Abstract
Elution of silicon (Si) from three types of slag fertilizers was tested in a paddy field. They were made from granulated blast furnace slag, dephosphorization slag and decarburization slag, respectively. Each fertilizer, embedded in epoxy resin to expose the cross section, was analyzed to get initial two-dimensional distribution images of Si, calcium (Ca), oxygen (O), magnesium (Mg), aluminum (Al), manganese (Mn) and iron (Fe) by electron probe micro-analyzer (EPMA). These resin specimens were set in a paddy field for 75 d. Then the second two-dimensional distribution images of Si, Ca, O, Mg, Al, Mn and Fe at the same site were analyzed again by EPMA. A comparison of the two-dimensional distribution images before and after setting in paddy field elucidated the following results: (1) Si eluted clearly from dephosphorization slag and decarburization slag; (2) Si, Ca, Mg and Al distributed homogeneously in granulated blast furnace slag. X-ray diffraction (XRD) clarified that granulated blast furnace slag was amorphous. The content of plant-available Si in each slag fertilizer was evaluated by the cation exchange resin extraction method. It was the highest in dephosphorization slag fertilizer. This result corresponded to Si elution from dephosphorization slag observed by EPMA. The content of plant-available Si was low in granulated blast furnace slag but high in air-cooled blast furnace slag. Although the content of plant-available Si in decarburization slag was low, the efficacy of Si elution was the highest in decarburization slag. From X-ray diffraction analyses, calcium silicate or larnite (Ca2SiO4) was considered to be the causative substance for efficient Si elution from decarburization slag and dephosphorization slag. Because of the high content of plant-available Si, dephosphorization slag and air-cooled blast furnace slag are recommended as silicate fertilizers in paddy fields.
Key words:
INTRODUCTION
Silicon (Si) is an important element for rice. It is absorbed by roots in chemical forms such as Silicic acid (H4SiO4) (Ma and Takahashi Citation2002). Si is transported to stems and leaf blades and used to form silica body cells (Sato et al. Citation1990). The formation of silica body cells depends on Si supply from soil and irrigation water (Husnain et al. Citation2008). It is well known that deficiency of Si causes pathogenic disease like brown spot disease and blast (Datnoff et al. Citation1997; Hayasaka et al. Citation2008). The importance of Si to rice was recognized earlier in Japan. The category of silicate fertilizer was first established in fertilizer control law in Japan in 1955. At first, silicate fertilizer was made from air-cooled blast furnace slag, until the middle of the 1960s. But the cooling method for hot blast furnace slag changed from air-cooling to water-cooling after the middle of the 1960s. Water-cooled blast furnace slag is called granulated blast furnace slag.
Production of slag silicate fertilizer in Japan peaked at 1,400,000 t per year in 1968 (Kato Citation2002) and decreased to 170,000 t per year in 2009 (Nourin Toukei Kyoukai Citation2010). This turning point in slag silicate fertilizer production almost corresponded to the timing of the replacement of air-cooled blast furnace slag with granulated blast furnace slag.
In the steel-making process, hot metal from the blast furnace is pretreated before a basic oxygen furnace (BOF) to remove Si and phosphorus (P) by the addition of lime and so on. Therefore, Ca, Si- and P-rich slag is obtained in this pretreatment process. This slag is called dephosphorization slag. Dephosphorization slag is utilized as silicate fertilizer and phosphate fertilizer in Japan. Hot metal after the pretreatment process contains relatively low Si and P. This hot metal is introduced into the BOF. Then steel is made by blowing oxygen into this hot metal to remove residual carbon (C), Ca, Si and so on in the BOF. Slag from BOF, which is called decarburization slag, is also utilized as lime fertilizer and special fertilizer in Japan.
shows the three types of slag fertilizers which we used in this study. It is meaningful to elucidate characteristic differences of Si elution from these three types of slag fertilizers. Si elution from fertilizer is generally tested in accelerated conditions. For example, 0.5 N hydrochloric acid (HCl) solution is used as a test solution to evaluate Si elution from slag fertilizers in the analysis method authorized by fertilizer control law in Japan (National Institute for Agro-Environmental Sciences Citation1992). But 0.5N HCl is a very acidic condition. Such a test causes the overestimation of Si elution from fertilizers. To solve such problems, elution in moderate conditions has been reported to evaluate Si elution from soil and fertilizers (Imaizumi and Yoshida Citation1958; Takahashi and Nonaka Citation1986; Sumida Citation1991; Kitada et al. Citation1992; Kato and Owa Citation1997). The most ideal evaluation of Si elution from fertilizer is direct observation of Si in a paddy field. Furthermore, it is meaningful to elucidate the microstructure in fertilizers where Si elutes from. Therefore, we devised a new method to observe the elution of Si from slag fertilizers in an actual paddy field. We also evaluated the available Si from slag fertilizers by laboratory elution test using cation exchange resin. Elutions of Si from fertilizers were compared between the paddy field test and the laboratory elution test. We also tried to identify the substances where Si eluted from.
