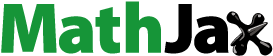
Abstract
In the present experimental study, the critical heat flux (CHF) of an oxidized zircaloy surface and its enhancement were investigated during saturated water pool boiling at atmospheric pressure. Three kinds of zircaloy specimens, oxidized at three different temperature conditions (i.e., 300, 450, and 600 °C), were prepared with a non-treated (i.e., fresh) zircaloy surface. The surfaces of the test specimens were characterized by an energy dispersive spectroscopy analysis, scanning electron microscopy image, and water contact angle measurement. The oxidized surface (OS) specimens increased the CHF, which could be because the oxidized surface improves the surface wettability (i.e., decreases the water contact angle). The OS specimens showed the similar water contact angles, and their CHF values became almost the same. In the present experimental conditions, the water contact angle could be considered as a reasonable parameter to explain the CHF data of test specimens. The CHF enhancement of the OS specimens was about 40%, as compared with the non-treated specimen, and interestingly, it was a comparable value to that of the specially treated zircaloy surfaces of the previous report, for a similar water contact angle condition. This implies that the oxidation process used in this work can be a simple, convenient, and cost-effective way to improve the CHF of the zircaloy surface. Using the present experimental data, the previous CHF correlations were assessed and discussed. Among the correlations tested, Kandlikar model best fitted the present CHF measurement data and enhancement factors.
Keywords:
1. Introduction
Nucleate pool boiling is known to be a very effective mechanism of phase change heat transfer to achieve a much higher heat transfer coefficient than a single phase at a given temperature difference condition. In the nucleate boiling regime, a number of bubbles are produced from the heat-generating surface, and the heat is rapidly transferred by their latent heat transport and local convection enhancement. However, the nucleate boiling regime is limited by a certain heat flux condition, the so-called critical heat flux (CHF). The CHF is a maximum heat flux value to sustain the nucleate boiling regime. After the CHF point, the heated surface is covered with the vapor blanket, and the surrounding liquid is not able to touch the heated surface. In other words, the heat transfer mode changes from nucleate boiling to film boiling. In such a case, it leads to a dramatic decrease in the heat transfer performance and a sudden increase in the surface temperature, and consequently results in a failure of the heater surface. Hence, the CHF enhancement is a key approach to maximize the efficiency and safety of a nuclear power plant.
For a large safety margin and high performance of the nuclear reactor core, investigations on the enhancement of the CHF have been performed and reported extensively using nanofluids [Citation1–8] and surface modification [Citation9–16].
Nanofluids, a dispersion of nanoparticles in water, have been reported to increase the CHF value [Citation1–8]. During the boiling, nanoparticles are deposited on the heater surface, which changes the surface conditions (e.g., morphology, roughness, and wettability). In other words, the surface change caused by the deposition of nanoparticles results in an increase in the CHF. The use of nanofluids could be an easy way to enhance the CHF, but it seems to have a limitation on nuclear core application, since there may be the undesired deposition on the components of nuclear power plant, and the effect of nanoparticles in nuclear reactor is not clear.
For an enhancement of the CHF through the surface modification, various techniques, e.g., anodizing, material coating, etching, and electrophoresis, have been adapted to uniquely modify and fabricate the heater surfaces [Citation9–16]. However, available research works on CHF enhancement using the surface treatment of nuclear fuel cladding material (e.g., zirconium-based alloys) are insufficient and limited. For a pressurized water reactor (PWR), zircaloy has been widely used as a nuclear fuel cladding material for more than three decades because it has a low neutron absorption cross-section and cracking rate. Ahn [Citation17] created and modified the zircaloy surface using the anodizing technique, and investigated the effect of surface modification on the CHF in saturated water pool boiling under atmospheric pressure. They varied the anodizing time, and various specially treated surfaces with micro/nanostructures were obtained. The treated zircaloy surfaces enhanced the CHF performance owing to an improvement of the surface wettability. However, they mentioned that the surface wettability effect cannot fully explain the CHF increase on anodized zircaloy surfaces having a very small contact angle (e.g., below ∼10°). On such surfaces, multi-scaled (i.e., microscaled and nanoscaled) structures were observed, and the liquid spreadability increased. They insisted that the good liquid spreadability contributes to enhancing the CHF further than expected by the surface wettability effect. Stange et al. [Citation18] carried out water pool boiling CHF tests using a zirconium wire under atmospheric pressure. The wire was coated by nanoparticles of 20–30 nm yttria-stabilized zirconia (YSZ), 50 nm titania, and 60–80 nm titanium through the electrophoretic deposition (EPD) technique. Two oxide-coated surfaces (i.e., YSZ and titania) appeared to have higher CHF enhancement than the titanium-coated surface, which may be due to the higher surface wettability of the oxide layers. They reported that the EPD technique can be a practical approach to improve the CHF for nuclear reactor application, as compared with nanofluids, because it does not alter the composition of the water coolant and exhibits more consistent improvement of the CHF. Based on both studies using treated zircaloy and zirconium, the formation of an (structured) oxide layer on the nuclear fuel cladding surface of zircaloy may result in an increase in the CHF. However, considering a practical approach to nuclear reactor application, the techniques [Citation9–18] previously introduced may not be easily applicable to nuclear fuel cladding owing to their complexity and high cost. More convenient and cost-effective processes for CHF-enhanced surfaces, therefore, need to be developed.
