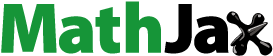
Abstract
The use of industrialised construction can help meet the growing housing demand for developing economies in Africa. In order to understand future scenarios for accelerated adoption of industrialised construction, it is necessary to identify the influencing factors. To do so, this paper conducts a formative scenario analysis which is a literature- and expert-based method, focussing on three countries that have high housing demands, i.e. Ethiopia, Kenya, and South Africa. The resulting analysis consists of three parts. The first is the identification of nineteen internal and external influencing factors. These factors range from product performance to policies and regulations. The second is the illustration of the importance of each factor as a function of its relationship with the other factors. The third is the description of three possible scenarios the adoption of industrialised construction may take in the three investigated countries. The findings show that the most important accelerators for the adoption of industrialised construction come from governments’ commitment to invest in future construction and incentivize companies to adopt industrial construction methods and for these companies to produce competitive products. The specific adoption policies to be implemented, however, depend greatly on the specific situation.
Introduction
Although there is high housing demand in many parts of the world, the most significant demand comes from developing economies. On the continent of Africa alone, there is an estimated backlog of 51 million housing units that need to be constructed (Bah et al. Citation2018). In association with this need, 65% of the next decade’s growth in construction is expected to occur in developing economies (WEF Citation2016). However, several reasons impede the sufficient supply of housing. There is, in many situations, a lack of clear housing and land governance policies from governments coupled with a lack of local capacity from the construction sector to build satisfactory houses in terms of quality and time (Bah et al. Citation2018, Adabre 2021). Furthermore, many people living in Africa cannot afford the current housing prices in the market (UN-HABITAT Citation2011). As a result, there is a need to increase the delivery of affordable housing units massively.
One advanced industry practice that can potentially supply the required amount of affordable housing is industrialised construction (IC), also referred to as prefabrication, off-site construction, or modern methods of construction (MMC). IC uses techniques from the manufacturing industry to increase productivity, improve quality, and reduce the final cost to customers (Gann Citation1996). Many of the fundamental principles of IC have been adopted in different countries for about 200 years (Ågren and Wing Citation2014). Nowadays, IC is characterised by a product platform that constitutes technical and process platforms, unlike conventional construction that primarily employs a project-based approach (Lessing Citation2006). The IC platform allows for efficient design, production, and continuous improvement from project to project in delivering housing (Lennartsson and Elgh Citation2018, Hall et al. Citation2020). Although IC draws many of its lessons from the manufacturing sector, it should not only maximise standardisation; housing needs to be designed and delivered with some product flexibility in consideration of the end customer needs (Gibb Citation2001). Examples of industrialised products include panelised, volumetric, and 3D printing systems (MMC Working Group, Ministry of Housing Citation2019). Industrialised products can be used to construct parts of housing, such as floor/wall elements or complete houses (Gibb and Isack Citation2003, Brege et al. Citation2014).
In a few examples, developing economies have successfully adopted IC to address the high demand for housing and productivity. For instance, public housing projects in Malaysia are required to include at least 70% industrialised products (Ali et al. Citation2018, Rahim and Qureshi Citation2018). The government also incentivizes construction companies to adopt IC through levy exemption (Musa et al. Citation2015). This policy has encouraged manufacturers to adopt IC and bring down the cost of products (Din et al. Citation2012). Other developing economies, such as India, have used IC to deliver low-cost housing since the 1950s (Smith and Narayanamurthy Citation2009).
Despite some successful examples and the potential benefits of IC to alleviate housing supply problems, IC is not widely adopted in many countries in Africa. There is little understanding of how future scenarios might play where the adoption of IC might (or might not) accelerate in this context. Therefore, there is a need to understand the key factors influencing the adoption of IC, investigate their interrelationships, and analyse suitable adoption scenarios. A few studies have qualitatively described factors from specific perspectives, such as regulation-related or market-related influences. However, there is still a need to provide a holistic view of influential factors for adopting IC in developing economies, especially in Africa.
Hence, this study investigates factors influencing the adoption of IC in developing economies in Africa. The paper is organised as follows. The next section presents the research departure with a comprehensive review of global trends of adopting IC and the specific developments in countries in Africa. The following section describes the research design and methodological steps used to identify factors that influence the adoption of IC in selected countries in Africa. The results section presents the list of decisive factors and their roles in adopting IC and three potential IC adoption scenarios for the studied countries. The broader implication of the results for future industry practices and policymakers are explored in the discussion section. Next, the limitations of the research and suggestions for future research directions are presented. Finally, the conclusion section summarises the contributions of the research and recommendations for stakeholders in housing construction.
Departure
Global trends of adopting industrialised construction
One of the foremost countries to adopt IC is Japan (Gann Citation1996), wherein 2012, there were about 150,000 housing units per annum delivered through standardised processes and automation technologies (Linner and Bock Citation2012). Sweden has also adopted industrialised production of timber houses (Malmgren Citation2014). Other countries, such as Singapore, have set out guidelines to support the adoption of IC (Park et al. Citation2011, El-Abidi and Ghazali Citation2015). Different countries have adopted IC for various reasons. For example, one of the primary reasons to adopt IC in Scandinavia is the weather. IC enables continual production during harsh weather conditions (El-Abidi and Ghazali Citation2015). In Germany and Japan, the motivation for IC is productivity gains and reduction of construction labour costs (Linner and Bock Citation2012, El-Abidi and Ghazali Citation2015). Nevertheless, there are still significant barriers and concerns about the adoption of IC (Akmam Syed Zakaria et al. Citation2018a). For example, stakeholders trained for conventional construction methods (e.g. supply chain and regulations) are reluctant or unwilling to adopt IC (Rahman Citation2014, Mohd Amin et al. Citation2017). Additionally, conventional construction is preferred for its economic performance in areas with a sufficient labour supply (Chiang et al. Citation2006). Industrialised products might not be cost-competitive due to the initial investment of setting up a factory and labour training (Chiang et al. Citation2006, Rahman Citation2014). For example, Australia has struggled to adopt mass timber products compared to central European countries. The technology for the products had to be imported from Central Europe and required “early risk-takers” to adopt the technology. Australia required new local expertise, networks, regulatory standardisation, and clients’ interests. During this period, there has been a performance gap in which unsatisfactory results were incurred (Loosemore and Forsythe Citation2019). In such instances, adoption attempts for IC could be delayed or abandoned.
To summarise, the adoption of IC is not straightforward; the institutional, cultural, and economic contexts of different countries and cities shape the level and form of IC adoption.
Industrialised construction adoption in Africa
Specific to countries in Africa, researchers link the current housing crisis to the potential for the adoption of IC. Africa has the fastest-growing population with growing housing demand (GlobalABC/IEA/UNEP Citation2020). The massive housing demand is seen as a reason to promote mass-scale building. IC, together with other housing strategies, is recommended as a possible means to deliver timely built, affordable, quality, and resource-efficient housing (Jerome and Ajakaiye Citation2019, GlobalABC/IEA/UNEP Citation2020, Kedir et al. Citation2020). Furthermore, IC utilises manufacturing processes and can contribute to the economic development of African countries by adding value to raw materials and creating job opportunities for low- to semi-skilled workers (Jerome and Ajakaiye Citation2019). In combination with good policies and incentives, countries in Africa can harness these benefits by adopting IC (Smith and Narayanamurthy Citation2009, Gao and Tian Citation2020).
