Abstract
To clarify the operating conditions for the homogenization of metallic low-level radioactive wastes (LLW), melting tests were conducted in the metal melting system of the Advanced Volume Reduction Facilities at the Japan Atomic Energy Agency (JAEA). Simulated metallic LLW with a non-radioactive tracer were melted in the induction furnace of the metal melting system. Regardless of the chemical composition or amounts of the simulated wastes, the tracer distribution in the solidified products was nearly homogeneous when the simulated wastes were completely melted in the range from 1550 °C to 1638 °C.
1. Introduction
The melting treatment for low-level radioactive waste (LLW) has advantages, such as a large volume reduction ratio, homogenization of the radionuclides distribution of the final product, and preparation of a final product that is stable and binds radionuclides. Therefore, the melting treatment has been adopted as the metallic LLW treatment technique for recycling and disposal in Germany, Sweden, and France, among other countries [Citation1]. In Japan, there are several melting treatment facilities in operation for the disposal of miscellaneous LLW arising from the operation of nuclear power plants [Citation2,Citation3]. The Japan Atomic Energy Agency (JAEA) has the experience of melting tests for metallic LLW arising from the Japan Power Demonstration Reactor decommissioning project by the induction furnace with a capacity of 500 kg [Citation4]. On the basis of the experience of the melting tests, the JAEA had adopted the induction furnace with a capacity of 4 tons as part of the metal melting system at the Advanced Volume Reduction Facilities (AVRF) of the Nuclear Science Research Institute not only for disposal but also for recycling [Citation5]. Most of the metallic LLW arising from the research and development in the JAEA are ferrous metals.
For disposal or recycling of radioactive wastes, the radioactive inventory of the final product after waste treatment should be evaluated. The distribution of radionuclides in the product is a very important factor for rapid and precise estimation of the radioactive inventory of the product. For a single batch melting process in the metal melting system, if the molten waste in the induction furnace (molten bath) is adequately homogeneous, the radioactive inventory of the waste in the batch can be evaluated via radioactivity analysis of a sample taken from the molten bath (molten-bath sample) after complete melting of the waste. Increasing the capacity of the furnace leads to improvement in the efficiency of the melting treatment and reduction of the radioactive analysis cost. Generally, homogenization of the liquid material is final state of mixture of the molecular interdiffusion. The liquid material would be homogenized easily if the viscosity of liquid is low, in other words, the molecular diffusion rate is high. Even in the case of the liquid with high viscosity, the time required to homogenize the liquid could fairly shorten by reduction of molecular diffusion length due to convection flow caused by stirring [Citation6]. It seems that the viscosity of molten ferrous metal at more than 1550 °C has a very small effect on the homogeneity because the estimated values from experimental data [Citation7,Citation8] are at an extremely low level similar to that of water at 20 °C (1.0 mPa·s). The metal melting process has a great advantage in homogenization because the viscosity of the molten metal is about 1/1000 as compared to that of non-metal materials (e.g. Borosilicate glass [Citation1]).
However, it could not exclude the possibility that the melting of a large amount of radioactive wastes at one time would produce solidified products with an inhomogeneous distribution of radionuclides, depending on the melting conditions. Therefore, melting tests with simulated metallic wastes and non-radioactive tracers were conducted to clarify the operating conditions for the homogenization of metallic LLW in the induction furnace at the AVRF in advance of actual LLW treatment.
2. Test
2.1. Outline of the metal melting system
The metal melting system used in this study was composed of an induction furnace (1200 kW, 300 Hz), an off-gas cleaning system, a ladle, and casting equipment (ingot mold, receptacle mold, centrifugal casting machine) [Citation9]. shows a schematic diagram of the metal melting system.
An induction furnace was designed on the basis of the principle of electromagnetic induction. A magnetic field, generated by applying an alternating current to the coil surrounding the furnace, induces an eddy current in the metallic wastes in the furnace. This induced current produces heat that causes the metallic wastes to rapidly reach the melting point. The induction furnace has a capacity of 4 tons for ferrous metals. The molten metal is discharged from the bottom of the furnace by manipulating a slide valve, which enables selectively obtaining the molten metal that contains very little slag. Several solidified products (receptacles, ingots) can be produced per a single batch.