In general, the normal and accident operating conditions of a nuclear reactor are under high temperature. In such a case, the nuclear fuel cladding undergoes a surface change, and an oxide layer may be naturally formed [Citation19]. The oxidation phenomenon of the heat transfer surface is frequently observed in most thermal energy systems. However, investigations on the effect of metal oxidation on CHF are insufficient, and the metals used and tested are limited [Citation20–23]: Tachibana et al. [Citation20] reported that an oxide film made out of aluminum can increase the CHF, and believed that a higher CHF is due to the hydrophilicity of the oxide layer with water. Liaw and Dhir [Citation21] carried out a CHF test using a copper surface in saturated water pool boiling at atmospheric pressure. Through the oxidation process of a copper surface in air, the contact angle decreased from 90° to 14°, and a 90% enhancement of the CHF was observed. Coursey and Kim [Citation22] performed CHF tests using a copper heater surface with five different surface oxidation levels. They reported that the oxidized copper surface decreased the water contact angle, and clearly exhibited higher CHF values. The well-oxidized surface enhanced the CHF by about 41%. Recently, Lee and Chang [Citation23] examined a water pool boiling CHF using an SA508 test heater, which is the material of the reactor pressure vessel in a nuclear power plant. They reported that SA508 material showed a higher CHF value, which was due to the change of surface. In other words, on the surface of the test heater, corrosion occurred, which was analyzed to be magnetite (Fe3O4). However, the morphology and material of the oxide layer formed may be dependent on the kind of metal itself, and may differ from each other. Hence, the CHF tests using a variety of oxidized metal surfaces can be a valuable contribution for industrial applications. Furthermore, for a prediction and analysis of the thermal-hydraulic performance in a nuclear reactor core, previous correlations have been used. In such a case, the oxidation effect on the nuclear fuel cladding should be considered. In other words, the previous CHF correlations may be assessed and examined using the experimental results for not a fresh zircaloy surface but an oxidized one. For these reasons, the oxidized zircaloy surface is a good candidate for CHF testing, and the experimental data using the oxidized zircaloy surfaces need to be quantitatively provided.
In this paper, the CHF experiments are carried out using oxidized zircaloy surfaces, and its enhancement is investigated. Three kinds of oxidized zircaloy surfaces are prepared together with a non-treated (i.e., fresh) surface. Their surface characterizations are performed using various methods, such as an energy dispersive spectroscopy (EDS) analysis, scanning electron microscopy (SEM) image, and water contact angle measurement. Then, the CHF performances are tested and discussed, and the previous correlations are compared and assessed based on the experimental data. Our belief is that this work could provide useful information to examine qualitatively the effect of oxidized zircaloy surface on CHF.
2. Description of experiment
2.1. Pool boiling apparatus
In , a schematic diagram of the experimental setup for pool boiling is shown. A glass chamber of 160 mm (L)×50 mm (W)×150 mm (H) was prepared with a Teflon cover, which was placed on a hotplate (WiseStir, MSH-20A). In the Teflon cover, an auxiliary heater, copper electrodes, a reflux condenser, and thermocouples were installed. To provide additional heating, an auxiliary 200 W cartridge heater of 9.525 mm (3/8 inch) diameter was used, and the amount of power was supplied to it using a variable alternating current autotransformer. The hotplate and auxiliary cartridge heater were operated to heat up and maintain the saturated temperature of water. The water temperature was measured by a T-type thermocouple of 3.175 mm (1/8 inch) diameter, and a reflux glass condenser and a temperature controller (JeioTech, RW-1040G) were used to condense the vapor generated from the boiling chamber. The copper electrodes connected to the direct current (DC) power supply (Agilent, N8754A, 20 V×250 A) were mounted on the Teflon cover to support the test assembly. To measure the current accurately through the test specimen, 250 V and 50 mV shunts were installed. All voltages and currents were collected by a data acquisition system (Agilent, 34972A and VEE software). The temperature was monitored by another data acquisition system (Omega, OM-USB-TC).