MATERIALS AND METHODS
Experiment materials
Three types of Si-containing fertilizers made from granulated blast furnace slag, dephosphorization slag and decarburization slag were used in this study. Each fertilizer consisted of spherical granules made from each slag powder (diameter < 600 μm). Each granule was about 3 mm in diameter and 0.08 g in weight. Granulated blast furnace slag was the water-cooled type. We also used air-cooled blast furnace slag which was obtained from the same steel-making works where the granulated blast furnace slag was produced.
Composition of fertilizers
All fertilizers in this study were made from steel slag. We analyzed the composition of each fertilizer by glass bead X-ray fluorescence spectroscopy (XRF) which is ordinarily used to analyze the composition of steel slag. Each fertilizer was crushed by disk mill to make fine powder under 210 μm diameter. Contents of Ca, Si, Mg, Mn, Fe, Al and P in each fertilizer powder were determined by glass bead XRF (ZSX Primus II, Rigaku) (Kimura and Yamada Citation1996).
Observation of Si and other minerals in slag fertilizers by EPMA
In order to observe Si and other minerals in a cross section of slag fertilizers by electron probe micro-analyzer (EPMA), we prepared the fertilizer specimens as follows (). Several spherical granules of each fertilizer were embedded in a pillar-shaped epoxy resin (Epomount, REFINETECH) of diameter 25 mm and height 25 mm. This pillar-shaped resin specimen was ground from the top to the level where the cross section of the fertilizer granule appeared using a plane grinding machine (GS-52PF, Kuroda Precision Industries). The cross section of fertilizer was polished on a plain glass plate using diamond pastes (SP-O, Asahi Diamond Industrial) with diameter 25 and 9 μm in series. Then it was polished using diamond pastes with diameter 6 and 1 μm in series. After removal of the diamond pastes, the surface of the cross section of the resin specimen was coated with gold using an auto fine coater (JFC-1600, JEOL). The gold-coated resin specimen was analyzed by EPMA (JXA-8621MX, JEOL). A square region (3 × 3 mm) including the cross section of one fertilizer granule was analyzed by EPMA to elucidate two-dimensional distribution images of Si, Ca, O, Mg, Al, Mn and Fe, respectively, in the cross section of the fertilizer granule. After the first analysis by EPMA, the gold coat on the surface of resin specimen was removed with tissue paper coated with diamond paste, diameter 1 μm. One resin specimen was prepared for each fertilizer. Thus we prepared the resin specimens to be set in a paddy field in Shibata city, Niigata prefecture, Japan (soil type: Bleached Lowland Paddy Soils, generally called ‘degraded paddy soils’). Analysis data of the soil are shown in . A square area, 50 × 50 cm, in the paddy field was not transplanted for setting the resin specimen. This square area was surrounded by cultivated rice plants (Oryza sativa L., cv. Koshihikari) during experiments. At 45 d after transplanting, the resin specimen was set on soil in the water-flooded paddy field. The cross section of the fertilizer granule was positioned at the same level as the paddy soil surface (). At 75 d after setting in paddy, each resin specimen was re-collected. After removal of adhesion matter from the top surface of the resin specimen, this surface was coated again with gold using the auto fine coater (JFC-1600, JEOL). The gold-coated resin specimen was analyzed again by EPMA (JXA-8621MX, JEOL) to elucidate two-dimensional distribution images of Si, Ca, O, Mg, Al, Mn and Fe, respectively, at the same position as the first EPMA analysis. The contents of each element are shown using colors from high content to low content: white, pink, red, yellow, light green, green, light blue, blue and black in turn, in the EPMA mapping images (–). A comparison of two images of Si, Ca, O, Mg, Al, Mn and Fe distributions before and after setting in paddy field clarifies the elution of each element in the paddy field in static condition and the microstructure where each element eluted from.
Figure 1 Slags used for fertilizers from the steel-making process. Water-cooled granulated blast furnace slag and air-cooled blast furnace slag come from the blast furnace. Dephosphorization slag comes from the hot metal pretreatment process. Decarburization slag comes from the basic oxygen furnace. These slags are used for silicate fertilizer, lime fertilizer, phosphate fertilizer and special fertilizer in Japan.
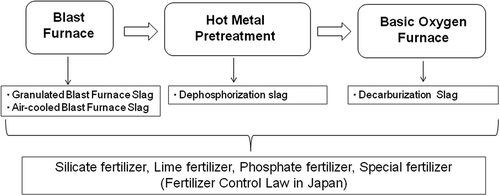
Figure 2 Preparation of slag fertilizer in epoxy resin, and electron probe micro-analyzer (EPMA) analysis. Steel slag fertilizers were embedded in epoxy resin. Epoxy resin was ground and polished to expose the cross section of each fertilizer. After the first EPMA analysis, this resin specimen was set in paddy soil for 75 d. Then it was re-collected for the second EPMA analysis. The first and second EPMA mapping images were compared.