“Receptacles”, which is produced as metallic LLW recycled products, will be used for the container of molten non-metal waste generated from the plasma melter of the AVRF [Citation5,Citation9]. For the production of these receptacles, the molten metal is poured first into a ladle and then poured from the ladle into the receptacle or ingot molds by tilting the ladle (ladle casting mode). When producing only metallic ingots, the molten metal is poured directly into the ingot molds (direct casting mode) [Citation10,Citation11]. shows a schematic diagram of the induction furnace of ladle casting mode.
2.2. Test methodology
2.2.1. Simulated wastes and non-radioactive tracer
In the melting tests, the simulated LLW were prepared by storing a predetermined amount of commercial carbon steel (SS400, carbon: 0.13%) and/or austenitic stainless steel in 200 L drum. The weight of simulated wastes in the drum was from 250 to 750 kg. Considering the steady operation of the metal melting system, 2.5 tons (approximately 60% of the capacity of the furnace) of simulated wastes was used as a standard value in this study. In addition, to investigate the influence of the weight of the simulated wastes on the homogeneity, melting tests were also conducted over the range from 1.2 tons (the minimum weight for taking a molten-bath sample) to 4.0 tons (the maximum weight of the metal melting system).
Metallic cobalt particles (99.0%, 1–2 mmφ) were added as a non-radioactive cobalt tracer, because cobalt 60 is one of a major nuclide included in the LLW generated from research facilities or nuclear power plants [Citation12,Citation13]. In addition, it seems that cobalt is suitable for discussing about the homogeneity in the melting process since the boiling point of it is extremely high (2927 °C) and a possibility of volatilizing in the gaseous phase by melting is very low. The amount of the tracer was determined such that the final concentration of cobalt in the molten bath was approximately 2.0 wt% considering the accuracy of the chemical component analysis using an X-ray fluorescence spectrometer (described below). The composition of the simulated wastes used in the tests is shown in .
Table 1. Composition of the simulated wastes.
2.2.2. Operating procedure for the metal melting system
First, one 200 L drum of simulated wastes was placed in the empty furnace and then heating was initiated by applying the current to the induction furnace. After the first drum melted, additional waste drums were fed to the furnace one by one until the predetermined amount () was added. As the melting of the drums progressed, the residual metallic wastes moved with the fluid flow in the molten bath owing to the electromagnetic stirring force resulting from the interaction between the induced current and magnetic field. The surface of the molten bath was monitored using two surveillance cameras placed on the upper part of the furnace in order to confirm the complete melting of the simulated wastes in the molten bath. The tracer was added to the final drum for each batch except in Test 4, in which the tracer was added to the penultimate drum of the batch in order to confirm the response behavior of the concentration change of the tracer in the molten bath.
To avoid the risk of the clogging the bottom nozzle owing to a sudden drop in temperature during pouring of molten metal from the furnace, the operating temperature of the furnace was set above 1550 °C, which exceeds the melting temperature of pure iron (1535 °C). To confirm the influence of the temperature of the molten bath on homogeneity, melting tests were conducted in the range from 1550 °C to 1638 °C.
The temperature of the molten bath was measured using a fiber optic radiation thermometer (FIMTHERM-HM, JFE Mechanical Co., Ltd.) and a disposal thermocouple (SK-HLNS1117, Kawaso Electric Ind. Co., Ltd.). Temperature measuring point was several cm below from the surface of the molten bath. After confirming that the simulated wastes were completely melted and the temperature of the molten bath exceeded 1550 °C, a molten-bath sample was obtained by inserting a sampling probe (STP-S, Kawaso Electric Ind. Co., Ltd.). The sampling probe was immersed at about 10 cm below from the surface of the molten bath for a few seconds. In the operation of the melting system, the temperature holding time, or the time required to homogenize the tracer distribution in the molten bath (the tracer concentration in the molten bath becomes a constant value) was found to be the most important factor for determining the appropriate treatment time. Therefore, several molten-bath samples were taken at different times following the completion of the melting of the final drum containing the tracer (Tests 1–3). The molten-bath samples were 30 mm in diameter, approximately 50 mm in length, and weighed approximately 270 g. The molten bath was then poured into ingot molds or the ladle several times after molten-bath sampling was complete.
Samples for analysis were cut from the edge of the solidified ingots and receptacles using a band saw or a grinder as shown in . Because of the difference in the number of stirring processes of molten bath by pouring, there was the possibility of the certain variation in the homogeneity of metal ingots between the direct casting mode and the ladle casting mode. Therefore, samples for analysis were cut from the top and the bottom of the solidified products in direct casting mode in order to confirm the change in homogeneity between the casting modes. The casting mode (direct or ladle) and number of samples obtained for analysis in each of the tests are shown in .
