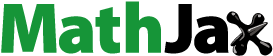
Abstract
Phase equilibrium experiments for the simulated high-level waste (HLW) glass containing palladium, rhodium and ruthenium discharged from a full scale mock up melter have been carried out between 1073 and 1473 K under air and CO2 atmosphere. The chemical compositions of Pd–Rh–Ru–Te (Pd metal phase) and (Ru, Rh)O2 (Ru oxide phase) solid solutions and glass matrix were measured by electron probe micro analysis. Palladium content in the Pd metal phase decreased and ruthenium content in the Ru oxide phase increased with increasing temperature and decreasing oxygen fugacity due to progressive reduction of rhodium. The chemical compositions of these crystalline phases are independent of that of borosilicate glass matrix. Partition coefficient of rhodium between Pd metal phase and Ru oxide phase (KRh) can be expressed by
where T and represent absolute temperature and oxygen fugacity. Based on the comparison of crystal compositions in the HLW glass with experimental results, it can be expected that the HLW glass examined in this study had been equilibrated in the temperature range from 1273 to 1373 K and oxygen fugacity close to that of air just before discharging from the melter.
1. Introduction
High-level waste (HLW) arising from reprocessing of spent nuclear fuel is immobilized by vitrification in an alkali borosilicate glass. The HLW is composed of about 30 different elements including fission products, corrosion products and actinoids. Most of these elements are dissolved in the glass matrix. However, fission platinum group metals (PGMs) (palladium, Pd; rhodium, Rh; ruthenium, Ru) are crystallized as Pd–Rh–Te alloy (Pd metal phase) [Citation1–8] and (Ru, Rh)O2 solid solution (Ru oxide phase) [Citation1,Citation2,Citation5–7] due to their very low solubility in silicate melts (10–1000 ppm) [Citation9–12]. In laboratory-scale experiments, these crystals are not distributed homogeneously throughout glass, but are present on the surface and in the inner part of glass as agglomerates [Citation1].
The PGMs have various effects on vitrification process and physical and chemical durability of HLW glass. Due to radiogenic heat produced by decaying radionuclides, molten HLW glass is slowly cooled from its melting temperature. Then the many types of crystal phases (chrome spinel, cerianite, cristobalite, powellite, Na2MoO4, etc.) can be further precipitated [Citation6,Citation7,Citation13–15]. It has been considered that existence of Pd metal and Ru oxide enhances nucleation and crystal growth during cooling process [Citation2,Citation7,Citation16,Citation17]. Furthermore, viscosity and density of HLW glass increase with increase amount of the Ru oxide phase even at low contents (about 1wt%) [Citation3,Citation18]. In Ru-rich HLW glasses, thermal expansion mismatch between Ru oxide and borosilicate glass matrix is responsible for crack initiation [Citation7].
In Japan, liquid-fed joule-heated ceramic melter (LFCM) is used for HLW vitrification, where thermal energy required for melting is generated using metallic electrodes immersed in an electrically conducting molten glass [Citation19–23]. In the vitrification process using LFCM, the PGMs tend to accumulate on the bottom of the melter due to their high density and result in metallic sludges [Citation3,Citation6,Citation20,Citation22,Citation23]. Because these sludges have higher conductivity and viscosity than those of the molten glass [Citation18,Citation24], they cause a loss of heat input and an obstruction of glass discharge from the melter [Citation20,Citation22,Citation23,Citation25]. It is important to understand behavior of the Pd metal phase and the Ru oxide phase in molten HLW glass for stable operation of vitrification process.
The objective of this study is to investigate relationship of chemical composition between coexisting Pd metal phase, Ru oxide phase and borosilicate glass. Using a simulated HLW glass sample discharged from a pilot melter, phase equilibrium experiments were carried out as a function of temperature in air and in CO2 atmosphere. Partition coefficient of Rh between Pd metal phase and Ru oxide phase was determined from the experimental results. The temperature and oxygen fugacity conditions in the vitrification melter were estimated based on the chemical compositions of Pd metal phase and Ru oxide phase.
2. Experimental method
2.1. Experimental sample
Glass sample used in this study is simulated HLW glass containing PGMs discharged from the LFCM which is a full scale mock-up (KMOC) of an active melter facility in the Rokkasho Reprocessing Plant, located in northern Japan [Citation23,Citation26,Citation27]. This glass (KMOC glass) includes spherical shaped Pd metals with a diameter of 2–10 μm and elongated or needle shaped crystals of Ru oxide with a length of 1–5 μm and a width less than 1 μm. No other metallic or oxide crystals are present. The massive KMOC glass with a mass of about 1 kg was crushed to coarse fragments by a hammer. Glass fragments, each of 50–200 mg mass, were randomly selected and prepared for study. shows bulk chemical composition of the KMOC glass analyzed by inductively coupled plasma atomic emission spectroscopy (ICP-AES) [Citation28] (Li2O, PdO, Rh2O3 and RuO2), mannitol titration method [Citation29] (B2O3) and X-ray fluorescence analysis (XRF) (other oxides). The chemical compositions of crystalline phases included in the KMOC glass measured by electron probe micro-analyzer were shown in . The analytical method will be described later.
