Abstract
The Architecture, Engineering and Construction (AEC) industry finds itself in an accelerating shift towards the use of more digital fabrication (DFAB) technologies. DFAB promises great advantages in AEC, but its adoption is so far lagging and there are few examples of building projects employing DFAB at scale. To facilitate DFAB adoption, we need to identify its challenges and opportunities of in the project context and understand its implications beyond project boundaries. To do this, this paper conducts a single case study on DFAB HOUSE, the first project to introduce several fundamentally new DFAB technologies to construct a fully functional building. Using Qualitative Content Analysis, we provide an overview of the challenges to consider and the strategies available to successfully adopt DFAB technologies in construction projects, establishing a socio-technical framework for DFAB adoption in AEC projects. We find that full-scale projects are an effective exploration method of DFAB in AEC, implementation at scale increases acceptance of DFAB in AEC, and projects are instrumental in establishing an emergent praxis of DFAB.
Introduction
The Architecture, Engineering and Construction (AEC) industry finds itself in an accelerating shift towards the use of digital fabrication (DFAB) technologies. The adoption of DFAB promises great advantages such as improved resource efficiency and productivity, reduction of construction waste, and better worker safety (Bock Citation2015, WEF Citation2016, Agustí-Juan et al. Citation2018). Although the need for rapid innovation in AEC is widely recognised (Ribeirinho et al. Citation2020), there is still much resistance to adopting systemic innovations such as DFAB. As a result, the AEC industry “struggles with significant gaps between the available technology and the technology used in practice” (Singh and Holmstrom Citation2015).
DFAB in AEC is a domain in which technology uptake in practice proves particularly challenging. DFAB is a process where manufacturing devices are directly controlled by digital design data (Gershenfeld Citation2012), such as robotics or 3D printing. DFAB adoption depends on the integration of digital technologies with physical components (Meuer et al. Citation2019). For about two decades, building with digitally controlled tools has been explored in research, but few projects have reached full construction scale. To accelerate adoption, it is important to shorten time to market of new technologies (Richner et al. Citation2017), but this has been difficult for DFAB. This large gap between research feasibility and industry adoption suggests that limited DFAB adoption stems not from technology itself but from barriers to its integration into existing practice, business structures and processes (Chen et al. Citation2018), product architecture (Hall et al. Citation2020), and organizational structures (Pan and Pan Citation2019).
This paper seeks to understand how practitioners in AEC can overcome these challenges and capitalise on the opportunities of DFAB. Although DFAB projects remain rare, detailed research is needed on the reality of practice when DFAB technologies are implemented at scale. Here, we conduct a single-case study of the DFAB HOUSE, a seminal demonstrator project that uses a combination of six new DFAB technologies to construct a fully operational, code-compliant building, offering one of the first chances to study the integration of DFAB in the planning and delivery at 1:1 scale.
To learn from DFAB HOUSE, we examine how technology implementation on the project succeeded by addressing challenges related to technology, organisation, socio-cultural factors, knowledge, and perception. We summarize our findings in a socio-technical framework of DFAB adoption in AEC projects and discuss their implications for AEC practice.
Research background
Definition and fundamentals of DFAB in AEC
DFAB is defined as a fabrication or building process relying on a seamless conversion of design and engineering data into digital code to control manufacturing devices (Gershenfeld Citation2012). DFAB processes rely on “translation of computer generated data to physical artefact” (Dunn Citation2012). Through the direct transfer of digital design data to 1:1 assembly operations, DFAB combines design and construction into an integrated process (Willmann et al. Citation2016), leading to a continuous digital data chain from design to manufacturing (Bonnard et al. Citation2010, Helm et al. Citation2012). To achieve this, designers require information and knowledge about production parameters (Ng et al. Citation2020, Scheurer and Stehling Citation2020). This is similar to the characteristics of process and product innovation in industrial manufacturing (Nam and Tatum Citation1990; Scheurer and Stehling Citation2020).
Emerging implications of DFAB on the AEC industry
DFAB adoption is expected to widely impact AEC (WEF Citation2016, Ribeirinho et al. Citation2020) and increasingly replace conventional construction methods (Bock Citation2015). It is an essential component in the digitalisation of AEC, often referred to as Construction 4.0 (Meuer et al. Citation2019, Forcael et al. Citation2020, Muñoz-La Rivera et al. Citation2020). The term derives from the Industry 4.0 concept which describes “the digitization and integration of the entire value chain of the lifecycle of products” (Ghobakhloo Citation2020).
The potential impact of DFAB is extensive. Scholars suggest DFAB can help improve material efficiency and waste avoidance (Agustí-Juan et al. Citation2017, Citation2019, Mata-Falcón et al. Citation2019), reuse of materials (Kuzmenko et al. Citation2021), workplace health and safety (Keating et al. Citation2017, Garcia de Soto and Skibniewski Citation2020), integrative work design (Bharadwaj et al. Citation2020), and productivity (García de Soto et al. Citation2018; Fardhosseini et al. Citation2020; Hu et al. Citation2021). The implementation of DFAB will have important implications for AEC, including changes to: workforce and organisational structures, (García de Soto et al. Citation2019); integration of digital manufacturing with BIM and computational design, (Hamid et al. Citation2018); automation of construction tasks (Bock Citation2015, Fardhosseini et al. Citation2020, Chen et al. Citation2018); collaborative design and human-machine interaction (Vazquez and Jabi Citation2019); and architectural practice and education (Gramazio et al. Citation2014, Yuan et al. Citation2018).
State of the art in DFAB construction
Some DFAB processes have been used in practice (Caneparo Citation2014), and implementations at scale fall into three sub-domains (Kaseman and Graser Citation2020):
robotic processes;
additive manufacturing;
specialised digitally controlled material processing technologies.
Built examples of robotically manufactured structures include pavilions by ICD (Institute for Computational Design and Construction) at the University of Stuttgart (Menges and Knippers Citation2020b, Citation2020a). Additive construction demonstrators include on-site concrete printing, for example, housing prototypes by ICON 3D and Apis Cor (Valente et al. Citation2019); 3D printed concrete prefabrication (Xu et al. Citation2020); and metal printing, for example, a footbridge by MX3D (Gardner et al. Citation2020). Specialized technologies include robotic concrete slip-forming (Lloret-Fritschi et al. Citation2019) and digitally knit tensile formwork (Popescu et al. Citation2020).
Yet, full-scale, permanent buildings that prominently feature DFAB are still rare, and examples of implementations such as Sequential Roof at ETH Zurich (Apolinarska et al. Citation2019) and the Théâtre Vidy in Lausanne (Robeller et al. Citation2017) show that technical challenges still exist (Melenbrink et al. Citation2020, Menges and Knippers Citation2020b).
Challenges to DFAB adoption
In addition to technical challenges, there are organisational and process barriers to DFAB adoption. DFAB for construction represents a systemic innovation, crossing the boundaries of multiple research disciplines and professions (Knippers et al. Citation2021), including architects, materials scientists, roboticists, structural engineers, manufacturers and trade contractors (Wangler et al., Citation2016; Willmann et al. Citation2016). Systemic innovations require collaboration across organisational boundaries for their successful implementation, and only add their full value from within a cross-organisational innovation system that allows coordination with complementary innovations (Chesbrough & Teece, Citation2002; Taylor & Levitt, Citation2004). Complementary innovations to DFAB include computational design tools (Knippers et al. Citation2021), product configurators (Cao et al. Citation2021), and Digital Twin information systems (Grieves Citation2015, Sacks et al. Citation2020). We adhere to this definition of systemic innovation in the context of our research, acknowledging the existence of other definitions in different contexts (Midgley and Lindhult Citation2017).
Systemic innovations face great adoption challenges in AEC which suffers from fragmentation caused by competitive bidding, weak coordination between contractors, and high participant turnover between project phases (Dubois and Gadde Citation2002; Katila et al. Citation2018). Therefore, the organisational and social context can be as important for industry adoption of DFAB as technological feasibility (Nascimento et al. Citation2016, Pan and Pan Citation2019).
Research gap and research questions
To summarise, (i) DFAB has important implications for AEC, (ii) many DFAB technologies are under development, and (iii) the interdisciplinary and systemic characteristics of DFAB present barriers to its adoption in AEC.
Although much literature identifies the challenges to DFAB and other systemic innovations, little attention has been paid to the strategies developed on projects to successfully adopt DFAB. Until recently, DFAB had not yet been implemented at scale, and there were few opportunities to conduct empirical research on the topic. Thus, we focus on the following research questions:
When introducing DFAB technologies in a full-scale construction project,
How do we recognise and address challenges to, and seise opportunities of DFAB adoption in the project context?
What are the implications for DFAB adoption in AEC practice beyond project boundaries?
