Abstract
Li2TiO3 is one of the most promising candidates among tritium breeders. In this work, Li2TiO3 pebbles with a narrow size distribution, high density, small grain size, and good sphericity are synthesized using the commercial Li2TiO3 powder as the raw material by a co-flow capillary-based microfluidic wet process. Highly uniform slurry droplets containing Li2TiO3 powder and polyvinyl alcohol were formed in the microfluidic device and then solidified with the cross-linking reaction between polyvinyl alcohol and borax. Li2TiO3 pebbles were finally obtained after sintering the green bodies. The size of sintered Li2TiO3 pebbles with a good sphericity (Dmax/Dmin < 1.05) can be controlled precisely in a size range of 400–1000 µm by adjusting the flow rate of disperse and continuous phases. The effects of the calcination method, sintering condition, solid content of slurry, and the particle size of Li2TiO3 powder on the relative density of Li2TiO3 pebbles prepared were studied in detail, and 97.16% T.D. (Theoretical Density) maximum relative density of the pebbles with 5 µm grain size were fabricated.
1. Introduction
The International Thermonuclear Experimental Reactor's (ITER) Demonstration Power Reactors (DEMOs) require advanced tritium breeders and neutron multipliers to have higher structural integrity at elevated temperature. The pebble beds form for the tritium breeder is a pivotal component of the Helium-Cooled Pebble Bed (HCPB), which was put forward as one of the two concepts for fusion DEMO reactor blanket to be irradiated in the ITER. A number of optional forms of pebble beds for the DEMO blanket have been adopted by researchers from both Europe and China [Citation1,Citation2].
Lithium-based ceramics (e.g., Li2O, Li2TiO3, Li2ZrO3, and Li4SiO4) have been proposed as tritium breeding materials for D-T fusion reactors. Among them, Li2TiO3 and Li4SiO4 are considered to be prospective candidates for the tritium breeder due to their reasonable lithium atom density, low activation, good compatibility with structure materials, and excellent tritium release characteristics at low temperature [Citation3,Citation4]. Li2TiO3 is one of the suitable materials for ITER Test Blanket Modules (TBMs) [Citation5,Citation6] because of its superior properties, such as high lithium density, high thermal stability, tritium release at low temperature, and high thermal conductivity [Citation7] as compared with Li2ZrO3 and Li4SiO4.
The pebble configuration of the tritium breeder could be columnar, cyclic annular, and spherical, but the spherical breeder has advantages in the assembly of blankets with complex geometry, as well as in the relief of thermal stress and irradiation cracking. In addition, it is also beneficial for tritium release and diffusion as a result of increased number of channels between pebbles [Citation8,Citation9]. It is known that smaller pebbles with narrower size distribution raise the density and thermal conductivity of pebble beds. Moreover, the smaller the dimension of the pebbles, makes it easier for pebbles to fill into the complex geometry blanket homogenously [Citation10]. Obviously, it is easier to achieve a designed packing density for pebbles with a high degree of monodispersity.
