductively curing. Tensile shear tests were performed to determine the adhesion of the adhesives to uncoated and coated steel. Water absorption without and with induction makes both adhesives more elastic. The water saturation of less than 4 M% is not critical for marine applications, as the low water absorption[Citation47] does not significantly change the adhesive properties. The determined glass transition temperatures from minimum 55°C and beyond, do not restrict the use of the non-inductively cured and inductively cured adhesives. The range of application of the adhesives in the maritime field is in the temperature range of 5 to 25°C [11]. 2K-EP specimens exhibited greater tensile brittleness than the more elastic 2K-MMA specimens. The tensile strength of the inductively cured 2K-EP specimens in artificial seawater was low and the adhesive was not resistant to handling. According to the DSC, the 2K-EP showed high enthalpy after evaporation of the water after induction in artificial seawater. The system continued to cure during the measurement. Cure progress was not detectable. No other abnormalities were found in the tensile adhesive bulk specimens. It should also be noted that there is a strong dependency between the inductor and the joining part material, adhesive system, medium (air or water) and part geometry in the controlled induction of tensile shear specimens. With inductive rapid curing, the test objective of a tensile shear strength more than 1 MPa was achieved early within the 30-minute window of the diving process. It is suggested that bonding to uncoated steel S1 with the 2K-MMA should not be used in marine applications, because the reference without rapid curing and the inductive rapid curing specimens for the 2K-MMA on uncoated steel S1 in artificial seawater did not achieve handling strength. On the coated structural steel, the adhesive is optimally applied and fully cured. The conclusion of the tests extends the state of the art by confirmed for the first time the economic potential of inductive rapid curing of adhesives for marine bonding applications.
6. Outlook
Based upon these observations, future studies should deal with the following aspects: Accelerated ageing laboratory tests need to be developed to predict the stability of the bond to match the standards for durability of secondary elements for application offshore. The investigations showed that adhesive bonding is suitable as a joining method for use in saltwater in combination with inductive rapid curing. Induction allows the adhesives to cure at an accelerated rate. By combining adhesive application and inductive heating, it is possible to remove the inductive bonding elements in a single dive. To make representative statements on the long-term stability of adhesive bonds in artificial seawater, specific tests were carried out in addition to the current investigations. The bonded joints were exposed to the weather off Helgoland in the North Sea. They were then subjected to a destructive tensile test to check their strength and durability. These tests provide important information about the suitability of the bonded joints for use in a marine environment. The investigations will be addressed in future publications.
CRediT author statement
Amelie Knape: Conceptualization, Methodology, Investigation, Formal analysis, Validation, Writing – Original Draft, Visualization, Definition of the objectives
Jonas Wirries: Review & Editing
Acknowledgments
Parts of this work were developed as part of the TransHyDE Helgoland project and funded by the Federal Ministry of Education and Research (BMBF). The authors thanks for the support by the company SIKA Technology AG (Zürich, Switzerland) and Huntsman Advanced Materials GmbH (Basel, Switzerland) for delivering the adhesives. Thanks to Muehlhan Deutschland GmbH for the coatings.
Disclosure statement
No potential conflict of interest was reported by the author(s).
Additional information
Funding
References
- Kristiansen, M.; Darula, R.; Endelt, B.; Mikkelstrup, A. F.; Schjødt-Thomsen, J.; Andreasen, J. H.; Farrokhi, F.; Hansen, P. K.; Jensen, P. B. W.; Putnam, E., et al. Improving the Fatigue Life of Large Offshore Foundations. Mar. Struct. 2023, 87, 103314. DOI: 10.1016/j.marstruc.2022.103314.
- Iqbal, M.; Karuppanan, S.; Perumal, V.; Ovinis, M.; Rasul, A. Rehabilitation Techniques for Offshore Tubular Joints. J. Mar. Sci. Eng. 2023, 11(2), 461. DOI: 10.3390/jmse11020461.
- Deutsches Institut für Normung. DIN EN ISO 12944-2: Korrosionsschutz von Stahlbauten durch Beschichtungssysteme. Teil 2: Einteilung der Umgebungsbedingungen; Beuth Verlag GmbH: Berlin, 1998.
- Buchbach, S.; Plagemann, P.; Momber, A. W. Untersuchungen zum Korrosionsschutz von Kanten an Stahlkonstruktionen- Problemstellung und Versuchsdurchführung (Teil 1). Stahlbau 2011, 80, 30–38. DOI: 10.1002/stab.201001389.
- Juhl, M.; Hauschild, M. Z.; Dam-Johansen, K. Sustainability of Corrosion Protection for Offshore Wind Turbine Towers. Prog. Org. Coat. 2024, 186, 107998. DOI: 10.1016/j.porgcoat.2023.107998.
- Lindhorst, L.; Mahrenholtz, O. On the Influence of Wet Underwater Welding on CTOD-δ5. Int. J. Fract. 1999, 97(1/4), 263–277. DOI: 10.1023/A:1018319607081.
- Deutsches Institut für Normung. DIN EN 12063- Spundwandkonstruktionen, 1999.
