ABSTRACT
High-entropy carbides (HEC) are a class of promising new hard phases for a sustainable improvement of hardmetal properties. In this work, hardmetals of the HEC (Ta,Nb,Ti,V,W)C were studied with two typical binder volume fractions of 16 and 24 vol-% consisting of Co, Ni and FeNi. The sintering behaviour, microstructure, phase composition, magnetic and mechanical properties are discussed and are compared to a conventional WC-Co hardmetal. It was shown that the HEC has a high-phase stability and that dense hardmetals with promising mechanical properties were obtained.
Introduction
Standard hardmetals or cermets consist of a hard phase skeleton, where mostly tungsten carbide (WC) and titanium carbonitride (Ti(C,N)) are used, respectively, and a metal (Me) binder matrix. Often additional hard phases such as TiC, Mo2C and Cr3C2 are added in small quantities to adjust thermophysical properties or to enhance wetting and sintering [Citation1]. Most often used binder metals are plain Co, Ni or a combination of both. More complex binder materials such as CoNiFe or combinations with low amounts of Cr and Mo have also been studied but are so far not commercialised [Citation2].
In metal alloy development within the last 15 years an interesting concept of so-called high-entropy alloys (HEAs) was investigated [Citation3]. Here, HEAs as, ‘those composed of five or more principal elements in equimolar ratios’ [Citation4] were introduced as novel single-phase alloy phases. Inspired from this development, the high-entropy concept has been extended also to the development of high-entropy ceramics. Inside this group, the high-entropy carbides (HEC) are currently the second most investigated subgroup [Citation5]. The numerous developments are summarised in a number of recent reviews [Citation5–7]. There is a lot of work on the computation of HEC, e.g. [Citation8,Citation9]. Among them, there have been attempts to define descriptors in order to predict their formation, like the entropy-forming ability (EFA) [Citation8]. In experimental studies, HEC are described as binderless hardmetals or as ultra-high temperature carbides (UHTC), which showed promising properties regarding hardness, thermal conductivity, oxidation resistance and mechanical properties at high temperatures [Citation9–13].
With respect to hardmetals or cermets, this concept has mostly been applied by the use of HEA as metal binders, e.g. [Citation14–16], while investigations using HEC as a hard phase are still very limited [Citation17–20]. Different technologies have been applied for their preparation, including Sinter-HIP [Citation17] spark-plasma sintering (SPS) [Citation18], pressureless melt infiltration using SPS [Citation19] and precipitation in a steel matrix [Citation20].
In a previous own study, two different HEC compositions (Hf,Ta,Nb,Ti,V)C and (Ta,Nb,Ti,V,W)C were synthesised and studied as bulk materials without binder [Citation12] and as hardmetals with Co binder prepared by SinterHIP [Citation17]. These two HEC compositions were selected on the base of their high EFA, which is described as 100 and 77, respectively [Citation8,Citation9].
In this study, we report the investigation of hardmetals of HEC (Ta,Nb,Ti,V,W)C and different binder metals. Thus, six hardmetal compositions with binder volume fractions of 16 and 24 vol-% of Co, Ni and FeNi as binders were prepared by using conventional powder metallurgy routes to investigate their influence on the microstructure and mechanical properties.
Materials and methods
The compositions of the HEC-based hardmetals investigated in this study are compiled in . The equimolar (Ta,Nb,Ti,V,W)C powder with a lattice parameter of 4.354 Å was prepared at Fraunhofer IKTS from commercial carbide powders by mixing, sintering of cold isostatic pressed bars at 2250°C and subsequent crushing to <45 µm by means of a vibratory disc mill (more details can be found in [Citation17]). For the preparation of HEC-based hardmetals binder contents of 16 and 24 vol-% were selected, since they represent the same binder content as in WC-10 wt-% Co and in WC-15 wt-% Co, respectively. The corresponding mixtures were produced by mixing of the HEC powder with Co, Ni or a Fe – 25 wt-% Ni mixture by ball milling for 48 h in n-heptane at 70 rpm with about 2 wt-% of paraffine as a pressing aid. The mean grain size as measured by the Fisher Sub Sieve Sizer method of Co (S80, Freeport Cobalt), Ni (Ni2800, Eurotungsten) and Fe (CIP-HQ, BASF) were 1.0, 2.5 and 2.2 µm, respectively.
Table 1. Composition and properties of the HEC-Me samples.