Table 1. Chemical composition of the KMOC glass.
Table 2. Chemical compositions (wt%) of Pd metal phase and Ru oxide phase included in the KMOC glass. Numbers in parenthesis represent standard deviation.
2.2. Phase equilibrium experiments
Phase equilibrium experiments were carried out using a vertical tube gas mixing furnace and a muffle furnace. Sample temperature was measured with a type R thermocouple located near the sample. Glass samples were held at 1473 and 1373 K for 24 hours, 1273 K for 48 hours and 1073 K for 96 hours, and then quenched by quickly removing it from the furnace. It has reported that temperature distribution and residence time of glass melt in a LFCM in Japan range between 1073 and 1573 K and 8.0–9.5 hours, respectively [Citation20,Citation23]. The heating temperatures in our experiments are within the temperature distribution, whereas the samples were held for longer duration in order to obtain a composition close to chemical equilibrium. We also evaluated effect of oxygen fugacity on the phase equilibrium. Equilibrium oxygen fugacities () for the reaction MOx = M+x/2O2 (M = Pd, Rh and Ru) calculated using FACT thermodynamic database [Citation30] are higher in the order Pd > Rh > Ru (). The existence of palladium as a metallic phase and ruthenium as an oxide phase suggests that oxygen fugacity in vitrification melter would be located between Pd/PdO and Ru/RuO2 buffers. This
range corresponds to concentration of O2 in air (0.21). The lower bound (Ru/RuO2 buffer) is close to equilibrium
of CO2 = CO + 0.5O2 (). Therefore, we tested heating experiments under two redox conditions, in air and in CO2 atmosphere. In the later experiments, the CO2 with a purity of 99.9% flowed from the bottom of vertical tube furnace under the flow rate of 500 ml/min.
Figure 1. Temperature and oxygen fugacity of Pd/PdO, Rh/Rh2O3 and Ru/RuO2 equilibria calculated from FACT thermodynamic database [Citation30]. Dashed and dotted lines represent in air and equilibrium
of CO2 = CO+0.5O2, respectively. Experimental temperature and oxygen fugacity are indicated by solid circles.
![Figure 1. Temperature and oxygen fugacity of Pd/PdO, Rh/Rh2O3 and Ru/RuO2 equilibria calculated from FACT thermodynamic database [Citation30]. Dashed and dotted lines represent fO2 in air and equilibrium fO2 of CO2 = CO+0.5O2, respectively. Experimental temperature and oxygen fugacity are indicated by solid circles.](/cms/asset/47cb106d-9847-4cea-969b-e9731956946e/tnst_a_1050474_f0001_b.gif)
Sample-holding methods tested in this study were illustrated in . In the beginning of this study, two different methods of sample holding were tested. First, platinum wire of 0.3 mm diameter was gently twisted round a glass fragment with a mass of 30–40 mg, and the glass was partly fused to form a bead by suspending it in a furnace controlled at 1473 K for about 30 sec. Then, the resulting glass bead with a diameter of about 3 mm with platinum wire loop was suspended in the hot spot of the vertical furnace. This technique is known as “wire-loop method” and is a common technique in an experimental petrology [Citation31–33]. The wire-loop method has advantages that losses of noble metals and transition metals from molten glass are minimized compared with experiments using platinum container and that oxygen fugacity of a sample can be quantitative controlled by flowing gas. The latter is caused by the small sample size and large surface area of glass bead, whereas they could lead to a serious loss of volatility elements such as B2O3 and Na2O. Therefore, as a second method, we suspended the wire-looped glass bead in a covered alumina crucible. Then another KMOC glass (6–7 g) was placed in the alumina crucible in order to minimize evaporation losses of elements. The crucible was then put in a muffle furnace. It is described as “crucible method” in this paper.
Figure 2. Methods of sample holding tested in this study. (a) Wire-loop method, (b) crucible method, (c) SiO2 tube method and (d) Al2O3 tube method. In all methods, molten samples are held by a surface tension between glass melt and Pt wire or tubes.
