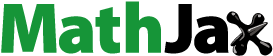
ABSTRACT
Manganese is a standard alloy element in many wrought steels, offering improved strength and hardenability and, in Hadfield steels, also a unique combination of strength, ductility and work hardening behaviour. In sintered steels Mn has been used rarely so far because of two reasons: one is the high oxygen affinity of Mn which promotes oxygen pickup during heat treatment and inhibits removal of oxygen in part through the ‘internal getter’ effect. The other reason is the high vapour pressure of Mn which results in Mn loss during sintering. In this presentation, these problems are discussed on Mn-alloyed sintered steels with transformation-induced plasticity behaviour. It is shown that by suitable alloying techniques, combined with adjustment of the manufacturing parameters, the problems can be overcome and the benefits of Mn addition can be reaped, obtaining PM steels for which potentially surface densification and hardening can be attained in one run.
Introduction
Manganese is a very common alloy element in steels produced by ingot metallurgy (IM) – in fact so common that steel grades containing up to 0.4% of Mn are still regarded as ‘unalloyed’ [Citation1]. The reasons for the widespread use of Mn in steel metallurgy – in part also for cast iron – are its low price, its hardening effect in the ferrite lattice and its high Grossmann factor, which significantly improves the hardenability. In that respect, Mn is the most effective of the common alloy elements for steels [Citation2]. Mn is also contained by many modern steel grades, such as e.g. dual phase, transformation-induced plasticity (TRIP) and twinning-induced plasticity (TWIP) steels used, e.g. as sheets for producing car bodies [Citation3–5]. A unique class of Mn steels are the so-called Hadfield steels, grades with high Mn and C levels, typically 12%Mn and 1.2%C, which are rather soft as-quenched but present excellent work hardening capability while retaining toughness [Citation6–9]. In this class of steels, Mn is in fact indispensable as alloy element.
In sintered steels, in contrast, Mn has been used rarely, although its benefits have been recognised very early, in particular by Andrej Šalak [Citation10] who thoroughly studied Mn alloying of sintered steels for decades, starting in the 1970s (e.g. [Citation11–16]). The main problem usually associated with Mn in powder metallurgy (PM) is its high oxygen affinity, the Gibbs free energy of formation for the most stable oxide MnO being more negative than that of Cr2O3 and only slightly less than that of SiO2 [Citation17]. This plays a much more critical role for sintered steels as compared to IM grades since in PM the temperatures are lower (and thus less favourable for carbothermal reduction of oxides), and the specific surface is much higher, enhancing the reactivity towards the environment, in particular the sintering atmosphere.
This reactivity of PM compacts is the main reason why the traditional alloy elements for sintered steels have been those with fairly low oxygen affinity, which means low stability of the oxides. Today, a major proportion of all ferrous PM parts are based on Fe–Cu–C usually prepared through the mixing route. For higher requirements towards mechanical properties, diffusion bonded grades Fe–Ni–Cu–Mo–C are highly popular [Citation18]. The oxides of these elements are less stable than the iron oxides, and sintering conditions that result in the reduction of the ‘natural’ oxide content of the base iron powders also cause reduction of the alloy element oxides (which process usually even goes unnoticed). On the other hand, these alloy elements are expensive and suffer from volatile prices [Citation19], furthermore, Cu is problematic during steel recycling, and Ni is classified as carcinogenic.
Therefore, choosing alternative alloy elements has been a focus in ferrous PM for a considerable time. Initially, the interest of the ferrous PM community concentrated on Cr, both mixed [Citation20] and prealloyed [Citation21,Citation22] variants being studied. The latter route was further supported by the availability of reasonably cheap water atomised Cr–Mo and Cr-prealloyed powders in the 2000s [Citation23,Citation24]. Here, one benefit was the fairly low hardening effect of Cr in the ferrite lattice and another the lower chemical activity – and thus oxygen affinity – of Cr in prealloyed powders compared to elemental Cr. However, also Mn has been combined e.g. with Cr [Citation25–27], Mo [Citation28,Citation29] or Si [Citation30,Citation31], and in part very attractive mechanical properties have been attained, but acceptance in industrial practice has been sluggish.
Effects of manganese vapour pressure
One peculiar feature of manganese is its high vapour pressure which is much higher than that of all other elements employed in ferrous PM, as can be seen in . This plays a considerable role in sintering since Mn evaporation is a natural and inevitable effect. Mn loss occurs predominantly at the surface where Mn alloying is usually needed most to ensure hardness, strength and wear resistance. In that respect, the effects of Mn evaporation can be roughly compared to those of surface decarburisation.
Table 1. Vapour pressure (in Pa) of elements used in ferrous powder metallurgy at different temperatures [Citation10].
On the other hand, Mn evaporation can also be regarded as positive, due to the so-called ‘self-getter effect’ described by Šalak. Mn vapour forms a shell around the specimens, gettering all oxidising species in the atmosphere before they can reach the surface of the specimen. A reaction front is formed in which the concentration of oxidising species – especially O2 and H2O – and of Mn vapour are minimum (schematically described in [Citation16] ). The distance of this reaction front from the surface depends on the Mn vapour pressure – primarily defined by the temperature – as well as on the O2 and H2O concentrations in the atmosphere. This self-getter effect is discernible by a layer of MnO dust on the surface of the PM component. It enables sintering of Mn alloyed steels also in atmospheres that would be regarded too impure – too oxidising – with regard to the high oxygen affinity of Mn. The price to be paid is, however, the Mn loss mentioned above.