After vacuum drying and sieve granulation, the mixtures were cold isostatically pressed at 3000 bar to form cylinders (h = 10 mm, Ø = 10 mm). Sintering behaviour was studied first by thermal analysis. For dilatometry (Netzsch DIL 402 C/7/G) pressed samples with approximately 7 mm length were used. In the thermogravimetric experiments (Netzsch STA 449 F1/Jupiter) pieces of approximately 150 mg cut off the pressed samples were studied in pure alumina sample holders. For both methods, helium was chosen as the atmosphere, since it resamples the sintering behaviour in vacuum quite well and it avoids unwanted oxidation due to gas leaking into the measurement devices and a heating rate of 10 K min−1 was applied.
After debinding, i.e. paraffine removal, in hydrogen atmosphere sintering was carried out in a SinterHIP furnace at 1400°C for 30 min at 10 mbar Ar and 45 min at 100 bar Ar gas pressure (∼10 MPa).
After metallographic preparation, the microstructures were studied by field emission scanning electron microscopy (FESEM) ULTRA 55 (Carl Zeiss Microscopy, Oberkochen, Germany) and energy-dispersive X-ray spectroscopy (EDS). The phase composition was analysed by X-ray diffraction (XRD) using D8 Advance (Bruker AXS, Karlsruhe, Germany; CuKα-radiation). The accurate determination of the lattice parameter of the cubic phase was performed with a Pawley fit algorithm by using the software TOPAS [Citation21,Citation22]. Important structural information of hardmetals can be obtained by measurement of the magnetic saturation and the coercitive force. The magnetic saturation polarisation mS was measured using a Sigmameter D6025 (Setaram, Caluire, France). Magnetic measurement of coercivity Hc was done according to ISO 3326 with a Koerzimat CS 1097 (Institut Dr. Foerster, Reutlingen, Germany).
Furthermore, density was measured according to ISO 3369. The rule of the mixture was used to calculate the HEC density from those of the individual carbides. Vickers hardness was measured according to ISO 3878 using 294 N load (HV30). Fracture toughness was determined from the indentations using Shetty’s formula [Citation23].
Results
Sintering behaviour
The sintering behaviour was studied in terms of linear shrinkage (dilatometry) ( and ) and mass loss (thermogravimetry) () for the HEC samples with 24 vol-% binder.
Figure 1. Length change of the HEC-24 vol-% binder composites during sintering, (a) overview, (b) initial stage of sintering up to 1000°C.
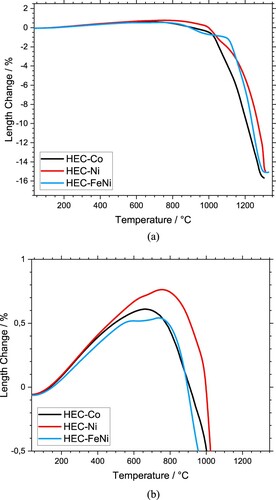
Figure 3. Mass change of the HEC-24 vol-% binder composites during sintering, (a) mass loss and (b) mass change rate.
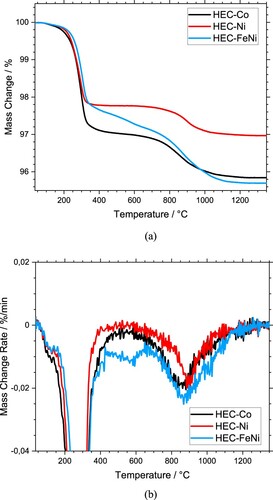
The FeNi-containing grade shows a retardation of thermal expansion already at approximately 550°C. For the other grades, the shrinkage starts above 650°C, while sintering with Co binder occurs significantly faster than with Ni binder ((a,b)). Thus, the shrinkage starts in the following order of the binder materials: FeNi < Co < Ni. With Ni and Co binder, accelerated sintering starts at approximately at 1000°C ((a)). For the grade with FeNi binder accelerated shrinkage starts later at approximately 1100°C with the highest shrinkage rate at approximately 1250°C. Up to approximately 1200°C, the shrinkage rate of the grade with Co binder is higher in comparison with Ni- and FeNi-bonded samples (). A strong shrinkage rate peak is observed for the grade with Co binder at approximately 1270°C, while for the grade with Ni binder a very pronounced peak is observed at 1300°C. Thus, the order of the grades Co < FeNi < Ni for finishing of sintering is different from the start of shrinkage.
Debinding occurs in the temperature range 200–300°C. Remarkably, in the range of about 400–600°C the mass loss for the samples with Co and Ni is low, while for the FeNi-containing grade a permanent mass loss is observed ((b)). A permanent mass loss for all grades occurs during a broad temperature range between 600°C and 1200°C ((a,b)) with a peak temperature at approximately 850–900°C.