Case study
The case study project, DFAB HOUSE, presents an important first-time opportunity to study DFAB adoption in the context of a full-scale construction project. DFAB HOUSE is a demonstrator building by the Swiss National Centre of Competence in Research (NCCR) Digital Fabrication, one of the world-leading research centres in DFAB for AEC. DFAB HOUSE is ground-breaking in two ways: first, it is unique for employing six fundamentally new DFAB technologies to construct all substantial parts of a multistory building; second, it is the world’s first full-scale, permitted and occupied residential building constructed by means of multiple DFAB technologies. These technologies are the result of interdisciplinary research and development by the NCCR DFAB and its industry partners. The project includes research across disciplines of architecture, structural engineering, materials science, computer science, robotics and digital manufacturing. More than 40 industry partners contributed to the project, including specialist engineering firms, material and technology suppliers, and contractors (NCCR Digital Fabrication Citation2021).
The project site is NEST, a modular building platform operated by Empa, the Swiss Federal Laboratories for Materials Science and Technology. The NEST superstructure provides empty floor slabs as sites for independent construction projects (Units) aimed at accelerating market entry of new technologies, materials and building systems (Richner et al. Citation2017). DFAB HOUSE represents one such Unit, situated on the top-most floor slab of NEST ().
NEST Units are required to be fully compliant with local building codes and an additional, stricter set of performance standards prescribed by NEST. By meeting these requirements, each DFAB technology implemented in DFAB HOUSE represents a “system prototype demonstration in operational environment” as defined on Level 7 of the Technology Readiness Level (TRL) scale (European Commission Citation2019). Thus, DFAB HOUSE can be described as a multi-technology demonstrator, proving the technical feasibility of new technologies not yet adopted to practice in a realistic context in preparation for broader adoption.
DFAB HOUSE demonstrates six DFAB technologies, illustrated in . For a full description of these technologies, readers are referred to Graser et al. (Citation2020).
Figure 2. Building parts of DFAB HOUSE and associated DFAB applications: Mesh Mould (a), In Situ Fabricator (b), Smart Dynamic Casting (c), Smart Slab (d), Spatial Timber Assemblies (e), Lightweight Translucent Façade (f).
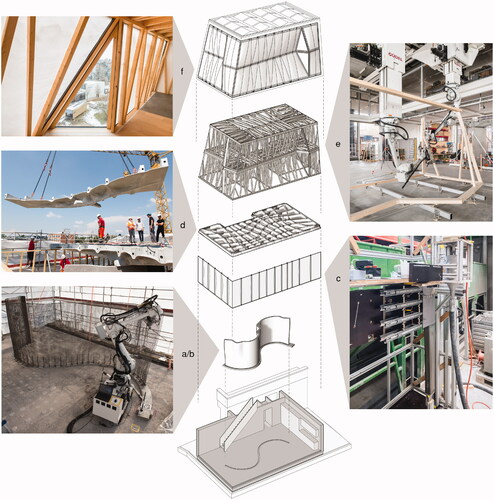
Mesh Mould () is a robotically welded rebar mesh combining the functions of stay-in-place formwork and reinforcement. It enables on-site, waste-free, structurally optimised concrete construction (Hack et al. Citation2020).
The In situ Fabricator () constitutes the world’s first on-site application of an autonomous, mobile construction robot, to fabricate the Mesh Mould rebar system (Dörfler et al. Citation2019).
Smart Dynamic Casting () is an automated system for concrete slip forming using a reusable, actuated formwork with changing cross-section, and the first system to unify reinforcement and concreting in a single robotic process (Lloret-Fritschi et al. Citation2019).
Smart Slab () is a pre-cast concrete ceiling slab fabricated with sand-based binder jet 3D printed formwork It combines design freedom with significantly reduced material volume (Aghaei-Meibodi et al. Citation2018).
Spatial Timber Assemblies () is a robotic prefabrication process for timber modules. Collaborating robot arms fabricate and assemble structurally performant, material-efficient structures (Thoma et al. Citation2019, Adel Citation2020).
Lightweight Translucent Façade () is a membrane facade with aerogel insulating filling integrated with Spatial Timber Assemblies. It combines freedom of shape with high thermal performance, daylighting and weight reduction (Graser et al. Citation2021).
Research methodology
By demonstrating multiple new DFAB technologies at full construction scale, DFAB HOUSE represents an unusually rich and complex case to study DFAB in the real-life context of a construction project. It can be considered a rare source of insight into an emerging subject that is still lacking larger, quantifiable datasets (Yin Citation2014). Therefore, this research uses a single case study approach as “an opportunity to describe the process by which a complex phenomenon unfolds” (Taylor et al. Citation2011).
Data collection
Primary data were collected through a total of 37 semi-structured interviews with project participants, Participant questions included information about background experiences, roles and responsibilities, work processes, and project experience. 36 interviews were recorded (total time 30.5 hours) and notes were taken on all interviews. The sample includes 17 technology researchers (e.g., principal investigators (PIs), PhD and postdoctoral researchers, scientific assistants), 11 industry partners (e.g., managers, engineering and construction specialists and executing site personnel), and 9 other participants (e.g., planners, technicians, client’s representatives, and R&D managers). Interviewees were selected based on the authors’ knowledge of the project, following the principle of purposeful sampling which aims to “obtain cases deemed information-rich for the purposes of study” (Sandelowski Citation2000). Interviewee selection was guided by their active role in the development and application of DFAB or in decision-making on the project. Data were collected until theoretical saturation was reached (Strauss and Corbin Citation1990).
The first author was himself involved in the project management of DFAB HOUSE. First-hand knowledge of the project was an important asset for this research as the project organization was dynamic, decentralized and characterized by informal collaboration. These factors would have made access difficult to researchers without prior knowledge of the project. A trade-off to this access is a greater risk that personal biases can affect the research process (Dainty Citation2008). To mitigate this risk, the two co-authors were kept external to the project to provide an outsider perspective (Gioia et al. Citation2013) and to challenge the first author towards increased reflexivity regarding research design and data analysis.
Data analysis
This research uses Qualitative Content Analysis, a method of qualitative data analysis deemed appropriate for examining a nascent field (Mayring Citation2014, Kuckartz Citation2019). The focus of the method is on developing a category system to describe and explicate qualitative data from a research-led perspective (Eisenhardt Citation1989; Kuckartz Citation2019). There are two main variants: deductive, i.e., driven by pre-existing literature or theory; or inductive, i.e., derived from the content of the data itself. For this study we chose the specific technique of Inductive Category Development, a summarising approach deriving categories from the entire collected data. The aim is understanding “without bias owing to the preconceptions of the researcher” (Mayring Citation2014). This approach is similar to the “open coding” process in Grounded Theory (Strauss and Corbin Citation1990) but relies less on interpretative transformation and theory-building, allowing researchers to “stay closer to their data” (Sandelowski Citation2000). This makes it a more suitable methodology for case research conducted with prior knowledge of the object of study. The text analysis software MAXQDA was used to perform the analysis.
In a second step, we performed a Strengths – Weaknesses – Opportunities – Threats (SWOT) analysis (Helms and Nixon Citation2010) of each of the main categories that resulted from Qualitative Content Analysis. SWOT analysis is recognised as one of the most extensively used techniques of strategic planning (Glaister and Richard Falshaw Citation1999). Using SWOT analysis, we develop an early perspective on the strengths and weaknesses and the future opportunities and threats of the DFAB adoption strategies found in the case data.
Data validation
To meet the burden of proof in case study research, this study uses five strategies to achieve validation (Taylor et al. Citation2011, Yin Citation2014). First, good practice in qualitative research requires employing multiple data sources for triangulation (Cho and Lee Citation2014). Therefore, project protocols covering research, coordination and client meetings, permit submissions and yearly scientific reports were reviewed. Using data produced at different project stages helped control for various types of biases in the interviews, for example, hindsight and social desirability bias. Second, the author team was chosen up-front with different disciplinary backgrounds and affiliations to include a plurality of views and limit social determinants such as groupthink and conformity pressures. Third, the three authors conducted a coder conference to control for inter-coder reliability. Three interviews were first coded independently by each of the authors using the first author’s proposed code system, allowing each to make amendments, take notes privately and report their initial stance at the beginning of the conference. This was followed up by an open discussion with focus on logical, unanimous resolution of disagreements regarding the categories and the coding. This strategy served to enhance internal consistency and the accuracy of the code system. Fourth, the findings were discussed with a group of interviewees for communicative validation to control for construct validity. Fifth, we included direct case data quotes to validate the constructs described in the findings, thus “letting the data speak for itself” (Taylor et al. Citation2011).
The authors used these strategies to proactively and consciously control for biases in the analysis. Nevertheless, we acknowledge that some biases likely still exist in the qualitative, single-case research approach taken in this study.
