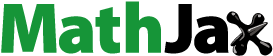
Abstract
In boiling water reactor (BWR) plants, cobalt-60 (60Co) is the main source of radiation exposure, and it builds up on oxide films of structural materials. The 60Co buildup is caused by its incorporation into the oxide films. In the BWR plants using hydrogen water chemistry (HWC) to mitigate the oxidative environment, Zn injection has been applied to reduce the 60Co incorporation. In this work, we studied the incorporation mechanism of 60Co into the oxide films on type 316 stainless steel and the suppression mechanism of 60Co incorporation. In order to discriminate between coprecipitation and adsorption of 60Co incorporation under HWC conditions, we measured the corrosion amount of the base metal and the 60Co buildup amount, using simultaneous continuous measurements for 500 h. The 60Co incorporation increased with time both with and without Zn injections. We found that the time dependencies of 60Co incorporation with and without Zn have one and two regions, respectively. In the initial stage for both, 60Co was incorporated mainly by coprecipitation. After 100 h without Zn, 60Co was incorporated by both coprecipitation and adsorption. These results mean that Zn suppressed both coprecipitation and adsorption of 60Co.
1. Introduction
In boiling water reactor (BWR) plants, corrosion products are released from structural materials into the reactor water and transported to in-core regions. These corrosion products become radioactive species by neutron exposure. Then these species are redissolved as radioactive ions or released as radioactive crud into the reactor water. Most of the ions and crud redeposit on the fuel cladding surface. However, some of the ions and crud reach the surface of the primary loop re-circulation system (PLR) piping and other reactor components. The oxide films incorporating the radioactive species grow on the surface of the components, and so become a radiation source [Citation1]. Since cobalt-60 (60Co) is the main radioactive nuclide associated with this radiation source, some research groups have been developing countermeasure technologies for the 60Co buildup on the surface of the components and have been studying the mechanisms of 60Co incorporation into the oxide films [Citation2–7].
In many aging BWR plants, hydrogen water chemistry (HWC) [Citation8] and noble metal chemical addition [Citation9] into reactor water are used to mitigate the oxidative environment of the plants to suppress stress corrosion cracking (SCC) of the structural materials. In these plants that apply such SCC mitigation technologies, zinc (Zn) injection is essentially applied to suppress 60Co incorporation into the oxide films on the surface of the components which are made of stainless steel, e.g. the PLR piping [Citation3]. In the corrosion of stainless steel, metal ions elute from the base metal and diffuse through the oxide films. The reported effect of Zn is stabilization of the oxide films to suppress the diffusion of metal ions. Therefore, Zn injection decreases the oxide film amount and lowers the 60Co concentration in the oxide films formed on stainless steel [Citation4,5].
According to previous reports [Citation1,Citation10], the 60Co buildup consists of two processes: coprecipitation and adsorption. In coprecipitation, 60Co and Fe ions coprecipitate to form oxide films. In adsorption, 60Co is adsorbed on the formed oxide films. In the coprecipitation process, the 60Co buildup amount is proportional to the corrosion amount of the base metal. In the adsorption process, the 60Co buildup behavior is assumed to depend on the corrosion behavior of the base metal, but details are unclear.
In order to suppress the 60Co incorporation by Zn injection more effectively, we studied the mechanisms of the 60Co incorporation into the oxide films on type 316 stainless steel (316 SS) which is used for the PLR piping and of the 60Co incorporation suppressed by Zn injection. In order to discriminate between coprecipitation and adsorption of 60Co incorporation under the conditions simulating HWC, we measured the corrosion amount of the base metal and the 60Co buildup amount, using simultaneous continuous measurements consisting of the potential drop method (PDM) and a NaI γ-ray detector, respectively. The formed oxide films were analyzed with a scanning electron microscope (SEM).
2. Experimental procedure
2.1. Immersion test
2.1.1. Apparatus and water chemistry conditions
A schematic drawing of the immersion test apparatus is shown in .