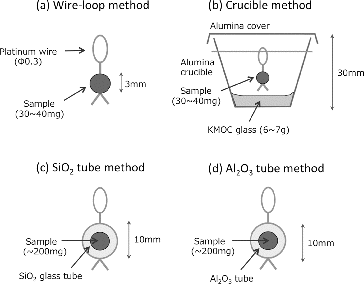
We tried wire-loop method and crucible method in preliminary experiments. However, above 1373 K, equilibrium phase relations were not obtained by these methods. This is due to a reaction between platinum wire and Pd and Rh in glass samples as shown in later section. Thus, we carried out experiments that do not use platinum wire as described below. The glass fragments (about 200 mg) were put in the center of silica glass tube or alumina tube (Nikkato, SSA-S) with an inner diameter of 8 mm (silica glass) or 6 mm (alumina), an outer diameter of 10 mm and a length of 10 mm. These tubes were suspended in a horizontal position at a hot spot of vertical furnace. In this technique, it could be expected that the amount of PGMs in a glass sample is kept constant during melting, while glass composition would be changed due to the reaction with tubes. Furthermore, redox reaction would also immediately reach equilibrium because of small sample volume. These methods are described as “SiO2 tube method” and “Al2O3 tube method”. We could obtain satisfactory results by these methods and report them in this paper.
2.3. Analytical method
The electron probe micro-analyses (EPMA) were performed using JEOL JXA-8800 electron microprobe at the Akita University, operated at an accelerating voltage of 15 kV and 20 nA beam current. Eleven oxides in the glass phase (SiO2, B2O3, Al2O3, FeO, CaO, Na2O, ZnO, ZrO2, La2O3, Nd2O3 and Ce2O3) were measured. Then a simulated HLW glass which does not contain PGMs reported previously (Sample-B in Sugawara et al. [Citation34]) was used for standard material. Beam diameter was 50 μm. The counting times were 10 sec on both peak (except for B2O3) and background and 120 sec on peak for B2O3. Counts were converted to concentrations using ZAF correction procedure [Citation35]. Five–ten spot analyses were made on each sample and mean compositions were determined.
In contrast to the glass analysis, quantitative measurements of platinum group elements are generally difficult due to proximity of the L lines of Ru, Rh and Pd. The Lα1 of ruthenium (2.558 keV) is independent of any other lines and was used for the Ru analysis. However, the Lα1 lines of palladium (2.838 keV) and rhodium (2.696 keV), which are the most remarkable peaks, overlap Lβ1 lines of rhodium and ruthenium, respectively. This is the same in the other Lα are Lβ lines. Consequently, we used Lγ1 of palladium (3.328 keV) and rhodium (3.143 keV), which are very small peak but independent of other L lines. Tellurium was measured by Lα1 (3.769 keV). Counting times were 10 sec on peak of Ru and Te, 30 sec on peaks of Pd and Rh, and 10 sec on background. Pure metallic Pd, Ru and Te and 40 wt% Rh–Pt alloy were used as standards. Beam diameter of 1 μm was used for analysis in both Pd metal phases and Ru oxide phases.
In the analysis of Ru oxide phase, totals of RuO2 and RhO2 contents were always lower than 100 wt% and ranged from 54 to 96 wt%. This is because the Ru oxide has a crystal size smaller than spatial resolution of the EPMA (1 µm). We observed that the measurement total decreases with decreasing an apparent crystal size. In spite of these total losses, RhO2/(RuO2 + RhO2) ratios in the Ru oxide were independent of totals and nearly constants in each of the experimental samples. This suggests that contamination of glass matrix does not affect relative concentration in the Ru oxide in EPMA analysis. This is because of very low solubility of PGMs in a silicate melt [Citation9–12]. Therefore, analytical results of the Ru oxide normalized to 100 wt% are reported in this paper.
3. Experimental results
3.1. Chemical composition of glass phase in the experimental samples
shows SiO2, Al2O3, B2O3 and Na2O contents of glass matrix in experimental samples. It was observed that the glass compositions after phase equilibrium experiments significantly differ from that of starting KMOC glass () due to evaporation and contamination. The compositional changes depend on the experimental method. Generally, B2O3 and Na2O contents decrease and SiO2 increases relatively with increasing temperature. This is caused by evaporation of boron and sodium during melting. The B2O3 loss in the crucible method is lower than that in the wire-loop method as expected, whereas the B2O3 losses in the Al2O3 tube method and SiO2 tube method are much lower than the crucible method. The Al2O3 content in Al2O3 tube method and the SiO2 content in SiO2 tube method increase with increasing temperature because of dissolution of tube materials. The SiO2 content in Al2O3 tube method and the Al2O3 content in SiO2 tube method are nearly constant and close to those in the starting KMOC glass. This is probably due to compensation of loss of boron and sodium and enrichment of alumina and silica in glass phase.
3.2. Chemical composition of crystal phases in the experimental samples
Crystals of both Pd metal and Ru oxide were observed in all of the experimental samples. Square shaped CeO2 phase was also crystallized below 1273 K and the amount was significantly increased at 1073 K. It was observed that some CeO2 crystals contain a core of Pd metal, indicating that the Pd metal phase act as nucleation agents as suggested by Mitamura et al. [Citation2]. There were no silicate crystals and spinel phase in all samples.