Research findings
Challenges and strategies of DFAB adoption
From the analysis, five Main Challenges emerged with respect to the implementation of DFAB, each related to a different Focus Area. Corresponding to these Main Challenges, we identified five Focal Strategies subsuming the individual actions reported by the project participants to address these challenges (). For each Main Challenge, we then identified a set of individual practices, or courses-of-action, pursued by the actors in the project organisation to facilitate DFAB adoption.
Table 1. Main Challenges, Focus Areas and Focal Strategies for DFAB adoption on projects.
Synopsis of findings
The following synopsis presents the results of the Qualitative Content Analysis for each of the five Main Challenges, Focus Areas, and Focal Strategies identified, followed by a SWOT analysis of each Focal Strategy, referencing the results detailed in the descriptive analysis ().
Table 2A. SWOT analysis of co-developing DFAB processes and production systems.
Table 2B. SWOT analysis of integrating project management and organisation for DFAB adoption.
Table 2C. SWOT analysis of merging social and cultural perspectives for DFAB adoption.
Table 2D. SWOT analysis of generating and capturing knowledge from a collaborative experimental DFAB project.
Table 2E. SWOT analysis of understanding and leveraging the project’s impact on DFAB adoption outside project boundaries.
A Co-developing processes and production systems
Main Challenge A, How to develop new processes and production systems with emerging DFAB technologies, was addressed by four practices.
A.1 Pooling expertise for co-development
An important step at the outset was pooling expertise from both research and practice to assemble teams of experts. Research teams formed across groups with complementary expertise (e.g., robotics, structural engineering and material science). Industry experts and trained technicians were directly included in R&D activities, and executing contractors participated as future users of the technologies, contributing their expertise in determining how best to apply a technology. One firm’s CTO remarked, “That's the crucial difference with this project, that we actively pursued solutions together with the research groups and the project management.”
Researchers and industry alike emphasised the value of building an early understanding of the different fields of expertise required for “looking into all the complexity that one technological development needs”, albeit an incomplete awareness of needs could make the ex-ante forming of consortia challenging.
A.2 Integrating digital processes and workflows
Project implementation required making stand-alone DFAB technologies part of a production system integrated across scales and functions. For example, Mesh Mould required the development of a new robotic end-effector, its integration with the mobile robotic base, and an optimized repositioning sequence.
Integrating digital information from design to production was central to the project. Especially important was the upstream integration of production parameters (e.g., the limitations of robot reach or the angle constraint of a saw blade). Data integration offered synergies, such as embedding analysis and fabrication data in one model, automating fabrication data generation, and streaming back sensor data to an as-built digital model. Limitations were also reported. Digital workflow integration lagged behind the technically feasible. For example, a structural analysis workflow proposed by researchers to provide immediate feedback on design iterations proved unfeasible as it lacked interoperability with a contracting engineer's established tools. Additionally, a lack of maturity in process automation led to time-consuming iterations and “fiddling”. Researchers viewed these drawbacks as challenges to integrating DFAB in future construction processes.
The integration of digital and manual tasks was essential for the project. No DFAB process was fully automated. The need for a better understanding of collaborative processes with digital machinery was frequently highlighted. A contractor said DFAB required a new type of “digital construction worker” with “knowledge in computing and robotics and practical knowledge of doing the work onsite”, a skillset that will likely continue to be hard to find in the workforce.
A.3 Scale-up and prototyping
To achieve scale-up from laboratory experiments to viable full-scale construction, all core teams included researchers from additional disciplines and professional experts. One planner called this the moment “when an engineering approach entered the research.” Physical prototyping was used for the concurrent development of the emergent technologies, design and implementation processes. It allowed for learning about relevant parameters in advance of full-scale implementation, for example, structural safety, the true cost of the system, and full-scale assembly challenges. Multiple prototypes enabled improvements through trial and error, a time-consuming process sometimes requiring fundamental changes. Unexpected problems - making things “more complicated than you think” – frequently occurred, but raised the R&D teams’ awareness of important factors originally not considered. Industry professionals embedded in the teams raised constructability concerns and brought in practical experience researchers were lacking.
A.4 1:1 implementation of DFAB
The stated project goal was implementing DFAB with construction grade quality and full functionality in “a building beyond one research project or specific design task.”
Researchers were challenged by tight delivery schedules and the sheer “scale and volume of production.” The project was more complex than anticipated and required more resources and suppliers. One research leader said: “What I really learned was how complicated it was to make a very simple, flexible formwork. That the system has many more constraints than I had ever imagined.”
Many saw rewards, too: Dealing hands-on with site conditions and external constraints, researchers “gained insights you wouldn't have had without the 1:1 project.” Likewise, industry partners emphasised the relevance of “being close to the process” and learn about practical and legal challenges. A technician underscored, when building in 1:1 “you see what's possible, what's not.”
Making the researchers’ ideas comply with building code and safety approvals proved challenging. As a PM observed, approvals were “not part of DFAB thinking” yet. For example, DFAB technology enabled design changes up to the last minute, while administrative approval timelines forced earlier design freezes. Successful permitting lent the technologies legitimacy, but researchers found some constraints currently imposed by codes misaligned with the potential of DFAB.
B. Integrating project management and organisation
Four practices addressed Main Challenge B, How to manage and organise the adoption of new DFAB methods.
B.1 Bottom-up organizing
Self-organising was crucial in implementing multiple new DFAB processes in parallel. Researchers described the project organization as a dynamic process in which they were “not being assigned a task but more organically developing the project together.” Because DFAB implementation required role flexibility, bottom-up organizing enabled new roles to emerge in response to specific needs. For example, one research assistant described his role as “jack of all trades, master of none”, filling responsibility gaps emerging as DFAB processes developed, such as wiring and trial runs of one-off robotic tools.
Network-like, horizontal decision-making strongly relied on regular personal exchange. Communication between disciplines was “less formal exchange and more intermingling”. Informal “coffee meetings” were instrumental between roboticists, structural engineers, and material scientists. Bottom-up organizing led to unclear boundaries of responsibility and redundant developments. However, industry partners and the client recognized the need “to let [researchers] use their imagination and explore” to fully understand the possibilities of DFAB.
B.2 Managing modularity and interfaces
In addition to bottom-up organising, an element of top-down control balanced self-directed exploration with the realities of project delivery. The research-led development was important, a contractor remarked, but “if you would have let them do this indefinitely, there still wouldn’t be a finished building.” To mitigate this required both modularity and integration in the project organisation.
Modularity was necessary to allow independent technical development of the DFAB applications, each of which was developed within a separate, self-managed and highly integrated organizational module. This kept complexities and uncertainties of DFAB development away from the interfaces. One PI likened this to software development; operative project management was separated from technology development and focussed on integration, relieving researchers of the “managerial side” of the project.
Nonetheless, coordinating the interdependencies between multiple parallel DFAB developments was challenging. A CEO said, “it was essential to look at the interfaces in a seamless way without sharp lines saying ‘This is where my responsibility ends’.” Well-coordinated interfaces at module boundaries enabled the integration between the different DFAB applications. “You are just a part of the project, you are not alone ... Everyone depends on the others.” Thus, project organisation depended on actors with a “bridge function” who had the breadth of skills and experience to manage information exchange across module interfaces.
B.3 Integration of project delivery
Organising the successful delivery of DFAB at the project scale hinged on the integration of actors, most importantly through early stakeholder involvement and co-location.
Early involvement of stakeholders was considered crucial to DFAB implementation by researchers, contractors and the client. The development team for each DFAB application included the main trade (e.g., concrete or timber) contractors in the earliest conceptual project stages, along with essential engineering specialists, and involved every party to the final project in hands-on prototyping. Notably, this included construction crews to contribute their ideas about feasibility and gain experience for final execution. A site foreman said, “you could really develop [the DFAB process] together”, a stark contrast to their usual experience.
Co-location supported short communication paths and direct interaction with DFAB tools. Most of the project team was “sitting together as a bigger body of knowledge”. Industry partners were present on a regular schedule, allowing for “constant interaction” during development, prototyping and fabrication. This allowed decision makers in planning, research and industry to not just “judge things from their office” but to be physically close to the production process and better understand how to make improvements.
B.4 Communicating DFAB workflows
Finding communication strategies for DFAB processes was challenging in three ways: communicating a design in flux typical for DFAB; the complexities and interdependencies inherent in DFAB workflows; and the potentials and limitations of novel DFAB technologies. Some potential of DFAB was “left by the wayside” for lack of a communication strategy; to contractors, the difficulty to communicate the requirements and rules of DFAB between stakeholders is a likely hurdle to its future commercial adoption.
Accordingly, actors tried to find more intuitive ways of communicating. Tangible techniques such as virtual reality and model-scale rapid prototyping were used alongside ad-hoc methods such as sharing digital 3D models on-screen, exchanging sketches and screen captures, and live DFAB observations. Participants noted that DFAB practice would benefit from more intuitive ways to simulate, visualise and interact with DFAB processes, e.g., augmented reality applications or model-based collaboration tools. Such options would decrease dependency on in-person interaction, ensuring inadequate communication will not cancel out the efficiency gains DFAB promises.
