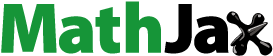
ABSTRACT
Impact limiters installed on nuclear spent fuel transport casks are used to absorb energy and limit overload during transport and accidents. The two-way corrugated aluminum honeycomb, a new kind of filler material, is designed based on the action mechanism of the impact limiter. Quasi-static compression tests are used to compare the properties of the honeycomb and the traditional filler material, paulownia wood. Experimental results indicated that the compressive and energy absorption properties of paulownia wood with axial wood grain and radial wood grain were very different. Also, the moisture content of paulownia wood led to a significant decrease in its properties. The two-way corrugated aluminum honeycomb, as a new porous material, showed better compression and energy absorption properties than paulownia wood in the x, y, and z directions. The peak stress (σpe), platform stress (σpl), and energy absorption capacity (WEA) were 2.10 times, 2.07 times, and 1.69 times higher than that of paulownia wood with axial wood grain. The two-way corrugated aluminum honeycomb is a filler material that has essential application value in impact limiters of spent fuel transport casks.
1. Introduction
In recent years, there has been a ‘nuclear renaissance’ due to the perception of nuclear power as a kind of green renewable energy. Hence, the nuclear power is predicted to experience large-scale development in the coming decades [Citation1–Citation3]. However, massive scale nuclear energy construction leads to the production of a large amount of spent fuel. Spent fuel decays, has high radioactivity, and contains a considerable amount of fissile material that can cause great harm if not handled properly [Citation4,Citation5]. Thus, there will be a need for high safety spent fuel transport casks. To ensure the integrity of a transport cask under normal transport and accident conditions, the International Atomic Energy Agency (IAEA) issued the ‘Regulations for the Safe Transport of Radioactive Materials’ document [Citation6]. In addition, China had developed the GB11806 standards based on this document [Citation7]. A transport cask needs to be tested and withstand a 9-m fall test, a 1-m penetration test, a 30-min fire (800°C), and a 200-m immersion test. In the first test, the cask needs to withstand a 9-m free fall onto an unyielding surface. This requires the addition of a pair of impact limiters installed on the top and the bottom of the transport cask to absorb most of the impact energy and limit overload, which can ensure the integrity of the cask structure.
Many scholars have studied several types of impact limiter filler materials. Zhou et al. [Citation5] designed and studied China’s RY-I type spent fuel transport cask in experiments that used paulownia wood to replace light wood as the impact limiter filler material. Vural and Ravichandran [Citation8] studied and analyzed the dynamic response and energy dissipation characteristics of balsa wood. Silva and Kyriakides [Citation9] evaluated the compressive response and failure behavior of balsa wood based on its microstructure. They found that the internal structure of balsa wood was composed of slender cells with similar hexagonal cross-sections that were arranged axially. Choi and Seo [Citation10] conducted dynamic impact experiments on polyurethane foam, honeycomb, and balsa wood. The experimental results showed that balsa wood with axial wood grain absorbed the most significant amount of energy. Yin et al. [Citation11] studied the design of a high fuel consumption spent fuel transport cask that used fir and light wood as the main filler materials for the impact limiter.
The filler material used for the impact limiter of transport casks has primarily been wood, and the application of other materials has rarely been investigated. In this study, paulownia wood and a new porous material, two-way corrugated aluminum honeycomb, are selected as test materials based on the action mechanisms of impact limiter filler materials. Then, comparison tests are performed to investigate their properties.
2. Materials and methods
2.1. Paulownia wood
Clear-grained paulownia wood, without knots and splits, was selected as the experimental material. To avoid the influence of friction and inertia effects, the paulownia wood samples were made into cuboid structures by sawing and sanding. The samples produced were then marked as PW1, PW2, PW3, and PW4. Additionally, the PW3 and PW4 samples were immersed in clean water for 2 h and 6 h, respectively, at atmospheric pressure and room temperature [Citation12]. Then, the relative moisture content of the PW3 and PW4 samples was calculated based on EquationEquation (1(1)
(1) ). The parameters of specific samples are shown in . The following equation calculates the relative moisture content:
Table 1. Experimental parameters of the paulownia wood samples
where w is the relative moisture content of paulownia wood; mwet is the quality of wet paulownia wood; and mdry is the relative quality of dry paulownia wood.
2.2. The two-way corrugated aluminum honeycomb
A corrugated box is characterized by lightness, firmness, shock absorption, and easy mechanization [Citation13,Citation14]. These characteristics were combined with the high energy absorption of a traditional aluminum honeycomb [Citation15] to put forward the two-way corrugated aluminum honeycomb. A complete hexagon hole was divided into two trapezoid holes that were corrugated and placed in two orthogonal directions. Therefore, this material is called the two-way corrugated aluminium honeycomb, and its structure is shown in .