Previous research identified two strategies that countries in Africa may take to adopt industrialisation in construction and other industries. The first one, titled “import reproduction strategy” solely focuses on the product but not its function and suitability to the existing domestically available resources (Mytelka Citation1989, Jackson and Jabbie Citation2021). The second one, the “import substitution strategy” looks at existing solutions elsewhere and adapts them to local construction capacity and processes (Mytelka Citation1989, Jerome and Ajakaiye Citation2019). Such considerations have worked in Japanese industrialisation but have not sufficiently been used in African countries (Mytelka Citation1989, Bah et al. Citation2018, Jackson and Jabbie Citation2021). Historical IC implementations such as the Maison Tropical, a flatpack system that was built with aluminium and steel in Europe and transported to remote locations in Africa in the 1940s, are perceived to be the wrong types of IC adoption (O’Day Citation2009, Nelson Citation2011). Other researchers have suggested a hybrid approach whereby parts of houses are manufactured in developed nations and combined with local solutions that consider local resources (Richard Citation2008). Current IC adoption often follows two pathways: low-quality mobile solutions or bespoke and expensive solutions (Nelson Citation2011, Kolo et al. Citation2014). However, these approaches do not address the current need for more housing on a large scale.
Much of the adoption of IC in the world has not occurred in Africa. One barrier to IC adoption in Africa is the public’s perception of houses that are built with non-conventional methods. Generally, people associate quality housing with the traditional brick and mortar housing structure. There is also general scepticism that industrialised methods could result in the loss of jobs and other social consequences (Bah et al. Citation2018). The scepticism leaves a resistance to change in the way housing is designed and delivered (Bah et al. Citation2018, Signé and Johnson Citation2018, Kedir et al. Citation2020). As a result, the adoption is seen and recommended to happen in conjunction with conventional construction techniques that involve on-site work (Lal Citation1991). From the side of IC companies, the lack of sufficient capital, infrastructure, and skilled labour are some of the hurdles to adopt IC in developing economies (Baghchesaraei et al. Citation2015, Jerome and Ajakaiye Citation2019). Currently, about 87% of business owners in Africa are concerned about finding skilled labour (WEF Citation2019). Starting and running a business in African countries is also seen as a difficult task. For example, around 80% of firms working in Africa experience about nine power outages per month (African Development Bank Group Citation2018). It is estimated that the poor infrastructure in Africa inhibits the productivity of firms by 40% (Jerome and Ajakaiye Citation2019). In summary, the private sector relies on major initiation from government bodies to accelerate a sustainable adoption of industrialisation in construction (Jerome and Ajakaiye Citation2019).
Research gap and questions
There is a clear need to understand the factors that influence the adoption of IC in countries with high housing demands that are unmet (Smith and Narayanamurthy Citation2009). However, the literature on IC adoption for developing economies in Africa represents isolated views on singular parts of the adoption of IC; a clear and comprehensive picture of the different aspects that influence the adoption does not yet exist. Several scholars have identified factors that determine the adoption of IC (Steinhardt and Manley Citation2016, Akmam Syed Zakaria et al. Citation2018a, Hwang et al. Citation2018, Lu et al. Citation2018, Steinhardt et al. Citation2020; Wang et al. Citation2020) and analysed them using pros and cons lists, SWOT analysis, and systems dynamics (Baghchesaraei et al. Citation2015, Park et al. Citation2011, Zhou et al. Citation2019). Further intensity analysis and risk analysis show the impact strength different external and internal factors have on the adoption of IC (Wang et al. 2020, Zhou et al. Citation2019). While such studies have been valuable, they are not focussed on identifying unknown relationships among factors and constructing possible future scenarios of IC adoption. Moreover, the studies are not focussed on the context of developing economies in Africa.
This study aims to thoroughly investigate the adoption of IC using a suitable scope and method. This would be important to overcome the housing challenges in practice and fill the gap in the current body of knowledge around IC adoption. The guiding research questions in this paper were:
What are the relevant factors that influence the adoption IC in developing economies in Africa?
What are the interrelationships between the different factors and their roles in the adoption of IC?
What are the potential future IC adoption scenarios in developing economies in Africa?
Research design
This paper conducts a formative scenario analysis (FSA) to address the research questions. FSA is a suitable method used to gain insight into a case and its potential future development (Scholz and Tietje Citation2002). Furthermore, FSA has precedence as a method used to convert qualitative knowledge into quantitative understanding for studies on housing and the built environment (Spielmann et al. Citation2005, Spoerri et al. Citation2009a, Brand et al. Citation2013; von Wirth et al. Citation2014, Pagani et al. Citation2020) and for future states of developing economies (Binder et al. Citation2010, Zhang Citation2014).
This paper investigates factors that influence the adoption of IC in three countries in Africa: Ethiopia, Kenya, and South Africa. The criteria for selection were as follows. First, researchers identified seventeen countries in Africa with more than one million housing units backlog (Bah et al. Citation2018). Second, three countries were selected using a convenience sampling technique from the seventeen countries with significant housing backlogs. Convenience sampling is a nonprobabilistic sampling method in which subjective selection criteria such as geographical proximity or data availability are used (Etikan Citation2016). In this paper, the selection criteria was data availability in connection with the authors’ existing industry and research relationships with local stakeholders.
Because IC adoption factors and their interrelationships in developing economies are generally unknown, primary data is gathered through semi-structured expert interviews in the three countries. The first set of interviewees was selected following a purposeful sampling technique. This technique allows to select “information-rich” samples (Palinkas et al. Citation2015). We then followed a snowball sampling technique which allowed us to expand our list of experts across different disciplines. Once we gathered a list of willing participants with sufficient professional background and expertise in housing and IC, the first author carried out semi-structured interviews. The primary data is triangulated with literature and statistical projections to identify current and future IC adoption in the three countries.
Because there is limited research that systematically analysed IC adoption factors and identified possible adoption scenarios in the African context, this study presents the findings of the three cases collectively. This is a suitable approach to give a general overview of the state of large-scale challenges such as housing demand shared across countries (Zhang Citation2014). Hence, the findings do not represent individual assessments of each country. It is recognised that there are limitations to this approach; however, it is still possible for cities and countries to add or remove factors and tailor their own IC adoption trajectories following the methods employed in this paper.
The study regions
The current housing supply and developments in adopting IC in Ethiopia, Kenya, and South Africa are described further in this section.
In Ethiopia, the housing backlog is estimated to be 1 million housing units (Bah et al. Citation2018). Through the integrated housing development programme (IHDP), the Ethiopian government has taken the lead in delivering affordable housing (UN-HABITAT Citation2011, Daget and Zhang Citation2018). The government has also partially adopted IC to address the housing demand. However, there is still an enormous gap between the supply and demand of quality housing (Gemeda Citation2003). Examples of IC products entering the construction market in Ethiopia include a wall system made with light gauge steel (LGS) system (Kedir et al. 2020).The research of Daget and Zhang (Citation2018) shows the three top factors that influence the adoption of IC products in Ethiopia. These are customers’ needs such as design flexibility, supply chain factors such as the country’s manufacturing capacity, and construction industry factors such as skills and knowledge. Current IC adoption relies on imported materials and products since local manufacturing capacity is low (Daget and Zhang Citation2018). Furthermore, most construction is executed using unskilled labour (Daget and Zhang Citation2018). Due to the factors mentioned above and others, the adoption of IC in Ethiopia is currently minimal (Tessera Citation2020).