C. Social and cultural factors
Main Challenge C is mitigating and leveraging the social and cultural diversity of a project for DFAB adoption. Three practices addressed this.
C.1 Developing a common language
Advancing the nascent field of DFAB, a researcher observed, “only makes sense in an interdisciplinary manner.” This required cooperation of a broad diversity of actors, but “the biggest challenge was just how to be able to understand each other in a way that would promote the success of the project.”
The initial lack of a common terminology was an obstacle: “You come in, you misunderstand each other.” This was seen as a threat to future DFAB implementation. However, the two-year project timeframe and the repeated interactions it required were a good precondition for developing a common language.
A researcher described this process as follows.
“Because I do not have the background, the information that [another team member] gives out doesn't stick. Then it takes…going back to the same points again and again. Then these things start to stick. You start to learn the language. All of a sudden you can start to connect it to your background…That's where the innovation starts.”
Misunderstandings were a common issue between researchers and practitioners. When groups used the same term to talk about different things (e.g., “ribs” as structural elements vs. surface articulation), it led to confusion, errors and rework. When construction professionals were working with researchers, “what's crystal clear, or not worth mentioning to one person is 'never heard of' to another.” However, actors with prior interdisciplinary work experience felt better equipped to avoid such misunderstandings.
C.2 Pushing disciplinary boundaries
DFAB depends on interactions across discipline boundaries, ensuing the transfer of expertise to and from others outside one’s own discipline. This pushing of disciplinary boundaries was considered one of the central opportunities of the project, as it resulted in new solutions no one would have thought of individually. For example, roboticists getting their technology “into the hands of people that are not ... familiar with the way we think” received back new ideas about “how you can use and what you can do with it.”
Researchers said DFAB helped break open ensconced thought silos in academia. They learned to “understand the other disciplines’ point of view”, even between traditionally distant research fields. “Structural engineers and material scientists are in the same departments, but they don't work together, and I think DFAB has changed that.” A structural engineer experienced an “enormous widening of the horizon” towards knowledge of materials, robotics and computer science. In addition, DFAB HOUSE taught them socio-technical aspects: “What are the roadblocks on the way to deployment of technology? The social and human aspects ... This is something that, as engineers, we're absolutely not trained to think about.”
The cross-over extended to the traditional divide between research and professional cultures as well. Researchers and contractors challenged each other “to find out how far they can deviate from their usual ways” in establishing new shared practices. Practitioners learned “what possibilities already exist” and to accept the risk of failure. Researchers learned about pragmatic industry needs, market focus and external constraints.
As a result, participants started identifying as experts in the emerging field of DFAB. “You understand the importance of those collaborative settings when you cannot any longer get back into a research field where that doesn't happen.” At the time of project completion, one of them said, “I have about three and half years in this. Considering how young the field is, it kind of made me an expert by default.”
The pushing of disciplinary boundaries has significance beyond the individual: participants saw in DFAB HOUSE a case-study of a new work environment and “digital culture” firms will need once DFAB technologies enter the market. A CEO said “It is important for a firm to ... take part in this expansion of the horizon, “and to “crack open the resistance to change” prevailing in the workforce.
C.3 Building networks and relationships
Networks and relationships across research, industry and the client organisation enabled DFAB implementation in three ways.
First, connections between researchers were important. DFAB research caused groups to establish new connections with other disciplines, and build new personal relationships. A coordinating researcher stated, “I got new skills, but still I [now] know people that are much more talented in these skills.”
Second, connections between research and industry partners were a major value proposition of the DFAB HOUSE project. On the research side, a technology transfer manager said, “DFAB HOUSE is the NCCR project that has produced the most industry partnerships.” An engineering PI called DFAB HOUSE a “door opener” for industry involvement: DFAB had “changed the scale” by attracting the interest of global industry leaders who were looking for insights into new technologies.
Third, DFAB HOUSE created a new network for industry partners around DFAB both inside the firm and with external complementors and clients. A CTO said DFAB HOUSE R&D moved them from “outsider” to “insider” in an expert network around digital capabilities: it helped them know who to ask about digital topics, get help on other projects, and validate potential new hires. In addition to direct partnerships, the project created a new ecosystem of likeminded partners.
However, building and maintaining partnerships requires effort and resources. In early project phases, NCCR management and research groups organised firm visits, research presentations and networking events to find partners. Still, a successful partnership took two years to ramp-up, requiring constant attention to balancing mutual interests. In one case, losing an industry partner led to resource problems and increased workload for researchers. Partnerships helped the project succeed and become “a binding object that creates a community around it.” Going forward, a researcher stated, the project network was a good basis for “knowing who to make the next steps with.”
D. Generating and capturing knowledge
Four practices responded to Main Challenge 4, how to capture knowledge in a collaborative experimental DFAB project.
D.1 Knowledge sharing and generating collective knowledge
Direct, interpersonal information exchange was clearly identified as the main source of learning on the project, followed by observing the other disciplines’ approaches. Participants continuously learned throughout the project, making it what an industry partner called a “new learning territory.”
Two ways of knowledge trading dominated the project. First, sharing knowledge formerly residing just with one individual or group, leading to a broader common knowledge base. In a team of experts with disparate backgrounds each could broaden their knowledge. An engineer remarked, “those who needed to learn from me were exactly the people I needed information from.” For example, roboticists learned about construction while an architecture researcher acquired robotics skills, and both learned understand the material science behind their processes. Industry experts helped researchers better understand important external constraints. The experts, in turn, gained insights into new technologies.
Second, generating collective new knowledge by learning together on the job, yielding a new transdisciplinary body of knowledge specific to DFAB. Establishing meaningful collaborations with experts from other fields took time, a team leader said. However, “eventually we built up this collective knowledge [to] tackle a very specific challenge, which is beyond your discipline, and beyond their discipline, but you can solve it together.” A researcher said Mesh Mould exemplified this process: “It's not my work, it's really a work that has been created through the knowledge of many.” In turn, results could only be achieved in an environment where such complex and heterogeneous knowledge inputs were available.
D.2 Conducting the project as experiment
Rather than a mere demonstration of previous research results, DFAB HOUSE constituted a collective experiment and thus a source of new evidence, ideas and research questions. A researcher called this “empirical research on a 1:1 scale.” Our findings support this statement in four ways.
First, research had to address “a lot of other challenges that are not necessarily responding to your objective” (e.g., structural engineering, facade planning, and approvals) and integrate industry in the inquiry, along with its different priorities and skills. The research became contextualised, addressing cross-topics “isolated research” could not explore.
Second, the project expanded the scope of DFAB research to include questions of integration into practice. A researcher said, “It's integration of all these layers, all the complexity that make one building happen, the economy, the approval, all that.” This required learning how to do collaborative research on a project scale, a task a project manager suggested “should have been a research project on its own”. A PI said this could broaden the definition of DFAB research, emphasizing “higher scale thinking ... in a context where it's not just a pure technical challenge.” However, a scientific methodology for project-scale research in AEC was lacking.
Third, going from research lab to construction yielded different and broader datasets because of scale and the need to consider more variables. A robotics researcher said, “in a prototype, we wouldn't have had many of the findings.” In addition, long-term data collection after completion (e.g., by built-in sensors) allows continued analysis of structural behaviour over the building lifecycle.
Fourth, full-scale implementation helped find limitations of DFAB and identify opportunities for its further development. A researcher called DFAB HOUSE “a huge enabler for really finding out where the problems are in the systems under development.” For example, understanding the material science of early concrete hydration was “a completely new problem in the industry.”
D.3 Substantiating scientific output
The primary outlet for research results from the project were scientific publications. Collaborative, interdisciplinary papers focussed on the broader DFAB applications. In-depth technical papers on specific components (e.g., a robotic end-effector or feedback system) were published in discipline-specific journals and conferences. In sum, “every researcher wrote one or two papers on this collaborative effort with the focus on very specific topics.” Researchers emphasised the project’s importance in producing high-profile academic publications.
However, relying on technical publications had limitations. It mostly captured outcomes deemed scientifically relevant in the separate technical disciplines, leaving other important project learnings undocumented. Some results could be crucial for construction but dispensable for scientific output. While implementation knowledge is essential for advancing DFAB, a PI said, it may not get researchers “the scientific recognition that will boost [their] academic career.”
In addition, proper quantification of outcomes proved challenging. A researcher said field data from a single project-specific application was not meaningful for measuring DFAB performance, for example, on material efficiency. Thus, data output differed from quantitative results expected in the various disciplines. Researchers highlighted a need to rethink established metrics to avoid losing critical knowledge outputs in an interdisciplinary research domain such as DFAB.