Several fabrication techniques for primary Li2TiO3 production have been reported: the extrusion–spheronization–sintering process, wet process including direct-wet and indirect-wet, and the sol–gel method [Citation11–14]. The sphericity of pebbles fabricated by the solid reaction method was poor and the size of Li2TiO3 pebbles was hard to control. It is difficult to improve the density of Li2TiO3 pebbles using the wet process. However, the wet process and sol–gel methods are favorable from the perspective of scale-up production. Recently, various pebble fabrication techniques have been developed and optimized by many groups. An India group [Citation15] prepared Li2TiO3 pebbles of 0.6–0.7 mm diameter by internal gelation sol–gel process using LiNO3 and TiOCl2 as the raw materials, and the density of sintered pebbles was 90% T.D. (Theoretical Density) at 1100 °C. Lee [Citation16] used a freeze drying process to prepare Li2TiO3 pebbles, and the sintered pebbles revealed a porous microstructure with a uniform pore distribution and the sintered pebbles were crushed under an average load of 50 N in the compressive strength test. Hong [Citation17] synthesized the β-Li2TiO3 powder via a modified sol–gel combustion method, and in the pebble fabrication process the gel-casting method was used, and the density of Li2TiO3 pebbles was 86% T.D. after being sintered at 1373 K for 2 hours. Hoshino [Citation18,Citation19] proposed a new direct pebble fabrication technique for fabricating Li2TiO3 with additional Li (Li2+xTiO3+y) and Li2TiO3 pebbles. In his work, a T-junction microchannel-based microfluidic device was built to prepare the gel beads that were composed of tritium breeder powders and binder. After calcining and sintering the gel beads, he successfully synthesized Li2TiO3 and Li2+xTiO3+y tritium breeder pebbles with a good performance, which provide a promising technique for the fabrication of advanced tritium breeder pebbles.
A capillary-based microfluidic technique has recently been developed as an effective approach for the fabrication of uniform-size microspheres. Droplets with an extremely narrow size distribution (the coefficient of variation of the particle size distribution is typically lower than 5%) can be produced and dispersed in a continuous fluid flowing along with microfluidic device. The capillary-based microfluidic process offers the possible means to control not only the dimension of the particles but also the size distribution, shape, and morphology over the above-mentioned conventional methods precisely and conveniently. As a disperse phase droplet is formed and delivered in the centerline of continuous phase flow in a capillary-based microfluidic system, the droplets are easily kept away from the wall of the device which prevents any phase inversion. Moreover, these capillary-based devices solve the clogging of microchannels that can be encountered in the microchannel-based devices as well as the possibility to get O/W (oil in water) or W/O emulsion with a single microsystem [Citation20,Citation21].
In our previous work, an assembly–disassembly capillary-based microfluidic device was successfully used to fabricate Li4SiO4 pebbles and Pt/C/polytetrafluoroethylene (PTFE) hydrophobic catalyst pellets [Citation22,Citation23]. In this work, we focus on using the device that consists of commercially available capillaries, ordinary laboratory tubing, T-junction, and with relative easiness for scale-up production to prepare Li2TiO3 breeder pebbles with a narrow size distribution, high density, small grain size, and good sphericity by wet processes based on polyvinyl alcohol (PVA)–Borax cross-linking reaction. In order to improve the sphericity of the as-prepared Li2TiO3 breeder pebbles, isoamyl alcohol was added to the continuous phase and coagulation bath, respectively, to strengthen the solidification of the feed solution droplets in the fabrication processes. The step-by-step temperature-rising strategy was used in the calcination and sintering process to burn off impurities completely and increase the density of Li2TiO3 pebbles. The effect of sintering condition, solid content of slurry, and the particle size of Li2TiO3 powder to the density of pebbles was studied in detail.
2. Experimental
2.1. Materials
Li2TiO3 powder (Alfa Aesar, purity > 99%), PVA (polymerization degree: 1750 ± 50, Sinopharm Chemical Reagent Co., Ltd.), dimethyl silicon oil (Sinopharm Chemical Reagent Co., Ltd.), Na2B4O7·10H2O, triethanolamine, isoamyl alcohol, petroleum ether, carbon tetrachloride, and isopropyl alcohol (AR, Sinopharm Chemical Reagent Co., Ltd.) were used as received.