In Kenya, housing authorities have faced difficulties meeting the housing demand (Hendriks Citation2014, Peter Citation2016, Ogaro Citation2018). Currently, the housing backlog is estimated to be 2 million housing units (Hendriks Citation2014, Bah et al. Citation2018). Housing in Kenya is divided into regulated and unregulated housing construction. The regulated housing construction is executed by private, public, and self-help housing, while the unregulated are primarily informal settlements (Hendriks Citation2014, Chege Citation2017). Both the private and public sectors are thought to have failed to supply the required housing demand, especially for the low-income bracket (Chege Citation2017). The construction industry in Kenya is also considered to have a low institutional capacity, making it challenging to obtain sufficient information about the construction industry (Nyambara Ngugi Citation2017, Kierti et al. Citation2020). In general terms, most construction is characterised by brick and mortar construction techniques. Alternative ways such as IC have not been sufficiently embraced because of higher costs and inadequate knowledge about them (Ogaro Citation2018). The government of Kenya has in 2018 announced plans to deliver 500,000 affordable homes using both conventional and IC methods by 2022 (Government of Kenya Citation2018). Examples of IC product adoption include wall elements constructed with prefabricated expanded polystyrene (EPS) with a shotcrete application on-site as an outer layer (Kedir et al. Citation2020). To increase IC adoption, researchers recommend demonstrative projects to improve their acceptance levels by end-users and promote IC companies through government subsidies (Peter Citation2016, Ogaro Citation2018).
South Africa has a significant housing shortage which is estimated to be 2.3 million housing units (Bah et al. Citation2018). The government of South Africa provides housing for the low-income market segment through programs called the reconstruction and development programme (RDP) and the breaking new ground (BNG) policy which was designed to expand the RDP (Greyling Citation2009, Botes Citation2013). However, research shows that the implementations of these housing programs have lagged behind demand and are widely not accepted by the end-users (Windapo and Goulding Citation2013, Osunsanmi et al. Citation2018). One of the factors mentioned as dissatisfaction is the inability of the houses to provide flexibility in the extension of the housing units and scepticism towards innovative building materials (Windapo and Goulding Citation2013). Innovative and industrialised products are considered inferior to conventional construction by end-users, and some proposed solutions have been proved to be more costly and have low use of the labour market (Botes Citation2013). New market-entry level adoption of IC products in South Africa includes the introduction of prefabricated cross-laminated timber (CLT) walls (Kedir et al. Citation2020). However, the overall adoption of IC in South Africa remains low. For example, in 2010, only 0.68% of all constructed houses since 1994 are thought to be built using alternative forms of construction, including IC (Botes Citation2013).
Methodology
The FSA consists of seven methodological steps, as illustrated in . Due to space limitations, the key points of the method are summarised below. A complete description of the methods can be found in the supplementary material.
Figure 1. Methodological steps in the Formative Scenario Analysis (FSA). Adapted from (Scholz and Tietje Citation2002).
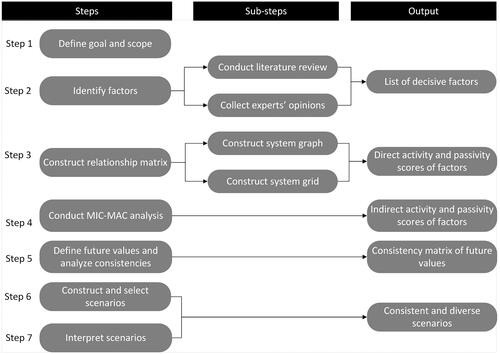
Step 1: Goal and scope definition
The goal of the FSA is to investigate the key factors influencing the adoption of IC and drive potential adoption scenarios. The scope is the countries of Ethiopia, Kenya, and South Africa. The temporal focus of the analysis is between 2019 and 2030.
Step 2: Factors identification
Factors that positively or negatively affect the adoption of IC in the studied countries are identified using the following approaches. First, a literature review on the factors that enable and inhibit IC adoption was conducted, resulting in the identification of 60 potential factors. The list was reduced to contain 34 unique factors by removing duplicates (shown in Table S1 of the supplementary materials section). Next, the list was refined to the 19 most relevant factors for the case study countries following interviews with 36 local and international experts who have direct knowledge of the topic (). Furthermore, each adoption factor was concisely defined using literature and expert opinion. The authors then grouped the 19 factors into six main higher-level categories to associate the factors with broader and easily understandable terminologies.
Table 1. List of experts that participated in the study.
Step 3: Construct a relationship matrix
In this step, the interrelationship between each factor is identified. A matrix was formed by assigning two cell values indicating how the value of one factor affects another factor
and vice-versa. The authors developed a relationship matrix
considering expert opinion representing different stakeholder groups in the construction industry. The matrix shows the strength of the relationship between the factors which is defined on a three-point scale (0, 1, 2): 0 = no or very little direct impact, 1= medium direct impact, 2 = high direct impact. In the end, each factor’s activity (the sum of direct impact one factor has on all other factors) and passivity (the sum of direct impact all factors have on a given factor) scores are calculated. The output of the relationship matrix is further visualised and interpreted using a system graph and system grid.
System graph – shows the relationship matrix using a graphical network representation (Scholz and Tietje Citation2002).
System grid – shows the roles of each factor in the adoption of IC in a system grid format (Scholz and Tietje Citation2002). The system grid has four sections and shows the systemic significance of the factors based on the activity and passivity scores, i.e. active, passive, buffering, and ambivalent.
Step 4: Cross impact matrix-multiplication applied to classification (MIC-MAC) analysis
In this step, indirect impacts are identified using the relationship matrix output from step 3. The output in a simple form reflects the system’s dynamics, similar to feedback loops. The direct and indirect activity and passivity scores of factors were compared to identify if the impact of a factor has been under- or over-estimated (Scholz and Tietje Citation2002). In line with the FSA method, the MIC-MAC output was used to filter the most active factors and reduce the number of factors from 19 to 12. As a result, the most important factors for scenario construction and interpretations were retained.
Step 5: Future value definition and consistency analysis
As an initial step to construct scenarios, three different future values for each factor are determined. For example, a factor has three future values
The first value
is considered a realistic future value of factors in 2030 and is based on statistical projections of well-known institutions such as the World Bank and expert opinion. The other two future values
and
offer two alternative sets of values that are contrasting to
Next, the pairs of future values of factors are rated in terms of their consistency
The consistency rating values are shown in . These values are assigned by the authors and selected experts using a matrix format.
Table 2. Consistency ratings
Step 6: Scenario construction and selection
In total, 531,441 scenarios are constructed using the scenario analysis software KD scenarios (KD-Consistency Analysis Citation2016) from the combination of twelve factors and three different future values for each factor (312). Each specific scenario is constructed as a vector containing a specific future value for each factor. Next, as illustrated in below, two filtering approaches were used for the scenario selection process, i.e. bottom-up (inductive) and top-down (deductive). In the bottom-up approach, two main consistency indices were used to narrow down the list of scenarios. First, 200 scenarios with the highest additive consistency value
are filtered. The additive consistency value represents the sum of all the non-zero consistency rating values. Next, using a top-down scenario selection approach, the authors selected three distinct scenarios representing possible future IC adoption scenarios in the studied countries. To ensure that the scenarios were significantly different from each other, they were selected so that distance-to-selection
values of the scenarios were contrasting. The dts values show the differences between scenarios. This paper’s supplementary material gives further information on the selected scenarios (Table S3).
Figure 2. The scenario selection process.