In this study, 3003 aluminum alloys with good formability and corrosion resistance were used as the experimental material [Citation16]. A roll forming machine was used to roll the aluminum sheets into corrugated sheets with a smooth surface, precise size, and regular structure. At the same time, the aluminum sheets were cut into a same size. The two sheets were then bonded together with aviation glue after the surfaces of the corrugated sheets and the aluminum sheets were ground. Then, repeating the above operations, the corrugated sheets were glued to two sides of the aluminum sheets orthogonally. Finally, the two-way corrugated aluminum honeycomb product was obtained by packing. The specific manufacturing process is shown in .
The samples used in this experiment were labeled TCH5, TCH6, and TCH7. The size of each sample was 85 × 55 × 85 mm3, and the density was 1,070 kg/m3 for TCH5, 1,040 kg/m3 for TCH6 and 1,102 kg/m3 for TCH7. The primary parameters of the two-way corrugated aluminum honeycomb are shown in .
2.3. Methods
Quasi-static compression tests were conducted to verify the compressive properties of the two materials under different conditions, and the energy absorption properties of the two materials were then calculated. The tests were implemented using a universal testing machine (YAW-3000A) under a pressure head speed of 5 mm/min (the strain rate was 9.8 × 10−4 s−1) up to ε = 0.8, which ε defined as nominal strain. The specific experimental design is shown in .
Table 2. Design of the quasi-static compression experiment
3. Results and discussion
3.1. Deformation processes
shows the deformation process of the seven samples under different strains. It can be observed that the deformation of the PW1, PW3, and PW4 samples are primarily buckling deformations, but they are slightly different. The buckling deformation of the PW1 sample begins in the middle portion of the sample. When ε = 0.4, a cracking deformation appeared in the inner and both sides of the PW1 sample, and it was accompanied by a buckling deformation during the subsequent deformation process. Nevertheless, the deformations of PW3 and PW4 samples are similar. The buckling deformation of them began from both ends of the sample at about the same time, and obvious cracks did not appear during the process. However, under the influence of moisture content, the absorbed water softened the cell wall, which resulted in a total tilt when ε = 0.4. This event resulted in the middle portions of two samples no longer subject to buckling deformation during the later stage. The deformation process of the PW2 sample was smooth and steady. The whole deformation process consisted of a compact accumulation of transverse fibers without an obvious yield procedure. From the left and top views of the compressed PW1 sample (), it can be seen that, apart from the buckling deformation, three local deformation behaviors occurred. These included tensile cracking (marked 1 and 3), unchanged behavior (marked 2), and densification (marked 4) that occurred during the entire deformation process. In addition, because paulownia wood has a positive Poisson’s ratio, the cross-sectional area increased after the compression test and the increased area was the area outside the red wire frame, as shown in ).
shows that the deformation processes of the TCH5 and TCH6 samples are roughly the same. Under compressive loads, TCH5 and TCH6 conducted elastic deformation during the initial stage. After the yield stress had been reached, deformation was initiated in the weaker regions, where several local deformations formed. These deformations included the following: (i) Buckling (marked 1 in )) is the main form of a quasi-static compression process. When the load exceeded the yield limit of the two-way corrugated aluminum honeycomb, the high plastic corrugated sheet began to buckle along the two sloping sides of the trapezoid hole as a plastic hinge, rather than an instant burst [Citation17,Citation18]. (ii) When ε = 0.2, the excessive transverse force at the edge of the sample caused cracking in the left side, which eventually formed the fracture deformation shown in ) (marked 2), and the behavior resulted in the original sample had no change (marked 3). (iii) Due to the slight cracking on the left and right sides, the curvature of the buckling deformation was enlarged. This resulted in the corrugated sheet being leveled and compacted during the densification stage, as shown in ) (marked 4 and 5). In addition, during the compression process, the deformation of the two-way corrugated aluminum honeycomb began at the end face and then subsequently collapsed in turns. The reason for this is because the pore structures of the honeycomb aluminum at the edges are incomplete, and the strength is relatively low here, leading to the formation of a stress concentration easily. The difference between the two samples was that the deformation in TCH5 was from the bottom to top, while in TCH6, it was the opposite. However, the result of this experiment was not affected by the difference. ) shows the outer area of the red line box, and this area is the increased area of sample after compression, indicating that the two-way corrugated aluminum honeycomb material had a positive Poisson’s ratio. The deformation process of the TCH7 sample was approximately the same as that of the PW2 sample. It was caused by a stack of buckling deformations in the layers with corrugated holes. Since the height of a corrugation hole is small, a brief yield stage was observed.
3.2. Compression property
The stress-strain curves of two kinds of materials under quasi-static compression tests are plotted in . The figure shows three typical stages: i) elastic deformation stage, ii) yielding plateau stage, and iii) densification stage.