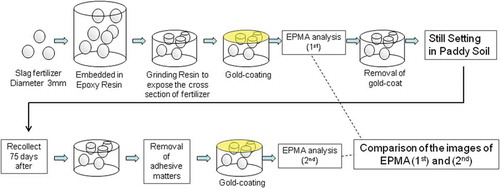
Figure 3 Slag fertilizers in epoxy resin set in paddy soil. The resin specimen was put on paddy soil. The cross section of fertilizer was positioned at the same level as the paddy soil surface.
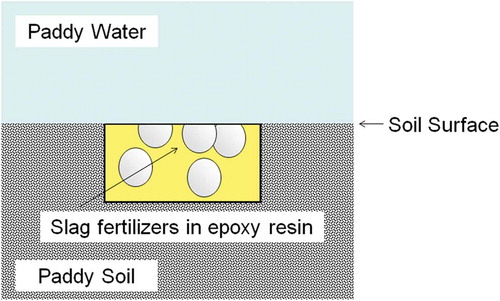
Table 1 Analysis data of soil.
Evaluation of available silicate by an extraction method using cation exchange resin
We tried to analyze available silicate in slag fertilizers by an extraction method using cation exchange resin (Kato and Owa Citation1997). But the cation exchange resin used by Kato and Owa (Citation1997; amberlite IRC50, Organo) was not commercially available. Yamashita et al. (Citation2013) reported that cation exchange resin (DIAION WK40L, Mitsubishi Chemical) was available instead of Amberlite IRC50 to evaluate available silicate in slag fertilizers. Therefore, we used DIAION WK40L as the cation exchange resin to evaluate available silicate. Each slag fertilizer was crushed with a ball mill to fine powder under 210 μm diameter. One tenth of a gram of this fine powder of slag fertilizer and 0.5 g of cation exchange resin were added into 400 mL of distilled water in a plastic bottle (volume 500 mL). The screw cap of the bottle was fastened. This bottle was shaken at 100 rpm at 25°C. Ten milliliters of solution in the bottle was collected at 24, 48, 96, 192 and 288 h after addition of slag fertilizer into water. The collected solution was filtrated with a 0.2 μm pore size filter. The filtrated solution was used for the determination of Si concentration. The Si concentration in the collected solution was analyzed with a spectrophotometer (U-2910, Hitachi). The Si content in 1 kg of slag fertilizer was calculated from the determined Si concentration in the collected solution (n = 3).
Substance identification by X-ray analysis
Substances contained in the slag fertilizers were identified using a wide angle X-ray diffractometer (RINT1000, Rigaku).
RESULTS
Composition of fertilizers
The compositions of three types of fertilizers made from granulated blast furnace slag, dephosphorization slag and decarburization slag are shown in . Si, Ca, Mg, Al and P contents are described in their oxide forms in . The silica (SiO2) content was highest in the fertilizer made from granulated blast furnace slag. The calcium oxide (CaO) content was about the same in these three types of slag fertilizers. The magnesium oxide (MgO) content was low, about one tenth of the CaO content, in these three types of slag fertilizers. The aluminum oxide (Al2O3) content in the fertilizer made from granulated blast furnace slag was clearly higher than that in other two slag fertilizers. The Mn content had a similar value in the three types of slag fertilizers. The Fe content in the fertilizer made from decarburization slag was the highest. There was little Fe in the fertilizer made from granulated blast furnace slag. The phosphorus pentoxide (P2O5) content in the fertilizer made from dephosphorization slag was slightly higher than that from decarburization slag. The P2O5 content in the fertilizer made from granulated blast furnace slag was very low.
Table 2 Composition of three types of slag fertilizers (kg kg–1 fertilizer).
Observation of Si and minerals in slag fertilizers by EPMA
EPMA mapping images of Si, Ca, O, Mg, Al, Mn and Fe in the cross section of slag fertilizers before and after setting in the paddy field for 75 d are shown in (granulated blast furnace slag fertilizer), (dephosphorization slag fertilizer) and (decarburization slag fertilizer).
Figure 4 Electron probe micro-analyzer (EPMA) mapping images of granulated blast furnace slag fertilizer. Two-dimensional distribution images of silicon (Si), calcium (Ca), oxygen (O), magnesium (Mg), aluminum (Al), manganese (Mn) and iron (Fe) in the cross section of granulated blast furnace slag fertilizer before and after setting in paddy field for 75 d. Contents of each element are shown using colors from high content to low content: white, pink, red, yellow, light green, green, light blue, blue and black in turn.