Chemical composition of the Pd metal phase and the Ru oxide phase are given in and . Significant differences were observed in composition of metal phase above 1373 K depending on the experimental methods. The chemical composition of Pd metal by SiO2 tube method is consistent with that by Al2O3 tube method at the same temperature and condition, whereas in crucible method, metal phase shows more Rh-rich and Pd-poor composition at 1373 K and Rh-rich metals were also observed at 1473 K in air. Ru-rich metals were crystallized by wire-loop method at 1373 K in CO2 atmosphere. In those experiments, it was observed that platinum wire suspending a glass bead includes 0.6 to 6 wt% Pd and Rh at the rim (). The Pd and Rh contents in Pt wire increased with increasing temperature and decreasing oxygen fugacity. These facts suggest that adsorption of Pd and Rh onto platinum wire causes depletion of Pd metal phase and results in the crystallization of Rh and Ru-rich metal phases. The Pd and Rh were not detected at the core of platinum wire, indicating that the Pt wire have a heterogeneous composition. This implies that it is difficult to obtain equilibrium phase relation by the crucible method and the wire-loop method. Furthermore, tellurium contents of Pd metal phase crystallized by the crucible method and the wire-loop method were significantly lower than those by tube methods (), indicating that evaporation loss of Te from glass beads occurred. Therefore above 1373 K, we concluded that the only results by the Al2O3 tube method and the SiO2 tube method () can be regarded as equilibrium relationship.
Table 3. Chemical compositions of the Pd metal phase and the Ru oxide phase crystalized in the phase equilibrium experiments and calculated partition coefficient of Rh (lnKRh). Values normalized to total 100wt%. Numbers in parenthesis represent standard deviation.
Table 4. Chemical compositions of the Pd metal phase and the platinum wire used for sample holding by the crucible method and the wire-loop method above 1373 K. Numbers in parenthesis represent standard deviation.
and represent chemical compositions of metal phase and oxide phase, respectively. Palladium and tellurium contents in the Pd metal decrease and Rh content increases with increasing temperature and oxygen fugacity. Ruthenium content in the Pd metal is up to 5 wt% at the most reducing condition (1473 K, CO2 atmosphere). The composition of the Ru oxide in air is constant between 1073 and 1373 K, while RhO2 decreases at 1473 K. Under CO2 flow, Ru oxide shows lower RhO2 contents compared with those in air. The increase of Rh in Pd metal and decrease of Rh in Ru oxide with increasing temperature and decreasing can be accounted for by reduction of Rh in the sample. It is of interest to note that the compositions of Pd metal and Ru oxide by Al2O3 tube method are consistent with those by SiO2 tube method despite the compositional differences of glass matrix in those two methods (). This is probably related to the low solubility of PGMs in silicate melts. Solubility of Pd and Rh in SiO2–Al2O3–CaO–MgO melt at 1723 K is 338 and 35 ppm at 50 wt% SiO2, respectively, while they are 316 and 22 ppm at 70 wt% SiO2 [Citation12]. The compositional dependence of PGMs solubility is not significant. Solubility in the alkali-borosilicate melt should be of the same order of magnitude. We conclude that the chemical compositions of Pd metal phase and Ru oxide phase in HLW glass are independent of composition of glass matrix because amounts of Pd, Rh and Ru in the glass matrix are very limited.
Figure 4. Chemical compositions of the Pd metal phase in experimental samples; (a) Pd, (b) Rh, (c) Te. Solid circle and open circle are results in air and in CO2 atmosphere, respectively. Open square represents composition of Pd metal included in the starting KMOC glass. Error bar is a standard deviation (1σ).
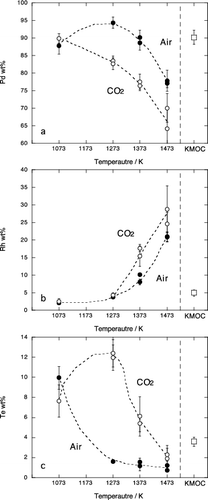
Figure 5. Chemical compositions of the Ru oxide phase in experimental samples; (a) RuO2 and (b) RhO2. Values normalized to total 100wt%. Solid circle and open circle are results in air and in CO2 atmosphere, respectively. Open square represents composition of Ru oxide included in the starting KMOC glass, respectively. Error bar is a standard deviation (1σ).
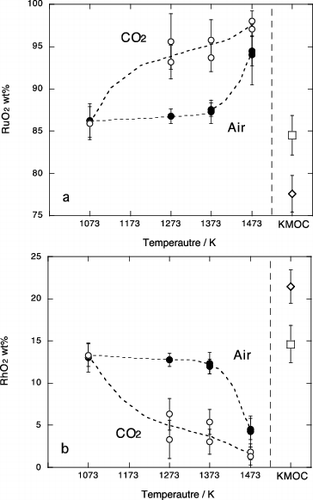
3.3. Mass fraction of crystalline phases
Mass fractions of crystalline phases were determined by a mass-balance calculation using compositions of both phases (), bulk contents of Pd, Rh and Ru in the KMOC glass () and the Pd, Rh and Ru contents in glass matrix. Then the solubilities of Pd, Rh and Ru in borosilicate melt were assumed as 300, 30 and 30 ppm, respectively [Citation12]. The results are shown in . The amounts of Pd metal phase and Ru oxide phase in the starting KMOC glass are calculated to be 0.32 and 0.21 wt%, respectively. In the experimental samples, Pd metal increases and Ru oxide decreases with increasing temperature and decreasing oxygen fugacity due to the reduction of oxygen.