As the test assembly, an insulation bed of 110 mm (L)×40 mm (W)×15 mm (H), made of Teflon, was used, and a slit of 85 mm (L)×3 mm (W)×0.45 mm (H) was machined along its center. A test specimen of 85 mm (L)×3 mm (W)×0.48 mm (H) in size was prepared using wire cutting method, and then was placed on the slit. Both ends of the test specimen were made to be connected to the copper electrodes to apply DC power. A surface size of 51 mm (L)×3 mm (W) was exposed to water for boiling, where the voltage drop was measured to calculate the heat flux. The remaining part of test specimen was thoroughly insulated using a transparent two-tone epoxy.
2.2. Preparation of test specimens
Four kinds of test specimens were tested. As a non-treated specimen, to remove the contaminants on the surface by wire cutting method, the zircaloy-4 surface was mechanically polished using an ultrafine sandpaper of 2000 grit, and then cleaned thoroughly with methanol and pure water. The oxidized specimens were prepared as follows: non-treated surface specimens were put into a furnace (NITTO KAGAKU, BMINI-1) set to target temperatures of 300, 450, and 600 °C, respectively, and gradually heated up. The averaged heating rate was about 2–2.5 °C/s. The furnace maintained a given temperature condition for 10 min, and then slowly cooled down to about 30 °C. The averaged cooling rate was about 2–3 °C/min. Finally, three kinds of oxidized surfaces were simply obtained. As the targeted temperature, the minimum furnace temperature of 300 °C was determined based on the operating temperature of the reactor in the PWR. On the other hand, the maximum furnace temperature was set to 600 °C because the test specimen treated at a higher temperature was too brittle to be easily handled for the CHF test. In this paper, acronyms are used for the test specimens: NS and OS stand for the non-treated (i.e., fresh) surface and oxidized surface, respectively. The number with OS indicates the setting temperature of the furnace for oxidation. In other words, OS-300, OS-450, and OS-600 are the surfaces oxidized in the furnace at 300, 450, and 600 °C, respectively.
2.3. Details of the CHF test
The experimental procedure of the CHF is described as follows:
Deionized water of around 25 °C was filled in the glass chamber.
The hotplate and auxiliary cartridge heater were turned on, and a heat flux (q″) of about 100 kW/m2 was applied to the test specimen. The heat flux was calculated as follows:
(1)
(1) where Q and A are the heating rate and surface area for boiling, respectively. V and I are the voltage and current measured in the test specimen, respectively. L and W are the length and width of the test specimen for boiling, respectively.
Deionized water was heated to the saturation temperature at atmospheric pressure, and vigorously boiled to remove dissolved gases using a hotplate and auxiliary cartridge heater. The water reached a saturation temperature condition after about 50 min, and boiled additionally for about 40 min. In other words, the total heating time was about 90 min. Then, the power applied to the hotplate and auxiliary cartridge heater was minimized to maintain the saturation temperature of the water.
As shown in , the heat flux of the test specimen increased from 100 kW/m2 using a DC power supply. At q″ ≤ 900 kW/m2, the heat flux of 200 kW/m2 was gradually increased for about 40 s, and the data on the current, voltage, and heat flux were obtained for about 60 s. At q″ > 900 kW/m2, a heat flux of about 10 kW/m2 was carefully increased for about 10 s, and the experimental data were obtained for about 20–30 s.
The CHF was determined through visualization and current measurements [Citation23]. When the CHF occurs, the surface glows visually, as shown in , and the current drastically decreases. After the CHF, the film boiling regime, where the vapor film covers the heater surface, was observed.
The uncertainties of voltage, current, length, and width of boiling surface evaluated were 0.025%, 0.12%, 2.9%, and 4%, respectively. Using Equation (Equation2(2)
(2) ) [Citation24], the uncertainty of the CHF data was estimated, which was within about ±5%.
(2)
(2)
where U is the uncertainty of each measurement parameter.
3. Results and discussion
3.1. Surface characterization
Based on the previous literatures on nanofluids and surface modification [Citation1–18], the characterization and control of the surface conditions are the critical parameters that affect and increase the CHF. In this work, a surface characterization of the test specimens was carried out through an EDS analysis, SEM image, and water contact angle measurement.