- Deutsches Institut für Normung. DIN EN 10248-1 - Warmgewalzte Spundbohlen Aus Unlegierten Stählen Teil 1: Technische Lieferbedingungen, Berlin, 1995.
- VGB/BAW-Standard Korrosionsschutz von Offshore-Bauwerken zur Nutzung der Windenergie Teil 1: Allgemeines; VGB Powertech Service GmbH: Essen. 2017. https://hdl.handle.net/20.500.11970/104583.
- Bundesamt für Seeschiffahrt und Hydrologie. Oktober 2009 bis Oktober 2019, Messdaten Fino 1. https://www.fino1.de/de/. (accessed Aug 30, 2021).
- Myslicki, S.; Kordy, H.; Kaufmann, M.; Créac’hcadec, R.; Vallée, T. Under Water Glued Stud Bonding Fasteners for Offshore Structures. Int. J. Adhes. Adhes. 2020, 98, 102533. DOI: 10.1016/j.ijadhadh.2019.102533.
- Buck, B. H.; Buchholz, C. M. The Offshore-Ring: A New System Design for the Open Ocean Aquaculture of Macroalgae. J. Appl. Phycol. 2004, 16, 355–368. DOI: 10.1023/B:JAPH.0000047947.96231.ea.
- Heusinger von Waldegge, T.; Stübing, D.; Zimbelmann, S.; Emde, B.; Hermsdorf, J.; Baumann, M. Underwater Hull Cleaning by Laser-Feasibility and Perspectives. 2022.
- DIN EN ISO 9001:2015-11, Qualitätsmanagementsysteme_- Anforderungen (ISO_9001:2015); Deutsche und Englische Fassung EN_ISO_9001:2015, Beuth Verlag GmbH: Berlin.
- Weitzenböck, J. R., Ed. Adhesives in Marine Engineering : Woodhead Publishing Series in Welding and Other Joining Technologies; Woodhead Publishing: Cambridge, UK, 2012.
- Waite, J. H. Nature’s Underwater Adhesive Specialist. Int. J. Adhes. Adhes. 1987, 7, 9–14. DOI: 10.1016/0143-7496(87)90048-0.
- Fröck, L.; Glück, N.; Flügge, W. Untersuchung des Prozesses zum Unterwasserkleben von Halterungssystemen. Ce/papers 2022, 5(3), 63–76. DOI: 10.1002/cepa.1865.
- Blumentritt, B.; Glück, N.; Flügge, W. Halterungen im Unterwasserbereich klebtechnisch fügen (Teil 1). Adhaes. Kleb. Dicht. 2019, 63(6), 42–47. DOI: 10.1007/s35145-019-0040-y.
- Blumentritt, B.; Glück, N.; Flügge, W. Halterungen im Unterwasserbereich klebtechnisch fügen (Teil 2). Adhaes. Kleb. Dicht 2019, 63(7–8), 42–47. DOI: 10.1007/s35145-019-0045-6.
- MultiMetall Reiner Schulze e. K. Technisches Datenblatt MM-metall UW. PolymerMetall zur Instandsetzung unter Wasser liegender oder feuchter Metalloberflächen, 2013.
- Li, S.; Ma, C.; Hou, B.; Liu, H. Rational Design of Adhesives for Effective Underwater Bonding. Front. Chem. 2022, 10, 1007212. DOI: 10.3389/fchem.2022.1007212.
- Habenicht, G. Kleben: Grundlagen, Technologien, Anwendungen, 6th ed.; Springer: Berlin, 2009.
- Momber, A.; Fröck, L.; Marquardt, T. Nachträgliches Klebtechnisches Fügen von Haltern Auf Bereits Beschichtete Stahloberflächen. Stahlbau 2020, 89(11), 923–931. DOI: 10.1002/stab.202000020.
- Bowditch, M. R.; Clarke, J. D.; Stannard, K. J. The Strength and Durability of Adhesive Joints Made Underwater. In Adhesion 11, Allen, K. W., Ed.; Springer Dordrecht: Netherlands, 1987; pp. 1–16.
- Clarke, J. D.; Sharp, J. V.; Bowditch, M. R. An Underwater Adhesive-Based Repair Method for Offshore Structures. Int. Conf. Struct. Adhes. Eng. 1986, 6 , C152/86x.
- Albiez, M.; Boretzki, J.; Ummenhofer, T. Adhesive Bonding of Secondary Steel Components for Offshore Wind Turbines. Ce/papers 2023, 6(3–4), 959–963. DOI: 10.1002/cepa.2650.
- Ahn, Y.; Jang, Y.; Selvapalam, N.; Yun, G.; Kim, K. Supramolecular Velcro for Reversible Underwater Adhesion. Angew. Chem. (int. Ed. in Engl.) 2013, 52(11), 3140–3144. DOI: 10.1002/anie.201209382.
- Stewart, R. J. Protein-Based Underwater Adhesives and the Prospects for Their Biotechnological Production. Appl. Microbiol. Biotechnol. 2011, 89(1), 27–33. DOI: 10.1007/s00253-010-2913-8.