Another positive effect of the high Mn vapour pressure is the accelerated homogenisation during sintering when starting from powder mixes. If the alloy elements are added either as elemental powders, as masteralloys or as diffusion bonded, the system is initially chemically heterogeneous. In this situation, if the alloy elements are to be evenly distributed in the iron lattice, this has to be attained during sintering. Solid-state diffusion is the usual mechanism but is particularly slow in case of Mn since the diffusion coefficient of Mn in austenite at the common sintering temperatures is rather low, similar to that of Ni [Citation32]. Sintering with a transient liquid phase is a frequently used mechanism to accelerate homogenisation, but it requires exceeding a certain temperature threshold that is moderate for Cu [Citation33] but fairly high for Mo, Cr, W and V (e.g. [Citation34]). In case of Mn, homogenisation within the porous skeleton of the ferrous matrix occurs through gas phase transport. The Mn vapour fills the pore space and is deposited on the surfaces of the base metal particles, as can be clearly seen in depicting an Mn-alloyed sintered steel after short-time sintering. The smaller Fe particles are more or less completely alloyed with Mn, while the larger ones exhibit a regular surface layer alloyed with Mn but the cores are plain iron. This shows that the Mn vapour can afford the regular coating of all base powder particles with Mn, while the complete homogenisation has to be afforded by solid-state diffusion. Nevertheless, the diffusion distances are much smaller there than if Mn would have to cover also the interparticle distances by solid-state diffusion.
Figure 1. PM steel Fe-4%Mn-0.3%C, sintered 10 min at 1120°C (water atomised Fe, electrolytic Mn) [Citation34].
![Figure 1. PM steel Fe-4%Mn-0.3%C, sintered 10 min at 1120°C (water atomised Fe, electrolytic Mn) [Citation34].](/cms/asset/ce636521-a89c-43db-b90c-54914e219379/ypom_a_1886717_f0001_ob.jpg)
As stated above, Mn is transported from the Mn carrier particles to the Fe surfaces, but the reverse transport of Fe is not possible due to the very large differences of the vapour pressures of Mn and Fe, about 4 orders of magnitude according to . This, however, means that Mn is transported also to the sintering necks into which additional material is introduced, which results in a displacement of the particle centres and thus in macroscopic swelling (e.g. [Citation31]). This ‘Mn swelling’ is roughly similar to the well-known ‘copper swelling’ caused by transient liquid phase. The difference is that there is not a sharp onset of swelling above a given temperature, as in case of Cu, but the expansion is gradual, increasing with temperature, as shown in [Citation34]. This Mn swelling might be useful for sintering to zero dimensional change, similar to Cu used today.
Alloying techniques
When sintering Mn-alloyed steels, it should be considered that there is always a compromise to be found regarding the sintering conditions, in particular the temperature. On one hand, high temperatures are required to reduce the stable oxides present on the Mn carrier particles from the beginning (each metal powder that has been exposed to air carries oxygen), and those oxides that are formed during sintering as a consequence of the ‘internal getter’ effect (see below). In both cases, temperatures >1100°C are required to ensure carbothermal reduction, higher temperature strongly enhancing the reduction process. High temperatures also enhance Mn homogenisation. On the other hand, higher temperatures of course promote Mn evaporation and thus Mn loss at the surface.
One solution to this dilemma is the alloying technique. Compared to IM, PM offers more options to introduce alloy elements into a base metal. Here, variants in which Mn is present in lower concentration – and thus lower chemical activity – than in elemental Mn are beneficial. Lower chemical activity implies both lower vapour pressure and less tendency to oxidation/easier reducibility of the oxides (since the generated Mn metal is more easily dissolved in the matrix).
Against that background, prealloying would be the optimum solution since in this case the Mn concentration is the lowest among all options. However, here it must be considered that in contrast to e.g. Cr or Mo, Mn has a strong hardening effect on the ferrite lattice (see [Citation35] p.202), which means that prealloyed powders are significantly less compactible than, e.g. plain Fe or Cr / Mo prealloyed powders. As will be shown below, this effect is less critical than generally assumed, and prealloying is therefore a feasible way for low Mn levels, but the threshold is at 2%Mn maximum [Citation36].