The EDS analysis of the test specimens was performed to check the oxide formation on all OS specimens together with the NS specimen, using a scanning microscope (JEOL, JSM-6300). As shown in , for all test specimens, the peaks of zirconium and oxygen elements were detected. In the NS specimen, small amount of oxygen (∼3 wt%) was detected, which might be because of keeping it in air environment. On the other hand, OS specimens contained much more oxygen element (∼20 wt%), as compared with the NS specimen, and the detailed compositions of elements in OS specimens were not much different.
In the surfaces of the specimens tested, the NS specimen had a shiny gray surface. On the other hand, in OS specimens, the surface turned black, and on some parts of the surface, white-like spots appeared. For detailed observations of the test specimens, their SEM (Magellan400) images are displayed in . In the NS specimen, the surface was smooth without any striking featured structures. However, in OS specimens, the surfaces seemed to become uneven and rough due to the white spots produced. On the white spots, cracked morphologies were observed, which might result from the volume expansion induced by the growth of the oxide layer.
Figure 5. Surface image of test specimens (magnification: ×200): (a) NS, (b) OS-300, (c) OS-450, and (d) OS-600.
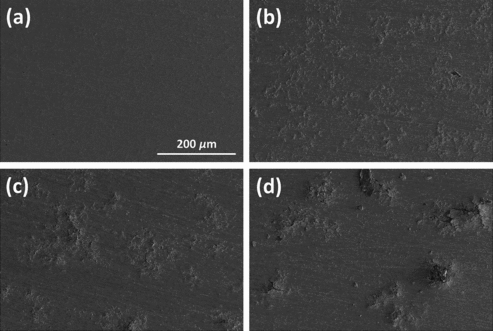
It is known that a hydrophilic surface (i.e., with small water contact angle) may have the advantage of improving the CHF performance [Citation25]. The water contact angles of all specimens were measured using a contact angle analyzer (SEO, Phoenix-300 Touch), as shown in . The water contact angles on each surface were measured three times, and then averaged. The accuracy of contact angle measurement analyzer is ±0.1° in specification, and the error bar in indicates the standard deviation of the measured data for each specimen. The water contact angle of the NS specimen appeared to be about 58°. On the other hand, the OS specimens made the water contact angle much smaller. Once the water droplet contacted such surfaces, it spread out in an instant. The water contact angles on all OS specimens appeared to be around 10°.
3.2. Interpretation of the CHF data
In , the measurement results of the CHF are shown. For all specimens, the CHF measurements were carried out three times, and then averaged. The error bar indicates the standard deviation of the measured data for each specimen, and all repeated tests were performed using the different test specimens. The NS specimen appeared to have a CHF value of about 1280 kW/m2. On the other hand, the OS specimens had much larger CHF values of around 1800 kW/m2, which achieved an enhancement of about 40% based on the averaged measurement values, as compared with the NS specimen. The present experimental results are consistent with previous reports [Citation20–23] in that the oxides on the heater surface can improve the CHF. Based on the previous [Citation20–23] and present experimental results, it was found that the oxide formation on the surface can improve the CHF, which might be due to a decrease in the water contact angle (i.e., increase in surface wettability), as one of the possible reasons. Furthermore, the OS specimens with the similar water contact angles exhibited the similar CHF values. Based on the observations of the CHF and water contact angle in the present experimental ranges, it was revealed that the water contact angle can be one of the good factors to predict and estimate the CHF performance of oxidized zircaloy surfaces.
An increase in the CHF of the OS specimens with small contact angles can be explained by the macrolayer and by hot and dry spot theories.
In the macrolayer theory, it is assumed that the CHF occurs when the macrolayer, which is formed between large mushroom-shaped bubbles and the heated surface, dries out before the mushroom bubbles depart from the surface [Citation5,Citation26]. In , the illustration of the macrolayer concept of Sadasivan et al. [Citation26] is shown. Here, θ, rb, and δmax are the contact angle, bubble radius, and the maximum thickness of liquid layer, respectively. The uniform-sized bubbles are assumed to be uniformly distributed over the heated surface. In the cell of 2rb×2rb, the volume of liquid trapped below the plane of coalescence can be expressed as follows [Citation26]:
(3)
(3)
Figure 8. Illustration of the macrolayer concept of Sadasivan et al. [Citation26]: (a) side-view and (b) top-view.