2.2. Capillary-based microfluidic device
The microfluidic device was assembled from several components, including a hydrophilic capillary tube (Fused silica tubing of 531/670 µm inner/outer diameter, Polymicro Technologies), PTFE tubing (1.8 mm inner diameter, Fisher Scientific Bioblock), a T-junction (P-728-01, Upchurch Scientific), two syringes and two syringe pumps (LSP01-1A, Longer pump). As shown in (a), the capillary tube was inserted inside the T-junction along its main axis. The capillary tube tip exits the T-junction at the center of an outlet PTFE tube. Two syringe pumps were used to deliver the continuous and dispersed phases at a specific and pulse-free flow rate. The liquid to-be-dispersed phase was injected via the capillary tube, and the continuous phase was injected perpendicular to the main axis of the T-junction. At the outlet of the capillary, two different phase liquids met. Therefore, the dispersed phase formed monomer droplets under the shear force of the continuous phase. The formation of droplets was directly observed using a CCD camera (uEye UI-2220SE, IDS) with a microscope (XSP-30E, Shanghai Halibut Instrument Limited Company), as shown in (b1)–(b7).
2.3. Fabrication process
Li2TiO3 powder (Alfa Aesar, purity > 99%) was chosen as the raw material. The procedure for fabricating Li2TiO3 pebbles is shown in , and its detailed process steps are as follows:
The initial Li2TiO3 powder is wet ball-milled for 48 hours at the revolving speed of 350 r/min to get the refined particle size Li2TiO3 powder. Isopropyl alcohol was chosen as the dispersing agent, and the weight composition ratio was 1:1 (isopropyl alcohol:Li2TiO3 powder).
The ball-milled, dried, and sieved Li2TiO3 powder is mixed and ball-milled with PVA solution and distilled water to make the Li2TiO3 slurry.
In the capillary-based microfluidic device, the Li2TiO3 slurry is applied as the dispersed phase, and dimethyl silicon oil and isoamyl alcohol are used as the continuous phase. Highly uniform-size droplets are formed with a proper flow ratio of continuous and dispersed phase.
The solidified droplets are obtained immediately after the droplets flow toward the coagulation bath due to the cross-linking reaction between PVA and borax. Then, the dimethyl silicon oil, isoamyl alcohol, and triethanolamine are washed off from the surface of the spheres with petroleum ether, and the borax located at the surface is washed off with water.
The washed spheres are dried in a dry oven at 50 °C for 12 hours, and, then the oven temperature is increased to 85 °C for another 4 hours. Finally, these spheres were calcined and sintered at 950 °C for 3 hours and the Li2TiO3 pebbles are produced.
The composition of the solution used in this study is provided in .
Table 1. Composition of the solution used in this study.
2.4. Characterization
The thermal behavior of the Li2TiO3 pebbles was analyzed by thermogravimetry and differential scanning calorimetry (TG/DSC) (SDT Q600, TA Instruments Co., Ltd., USA) in air, increasing temperature at the rate of 10 °C min−1 from room temperature (RT) to 1200 °C. The microstructure of the Li2TiO3 pebbles was observed with a scanning electron microscope (SEM) (KYKY-AMRAY 1000B, Scientific Instrument Factory of Chinese Academy of Sciences, China). Crystallographic phase analysis was conducted by X-ray diffraction (XRD) (MXPAHF, 18 kW, MacScience Co., Ltd., Japan) at RT using Cu Kα radiation (λ = 0.154056 nm) at a scanning rate of 2° min−1 from 10° to 70°. The XRD diffractograms were analyzed by the corresponding Joint Committee on Powder Diffraction Standards (JCPDS) by virtue of MDI Jade6.5 software. Density of the Li2TiO3 pebbles was determined by mass and volume measurements. The volume of microspheres was measured using a drainage method. The microspheres were put into a certain volume of water, and the increasein the water volume was equal to the volume of pebbles.
3. Results and discussion
3.1. Preparation of Li2TiO3 precursor beads
The key step in making uniform microspheres is to first produce the uniform precursor droplets. In this study, the capillary-based microfluidic process was used to control the dimension and size distribution of precursor droplets; subsequently, uniform Li2TiO3 microspheres were made.