Adding Mn as elemental powder, e.g. fine electrolytic Mn, usually offers better green density, but as stated above the risk of Mn loss through evaporation is higher and also removal of the natural oxygen content is more difficult. Furthermore, it has been shown that near the location of Mn particles, oxygen enrichment at the grain boundaries occurs, promoting intergranular failure [Citation37]. Here, using ferromanganese as Mn carrier proved to be helpful [Citation38], even the moderate reduction of the Mn content from 100% in electrolytic Mn to typically 80% in the common Ferro-Mn grades significantly lowering the problems encountered with elemental Mn. Another attractive route is the use of masteralloys that contain not only Mn but also other alloy elements such as Cr and/or Si. This route has been tried already in the 1970s by Zapf, Thümmler et al. [Citation39–42], but today, advanced atomisation techniques have made this route more economical [Citation43,Citation44]. Furthermore, by the use of thermodynamic software, low-melting compositions can be defined that enable homogenisation through transient liquid phase, which acts similar to gas phase transport while avoiding Mn loss through evaporation [Citation45]. Of course, the ‘self-getter effect’ cannot be used any more here since Mn does not (and should not) evaporate any more. But since for advanced high strength PM steels the purity requirements for the atmosphere are strict anyhow, the self-getter effect does not offer sufficient advantages to compensate for the unwelcome loss of superficial Mn.
Furthermore, it should be considered that in all cases when systems with heterogeneous oxygen affinity are used – and thus in all alloying techniques except prealloying – the ‘internal getter effect’ occurs, i.e. transfer of oxygen from the base powder – Fe or low alloy steel – to the Mn carrier particles. As shown e.g. in [Citation46], reduction of the iron oxides occurs at relatively low temperatures, for carbothermal reduction at about 700–800°C, resulting in an atmosphere with a CO partial pressure that is at first defined by the reaction between iron oxide and carbon. However, this atmosphere is strongly oxidising for the alloy elements, e.g. Mn (see (a)), and the CO generated immediately reacts with adjacent Mn carrier particles, oxidising them, as shown schematically in (b). The reactions are:
The net reaction therefore is:
In fact this is simply a metallothermic reduction of iron oxide by Mn, CO acting just as a transfer medium.
Macroscopically this means that for deoxidation of the powder compacts, conditions are required that apply for the reduction of the oxides of Mn and not of Fe. This can be seen in , depicting the mass spectrometry m28 (CO) and m44 (CO2) signals as well as the mass signals for Fe–C and Fe–C–4%Mn. In case of plain Fe–C ((a)), two clearly defined reduction peaks are evident, one at about 800°C, indicating reduction of the surface oxides, and the other a broader one with a maximum at about 1100°C, which signals a reduction of internal and interparticle oxides. In presence of 4%Mn admixed, in contrast ((b)), only one single large peak is evident with its maximum at 1200°C. This clearly shows that although also in this latter specimen the iron oxides have been reduced carbothermally in the temperature ranges shown in (a), the CO generated cannot escape from the pore channels (and thus be detected by mass spectrometry) before being gettered by the Mn particles, and the reduction peak externally visible in fact shows the reduction of MnO. The practical conclusion is that for Mn alloyed steels the reduction behaviour is rather similar for prealloyed and mixed systems, in both cases reduction of the Mn oxides being the crucial process that determines oxygen removal.
Manganese alloyed steels with TRIP behaviour
As stated above, Mn low alloy steels offer attractive mechanical properties, but these can also be attained by using other alloy elements such as, e.g. Cr or Mo. There are, however, Mn alloyed steel grades that are unique, such as, e.g. the Hadfield steels with their specific work-hardening behaviour. Mn steels with slightly different Mn and C contents can be adjusted such to exhibit the TRIP effect, i.e. transforming to martensite if deformed. This offers particular advantages for PM precision parts that are surface densified locally, such as gears. Today, such parts are produced by sintering, surface rolling and then thermochemical heat treatment such as carburising or carbonitriding [Citation47]. When using the TRIP effect it might be feasible to combine densification and surface hardening by using the transformation to martensite occurring during deformation to increase the surface hardness [Citation48].
For producing this class of materials through the PM route, the problems associated with Mn as described above are multiplied compared to low alloy steels. Therefore, these materials are excellent examples for describing how to handle these problems, and their production is described in detail here.
Assessment of TRIP behaviour
In order to estimate the relationship between composition and TRIP behaviour, specimens were produced using Carbonyl iron (BASF CN) as base powder and electrolytic Mn; carbon was added as fine natural graphite (Kropfmühl UF4). The powders were mixed and compacted at 600 MPa to bars ISO 5754. Sintering was done at 1400°C for 60 min, to ensure homogeneous Mn distribution (the surface demanganizing was at first neglected for this run). Since for TRIP behaviour both austenite-stabilising elements, Mn and C, are relevant, the nominal Mn content was held constant at 12% – corresponding to the well-known Hadfield steels –, and the admixed C content was varied between 0.2 and 0.8%. After sintering, the specimens were deformed by cold rolling in order to assess the deformation and transformation behaviour, respectively.
The rolling tests showed that at lower C contents, deformability is insufficient, rolling resulting in crocodiling as shown in (a). At 0.2%C, this occurred already in the first pass, at 0.4%C in the second. At 0.6%C, in contrast, the specimens could be cold rolled in five passes without cracking, and the same was observed for 0.8%C as shown in (b).
Figure 4. Fe-12%Mn-x%C, compacted at 700 MPa, sintered 60 min at 1400°C, cold rolled. (a) Fe-12%Mn-0.2%C, rolled, after 1 pass. (b) Fe-12%Mn-0.8%C, rolled, after 5 passes.