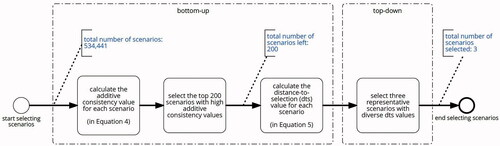
Step 7: Scenario interpretation
In the last step, the selected scenarios are described and discussed in detail. The interpretation of the scenarios is based on the results of the relationship matrix and consistency analysis of future values. This process of selective interpretation is used by the FSA method to create descriptive narratives that can further illustrate logically consistent scenarios.
Results
The following subsections show the results of the FSA performed according to the research methodology section.
Factors influencing the adoption of IC in the studied regions
The 19 identified factors are listed in , with a short definition of each factor. The factors are broadly put into the following six main categories.
Table 3. The decisive set of industrialised construction adoption factors identified.
Product performance – factors related to the performance of industrialised products in comparison to conventional products.
State of industry – factors related to the state of the construction industry.
State of country – factors related to the planning and delivery of infrastructure and housing.
State of market/economy – factors related to the availability of funding and the status of the job market.
Policies and regulations – factors related to readiness to adopt and facilitate industrialised methods and products.
Society – factors related to the end-users’ perception towards industrialised products.
Relationship matrix of factors
The 19 identified factors were rated using a three-point rating scale to identify their relationship. A detailed table of this relationship matrix can be found in in the Appendix section. shows the relationship matrix in a system graph (network format).
Figure 3. System graph of factors.
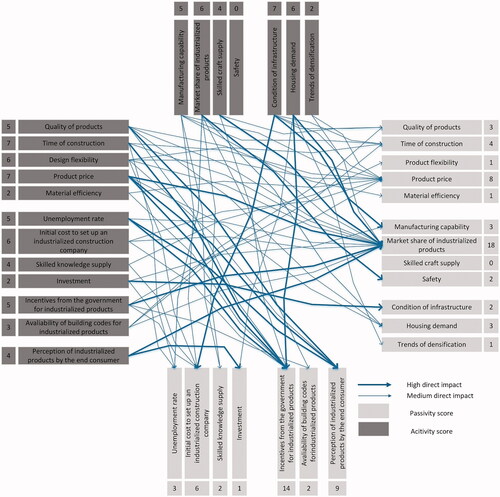
The activity scores show the level of direct impact that one factor has on other factors. All factors except safety show a varying degree of an active role in the adoption of IC. The highest activity scores come from condition of infrastructure and time of construction. The condition of infrastructure has a high direct impact on the initial cost of setting up an IC company and manufacturing capability. The provision of key infrastructure such as quality roads, electricity networks, and water supply networks greatly affects the ease of setting up factories for IC companies. Similarly, the time of construction has the most direct impact on incentives towards industrialised products. The faster that housing can be delivered through industrialised methods, the more incentives that industrialised products can receive from government agencies.
The passivity scores show the total direct influence factors have on a factor. All factors except skilled craft supply show a varying degree of a passive role in the adoption of IC. The market share of industrialised products has the highest passivity score. Most factors have either medium or high direct impact on the potential market share of industrialised products. This is also similar to incentives given towards industrialised products. Changes in other factors influence the level of incentives given to industrialised products. Particularly, the housing demand, product price, and unemployment rate have a strong impact on the level of incentives given towards industrialised products. Higher demand for housing can lead to better availability of incentives towards IC to expedite supply. On the contrary, an increase in the industrialised product price and unemployment rate in a country can decrease the levels of incentives towards industrialised products. Product price has simultaneously high passivity and high activity scores.
The relationship matrix is further understood using a system grid (). The system grid plots the factors in accordance with their specific roles in the adoption of IC. The four types of factor categories are:
Active factors (top left of ) have high impact on other factors. A change in the values of these factors will strongly impact the values of a large number of other factors. The system grid shows condition of infrastructure, time of construction, design flexibility, housing demand, manufacturing capability, and quality of product as active factors. Condition of infrastructure which includes the provision of quality roads, water, and electricity supply networks and the time it takes to construct housing has the highest activity score.
Passive factors (bottom right of ) are factors that are frequently influenced by other factors but do not greatly influence other factors. Initial costs to set up an IC company and perception of industrialised products by end-users are both categorised here as passive factors.
Ambivalent factors (top right of ) are factors that have a strong two-way influence. Product cost, incentives from the government for industrialised products, and the market share of industrialised products are these types of factors. Ambivalent factors are also categorised as having dynamic and unpredictable effects on the adoption of IC.
Buffering factors (bottom left of ) are factors that have below-average activity and passivity values and are believed to have low to moderate influence on the adoption of IC. This category includes the availability of skilled craft and knowledge workers supply, material efficiency, availability of building codes for industrialised products, safety, and investment.
Current and future values of factors
Following steps 4 and 5 in the methodology section, 12 factors with the highest activity scores are retained to construct scenarios. Furthermore, the factor skilled labour supply was created by combining skilled knowledge workers and skilled craft workers. Three possible future values were defined for the year 2030. shows the current average value of each factor and three potential future values for the study regions, i.e.
and
A detailed description of the measurements for each factor is provided in Table S4 in the supplementary materials.
Table 4. Current and future values of factors.
Scenario construction and selection
Each combination of future values of factors was rated for consistency. For example, a much better quality improvement (0.94) and much more time improvement with industrialised products (0.9) was found to be a co-existent scenario. These two factors can improve in parallel. The output of the consistency analysis can be found in the appendix section of this paper, . Next, 200 most consistent scenarios were selected using consistency indices (Step 6). Finally, from the 200 scenarios, the authors selected three consistent and diverse scenarios for further description and exploration (see Section Methodology, Step 6).
Scenario description
The three scenarios selected for interpretation are named private-public tandem, slow adoption, and manufacturing-led adoption of IC. shows the scenarios and the future values of the 12 factors. Each scenario has a set of 12 factors with their future values. The key storylines in the selected scenarios are governed by the future values of six factors. These are manufacturing capability, market share of IC, skilled worker supply, condition of infrastructure, the demand for housing, and investment. Other factors, specifically those under product performance (i.e. quality of products, time of construction, and design flexibility), presented similar future values across the three scenarios.
Table 5. Selected scenarios and future values of factors.
Scenario A – private-public tandem
In the first scenario public-private tandem, both public and private entities lead the efforts for IC adoption. These efforts occur alongside high investment in the construction of crucial infrastructure, including the construction of new housing. Overall, the three studied regions experience an increase in investment (Investment = 80 billion USD) at levels estimated to achieve the United Nations (UN) sustainable development goals (SDGs). From this substantial investment, the countries gain strong improvements in their current conditions of infrastructure, such as road quality and access to electricity and water. Following this investment, overall infrastructure improves significantly (Condition of Infrastructure = RQ 64.4, AE 100, AW 99.8) along with an increase in capability for manufacturing (71 billion USD annual output).
Government agencies promote IC adoption using specific incentives such as tax credits. The combination of significant housing projects, infrastructure availability, and government support creates a growing market where private companies set up new or expand current IC companies. This drives the market share of industrialised products in these countries higher than in comparable regions (Market share = 0.8). In addition, the housing backlog decreases to 25% of current levels (housing backlog = 450,000 million housing units). This housing is delivered using skilled workers (skilled labour supply = 0.59) such that the design and construction of housing results in higher-performing end products. The massive promotion of industrialised products leads to a decline in the prices of industrialised products to levels below the price of conventional construction products (product price = 0.78). Additionally, houses are delivered much faster (Time of construction = 0.9) and with increased quality (quality of products 0.94) than conventional construction. Furthermore, end users are offered more design options for houses with industrialised products compared to conventional products (design flexibility 0.72).