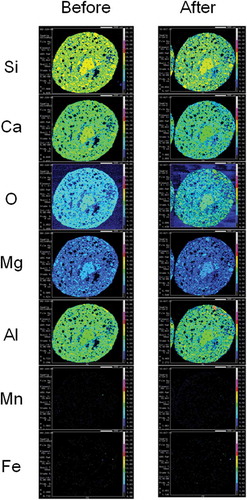
Figure 5 Electron probe micro-analyzer (EPMA) mapping images of dephosphorization slag fertilizer. Two-dimensional distribution images of silicon (Si), calcium (Ca), oxygen (O), magnesium (Mg), aluminum (Al), manganese (Mn) and iron (Fe) in the cross section of dephosphorization slag fertilizer before and after setting in paddy field for 75 d. Contents of each element are shown using colors from high content to low content: white, pink, red, yellow, light green, green, light blue, blue and black in turn.

Figure 6 Electron probe micro-analyzer (EPMA) mapping images of decarburization slag fertilizer. Two-dimensional distribution images of silicon (Si), calcium (Ca), oxygen (O), magnesium (Mg), aluminum (Al), manganese (Mn) and iron (Fe) in the cross section of decarburization slag fertilizer before and after setting in paddy field for 75 d. Contents of each element are shown using colors from high content to low content: white, pink, red, yellow, light green, green, light blue, blue and black in turn.
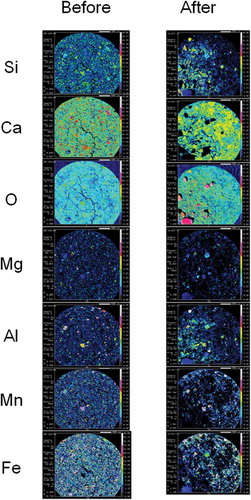
Observation of Si by EPMA
In , Si was detected homogeneously in the EPMA mapping image of granulated blast furnace slag fertilizer. A comparison of Si EPMA mapping images before and after setting in the paddy field elucidated that Si eluted slightly from granulated blast furnace slag fertilizer. As shown in , Si was detected in localized microstructures in the EPMA mapping image of dephosphorization slag fertilizer. A comparison of the Si EPMA mapping image before and after setting in the paddy field elucidated that Si eluted clearly from dephosphorization slag fertilizer in paddy field. Si eluted from the microstructures where Si, Ca and O coexisted. But Si did not elute from the microstructures where Si, Ca, O, Al and Mg coexisted. Therefore, Si elution from dephosphorization slag fertilizer depended on localized microstructures. As shown in , Si was also detected in localized microstructures in the EPMA mapping image of decarburized slag fertilizer. The left side of the EPMA mapping image of decarburization slag fertilizer was contaminated by inseparable adherents which we failed to remove. Therefore, the EPMA mapping image of decarburization slag fertilizer after setting in paddy field should be compared on the right side of the image. Si also eluted clearly from decarburization slag fertilizer in paddy field.
Observation of Ca by EPMA
As shown in , Ca was detected homogeneously in the EPMA mapping image of granulated blast furnace slag fertilizer. A Comparison of Ca EPMA mapping images before and after setting in the paddy field elucidated that Ca eluted slightly from this fertilizer. As shown in , Ca was detected in localized microstructures in EPMA mapping images of dephosphorization slag fertilizer. A comparison of Ca EPMA mapping images before and after setting in the paddy field elucidated that Ca eluted clearly from dephosphorization slag fertilizer in paddy field. Ca eluted from microstructures where Si, Ca and O coexisted. But Ca did not elute from microstructures where Si, Ca, O, Al and Mg coexisted similar to Si elution. Therefore, Ca elution from dephosphorization slag fertilizer depended on localized microstructures. As shown in , Ca was also detected in localized microstructures in EPMA mapping images of decarburized slag fertilizer. A comparison of Ca EPMA mapping images before and after setting in the paddy field elucidated that Ca eluted from this fertilizer but diffused from the high Ca content microstructures (red color) to surrounding area (yellow color; ).
Observation of O by EPMA
O was detected uniformly in the three types of steel slag fertilizers (Figs 5–7). There was no clear difference in O content between before and after setting in the paddy field. Therefore, oxides of Ca, Si, Mg, Al, Mn and Fe are possible components in these slag fertilizers. Some high O content islands (red color) in decarburized slag fertilizer () are inseparable adherents which we failed to remove.