Table 2. Casting mode and number of samples for analysis in the tests.
2.2.3. Sample analysis
The chemical composition of the molten-bath and solidified product samples was measured using a wavelength dispersive X-Ray fluorescence spectrometer (Shimadzu Corporation XRF-1800). The sample measurement area was the smooth surface produced by sample cutting (and grounding if necessary). The peaks for each chemical element were analyzed by the fundamental parameter method generally used in X-Ray fluorescence analysis.
The coefficient of variation (i.e., the relative standard deviation) was applied as the index of homogeneity for the melting treatment. The smaller the coefficient of variation, the better the homogeneity. If the coefficient of variation in the concentration of the chemical element in the molten-bath sample, which is taken just before pouring, and of that in samples cut from the solidified products is sufficiently small, it could be said that the homogeneity of molten bath is fairly well and therefore the concentration of chemical element in the molten-bath sample is representative value of the batch. With reference to the results of other melting tests [Citation4,Citation14–16], it is determined that the distribution of cobalt tracer in the solidified product is sufficiently homogeneous when the coefficient of variation is smaller than 10%.
3. Results and discussion
3.1. Temperature holding time
The temperature holding time is a system-specific value depending on the furnace type and the characteristics of the waste material. It was necessary to determine the appropriate temperature holding time in advance of a discussion of the homogenization of metallic LLW. (a) shows the concentration of the cobalt in the molten-bath samples as a function of the temperature holding time. In this figure, the time of complete melting of the final drum is defined as time zero. Despite the change in the chemical composition of the simulated wastes, the concentration of cobalt was nearly constant immediately after complete melting in each test. and show the concentrations of the major chemical elements (Fe, Ni, and Cr) in the molten-bath samples as a function of the temperature holding time. Despite the addition of cobalt, the concentration of each chemical element was nearly constant just after complete melting in each test.
Figure 4. Concentration in the molten-bath samples as a function of the temperature holding time (a) cobalt (Tests 1–3), (b) iron (Tests 1–3), and (c) nickel and chromium (Tests 2 and 3).
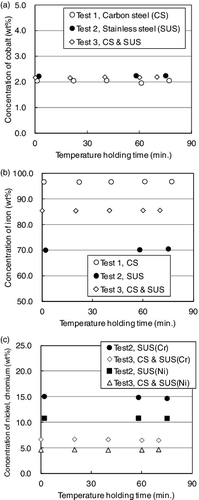
To confirm the response behavior of the concentration of cobalt in the molten bath, in Test 4, the cobalt tracer was added to the next to last drum. shows the response of the concentration of cobalt in the molten-bath samples as a function of the weight of the molten bath (Test 4). The measured values for the cobalt concentration were in good agreement with the values predicted on the basis of the weight change in the molten bath.
Figure 5. Response behavior of the cobalt concentration in the molten-bath samples as a function of the weight of the molten bath (Test 4).
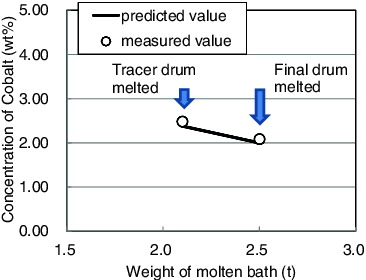
In this study, there was no need to set a particular temperature holding time because the tracer distribution in the molten bath became homogeneous immediately after complete melting of the simulated wastes. In other words, the timing of the molten-bath sampling for radioactive analysis from the molten bath could be selected arbitrary after confirmation of complete melting.
3.2. Homogeneity of the solidified products
3.2.1. Chemical elements in the simulated wastes
Melting tests in the ladle casting mode were conducted with simulated wastes of different chemical compositions in order to clarify the level of homogeneity of the solidified products. The concentration of chemical elements in the molten-bath and the corresponding solidified product samples is shown in . Each of molten-bath samples in was taken from the molten bath just before pouring. The coefficients of variation in the concentration of chemical elements were calculated from the values of Mb and S1–S5 in .
Table 3. Concentration of the chemical elements in the samples from simulated wastes with different compositions.