Scenario B – slow adoption
In the second scenario slow adoption, there is no active push to adopt IC. Contrary to the public-private tandem, governments or industry do not promote the adoption of IC. In this scenario, investment levels are consistent with the current prediction for 2030 (Investment = 38.8 billion USD/year). The current condition of infrastructure remains the same (RQ 55.14, AE 68, AW 71) and does not enable significant development in industrialisation to occur in the countries. To that end, there is little change in the manufacturing capability ($60 billion).
Overall, this scenario shows little change in most factors’ status, resulting in a prolonged change in housing delivery. The current housing backlog remains the same (housing demand = 1.8 million housing units). Although industrialised methods can deliver products faster (time of construction = 0.6) and with better quality (quality of products = 0.6), the lack of infrastructure, financial incentives to set up IC companies (Incentives = 0.4), and the lack of market demand to enable scalable growth means that industrialised products remain more expensive to end-users than conventional products (product price = 0.2). Moreover, with the current amount of skilled labour (skilled labour supply = HCI 0.5), there is a shortage of new professionals with the technical knowledge such as CAD and advanced parametric tools to offer products appropriate to achieve design flexibility in houses. Hence, in this scenario, industrialised products’ design flexibility (0.2) is much lower than conventional products. Overall, the market share (0.34) of industrialised products does grow slightly but will remain less than in comparable places.
Scenario C – manufacturing-led
In the final scenario, manufacturing-led, there are efforts to increase some factors such as manufacturing capability coupled with lack of similar effort on other factors such as incentives going towards industrialised products. In this scenario, the manufacturing capability of the three countries increases significantly ($190 billion annual output by 2030). With a greater emphasis on increasing the annual manufacturing output, skilled labour supply increases (HCI 0.69). The growth in manufacturing capability is supported by investment in infrastructure (52.4 billion USD/year). The level of investment in this scenario provides basic required infrastructure in the countries without fully addressing the SDGs. The manufacturing-led scenario is also reinforced by the significant improvement in the condition of infrastructure (RQ 60, AE 85, AW 85), which provides a suitable platform for IC companies to form and grow.
Overall, the product performance indicators of IC show a significant improvement from their current values. However, the housing backlog (housing demand = 900,000 housing units) is not addressed, and the level of industrialised products’ market share (0.6) remains at a middle level.
Discussion
This section discusses the study’s findings in two parts. The first part discusses the decisive factors and their interrelationships in adopting IC are discussed. The second part discusses the three potential scenarios in which the three countries may adopt IC using contextual developments.
Decisive factors and their interrelationships in adopting IC in developing economies in Africa
Many different factors influence the adoption of IC, and their importance is dependent on the country in which IC is to be adopted. The 19 factors identified as decisive factors can be considered to capture the existing political, technical, social, and economic circumstances that influence the adoption of IC in the studied countries. For example, a factor of great relevance in the three countries is housing demand. The average housing backlog is quantified to be 1.8 million housing units (Bah et al. Citation2018) and is seen as an enormous opportunity to adopt IC to deliver housing. Similarly, the inclusion of the initial costs to set up an IC company in the list of decisive factors is influenced by the specific economy-related circumstances in the study regions. Due to a lack of sufficient infrastructure and incentives, doing business mainly in developing economies is difficult for developers (Signé and Johnson Citation2018). Inadvertently, this impacts the price of IC products and the market share of IC.
The decisive factors are further studied by identifying the interrelationships between them and the role of each factor in IC adoption. For example, the infrastructure condition is strongly linked to productivity and sustainable growth in Africa. The lack of sufficient infrastructure is a significant constraint on Africa’s growth (African Development Bank Citation2021). Similarly, this study identifies that the infrastructure condition is an active factor, and the adoption of IC relies on access to quality roads, water, and electricity supply networks. IC companies require reliable access to this infrastructure to set up and run factories. Poor infrastructure conditions can also jeopardise the quality of IC products during production or transportation. The manufacturing and delivery of industrialised products can be delayed if IC companies do not have reliable access to high quality infrastructure.
The complexity in the interrelationship between factors is noteworthy. High housing demand can be a motivating factor in the adoption of IC; however, governments must commit to investing in crucial infrastructure, giving monetary incentives to set up IC companies, and promoting the use of IC products in housing projects. Additionally, IC companies are expected to produce competitive products in terms of quality, price, time, and design flexibility.
Potential adoption scenarios for industrialised construction in developing economies in Africa
In addition to understanding the decisive factors, countries that intend to adopt IC should also construct adoption scenarios using factors’ current and potential future values. These scenarios can help them identify the best ways to reach a desirable IC adoption. This study presents three IC adoption scenarios for the three countries.
The first scenario, public-private tandem, demonstrates a future state in which governments and private bodies take substantial measures to address the enormous housing backlog and high urbanisation rates. Governments invest in infrastructure and incentivize IC companies and products to enter the housing construction market. These interventions by governments boost local IC companies to produce products and compete in the housing market. This is a critical element in the study regions as most companies in Africa are small and medium enterprises (SMEs) that do not have access to a large amount of funding (Yadav et al. Citation2020). Experts in the study regions mentioned fear of loss of jobs as a recurring theme in opposition to the adoption of IC. Interestingly, unemployment rates in the study regions are not increased in this scenario. Other studies also show that countries in Africa are expected to absorb about 100 million labour-intensive and well-paying jobs by 2030 through increasing manufacturing capabilities (Signé and Johnson Citation2018). In summary, through strengthening collaboration between governments in African countries and IC companies, such adoption scenarios can be instrumental in delivering housing with desired product performance. In contrast, the slow adoption scenario depicts a future whereby current values of adoption factors only slightly change. Notably, government bodies do not invest in improving the current condition of infrastructure and provide little incentive for IC companies and products. As a result, the current situation with housing demand in the study regions does not improve. One of the key challenges with following the slow adoption scenario is that the price of IC products remains more expensive than conventional ones. Such scenarios significantly affect low, low-middle, and middle-income groups in the society (Bah et al. Citation2018). Experts currently assess IC as a more expensive solution due to the cost of construction materials, which is highly associated with the high rate of import of major construction materials (Signé and Johnson Citation2018). Most manufacturing outputs, including IC products, are currently imported, leading to “import reproduction” rather than identifying and harnessing local resources (Mytelka Citation1989). Without a significant change in local manufacturing capacity and investment, achieving economy of scale and bringing down the housing price becomes challenging. Hence, such adoption scenarios do not improve the process of delivering affordable housing.
Lastly, in the manufacturing-led scenario, significant improvements are made on some adoption factors while not on others. Specifically, the manufacturing capability is enriched while investments into infrastructure and incentives towards IC industrialised products are considered to progress at about half the pace as would be ideal. Subsequently, the housing backlog is not addressed in similar ways to the public-private tandem scenario. Similar studies indicate a potential abandonment of IC adoption when not correctly implemented the first time around (Loosemore and Forsythe Citation2019). One conclusion from this is that there is need for equal commitment to the adoption factors by government bodies and IC companies to significantly increase housing supply with desired product performance.