Likewise, industry partners could not quantify most effects of their DFAB R&D investments on firm performance. While a CEO said, “that is not a reason not to do it,” a continued lack of such evidence would likely deter higher management of firms from investing in DFAB.
D.4 Managing and preserving implicit knowledge
Managing and preserving knowledge not captured in science publications was recognized as a significant issue, in order “to not forget what we all have learned, and to somehow make it accessible to others.” Passing on such implicit know-how in transient, interdisciplinary teams was a new challenge researchers faced: “We don't have special protocols. We probably should.” Despite this, three strategies prevailed.
First, archiving software and machine code as “algorithmic know-how” was a knowledge preservation strategy considered highly important for DFAB. Making existing code available for new projects required documentation protocols and use instructions not yet fully established in many research groups. This was also considered a potential barrier to establishing complex DFAB in industry.
Second, research groups tried to produce internal project reports to bundle the “sticky”, localised practical knowledge single group members had won when implementing DFAB. Although such documentation was an opportunity for retrospective learning, it was challenging to divert time and resources away from new research projects.
Third, understanding and sharing non-technical experience values required a more in-depth “discussion of projects.” A PI realized: “I think what we're lacking is a proper debriefing." Some industry partners, on the other hand, conducted debriefings to share experience and report challenges and chances resulting from the project, both internally and with the client.
E. Leveraging impact
The case data show three practices responding to Main Challenge E, how to understand and exploit the impact of the project on DFAB adoption beyond its organizational boundaries.
E.1 Delivering proof of concept
Proving the technical feasibility at scale was credited with increasing acceptance of DFAB as a viable option to further explore in AEC in four ways.
First, researchers found their own initial doubts dispelled about whether DFAB could be translated to real applications, because “the project simply showed that you can very well master such big challenges.” Within the research community, a PI said “it gave us credibility to show that our research can be applied on a scale that was never done before.”
Second, DFAB HOUSE secured essential industry buy-in. “Showing that you can reach real, commercially usable results” convinced multiple companies to move forward with partnerships aimed at developing market-ready technologies. The maturity DFAB had reached on the project reduced the remaining distance to market and helped industry acceptance. A PI said, “it contributes to…an increased belief that digital transformation will take place in construction.”
Third, contractors used the project to signal their digital capabilities to clients. When showing clients “we've actually built this building using this technology, they're going to believe you that you can actually deliver things later on as well.” A client’s representative confirmed: “In AEC you need physical reality to demonstrate it's feasible. Without this end achievement it's not trusted and won't be accepted in the market.”
Fourth, stakeholders outside AEC needed convincing. A leading researcher said a demonstration like DFAB HOUSE was necessary, as “many decision-makers in politics, press, general public, universities etc. only then start to see and believe,” as do building authorities and regulators. For these audiences a “hands-on”, “real” and “tangible” experience was important. With this, the client emphasised, “we can prove it is possible. We can do things differently.” Despite such initial proof, many open questions regarding DFAB implementation beyond the demonstrator, and how to commercialise, remained unanswered. Still, a leading investigator said, “when you look back in 20 years, you will see that this has led to [innovation].”
E.2 Expanding capabilities enabling DFAB
DFAB HOUSE presented an opportunity to researchers and firms alike to build new capabilities persisting beyond project completion.
Research teams developed new, re-deployable methods and systems for the project, along with the expertise to use them. For example, the effort to implement a fully functional version of the on-site robotic fabrication system was contingent on DFAB HOUSE. The project also allowed the research institution to expand its technology capabilities by adding functionality to the Robotic Fabrication Lab (e.g., an automated tool changer and developing reusable core algorithms).
Several formalised industry collaborations sprung from DFAB HOUSE. A researcher observed that “ramping up” the technology for DFAB HOUSE helped “bring it to a stage where now industry wants it.” Follow-on industry collaborations are targeting product development as well as joint building of IP and filing patents. For example, two spin-outs were formed with leading industry partners, aiming specifically at market implementation of the demonstrated DFAB technologies.
Partnering firms used the project as a vehicle to extend capabilities as well: they rapidly developed processes enabling or complementing DFAB applications, invested in DFAB equipment and hired new know-how. New processes such as 3D printed formwork or post-tensioning (a high-performance reinforcement method) in curved concrete elements were fundamentally new solutions that are now available to clients. One contractor used process knowledge from DFAB HOUSE to implement an automated 3D planning tool for standard products. Equipment investments triggered by DFAB HOUSE included an automated concrete batching system (enabling DFAB applications), advanced software, and an industrial robot retrofitted for DFAB tasks. One firm reported hiring full-time digital planning and DFAB specialists as a direct project outcome.
However, firms were aware of the risk that these investments could not be fully utilised in day-to-day operations after project completion and therefore favoured incremental capability-building. Nevertheless, they saw even small investments as a substantial increase in readiness to adopt DFAB innovation. A CEO called them the “missing puzzle piece” necessary for taking on “new chances and changes” complementary to their core business.
E.3 Increasing visibility of DFAB
As a first-of-its-kind demonstrator of DFAB in construction, the project aimed at increasing visibility of DFAB to a variety of audiences. The project was disseminated through many channels, both during construction and after completion. Formats included live tours on site, the project website, a dedicated video channel, social media, as well as press, radio and TV coverage. As a result, a leading researcher said, DFAB HOUSE “is clearly…already seen as a major realisation in the field [and] an icon of DFAB integration.”
However, this communication required significant resources from research institutions, industry partners and the client. Addressing a varied audience, the project’s message could not be tailored just to one group’s expectations and values (e.g., automation, sustainability, architectural design). Rather, it needed to strike a balance and thereby expose itself to critical reception. In addition, publicising the construction process bore the risk of exposing failures or shortfalls for research and industry alike.
Many researchers found value in the extended visibility of their research. It “increased the chance of technology transfer” and helped attract research funding. For the NCCR as a young research centre, building DFAB HOUSE “was a very good move, because building something ... generates a huge amount of interest in the AEC world.” This lighthouse effect created an international following. In addition, a technology transfer officer said, it generated “a completely different perception” of DFAB research in the AEC industry which now could “see what's already possible today.”
Industry partners welcomed the project’s high visibility. A manager said, “externally, on the market, it's a brilliant statement: the firm helps develop and test something new…That's a strong, very effective signal.” However, effects on new work acquisition were not yet measurable. Internally, firms could signal their innovative mindset to their own workforce: “The whole firm noticed that we were part of an innovative project ... and thinking seriously about the future,” a much needed chance to tell employees “be more open!” A field worker confirmed: He felt proud of his contribution, and had lost common reservations towards working with DFAB.
The architectural scale of DFAB HOUSE was credited with appealing to the general public more than a merely technology-focussed demonstrator. This public perception bore risks, too: For example, concerns about the negative effects of automation on employment and workplace quality needed to be addressed carefully “in the research arena, but also within the society in Switzerland.” In fact, a lead investigator said, DFAB HOUSE triggered a “cultural discourse on the digital in architecture” that could prove essential for increasing societal acceptance and trust needed to support the ongoing digitalisation effort.
Socio-technical framework of DFAB adoption
The strategies and practices identified above are diverse and could be taken as individual lessons; however, they are unified in a twofold manner: First, all of them are ways to overcome challenges to DFAB adoption in AEC. Second, they could not have been learned without implementing a full-scale demonstrator of DFAB. Through further analysis of how these strategies and practices relate to each other, we can develop an early a socio-technical perspective of DFAB adoption in the project context.
The Focal Strategies of DFAB adoption can be divided into two interrelated spheres we label the Project-internal environment of DFAB adoption and the Project-external environment of DFAB adoption. The former, internal environment relates primarily to the ability to successfully adopt DFAB within project boundaries. Main Challenges A and B fall into this sphere, because actions responding to them primarily have consequences for DFAB adoption within the project itself. The Focal Strategies A and B and their Practices, consequently, are geared towards enabling DFAB implementation within the project scope.
The latter, external environment relates mainly to the effects the project has on DFAB adoption beyond its boundaries. Main Challenges D and E belong in this environment, as action taken in response to these challenges has consequences for DFAB adoption in the project’s surrounding environment (e.g., academic research, AEC industry and potential clients) and beyond the project organisation’s limited lifespan (e.g., follow-on projects and long-term investments). Accordingly, Focal Strategies D and E, with their associated Practices, have effects exterior to the project.
These two spheres are connected by a third we name the Socio-cultural setting of the DFAB project. Main Challenge C, taking a central role by its relevance to both the internal and external environments, belongs into this setting. Focal Strategy C and its Practices, by making a meaningful multi-sided exchange possible in the transdisciplinary project collective, are informed by the Practices in the internal and external environment. In turn, they represent the socio-cultural tissue that enables all these Practices. By recognising the central role of the socio-cultural setting of the DFAB project, we arrive at a full conceptualisation of the project as a socio-technical system.