In order to simulate HWC, as shown in , demineralized water with an electrical conductivity (EC) of <10 μS m−1 at 298 K was stored in a reservoir tank, and H2 and N2 gases were bubbled into this water to keep their concentrations at the desired levels of under 5 μg kg−1 for dissolved oxygen and 50 μg kg−1 for dissolved hydrogen. 60Co (activity: 6.7 Bq kg−1), cobalt sulfate (cobalt ion concentration: 0.1 μg kg−1) and zinc nitrate (zinc ion concentration: 0, 5 μg kg−1) were added before reaching the test section. The tests carried out under the conditions of Zn = 0 μg kg−1 and Zn = 5 μg kg−1 are described as “without Zn” and “in the presence of Zn”, respectively. In the test section, simulated reactor conditions of high water temperature and pressure (553 K, 7.8 MPa) were used.
Table 1. Water chemistry conditions.
The PDM part and the NaI γ-ray detector (51B51/2, Scionix Holland) were installed in the test section of the apparatus to allow simultaneous and continuous measurements of the corrosion amount and the 60Co buildup amount. The test pieces (T.P.s) part was also installed in the test section.
2.1.2. Continuous measurements of corrosion amount
The corrosion amount of 316 SS was measured by PDM, which can continuously evaluate the corrosion amount using electrical resistance measurements. Details of PDM have been described elsewhere [Citation11]. In this work, “corrosion amount” means the decreased amount of the base metal due to oxidation and elution.
The relationship between the corrosion amount (Δr (μm)) and the change of resistance of the test wire is represented by the following equation:
(1)
(1)
Here, r0 (μm) is the initial radius of the test wire, R0 (Ω) is the resistance of the test wire at 0 h and Rt (Ω) is the resistance of the test wire at t (h). Equation (1) shows that Δr can be obtained from the measurement of Rt.
A schematic drawing of the PDM part is shown in . In order to measure the corrosion amount, 316 SS fine wire (ϕ50 ± 5 μm × 180 mm) was used as test wire. Lead wires of 316 SS (ϕ0.5 mm) were silver-soldered to both ends of the test wire. The connected lead wires were insulated with polytetrafluoroethylene (PTFE) heat-shrink tube to avoid contact with water. A 316 SS tube was polished with 600-grit emery paper and used as a test tube. The test wire and test tube were degreased in a 10-minute ultrasonication with acetone. The test wire was fixed coaxially in the test tube. The lead wires were extracted from the PDM part and connected to a DC source meter (2400, Keithley Inc.) and a low voltage meter (2812A, Keithley Inc.).
The resistance of the test wire was continuously measured by PDM under the conditions shown in . Resistivity of the test wire was calculated, supposing that the diameter of the test wire was 50 μm at 0 h. The resistance of the test wire measured by PDM was converted to the corrosion amount via Equation (1).
Table 2. Parameters of PDM system.
2.1.3. Continuous measurements of 60Co buildup amount
The NaI γ-ray detector was located outside the test tube in the PDM part, and the γ-rays radiated from the 60Co buildup on the inner surface of the test tube which had an energy of 1.3325 MeV were counted. The 60Co counts were collected for 10 h intervals.
The T.P. was used as a reference to convert the counts, which were obtained by the NaI detector, to the 60Co buildup amount. A schematic drawing of the T.P. part is shown in . 316 SS T.P.s (surface area, 8 mm × 15 mm; thickness, 1.5 mm) were polished with 600-grit emery paper, and degreased with acetone, and installed in the T.P. part. The 60Co buildup amounts on the T.P.s were measured with a Ge γ-ray detector (GEM-15190-P, Seiko EG&G Co. Ltd.) with a multichannel pulse height analyzer (MCA7600, Seiko EG&G Co. Ltd.).
Assuming that the 60Co buildup amounts on the test tube used with the PDM and the reference T.P. agreed with each other, we calculated the amount of 60Co buildup on the test tube using the following equation:
(2)
(2)
Here, Γmea (kBq m−2) is the 60Co buildup on the inner surface of the test tube at t, Γ500 (kBq m−2) is the 60Co buildup on the surface of the T.P. at 500 h, and Ct and C500 are the γ-ray counts at t and 500 h, respectively. CB.G. is the γ-ray count from the background.
2.1.4. Control of ECP
Platinum (Pt) and 316 SS coils were mounted in the downstream region of the test section, as shown in , to measure the electrochemical corrosion potential (ECP). The coils were connected to an electrometer (6517B, Keithley Inc.). In all measurements in this work, the water chemistry conditions were HWC; therefore, the Pt coil worked as a hydrogen electrode. The ECP of 316 SS was calculated every 10 minutes using the Pt potential as the reference which is −0.5 V vs. standard hydrogen electrode (SHE). ECP of 316 SS was in the range of −0.53 ± 0.02V vs. SHE during 500 h under both conditions with and without Zn.