It should be noted that the passive factors identified in this study should be considered in the adoption as well. Experts in the studied countries have indicated the need to have a systemic change across the value chain to adopt IC. This includes improving the availability of building codes for IC, trends of densification, and public perception towards IC. Similarly, the adoption of industrialisation in Africa is expected to avert adverse outcomes in terms of environmental sustainability and inclusivity (UN Citation2020). Inevitably, passive factors such as the perception of end-user and material efficiency play a role. It is then essential to account for parameters such as design and material preferences of the end-user and local context (Greyling Citation2009, Peter Citation2016, Ogaro Citation2018).
The development of institutional and regulatory instruments (e.g. benchmarks, policies, best practice programs, and codes and standards) can assist the adoption of IC (Milford Citation2000, Akmam Syed Zakaria et al. Citation2018a, Yadav et al. Citation2020). In contexts where governments have embraced IC, such as Malaysia and Hong Kong, these initiatives are recognised as important tools (Akmam Syed Zakaria et al. Citation2018b). There is a need to form tailored frameworks for the case of developing economies in Africa. The collection of the decisive factors and a description of consistent scenarios from this study provides a sound basis for developing those frameworks for government and private entities to expand the IC market.
Limitations and future research opportunities
Several limitations to this research should be noted. First, the identification of factors and adoption scenarios was made by generalising and taking average values across the studied countries. As a result, the list of factors, their interrelationships, and future adoption scenarios are not specific to one of the study regions. This research presents a first overview of the state of IC adoption for a housing challenge shared by many in developing economies. However, further research could uncover the unique positions of each country to adopt IC. Second, the list of factors may not be exhaustive. Other factors that may be relevant could have been overlooked or not identified due to limited scope and time. Third, some of the factors’ current and future values are based on a limited number of literature and expert opinions. This work represents a starting point but could be extended or modified through additional expert involvement.
Based on the research design and findings of the paper, two main future research directions that can improve the knowledge on IC adoption are discussed below.
There is a need to study IC adoption using a narrower scope than the one used in this study. The adoption of IC is likely going to be different across the studied countries. Using the research design and methods presented here, a more nuanced individual assessment of each country can reveal specific insights. For example, future studies can identify various IC adoption strategies that are fitting to a specific country’s context. Furthermore, the adoption of IC can be studied on a city level to identify factors that influence the adoption of IC at a city scale.
The adoption of IC is studied as a whole without specifying IC products. However, future research could identify industrialised materials and products that are compatible with required technical performance, local supply chains and resources, and housing typologies to meet housing demand with minimal environmental footprint. These may include research on specific industrialised products such as volumetric, panelised, and 3D printing systems and their compatibility with current and projected values of decisive adoption factors. Furthermore, research on imported solutions versus industrialised products with local sustainable materials can shed light on the different IC adoption strategies.
Conclusions
The adoption of industrialised construction in developing economies has the potential to help meet the rising demand for housing. Before policies are developed to encourage the adoption, however, there is a need to understand the factors that may influence their effectiveness while avoiding potentially adverse outcomes. This paper used formative scenario analysis to help policymakers and stakeholders systematically understand factors influencing the adoption of industrialised construction across three countries with high housing demand, i.e. Ethiopia, Kenya, and South Africa.
The paper identified 19 decisive factors that play a role in the adoption of industrialised construction for housing. These factors were grouped into the following six categories that represent the full landscape the factors belong to, i.e. product performance, state of the industry, state of country, state of market/economy, policies and regulation, and society. The adoption is further understood through identifying the relationship between factors and constructing a system grid to show the characteristics of each factor, i.e. active, passive, buffering, or ambivalent. Active factors such as the condition of infrastructure and time of construction are instrumental in the adoption of industrialised construction. Passive factors such as the initial cost of setting up an industrialised construction company and end-users’ perception of industrialised products depend on changes in other factors. Next, three adoption scenarios with different future values of factors are identified and interpreted. The first, labelled public-private tandem, is where governments invest in crucial infrastructure and incentivize industrialised construction companies. As a result, companies are able to produce competitive products in terms of adoption factors for end-users. The second, labelled slow adoption, is one where there is very little initiation from both government and private entities to adopt industrialised construction. With inadequate manufacturing capabilities and investment in crucial infrastructure, industrialised construction companies offer more expensive housing solutions in this scenario. The last, labelled manufacturing-led, has little encouragement by the government, but the construction industry is attempting to adopt industrialised construction. The unmatched commitment in this scenario leads to an insufficient supply of houses.
In summary, high housing demand in countries in Africa is a motivation to adopt industrialised construction. For countries that wish to increase the adoption of industrialised construction as a means to address this demand, there is a significant need to improve the current state of key adoption factors identified in this work. Specifically, industrialised construction companies need to offer more design flexibility while meeting current market prices. These efforts need to be accelerated and complemented by government agencies who can invest in industrialised construction companies, provide greater availability of building codes that support the adoption of industrialised housing products, and dedicate housing projects for industrialised construction. When the above efforts are not synchronised, this research shows it is unlikely to improve product offerings of industrialised companies nor make a meaningful increase in the current housing supply.
Through identifying decisive factors, their pull and push effects from interrelationships, and potential future scenarios, this paper can guide stakeholders aiming to adopt industrialised construction in their local context. However, future research could expand this paper’s methodological approach and findings by assessing factors influencing the adoption of industrialised construction using a more granular scope, such as using a city as a unit of analysis. Furthermore, further research could investigate the adoption of different industrialised product types and adoption differences across housing typologies.
Authors’ contributions
Author 1: Conceptualisation, methodology, investigation, visualisation, writing draft, and editing. Author 2: Methodology, visualisation, writing review. Author 3: Conceptualisation, editing, writing review, and supervision. Author 4: Editing and writing review. Author 5: Conceptualisation and writing review
Supplemental Material
Download MS Word (105.8 KB)Acknowledgments
We would like to acknowledge Jo da Silva, Marco Zumstein, Timothy Partl, and Tyler Pullen for contributing during the conceptualization and investigation phases.
Disclosure statement
No potential conflict of interest was reported by the author(s).
Additional information
Funding
References
- African Development Bank Group, 2018. African economic outlook. Annual yearly review study. Available from: https://www.afdb.org/en/knowledge/publications/african-economic-outlook
- African Development Bank, 2021. Available from: https://www.afdb.org/en/knowledge/publications/tracking-africa’s-progress-in-figures/infrastructure-development
- Ågren, R., and Wing, R.D., 2014. Five moments in the history of industrialized building. Construction management and economics, 32 (1–2), 7–15.
- Akmam Syed Zakaria, S., et al., 2018a. Contextual, structural and behavioural factors influencing the adoption of industrialised building systems: a review. Architectural engineering and design management, 14 (1–2), 3–26.
- Akmam Syed Zakaria, S., et al., 2018b. Key factors influencing the decision to adopt industrialised building systems technology in the Malaysian construction industry: an inter-project perspective. Architectural engineering and design management, 14 (1–2), 27–45.
- Ali, M.M., et al., 2018. Factors impeding the industrialized building system (IBS) implementation of building construction in Malaysia. International journal of engineering and technology, 7 (4), 2209–2212.
- Baghchesaraei, A., Kaptan, M.V., and Baghchesaraei, O.R., 2015. Using prefabrication systems in building construction. International journal of applied engineering research, 10 (24), 44258–44262.
- Bah, E. M., et al., 2018. Unlocking land markets and infrastructure provision. In: Housing market dynamics in Africa. London: Palgrave Macmillan.