The optical micrographs of the Li2TiO3 droplets produced by the capillary-based microfluidic device is shown in (a), and the biggest and smallest Li2TiO3 droplets prepared under different flow rate ratios of continuous phase to disperse phase is shown in (b). The droplets possessed a narrow distribution with a coefficient of variation of 1.27%. The shape of the produced Li2TiO3 droplets was nearly spherical and the average sphericity of the obtained droplets was approximately 1.007.
Figure 3. Optical micrographs of the microspheres: (a) Li2TiO3 droplets produced by the capillary-based microfluidic device (flow rate of continuous phase: 150 µL min−1, flow rate of dispersed phase: 5 µL min−1); (b) the biggest Li2TiO3 droplet (flow rate of continuous phase: 150 µL min−1, flow rate of dispersed phase: 10 µL min−1) and smallest droplet (flow rate of continuous phase: 180 µL min−1, flow rate of dispersed phase: 1 µL min−1); (c) small Li2TiO3 pebbles after sintering at 950 °C for 3 hours; (d) big Li2TiO3 pebbles after sintering at 950 °C for 3 hours.
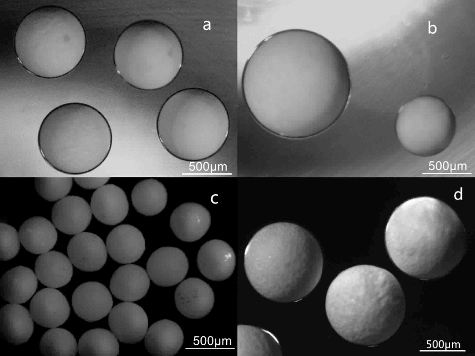
These uniform droplets are dropped into the coagulation bath at the outlet of the PTFE tube and solidify rapidly with good sphericity because of the fast cross-linking reaction of PVA, which was contained in the droplets. The content of isoamyl alcohol used in this study was as high as 33.33 wt%. The authors, however, believe that it has no effect on the cross-linking solidification reaction but plays a critical role in the solidification process. As the continuous phase and dispersed phase droplets flowed downstream toward the coagulation bath at the same time, the dispersed phase droplets are wrapped with the continuous phase film. If the continuous phase is completely immiscible with coagulation bath solution, the continuous phase film covering the disperse phase droplet will prevent direct contact between PVA and borax, leading to the failure of solidification. Isoamyl alcohol was added to both the continuous phase (silicone oil) and the coagulation bath (borax/triethanolamine) to increase the solubility and intermiscibility of both phases, which allowed borax to more easily infiltrate into the dispersed phase droplets and react with PVA [Citation23].
With the microfluidic-assisted process, as presented in (c) and (d), the size, shape, and morphology of Li2TiO3 pebbles is nearly spherical and the average sphericity of the obtained pebbles is close to 1.05. The size of pebbles (400–1000 µm) has a narrow size distribution with a coefficient of variation of 2.38%. Due to the presence of borax in the coagulation bath, boron residue may exist in the prepared Li2TiO3.pebbles. Based on the result of ICP (Inductively Coupled Plasma) analysis, boron impurities (0.04 wt%) in the pebbles were detected. The production volume of Li2TiO3 pebbles was 0.63 g/h in the as-built single-capillary-based microfluidic device. To increase the production volume of Li2TiO3 pebbles in unit time, a scale-up capillary-based microfluidic device is being fabricated.
