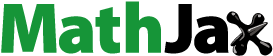
Abstract
In this article, the breaking elongation properties of woven fabrics with incorporated PBT yarns are presented. Different polybutylene terephthalate (PBT) yarns (multifilament PBT yarn, cotton core yarn and twisted viscose yarn, both with PBT in the core) were used. Textured PBT yarns have latent elastic properties, which become visible after the thermal treatment by the finishing process. The aim was to determine which of the constructional parameters is most important in analysing the shrinkage of fabrics after treatment, breaking elongation properties of all tested fabrics, and breaking elongation properties of woven fabrics before and after treatment. A multivariate statistical method ANOVA was used for the analysis. The results show that treatment was by far the most influential factor in the study of breaking elongation of all tested fabrics. When analysing the fabrics separately before and after treatment, the construction of the PBT yarn and the weave were found to be statistically significant parameters.
Introduction
In recent decades, the demand for woven fabrics with higher elastic properties under small loads has increased. The most common method to achieve higher elasticity of woven fabric is the incorporation of elastic yarns into woven fabrics. But the use of elastic yarns makes the product more expensive by reducing the speed of weaving (Kadoğlu et al., Citation2016).
Stretch woven fabrics are comfortable to wear, easy to maintain and have a nice handle (Dimitrovski et al., Citation2012; Štrukelj, Citation2012; Štrukelj & Dimitrovski, Citation2012). The most popular stretch fibres, the so-called elastane fibres, have different trademarks. Spandex is any synthetic fibre that consists of at least 85% segmented polyurethane. It is a general term used to describe elastomeric fibres that have an extension – at break of more than 200%. The word ‘spandex’ is an anagram of the word ‘expands’ and is also known as Elastin. Well-known trademarks for elastane fibres are Lycra from DuPont and Dorlastan from Bayer (Senthilkumar et al., Citation2011). The most commonly used elastane fibre is Lycra, which has many advantages but also some disadvantages; for example, it cannot be washed at temperatures above 40 °C, it can cause problems in production because of its too high elasticity, it is quite expensive and it is difficult to dye. For this reason, Lycra cannot be combined with other dyed synthetic multifilament yarns and should be used as core spun yarn or as twisted yarn in combination with natural fibres, which increases the price. There are also problems in the production of woven fabrics with elastane yarns, even if the proportion of elastane yarns in woven fabrics is low (2% to 5%). The problems are caused by the high elongation of the elastic yarns; therefore, the tension of the yarns must be controlled progressively, which usually leads to a reduction in production speed (Štrukelj & Dimitrovski, Citation2012).
At the beginning of the 2000s, a new, cheaper material with elastic properties came onto the market. This material is polybutylene terephthalate (PBT). PBT is more expensive than polyethylene terephthalate (PET), the most commonly used polyester, but cheaper than elastane yarns (Dimitrovski et al., Citation2012; Štrukelj, Citation2012; Štrukelj & Dimitrovski, Citation2012).
PBT is a semi-aromatic polyester. The polymer production of PBT is similar to polyetilen teraphtalate (PET) synthesis and includes direct esterification and ester interchange polymerization. In the condensation reaction of the dihydric alcohol with terephthalic acid, ethylene glycol is replaced by butanediol with four methylene groups (Celik et al., Citation2018; Hu et al., Citation2008).
PBT has a lower Tdi value (initial degradation temperature), lower tensile strength and similar surface characteristics compared with normal PET. On the other hand, PBT has a higher elongation and recovery performance than standard PET.
Filament yarns are textured to achieve more softness, volume, warmth and elongation. PBT-textured yarns have latent elastic properties, which become apparent after the thermal treatment achieved by the finishing process (Bizjak et al., Citation2017; Štrukelj & Dimitrovski, Citation2012).