- Binder, C. R., Schoell, R., and Diaz, J., 2010. Bringing together diverging system perspectives: the utility of transdisciplinary scenario analysis. In: Building sustainable rural futures: the added value of systems approaches in times of change and uncertainty. 9th European IFSA symposium, Vienna, Austria, 4-7 July 2010, 470–478.
- Botes, A. W., 2013. A feasibility study of utilising shipping containers to address the housing backlog in South Africa. Available from: https://scholar.sun.ac.za/handle/10019.1/85714
- Brand, F.S., et al., 2013. Constructing consistent multiscale scenarios by transdisciplinary processes: the case of mountain regions facing global change. Ecology & society, 18 (2), 43. https://doi.org/10.5751/ES-04972-180243
- Brege, S., Stehn, L., and Nord, T., 2014. Business models in industrialized building of multi-storey houses. Construction management and economics, 32, 208–226.
- Chege, P. W., 2017. Factors affecting housing supply in Nairobi county Kenya. Nairobi: KCA University.
- Chiang, Y.H., Hon-Wan Chan, E., and Ka-Leung Lok, L., 2006. Prefabrication and barriers to entry-a case study of public housing and institutional buildings in Hong Kong. Habitat international, 30 (3), 482–499.
- Daget, Y.T., and Zhang, H., 2018. Application of industrialized housing system in Addis. Available from: https://www.worldresearchlibrary.org/up_proc/pdf/1929-154089910301-03.pdf
- Din, M.I., et al., 2012. The adoption of industrialised building system (IBS) construction in Malaysia: the history, policies, experiences and lesson learned. 2012 Proceedings of the 29th International Symposium of Automation and Robotics in Construction, ISARC 2012.
- El-Abidi, K.M.A., and Ghazali, F.E.M., 2015. Motivations and limitations of prefabricated building: an overview. Applied mechanics and materials, 802, 668–675.
- Etikan, I., 2016. Comparison of convenience sampling and purposive sampling. American journal of theoretical and applied statistics, 5 (1), 1.
- Gann, D.M., 1996. Construction as a manufacturing process? Similarities and differences between industrialized housing and car production in Japan. Construction management and economics, 14 (5), 437–450.
- Gao, Y., and Tian, X.L., 2020. Prefabrication policies and the performance of construction industry in China. Journal of cleaner production, 253, 120042.
- Gemeda, H.B., 2003. Effect of poor project performance on the quality of housing construction: case of condominium houses in Addis Ababa. Engineering education, 2 (December), 6–8.
- Gibb, A.G.F., 2001. Standardization and pre-assembly-distinguishing myth from reality using case study research. Construction management and economics, 19 (3), 307–315.
- Gibb, A.G.F., and Isack, F., 2003. Re-engineering through pre-assembly: client expectations and drivers. Building research and information, 31 (2), 146–160.
- GlobalABC/IEA/UNEP, 2020. GlobalABC regional roadmap for buildings and construction in Africa. Available from: https://globalabc.org/sites/default/files/inline-files/GlobalABC_Roadmap_for_Buildings_and_Construction_in_Africa_FINAL2.pdf
- Government of Kenya, 2018. The 500,000 affordable housing programme. Available from: https://bomayangu.go.ke/downloads/Affordable_Housing_Program_Presentation.pdf
- Greyling, C., 2009. The RDP housing system in South Africa. Available from: https://repository.up.ac.za/bitstream/handle/2263/14433/Greyling_RDP(2009).pdf
- Hall, D.M., Whyte, J.K., and Lessing, J., 2020. Mirror-breaking strategies to enable digital manufacturing in Silicon Valley construction firms: a comparative case study. Construction management and economics, 38, 322–339.
- Hendriks, B., 2014. Housing and the urban poor. In: J. Bredenoord, P. van Lindert, and P. Smets, eds. Affordable housing in the urban global south: seeking sustainable solutions. Abingdon, Oxon: Routledge, 363.
- Human Capital Index, World Bank, 2020. Available from: https://datacatalog.worldbank.org/dataset/human-capital-index
- Hwang, B.G., Shan, M., and Looi, K.Y., 2018. Key constraints and mitigation strategies for prefabricated prefinished volumetric construction. Journal of cleaner production, 183, 183–193.
- Infrastructure Outlook, 2021. Available from: https://outlook.gihub.org/
- ISIC, 2008. International Standard Industrial Classification of all economic activities (ISIC), rev.4. New York: UN Department of Economic and Social Affairs, Statistics Division, Vol. 13.
- Jackson, E.A., and Jabbie, M.N., 2021. Import substitution industrialization (ISI): an approach to global economic sustainability. In: W. Leal Filho, et al., eds. Industry, innovation and infrastructure. Encyclopedia of the UN sustainable development goals. Cham: Springer. https://doi.org/10.1007/978-3-319-95873-6_116
- Jerome, A., and Ajakaiye, O., 2019. Reviving industrialization in Africa. In: E. Nnadozie and A. Jerome, eds. African economic development. Bingley: Emerald Publishing Limited, 425–448. https://doi.org/10.1108/978-1-78743-783-820192021
- KD-Consistency Analysis. 2016. KD-Consistency Analysis.
- Kedir, F., et al., 2020. A sustainable transition to industrialized housing construction in developing economies. Zurich: ETH Zurich. https://doi.org/10.3929/ethz-b-000418072
- Kierti, R.M., et al., 2020. Affordable Housing in Kenya: status, opportunities and challenges. Africa habitat review journal, 14, 18–25.
- Kolo, S.J., Pour Rahimian, F., and Goulding, J.S., 2014. Offsite manufacturing: the way forward for Nigeria’S housing industry. ALAM CIPTA, international journal of sustainable tropical design research and practice, 7 (1), 35–40.
- Lal, A.K., 1991. Housing-India Adoption of low-cost technology for mass housing-the Indian experience: successful Indian experience of mass housing technology worthy of replication in Asia, Africa and parts of Latin America. Building research & information, 19 (4), 214–226.
- Lennartsson, M., and Elgh, F., 2018. Exploring product development in industrialized housing to facilitate a platform strategy. In: IGLC 2018 - proceeding 26th annual conference international group lean construction, 538–548.
- Lessing, J., 2006. Industrialised house-building, concept and processes. Lund: Lund University.
- Linner, T., and Bock, T., 2012. Evolution of large-scale industrialisation and service innovation in Japanese prefabrication industry. Construction innovation, 12 (2), 156–178.
- Loosemore, M., and Forsythe, P., 2019. Sustainable construction technology adoption. In: V.W.Y. Tam and K.N. Le, eds. Sustainable construction technologies. Amsterdam: Elsevier, 299–316. https://doi.org/10.1016/B978-0-12-811749-1.00009-2
- Lu, W., et al., 2018. Searching for an optimal level of prefabrication in construction: an analytical framework. Journal of cleaner production, 201, 236–245.
- Malmgren, L., 2014. Industrialized construction - explorations of current practice and opportunities. Available from: https://www.lunduniversity.lu.se/lup/publication/82d183c5-5b35-4117-bba5-c62e63a67f01
- Milford, R., 2000. National systems of innovation with reference to construction in developing countries. Buildnet. Available from: http://buildnet.csir.co.za/Cdcproc/Docs/2nd/….