2.2. Oxide film analysis
In order to study the effect of Zn on corrosion of base metal and on 60Co incorporation into the oxide films, the T.P.s were analyzed. The oxide films formed on the T.P.s were observed with SEM (S-3000FB/H, Hitachi, Ltd.).
According to previous reports [Citation4,5], a double-layer oxide film consisting of outer and inner layers is formed on the SS surface. The immersed T.P.s were processed as described below to determine the amounts of Zn, 60Co and total amounts of the oxides in each layer. The outer layer could be dissolved in a reductive condition, and was therefore separated by cathodic electrolysis. Each T.P. was electrolyzed in an electrolyte solution of 5 wt% H2SO4 and 0.5 wt% hexamethylenetetramine with 1 kA m−2 current. The inner layer could be dissolved in alternating oxidizing and reducing atmospheres, and was separated by alternately soaking in potassium permanganate solution (300 ppm KMnO4 solution) and 10 wt% ammonium citrate solution at 368 K. The amounts of 60Co in the separated oxide films were measured using the Ge γ-ray detector with a multichannel pulse height analyzer. The amounts of Zn in the separated oxide films were determined with an inductively coupled plasma atomic emission spectroscope (ICP-AES; P-4010, Hitachi Ltd.).
3. Results and discussion
3.1. Suppression of SS corrosion by Zn
shows the time dependencies of the corrosion amount of the test wire under the test conditions in . (a) shows the entire immersion time and (b) shows the initial 50 h with an expanded time scale. The corrosion amounts of the 316L SS under HWC conditions without Zn, which were reported by Ishida and Lister [Citation11], are also plotted. Our results and those of the previous report agreed with each other within a margin of error of 10%. This indicated that the PDM measurements well monitored the corrosion amounts of 316 SS.
The corrosion amount of the base metal increased with time in each condition for immersion times of less than 10 h. The corrosion amounts at 10 h without Zn and in the presence of Zn were 0.109 ± 0.007 and 0.102 ± 0.007 μm, respectively. This indicated that the corrosion amounts of these conditions were equivalent to each other during 10 h. On the other hand, the corrosion amount in the presence of Zn had a tendency to saturate after 10 h. The difference between the corrosion amounts without Zn and in the presence of Zn increased with time, and the corrosion amount at 500 h in the presence of Zn was about half of that without Zn. We concluded from these results that the suppression effect of Zn on the corrosion appeared with a delay time of 10 h and the effect increased with time.
In order to study the suppression effect of Zn on the corrosion, we analyzed the compositions of the oxide films. According to [Citation4,5], the oxide films formed on the SS surface have a double-layer structure comprising outer and inner layers. The outer layer is mainly magnetite (Fe3O4), and the inner layer is mainly chromite (FeCr2O4). We separated the oxide films into outer and inner layers, as mentioned in Section 2.2. Total amounts of the oxides and the amounts of Zn which were incorporated in each layer are shown in . The amounts of Zn in the outer and inner layers formed in the presence of Zn were 41 and 49 mg m−2, respectively. We considered that Zn ions in the water environment had been incorporated into the inner layer which is mainly FeCr2O4, and the inner layer had changed to the thermodynamically stable ZnCr2O4. Haginuma et al. [Citation4] proposed a similar effect by Zn injection on the SS corrosion under HWC conditions.
Table 3. Total amounts of metals and oxygen, and amounts of Zn and 60Co in each separated layer.
To confirm the influence of the corrosion suppression of Zn on the oxide films, SEM observations were made. We compared the SEM images of T.P.s () and the film amounts () without Zn and in the presence of Zn. Maximum diameters of the polyhedron particles in the outer layer without Zn and in the presence of Zn were 1.2 and 0.4 μm, respectively. The amounts of the outer layers without Zn and in the presence of Zn were 1321 and 615 mg m−2, respectively. As regards the outer layer, the film amount was decreased and the maximum diameter of the particles became small when Zn was present. We considered that the inner layer stabilized by Zn had suppressed the dissolution of metal ions from the base metal; therefore, the number of polyhedron particles for the outer layer was lowered and the size of them became smaller. On the other hand, the thicknesses of the inner layers without Zn and in the presence of Zn were 0.3 and 0.2 μm, respectively. The amounts of the inner layers without Zn and in the presence of Zn were 1343 and 944 mg m−2, respectively. We considered that the inner layer stabilized by Zn had suppressed the oxidation of the base metal; therefore, the amount of the inner layer was lowered and the inner layer became thinner. These results indicated that Zn decreased the amounts of the oxide films in which 60Co is incorporated as mentioned in [Citation4,5].