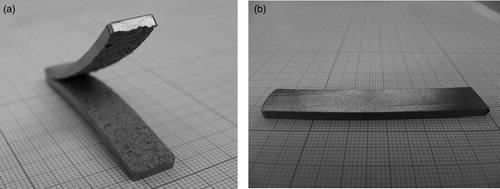
To check the transformation behaviour, the magnetic saturation was measured using a Foerster Koerzimat [Citation49]. This technique is well established for determining retained austenite in steels. In the present case, the results have to be regarded with some caution since this is an integral measurement, i.e. transformations that occur predominantly at the surface will be partially masked by the untransformed core regions. Furthermore, also the problem of the reference material (i.e. the austenite-free material with the same composition) arises [Citation49], since in the present case such a material simply does not exist; therefore, plain iron was used as reference, which also introduces an error. Nevertheless, at least qualitative trends should be noticeable. In (a), the magnetic saturation is shown for different C contents and as-sintered as well as after rolling. As can be seen, at very low C levels, the steel is partially martensitic already as sintered, and after one rolling pass, almost the entire specimen has turned into martensite, which explains the poor deformability. At 0.4%C the steel is virtually austenitic as sintered, but also here the martensite content increases dramatically even after one pass, indicating low stability of the austenite. In case of 0.6%C, transformation from a fully austenitic state is gradual, the fraction of ferromagnetic phase (martensite) increasing with the number of passes, which means that here controllable TRIP behaviour is attained. At 0.8%C, finally, the materials remains fully austenitic even after five passes, i.e. in this case the carbon content stabilises the austenite to a degree that TRIP is suppressed.
Figure 5. Magnetic saturation, apparent hardness and microhardness of Fe-12%Mn-x%C as sintered and after rolling. Compacted at 600 MPa, sintered 60 min at 1400°C.
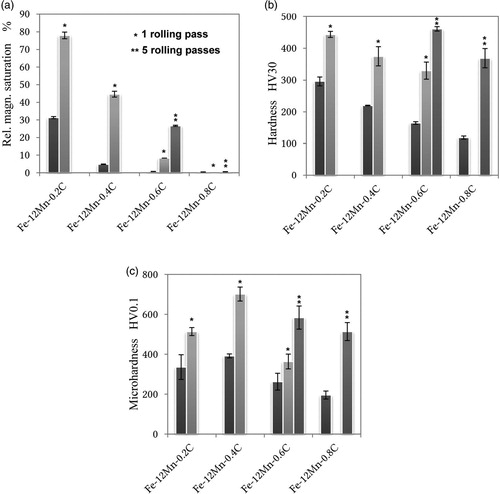
When comparing the apparent hardness data ((b)), it is evident that in the as-sintered state HV30 steadily decreases with higher C content, as would be expected from the dropping martensite content. By rolling the hardness is increased in all cases, in part by transformation, in part by work hardening, but the maximum hardness is attained for 0.6%C where both effects are combined. For the microhardness ((c)), lower C levels are slightly better, the maximum HV0.1 being attained at 0.4%C. This indicates that for the apparent hardness also densification plays a major role and not only the hardness of the matrix alone. In any case, it could be shown that even already in this first, very tentative, test run, microhardness levels of up to >700 HV0.1 could be reached.
Selection of the base powder
If regular TRIP behaviour is aimed at, homogeneous Mn distribution should be attained. As discussed above, coarser powder particles might be problematic here since their cores are Mn alloyed rather slowly and at least only when sintering at high temperatures, at which Mn loss is more probable regarding the high Mn contents – and thus activities – present here. Therefore, using fine Fe powders as base seemed to be advisable, both regarding the homogeneity and the high sintering activity which promises high relative densities after sintering, and Carbonyl iron was therefore used for the first experiments.
Although the specimens thus produced could be sintered and in part also rolled, as shown above, it was found that using Carbonyl Fe as base powder bears risks during sintering because of collision between deoxidation and densification. As is known also from other systems, e.g. hardmetals [Citation50], densification that results in closed porosity before oxygen removal is complete tends to result at least in insufficient reduction and frequently porosity, in some cases in blistering, in particular when liquid phase is present. In , a particularly pronounced case of blistering is shown as well as the respective thermoanalytical graphs ((b)). Here it is evident that in the intermediate temperature range, about 700 … 900°C, CH4 is formed (indicated by masses m16 and m15). This, however, is uncritical regarding blistering, although it results in carbon loss, see [Citation51,Citation52]. The problem rather lies in the high-temperature range, in the collision between the pronounced densification and the maximum of CO formation (see arrow), pore closure preventing removal of the reaction products and thus stopping further reduction. This m28 peak indicates the reduction of the Mn oxides, which are in part ‘natural’ oxides on the Mn powder, in part those formed through internal gettering, and esp. for the latter, also the oxygen content of the base powders is a crucial factor. In principle, pronounced densification during sintering is welcome, but for Mn alloyed steels the high temperature of the deoxidation ‘window’ has to be considered.
Figure 6. Fe-12%Mn-2.0%C (Carbonyl Fe, electrolytic Mn). (a) Specimen sintered at 1350°C. (b) Dilatometric graph + MS.