3.2. Density of Li2TiO3 pebbles
The thermal treatment of the precursor spheres was performed by TG/DSC from RT to 1200 °C to determine the condition of weight changes and temperature of the sintering process. indicates the typical TG/DSC profiles of the precursor spheres. As shown in the TG/DSC graph, from RT to 101.27 °C, the weight loss was approximately 0.834% due to removal of the remaining water from the dried precursor spheres. From 101.27 °C to 583.32 °C, the loss of weight was approximately 8.902%, which was accompanied by a significant exothermic peak at 303.6 °C in the DSC curve due to the decomposition of PVA and the onset temperature was 235 °C. As expected, weight of the precursor spheres showed little variation when the temperature stayed above 600 °C. A significant endothermic peak was observed at 949.73 °C in the DSC curve with almost no weight loss on the TG curve. However, the endothermic peak at 949.73 °C appeared again in the DSC curve of the sintered pebbles, which reveals that a reversible crystalline phase change may have occurred. The decomposition of organic polymer in the rapid fabrication of these ceramics could be divided into two steps associated with the removal of volatile organic compounds and volatile products. The first stage was the volatilization of water and organic solvents. The volatile organic compounds diffused to the surface of the prepared green body through the pore space in the follow-up drying process due to its high vapor pressure. During the second stage of the process of thermal decomposition, volatile decomposition products emerged, spread to the body surface, and evaporated into the air unremittingly. Sufficient diffusion time provided opportunities to avoid the production of pores and, as a consequence, volatile organic compounds concentrated in the polymer. As a result, the vapor pressure overtopped its saturated vapor pressure both at the surface and inside of the green body [Citation24]. Therefore, the principle of the temperature-rising strategy, on the one hand, was that the heating rate should be decreased before the start of decomposition to avoid the potential remnant of volatile components of the decomposition products; on the other hand, temperature should be held at the decomposition curve peak long enough to allow the decomposition products to have time to escape to the surface of the green body completely. It is beneficial to burn off impurities and increase the density of Li2TiO3 pebbles with a gentle heating rate and stay at critical temperatures. However, the grain size of Li2TiO3 pebbles would grow fast with an increase in the sintering time and temperature; hence, sintering time must be controlled under a suitable condition. Based on the above discussion, the heating rates for this study are set as follows: (1) set 1 °C/min and hold at 100 °C, 235 °C, 300 °C, and 600 °C for 3 hours, respectively; (2) when temperature exceeds 600 °C, increase the temperature to 5 °C/min; and (3) sinter at 950 °C for 3 hours.
The relationship between sintering temperature and time and the change of Li2TiO3 pebbles density is shown in . The sintering time was set as 3 hours, and the sintering temperature was 950 °C, 1050 °C, and 1150 °C. As shown in (a), the relative density of Li2TiO3 pebbles is 92.6%, 95.1%, and 98.4%, respectively, while theoretical density of Li2TiO3 is 3.42 g/ml. Therefore, the higher the sintering temperature was set, the higher the density of the Li2TiO3 pebbles. (b) also shows that the relative density of Li2TiO3 pebbles increases with the sintering time from 90.6% to 97.9% at a fixed temperature of 950 °C.
Figure 5. Relationship between sintering temperature (a) and sintering time (b) (the sintering temperature was 950 °C) with Li2TiO3 pebbles density.
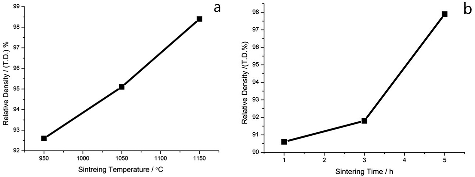
To study the effect of the solid content of the slurry on the density of Li2TiO3 pebbles, the weight content of Li2TiO3 powder was varied from 20% to 55%, the sintering temperature was 950 °C, and the sintering time was 3 hours. The relationship between the content of Li2TiO3 powder with the relative density of Li2TiO3 pebbles is shown in . In essence, the pebble density rises with increasing solid content of the slurry. There is a slight increase in relative density of Li2TiO3 pebbles as the solid content of the slurry increases from 25% to 35%, but the highest point of relative density is reached at 35% of the solid content. When the Li2TiO3 droplets are dropped into the coagulation bath, they solidified rapidly. At this moment, the solidified Li2TiO3 droplets still contain substantial amount of water. Triethanolamine, a dehydrating agent, is incorporated into the coagulation bath ingredients. As such, the Li2TiO3 droplets are solidified and dehydrated quickly at the same time in the coagulation bath. During the transformation process from droplets to precursor beads, Li2TiO3 droplets will solidify, lose water, and shrink volume simultaneously. At the same time, dynamic equilibrium is also reached. As a matter of fact, the solid content of the slurry affects the content of water loss of the Li2TiO3 droplets instead of increasing the Li2TiO3 pebbles density. In addition, failure of the formation of droplets results as the viscosity of slurry increases with solid content.