In , the densities of the HEC-based hardmetals are presented. There can be several reasons for the relative densities being above 100%, as discussed below.
Phase composition and microstructure
illustrates the XRD patterns for the samples with 16 vol-% binder. All patterns show the distinct peaks of the cubic HEC phase as well as those of the corresponding cubic binder phases. No hexagonal Co phase was found in the HEC-Co sample. In case of the HEC-FeNi sample, there are two peaks visible in the vicinity of 75° 2θ, which correspond to the binder phase and HEC phase respectively, while an overlapping of these peaks occurs for the HEC-Co and HEC-Ni samples. The diffraction patterns of the samples with 24 vol-% binder are similar to those with 16 vol-% binder content, with exception of the FeNi-bonded sample where two additional small peaks at 39.6 and 42.15 2θ were observed. The lattice parameters of the HEC phase were found to be in the range of 4.358–4.363 Å. Thus, in all cases lattice parameters are significantly higher than the value of the initial HEC powder (4.354 Å). Also, for the three binder phases an increase of the lattice parameter was observed (see ).
Figure 4. X-ray diffraction pattern of HEC-Co, HEC-Ni and HEC-FeNi hardmetals with 16 vol-% binder content in the range 2θ = 20–80°.
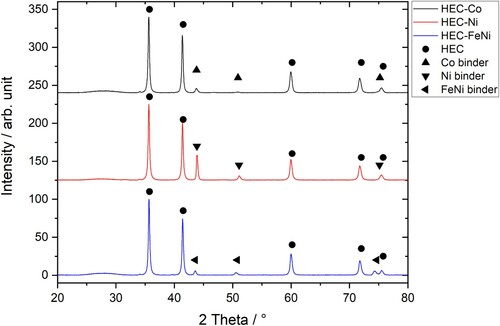
Table 2. Lattice parameters of the metallic binder phases.
In the FESEM images of the HEC-Co samples in , the HEC phase skeleton is visible together with the binder phase. The elemental distribution in the EDS mapping of the HEC-16 vol-% Co sample in shows the even distribution of the transition metal elements within the HEC phase and seemingly homogenous pure Co binder phase. However, the mapping of W reveals a non-homogeneous concentration in the hard phase area, and some dissolved W in the binder phase. The content of W in the rim areas of the HEC grains is lower.
presents the FESEM images of the HEC-Ni samples, showing a similar microstructure as the Co-bonded sample but a significantly bigger HEC grain size (compare ). In the EDS mapping of the HEC-16 vol-% Ni sample () the elemental distribution in the HEC phase is homogeneous for all elements, and the Ni binder is evenly distributed between the hard phase grains.
presents the FESEM images of the HEC-FeNi samples, and the EDS mapping of the HEC-16 vol-% FeNi sample. The HEC grain size appears to be the largest for the three different binders. According to the elemental mappings, Fe and Ni are homogeneously distributed in the binder phase (). In the FESEM image of the HEC-16 vol-% FeNi sample a very small amount of a bright appearing third phase is observed. It is located at the interface of the HEC grains and the binder areas. The corresponding elemental mapping indicates W as the only metallic element within. Moreover, this mapping reveals also a non-homogeneous distribution of W, which is highly concentrated at the HEC–HEC grain boundaries. Different from the sample with Co-binder, the dissolution of W within the metallic binder phase appears to be limited.
compiles also the results of the magnetic saturation and coercive force measurements. High values for the magnetic saturation were measured for the composition with Co-binder, and lower values for the FeNi-binder. However, for the Ni-bonded samples, no magnetic saturation was measured at all. A coercive force was measured for the Co-bonded samples only.
Hardness and toughness are also given in . As expected, the hardness values of the samples with the lower binder content are higher, while the toughness values are lower. The highest hardness value is 1490 HV30 (HEC-16 vol-% Co) while the lowest value is 1060 HV30 (HEC-24 vol-% Ni). Fracture toughness values are in the range between 7.3 MPa·m1/2 (HEC-16 vol-% FeNi) and 11.9 MPa·m1/2 (HEC-24 vol-% Ni).
For comparison, the properties of a WC-16 vol-% Co hardmetal (prepared under the same conditions as the HEC-based hardmetals) are also included in [Citation24]. The microstructure is presented in .