![Figure 8. Illustration of the macrolayer concept of Sadasivan et al. [Citation26]: (a) side-view and (b) top-view.](/cms/asset/dbf7cc5a-ccbe-4b1c-b3cc-b3bd4acc9c7f/tnst_a_956830_f0008_oc.jpg)
Sadasivan et al. [Citation26] then modeled and calculated the equivalent thickness of the macrolayer (δe), adapting the assumption of the uniform spreading of the trapped liquid over the surface, as shown in the following equation:
(4)
(4)
Meanwhile, according to the macrolayer theory, the following energy balance relation can be obtained [Citation5]:
(5)
(5) where τ, ρf, and ifg are the dry-out time of the macrolayer, liquid density, and latent heat of vaporization, respectively. Sadasivan et al. [Citation26] hypothesize that CHF occurs if the dry-out time of the macrolayer becomes shorter than the hovering time of the mushroom bubbles departed from the surface. Based on the model of Sadasivan et al. [Citation26], a decrease in the contact angle makes the macrolayer thicker for a given vapor bubble size, which can increase the CHF. In other words, OS specimens with smaller contact angles can be predicted to have much thicker equivalent thickness of the macrolayer than the NS specimen with a larger contact angle (i.e., based on Equation (Equation4
(4)
(4) )), which may lead to an increase in the CHF (i.e., based on Equation (Equation5
(5)
(5) )).
In the hot and dry spot theory, the hot and dry spots are developed under a vapor bubble generated from the cavities at a high-heat-flux condition, and a burnout occurs if the rewetting process does not happen upon bubble departure. The improved surface wettability of the OS specimens can contribute to promoting the rewetting process on the heater surface. Theofanous and Dinh [Citation27] proposed an expression of the CHF, i.e., Equation (Equation6(6)
(6) ), using the balance of the evaporation recoil and surface tension forces. They mentioned that the CHF occurs when the evaporation recoil force is larger than the surface tension force.
(6)
(6)
where ρg, σ, and g indicate the vapor density, surface tension, and acceleration due to gravity, respectively. In addition, k is the surface-dependent parameter, which can be given as follows [Citation5]:
(7)
(7)
The parameter of k is derived by a function of the contact angle. Based on Equations (6) and (7), in saturated water pool boiling under atmospheric condition, the CHF is estimated to increase with a decrease in the contact angle, owing to a decrease in the value of k. In summary, the OS specimens may have a thicker macrolayer and promote the rewetting process on the heater surface with hot and dry spots, and consequently lead to enhancing the CHF.
Here, it is quite meaningful to compare the CHF enhancement of the present experimental data with the previous research using the specially treated zircaloy surface [Citation17]. The specially fabricated zircaloy surface using the anodizing technique with a contact angle of around 10° (i.e., with a close water contact angle to the present OS specimens) exhibited a CHF enhancement of around 30%–50% [Citation17]. Interestingly, this is a similar and comparable CHF enhancement value of about 40% achieved in the present OS specimens which were simply and easily treated through oxidation. In other words, the oxidation process used in this work may be a simple, convenient, and cost-effective way to increase the CHF for a practical approach, as compared with complicated and expensive techniques. Even though the oxidation can enhance the CHF performance, it can make test specimen embrittled (i.e., cause the strength problem), as the downside. Therefore, both effects should be properly considered and optimized to apply the oxidation method for CHF enhancement to specific industrial applications.
The present experimental data on the CHF are compared with previous correlations. The assessment of previous correlations using the CHF data of OS specimens, considering the effect of oxidation on the nuclear fuel cladding, may be a worthwhile contribution to predict and examine the thermal performance of a real nuclear reactor core.
Equation (Equation8(8)
(8) ) shows the famous and well-known CHF correlation proposed by Zuber [Citation28], which is based on the hydrodynamic instability theory:
(8)
(8)
In the hydrodynamic instability theory, the CHF phenomenon is governed by the transition of hydrodynamic flow pattern near the heated surface. With an increase in the heat flux, the heated surface becomes occupied by many rising vapor columns, and the liquid flow area to approach down to the heated surface becomes smaller. The flow directions of the vapor columns and liquid jets are opposite. As the heat flux increases further, the rising vapor velocity increases, and the relative velocity between the vapor column and liquid becomes faster. In such a case, the Kelvin–Helmholtz instability occurs in the liquid–vapor interface, and the vapor columns are collapsed. The vapor blanket covers the whole heated surface, and sufficient liquid flows are not able to reach the surface. Finally, the CHF occurs. Zuber [Citation28] model postulates that the flow pattern on a heated surface is a square array of vapor jets leaving the heated surface with the pitch equal to the fastest growing Taylor instability wavelength. In addition, the volumetric flux of rising vapor jet from the surface is assumed to be limited by the Helmholtz instability of interaction between the neighboring vapor jets. If the liquid is at the saturation temperature condition, and all vapor jets are generated from the heated surface, Zuber [Citation28] correlation of Equation (Equation8(8)
(8) ) can be derived.