- MMC Working Group, Ministry of Housing, 2019. Modern methods of construction, introducing the MMC definition framework. https://doi.org/10.1016/B978-0-08-047163-1.00588-9
- Mohd Amin, M.A., et al., 2017. A review on the current issues and barriers of Industrialised Building System (IBS) adoption in Malaysia’s construction industry. IOP conference series: materials science and engineering, 271 (1), 012031. https://doi.org/10.1088/1757-899X/271/1/012031
- Musa, M.F., et al., 2015. The way forward for industrialised building system (IBS) in Malaysia. In: R. Hassan, et al., eds. InCIEC, 2014: proceedings of the international civil and infrastructure engineering conference 2014. Cham: Springer.
- Mytelka, L.K., 1989. The unfulfilled promise of African industrialization. African studies review, 32 (58), 99–104.
- Nelson, M.I., 2011. Re-imagining the Maison Tropicale: a 21st century prefabricated building system inspired by Jean Prouvé. Available from: https://dspace.mit.edu/handle/1721.1/65657
- Nyambara Ngugi, H., 2017. Use of expanded polystyrene technology and materials recycling for building construction in Kenya. American journal of engineering and technology management, 2 (5), 64.
- O’Day, K., 2009. Tropical or colonial? A reception history of Jean Prouve’s prefabricated houses for Africa. Thesis, LSU. https://doi.org/10.31390/gradschool_theses.3295
- Ogaro, G.S., 2018. Factors determining adoption of alternative affordable housing solutions in Kenya. United States International University – Africa. Available from: https://erepo.usiu.ac.ke/handle/11732/4374
- Osunsanmi, T., et al., 2018. Construction 4.0: its impact towards delivering quality and sustainable houses in South Africa. Budapest: Budapest University of Technology and Economics, 147–156.
- Pagani, A., et al., 2020. Sustainability assessment of the housing system: exploring the interplay between the material and social systems. In: C.R. Binder, R. Wyss, and E. Massaro, eds. Sustainability assessment of urban systems. Cambridge: Cambridge University Press, 384–416. https://doi.org/10.1017/9781108574334.018
- Palinkas, L.A., et al., 2015. Purposeful sampling for qualitative data collection and analysis in mixed method implementation research. Administration and policy in mental health and mental health services research, 42 (5), 533–544.
- Park, M., et al., 2011. Construction policymaking: with an example of Singaporean Government’s Policy to diffuse prefabrication to private sector. KSCE journal of civil engineering, 15, 771–779.
- Peter, N.N., 2016. Evaluation of alternative construction technologies in the delivery of affordable housing - a case study of Nairobi County Peter Njoroge Ngigi. Master of Construction Project Management, Jomo Kenyatta University of Agriculture and Technology.
- Quality of roads, World Economic Forum, 2019. Available from: https://reports.weforum.org/pdf/gci-2017-2018-scorecard/WEF_GCI_2017_2018_Scorecard_EOSQ057.pdf
- Rahim, A., and Qureshi, S., 2018. A review of IBS implementation in Malaysia and Singapore. Journal of the Malaysian institute of planners, 16 (2), 323–333.
- Rahman, M.M., 2014. Barriers of implementing modern methods of construction. Journal of management in engineering, 30 (1), 69–77.(asce)me.1943-5479.0000173
- Richard, R., 2008. Building abroad procurement of construction and reconstruction projects in the international context. Montréal: Université de Montréal.
- Scholz, R., and Tietje, O., 2002. Embedded case study methods: integrating quantitative and qualitative knowledge. Thousand Oaks, CA: Sage.
- Signé, L., and Johnson, C., 2018. The potential of manufacturing and industrialization in Africa: Trends, opportunities, and strategies. Available from: https://www.brookings.edu/wp-content/uploads/2018/09/Manufacturing-and-Industrialization-in-Africa-Signe-20180921.pdf
- Smith, R.E., and Narayanamurthy, S., 2009. Prefabrication in developing countries: a case study of India. In: Wood structures symposium, 48–53. https://scholarworks.umass.edu/cgi/viewcontent.cgi?article=1006&context=wood
- Spielmann, M., et al., 2005. Scenario modelling in prospective LCA of transport systems. Application of formative scenario analysis. The international journal of life cycle assessment, 10 (5), 325–335.
- Spoerri, A., et al., 2009. Expert-based scenarios for strategic waste and resource management planning-C&D waste recycling in the Canton of Zurich, Switzerland. Resources, conservation and recycling, 53 (10), 592–600.
- Steinhardt, D.A., and Manley, K., 2016. Adoption of prefabricated housing-the role of country context. Sustainable cities and society, 22, 126–135.
- Steinhardt, D., et al., 2020. The structure of emergent prefabricated housing industries: a comparative case study of Australia and Sweden. Construction management and economics, 38 (6), 483–501.
- Tessera, B.M., 2020. Review on the practicing of prefabricated building construction technology in Ethiopia Vs world experiences. International journal of innovations in engineering research and technology, 7, 161–169.
- The World Bank, 2018. Access to electricity. Available from: https://data.worldbank.org/indicator/EG.ELC.ACCS.ZS
- UN, 2020. Making industrialization in Africa sustainable. Available from: UN chronicle website: https://www.un.org/en/un-chronicle/making-industrialization-africa-sustainable
- UN-HABITAT, 2011. Affordable land and housing in Africa. Available from: https://unhabitat.org/affordable-land-and-housing-in-africa
- von Wirth, T., et al., 2014. Identifying urban transformation dynamics: Functional use of scenario techniques to integrate knowledge from science and practice. Technological forecasting and social change, 89, 115–130.
- Wang, Y., et al., 2020. Mapping the dynamics of China’s prefabricated building policies from 1956 to 2019: a bibliometric analysis. Building research & information, 49 (2), 216–233.
- WEF, 2016. Shaping the future of construction a breakthrough in mindset and technology. https://www.weforum.org/reports/shaping-the-future-of-construction-a-breakthrough-in-mindset-and-technology/
- WEF, 2019. World Economic Forum. Available from: https://www.weforum.org/agenda/2019/09/why-the-skills-gap-remains-wider-in-africa/
- WHO/UNICEF, 2015. Access to drinking water. Available from: https://ourworldindata.org/water-access#:∼:text= Access to improved water sources is increasing across the world,to an improved water source.&text=In 2015%2C most nations had,greater than 90%25 of households.
- Windapo, A.O., and Goulding, J., 2013. Value-based perspectives of stakeholders’ building requirements in low cost and government subsidised housing projects in South Africa. Construction innovation, 13 (4), 424–444.
- Yadav, G., et al., 2020. Development of a lean manufacturing framework to enhance its adoption within manufacturing companies in developing economies. Journal of cleaner production, 245, 118726.
- Zhang, Y., 2014. Strategic scenario study on international cooperation of e-waste management and metal recycling. Graz: Karl-Franzens-University of Graz.
- Zhou, J., et al., 2019. A selection model based on SWOT analysis for determining a suitable strategy of prefabrication implementation in rural areas. Sustainable cities and society, 50, 101715.
Appendix 1
Figure A1. relationship matrix of factors (0=no or very little direct impact, 1= medium direct impact, 2 = high direct impact.)
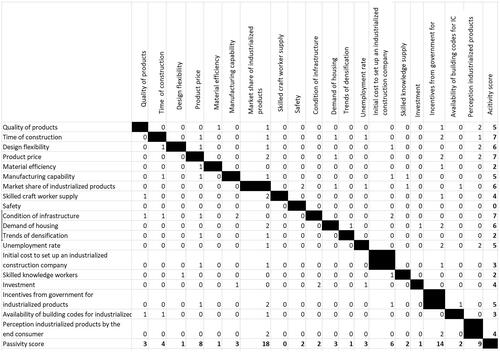