Based on this reasoning, we lay out the findings in a comprehensive socio-technical framework of DFAB adoption in AEC projects. This framework conceptualises the relationships and mutual influences between the Focal Strategies, and practices, of DFAB adoption.
Discussion
At the outset of this case study, we asked two questions. First, how do we recognise and address challenges to, and seize opportunities of DFAB adoption in the project context? And second, what are the implications for DFAB adoption in AEC practice beyond the project boundaries?
In the case data, we found various specific challenges and opportunities of DFAB uptake, and a set of corresponding strategies and practices used on the project. We subsumed these findings in a conceptual framework, offering a template for areas of relevance to the adoption of DFAB in future AEC projects.
In the following section, we take a holistic view of these findings and their relevance. As we do so, three overarching implications stand out:
Full-scale projects are an effective exploration method of DFAB in AEC
Implementation at scale increases acceptance of DFAB in AEC.
Projects are instrumental in establishing an emergent practice of DFAB.
Full-scale projects are an effective exploration method of DFAB in AEC
The case of DFAB HOUSE shows that a building-scale demonstrator project of DFAB in AEC, rather than a mere validation of prior knowledge, constitutes an effective format of exploration. Therefore we suggest that DFAB HOUSE, rather than just a demonstrator, is more aptly defined as an exploratory project (Lenfle et al. Citation2019) for two reasons.
First, the project informs DFAB on the level of applicability at scale. It is a first-time introduction of DFAB construction technologies to their relevant context. It thus offers a first chance to test each technology against constraints and influences that are external to its technical core but nevertheless critically important to its successful implementation. These external constraints relate to the robustness of processes at scale, production time and cost, integration with established technology, logistics, and codes and regulations, among other factors. Thus, full-scale project implementation opens up an application-centred perspective rather than a fundamental research perspective of DFAB, acting as an instrument for technical integration. AEC projects as a rule span organisational boundaries (Katila et al. Citation2018). The exploratory project provides one organisational unit in which multiple parties in industry and academia can co-develop new DFAB solutions. Therefore, it is uniquely suited to enable systemic innovation activity in an industry defined by inter-organisational projects, where R&D internal to one firm or organisation cannot cover the scope of change required to implement DFAB technologies.
Second, the project informs DFAB on the level of socio-technical interaction. The full-scale DFAB project represents a first-time engagement of each new technology with the full set of project collaborators present on AEC projects. It introduces precisely those stakeholders in its planning and implementation who are not typically involved in technology development but will be instrumental in future applications of DFAB. By facilitating the mutual exposure of technology researchers, industry practitioners and decision-makers, the exploratory project provides a common framework for a diversity of stakeholders and perspectives usually not present in either practice or academia. This is a unique value proposition of using a project for exploration. It opens up a new perspective on DFAB which addresses the needs of the prospective users (Slaughter Citation1993) and the practice environment (Hartmann and Trappey Citation2020), rather than the stand-alone technology only. Because it brings together a transdisciplinary constellation of actors, the organisational context of a full-scale DFAB project raises socio-technical challenges that do not emerge when research stays confined to a laboratory setting.
Exploration, by definition, aims at new knowledge. The exploratory project generated new technical and socio-technical knowledge in the act of DFAB implementation. This new knowledge, embodied in the practices we identified in the framework, is produced and shared between the participating disciplines and organisations. In their unique ability to integrate complex knowledge (Lindgren et al. Citation2018), projects allow exploration that can make a significant contribution to an emerging body of knowledge specific to DFAB in AEC.
Implementation at scale increases acceptance of DFAB in AEC
The case data show that project implementation increases acceptance of DFAB as a viable part of AEC practice. DFAB adoption relies on acceptance both inside and outside the project organisation.
Inside the project organisation, acceptance of DFAB grew on the part of participating firms, research groups, and the client organisation. This acceptance is grounded in the immediate project experience, and can be tied to multiple identified adoption practices across all the Focal Strategies. For example, co-development of DFAB processes lead to a positive identification with the results across a wider range of participants; early integration of management and execution secured buy-in for DFAB by both these realms; reaching across disciplinary boundaries allowed new vantage points to see past discipline-specific perceptions of barriers to using DFAB; establishing relationships across complementing areas of expertise expanded the notion of feasibility; joint knowledge enabled this feasibility; and achieving proof of concept extended the participants’ trust in their own abilities to use DFAB.
One of the most significant effects of this inside acceptance is the ability of firms to build social support for DFAB adoption from within. Adoption of new technologies depends on its acceptance and perceived usefulness (Davis Citation1985). The case data show how through the project DFAB acceptance in firms expanded from the initiating individuals or small groups to a broader basis spanning from key strategic management to field workers. We argue that through a mechanism like this, DFAB exploration can become part of the firm culture. Through direct engagement in an exploratory project, this mindset can be communicated to the entire workforce, convince sceptics, and encourage exploration. By creating a culture around digital capabilities and learning, firms can acquire contextual ambidexterity, i.e., the ability to explore in parallel with their exploitative core business activities on many levels within the workforce (Birkinshaw and Gibson Citation2004). However, most adoption processes by users in the industry usually begin when technologies become available on the market. By contrast, to get exposure to DFAB in AEC requires engaging with experimental, pre-market technologies. Our case data indicate that demonstrators of such technologies offer a unique chance to create acceptance of DFAB inside firms through hands-on experience, increasing their readiness to absorb DFAB in their workflows once technologies become available in the future.
Outside the project organisation, full-scale implementation also enhances acceptance of DFAB. Building a real project can put new technologies “on the map”, generate visibility and disseminate new ideas not yet known outside the specialised DFAB community. As a signal to the environment – which includes leadership in the AEC industry, regulators and policy makers, and the general public, among others – it can break down perceptual barriers and change expectations. For example, by making tangible the potential DFAB has for sustainability, safety, and construction quality, full-scale projects may help break stereotypes, such as the one-sided association of DFAB with full automation and reduction of labour cost or its reputation as a tool for high-end, boutique designs. Thus it may help strategic and public support for DFAB in AEC that could be crucial for adoption, especially because AEC innovation depends strongly on the external environment (Pries and Janszen Citation1995). This case study allowed early observations on the subject of the outside perception of DFAB projects in AEC, an area that warrants further attention going forward.
Projects are instrumental in establishing a new praxis of DFAB
The case study shows how a project implementing DFAB produces DFAB practitioners – actors who combined their disciplinary and practical backgrounds with new skills to become experts in the young field of DFAB in AEC. In sum, the actions of these practitioners are what people actually do when implementing DFAB, and we can argue that they amount to a new praxis of DFAB in AEC. In projects, “a dynamic setting for action is created on the local arena where knowledge and action come together in practice” (Blomquist et al. Citation2010). Our case study shows how, through a number of specific practices employed towards its adoption, a new praxis of DFAB can emerge from such a project setting. As a consequence, the praxis of DFAB is informed by the core strategies and enabling practices we identified in the framework of DFAB adoption. Thus, its roots are in process and organisation, socio-cultural factors, and knowledge specific to DFAB.
On the spectrum of these factors informing the new DFAB praxis, two are particularly noteworthy. First, in its current early forming stage, the new praxis of DFAB is grounded in the unique knowledge derived from the process of implementing DFAB technologies in the project context. This dynamic process facilitated the combination of a diversity of explicit scientific and technical knowledge but also the integration of tacit, hands-on skills (Nonaka and Lewin Citation1994). The practitioners of DFAB form a new community of practice, bound together by their joint knowledge as well as a shared identity (Brown and Duguid Citation2001).
Second, the new practice of DFAB draws from another, perhaps more lasting effect: the changing of disciplinary and professional cultures, which often starts with individual experiences but has effects beyond them. By practicing DFAB, individuals and organisations acquire not only technical capabilities but also a different cultural disposition. Bringing together disciplines is a necessity for enabling DFAB. The new, wider cultural setting it creates can open up new avenues of exploration by preventing over-socialization and helping “un-learn” some discipline-specific limitations in thinking. Challenging established disciplinary and professional cultures through the practice of DFAB may amount to a first step in shaping a new disciplinary culture of DFAB.
Recent literature has conceptualised new roles emerging in the context of DFAB in AEC at a high level and projected their growing share of participation in the construction organisation (García de Soto et al. Citation2019). Complementing this perspective, our case study allowed us a first chance to empirically study the practical reality of these emerging roles. Thus, DFAB HOUSE helped us gain an early understanding of the actual shape these roles may take in the future practice of DFAB, and who the practitioners are who will occupy these new roles. Importantly, this empirical angle may help us better understand how people, not technologies alone, change an industry.
Limitations and future research opportunities
This research has several limitations. First, it is a single case study, and generalisation can only be reached within the case context. Outcomes of other projects may be different. Furthermore, this study is limited to the project perspective; DFAB innovation adoption could be further studied from a firm and market-focussed perspective to address the multi-scale challenges of innovating and “transforming” the AEC industry (Glass et al. Citation2020).