Observation of Mg by EPMA
As shown in , Mg was detected homogeneously in EPMA mapping images of granulated blast furnace slag fertilizer. A comparison of Mg EPMA mapping images before and after setting in the paddy field elucidated that Mg elution from this fertilizer was not clear. As shown in , Mg was detected in localized microstructures in EPMA mapping images of dephosphorization slag fertilizer. Comparison of Mg EPMA mapping images before and after setting in the paddy field elucidated that Mg slightly eluted from dephosphorization slag fertilizer in paddy field. Mg did not elute from microstructures where Si, Ca, O, Al and Mg coexisted, similar to Si and Ca elution. As shown in , a small amount of Mg was detected in localized microstructures in EPMA mapping images of decarburization slag fertilizer. A comparison of Mg EPMA mapping images before and after setting in the paddy field elucidated that there was no clear difference in Mg content before and after in decarburization slag fertilizer.
Observation of Al by EPMA
As shown in , Al was detected homogeneously in granulated blast furnace slag fertilizer in EPMA mapping images, similar to Ca, Si, Mg and O. These homogeneous distributions of Si, Ca, Mg, Al and O in granulated blast furnace slag fertilizer mean that this slag is amorphous. There was no clear difference in Al content before and after setting in the paddy field. Therefore, Al did not elute from granulated blast furnace slag fertilizer. As shown in , Al was detected in localized microstructures in EPMA mapping images of dephosphorization slag fertilizer. A comparison of Al EPMA mapping images before and after setting in the paddy field elucidated that Al eluted very little from dephosphorization slag fertilizer in the paddy field. Al coexisted with Si, Ca and Mg but not Mn and Fe in microstructures of dephosphorization slag fertilizer. Si in such Al- and Mg-rich microstructures could not elute in paddy field. As shown in , a small amount of Al was detected in localized microstructures in EPMA mapping images of decarburization slag fertilizer. A comparison of Al EPMA mapping images before and after setting in the paddy field elucidated that there was no clear difference in Al content before and after setting in the paddy field in decarburization slag fertilizer.
Observation of Mn by EPMA
As shown in , Mn was not detected by EPMA in granulated blast furnace slag fertilizer. As shown in , a small amount of Mn was detected in localized microstructures in EPMA mapping images of dephosphorization slag fertilizer. A comparison of Mn EPMA mapping images before and after setting in the paddy field elucidated that Mn content increased after setting in the paddy field (white- and red-colored microstructures). Therefore, we could not confirm Mn elution from dephosphorization slag fertilizer from EPMA observation. As shown in , Mn was also detected in localized microstructures in EPMA mapping images of decarburization slag fertilizer. Many high Mn content microstructures like fine stars (white color) were detected in this fertilizer. A comparison of Mn EPMA images before and after setting in the paddy field elucidated that Mn eluted slightly from this fertilizer in the paddy field.
Observation of Fe by EPMA
As shown in , Fe was not detected by EPMA in granulated blast furnace slag fertilizer. As shown in , Fe was detected in localized microstructures with high content (white color) in EPMA mapping images of dephosphorization slag fertilizer. A comparison of Fe EPMA mapping images before and after setting in the paddy field elucidated that Fe content did not change clearly. Therefore, we could not confirm Fe elution from dephosphorization slag fertilizer in paddy field. As shown in , Fe was also detected in localized microstructures in EPMA mapping images of decarburization slag fertilizer. Many high Fe content microstructures like fine stars (white and red), similar to Mn, were detected in this fertilizer. A comparison of Fe EPMA mapping images before and after setting in the paddy field elucidated that Fe eluted slightly from this fertilizer in the paddy field.
Available silicate by extraction method using cation exchange resin
Contents of available silicate in three types of slag fertilizers and air-cooled blast furnace slag were analyzed by an extraction method using cation exchange resin (DAIAION WK40L, Mitsubishi Chemical, Japan; ).
The contents of available silicate in three types of slag fertilizers and air-cooled blast furnace slag were as follows: dephosphorization slag fertilizer (0.152 kg SiO2 kg–1 fertilizer) > air-cooled blast furnace slag (0.137 kg SiO2 kg−1 fertilizer) > decarburization slag fertilizer (0.105 kg SiO2 kg−1 fertilizer) > granulated blast furnace slag fertilizer (0.094 kg SiO2 kg−1 fertilizer).
Identification by X-ray diffraction of substances composing slag fertilizers
X-ray diffraction of granulated blast furnace slag fertilizer is shown in a. A broad peak in X-ray diffraction means that this fertilizer has an amorphous structure. Rapid cooling of hot blast furnace slag by water to make granulated blast furnace slag is possible because of this amorphous structure. X-ray diffraction of air-cooled blast furnace slag is shown in b. Gehlenite (Ca2Al2SiO7) and akermanite (Ca2MgSi2O7) were identified as the main components of air-cooled blast furnace slag. Slow cooling of hot blast furnace slag in air is possible because of the crystallization of these substances. X-ray diffraction of dephosphorization slag fertilizer is shown in c. Calcium silicate or larnite (Ca2SiO4) was identified as a main component of dephosphorization slag fertilizer. Gehlenite and akermanite were also identified in this fertilizer. X-ray diffraction of decarburization slag fertilizer is shown in d. Ca2SiO4 was identified as a main component of decarburization slag fertilizer, similar to dephosphorization slag fertilizer. Srebrodolskite (Ca2Fe2O5), calcium iron oxide (CaFeO2), brown millerite [Ca2(Al,Fe+3)2O5] and wustite (FeO) were also detected in this fertilizer. Substances identified by X-ray diffraction are shown in .