Moissis and Berenson [Citation29] took account of the lateral interaction of the vapor columns and Taylor–Helmholtz instability at the interface between the vapor flow columns and liquid flow. They proposed the CHF correlation of Equation (Equation9(9)
(9) ) based on the hydrodynamic instability theory [Citation17]:
(9)
(9)
Kandlikar [Citation30] proposed the CHF correlation considering the heated surface condition through adapting the contact angle as an important parameter. He developed the theoretical model of Equation (10) using the balance of the recoil force and the surface tension on the heated surface. He mentioned that evaporation at the liquid–vapor interface of a bubble induces a parallel force to the heated surface, which is an essential factor to determine the CHF. When this force exceeds the retaining forces (e.g., from gravity and surface tension), the vapor in the bubble spreads over the heated surface, and consequently, the CHF can be initiated.
(10)
(10) where β and φ are the receding contact angle and surface inclination angle, respectively.
Another CHF correlation considering the effect of the contact angle, proposed by Kirichenko and Chernyakov [Citation31], is as follows:
(11)
(11)
Kirichenko and Chernyakov [Citation31] mention that their correlation is in close agreement with the experimental data for water within the range of 20° ≤ θ ≤ 60°.
shows a comparison of the measured CHF data with the previous correlations. Zuber [Citation28] and Moissis and Berenson [Citation29] correlations, developed based on the hydrodynamic instability theory, predicted the CHF values of all specimens to be the same, because they do not take into account the heater surface condition (e.g., the contact angle). The present experimental data decreased with an increase in the contact angle, and this trend was consistent with the previous correlations considering the contact angle, proposed by Kim et al. [Citation5], Theofanous and Dinh [Citation27], Kandlikar [Citation30], and Kirichenko and Chernyakov [Citation31]. Theofanous and Dinh [Citation27] and Kim et al. [Citation5] correlations over-predicted the measurement data, which might be due to the surface-dependent parameter (k) of Equation (Equation7(7)
(7) ). It was obtained from the elementary geometry and Lord Rayleigh's formula for the volume of a static liquid meniscus [Citation5,Citation32], which might be improved and modified for better prediction of the CHF. In the Kirichenko and Chernyakov [Citation31] correlation, the range of 20° ≤ θ ≤ 60°, which was recommended for applying their correlation, was expressed by the solid line. The Kirichenko and Chernyakov [Citation31] correlation seemed to also over-predict the averaged measurement values. Their correlation has some limitations [Citation31]: the predicted CHF value becomes infinite as the contact angle approaches 0°. They mentioned that this could be because the Fritz [Citation31,Citation33] formula does not apply to the bubble departure diameter in the case of small contact angles. In addition, they pointed out that the constant value of 0.171 in Equation (11) is somewhat too high, which can be modified more accurately with a sufficient amount of experimental data on the bubble departure diameter of bubble and CHF as a function of contact angle. On the other hand, the Kandlikar [Citation30] correlation estimated well the averaged CHF values as well as the general trend of the CHF, which could be because his theoretical approach is reasonable and reflects well the real CHF phenomena in the present experimental conditions.
In , the CHF enhancement factors (i.e., η = q″CHF,OS/q″CHF,NS) evaluated from the averaged CHF measurement data are compared with previous correlations considering the contact angle. The correlations of Kim et al. [Citation5] and Theofanous and Dinh [Citation27] appeared to have poor accuracy in terms of the averaged CHF measurement values of the test specimens, as shown in , but they predicted well the CHF enhancement factors. This may imply that the hot and dry spot theory is a reasonable approach to describe the CHF improvement of OS specimens, as mentioned earlier. Based on and , in the present experimental range, the Kandlikar [Citation30] correlation best fitted the averaged measurement values of both the CHF data () and enhancement factors () in the previous correlations tested in this work.
The nuclear fuel cladding surface could be influenced by the environmental conditions such as temperature, pressure, and medium (e.g., water, air, and steam). The nuclear fuel cladding surface under the operating condition of a real nuclear reactor may not be the same as the test specimens treated in this work. Also, the surface wettability is known to be changed by the surrounding condition [Citation34]. Hence, the CHF behaviors of nuclear fuel cladding under the real operating condition differ from those under the atmospheric pressure condition. For accurate prediction and clear understating of the CHF under the real operation condition, further investigations on relations of contact angle, bubble dynamics (e.g., bubble departure frequency and diameter), active nucleation site density, nuclear fuel cladding material, and CHF under high-temperature and high-pressure conditions should be performed.