The latent elastic properties of textured PBT yarn have been explained by changes in the crystal structure of fabrics. Two different crystalline forms are called the forms α and β. The crystal structure of PBT changes to the β form when subjected to a hot stretch treatment and to the α form when relaxed. The raw PBT yarn represents an extended β form, which changes to the α form during thermal treatment, which causes the shrinkage of fabrics depending on the amount of PBT yarn and the fabric structure (Štrukelj & Dimitrovski, Citation2012).
shows the properties of PBT, PET, PA6/66 and Spandex fibres. The performance of PBT fibres can be summarized as follows (Bizjak et al., Citation2017; Hu et al., Citation2008; Štrukelj & Dimitrovski, Citation2012):
Table 1. Comparison of fibre properties (Hu et al. Citation2008).
high elongation even at low loads and fast recovery from deformation after re-loading;
resistance to chlorine, saltwater and colour fading;
hydrophobic fibre;
the chemical resistance of PBT yarns is better than that of elastane;
good dyeing properties at boiling point (it can be dyed with disperse dyes under atmospheric pressure without carrier in bright colours);
good colour fastness;
good dimensional stability even when wet.
PBT yarns can be used in various applications as clothing (both knitted and woven in hosiery and intimate apparel, lining, denim and swimwear, sportswear), upholstery, carpets, medical textiles and other new products containing elastic fibres (Bedez Ute, Citation2019; Bizjak et al., Citation2017; Hu et al., Citation2008).
The shrinkage of PBT yarns in the loose state differs from shrinkage in the clam state (yarns in the fabric structure), which is influenced by many factors, especially weave and thread density. A large number of interlacing points in the structure mean more friction surfaces, which inhibit the contraction of fibres/threads in the fabrics. The elasticity of PBT fabrics, which is achieved after finishing, depends not only on the design parameters of the fabrics (percentage of PBT in the yarn and in the fabrics, yarn structure …), but also on the settings on the weaving machine (tread tension, speed, weft insertion technology …) (Bizjak et al., Citation2017).
In the literature there are some studies describing the properties and use of PBT yarn.
Verdu et al. compared DOW XLATM fiber made from core-spun yarn with elastic PBT yarn in polyester/cotton woven fabrics used for workwear. The results showed that the use of DOW XLA™ fiber in a core-spun yarn to elasticize fabrics for workwear provides additional comfort compared with non-elastic fabrics by providing more stretch and improved hand feel. These fabrics showed a thermo-physiological and sensory comfort that remained constant during washing cycles. The performance differences found when comparing traditional non-elastic and elastic PBT fabrics were explained by an elastic fibre in the core yarn, which showed a weakened elastic behaviour after the yarn and fabric finishing process (Verdu et al., Citation2009).
Bedez Ute analysed the mechanical and dimensional properties of denim fabrics produced with double core and core-spun weft yarns with different weft densities. Elastane, PBT and end elastomulitester (EME) were used as core material. The research concluded that weft density is more effective for the mechanical and dimensional properties of denim yarns than weft composition (Bedez Ute, Citation2019).
Bizjak et al. investigated the properties of woven fabrics made of cotton/PBT yarn. They compared the properties of woven fabrics made of pre-treated core-spun cotton/PBT with the properties of untreated core-spun cotton/PBT yarns. Woven fabrics with untreated core-spun cotton/PBT yarns were then treated. The results showed large differences between samples with pre-treated cotton/PBT yarn in the weft direction and samples treated after weaving (Bizjak et al., Citation2017).
Kadoglu et al. compared fabrics made of 100% cotton, core-spun cotton/elastane and cotton PBT as well as elastane and PBT filament in the weft. They investigated fabric thickness, mass, elongation, dimensional stability, air permeability and thermal conductivity before and after the treatment of the fabrics. The fabrics gain elasticity through the treatment. The research concluded that fabrics containing PBT do not differ significantly from fabrics containing elastane after treatment in hot water (Kadoğlu et al., Citation2016).
Celik et al. are investigating the bursting strength and bursting distension values of knitted fabrics samples made from nine different false-twist textured, stretchable PBT yarn samples with the same fabric's structural parameters. They found that the texturing temperature has a significant influence on bursting distension performances and that the aspect ratio has a significant influence on both bursting strength and distension performances (Celik et al., Citation2018).
Chen et al. investigated the elastic elongation and elastic recovery of warp-knitted fabrics made of a combination of PET and PBT filaments. The results allow a better understanding of the elastic elongation and recovery behaviour of PET/PBT warp-knitted fabrics (Chen et al., Citation2017).
The tensile properties (load and elongation) are among the most important mechanical properties of woven fabrics and are also an indication of their quality when used for apparel and technical purposes. Elongation properties are one of the properties to which fabrics are exposed during their use and consequently during the lifetime of the products. Elongation properties are influenced by the constructional parameters of woven fabrics, such as warp and weft density, yarn properties and weave (Grosberg, Citation1969; Hu, Citation2004; Realff et al., Citation1991).