Figure 6. Effect of solid content of slurry on the density of Li2TiO3 pebbles (the sintering temperature was 950 °C and the sintering time was 3 hours).
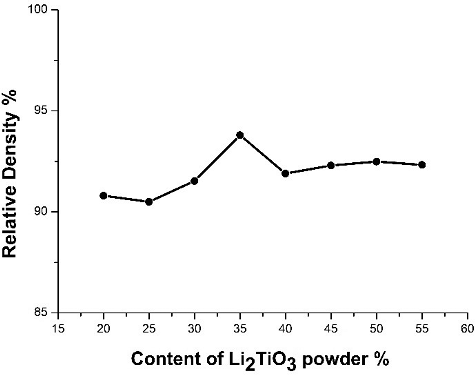
To refine the particle size of Li2TiO3 powder, the commercial grade Li2TiO3 powder was wet ball-milled in the production of the Li2TiO3 slurry. However, more importantly, the sieving test was a convenient, visual means of inspecting the result of the ball-milling process. The standard sieves with different mesh numbers were used to classify the ball-milled Li2TiO3 powder. In this research, the content of Li2TiO3 powder was 35 wt% and PVA solution was 1.5 wt%, and the sintering temperature was set at 950 °C for 3 hours. shows the relationship between particle size of Li2TiO3 powder and the relative density of Li2TiO3 pebbles. As indicated in , the density of Li2TiO3 pebbles rise as the particle size of Li2TiO3 powder decreases, and the growth rate is biggest from 200 to 300 mesh. However, the Li2TiO3 pebbles density rises to its peak of 97.16% as the sieve mesh size reaches 300. But the density of Li2TiO3 pebbles stops increasing as the mesh size of the powder exceeds 300, and remains at a high level. As the size of the particle gets smaller, the space volume between the particles decreases, and the density of the pebbles formed by the particles increases. However, when the particles’ size reaches the limit, the density stops increasing. Thus, smaller particles are not necessary from the viewpoint of pebbles density, and 300-mesh size might be an optimal grade.
3.3. Microstructure of Li2TiO3 pebbles
Li2TiO3 pebbles were obtained through a calcination and sintering process. Subsequently, the crystalline structure is studied by an XRD analysis. To avoid the production of the LiTiO2 phase, all the pebbles were sintered in air, since Ti can be reduced from its four-valence state to the three-valence state at low oxygen partial pressures [Citation25]. shows the XRD pattern of the Li2TiO3 pebbles sintered 3 hours at 950 °C. It has been identified as Li2TiO3 (JCPDS Card No. 33-0831).
The effect of sintering temperature on the microstructure of Li2TiO3 pebbles was examined. shows the microstructure of the fabricated Li2TiO3 pebbles sintered at a specified temperature for 3 hours as seen by electron beam lithography (EBL). (a) presents a whole sintered Li2TiO3 pebble exhibiting a smooth and densified surface. As observed from (b)–(d), the microstructure for the interior of the pebbles was significantly influenced by the sintering temperature. At a sintering condition of 950 °C, the pebbles exhibit homogeneous microstructure with a relatively narrow grain size distribution (∼4 µm; (b)). A small grain size (<5 µm) favors both tritium release and mechanical strength [Citation26]. (c) and (d) shows the pebbles sintered at 1050 °C and 1150 °C for 3 hours. Typical sintering phenomena such as neck growth, particle coalescence, and pore growth are observed in the microstructure. The grain size of the pebbles sintered at 1050 °C is above 10 µm. As shown in (d), when the sintering temperature is raised to 1150 °C, the grain size markedly increased showing a comprehensively different microstructure. Almost all pores are closed by further densification and the grain size of the pebbles is about 40 µm. However, the existence of the structure with open porosities provides continuous thermal conduction paths and large internal surfaces which favor tritium and helium release during irradiation [Citation27].