Discussion
Sintering behaviour
The main reduction step of oxides of the binder phase is overlayed by debinding of paraffin (main mass loss step in the temperature range between 200°C and 400°C) [Citation25,Citation26]. The initial retardation of thermal expansion for the sample with FeNi binder at approximately 550°C coincides with the first mass change rate peak (see (b)). This effect can be explained by the reduction of surface oxides of these samples, as samples with Fe-binder to have the reduction of Fe-oxides shifted to higher temperatures [Citation25]. The reduction of the oxides of the HEC phase obviously takes place during a broad temperature range between 600°C and 1200°C ((a,b)) and is most intensively in the temperature range of approximately 850–900°C. In WC-Co compositions, the reduction of W-oxides takes place already at about 750°C, which is around 100–150 K lower than found here for the HEC-based hardmetals [Citation26,Citation27]. The reduction of the oxides is a requirement for beginning of wetting of the surfaces of the HEC phase by the metallic binder and the beginning of sintering.
Accelerated sintering starts at approximately 1000°C, after the oxides of the HEC phase have been reduced. Here, the shrinkage rate of the grade with Co binder is up to temperatures of approximately 1250°C higher than for the Ni- and FeNi- bonded hardmetals.
The intensive shrinkage of all composites is comparable with WC-Co and may correspond to the end of melting of the eutectic binder phases [Citation28].
There are different possible explanations for the relative densities being above 100% as measured for all sintered samples. The density of the HEC could be higher than the calculated density from the individual transition metal-based carbides according to the rule mixture. Another reason might be the solution of heavier transition metal elements from the HEC phase into the corresponding binder phases.
The influence of the carbon content on the melting temperatures and the phase formation of the hardmetals, as known from the literature [Citation25] will be a topic of further studies.
Phase composition and microstructure
According to the XRD results and the FESEM images, the samples consist of the HEC and binder phase. The samples with FeNi binder have shown some tendency to form new phases. This is indicated by the formation of a low amount of a W-rich phase (see and ) in case of the sample with 16 vol-% binder, and the indication of small additional peaks in the XRD pattern of the sample with 24 vol-% binder. According to XRD and FESEM results, the samples with Co and Ni binder did not show any indication of the formation of an additional phase. The HEC lattice parameter of 4.354 Å is for the same composition somewhat lower than those reported by Harrington et al. [Citation9] (4.36(2) Å). Remarkably, there is an increase of the lattice parameters for the HEC and the binder phases as well (see ). The increase of the HEC lattice parameter might stem from the preferable solution of metals forming carbides with low lattice parameter. In case of the HEC composition in this study, V and Ti are the carbides with the lowest lattice parameter. In addition, WC decreases the lattice parameter of TiC in the binary TiC-WC system as well [Citation29]. The increase of the lattice parameter of the binder metals suggests also the solution of some HEC forming elements (see ). In case of the Co binder phase W is assumingly the metal with the strongest tendency of dissolution within it. However, in general this depends on the different solubilities of the HEC components in the different binder metals. The solution of metals from the HEC phase in the binder phase is confirmed by the values of the magnetic saturation in case of the Co binder. The magnetic saturation of 21.7 µTm³ kg−1 corresponds to a value of 64% of theoretical magnetic saturation (44.6 µTm³ kg−1).
The HEC grain size in the samples depends on the binder. The grain size of the Ni- and FeNi-bonded HEC is larger than that of the Co-bonded hardmetal. Under the premises of similar behaviour to WC-Co the coercive force value of 6.7 kA m−1 suggests a medium-sized HEC grain size after sintering (1.3–2.5 µm). This is in agreement with the observed grain size as seen in . In comparison with the conventional WC-Co samples (see ) a higher contiguity of the HEC grains is assumed due to a higher amount of HEC–HEC grain boundaries in all HEC samples as compared to the amount of WC–WC grain boundaries in the WC-Co reference sample (see ). By comparing the three HEC-based hardmetals the Ni bonded hardmetal is expected to have the lowest contiguity with values most comparable to the WC-Co reference samples.
The FESEM observations show that under certain conditions also within HEC-based hardmetals a core-rim structure can be formed. This effect seems to be most pronounced with the Co binder, where some dissolution leads to the formation of W-depleted rim areas of the hard phase grains. Thus, the mechanism of formation is different to TiCN-based cermets. In case of the FeNi binder the solution of W in the binder seems to be most limited and seems to lead rather to the formation of new phases at the HEC grain/binder interface.