Breaking elongation in one direction is influenced by the elongation of the threads in the tested direction, their density and the frequency of interlacing (weave). In general, higher elongation of the threads, higher density and higher frequency of interlacing lead to higher elongation of the fabrics in the tested direction (Grosberg, Citation1969; Hu, Citation2004; Vassiliadis et al., Citation2011).
The elasticity of the threads in woven fabrics, the frequency of thread interlacing (weave) and the tension of the threads during weaving influence the warp and weft crimp, which ultimately affects the elongation of woven fabrics (Vassiliadis et al., Citation2011). With such a number of influencing factors, it is difficult to predict which of them will have the greatest influence on the final properties of the fabric, especially for fabrics with increased elasticity.
The aim of this study was to investigate how constructional parameters (different construction of PBT yarns in the weft and different weave) of woven fabrics influence the shrinkage after treatment of fabrics in boiling water and the breaking elongation of woven fabrics. One of the objectives was also to determine which of the constructional parameters is the most important in the analysis of the shrinkage of fabrics after treatment, the elongation properties of all the fabrics tested and the elongation properties of woven fabrics before and after treatment. A multivariate statistical method ANOVA was used to determine the most influential factors.
Knowledge of the importance of construction parameters is important in the design and prediction of fabrics and their properties, both elastic and non-elastic. All final properties are influenced by several construction parameters, but their influence is impossible to predict without statistical methods. With the research, the comparison of the significant constructional parameters of elastic and non-elastic fabrics is carried out.
ANOVA allows to estimate the effects of individual independent variables – factors – on the response variable and also their interactions. The ANOVA determines the statistical significance of individual factors at a certain significance level α, in our case 0.05 and also defines their magnitude (Bona, Citation1993; Pavko Čuden et al., Citation2013).
Experimental part
Materials
For the purpose of this study, nine different woven samples were developed and produced. All samples were woven on a Minifaber loom with a jacquard mechanism T.I.S.
The warp yarn was 8 × 2 tex cotton yarn, the set warp density was 20 ends/cm and the set weft density 25 wefts/cm for all fabrics to ensure the compactness of the fabrics. The warp density could not be changed; therefore, the weft density was higher.
In the fabric construction, every fifth weft was a PBT containing yarn, and the other four wefts were the same yarn as the warp, 8 × 2 tex cotton. With this construction, we wanted to ensure the minimum quantity, i.e. the number of PBT yarns in the fabrics, which has a significant influence on the fabrics, and also to ensure that the PBT weft insertion does not interfere with weave pattern and the float of the yarns.
Yarns containing PBT had three different constructions:
100% PBT multifilament yarn (7.8 tex, 24 f) (PBT),
cotton core yarn (29.55 tex) with PBT (7.8 tex, 24 f) in the core (CO/PBT),
Twisted viscose yarn (20 × 2 tex) with PBT (5.6 tex) in the core of each individual yarn (CV/PBT).
shows the tensile properties of PBT yarns before and after treatment. As mentioned above, there is a significant difference between the shrinkage of yarns and the shrinkage of woven fabrics containing PBT yarns.
Table 2. Properties of used warp and weft yarns.
The samples were woven in three different weave types, using three different twill weaves with different floatation of the threads (one and two, two and three floating threads in both directions). The aim was to evaluate the influence of flotation on the shrinkage and elongation properties of the woven fabrics before and after treatment. The fabrics used are shown in .
Table 3. Weaves of investigated samples.
The woven fabrics were thermally treated in distilled, boiling water for 30 min and then dried for 24 h on a flat surface in a tension-free state. Two groups of samples were prepared, treated and non-treated. Comparisons between the groups were made to determine the difference in physical–mechanical properties.
Testing methods
In order to assess the influence of the constructional parameters on the physical–mechanical properties of the woven fabrics, various types of measurements were carried out.
Firstly, the physical properties of the treated and non-treated samples were measured according to standards: the density of the warp and weft threads (SIST EN 1049-2), the thickness (SIST EN ISO 5084), the mass per square metre (SIST EN 12127) and the shrinkage of the treated samples in warp and weft direction.