4. Conclusions
In this paper, the effect of oxidation on the CHF and its enhancement were investigated using three kinds of oxidized zircaloy surfaces together with a non-treated surface.
The OS specimens were observed to increase the CHF. This could be because the oxidized surface improves the surface wettability (i.e., decreases the water contact angle), which might lead to a thicker liquid macrolayer and promote the rewetting process on the heated surface with hot and dry spots. The CHF enhancement of the OS specimens appeared to be about 40% based on the averaged measurement values, as compared with the NS specimen. The OS specimens showed the similar water contact angles, which leaded to the similar CHF values. Interestingly, the simply obtained OS specimens exhibited a comparable CHF enhancement with the specially treated zircaloy surfaces reported previously for similar contact angle conditions. This means that the oxidation process used in this work can be a simple, convenient, and cost-effective method to increase the CHF of the zircaloy surface. Among the previous CHF correlations examined, the Kandlikar correlation, considering the contact angle effect, best fitted the averaged measurement values of the CHF and enhancement factors. Based on the present observations of the CHF and water contact angle, it was found that the water contact angle can be one of the good parameters to predict and evaluate the CHF performance of oxidized zircaloy surfaces.
Nomenclature
A | = | surface area (m2) |
g | = | acceleration due to gravity ( = 9.81 m/s2) |
H | = | height of test specimen (m) |
I | = | current (A) |
i | = | latent heat of vaporization (J/kg) |
k | = | surface-dependent parameter (−) |
L | = | length of test specimen (m) |
W | = | width of test specimen (m) |
Q | = | heating rate (W) |
q″ | = | heat flux (W/m2) |
r | = | bubble radius (m) |
t | = | time (s) |
U | = | uncertainty of measurement parameter |
V | = | voltage (V) |
Vol | = | volume (m3) |
Greek letters
β | = | receding contact angle (° or radian) |
δ | = | thickness of macrolayer (m) |
η | = | enhancement factor (−) |
θ | = | contact angle (° or radian) |
ρ | = | density (kg/m3) |
σ | = | surface tension (N/m) |
φ | = | surface inclination angle (° or radian) |
Subscripts
b | = | bubble |
CHF | = | critical heat flux |
e | = | equivalent |
f | = | liquid |
fg | = | liquid–vapor |
g | = | vapor |
I | = | current |
K | = | Kandlikar [Citation30] correlation |
K&C | = | Kirichenko and Chernyakov [Citation31] correlation |
L | = | length of test specimen |
M&B | = | Moissis and Berenson [Citation29] correlation |
max | = | maximum |
NS | = | NS specimen |
OS | = | OS specimen |
q″CHF | = | critical heat flux |
T&D | = | Theofanous and Dinh [Citation27] correlation |
V | = | voltage |
W | = | width of test specimen |
Z | = | Zuber [Citation28] correlation |
Additional information
Funding
References
- You SM, Kim JH, Kim KH. Effect of nanoparticles on critical heat flux of water in pool boiling heat transfer. Appl Phys Lett. 2003;83:3374–3376.
- Bang IC, Chang SH. Boiling heat transfer performance and phenomena of Al2O3–water nano-fluids from a plain surface in a pool. Int J Heat Mass Transfer. 2005;48:2407–2419.
- Kim H, Kim J, Kim MH. Effect of nanoparticles on CHF enhancement in pool boiling of nano-fluids. Int J Heat Mass Transfer. 2006;49:5070–5074.
- Kim HD, Kim J, Kim MH. Experimental studies on CHF characteristics of nano-fluids at pool boiling. Int J Multiphase Flow. 2007;33:691–706.
- Kim SJ, Bang IC, Buongiorno J. Surface wettability change during pool boiling of nanofluids and its effect on critical heat flux. Int J Heat Mass Transfer. 2007;50:4105–4116.
- Kwark SM, Kumar R, Moreno G, Yoo J, You SM. Pool boiling characteristics of low concentration nanofluids. Int J Heat Mass Transfer. 2010;53:972–981.
- Vazquez DM, Kumar R. Surface effects of ribbon heaters on critical heat flux in nanofluid pool boiling. Int Commun Heat Mass. 2013;41:1–9.
- Lee JH, Lee T, Jeong YH. The effect of pressure on the critical heat flux in water-based nanofluids containing Al2O3 and Fe3O4 nanoparticles. Int J Heat Mass Transfer. 2013;61:432–438.