Second, the proposed framework is conceptual and represents early-stage findings. It should be tested and refined through further case study research and/or comparative case studies as DFAB adoption progresses in AEC.
Third, DFAB HOUSE allows preliminary observations on future production capacity, productivity and organisation of DFAB (García de Soto et al. Citation2018, Citation2019, Lloret-Fritschi et al. Citation2019), but further research is needed to substantiate and quantify how future DFAB implementations will compare to other construction alternatives.
Fourth, this research focuses on the planning and implementation stages of DFAB but does not consider the later life cycle stages of the built result. With longer-term data on DFAB structures becoming available in the future, research is called for to assess the implications of DFAB for operation and maintenance, reconfiguration, and circularity of the built environment.
Conclusion
With this research, we make two contributions to the field of construction management.
Our first contribution is an early socio-technical framework of DFAB adoption in AEC projects. DFAB is expected to play an increasingly important role in AEC, and this framework is a first comprehensive overview of the challenges to consider and the strategies available to successfully adopt DFAB technologies to the benefit of future construction and project delivery. The findings show how uptake of DFAB technologies may shape project organisations and vice versa, how socio-technical integration plays a central role in DFAB adoption, and what effects DFAB implementation has on knowledge and practice in AEC. It is important to keep in mind that DFAB will depend on complementing advances in other areas of digitalization to play an essential role in the digital transition of the AEC industry to a more connected, sustainable, and productive future.
Second, we establish three theoretical propositions that demonstrate the relevance of adopting DFAB in the context of demonstrator projects. These propositions are: (I) Full-scale projects are an effective exploration method of DFAB in AEC (II) Implementation at scale increases acceptance of DFAB in AEC.; and (III) Projects are instrumental in establishing a new praxis of DFAB.
We conclude that exploratory projects bringing DFAB technologies to full-scale construction are an important source of learning about how to integrate DFAB technologies into the socio-technical context of design and construction practice. They facilitate the adoption of DFAB in AEC by prompting the use of individual practices to address technological, organisational, socio-cultural, knowledge-related and perceptual barriers hindering DFAB adoption in today’s AEC industry.
Acknowledgements
The authors thank the reviewers and the interviewees for the rich insights they provided.
Disclosure statement
No potential conflict of interest was reported by the author(s).
Additional information
Funding
References
- Adel, A. (2020). Computational Design for Cooperative Robotic Assembly of Nonstandard Timber Frame Buildings.
- Aghaei-Meibodi, M., Jipa, A., Giesecke, R., Shammas, D., Bernhard, M., Leschok, M., Graser, K., & Dillenburger, B. (2018). Smart Slab: Computational Design and Digital Fabrication of a Lightweight Concrete Slab. ACADIA 2018: Re/Calibration: On Imprecision and Infidelity.
- Agustí-Juan, I., Jipa, A., and Habert, G., 2018. Environmental assessment of multi-functional building elements constructed with digital fabrication techniques. International journal of life cycle assessment, 24, 1027–1039. https://doi.org/https://doi.org/10.1007/s11367-018-1563-4
- Agustí-Juan, I., Jipa, A., and Habert, G., 2019. Environmental assessment of multi-functional building elements constructed with digital fabrication techniques. The international journal of life cycle assessment, 24 (6), 1027–1039.
- Agustí-Juan, I., et al., 2017. Potential benefits of digital fabrication for complex structures: Environmental assessment of a robotically fabricated concrete wall. Journal of cleaner production, 154, 330–340.
- Apolinarska, A. A., et al., 2019., The sequential roof. In A. Menges, T. Schwinn, and O. D. Krieg eds. Advancing wood architecture. Abingdon: Taylor and Francis.
- Bharadwaj, A., et al., 2020. Work design, technology, and artificial intelligence: keeping humans at the center of work. Academy of Management Annual Meeting Proceedings, 2020(1), 12748.
- Birkinshaw, J., and Gibson, C., 2004. Building ambidexterity into an organization. MIT sloan management review, 45 (4), 47–55.
- Blomquist, T., et al., 2010. Project-as-practice: in search of project management research that matters. Project management journal, 41 (1), 5–16,
- Bock, T., 2015. The future of construction automation: technological disruption and the upcoming ubiquity of robotics. Automation in construction, 59, 113–121.
- Bonnard, R., Mognol, P., and Hascoët, J.Y., 2010. A new digital chain for additive manufacturing processes. Virtual and physical prototyping, 5 (2), 75–88.
- Brown, J.S., and Duguid, P., 2001. Knowledge and organization: a social-practice perspective. Organization science, 12 (2), 198–213.
- Caneparo, L., 2014. Digital fabricationin architecture, engineering and construction. Springer Science and Business Media. [AQ]
- Cao, J., et al., 2021. Cross-phase product configurator for modular buildings using kit-of-parts. Automation in construction, 123, 103437.
- Chen, Q., García de Soto, B., and Adey, B.T., 2018. Construction automation: research areas, industry concerns and suggestions for advancement. Automation in construction, 94, 22–38.
- Chesbrough, H.W., and Teece, D.J., 2002. Organizing for innovation: when is virtual virtuous? Harvard business review, 80(8), 127–135.
- Cho, J.Y., and Lee, E.H., 2014. Reducing confusion about grounded theory and qualitative content analysis: similarities and differences. Qualitative report, 19 (32), 1–20.
- Dainty, A. R. J., 2008. Methodological pluralism in construction management research. Advanced Research Methods in the Built Environment.
- Davis, F. D., 1985. A Technology Acceptance Model for Empirically Testing New End-User Information Systems: Theory and Results. Massachusets Institute of Technology.
- Dörfler, K., et al., 2019. Mobile robotic fabrication beyond factory conditions: case study Mesh Mould wall of the DFAB HOUSE. Construction robotics, 3 (1–4), 53–67.
- Dubois, A., and Gadde, L.-E., 2002. The construction industry as a loosely coupled system: implications for productivity and innovativity. Construction management and economics, 20 (7), 621–631.
- Dunn, N., 2012. Digital fabrication in architecture. Laurence King Publishing Ltd.
- Eisenhardt, K.M., 1989. Building theories from case study research. Academy of management review, 14 (4), 532–550.
- European Commission. 2019. Horizon 2020 Work Programme 2018-2020 (19 General Annexes, G. Technology Readiness Levels (TRL); p. 27).
- Fardhosseini, M. S., Karji, A., Dossick, C. S., Lee, H. W., Jebelli, H., & Beatty, S. (2020). The Cost-Effectiveness of Integrating Digital Fabrication for Concrete Formworks. Construction Research Congress 2020, March, 1077–1086.
- Forcael, E., et al., 2020. Construction 4.0: a literature review. Sustainability, 12(22), 9755.
- Garcia de Soto, B., & Skibniewski, M. J. (2020). Future of robotics and automation in construction. In Construction 4.0.
- García de Soto, B., et al., 2018. Productivity of digital fabrication in construction: cost and time analysis of a robotically built wall. Automation in construction, 92, 297–333.
- García de Soto, B., et al., 2019. Implications of Construction 4.0 to the workforce and organizational structures. International journal of construction management, 0 (0), 1–13.
- Gardner, L., et al., 2020. Testing and initial verification of the world’s first metal 3D printed bridge. Journal of constructional steel research, 172, 106233.
- Gershenfeld, N., 2012. How to make almost anything machine! SIGGRAPH 2015: Studio. Siggraph 2015(6), 91.
- Ghobakhloo, M., 2020. Industry 4.0, digitization, and opportunities for sustainability. Journal of cleaner production, 252, 119869.
- Gioia, D.A., Corley, K.G., and Hamilton, A.L., 2013. Seeking qualitative rigor in inductive research: notes on the Gioia methodology. Organizational research methods, 16 (1), 15–31.
- Glaister, K.W., and Richard Falshaw, J., 1999. Strategic planning: still going strong? Long range planning, 32 (1), 107–116.
- Glass, J., Bygballe, L. E., and Hall, D., 2020. Transforming Construction: The multi-scale challenges of changing and innovating in construction. Construction Management and Economics, Call for P.
- Gramazio, F., Kohler, M., and Willmann, J., 2014. The robotic touch how robots change architecture. Zurich: Park Books.
- Graser, K., et al., 2021. Parallel Paths of Inquiry: Detailing for DFAB HOUSE. Technology Architecture and Design, 5 (1).
- Graser, K., et al., 2020. DFAB HOUSE: a comprehensive demonstrator of digital fabrication in architecture. Fabricate 2020: making resilient architecture, 130–139.
- Grieves, M., (2015). Digital Twin: Manufacturing Excellence through Virtual Factory Replication. White Paper, March.