To measure the dimensional stability (shrinkage) in warp and weft direction, the fabric was cut into squares of 50 × 50 cm before treatment. After treatment, the new dimensions were measured and the shrinkage was calculated using Equation (1) according to the SIST EN ISO 6330 standard.
[1]
[1]
The breaking elongation was measured on the Instron 5567 dynamometer (Instron, USA) in accordance with SIST ISO 5081:1996 standard, with five measurements made for each sample. The results for all the measurements were carried out on the nontreated and treated fabrics to analyse the shrinkage effect and breaking elongation are presented in Appendix ( and ).
The experimental results were statistically processed by multifactor ANOVA at a significance level of 0.05. Three independent variables – factors – were selected for the statistical analysis of woven fabrics with PBT yarn incorporated in the weft, as shown in . Each factor had either two or three levels.
Table 4. Experimental design diagram.
The experiments consisted of three parts () as follows:
Table 5. Design of the study.
As preliminary studies, the treated fabrics containing different PBT yarns were tested. The purpose of this study was to estimate which of the two investigated factors are statistically more significant, i.e. had a stronger influence on the shrinkage of the fabrics.
The breaking elongation of all tested fabrics with incorporated PBT yarns was examined. According to the experimental design (), the number of treatments was 90 (2 × 3 × 3 × 5 repetitions). The purpose of this part was to find out how and to what extent the three examined factors influence the elongation of the woven fabrics.
Finally, the experimental results from B) were divided into two groups: before and after treatment, in order to study which are the most influential factors of fabrics before treatment in boiling water and after thermal treatment. The fabrics before the treatment have similar properties to conventional non-elastic fabrics and fabrics after the treatment exhibit elastic properties.
Results and discussion
Shrinkage after thermal treatment
The shrinkage of PBT yarns in the loose state is different from the shrinkage in the clamped state, that is, the yarn in the fabric structure.
The properties of PBT yarns and yarns containing PBT differ with treatment, as shown in . After treatment, the linear density increases, the breaking elongation of all tested yarns increases and the breaking strength of all tested yarns decreases.
After treatment, the physical properties of all tested fabrics change as shown in in the Appendix. Shrinkage of fabrics showen in in Appendix is affected by many factors, such as weave type and thread density, and results in a change in warp density, weft density, thickness and mass per square metre.
The warp density of the tested fabrics changes by 15% on average, while the weft density changes by only 5% on average. This is understandable since the PBT yarn is added in the weft direction and shrinks after treatment, which affects the warp density of the fabric. The results show that in the warp direction the highest density change is seen in Weave 3, as the flotation is the highest and therefore, the shrinkage is also the highest.
As already suspected, the thickness of the fabrics also increases on average by 76% and the mass per square metre increases on average by 23%. As expected, the highest increase in thickness and mass was found in fabrics with weave type 3, fabrics with the highest shrinkage. As the yarn in the fabrics shrinks, the thread density increases, resulting in an increase in the thickness and mass of the fabrics.
The statistical analysis of shrinkage in warp direction (S1) shows that there is no statistically significant factor affecting shrinkage (). The warp threads have the same linear density and the same construction for all woven fabrics and weft threads, including different PBT threads and different weaves, does not statistically influence shrinkage in the warp direction.
Table 6. Impact of PBT (in weft) and Weave on the shrinkage of fabrics in warp direction (S1).
The analysis of shrinkage in the weft direction (S2) shows two factors, Weave and PBT (), as statistically significant factors. According to the F-ratio, the influence of Weave is almost three times higher than the influence of PBT. Our results show that the weave has a higher influence on shrinkage due to the different floating of the threads, which shrink when treated in boiling water. If there were more PBT yarns in our samples and not only every fifth weft, the influence of the significant factors would probably be different because more PBT yarns in the fabrics should shrink more.
Table 7. Impact PBT (in weft) and Weave on the shrinkage of fabrics in weft direction (S2).