Regardless of the chemical composition of the molten bath, the concentration of cobalt in the solidified product samples reached approximately 2.0 wt% as planned and was nearly the same as that in the molten-bath samples in each test. The coefficient of variation in the concentration of cobalt in Test 1 was relatively larger than that of the other two tests. However, the value of the coefficient of variation, 2.7% in Test 1, is a very small enough from the viewpoint of homogeneity of the melting process.
With respect to the other major chemical elements, the coefficient of variation in the chromium concentration for Test 3 was relatively larger than that of the other elements in each test. However, the value of the coefficient of variation, 3.7% in Test 3, is a very small enough from the viewpoint of the homogeneity of the melting process as mentioned above.
As a result, the homogeneity of the molten baths in Tests 1–3 was so high because the coefficient of variation for the concentration of the chemical elements in each test was very small. Therefore, the concentrations of the major chemical elements in the molten-bath sample are representative of the corresponding concentrations in the solidified products, regardless of the chemical composition.
3.2.2. Temperature of the molten bath
Melting tests with carbon steel were conducted in direct casting mode with changing the temperature of the molten bath. The cobalt concentration in the samples as a function of the temperature is shown in . Molten-bath sample of Test 4 in was taken from the molten bath just before pouring. The concentration of cobalt in the solidified product samples was nearly the same as that in the corresponding molten-bath samples in each test. The coefficients of variation in the cobalt concentration increased slightly with increasing temperature though the estimated viscosity values of the molten metal for a Fe–C alloy (carbon concentration: 0.13%) decreased with increasing temperature [Citation7]. However, the maximum value for the coefficient of variation, 1.9% in Test 3, was very small enough from the viewpoint of the homogeneity in the melting process.
Table 4. Cobalt concentration in the samples at different temperatures.
Therefore, the concentration of the chemical elements, including cobalt, in the molten-bath sample is representative of the concentration in the solidified products regardless of the casting mode, because the homogeneity of the molten bath is very high above 1550 °C.
Also, there seems to be no obvious differences in homogeneity of solidified products between the casting modes.
3.2.3. Amount of molten bath
The power and distribution of the electromagnetic stirring force change with the quantity of the molten bath. Therefore, to obtain practical operational data, melting tests with carbon steel were conducted in the direct casting mode using different amounts of molten bath in each batch. The cobalt concentration in the samples as a function of the weight of the simulated wastes is shown in . The concentration of cobalt in the solidified product samples was nearly the same as that in the corresponding molten-bath samples for each test. The coefficients of variation for the cobalt concentration were also very small, as was observed in the previous tests. Therefore, the concentration of the chemical elements, including cobalt, in a molten-bath sample is representative of the concentrations in the solidified products regardless of the amount of molten bath used in the melting process.
Table 5. Cobalt concentration in the samples as a function of the weight of the simulated wastes.
4. Conclusion
In advance of actual LLW treatment in JAEA's metal melting system, melting tests with simulated metallic wastes and non-radioactive tracers were conducted to clarify the operating conditions for the homogenization of the metallic LLW. The following results were obtained.
Samples for radioactive analysis could be taken from the molten metal in the furnace (molten bath) at an arbitrary time after confirmation of complete melting of the waste, without the need to establish a particular temperature holding time.
The distribution of chemical elements, including the tracer, in the solidified products was nearly homogeneous regardless of the chemical composition or amount of the simulated wastes or the casting modes, when the simulated wastes were completely melted in the range from 1550 °C to 1638 °C.
Acknowledgements
The authors wish to thank Mr Kenji Takahashi of Mitsubishi Materials Corporation and Mr Keita Someya and Mr Ritsu Hanawa of Nuclear Engineering Co., Ltd. for their help in formulating the plan for commissioning and conducting the melting tests. The authors also wish to thank Nuclear Engineering Co., Ltd and its staff for technical support in the operation and maintenance of the metal melting system.
Disclosure statement
No potential conflict of interest was reported by the authors.
References
- International Atomic Energy Agency (IAEA). Application of thermal technologies for processing of radioactive waste: IAEA. 2006. IAEA-TECDOC-1527.
- Mitsuta Y, Takeuchi Y, Minami T, Kataoka H, Aoyama A, Mutou S, Torita K, Torii A. [Melting treatment of non-combustible solid waste for MIHAMA nuclear power plant.] Nihon-Genshiryoku-Gakkai 2003-Nen Aki-No-Taikai Yoko-Shu [Proc Ann Fall Mtg At Energy Soc Jpn]; 2003 Sep 24–26; Shizuoka (Japan) [in Japanese].