4. Discussion
4.1. Estimates of temperature and redox condition from crystal compositions
Operation temperature of LFCM for HLW vitrification ranges from about 1273 to 1573 K at main portion, while it is lowered to about 1073 K in the bottom portion [Citation20,Citation22,Citation23]. Although an actual melt temperature can be measured by thermometer, the measurement position is restricted. Therefore, a numerical simulation has been attempted to estimate temperature distribution and material flow in glass melter [Citation22,Citation34,Citation36,Citation37]. We propose that the chemical compositions of Pd metal and Ru oxide can be used for independent estimates of the temperature and redox condition in vitrification melter.
The Pd metal in the KMOC glass contains 91wt% Pd. This is consistent with metal composition below 1373 K in air and that at 1073 K in CO2. Similarly, Rh content in the Pd metal (5.5wt%) agrees with that between 1273 and 1373 K and at 1073 K in air and CO2 condition, respectively (). The composition of Ru oxide in the KMOC glass is consistent with results below 1373 K in air (). From these comparisons, it can be expected that crystalline phases included in the KMOC glass were equilibrated at the temperature from 1273 to 1373 K and atmospheric oxygen fugacity.
The Te contents of experimental Pd metal in air (1.2–1.6 wt%) are slightly lower than that in the KMOC glass (3.6 wt%). This is considered to be due to the evaporated nature of the tellurium at high temperature.
4.2. Rhodium partitioning between Pd–Rh–Ru–Te and (Ru, Rh)O2 solid solutions
Comparison between chemical compositions of experimental products and of crystal phases in a HLW glass is useful to estimate physical condition in a vitrification melter. However, the compositional changes given in the and are not always common in an HLW glass since the phase relationship is basically dependent on the proportion of PGMs included in a glass. On the contrary to this, thermodynamic relationship of element partitioning among crystalline phases give insight into more general relationship of chemical composition, temperature and oxygen fugacity.
The rhodium partitioning between Pd–Rh–Ru–Te and (Ru, Rh)O2 solid solutions can be represented by the reaction:
(1)
(1)
The chemical potentials (μji) for each component can be described as follows:
(2a)
(2a)
(2b)
(2b)
(2c)
(2c) where a and
are activity and oxygen fugacity, respectively. Inserting EquationEquations. (2
(2a)
(2a) a)–(Equation2
(2c)
(2c) c) into
yields
(3)
(3) where Xji and γji are mole fraction and activity coefficient of i component in j phase, respectively. ΔG0f(RhO2) and R represent Gibbs energy of formation of RhO2 at temperature T and gas constant.
is partition coefficient of rhodium between Pd metal phase and Ru oxide phase. ΔG0f(RhO2) was measured by electro chemical cell in the temperature range from 850 to 1050 K [Citation38]. Based on these results and estimated value of heat capacity change, ΔC0P= 10 J K−1 mol−1, enthalpy and entropy of formation at 298 K [ΔH0f(298K) and ΔS0f(298K)] were calculated to be −244.94 kJ mol−1 and −191.48 J K−1 mol−1, respectively [Citation38]. Using these values, we calculated the ΔG0f(RhO2) between 1073 and 1473 K, and obtained the following equation:
(4)
(4) where T represents absolute temperature. shows comparison of the lnKRh determined by phase equilibrium experiments () with the values calculated from the Equations(3) and (Equation4
(4)
(4) ) at three different
conditions. Then
is assumed as unity since thermodynamic mixing properties for the Pd–Rh–Ru–Te and the (Ru, Rh)O2 solid solutions are not known.
Figure 7. Partition coefficient of Rh (KRh) between Pd metal and Ru oxide. Solid circle and open circle are results in air and in CO2 atmosphere, respectively. Open square represents the KRh calculated from crystal compositions in the KMOC glass. Dash lines are the KRh calculated from thermodynamic data assuming three difference oxygen fugacities: 0.21(air), 0.021 and equilibrium of CO2 dissociation. Errors are comparable to symbol size.