The influence of the Weave is statistically significant due to the types of weave used, with weave types with higher floating, exhibit higher shrinkage. During treatment, these threads can swell more than those with less floating. also shows that weave types 1 and 2 have almost the same influence on shrinkage in the weft direction, while weave type 3 gives the highest shrinkage. The shrinkage of weave type 3 is almost 10% higher than the shrinkage of weave types 1 and 2 due to its higher floating. Weave type 3 has the highest floating of the threads, i.e. threads between interlacing points have higher floats and are less clamped than weave types 1 and 2, which cause the highest shrinkage.
shows that multifilament PBT yarns and twisted CV/PBT yarns have almost the same influence on woven fabric shrinkage in the weft direction – fabric shrinkage is about 19%. The shrinkage of the fabrics with core CO/PBT yarn is lower for approximately 13%. These yarns have a higher number of twists, which prevents higher shrinkage when treated in boiling water. PBT yarn has been used as core, if cotton cover yarn has a high number of twists, yarn in the core cannot shrink during treatment while it is fixed between cover cotton yarns.
The interaction between PBT and Weave () is also statistically significant in the weft direction, but it is the least important, as shown by its low F-ratio value. This was to be expected, as both factors are statistically important and influence shrinkage in the weft direction. shows that woven fabrics made in weave type 3 and CV/PBT and PBT yarn have the highest shrinkage of the fabrics.
Breaking elongation of fabrics
Breaking elongation in warp direction
ANOVA table () shows that all three factors have a statistically significant influence on the breaking elongation in warp direction (BE_1). Treatment (fabrics treated in boiling water) is by far the most important of the three main factors, PBT has 15 times smaller influence than the Treatment. The Weave is the least important factor.
Table 8. Impact of Treatment, PBT (in weft) and Weave on the breaking elongation in warp direction (BE_1).
The importance of the treatment can be explained as follows: due to the thermal treatment of the samples and consequently the large shrinkage in the weft direction, the number of warp threads increases, resulting in an increase of breaking elongation in the warp direction for almost 2.5% on average for all samples (). This is less than expected, since the shrinkage of the fabrics in warp direction, was higher – on average around 3.5% (see Appendix) – than the increase of the breaking elongation of the fabrics.
Another statistically important factor is PBT. The highest breaking elongation in the warp direction was achieved with the fabrics with CO/PBT yarns in the weft. A possible explanation for this behaviour is that the shrinkage of fabrics with CO/PBT yarns is the smallest and therefore, it allows the other systems of threads to shrink more during treatment, which is reflected in a higher breaking elongation in the warp direction (). Fabrics with CV/PBT yarns in the weft achieve a slightly lower breaking elongation at break in the warp direction. CO/PBT and CV/PBT are equally important statistically. Fabrics with multifilament PBT yarns in the weft have the lowest breaking elongation. It is exactly the opposite of CO/PBT yarns, where fabrics with multifilament PBT yarns shrink the most and do not allow the other systems to shrink.
Due to the shrinkage effect, the friction between warp and weft threads increases, which is why the importance of the main factor Weave is the smallest. Weaves 1 and 3 have almost the same effect on the breaking elongation in the warp direction and achieve a higher breaking elongation than Weave 2 ().
Two interactions were found to be statistically significant, namely the interaction between Treatment and Weave (AC) () and the interaction between PBT yarn in weft and Weave (BC). Statistically, the most important factor is interaction between Treatment and Weave (AC), and interaction between PBT yarn and Weave (BC) is less important.
Breaking elongation in weft direction
When analysing the breaking elongation in the warp direction (BE_2), it was found that all three main factors are statistically significant (). As expected, the Treatment has the greatest influence on the breaking elongation. The influence of the Weave is 10 times less, and PBT has an even smaller influence on the breaking elongation in the weft direction.
Table 9. Impact of Treatment, PBT (in weft) and Weave on the breaking elongation in weft direction (BE_2).
The Treatment is again by far the most important of the three main effects due to the high shrinkage in the weft direction caused by the thermal treatment of the samples, which results in a higher breaking elongation in the weft direction compared with the untreated samples ().
The Weave also plays an important role in the shrinkage of the woven fabrics. Weave types with more floating have a higher shrinkage (Weave 3) and accordingly achieve a higher breaking elongation in the weft direction ().
The influence of PBT is also easy to explain. Fabrics with PBT multifilament yarns and twisted CV/PBT yarns shrink more than fabrics with core CO/PBT yarns (). These fabrics achieve the lowest breaking elongation because the CO/PBT yarn is heavily twisted and cannot shrink as much as the other two yarns during treatment.