- Vallée, T.; Adam, M. Inductively Cured Glued-In Rods in Timber Using Curie Particles. Int. J. Adhes. Adhes. 2016, 70, 37–45. DOI: 10.1016/j.ijadhadh.2016.05.005.
- Beiß, T. Vibrationsfügen von duroplastischen Faserverbunden mit abrasiven Schmelzklebstoffen auf Basis von Polyamid 6; Friedrich-Alexander-Universitaet Erlangen-Nuernberg: Nuernberg, 2009.
- Potzmann, P. M.; Lopez Villanueva, F. J.; Liska, R. UV-Initiated Bubble-Free Frontal Polymerization in Aqueous Conditions. Macromolecules 2015, 48, 8738–8745. DOI: 10.1021/acs.macromol.5b02348.
- Maurer, A.; Lammel, C. Schnelles Fügen auch nichtmetallischer Werkstoffe. Adhaes. Kleb. Dicht 2013, 57(11), 24–27. DOI: 10.1365/s35145-013-0433-2.
- Voß, M.; Haupt, J. Accelerated Curing of Adhesively Bonded G-FRP Tube Connections — Part I: Experiments. Compos. Struct. 2021, 268, 113999. DOI: 10.1016/j.compstruct.2021.113999.
- Induction Heating Curing Type Adhesive. 1991.
- Induction Curing Epoxy Resin System. 1990.
- Maurer, A.; Lammel, C.; Beck, M.; Moritzer, E.; Friedrich, N.; Berger, J. Epoxidharzklebstoffe zum Kleben von Kunststoffen. Kunstst. erfolgreich kleben: Grundlagen, Klebstofftechnologien, Best-Pract.-Beispiele; Springer, 2017, 207–222. DOI: 10.1007/978-3-658-18445-2_6.
- Flügge, W. E. A. Steigerung der festigkeit und Dauerhaftigkeit von Stahl-Klebungen im Offshorebereich: final report, 2023.
- Unfallverhütungsvorschrift Taucherarbeiten BGV C23 bisher VBG 39 Berufsgenossenschaftliche Vorschrift für Sicherheit und Gesundheit bei der Arbeit.
- Böttcher, J. Handbuch Offshore-Windenergie; Oldenbourg Wissenschaftsverlag Verlag: Muenchen, 2013. DOI: 10.1524/9783486717761.bm.
- Crocombe, A. D.; Hua, Y. X.; Loh, W. K.; Wahab, M. A.; Ashcroft, I. A. Predicting the Residual Strength for Environmentally Degraded Adhesive Lap Joints. Int. J. Adhes. Adhes. 2006, 26(5), 325–336. DOI: 10.1016/j.ijadhadh.2005.04.003.
- Comyn, J. Diffusion of Water in Adhesives. In Design of Adhesive Joints Under Humid Conditions, Da Silva, L. F. M. Sato, C., Eds.; Springer Berlin Heidelberg: Berlin, Heidelberg, 2013; pp. 1–19.
- Huntsman. MAKE FAST REPAIRS in TOUGH CONDITIONS: ARALDITE® 2051 Adhesive Allows You to Reduce Asset Downtime by Up to 50% with the Power to Bond On-The-Go. https://d1io3yog0oux5.cloudfront.net/_2b58cc120f602b504b3d87b11a97f9c8/huntsman/db/871/10641/pdf/144793_Araldite_2051_flyer_EU_A4_%5B7%5D.pdf. (accessed Dec 18, 2023).
- Huntsman. Technisches Datenblatt Araldite 2051, Zähelastischer Zweikomponenten Klebstoff auf Methacrylsäureesterbasis. 2019.
- Sika. Product Data Sheet Sika-Power1200 Fast Curing, Tough and High Strength Assembly Adhesive. 2016.
- DIN EN ISO 62:2008-05, Kunststoffe_- Bestimmung der Wasseraufnahme (ISO_62:2008); Deutsche Fassung EN_ISO_62:2008, Beuth Verlag GmbH: Berlin.
- DIN EN ISO 527-1:2019-12, Kunststoffe_- Bestimmung der Zugeigenschaften_- Teil_1: Allgemeine Grundsätze (ISO_527-1:2019); Deutsche Fassung EN_ISO_527-1:2019, Beuth Verlag GmbH: Berlin.
- Da Silva, L. F. M.; Sato, C., Eds. Design of Adhesive Joints Under Humid Conditions; Springer Berlin Heidelberg: Berlin, Heidelberg, 2013.
- Habenicht, G. Kleben - erfolgreich und fehlerfrei: Handwerk, Praktiker, Ausbildung, Industrie, 7th ed.; Springer Vieweg: Wiesbaden, 2016.
- Alessi, S.; Conduruta, D.; Pitarresi, G.; Dispenza, C.; Spadaro, G. Accelerated Ageing Due to Moisture Absorption of Thermally Cured Epoxy Resin/Polyethersulphone Blends. Thermal, Mechanical and Morphological Behaviour. Polym. Degrad. Stab. 2011, 96(4), 642–648. DOI: 10.1016/j.polymdegradstab.2010.12.027.