Figure 7. Compressive property curves of two materials under various strains: (a) paulownia wood; (b) two-way corrugated aluminum honeycomb.
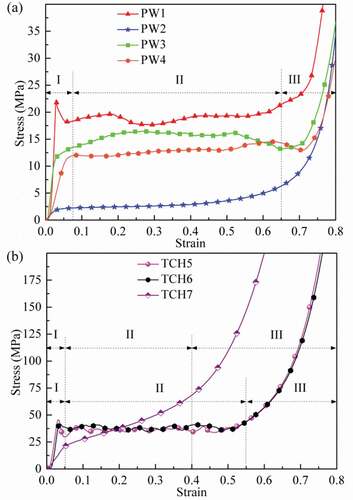
As shown in ), the property curve of the PW1sample is located at the top of the four curves, while the property curve of the PW2 sample is on the bottom. The property curve of the PW3 sample is slightly higher than that of PW4, and these two curves lay in the middle region. Accordingly, this result shows that paulownia wood with axial wood grain has a good compression property, but the compressive property of paulownia wood with radial wood grain is inferior. In addition, the compressive property of paulownia wood is affected by moisture content. The compressive property of PW3 with a moisture content of 22.3% was slightly higher than that of PW4, with a moisture content of 38.2%. Since the fiber saturation point of wood is generally 30% [Citation12], after reaching the fiber saturation point, the compression property was stable and no longer changed with an increase in moisture content. Nevertheless, the moisture content of PW3 and PW4 was on both sides of the fiber saturation point. Therefore, the curve of PW3 is slightly higher than that of PW4, but the curve of PW4 is more stable than that of PW3.
) shows the stress-strain curves of the two-way corrugated aluminum honeycomb in the x, y, and z directions. The property curves of the TCH5 and TCH6 samples are similar. The property curve of the latter is slightly higher than that of the former, and the fluctuation of the latter is somewhat less than that of the former. This demonstrates that the two-way corrugated aluminum honeycomb has similar compressive properties in two directions, and the compressive properties are very prominent. In addition, different from the TCH5 and TCH6 samples, the property curve of the TCH7 sample is a smooth upward curve with a short yielding plateau stage.
To compare and characterize the test data of the two materials under different conditions, the peak stress (σpe) and the plateau stress (σpl) were selected as the main parameters for comparison in compressive property. σpe is defined as the highest stress point during the elastic deformation stage, and σpl is defined as the average stress of strain between 0.2 and 0.4 [Citation19]. The above parameters were statistically calculated, and the obtained data are shown in .
Table 3. The peak stress (σpe) and the plateau stress (σpl) of two materials under various conditions
As shown in , the maximum values of σpe and σpl are 45.65 MPa (TCH5) and 50.88 MPa (TCH7). Among them, σpe and σpl of PW1 are approximately 10 times that of PW2, while the differences between σpe and σpl of TCH5 and TCH7 are just 2.18 times and 0.72 times, respectively. Additionally, the σpe and σpl of TCH6 are similar to those of TCH5. Also, the σpe and σpl of TCH5 are 2.10 and 2.07 times of that of the PW1, respectively, and the σpe and σpl of TCH7 are 10.25 and 19.35 times that of PW2, respectively. Obviously, paulownia wood with axial wood grain has a good compressive property, but the compressive property of paulownia wood with radial wood grain is poor. However, the two-way corrugated aluminum honeycomb displayed outstanding compressive properties in all three directions, and it was higher than that of the paulownia wood. In addition, the σpe and σpl of PW3 and PW4 compared to that of PW1 decreased nearly two times. Accordingly, the moisture content of paulownia wood also significantly reduced the compressive property, while the two-way corrugated aluminum honeycomb, as we all know, could not be affected by this factor.
3.3. Energy absorption property
To compare the advantages and disadvantages of the two materials in different situations more clearly, the energy absorption capacity (WEA) was applied to characterize the energy absorption property of the materials, defined as:
where ε is the strain and σ (ε) is the stress at the strain.
The energy absorption capacities of PW1, PW2, PW3, PW4, TCH5, TCH6, and TCH7 were defined as WEA1, WEA2, WEA3, WEA4, WEA5, WEA6, and WEA7, respectively. shows the energy absorption properties of two materials under different conditions. The order of the energy absorption capacity is WEA5 > WEA6 > WEA7 > WEA1 > WEA3 > WEA4 > WEA2. As shown in , WEA1 is 6.09 times higher than WEA2, 1.24 times higher than WEA3, and 1.53 times higher than WEA4. Thus, the energy absorption property of paulownia wood was not only affected by the grain of direction, but also the moisture content led to a decline in this property. However, WEA5 is 1.69 times higher than WEA1, WEA7 is 7.70 times higher than WEA2, and WEA7 is only 5.13 × 103 KJ/m3 less than WEA5. The results indicated that the two-way corrugated aluminum honeycomb showed good energy absorption capacity, and the energy absorption properties were higher than that of paulownia wood, whether it was in the x, y, or z direction.