There are three statistically significant two-factor interactions. The most important one is the interaction between Treatment and Weave (AC), which has the same significance as the main factor Weave. This is understandable because both factors are statistically significant and influence the shrinkage of fabrics, which is explained in ‘Shrinkage after thermal treatment’ section. A higher shrinkage also leads to a higher breaking elongation of fabrics. The results are shown in , where it is shown that for Weave 3 (which has a higher floating) the effect of thermal treatment on the breaking elongation is much stronger compared with weaves 1 and 2, where this effect is smaller and similar.
Figure 11. Interaction between Treatment and Weave (AC), analysing breaking elongation in weft direction (BE_2).
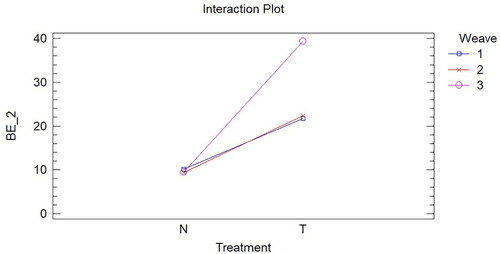
Also important are the interactions between Treatment and PBT (AB) (), which are almost as important as the main factor PBT. Statistically significant interaction PBT and Weave are the least important.
Breaking elongation before and after thermal treatment
The statistical analysis of the breaking elongation of the tested fabrics showed that the factor Treatment has a very strong influence in all cases. It was therefore decided to divide the group of fabrics from part B into two groups before treatment and after treatment. It was analysed which of the factors PBT and Weave had a statistically significant influence on the breaking elongation. The fabrics before treatment are not elastic and fabrics after treatment are elastic.
It has also been found that breaking elongation after treatment also affects fabric shrinkage and change in physical properties such as change in warp and weft density, thickness and mass per square metre. Fabrics with higher shrinkage have higher breaking elongation.
Breaking elongation in warp direction
The ANOVA table () shows that both these two factors have a statistically significant influence on the breaking elongation in the warp direction before treatment in boiling water (BE_1_N). The most influential factor is PBT (), followed by Weave (). The results were expected and are easy to explain because the PBT-incorporated yarns have a different linear density, which leads to different crimping of the yarns, which contributes to the breaking elongation of woven fabrics in warp direction. There is no evidence of statistically significant two-factor interactions.
Figure 14. Influence of Weave on the breaking elongation in warp direction before treatment (BE_1_N).
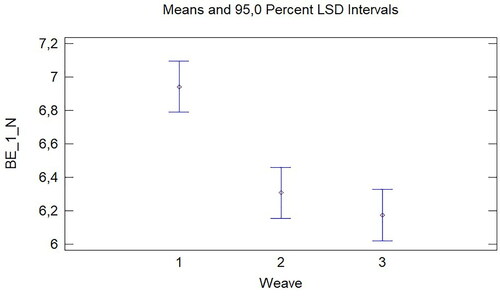
Table 10. Impact of PBT and Weave on the breaking elongation in warp direction before treatment (BE_1_N).
In the analysis of breaking elongation in the warp direction (BE_1_T) after treatment of the woven samples (), both main factors were again classified as statistically significant, and the order of importance is also the same. The most significant factor is PBT (), followed by Weave (). After treatment, the weft threads shrink, which causes the shrinkage of the warp threads. The shrinking effect and a higher crimp of the threads in the analysed direction lead to a higher breaking elongation of the warp threads.
Figure 16. Influence of Weave on the breaking elongation in warp direction after treatment (BE_1_T).
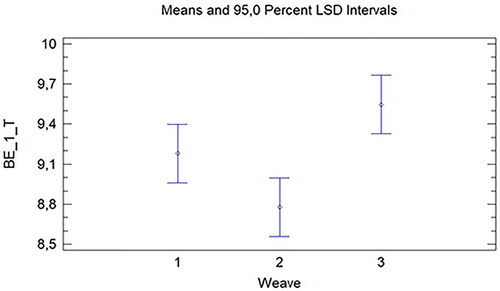
Table 11. Impact of PBT and Weave on the breaking elongation in warp direction after treatment (BE_1_T).
The interaction between PBT and Weave is also statistically significant (), but its effect is less pronounced compared with the main factors. In the treatment process, both factors cause higher shrinkage and higher crimp, thus leading to higher elongation at break.