- Hack, N., et al., 2020. Structural stay-in-place formwork for robotic in situ fabrication of non-standard concrete structures: a real scale architectural demonstrator. Automation in construction, 115, 103197.
- Hall, D.M., Whyte, J.K., and Lessing, J., 2020. Mirror-breaking strategies to enable digital manufacturing in Silicon Valley construction firms: a comparative case study. Construction management and economics, 38 (4), 322–339.
- Hamid, M., Tolba, O., and El Antably, A., 2018. BIM semantics for digital fabrication: a knowledge-based approach. Automation in construction, 91, 62–82.
- Hartmann, T., and Trappey, A., 2020. Advanced Engineering Informatics - Philosophical and methodological foundations with examples from civil and construction engineering. Developments in the built environment, 4, 100020.
- Helm, V., Ercan, S., Gramazio, F., & Kohler, M. (2012). In-situ robotic construction: Extending the digital fabrication chain in architecture. ACADIA 2012 - Synthetic Digital Ecologies: Proceedings of the 32nd Annual Conference of the Association for Computer Aided Design in Architecture, 2012-October, 169–176.
- Helms, M.M., and Nixon, J., 2010. Exploring SWOT analysis – where are we now? Journal of strategy and management, 3 (3), 215–251.
- Hu, R., et al., 2021. A simple framework for the cost-benefit analysis of single-task construction robots based on a case study of a cable-driven facade installation robot. Buildings, 11 (1), 1–17.
- Kaseman, K., and Graser, K., 2020. Digital fabrication in the construction sector. In A. Sawhney, M. Riley, and J. Irizarry, eds. Construction 4.0. Abingdon: Routledge.
- Katila, R., Levitt, R.E., and Sheffer, D., 2018. Systemic innovation of complex one-off products: the case of green buildings. Advances in strategic management, 40, 299–328.
- Keating, S.J., et al., 2017. Toward site-specific and self-sufficient robotic fabrication on architectural scales. Science robotics, 2 (5), eaam8986.
- Knippers, J., et al., 2021. Integrative computational design and construction: rethinking architecture digitally. Civil engineering design, 98, 194.
- Kuckartz, U., 2019. Qualitative text analysis: a systematic approach. In G. Kaiser and N. Presmeg eds. Compendium for early career education in mathematics researchers (pp. 181–197). Cham: Springer.
- Kuzmenko, K., et al., 2021. Assessing environmental impact of digital fabrication and reuse of constructive systems. Structures, 31, 1300–1310.
- Lenfle, S., Midler, C., and Hällgren, M., 2019. Exploratory projects: from strangeness to theory. Project management journal, 50 (5), 519–523.
- Lindgren, J., Emmitt, S., and Widén, K., 2018. Construction projects as mechanisms for knowledge integration: mechanisms and effects when diffusing a systemic innovation. Engineering, construction and architectural management, 25 (11), 1516–1533.
- Lloret-Fritschi, E., et al., 2019. Challenges of real-scale production with smart dynamic casting. RILEM Bookseries, 19, 299–310..
- Mata-Falcón, J., Bischof, P., and Kaufmann, W., 2019. Exploiting the potential of digital fabrication for sustainable and economic concrete structures. In: RILEM Bookseries, Vol. 19. https://doi.org/10.1007/978-3-319-99519-9_14
- Mayring, P. (2014). Qualitative Content Analysis. In Qualitative content analysis: theoretical foundation, basic procedures and software solution.
- Melenbrink, N., Werfel, J., and Menges, A., 2020. On-site autonomous construction robots: towards unsupervised building. Automation in construction, 119, 103312.
- Knippers, J. and Menges, A. 2020a. BUGA Fibre Pavilion. Architecture Research Building: ICD/ITKE 2010-2020. Berlin: Birkhäuser. 162–173. https://doi.org/10.1515/9783035620405-031
- Menges, A., and Knippers, J., 2020b. Buga wood pavilion. In Architecture research building Birkhäuser. 150–161.
- Meuer, J., et al., 2019. A typology of digital building technologies: implications for policy and industry. IOP conference series: earth and environmental science, 323 (1), 012053. https://doi.org/https://doi.org/10.1088/1755-1315/323/1/012053
- Midgley, G., and Lindhult, E., 2017. What is systemic innovation? Research Memorandum: University of Hull, 99.
- Muñoz-La Rivera, F., et al., 2021. Methodological-Technological Framework for Construction 4.0. Archives of computational methods in engineering, 28, 689–711.
- Nam, B.C.H., and Tatum, C.B., 1989. Toward understanding of product innovation process in construction. Journal of construction engineering and management, 115 (4), 517–534.
- Nascimento, S., et al., 2016. Sustainable technologies and transdisciplinary futures: from collaborative design to digital fabrication. Science as culture, (4), 25.
- NCCR Digital Fabrication. (2021). dfabhouse.ch. https://dfabhouse.ch/
- Ng, M. S., Bonanomi, M. M., Hall, D. M., & Hackl, J. (2020). Design for digital fabrication: an industry needs analysis of collaboration platforms and integrated management processes. Proceedings of the 37th International Symposium on Automation and Robotics in Construction (ISARC), 318–325.
- Nonaka, I., and Lewin, A.Y., 1994. A dynamic theory of organizational knowledge creation author(s): Ikujiro Nonaka Source a dynamic theory of organizational knowledge creation. Organization Science, 5 (1), 14–37.
- Pan, M., and Pan, W., 2019. Determinants of adoption of robotics in precast concrete production for buildings. Journal of management in engineering, 35 (5), 05019007.
- Popescu, M., et al., 2020. Structural design, digital fabrication and construction of the cable-net and knitted formwork of the KnitCandela concrete shell. Structures, 31, 1287–1299.
- Pries, F., and Janszen, F., 1995. Innovation in the construction industry: the dominant role of the environment. Construction management and economics, 13 (1), 43–51.
- Ribeirinho, M.J., et al., 2020. The next normal in construction. Mckinsey and company, 84.
- Richner, P., et al., 2017. NEST - A platform for the acceleration of innovation in buildings. Informes de la construccion, 69 (548), 1–8.
- Robeller, C., Gamerro, J., and Weinand, Y., 2017. Thétre Vidy Lausanne - A double-layered timber folded plate structure. Journal of the international association for shell and spatial structures, 58(4), 194.
- Sacks, R., et al., 2020. Construction with digital twin information systems. Data-Centric engineering, 1, e14.
- Sandelowski, M., 2000. Whatever happened to qualitative description? Research in nursing and health, 23 (4), 334–340.
- Scheurer, F., and Stehling, H., 2020. New paradigms for digital prefabrication in architecture. Design transactions, 42–49.
- Singh, V., and Holmstrom, J., 2015. Needs and technology adoption: observation from BIM experience. Engineering, construction and architectural management, 22 (2), 128–150.
- Slaughter, S., 1993. Innovation and learning during implementation: a comparison of user and manufacturer innovations. Research policy, 22 (1), 81–95.
- Strauss, A., and Corbin, J., 1990. Basics of qualitative research: grounded theory procedures and techniques. California: SAGE.
- Taylor, J. E., and Levitt, R. E., 2004. A new model for systemic innovation diffusion in project-based industries. In CIFE Working Paper #WP086 (Issue May). Stanford University.
- Taylor, J.E., Dossick, C.S., and Garvin, M., 2011. Meeting the burden of proof with case-study research. Journal of construction engineering and management, 137 (4), 303–311.
- Thoma, A., et al., 2019. Robotic fabrication of bespoke timber frame modules. Robotic fabrication in architecture, art and design, 2018, 447–458.
- Valente, M., Sibai, A., and Sambucci, M., 2019. Extrusion-based additive manufacturing of concrete products: revolutionizing and remodeling the construction industry. Journal of composites science, 3 (3), 88.
- Vazquez, A.N., and Jabi, W., 2019. Robotic assisted design workflows: a study of key human factors influencing team fluency in human-robot collaborative design processes. Architectural science review, 62 (5), 409–423.
- Wangler, T., et al., 2016. Digital Concrete: Opportunities and Challenges. RILEM Technical Letters, 1, 67.
- WEF. 2016. Shaping the Future of Construction A Breakthrough in Mindset and Technology. In World Economic Forum (WEF) (Issue May).
- Willmann, J., et al., 2016. Robotic timber construction - expanding additive fabrication to new dimensions. Automation in construction, 61, 16–23.
- Xu, W., et al., 2020., Fabrication and application of 3D-printed concrete structural components in the Baoshan Pedestrian Bridge Project. In J. Burry, J. Sabin, B. Sheil, & M. Skavara, eds. Fabricate 2020. UCL Press.
- Yin, R. K., 2014. Case study research: design and methods (5th ed.). Thousand Oaks, CA: SAGE Publications.
- Yuan, P., Menges, A., and Leach, N., 2018. Digital fabrication. Tongji University Press.