Figure 8 X-ray diffraction of slag fertilizers. Substances contained in slag fertilizers were identified using wide angle X-ray diffraction (RINT 1000, RIGAKU): (a) granulated blast furnace fertilizer, (b) air-cooled blast furnace slag, (c) dephosphorization slag fertilizer, (d) decarburization slag fertilizer.
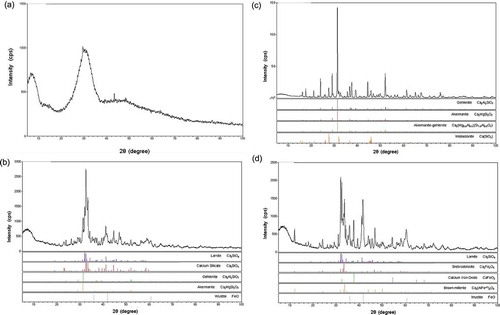
Table 3 Identification of substances by X-ray diffraction.
DISCUSSION
Si elution from fertilizers and soils has been evaluated by various elution tests (Imaizumi and Yoshida Citation1958; Takahashi and Nonaka Citation1986; Sumida Citation1991; Kitada et al. Citation1992; Kato and Owa Citation1997). In these tests, Si elution was accelerated by using fine powder samples and/or by stirring the elution test medium. But we wanted to clarify actual Si elution from fertilizers in a paddy environment in static conditions. In order to observe actual Si elution from steel slag fertilizers, we made epoxy resin specimens in which steel slag fertilizers were embedded. The cross section of fertilizers appeared on the surface of the epoxy resin specimen. EPMA analyses before and after setting these specimens on the paddy field elucidated the elution of Si and other minerals from microstructures in the fertilizers. This study is the first case to successfully observe the elution of Si and other minerals from fertilizers in a paddy field in static conditions.
Si eluted clearly from fertilizer made from dephosphorization slag and decarburization slag in a paddy field by EPMA analyses (Figs 4–6). This result corresponded to available silicate extraction using cation exchange resin, as shown in . Ca2SiO4 was the main peak of Si-containing matter in the X-ray diffraction of fertilizers made from dephosphorization slag and decarburization slag (c, d; ). In fact, Si eluted mainly from the microstructure where Ca, Si and O coexisted in fertilizers made from dephosphorization slag and decarburization slag, according to the EPMA mapping images (Figs 5 and 6).
A slight elution of Fe and Mn was observed only from fertilizer made from decarburization slag, in the paddy field by EPMA (Fig. 6). Therefore, fertilizer made from decarburization slag is suitable to supply Fe and Mn to a degraded paddy field where Fe and Mn have been lost. Fe is also effective in the suppression of methane emissions from paddy fields (Ali et al. Citation2008; Furukawa and Inubushi Citation2002, Citation2004; Thanh et al. Citation2013; Wang et al. Citation2012). The application of fertilizer made from decarburization slag is possibly effective on the supply of Fe to soil, and methane emission suppression. Singla and Inubushi (Citation2013) applied fertilizer made from the same decarburization slag to sandy soil in Chiba, Japan, and confirmed methane emission suppression.
A comparison of Mn EPMA mapping images before and after setting in a paddy field (Fig. 5) elucidated that Mn content increased after setting in the paddy field. There are two possible mechanisms of Mn content increase on the surface of dephosphorization slag fertilizer. One possible mechanism is the supply of Mn from irrigation water and deposition on the surface. Another possible mechanism is the deposition of Mn which eluted from the fertilizer. We speculate that these two possible mechanisms explain the increase of Mn content on the surface of fertilizer after setting in a paddy field.