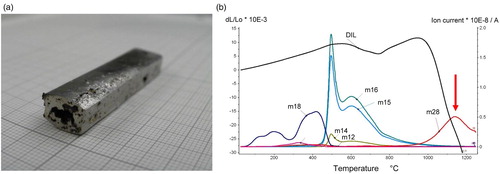
Therefore, standard water atomised powders must be regarded to be better suited here, even if some heterogeneity has to be taken into account. Further benefits of these base powders are the lower starting oxygen content compared to Carbonyl Fe and the better compactibility, which results in higher dimensional stability during sintering. Because of the lower shrinkage and generally slower densification during sintering, deoxidation is not inhibited, and high sintering temperatures can be applied to promote both homogenisation and deoxidation. In any case, high (local) density should be attained by deformation rather than sintering.
This different deoxidation behaviour is clearly visible when comparing Mn elemental mappings of Mn alloy steels prepared from both powder grades (): In case of atomised Fe ((a)), some areas with slightly lower Mn content are visible, originating from the cores of the largest powder particles. In case of Carbonyl Fe ((b)), in contrast, the matrix itself is fairly homogeneous, but there are numerous Mn- rich phases that indicate Mn oxides. These are generated through ‘internal gettering’ as a consequence of the higher oxygen content of the finer powders and the inhibited deoxidation through premature closing of the pores. This is also evident from the oxygen contents: even after sintering at 1350°C, at which temperature carbothermal reduction of MnO is strongly favoured, in case of Carbonyl Fe the oxygen content is as high as 0.276% ± 0.08%. With ASC100.29, in contrast, it is 0.014% ± 0.005%, which further corroborates the adverse effect of premature pore closure in the case of the finer powder.
Optimising of Mn introduction
From the results described above, it stands out clearly that for combining deformability and TRIP effect, optimum adjustment of both the Mn and C contents are required, 12%Mn + 0.8%C apparently being too effective in stabilising the austenite phase. Furthermore, the high Mn levels are of course also more prone to Mn loss at the surface. Therefore, it was attempted to decrease the Mn loss by two measures: lowering the Mn content and introducing Mn not as elemental powder but through masteralloys. Two grades of masteralloys were supplied by Atomising Systems Ltd., Sheffield UK, one of them (MA1) taken from another project [Citation43], with the composition Fe-42%Mn-6%Si-0.4%C, and the other one (MA2), tailor-made for the TRIP steels, with Fe-53%Mn-3.53%C, this composition having been optimised by ThermoCalc. The nominal compositions of the powder mixes prepared were Fe-9%Mn-1.3%Si-0.6%C andFe-9%Mn-0.77%C. In the latter case, the C content was increased to compensate for the additional carbon loss as a consequence of the higher oxygen content of this masteralloy (about 1.1 mass% O). The combined carbon content was in the range 0.45–0.48 mass%, similar to that of the specimens Fe-9%Mn-0.6%C prepared with electrolytic Mn as a reference.
The Mn content after sintering was measured by WD-XRF (Panalytical Axios, Rh Kα radiation) on the surface as well as in the core (the surfaces being slightly ground to avoid erroneous results by deposited Mn oxide dust, see [Citation53]). The respective contents are shown in . As can be seen, using masteralloys in place of elemental (electrolytic) Mn in fact significantly lowered the Mn loss during sintering, and the tailor-made MA2 is more efficient than MA1. Even at the highest sintering temperature of 1300°C the difference of the Mn content between surface and core was about 0.5 mass% for MA2 compared to about 1.5% for electrolytic Mn, in which case significant Mn loss is recorded also in the core.
Figure 8. Mn contents after sintering (analysed by WD-XRF) on the surface and core of Fe-9%Mn-0.45 … 0.48%Ccombined, prepared using Fe ASC100.29 and different Mn carriers.
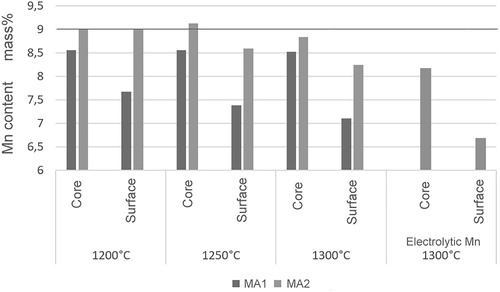
Rolling experiments proved that the sintered specimens prepared from MA2 could be rolled without cracking. Through measuring the magnetic saturation, the expected decrease of the austenite content was observed (). This shows that the TRIP effect was attained also here in all cases, i.e. the balance between too low and too high stability of the austenite was well established. The somewhat more pronounced transformation of the specimens sintered at 1300°C can be attributed to the slightly lower Mn content there and resulting lower stability of the austenite; nevertheless, deformability did not suffer. Therefore, the combination of water atomised iron powder and Masteralloy MA2 enables sintering at high temperature, with resulting low oxygen content and low Mn loss as well as homogeneous microstructure, the material thus being suited for simultaneous surface densification and hardening of PM components.
Conclusions
Using Mn as an alloy element in sintered steels is an attractive alternative to the more common but expensive alloy additives used today; in part Mn can result in unique behaviour of the steels.
The main peculiarities of Mn that have to be considered for the PM route are its oxygen affinity which is slightly higher than that of Cr – and much higher than that of Cu, Ni and Mo – as well as, as a unique feature, its high vapour pressure.