- Tsuji Y. Plasma arc melting treatment of low level radioactive waste with centrifugal hearth. Purazuma-Kakuyugo-Gakkai Shi [J. Plasma Fusion Res.] 1997;73:949–955 [in Japanese].
- Nakamura H, Fujiki K. Melting tests for recycling slightly radioactive metallic wastes arising from decommissioning. Nucl Technol. 1997;117:195–205.
- Nakashio N, Higuchi H, Momma T, Kozawa K, Touhei T, Sudou T, Mitsuda M, Kurosawa S, Hemmi K, Ishikawa J, Kato M, Sato M. Trial operation of the advanced volume reduction facilities for LLW at JAEA. J Nucl Sci Technol. 2007;44:441–447.
- Kagaku-Kougakukai [Soc. Chem. Eng. Jpn.]. Kagaku kougaku benran [Chemical engineering handbook]. 5th ed. Tokyo: Maruzen; 1988. p. 890 [in Japanese].
- Nihon-Imono-Kyokai [Jpn. Foundry Soc.]. Imono benran [Foundries handbook]. Tokyo: Maruzen; 1986. p. 498 [in Japanese].
- Sato Y, Sugisawa K, Aoki D, Yamamura T. [Viscosity of molten Fe-Cr-Ni ternary alloy as a basic system of stainless steel.] Zairyo To Purosesu [Curr Adv Mater Proc]. 2003;16:1017 [in Japanese].
- Higuchi H, Ohsugi T, Nakashio N, Momma T, Touhei T, Ishikawa J, Iseda H, Mitsuda M, Ishihara K, Sudou T, Yano M, Kato M, Irie H, Yokota A, Takahashi K, Makino M, Ichinosawa Y, Someya K, Kozawa K, Kurosawa S, Hemmi K. Construction, management and operation of advanced volume reduction facilities. Japan Atomic Energy Agency; 2007. JAEA-Technology 2007-038 [in Japanese].
- Touhei T, Someya K, Takahashi K, Iseda H, Kozawa K, Momma T. Improvement of the casting process in the metal melting system. Japan Atomic Energy Agency; 2009. JAEA-Technology 2009-031 [in Japanese].
- Touhei T, Nakashio N, Ohsugi T, Ishikawa J, Mizoguchi T, Hanawa R, Someya K, Takahashi K, Iseda H, Kozawa K, Momma T. Verification of improvement of the casting process in metal melting system. Japan Atomic Energy Agency; 2010. JAEA-Technology 2010-008 [in Japanese].
- Sakai A, Amazawa H, Nakata H, Takahashi K, Kihara S. Selection of main nuclides from the viewpoint of safety assessment for near surface disposal of low-level radioactive waste generated from research, industrial and medical facilities -Part 3. Japan Atomic Energy Agency; 2010. JAEA-Technology 2010-021 [in Japanese].
- Matsumura K, Hirai T, Kitajima H, Hayashi M, Kanagawa Y, Taniguchi T, Okamoto M. [A study on fabrication technology of waste package for non-combustible miscellaneous solid waste from nuclear power plant.] Hoshasei-Haikibutsu-Kenkyuu [J. Nucl Fuel Cycle Environ.] 1996;2:153–181 [in Japanese].
- Nakashio N, Nakashima M, Hirabayashi T. [Characterization of 50L-scale solidified products yielded by melting treatment of miscellaneous solid wastes and evaluation of radioisotope tracer distribution.] Nihon-Genshiryoku-Gakkai Wabun-Ronbun Shi [Trans At Energy Soc Jpn.] 2004;3:279–287 [in Japanese].
- Obata M, Teshima T, Kurahashi T, Kanagawa Y, Hayashi M, Karigome S, Akagawa Y. [Radionuclides behavior during nuclear waste melting by the induction heat melting system.] Genshiryoku-Bakkuendo-Kenkyuu [J. Nucl Fuel Cycle Environ.] 1998;4:21–30 [in Japanese].
- Amakawa T, Adachi K, Yasui S. [Fundamental research on thermal plasma technology for treatment of low level radioactive solid waste part II – influence of waste composition on material properties of solidified products.] Denki-Gakkai Ronbun Shi A [Trans IEE Jpn.]. 1999;119-A:357–364 [in Japanese].