4. Conclusion
The Li2TiO3 tritium breeder pebbles with a diameter of 0.4–1.0 mm were synthesized using commercial Li2TiO3 powder as the raw material and PVA/borax as the gelling agent by a co-flow capillary-based microfluidic technique. Isoamyl alcohol was added to both the continuous phase (silicone oil) and the coagulation bath (borax/triethanolamine) to increase the solubility and intermiscibility of both phases, which allowed borax to more easily infiltrate into the dispersed phase droplets and react with PVA to enhance the solidification process.
The size of Li2TiO3 pebbles could be easily and precisely controlled by adjusting the flow rate of disperse and continuous phases. The fabricated Li2TiO3 pebbles possess a good sphericity (Dmax/Dmin < 1.05) and a narrow size distribution the coefficient of variation of the particle size distribution is lower than 2.38%. The research results showed that the relative density of Li2TiO3 pebbles was sensitive to the calcination method, sintering condition, solid content of slurry, and the particle size of Li2TiO3 powder. Thus, the relative density of Li2TiO3 pebbles with more than 90% T.D. was easily obtained via controlling the mentioned conditions, and its peak value reached 97.16% T.D. Sintering temperature was influential to the microstructure of the Li2TiO3 pebbles, and the SEM analysis showed that the grain size of fabricated Li2TiO3 pebbles was controlled below 5 µm when the sintering temperature was 950 °C.
Acknowledgements
The authors wish to thank the Ministry of Science and Technology of the People's Republic of China [grant number 2011GB111004] for financial support for this research as well as the National Nature Science Foundation of China for funding this work [grant number 21076203], [grant number 91226109].
Disclosure statement
No potential conflict of interest was reported by the authors.
References
- Donne MD, Albrecht H, Boccaccini LV, Fischer U, Gordeev S, Hutter E, Kleefeldt K, Norajitra P, Reimann G, Ruatto P, Schleisiek K, Schnauder H. European helium cooled pebble bed blanket: design of blanket: module to be tested in ITER. J Fusion Eng Des. 1998;39–40:825–833.
- Xiang B, Ye XF, Feng KM. Conceptual and preliminary engineering design of experimental helium loop for China HCCB TBM components test. J Fusion Eng Des. 2010;85:2146–2149.
- Roux N, Hollenberg G, Johnson C, Noda K, Verrall R. Summary of experimental results for ceramic breeder materials. J Fusion Eng Des. 1995;27:154–166.
- Piazza G, Reimann J, Gunther E, Knitter R, Roux N, Lulewicz JD. Characterization of ceramic breeder materials for the helium cooled pebble bed blanket. J Nucl Mater. 2002;307–311:811–816.
- Van der Laan JG, Kawamura H, Roux N, Yamaki D. Ceramic breeder research and development: progress and focus. J Nucl Mater. 2000;283–287:99–109.
- Ying A, Akiba M, Boccaccini LV, Casadio S, Dell'Orco G, Enoeda M, Hayashi K, Hegeman JB, Knitter R, Van der Laan JG, Lulewicz JD, Wen ZY. Status and perspective of the R&D on ceramic breeder materials for testing in ITER. J Nucl Mater. 2007;367–370:1281–1286.
- Miller JM, Hamilton HB, Sullivian JD. Testing of lithium titanate as an alternate blanket material. J Nucl Mater. 1994;212–215:877–880.
- Roux N, Tanaka S, Johnson C, Verrall R. Ceramic breeder material development. J Fusion Eng Des. 1998;41:31–38.