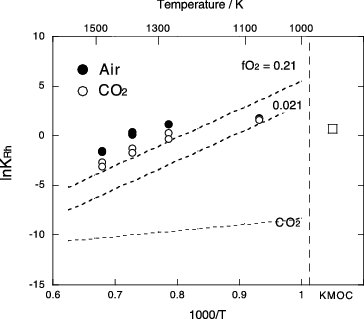
The partition coefficient of Rh determined by the experiments decreases with increasing temperature and decreasing oxygen fugacity. The lnKRh in air is slightly higher than the calculated partition coefficient at = 0.21. This indicates the actual value of
is less than 1. Slope of the lnKRh − 1/T plot () primarily depends on ΔG0f(RhO2) for the equilibrium reaction as expressed by EquationEquation (3)
(3)
(3) . Experimental lnKRh in air above 1273 K are close to calculated values, indicating that equilibrium was reached in these experiments. On the contrary to this, there is no difference between measured lnKRh in air and in CO2 at 1073 K, and these values are significantly smaller than that expected from low-temperature extrapolation of the lnKRh between 1273 and 1473 K. These facts suggest that the heating duration of 96 hours was too short to attain chemical equilibrium at 1073 K.
The discrepancy of the experimental lnKRh from calculated value is more significant for experimental results in CO2. The lower lnKRh in CO2 compared with that in air certainly suggests reduced oxygen fugacity. However, the difference between calculated and experimental lnKRh is probably too large to result in compositional dependence of or impurity oxygen in the CO2 gas. Therefore, we suspect that this discrepancy is caused by slow kinetics of redox reaction. Cochain et al. [Citation39] carried out in-situ high-temperature XANES observations of iron redox ratio in sodium-borosilicate melt, and determined redox diffusivity (Dred) of iron as a function of temperature and composition. They reported that the log Dred ranges from −9.6 to −11.6 between 1070 and 1570 K and decreases more than one order of magnitude as B2O3 increases in the range from 0 to 18 wt% at constant temperature. Assuming that the Dred of PGMs is similar to that of iron for 62SiO2–11B2O3–21Na2O–6FeO (wt%) melt [Citation39], the times required for redox equilibrium in molten glass by tube methods are expected to be 11 hours at 1473 K and 31 hours at 1273 K, which are comparable to heating duration in our experiments. However, if the Dred in multicomponent HLW glass is lower one order of magnitude than the simple sodium-borosilicate melt, the equilibration times become 10 times longer. Then our experimental duration would be too short to allow redox equilibrium. It has been considered that the iron redox reaction in silicate melt is rate limited by diffusion of network-modifier cations along with a counter flux of electrons [Citation40–43]. In RuO2-glass composites, electronic and ionic transport occurs over a wide temperature range even at very low Ru contents [Citation24]. Thus, the existence of Ru may affects mechanism of redox reaction, and the reaction kinetics in Ru-bearing silicate melts is possibly different from that in PGMs-free iron-bearing melts. Further studies are required to solve these points.
The experimentally determined partition coefficient between 1273 and 1473 K in air ( = 0.21) can be expressed as:
(5)
(5)
The above equation is nearly independent of the amounts of PGMs as long as that compositional dependence of is small. Therefore, it can be generally used for temperature estimate of the molten HLW glass. The lnKRh calculated from the crystal compositions in KMOC glass is 0.73(±0.03). Then the equilibrium temperature of the KMOC glass just before discharging is calculated to be 1320K from the EquationEqua-tion (5)
(5)
(5) at
= 0.21 (air). This is consistent with the temperature range estimated from crystal compositions described before (1273–1373 K), and nearly equal to the mean temperature of upper portion (1423 K) and lower portion (1223 K) in the KMOC melter [Citation23].
Another significance of EquationEquation (5)(5)
(5) is that the KRh is proportional to the oxygen fugacity at constant temperature. Ferric–ferrous ratio (Fe2+/ΣFe) of HLW glass has been used to evaluate redox state in vitrification melter [Citation44,Citation45]. The KRh can be used as another indicator of redox conditions. For example, if temperature of discharging molten glass is measured by a radiation thermometer, the oxygen fugacity could be roughly estimated by EquationEquation (5)
(5)
(5) from the discharging temperature and the chemical compositions of Pd metal and Ru oxide. We suggest that the partition coefficient of rhodium is useful to convert the chemical compositions of crystal phases into physical conditions (T,
) in the vitrification melter.
5. Summary
Phase equilibrium experiments were carried out using a simulated HLW glass containing Pd, Rh and Ru collected from a full-scale mock up facility. The relationship of chemical compositions of Pd–Rh–Ru–Te (Pd metal) and (Ru, Rh)O2 (Ru oxide) solid solutions was examined as a function of temperature and oxygen fugacity. The results are summarized as follows.
The chemical compositions and the amounts of Pd metal phase and Ru oxide phase are functions of amount of Pd, Rh and Ru in the glass, temperature and oxygen fugacity, whereas they are independent of composition of glass matrix.
RuO2 content in the Ru oxide phase increases and Pd content in the Pd metal phase decreases with increasing temperature and decreasing oxygen fugacity, which are caused by a progressive reduction of rhodium.