From the above results, we considered the delay of the suppression effect of Zn on the corrosion of 316 SS as follows. The oxide films incorporated Zn from the environment at the time of oxide formation and afterwards. Therefore, more ZnCr2O4 was formed and that stabilized the oxide films [Citation4]. There was a lead time of 10 h before the suppression effect by the stabilized film appeared. We considered that the growth rate of the oxide films had been fast, and the oxide films had grown before incorporation of enough Zn to be stabilized in the initial 10 h.
3.2. Suppression of 60Co buildup by Zn
(a) shows the entire immersion time dependencies of 60Co buildup amount without Zn and in the presence of Zn, and (b) shows the initial 50 h with an expanded time scale. Here, experimental error in the 60Co buildup measurements was within ±5 kBq m−2.
Figure 6. Comparison of 60Co buildup amounts for (a) the entire immersion time and (b) initial 50 h.
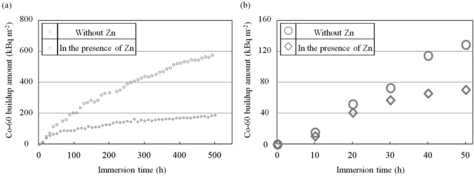
The 60Co buildup amount increased with time in each condition for immersion times of less than 10 h. The 60Co buildup amounts at 10 h without Zn and in the presence of Zn were 15 ± 5 and 11 ± 5 kBq m−2, respectively. This indicated that the corrosion amounts for these conditions were equivalent to each other at 10 h. On the other hand, the 60Co buildup amount in the presence of Zn showed a tendency to saturate after 10 h. The difference between the 60Co buildup amounts without Zn and in the presence of Zn increased with time, and the 60Co buildup amount at 500 h in the presence of Zn was about 1/3 of that without Zn. From these results, we concluded that the suppression effect of Zn on the 60Co buildup increased with time.
In order to study the suppression effect of Zn on the 60Co buildup, we analyzed the amounts of 60Co which were incorporated into the outer and inner layers. The 60Co amounts in each layer are shown in . Focusing on the cases without Zn, the 60Co amounts in the outer and inner layers were 0.19 and 0.39 MBq m−2, respectively. 60Co existed mainly in the inner layer. On the other hand, focusing on the cases in the presence of Zn, 60Co amounts in the outer and inner layers were 0.16 and 0.03 MBq m−2, respectively. 60Co existed mainly in the outer layer. From these results, we concluded that Zn decreased the 60Co amount in the inner layer to 1/10. In other words, Zn suppressed the 60Co incorporation into the inner layer.
3.3. Relationship between 60Co buildup and corrosion
The reported processes of 60Co incorporation are coprecipitation [Citation1,Citation10] and adsorption [Citation10]. We studied the contribution of both processes to the 60Co buildup.
In the coprecipitation process, the oxide films incorporate 60Co during the oxide formation, and the concentration of 60Co in the oxide depends on the concentration of 60Co in the environment. In this work, assuming that the production of oxide is proportional to corrosion, the concentration of 60Co in the environment is constant; therefore, the 60Co buildup by coprecipitation is proportional to the corrosion amount. The 60Co buildup by coprecipitation is expressed as
(3)
(3)
Here, Γcop (kBq m−2) is the 60Co buildup amount by coprecipitation, δ (kBq m−3) is the deposition rate coefficient and Δr is the corrosion amount measured by PDM. We considered that the 60Co buildup had been caused mainly by the coprecipitation in the initial stage for active corrosion, and δ was determined by fitting to the measured 60Co buildup amount and the measured corrosion amount in the range of 0–50 h using Equation (3). On the other hand, the 60Co buildup by the adsorption is expressed by Equation (4) and is the difference between the total 60Co buildup amount and the 60Co buildup amount by coprecipitation.