Concerning blast furnace slag, the method used to cool hot slag caused a very clear difference in Si elution characteristics. Si eluted slightly from fertilizer made from granulated blast furnace slag (Fig. 4). The homogeneous distribution of Si, Ca, Mg and Al in the fertilizer made of granulated blast furnace slag reflected its amorphous structure, proven by a broad peak found by X-ray diffraction (a). The extraction method using cation exchange resin elucidated that the available silicate content in granulated blast furnace slag was lower than that in air-cooled blast furnace slag (). Si probably eluted from Ca2Al2SiO7 and Ca2MgSi2O7 of air-cooled blast furnace slag but not from amorphous granulated blast furnace slag in the extraction method using cation exchange resin (Figs 7 and 8a, b). Therefore, air-cooled blast furnace slag is more suitable for use as a silicate fertilizer than granulated blast furnace slag is. Ando et al. (Citation1981) compared the Si solubility of water-cooled blast furnace slag and air-cooled blast furnace slag to ammonium citrate solution (pH 4.5). They reported that the Si solubility of the air-cooled blast furnace slag was lower than that of the water-cooled one. But they also reported that Si uptake by rice plants was higher from air-cooled blast furnace slag than from water-cooled blast furnace slag in pot experiments. Their results mean that rice plants can utilize Si more efficiently from air-cooled blast furnace slag than the water-cooled one. We speculate that the pH of 4.5 of ammonium citrate solution is too acidic to evaluate Si solubility from slag fertilizer, because the pH in paddy soil is generally between 5.5 and 6.5.
There have been various methods used to evaluate Si elution from fertilizers and soils (Imaizumi and Yoshida Citation1958; Takahashi and Nonaka Citation1986, Sumida Citation1991; Kitada et al. Citation1992; Kato and Owa Citation1997). Extraction of Si using cation exchange resin (DIAION WK40L, Mitsubishi Chemical; Yamashita et al. Citation2013) elucidated that contents of available Si in three types of steel slag fertilizers were as follows: dephosphorization slag fertilizer > decarburization slag fertilizer > granulated blast furnace slag fertilizer. This result corresponded to Si elution observed by EPMA analyses. Therefore, extraction of Si using cation exchange resin (DIAION WK40L, Mitsubishi Chemical) is a useful method to evaluate the available Si in steel slag fertilizers.
For comparison of the efficacy of Si elution from three types of slag fertilizers, available silicate data from , , and silicate content data from , , and the ratio of A/B are given in . The A/B value represents the efficacy of Si elution from slag fertilizers. The A/B value was the highest (0.81) in the fertilizer made from decarburization slag. Ca2SiO4 was the only Si-containing substance detected in decarburization slag by X-ray diffraction (). Therefore, efficient Si elution from decarburization slag comes from Ca2SiO4. The A/B value was the second highest (0.66) in the fertilizer made from dephosphorization slag. Dephosphorization slag also contained Ca2SiO4. Efficient Si elution from dephosphorization slag mainly comes from Ca2SiO4, as in decarburization slag. Compared with the A/B value of decarburization slag and dephosphorization slag, the A/B value of air-cooled blast furnace slag and granulated blast furnace slag was low—0.4 and 0.28, respectively. Air-cooled blast furnace slag did not contain Ca2SiO4 but did contain Ca2Al2SiO7, Ca2MgSi2O7 and Ca(SiO3) (wollastonite). From these results, we consider that Ca2SiO4 is the causative substance for the efficient elution of Si from slag fertilizers. Although the efficacy of Si elution is the highest from decarburization slag, Si content in decarburization slag is low (0.13) compared with dephosphorization slag (0.23) and blast furnace slag (0.34). The content of available Si was the highest in dephosphorization slag and the second highest in air-cooled blast furnace slag. Therefore, fertilizers made from dephosphorization slag or air-cooled blast furnace slag are suitable as silicate fertilizer.
Table 4 Comparison of efficacy of silicon (Si) elution from slag fertilizers.
We set the resin specimen so that the cross section of the fertilizer granule was positioned at the level of the soil surface. Therefore, the analysis in this study only elucidated Si and mineral elution at the soil surface. The soil surface is in an oxidative condition but deep soil is in a reductive condition. Elution of Si and minerals from the slag fertilizer is probably different between the soil surface and the deep soil. We want to investigate the dependency of Si and mineral elution from slag fertilizer on soil depth in future study. Furthermore, we produced only two-dimensional distributions of Si and minerals as colored mapping images by EPMA in this study. We plan to conduct quantitative analyses, such as how much Si eluted will be possible from EPMA data, in future study.
CONCLUSION
The combination of still setting of slag fertilizers embedded in epoxy resin and EPMA analyses made the observation of Si and mineral elution in a paddy field possible. Based on the results from EPMA analyses, available silicate extraction and X-ray diffraction, we concluded that fertilizers made from dephosphate slag and air-cooled blast furnace slag are suitable as silicate fertilizer. Ca2SiO4 (calcium silicate or larnite) is the main source of Si elution in decarburization slag and dephosphorization slag. Ca2Al2SiO7 (gehlenite) and Ca2MgSi2O7 (akermanite) are possible sources of Si elution in dephosphorization slag and air-cooled blast furnace slag. Water-cooled granulated blast furnace slag is amorphous; Si did not elute efficiently from granulated blast furnace slag. Decarburization slag is suitable for fertilizers to supply Fe and Mn in addition to Si and Ca.
ACKNOWLEDGMENTS
This research was conducted as joint research between Niigata Agricultural Research Institute, Chiba University and Nippon Steel & Sumitomo Metal Corporation.