The partition coefficients of rhodium between Pd metal and Ru oxide (KRh) determined in air are slightly higher than those calculated from standard thermodynamic data of formation of RhO2, because of non-ideal mixing properties in Pd–Rh–Ru–Te and (Ru, Rh,)O2 solid solutions. The KRh can be used to convert chemical compositions of Pd metal and Ru oxide into temperature and oxygen fugacity in a vitrification melter.
Based on the comparisons of crystal compositions and KRh in the HLW glass with the experimentally determined values, it can be expected that the HLW glass examined in this study (KMOC glass) had been equilibrated in the temperature range from 1273 to 1373 K and oxygen fugacity close to that of air just before discharging from the melter.
Acknowledgements
This work was supported by Grant-in-Aid for Japan Nuclear Fuel Limited by the Ministry of Economy, Trade and Industry, Japan.
Disclosure statement
No potential conflict of interest was reported by the authors.
References
- Mitamura H, Murakami T, Banba T, et al. Segregation of the elements of the platinum group in a simulated high-level waste glass. Nucl Chem Waste Manag. 1983;4:245–251.
- Mitamura H, Murakami T, Banba T. Crystalline phases in a devitrified simulated high-level waste glass containing the elements of the platinum group. J Nucl Mater. 1985;136:104–116.
- Krause C, Luckscheiter B. Properties and behavior of the platinum group metals in the glass resulting from the vitrification of simulated nuclear fuel reprocessing waste. J Mater Res. 1991;6:2535–2546.
- Pentinghaus H. Behavior of platinum metal elements during the vitrification of HLLW by means of the LFCM technology. Paper presented at: International Topical Meeting on Nuclear and Hazardous Waste Management; 1994 Aug 14–18; Atlanta (GA).
- Roth G, Weisenburger S. Vitrification of high-level liquid waste: glass chemistry, process chemistry and process technology. Nucl Eng Des. 2000;202:197–207.
- Sundaram SK, Perez JM Jr. Noble metals and spinel setting in high level waste glass melters. Richland (WA): Pacific Northwest National Laboratory; 2000. (Report no.PNNL-13347).
- Rose PB, Woodward DI, Ojovan MI, et al. Crystallization of a simulated borosilicate high-level waste glass produced on a full-scale vitrification line. J Non-Crystalline Solids. 2011;357:2989–3001.
- Hartmann T, Pentinghaus H, The ternary system palladium-rhodium-tellurium: a study to understand phase formation in the vitrification process of high-level waste concentrates (HLWC). J Nucl Mater. 2012;422:124–130.
- Mukerji J, Biswas SR, Solubility of ruthenium in soda-silicate glass. Cent Glass Ceramic Res Inst Bull. 1967;14:30–34.
- Schreiber HD, Settle FA, Jamison PL, et al. Ruthenium in glass-forming borosilicate melts. J Less Common Metals. 1986;115:145–154.
- Akai T, Nishii J, Yamashita M, Yamanaka H. Chemical behavior of platinum-group metals in oxide glasses. J Non-Crystaline Solids. 1997;222:304–309.
- Borisov A, Danyushevsky L. The effect of silica contents on Pd, Pt, Rh solubilities in silicate melts: an experimental study. Eur J Mineralogy. 2011;23:355–367.
- Dé AK, Luckscheiter B, Lutze W, et al. Development of glass ceramics for the incorporation of fission products. Am Ceramic Soc Bull. 1976;55:500–503.
- Turcotte RP, Wald JW, May RP. Scientific basis for nuclear waste management, vol.2: advances in nuclear science & technology. New York (NY): Plenum Press; 1980.
- Ross WA, Bradley DJ, Bunnell LR, et al. Annual report on the characterization of high-level waste glass. Richland (WA): U.S. Department of Energy, Battelle-Memorial Institute, Pacific Northwest Laboratory; 1978. (Report no. PNL-2625).
- Izak P, Hrma P, Arey BW, Plaisted TJ, Effect of feed melting, temperature history, and minor component addition on spinel crystallization in high-level waste glass. J Non-Crystalline Solids. 2001;289:17–29.
- Vernaz E, Gin S, Veyer C. Waste glass. In: Konings RJM, editor. Comprehensive nuclear materials, Vol. 5. Oxford: Elsevier Science; 2012. p. 451–483.
- Pflieger R, Lefebvre L, Malki M, et al. Behaviour of ruthenium dioxide particles in borosilicate glasses and melts. J Nucl Mater. 2009;389:450–457.
- Yoshioka M, Torata S, Igarashi J, et al. Glass melter and process development for PNC Tokai vitrification facility. Waste Manag. 1992;12:7–16.
- Ikeda H, Endo N, Yoshioka M, et al. Cold test for improvement of the glass melter performance [in Japanese]. JNC Tech Rev. 2002;3:25–38.
- Kanehira N, Yoshioka M, Muramoto H, et al. Melter operation results in chemical test at Rokkasho Reprocessing Plant. Paper presented at: International Conference on Nuclear Energy Systems for Future Generation and Global Sustainability; 2005 Oct 9–13; Tsukuba, Japan.