The better option to produce Mn alloy steels is the mixing route, using plain Fe as base powder and electrolytic Mn, ferromanganese grades or masteralloys as Mn carrier.
In mixed systems, reduction during sintering is characterised by the presence of the Mn carrier as an ‘internal getter’, i.e. by oxygen transfer from Fe to Mn, which implies that the conditions for effective oxygen removal are those for reduction of MnO.
This necessitates sufficiently high sintering temperatures for effective carbothermal reduction, which in turn increases the risk of Mn loss at the surfaces.
Mn evaporation can at least be alleviated by adding Mn through a suitable masteralloy.
When combining appropriate Mn and carbon levels (typically 8 … 12%Mn), sintered steels with TRIP behaviour can be produced. Precondition is, however, consideration of the peculiarities of Mn as alloy element.
This means controlling Mn distribution/evaporation and carbon loss during sintering as well as attaining effective oxygen removal.
Using fine powders with high sintering activity results in premature pore closure and thus in insufficient deoxidation, in extreme cases even in blistering.
Generating the TRIP effect on the surfaces of sintered steel specimens offers the chance to obtain densification and surface hardening within one process, thus greatly improving economy of parts production.
Acknowledgements
This work was in part supported by the Austrian Government through the FFG (Project Re Design Gear Process). Furthermore, the authors want to thank Atomising Sytems Ltd., Sheffield UK, in particular John J. Dunkley, for preparing and supplying the masteralloy powders used.
Disclosure statement
No potential conflict of interest was reported by the author(s).
Additional information
Funding
Notes on contributors
Herbert Danninger
Herbert Danninger is full professor of Chemical Technology of Inorganic Materials at Technische Universität Wien (Vienna University of Technology), Vienna, Austria. From 2011 to 2019, he was also Dean of the Faculty of Technical Chemistry. He has been active in powder metallurgy for more than 40 years and is author/co-author of 500+ publications as well as several books and book chapters. From 2009 to 2020, he was chairman of the ‘Gemeinschaftsausschuss Pulvermetallurgie’, the PM association of the German-speaking countries. He holds honorary doctoral degrees of Technical University Cluj-Napoca (Romania), Universidad Carlos III de Madrid (Spain) and Universitatea din Craiova (Romania) and is Fellow of APMI and EPMA. In 2020 he was awarded the ‘Ivor Jenkins Medal’ of IOM3.
Christian Gierl-Mayer
Christian Gierl-Mayer was born in Styria, Austria, in 1969. He studied Technical Chemistry at TU Wien, got his Master 1996 and his PhD in 2000 from TU Wien. After 3 years in a private research institute (ofi-Austrian Research Institute of Chemistry and Technology) he re-joined the powder metallurgy group of Prof. Herbert Danninger as senior researcher. He got his habilitation in 2019 for ‘Thermoanalytical Investigation of Interactions between Powder Metallury Steels and the Atmophere during Sintering’, and became Associate Professor in 2019. He is currently leading the research group Powder Metallurgy at TU Wien, Institute of Chemical Technologies and Analytics. His publication record is about 260 publications in journals and conference proceedings, 4 book chapters and 7 patents.
Mikhail Prokofyev
Mikhail Prokofyev was born in Leningrad (today: St. Petersburg), Russia, and went to school in Russia, Germany and Austria. He studied Technical Chemistry at TU Wien, earning his Master degree in 2017. He then continued with his doctoral thesis, earning the degree of Dr.techn. in May 2020. Since April 2020 he has been working with TÜV Austria, Vienna.
Marie-Christine Huemer
Marie-Christine Huemer studied Technical Chemistry at TU Wien, earning her Master degree in 2013. The topic of her master thesis was the effect of Mn vapour on sintering furnace linings. She then continued with a doctoral thesis on functional material design for ferrous PM precision parts, obtaining the degree of Dr.techn. in 2016.
Raquel de Oro Calderon
Raquel de Oro Calderon is Assistant Professor at the Institute of Chemical Technologies and Analytics at the Technical University of Vienna (Austria). She has been active in the field of PM for about 10 years, is author of more than 70 publications in journals, conference proceeding and book chapters, and has been invited speaker in several conferences in Europe, America and Japan. Her main areas of research are related to the study of PM processes and materials. She has intensely worked in the study of master alloys as a way to introduce oxygen-sensitive elements in PM steels, and in the design of liquid phases to tailor their behaviour during the sintering process.
Robert Hellein
Robert Hellein studied Technical Chemistry at Vienna University of Technology with PhD in the Field of ‘Co-sintering of cemented carbides’ (Institute of Chemical Technologies and Analytics) 2016 he joined Miba Sinter Austria GmbH as R&D Engineer Materials & Processing Technology. From 2018, he has been Teamleader for Material Development, R&D Sinter Group.
Alexander Müller
Alexander Müller studied Mechanical Engineering and Economics at Vienna University of Technology with a PhD thesis in the Field of RFID Technology. In 2006 he started at Miba Sinter Austria GmbH as Development engineer; from 2008, he was Teamleader in the area of R&D. In 2013 he became Manager R&D: Advanced Engineering, and since 2016, he has been Head of R&D Miba Sinter Group.