Breaking elongation in weft direction
When examining the breaking elongation in the weft direction before the treatment, the two main factors proved to be statistically significant: PBT and fabric (). Both factors are of similar importance. The significance of PBT is understandable due to the different construction and linear density of PBT yarns, and since at breaking elongation in the warp direction it causes different crimp of yarns, which influences the breaking elongation (). The interlacing of the threads also influences the breaking elongation of non-treated samples ().
Figure 19. Influence of Weave on the breaking elongation in weft direction before treatment (BE_2_N).
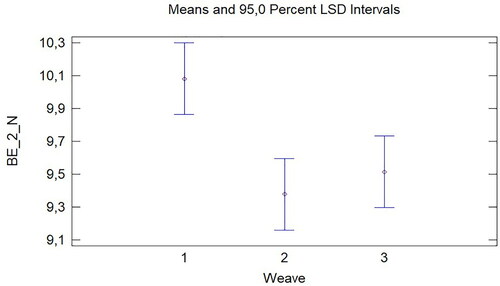
Table 12. Impact of PBT and Weave on the breaking elongation in weft direction before treatment (BE_2_N).
After thermal treatment, both of these two main factors are statistically significant (). The Weave has by far the greatest influence on the breaking elongation in the weft direction (), followed by PBT. Also statistically significant is the interaction between the factors PBT and Weave (AB), which is the result of very strong effects of PBT and Weave. The interaction is less significant compared with the main factors.
Table 13. Impact of PBT and Weave on the breaking elongation in weft direction after treatment (BE_2_T).
As can be seen in , the Weave with the largest floating of the threads (Weave 3) has the highest breaking elongation after the treatment, while weaves 1 and 2 have almost the same breaking elongation. As can also be seen in , the construction of the PBT yarns influences the breaking elongation, although only every fifth thread is a PBT yarn. Fabrics with CV/PBT and pure PBT have almost the same breaking elongation, while fabrics with CO/PBT have a lower breaking elongation. CO/PBT yarn is a more twisted yarn and cannot shrink as much as the other two yarns. The interaction between factors Weave and PBT yarns, analysing breaking elongation in weft direction after treatment is seen in .
Conclusions
The main findings of our comprehensive study — parts A, B and C — can be summarized as follows. There are no statistically significant factors when examining the shrinkage of fabrics after thermal treatment (part A) in warp direction. PBT, Weave and their interaction were found to be important for shrinkage in weft direction.
Treatment was by far the most influential factor in the study of breaking elongation of all fabrics tested (part B) in both warp and weft directions. Finally, the examination of the breaking elongation before and after thermal treatment (part C) showed that the elongation in warp direction before and after treatment was mainly influenced by PBT and Weave, respectively.
On the other hand, PBT and Weave were identified as the statistically important factors influencing breaking elongation in the weft direction before treatment, while after the treatment Weave is much more important than PBT yarn in the weft.
Before treatment the highest values of breaking elongation in warp direction have fabrics with CO/PBT yarn in weft and Weave 1. In weft direction before treatment, the highest values of breaking elongation have fabrics with CV/PBT and multifilament PBT yarn in weft and Weave 1, as in warp direction. After treatment, the highest values of breaking elongation in warp direction have fabrics which have CV/PBT and CO/PBT yarn in weft and Weave 3, while in weft direction, the highest breaking elongation values are achieved at fabrics with CV/PBT and multifilament PBT yarn in weft and Weave 3.
Disclosure statement
No potential conflict of interest was reported by the authors.
Additional information
Funding
References
- Bedez Ute, T. (2019). Analysis of mechanical and dimensional properties of the denim fabrics produced with double-core and core-spun weft yarns with different weft densities. The Journal of the Textile Institute, 110(2), 179–185. https://doi.org/https://doi.org/10.1080/00405000.2018.1470451
- Bizjak, M., Kadoğlu, H., Kostajnšek, K., Çelik, P., Başal Bayraktar, G., Duran, D., Bedez Üte, T., Ertekin, M., & Dimitrovski, K. (2017). Properties of elastic fabrics with treated and untreated Co/PBT yarns in weft direction. Proceedings of the 17th World Textile Conference AUTEX. https://doi.org/https://doi.org/10.1088/1757-899X/254/9/092001
- Bona, M. (1993). Statistical methods for textile industry (pp. 304–347). Eurotex- Textilia.