- Kawamura T, Ito K, Sakai T, et al. Numerical analysis of platinum group particle behavior in vitrification melter [in Japanese]. Nihon-Genshiryoku-Gakkai Shi [J At Energy Soc Jpn]. 2008;7:297–307.
- Matlack KS, Gan H, Pegg IL, et al. Scaled melter testing of noble metals behavior with Japanese HLW streams. Ceramics Environ Energy Appl II. 2014;246:225–235.
- Simonnet C, Grandjean A. Mixed ionic and electronic conductivity of RuO2-glass composites from molten state to glassy state. J Non-Crystalline Solids. 2005;351:1611–1618.
- Luckscheiter B, Nesovic M, Development of glasses for the vitrification of high level liquid waste (HLLW) in a Joule heated ceramic melter. Waste Manag. 1996;16:571–578.
- Pegg IL, Gan H, Matlack KS, et al. Mitigation of yellow phase formation at the Rokkasho HLW vitrification facility. Paper presented at: Radioactive Waste Management. 36th Annual Symposium; 2010 Mar 7–11; Arizona (AZ).
- Gan H, Matlack KS, Pegg IL, et al. Suppression of yellow phase formation during Japanese HLW vitrification. Ceramics Environ Energy Appl II. 2014;246:237–250.
- Satoh H, Ishiyama D, Mizuta T, Ishikawa Y. Rare earth element analysis of rock and thermal water samples by Inductively Coupled Plasma Mass Spectroscopy (ICP-MS). Scientific and Technical Reports of Graduate School of Engineering and Resource Science, Akita University. 1999;20:1–8.
- Japanese Industrial Standards (JIS) R. 3105 Methods for chemical analysis of borosilicate glasses. 1995.
- Bale CW, Bélisle E, Chartrand P, et al. Fact sage thermochemical software and databases – recent developments. Calphad. 2009;33:295–311.
- Presnall DC, Brenner NL. A method for studying iron silicate liquids under reducing conditions with negligible iron loss. Geochim Cosmochim Acta. 1974;38:1785–1788.
- Corrigan G, Gibb FG. The loss of Fe and Na from a basaltic melt during experiments using the wire-loop method. Mineral Magazine. 1979;43:121–126.
- O'Neill HSC, Eggins SM. The effect of melt composition on trace element partitioning: an experimental investigation of the activity coefficients of FeO, NiO, CoO, MoO2 and MoO3 in silicate melts. Chem Geol. 2002;186:151–181.
- Sugawara T, Shiono T, Yoshida S, et al. Density measurement of simulated radioactive waste glass by the Archimedean immersion method using molten chloride salts. Phys Chem Glasses. 2013;54:270–278.
- Armstrong JT. Electron probe quantification. New York (NY): Plenum Press; 1991.
- Eyler LL, Lowery PS, Lessor DL, et al. Waste glass melter numerical and physical modeling. Paper presented at: International Waste Management Conference; 1991 Oct 21–26; Seoul, Korea.
- Choi IG. Mathematical modeling of radioactive waste glass melter. Paper presented at: Symposium on Nuclear Waste Management; 1991 Apr 28–May 2; Cincinnati (OH).
- Jacob KT, Prusty D, Thermodynamic properties of RhO2. J Alloys Compounds. 2010;507:L17–L20.
- Cochain B., Neuville DR, Ligny D, et al. Dynamics of iron-bearing borosilicate melts: effects of melt structure and composition on viscosity, electrical conductivity and kinetics of redox reactions. J Non-Crystalline Solids. 2013;373–374:18–27.
- Cook GB, Cooper RF, Wu T. Chemical diffusion and crystalline nucleation during oxidation of ferrous iron-bearing magnesium aluminosilicate glass. J Non-Crystalline Solids. 1990;120:207–222.
- Cooper RF, Fanselow JB, Weber JKR, et al. Dynamics of oxidation of a Fe2+-bearing aluminosilicate (basaltic) melt. Science. 1996;274:1173–1176.
- Magnien V, Neuville DR, Cormier L, et al. Kinetics of iron oxidation in silicate melts: a preliminary XANES study. Chem Geol. 2004;213:253–263.
- Roskosz M, Toplis MJ, Neuville DR, Mysen BO. Quantification of the kinetics of iron oxidation in silicate melts using Raman spectroscopy and assessment of the role of oxygen diffusion. Am Mineral. 2008;93:1749–1759.
- Schreiber HB, Hockman AL. Redox chemistry in candidate glasses for nuclear waste immobilization. J Am Ceramic Soc. 1987;70:591–594.
- Jantzen CM, Johnson FC. Impacts of antifoam additions and argon bubbling on defense waste processing facility (DWPF) reduction/oxidation (REDOX). Aiken (SC): Savannah River National Laboratory; 2012. (Report no.SRNL-STI-2011-00652).