Gerold Stetina
Gerold Stetina studied Materials Science at Montanuniversität Leoben. In 2003, he joined Miba Sinter Austria GmbH as Development engineer; from 2008, he was Teamleader in the area of R&D. In 2013, he became Manager R&D: Materials & Processing Technology and in 2016, Business Unit Manager Electrification, Miba Sinter Group. Since 2019, he has been Business Unit Manager 3D Flux Technology, Miba eMobility GmbH.
References
- Metals Handbook. Vol.1. properties and selection: irons, steels, and high-performance alloys. 10th ed., ASM, Metals Park (OH); 1990; p.140.
- Krauss G. Steels – processing, structure, and performance. Materials Park (OH): ASM; 2005.
- Grässel O, Frommeyer G, Derder C, et al. Phase transformations and mechanical properties of Fe-Mn-Si-Al TRIP-steels. J Phys IV Colloq. 1997;7:383–388.
- Konieczny AA. On the formability of automotive TRIP Steels. Vol. 78, Proceedings 2003 SAE World Congress. 2003. SAE International.
- Frommeyer G, Brüx U, Neumann P. Supra-ductile and high-strength manganese TRIP/TWIP steels for high energy absorption purposes. ISIJ Int. 2003;43:438–446.
- Hadfield RA. Hadfield’s manganese steel. Science. 1888;12:284–286.
- Dastur YN, Leslie WC. Mechanism of work hardening in Hadfield manganese steel. Metall Trans. 1981;12A:749–759.
- Adler PH, Olson GB, Owen WS. Strain hardening of Hadfield manganese steel. Metall Mater Trans. 1986;17A:1725–1737.
- Ueji R, Tsuchida N, Terada D, et al. Tensile properties and twinning behavior of high manganese austenitic steel with fine-grained structure. Scripta Mat. 2008;59:963–966.
- Šalak A, Selecka M. Manganese in powder metallurgy steels. Cambridge: Springer-CISP; 2012.
- Šalak A. Sintered manganese steels part I: effect of structure of initial iron powders upon mechanical properties. Powder Metall Int. 1980;12:28–31.
- Šalak A. Sintered manganese steels part II: manganese evaporation during sintering. Powder Metall Int. 1980;12:72–75.
- Šalak A. Sublimation and condensation of manganese vapor. Pract. Metallogr. 1985;22(1):26–33.
- Šalak A. Manganese vapour-protection of premixed manganese steels against oxidation during sintering. Powder Metall Int. 1986;18:266–270.
- Šalak A. Activated alloying of Fe-Mn powder systems by manganese vapour during sintering. Sci Sintering. 1989;21(3):145.
- Šalak A, Selecka M, Bures R. Manganese in ferrous powder metallurgy. Powder Metall Progress. 2001;1:41–58.
- Glassner AR. The thermochemical properties of the oxides, chlorides, and fluorides to 2500°K. U.S. Atomic Energy Comm. Rep. ANL-5750, Washington (DC); 1957.
- Lindskog P. The history of Distaloy. Powder Metall. 2013;56:351–361.
- Donaldson I, Marucci M, Lindsley B. Adv. Powder Metall. & Partic. Mater. – 2011, compiled by IE Anderson, TW Pelletiers, MPIF, Princeton (NJ); 2011; Part 7, 54–63.
- Danninger H. Low alloy Chromium steels for highly loaded PM parts. Proc. Int. PM Conf. CSFR, Piestany; 1992; Vol.1, 81–90.
- Karasuno I, Koshiro K, Umino M, et al. Some properties of oil atomized low alloy steel powders containing chromium. Horizons of Powder Metallurgy (Proc, PM'86 Düsseldorf), WA Kaysser, WJ Huppmann eds., Verlag Schmid, Freiburg; 1986; Vol.1, p. 53–56.
- Unami S, Ogura K, Uenosono S. Effect of V on the strength of sintered Cr-Mo alloyed steel powder compacts. Proc. PM*98 World Congress, Granada; 1998; Vol.3, 173–178.
- Lindqvist B. Chromium alloyed steels – a new powder generation. Proc. Euro PM 2001 Nice, EPMA ed., Shrewsbury; 2001; Vol.1, p.13–21.
- Berg S, Maroli B. Properties obtained by chromium-containing material. In: V Arnhold, C-L Chu, WF Jandeska, HI Sanderow, editor. Advanced powder Metallurgy & Particulate Materials – 2002 part 8. Princeton (NJ): MPIF; 2002. p. 1–14.
- Tengzelius J, Grek SE, Blände CA. Limitations and possibilities in the utilization of Cr and Mn as alloying elements in high strength sintered steels. Mod Dev Powder Metall. 1981;13:159–182.
- Motooka N, Kuroishi N, Hara A, et al. Strength and ductility of Mn-Cr sintered steels. Met Powder Rep. 1983;38:629–631.
- Selecka M, Šalak A. Industrially sintered hybrid low carbon 3Cr-0.5Mo-xMn steels. Int J Powder Metall. 2010;46:29–42.