Mechanical properties
For comparison also the properties of a conventional WC-16 vol-% Co hardmetal [Citation24] prepared under the same conditions are given (see ). Independent of the kind of binder, the hardness for the lower binder contents is higher, as known from WC-Co hardmetals [Citation30]. The Co-bonded HEC have the highest hardness, followed by FeNi- and Ni-bonded HEC, respectively. This influence of binder metals on hardmetal hardness also corresponds to the general trend known from WC-based hardmetals [Citation30].
In comparison to the similarly grained WC-16 vol-% Co the fracture toughness to hardness ratio values for all HEC-based hardmetals are, however, significantly lower. In particular, it is supposed that the presence of W at the HEC–HEC grain boundaries in the case of the samples with FeNi binder lowers the overall toughness by producing a more brittle boundary phase.
As shown in Ni-bonded HEC show overall higher fracture toughness to hardness ratios compared to Co and/or FeNi-bonded HEC for the hardness range below 1300 HV30. This might relates to a lower solubility of metallic elements from the HEC phase in Ni as compared to the other binder compositions. The Co-bonded HEC seems to produce better combinations of fracture toughness and hardness than the FeNi binder in particular for a hardness above 1300 HV30.
Conclusion
In this work, the preparation of hardmetals with a (Ta,Nb,Ti,V,W)C HEC powder using different binder metals (Co, Ni and FeNi) was studied by thermal analysis and by characterisation of sintered samples.
Thermal analysis has shown that the reduction of HEC surface oxides takes places at a slightly higher temperature compared to WC surface oxides in WC-Co. However, the overall shrinkage behaviour is similar to WC-based hardmetals with Co, Ni and Fe binder metals. Dense samples were obtained using standard SinterHIP conditions. The HEC is relatively stable against the binder materials investigated in this study and retains its composition and phase structure during the sintering process. Differences might appear from the different solubility of metallic elements present in the HEC in the various binder metals. This obviously influences the HEC grain size, which is lowest for the Co binder. The Co-bonded HEC hardmetal showed also ferromagnetic properties. Thus, standard magnetic characterisation methods could be used to assess alloying state and mean grain size. In case of FeNi-bonded HEC hardmetals a dissolution of W out of the HEC grains is observed, resulting in a higher W content at the HEC–HEC grain boundaries. This is most likely one of the reasons why this composition shows the lowest fracture toughness values. The HEC–metallic binder interaction should be investigated in more detail in future studies.
Mechanical properties of the 16 vol-% Ni-bonded HEC show with values of 1 060 HV30 and a fracture toughness of 11.9 MPa·m1/2 a promising hardness to fracture toughness ratio, which could be suitable for a wide range of applications. It is expected that by further adjusting the composition and by using finer HEC starting powders mechanical properties can be enhanced further.
Additional work is also envisaged to investigate bending strength, oxidation resistance, thermophysical properties and corrosion resistance in more detail. This will help to get a deeper understanding about the application potential of HEC-based hardmetals and their performance in comparison with WC-based hardmetals and TiCN-based cermets.
Acknowledgements
The authors are responsible for the content of this publication. The authors would like to thank Susan Conze for the analysis of the XRD data.
Disclosure statement
No potential conflict of interest was reported by the authors.
Additional information
Funding
References
- García J, Collado Ciprés V, Blomqvist A, et al. Cemented carbide microstructures: a review. Int J Refract Met Hard Mater. 2019;80:40–68.
- Konyashin I, Ries B. Cemented carbides: Amsterdam: Elsevier; 2022. ISBN 9780128228203.
- Miracle DB, Senkov ON. A critical review of high entropy alloys and related concepts. Acta Mater. 2017;122:448–511.
- Yeh J-W, Chen S-K, Lin S-J, et al. Nanostructured high-entropy alloys with multiple principal elements: novel alloy design concepts and outcomes. Adv Eng Mater. 2004;6(5):299–303.
- Akrami S, Edalati P, Fuji M, et al. High-entropy ceramics: review of principles, production and applications. Mater Sci Eng: R Rep. 2021;146:100644.
- Feng L, Fahrenholtz WG, Brenner DW. High-Entropy ultra-high-temperature borides and carbides: a new class of materials for extreme environments. Annu Rev Mater Res. 2021;51:165–185.
- Wang Y. Processing and properties of high entropy carbides. Adv Appl Ceram. 2021: 1–22. DOI: 10.1080/17436753.2021.2014277.
- Sarker P, Harrington T, Toher C, et al. High-entropy high-hardness metal carbides discovered by entropy descriptors. Nat Commun. 2018;9(1):4980, DOI: 10.1038/s41467-018-07160-7.