(4)
(4)
Here, Γads (kBq m−2) is the 60Co buildup amount by adsorption and Γmea (kBq m−2) is the total 60Co buildup amount measured.
The time dependencies of the 60Co buildup amount without Zn, measured (shown in ) and calculated by Equations (3) and (4), are shown in . Here, δ (determined by fitting using Equation (3)) is 5.0 × 108 kBq m−3, Δr is the measured corrosion amount without Zn (shown in ). There were two different time dependencies of the 60Co buildup amount without Zn, one for 0–100 h immersion times and the other for 100–500 h immersion times. In the range of 0–100 h, the measured amount agreed with the amount calculated using Equation (3). In other words, the 60Co buildup amount was proportional to the corrosion amount. In the range of 100–500 h, the difference between the measured amount and the amount calculated using Equation (3) increased with time, and the measured amount was 20% greater than the amount calculated from Equation (3) at 500 h. We explained this as follows. 60Co built up mainly by coprecipitation in the range of 0–100 h, and by both coprecipitation and adsorption processes in the range of 100–500 h. From the time dependency of Equation (4), the 60Co buildup amount by adsorption was negligibly small in the range of 0–100 h, but increased with time in the range of 100–500 h. From the results, we concluded that the 60Co buildup by adsorption had a delay time of about 100 h.
Figure 7. Comparison of measured 60Co buildup amounts and amounts calculated using the equations (immersion without Zn).
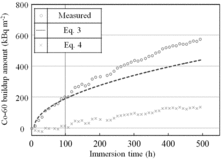
In the same way as the case without Zn, we made comparison of the 60Co buildup amounts measured and calculated using the equation of coprecipitation. The time dependencies of the 60Co buildup amount in the presence of Zn, measured (shown in ) and calculated using Equations (3) and (4), are shown in . Here, δ (determined by fitting using Equation (3)) is 3.7 × 108 kBq m−3 and Δr is the corrosion amount measured in the presence of Zn (shown in ). In the presence of Zn, the measured amount agreed with the amount calculated by Equation (3) during the entire 500 h. In other words, the 60Co buildup amount was proportional to the corrosion amount. From the results in the presence of Zn, we considered that 60Co had built up mainly by coprecipitation because of the suppression effect of Zn on the 60Co adsorption.
Figure 8. Comparison of measured 60Co buildup amounts and amounts calculated using the equations (immersion in the presence of Zn).
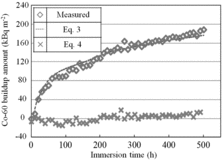
From the above results, we were able to summarize the mechanisms of the 60Co incorporation into the oxide films on 316 SS and of the 60Co incorporation suppressed by Zn. We consider that the process of 60Co incorporation into the oxide films on 316 SS under the conditions without Zn consists of two regions: (1) in the range of 0–100 h and (2) in the range of 100–500 h. In the range of 0–100 h, 60Co is incorporated mainly into the oxide films by the coprecipitation process. In the range of 100–500 h, 60Co is incorporated into the oxide films by both the coprecipitation and adsorption processes. In other words, the oxide films are formed on the surface of the base metal as a result of the corrosion of the base metal (>0.4 μm), and consequently the oxide films adsorb 60Co. In the presence of Zn, similar to the conditions without Zn, 60Co is incorporated mainly into the oxide films by the coprecipitation process in the range of 0–100 h. However, as mentioned in Section 3.1, Zn suppresses the formation of the oxide films which incorporate 60Co. As a result, in comparison with the case without Zn, the 60Co buildup amount at 100 h is reduced to about half of that when Zn is present. In the range of 100–500 h, adsorption of 60Co on the oxide films is suppressed by Zn, but 60Co is incorporated mainly into the oxide films by coprecipitation as in the range of 0–100 h. Therefore, in comparison with the case without Zn, the 60Co buildup amount is reduced to about 1/3 by Zn.
4. Conclusions
We investigated the mechanisms of the suppression of 60Co incorporation into oxide films on 316 SS surfaces by Zn under the conditions simulating HWC. In order to discriminate between coprecipitation and adsorption of 60Co incorporation, we measured the corrosion amount of the base metal and the 60Co buildup amount, using simultaneous continuous measurements. The conclusions are summarized as follows:
From the time tendencies of the corrosion amount, the suppression effect of Zn on corrosion appeared after immersion for 10 h and increased with time under the conditions of this work.