- Simkulet Y, Selecka M. Effect of manganese on fracture of premix and hybrid Fe-0.85Mo-xMn-0.3C sintered steel. Powder Metall Progress. 2006;6:156–163.
- Burow J, Menz R, Lindsley B, et al. Neue manganhaltige PM-Stähle - Herstellung und Anwendungspotential [New Mn alloys PM steels-manufacturing and porential for application]. in „Pulvermetallurgie in Wissenschaft und Praxis Bd.30, Fachverband Pulvermetallurgie; 2014;235–254 (in German).
- Klein AN, Oberacker R, Thümmler F. Development of new high strength sintered steels containing silicon and manganese. Metal Powder Rep. 1984;39:335–338.
- Klein AN, Oberacker R, Thümmler F. High strength Si-Mn alloyed sintered steels. Mechanical properties. Powder Metall Int. 1985;17:13–16. 71-74.
- Handbook of Chemistry and Physics, 67th Ed. Boca Raton (FL): CRC Press; 1985.
- Dautzenberg N, Dorweiler HJ. Dimensional behaviour of copper-carbon sintered steels. Powder Metall Int. 1985;17:279–283.
- Danninger H, Pöttschacher R, Bradac S, et al. Comparison of Mn, Cr and Mo alloyed sintered steels prepared from elemental powders. Powder Metall. 2005;48:23–32.
- Šalak A. Ferrous powder metallurgy. Cambridge: CISP; 1995.
- Jaliliziyaeian M. Sintering of manganese prealloyed powder metallurgy steels [PhD thesis]. TU Wien; 2008.
- Hryha E. Fundamental study of Mn containing PM steels with alloying method of both premix and pre-alloy [PhD thesis]. Slovak Academy of Sciences, Kosice; 2007.
- Hryha E, Nyborg L, Dudrova E, et al. Sintered steels alloyed with manganese: effect of alloying mode. Proc. PM2010 World Congress Florence, EPMA, Shrewsbury UK; 2010; Vol. 3; p. 87–94.
- Albano-Müller L, Thümmler F, Zapf G. High-strength sintered iron-base alloys by using transition metal carbides. Powder Metall. 1973;16:236–256.
- Zapf G, Dalal K. Introduction of high oxygen affinity elements manganese, chromium and vanadium in the powder metallurgy of P/M parts. Modern Dev Powder Metall. 1977;10:129–152.
- Schlieper G, Thümmler F. High strength heat-treatable sintered steels containing manganese, chromium, vanadium and molybdenum. Powder Metall Int. 1979;11:172–176.
- Banerjee S., Schlieper G, Thümmler F et al. New results in the master alloy concept for high strength sintered steels. Modern Dev Powder Metall. 1981;13:143–157.
- Castro F, Sarasola M, Sainz S, et al. Processing routes for obtaining novel high performance Mn-containing PM steels. Mater Sci Forum. 2007;524-526:705–708.
- De Oro Calderon R, Dunkley JJ, Gierl-Mayer C, et al. New opportunities for master alloys: ultra high pressure water atomized powders. Powder Metall Rev. 2019;8(1):55–66.
- De Oro Calderon R, Gierl-Mayer C, Danninger H. Master alloys in powder metallurgy: the challenge of exploring new alloying compositions. Powder Metall. 2017;60:86–96.
- Gierl-Mayer C, Danninger H, de Oro Calderon R, et al. “Internal gettering” – metallothermic reduction processes in the early stage of sintering. Int J Powder Metall. 2015;51:47–53.
- Sandner C, Dickinger J, Rößler H, et al. Advanced applications for sintered gears. Proc. PM2004 World Congress Vienna; H. Danninger, R. Ratzi eds., EPMA, Shrewsbury UK; 2004; Vol.5; 657–662.
- Gierl-Mayer C, Prokofyev M, Huemer M-C, et al. Powder metallurgy manufacturing of Hadfield-type Mn steels with TRIP behaviour, Proc. EuroPM2020 Virtual Congress, EPMA, Chantilly; 2020; paper no. 4849701.
- Ouda K, Danninger H, Gierl-Mayer C. Magnetic measurement of retained austenite in sintered steels – benefits and limitations. Powder Metall. 2018;61:358–368.
- Gestrich T. In situ Charakterisierung der Vorgänge beim Entbindern, Ausgasen und Sintern von WC-Co-Hartmetallmischungen mittels Komplexer Thermischer Analyse [PhD thesis]. TU Dresden; 2004.
- Danninger H, Avakemian A, Gierl-Mayer C, et al. Methane formation through substrate-atmosphere interaction during sintering of si containing steels. Proc. EuroPM2014 Salzburg, EPMA, Shrewsbury; 2014; paper no. 14038.
- De Oro Calderon R, Gierl-Mayer C, Danninger H. Effect of H2 atmospheres on sintering of steels containing oxidation-sensitive elements introduced through the master-alloy route. Int J Powder Metall. 2017;53(3):31–40.
- Jalilizyaeian M, Gierl C, Danninger H. Manganese evaporation during sintering of Fe-Mn-Cr compacts from prealloyed iron powders. Proc. Euro PM 2008 Mannheim, EPMA, Shrewsbury UK; 2008; Vol.1; 115-120.