- Harrington T, Gild J, Sarker P, et al. Phase stability and mechanical properties of novel high entropy transition metal carbides. Acta Mater. 2019;166:271–280.
- Wei X, Liu J, Li F, et al. High entropy carbide ceramics from different starting materials. J Eur Ceram Soc. 2019;39(10):2989–2994.
- Castle E, Csanádi T, Grasso S, et al. Processing and properties of high-entropy utra-high temperature carbides. Sci Rep. 2018;8(1):8609.
- Pötschke J, Dahal M, Herrmann M, et al. Preparation of high-entropy carbides by different sintering techniques. J Mater Sci 2021;56(19):11237–11247.
- Feng L, Chen WT, Fahrenholtz WG, et al. Strength of single-phase high-entropy carbide ceramics up to 2300°C. J Am Ceram Soc. 2021;104(1):419–427. DOI: 10.1111/jace.17443.
- Ezquerra BL, Biurrun TS, Cabezas LL, et al. Sintering of WC hardmetals with Ni-Co-Cr-Ti-Al multi-component alloys. Int J Refract Met Hard Mater. 2018;77:44–53.
- Luo W, Liu Y, Luo Y, et al. Fabrication and characterization of WC-AlCoCrCuFeNi high-entropy alloy composites by spark plasma sintering. J Alloys Compd. 2018;754:163–170.
- Chen CS, Yang CC, Chai H, et al. Novel cermet material of WC/multi-element alloy. Int J Refract Met Hard Mater 2014;43:200–204.
- Pötschke J, Dahal M, Vornberger A, et al. Production and properties of high entropy carbide based hardmetals. Metals 2021;11(2):271.
- Liu J, Xiong J, Guo Z, et al. Preparation of high-entropy (Zr0.25Hf0.25Ta0.25Ti0.25)C-Ni-Co composite by spark plasma sintering. Metall Mater Trans A. 2020;51(12):6706–6713. DOI: 10.1007/s11661-020-06034-2.
- Wang XC, Saunders TG, Sedlák R, et al. Synthesis and densification of (Zr-Hf-Nb-Ta)C-Co high entropy cermet prepared by pressureless melt infiltration using spark plasma sintering. J Alloys Compd. 2022;900:163412, DOI: 10.1016/j.jallcom.2021.163412.
- Kan WH, Zhang YM, Tang XH, et al. Precipitation of (Ti, Zr, Nb, Ta, Hf)C high entropy carbides in a steel matrix. Materialia. 2020;9:100540, DOI: 10.1016/j.mtla.2019.100540.
- Pawley GS. Unit-cell refinement from powder diffraction scans. J Appl Crystallogr 1981;14:357–361.
- Cheary RW, Coelho AA, Cline JP. Fundamental parameters line profile fitting in laboratory diffractometers. J Res Natl Inst Stand Technol 2004;109:1–25.
- Shetty D-K, Wright I-G, Mincer N, et al. Indentation fracture of WC-Co cermets. J Mater Sci. 1985;20:1873–1882.
- Vornberger A, Pötschke J, Gestrich T, et al. Influence of microstructure on hardness and thermal conductivity of hardmetals. Int J Refract Met Hard Mater. 2020;88:1–8.
- Roulon Z, Missiaen J-M, Lay S. Shrinkage and microstructure evolution during sintering of cemented carbides with alternative binders. Int J Refract Met Hard Mater. 2021;101:105665.
- Leitner G, Gestrich T, Gille G. Shrinkage, liquid phase formation and gaseous reactions during sintering of WC-Co hardmetals and correlation to the WC grain size. Proceedings of the 14th International Plansee Seminar; 1997. p. 86–99.
- Pötschke J, Richter V, Gestrich T, et al. Grain growth inhibition in ultrafine hardmetals. Int J Refract Met Hard Mater. 2017;66:95–104.
- Roulon Z, Missiaen JM, Lay S. Effect of Binder Phase on Sintering of Cemented Carbides. In 2018 World Congress on Powder Metallurgy proceedings: Beijing, China, 16-20 September 2018; European Powder Metallurgy Association (EPMA): The Chinese Society for Metals, China Powder Metallurgy Alliance; 2018. p. 770–774.
- Kieffer R, Benesovsky F. Hartstoffe. Wien: Springer; 1963.
- Tracey VA. Nickel in hardmetals. Int J Refract Met Hard Mater. 1992;12:137–149.