- Celik, I. H., Sarioglu, E., & Kaynak, H. K. (2018) Bursting strangth of knitted fabrics produced from od polybutylene terephtalate (PBT) yarns with different false-twist texturing parameters. Proceedings of the II. International Conference on Engineering Technology and Innovation, ICETI 2018. 7. – 11. March 2018. Budapest, Hungary, 1-5
- Chen, Q., Ma, P., Mao, H., Miao, X., & Jiang, G. (2017). The effect of knitting parameter and finishing on elastic property of PET/PBT warp knitted fabrics. Autex Research Journal, 17(4), 350–360. https://doi.org/https://doi.org/10.1515/aut-2017-0014
- Dimitrovski, K., Kostajnšek, K., Gündüz, A., Tanyely, M., Akleylek, A. (2012). Properties of cotton like woven fabrics containing different type of PBT yarns in weft. Proceedings of the 6th International Textile, Clothing & Design Conference – Magic World of Textiles 7–10.
- Grosberg, P. (1969). The tensile properties of woven fabrics. In Structural mechanics of fibres, yarns and fabrics (pp. 339–354). John Wiley&Sons.
- Hu, J. (2004). The tensile properties of woven fabrics. In Structure and mechanics of woven fabrics (pp. 91–121). Woodhead Publishing. https://doi.org/https://doi.org/10.1533/9781845690403.91
- Hu, J., Lu, J., & Zhu, Y. (2008). New developments in elastic fibers. Polymer Reviews, 48(2), 275–301. https://doi.org/https://doi.org/10.1080/15583720802020186
- Kadoğlu, H., Dimitrovski, K., Marmaralı, A., Çelik, P., Bayraktar, G. B., Üte, T. B., Ertekin, G., Demšar, A., & Kostanjek, K. (2016). Investigation of the characteristics of elasticised woven fabric by using PBT filament yarns. Autex Research Journal, 16(2), 109–117. https://doi.org/https://doi.org/10.1515/aut-2015-0025
- Pavko Čuden, A., Hladnik, A., & Sluga, F. (2013). Impact of material, structure and relaxation process parameters of elasticized single-knitted fabrics on loop length. Textile Research Journal, 83(1), 56–65. https://doi.org/https://doi.org/10.1177/0040517512447588
- Realff, M. L., Seo, M., Boyce, M. C., Schwartz, P., & Backer, S. (1991). Mechanical properties of fabric woven from yarns produced by different spinning technologies: Yarn failure as a function of gauge length. Textile Research Journal, 61(9), 517–530. https://doi.org/https://doi.org/10.1177/004051759106100904
- Senthilkumar, M., Anbumani, N., & Hayavadana, J. (2011). Elastane fabrics – A tool for stretch application in sports. Indian Journal of Fibre & Textile Research, 36(3), 300–307. http://nopr.niscair.res.in/handle/123456789/12655
- Štrukelj, D. (2012). Influence of textured polybutyleneterephtalate yarn and constructional parameters on elasticity of textile fabrics [Doctoral dissertation]. University of Ljubljana, Slovenia.
- Štrukelj, D., & Dimitrovski, K. (2012). Study of cotton woven fabrics with added polybutylene terephatalate yarns. Tekstil, 61(1–6), 18–24. https://hrcak.srce.hr/138646
- Vassiliadis, S., Kallivretaki, A., Domvoglou, D., & Provatidis, C. (2011). Mechanical analysis of woven fabrics: The state of the art. In S. Vassiliadis (Ed.), Advances in modern woven Fabrics technology (pp 41–64). InTech. https://doi.org/https://doi.org/10.5772/25255
- Verdu, P., Rego, J. M., Nieto, J., & Blanes, M. (2009). Comfort analysis of woven cotton/polyester fabrics modified with a new elastic fiber, part 1 preliminary analysis of comfort and mechanical properties. Textile Research Journal, 79(1), 14–23. https://doi.org/https://doi.org/10.1177/0040517508090888
Appendix
Table 14. Physical properties of untreated and treated samples.
Table 15. Shrinkage of fabrics in warp and weft direction after treatment.
Table 16. Elongation properties of fabrics in warp direction.
Table 17. Elongation properties of fabrics in weft direction.