Table 4. Energy absorption capacities (WEA) of two materials under various conditions
4. Conclusion
Paulownia wood with axial wood grain had good compression and energy absorption properties, but wood with radial wood grain was very poor. Also, the moisture content of the wood significantly reduced these properties. Therefore, the properties of paulownia wood were not only limited by the direction, but also changed with the environment. If this wood was used as a filler material for an impact limiter, it would be difficult to achieve the high safety requirements required for the transport process and accident conditions.
As a new type of porous material, the two-way corrugated aluminum honeycomb showed excellent compression and energy absorption properties in three directions. In addition, the manufacturing process is simple, and it is easy to control the parameters. The peak stress (σpe), platform stress (σpl), and energy absorption capacity (WEA) were 2.10 times, 2.07 times, and 1.69 times higher than that of paulownia wood with axial wood grain. The two-way corrugated aluminum honeycomb can not only have good compression property in all three directions, but the honeycomb is not affected by environmental factors. Therefore, it has enormous potential to be a filler material, and more studies should be conducted to advance its widespread application.
Acknowledgements
This work was supported by the Natural Science Foundation of Shandong Province under Grant [number ZR2018MEM006] and China Postdoctoral Science Foundation [number 2018M642683].
Disclosure statement
No potential conflict of interest was reported by the authors.
References
- Adamantiades A, Kessides I. Nuclear power for sustainable development: current status and future prospects. Energy Policy. 2009;37(12):5149–5166.
- Ahearne JF. Prospects for nuclear energy. Energy Econ. 2011;33(4):572–580.
- Salvatores M. Future nuclear power systems and nuclear data needs. J Nucl Sci Technol. 2002;39(sup2):4–12.
- You G-S, Choung W-M, Ku J-H, et al. Design and construction of an advanced spent fuel conditioning process facility (ACPF). Nucl Eng Technol. 2009;41(6):859–866.
- Zhou Y, You M, Zhang Y, et al. RY-I 型乏燃料运输容器研究试验 [Study and test on RY-I type transport cask for spent fuels]. China Nucl Sci Technol Rep. 1993;8(00):315–325. Chinese.
- IAEA. Regulations for the safe transport of radioactive material. Standard no. TS-R-1: 2009.
- AQSIQ and SAC. Regulations for the safe transport of radioactive material. Standard no. GB11806–2004: 2014.
- Vural M, Ravichandran G. Dynamic response and energy dissipation characteristics of balsa wood: experiment and analysis. Int J Solids Struct. 2003;40(9):2147–2170.
- Silva AD, Kyriakides S. Compressive response and failure of balsa wood. Int J Solids Struct. 2007;44(25):8685–8717.
- Choi W-S, Seo K-S. A simple sizing optimization technique for an impact limiter based on dynamic material properties. Nucl Eng Des. 2010;240(4):925–932.
- Yin Y, Li Q, Ma Q. 高燃耗乏燃料运输容器结构设计研究 [Study on the structural design of high burnup spent fuel transport cask]. Chin J Nucl Sci Eng. 2017;37(2): 308–313. Chinese.
- Hou Z, Guan N, Zhang L, et al. Water sorption behaviors of five woods above fiber saturation point. Chin For Sci Technol. 2003;2(2):35–40.
- Hong L, Cheng L. 瓦楞纸箱工艺 [Discussion on corrugated paper box technics]. Packag Eng. 2007;28(12): 282–285. Chinese.
- Frank B. Corrugated box compression—a literature survey. Packag Technol Sci. 2014;27(2):105–128.
- Cai M, Gao Q, Zong Z. 铝合金蜂窝结构轴向压缩吸能特性 [Energy absorption properties of honeycomb structured aluminum under axial compression]. J Mater Sci Eng. 2015;33(5): 675–679. Chinese.
- Pan F, Zhang D. 铝合金及应用 [Aluminum alloy and its application]. Beijing: Chemical Industry Press; 2006. Chinese.
- An Y, Yang S, Wu H, et al. Investigating the internal structure and mechanical properties of graphene nanoflakes enhanced aluminum foam. Mater Des. 2017;134:44–53.
- An Y, Yang S, Zhao E, et al. Characterization of metal grid-structure reinforced aluminum foam under quasi-static bending loads. Compos Struct. 2017;178:288–296.
- British Standards Institution (BSI). Mechanical testing of metals-ductility testing-compression test for porous and cellular metals. London: BSI; 2011. Standard No. ISO 13314: 2011.