REFERENCES
- Ali MA, Lee CH, Kim PJ 2008: Effect of silicate fertilizer on reducing methane emission during rice cultivation. Biol. Fertil Soils, 44, 597–604. doi:10.1007/s00374-007-0243-5
- Ando J, Takemura K, Sampei M 1981: Sturucture, solubility and agronomic response of blast furnace slags. Jpn. J. Soil. Sci. Plant Nutr., 52, 523–529. (in Japanese).
- Datnoff LE, Deren CW, Snyder GH 1997: Silicon fertilization for disease management of rice in Florida. Crop Protection, 16, 525–531. doi:10.1016/S0261-2194(97)00033-1
- Furukawa Y, Inubushi K 2002: Feasible suppression technique of methane emission from paddy soil by iron amendment. Nutr. Cycling Agroecosyst., 64, 193–201. doi:10.1023/A:1021150831735
- Furukawa Y, Inubushi K 2004: Evaluation of slag application to decrease methane emission from paddy soil and fate of iron. Soil Sci. Plant Nutr., 50, 1029–1036. doi:10.1080/00380768.2004.10408570
- Hayasaka T, Fujii H, Ishiguro K 2008: The role of silicon in preventing appressorial penetration by the rice blast fungus. Phytopathology, 98, 1038–1044. doi:10.1094/PHYTO-98-9-1038
- Husnain, Wakatsuki T, Setyorini D, Hermansah, Sato K, Masunaga T 2008: Silica availability in soils and river water in two watersheds on Java Island, Indonesia. Soil Sci. Plant Nutr., 54, 916–927. doi:10.1111/j.1747-0765.2008.00313.x
- Imaizumi K, Yoshida S 1958: Edophological studies on silicon supplying power of paddy fields. Bulletin Natl. Inst. Agric. Sci. series B, 8, 261–304. (in Japanese).
- Kato N 2002: Silicate and crop production, edited by Japanese Society of Soil Science and Plant Nutrition, p.120. (in Japanese).
- Kato N, Owa N 1997: Evaluation of Si availability in slag fertilizers by an extraction method using a cation exchange resin. Soil Sci. Plant Nutr., 43, 351–359. doi:10.1080/00380768.1997.10414759
- Kimura J, Yamada Y 1996: Evaluation of major and trace element XRF analyses using a flux to sample ratio of two to one glass beads. J. Min. Petr. Econ. Geol., 91, 62–72. doi:10.2465/ganko.91.62
- Kitada K, Kamekawa K, Akiyama Y1992: The dissolution of silica in soil in rotational paddy fields by the surface water dissolution method. Jpn. J. Soil Sci. Plant Nutr., 63, 31–38. (in Japanese).
- Ma JF, Takahashi E 2002: Soil, Fertilizer, and Plant Silicon Research in Japan, Elsevier.
- National Institute for Agro-Environmental Sciences 1992: Fertilizer Analysis Methods, Japan Fertilizer and Feed Inspection, Tokyo (in Japanese).
- Nourin Toukei Kyoukai 2010: Pocket Hiryou Youran, pp. 8. Nourin Toukei Kyoukai, Tokyo (in Japanese).
- Sato Y, Fujiwara H, Udatsu T 1990: Morphological differences in silica body derived from motor cell of indica and japonica in rice. Japan J. Breed, 40, 495–504. doi:10.1270/jsbbs1951.40.495
- Singla A, Inubushi K 2013: Effect of slag-type fertilizers on N2O flux from komatsuna vegetated soil and CH4 flux from paddy vegetated soil. Paddy Water Environ., doi:10.1007/s10333-013-0405-z (in press).
- Sumida H 1991: Characterization of silica dissolution and absorption in paddy soils. Application to soil test for available silica. Jpn. J. Soil Sci. Plant Nutr., 62, 378–385. (in Japanese).
- Takahashi K, Nonaka K 1986: Method of measurement of available silicate in paddy field. Jpn. J. Soil Sci. Plant Nutr., 57, 515–517. (in Japanese).
- Thanh N, Ha T, Hung N, Endoh K, Ito K, Inubushi K 2013: Initial research into the decrease of methane emission mitigation in paddy by steel-making slag. Sci. Technol. J. Agric. Rural Dev., 1, 51–58.
- Wang W, Li P, Zeng C, Tong C 2012: Evaluation of silicate iron slag as a potential methane mitigating method. Advanced Mater. Res., 468–471, 1626–1630. doi:10.4028/www.scientific.net/AMR.468-471
- Yamashita K, Nizuma S, Fujisawa E 2013: Evaluation of silicate availability in siliceous materials by the modified extraction method using a new cation exchange resin. Jpn. J. Soil Sci. Plant Nutr., 84, 166–170. (in Japanese).