- Chang JY, You SM. Boiling heat transfer phenomena from microporous and porous surfaces in saturated FC-72. Int J Heat Mass Transfer. 1997;40:4437–4447.
- Wei JJ, Honda H. Effects of fin geometry on boiling heat transfer from silicon chips with micro-pin-fins immersed in FC-72. Int J Heat Mass Transfer. 2003;46:4059–4070.
- Arik M, Bar-Cohen A, You SM. Enhancement of pool boiling critical heat flux in dielectric liquids by microporous coatings. Int J Heat Mass Transfer. 2007;50:997–1009.
- Ujereh S, Fisher T, Mudawar I. Effects of carbon nanotube arrays on nucleate pool boiling. Int J Heat Mass Transfer. 2007;50:4023–4038.
- Chen R, Lu MC, Srinivasan V, Wang Z, Cho HH, Majumdar A. Nanowires for enhanced boiling heat transfer. Nano Lett. 2009;9:548–553.
- Forrest E, Williamson E, Buongiorno J, Hu LW, Rubner M, Cohen R. Augmentation of nucleate boiling heat transfer and critical heat flux using nanoparticle thin-film coatings. Int J Heat Mass Transfer. 2010;53:58–67.
- Stutz B, Morceli CHS, Silva MDFD, Cioulachtjian S, Bonjour J. Influence of nanoparticle surface coating on pool boiling. Exp Therm Fluid Sci. 2011;35:1239–1249.
- Saeidi D, Alemrajabi AA. Experimental investigation of pool boiling heat transfer and critical heat flux of nanostructured surfaces. Int J Heat Mass Transfer. 2013;60:440–449.
- Ahn HS.. Study of CHF phenomenon on micro and nano structures [PhD thesis]. Pohang: Pohang University of Science and Technology; 2011.
- Stange G, Yeom H, Semerau B, Sridharan K, Corradini M. A study of nanoparticle surface modification effects on pool boiling critical heat flux. Nucl Technol. 2013;182:286–301.
- Moya JS, Diaz M, Bartolome JF, Roman E, Sacedon JL, Izquierdo J. Zirconium oxide film formation on zircaloy by water corrosion. Acta Mater. 2000;48:4749–4754.
- Tachibana F, Akiyama M, Kawamura H. Non-hydrodynamic aspects of pool boiling burnout. J Nucl Sci Technol. 1967;4:121–130.
- Liaw SP, Dhir VK. Void fraction measurements during saturated pool boiling of water on partially wetted vertical surfaces. J Heat Trans-T ASME. 1989;111:731–738.
- Coursey JS, Kim J. Nanofluid boiling: the effect of surface wettability. Int J Heat Fluid Flow. 2008;29:1577–1585.
- Lee J, Chang SH. An experimental study on CHF in pool boiling system with SA508 test heater under atmospheric pressure. Nucl Eng Des. 2012;250:720–724.
- Holman JP. Experimental methods for engineers. 7th ed. New York (NY): McGraw-Hill; 2001.
- Malla S, Amaya M, You SM. Experimental study of pool boiling heat transfer in water from hydrophilic and hydrophobic surfaces. 8th International Conference on Multiphase Flow (ICMF2013); 2013; Jeju, Republic of Korea.
- Sadasivan P, Chappidi PR, Unal C, Nelson RA. Possible mechanisms of macrolayer formation. Int Commun Heat Mass. 1992;19:801–815.
- Theofanous TG, Dinh TN. High heat flux boiling and burnout as microphysical phenomena: mounting evidence and opportunities. Multiphase Sci Technol. 2006:18:251–276.
- Zuber N. Hydrodynamic aspects of boiling heat transfer [PhD thesis]. Los Angeles (CA): University of California; 1959.
- Moissis R, Berenson PJ. On the hydrodynamic transitions in nucleate boiling. J Heat Trans-T ASME. 1963;85:221–226.
- Kandlikar SG. A theoretical model to predict pool boiling CHF incorporating effects of contact angle and orientation. J Heat Trans-T ASME. 2001;123:1071–1079.
- Kirichenko YA, Chernyakov PS. Determination of the first critical thermal flux on flat heaters. J Eng Phys Thermophys. 1971;20:699–703.
- Gupta SV. Capillary action in narrow and wide tubes – a unified approach. Metrologia. 2004;41:361–364.
- Kutateladze SS. [Fundamentals of heat transfer theory]. Mashgiz; 1962. Russian.
- Bernardin JD, Mudawar I, Walsh CB, Franses EI. Contact angle temperature dependence for water droplets on practical aluminum surfaces. Int J Heat Mass Transfer. 1997;40:1017–1033.