- Johnson CE, Noda K, Roux N. Ceramic breeder materials: status and needs. J Nucl Mater. 1998;258–263:140–148.
- Christopher GF, Anna SL. Microfluidic methods for generating continuous droplet streams. J Phys D Appl Phys. 2007;40:R319.
- Wen ZY, Wu XG, Xu XG, Lin J, Gu ZH. Research on the preparation of ceramic tritium breeders in SICCAS. J Fusion Eng Des. 2010;85:1551–1555.
- Tsuchiya K, Kawamura H, Fuchinoue K, Sawada H, Watarumi K. Fabrication development and preliminary characterization of Li2TiO3 pebbles by wet process. J Nucl Mater. 1998;258–263:1985–1990.
- Tsuchiya K, Kawamura H, Uchida M, Casadio S, Alvani C, Ito Y. Improvement of sintered density of Li2TiO3 pebbles fabricated by direct-wet process. J Fusion Eng Des. 2003;69:449–453.
- Tsuchiya K, Kawamura H, Casadio S, Alvani C. Effects of gelation and sintering conditions on granulation of Li2TiO3 pebbles from Li–Ti complex solution. J Fusion Eng Des. 2005;75–79:877–880.
- Vittal Rao TV, Bamankar YR, Mukerjee SK, Aggarwal SK. Preparation and characterization of Li2TiO3 pebbles by internal gelation sol–gel process. J Nucl Mater. 2012;426:102–108.
- Lee SJ, Park YH, Yu MW. Fabrication of Li2TiO3 pebbles by a freeze drying process. Fusion Eng Des. 2013;88:3091–3094.
- Hong M, Zhang Y, Mi Y, Jiang Y, Xiang M. Synthesis of Li2TiO3 by sol–gel combustion method and its gel-casting formation. J Nucl Mater. 2014;455:311–315.
- Hoshino T, Nakamichi M. Development of fabrication technologies for advanced breeding functional materials For DEMO reactors. Fusion Eng Des. 2012;87:486–492.
- Hoshino T. Trial examination of direct pebble fabrication for advanced tritium breeders by the emulsion method. Fusion Eng Des. 2014;89:1431–1435.
- Serra CA, Chang ZQ. Microfluidic-assisted synthesis of polymer particles. Chem Eng Technol. 2008;31:1099–1115.
- Serra CA, Berton N, Bouquey M, Prat L, Hadziioannou G. A predictive approach of the influence of the operating parameters on the size of polymer particles synthesized in a simplified microfluidics system. Langmuir. 2007;23:7745–7750.
- Li JL, Zhu YW, Ye B, Zhao ZC, Chang ZQ, Serra CA. Fabrication and characteristics of Li4SiO4 pebbles by a novel capillary-based microfluidic wet process. J Nucl Mater. 2013;440:283–287.
- Song ZF, Wei J, Li X, Zhou WY, Chang ZQ, Serra CA. Synthesis of size-controlled Pt/C/PTFE hydrophobic catalyst pellets in a capillary-based microfluidic system. Int J Hydrogen Energy. 2014;39:16944–16952.
- Calvert P, Cima M. Theoretical models for binder burnout. J Am Ceram Soc. 1990;73(3):575–579.
- Kleykamp H. Phase equilibria in the Li–Ti–O system and physical properties of Li2TiO3. J Fusion Eng Des. 2002;61–62:361–366.
- Lulewicz JD, Roux N, Piazza G, Reimann J, Van der Laanc JG. Behaviour of Li2ZrO3 and Li2TiO3 pebbles relevant to their utilization as ceramic breeder for the HCPB blanket. J Nucl Mater. 2000;283:1361–1365.
- Sharafat S, Ghoniem N, Sawan M, Ying A, Williams B. Breeder foam: an innovative low porosity solid breeder material. J Fusion Eng Des. 2006;81:455–460.