Under the immersion test condition without Zn, the time dependency of 60Co incorporation had two regions. In the range of 0–100 h, 60Co was incorporated mainly by coprecipitation. In the range of 100–500 h, 60Co was incorporated by both coprecipitation and adsorption.
In the presence of Zn, the time dependency of 60Co incorporation had only one region. Due to the suppression effect of Zn on the 60Co adsorption, 60Co was incorporated mainly into the oxide films by coprecipitation. In addition, Zn suppressed the corrosion of the base metal, and then reduced the 60Co buildup caused by coprecipitation. In other words, Zn reduced the 60Co buildup by suppressing both coprecipitation and adsorption, and the suppression effect increased with time.
Abbreviations
316L SS | = | Type 316L stainless steel |
316 SS | = | Type 316 stainless steel |
BWR | = | boiling water reactor |
DH | = | dissolved hydrogen |
DO | = | dissolved oxygen |
ECP | = | electrochemical corrosion potential |
HWC | = | hydrogen water chemistry |
ICP-AES | = | inductively coupled plasma atomic emission spectroscope |
PDM | = | potential drop method |
PLR | = | primary loop recirculation system |
PTFE | = | polytetrafluoroethylene |
SEM | = | scanning electron microscope |
SCC | = | stress corrosion cracking |
T.P. | = | test piece |
SHE | = | standard hydrogen electrode |
References
- Lister DH. The transport of radioactive corrosion products in high-temperature water – 2. The activation of isothermal steel surfaces. Nucl Sci Eng. 1976;59:406–426.
- Aizawa M, Ohsumi K, Asakura Y, Morikawa Y, Hirahara Y, Sakai T, Haraguchi K. Operating experience of Japanese improvement and standardization BWRs and behavior of radioactivity in reactor water. Proceedings: Water Chemistry of Nuclear Reactor Water System 6; 1992 Oct 12–15; Bournemouth (UK).
- Marble WJ, Cowan RL. Status of zinc injection passivation at U.S. BWRs. Proceedings of 1988 JAIF International Conference on Water Chemistry in Nuclear Power Plants; 1988 Apr 19–22; Tokyo (Japan).
- Haginuma M, Ono S, Takamori K, Takeda K, Tachibana K, Ishigure K. [Effect of zinc addition on cobalt ion accumulation into the corrosion surface of type 304 stainless steel in high-temperature water containing dissolved hydrogen]. Zairyo-to-Kankyo [Corros Eng]. 1997;46:565–571. Japanese.
- Hosokawa H, Nagase M. Investigation of cobalt deposition behavior with zinc injection on stainless steel under BWR conditions. J Nucl Sci Technol. 2004;41:682–689.
- Hosokawa H, Nagase M, Fuse M. Development of a suppression method for deposition of radioactive cobalt after chemical decontamination: (I) effect of the ferrite film coating on suppression of cobalt deposition. J Nucl Sci Technol. 2010;47(6):531–537.
- Ito T, Hosokawa H, Nagase M, Fuse M. Development of a suppression method for deposition of radioactive cobalt after chemical decontamination: (III) the suppression mechanism with preoxidized ferrite film for deposition of radioactive cobalt. J Nucl Sci Technol. 2013;50(9):865–872.
- Lin CC. Hydrogen water chemistry technology in boiling water reactors. Nucl Technol. 2000;130:59–70.
- Hettiarachchi S, Law RJ, Miller WD, Daiz TP, Cowan RL. First application of NobleChem to an operating BWR. Proceedings of 1998 JAIF International Conference on Water Chemistry in Nuclear Power Plants; 1998 Oct 13–16; Kashiwazaki (Japan).
- Ono S, Haginuma N, Kumagai N, Kitamura M, Tachibana K, Ishigure K. Distribution of cobalt in surface oxide film of type 304 stainless steel exposed to high-temperature water quantitative analysis by glow discharge optical emission spectrometry. J Nucl Sci Technol. 1995;32:125–132.
- Ishida K, Lister DH. In situ measurement of corrosion of type 316L stainless steel in 553 K pure water via the electrical resistance of a thin wire. J Nucl Sci Technol. 2012;49:1078–1091.