Abstract
Construction logistics services can, if implemented with high quality, positively impact both efficiency and sustainability of construction projects. However, present quality management frameworks have not been developed for temporary multi-actor contexts, such as construction, which is largely lacking industrialised processes. Still, construction logistics service providers provide service offerings to temporary settings and could thus benefit from a service quality perspective. Applying this perspective, this study supports the quality improvement of construction logistics services by using a service modularity approach to identify the services to prioritise for improvement. Building on interviews, concept mapping, and a service blueprint of a construction logistics setup, a priority matrix for improvements is developed. The first step in using this matrix is to operationalise the construction logistics setup in modules based on blueprinting. Second, the matrix evaluates the modules against nine empirically derived improvement enablers such as practices and forums for learning, and data measurements enabling the comparison and follow-up of construction logistics services. In conclusion, the priority matrix helps focus the improvements on modules with high likelihood of successful improvements. Improvements that can become sustained over time through the reuse of standardised modules in upcoming projects.
Introduction
Often one-of-a-kind, customised (Gosling et al. Citation2015), large and immobile constructions tend to be produced at the use site. In other words, construction supply chains are typically convergent, as all resources and materials must be delivered to the construction sites. A construction project includes multiple flows that run across functional and corporate boundaries (Vrijhoef Citation2020). Improving the coordination between these flows has the potential to reduce environmental impact and cost (Vrijhoef Citation2020) and to achieve this, it has become increasingly common to implement logistics services specifically aimed at construction projects (Fredriksson et al. Citation2021). Construction industry representatives refer to these as construction logistics setups (CLSs).
Owing to the temporary nature of construction and the use of a new location for each project, most new construction sites require a CLS adapted to the context of the project (Dubois and Gadde Citation2002, Fredriksson et al. Citation2021). A CLS can combine a few or several services and the CLSs are organised based on either an asset-based terminal setup, that is, a construction logistics centre, or a non-asset-based checkpoint (Hamzeh et al. Citation2007, Janné and Fredriksson Citation2019). Construction logistics centres have the purpose of reducing unnecessary freight movements through coordination and consolidation (Lundesjö Citation2011, Transport for London Citation2013). Checkpoints have been developed to secure just-in-time deliveries through time-slot bookings specifying e.g. the materials and volumes arriving and type of delivery vehicle (Sundquist et al. Citation2018). In summary, a CLS is a bundle of logistics services provided by a construction logistics service provider (Fredriksson et al. Citation2021) delivered to a temporary setting (Dubois and Gadde Citation2002).
As concerns construction logistics services, there is a wide agreement that these impact efficiency and sustainability, which in turn calls for a more structured approach to improving these services as a means to realise the potential impact (see e.g. Agapiou et al. Citation1998, Akintoye et al. Citation2000, Vrijhoef and Koskela Citation2000, Sundquist et al. Citation2018). However, improvements of construction logistics services are challenged by the project-based organisation with a lack of well-defined, in-house, continuous processes (Smyth Citation2010, Backlund and Sundqvist Citation2018), and the multiple actors needed to be involved that makes it difficult to decide whom to involve in improvement activities, and who will benefit from these improvements (Janné and Fredriksson Citation2019). Other service sectors also to some extent lack continuous processes to use as a basis for improvements, which has challenged a process-based view on improvements. This has led to significant developments in the quality management area, where quality is no longer measured on physical outcomes from standardised, continuous improvement, but being defined in interactions between different actors in a value-creating process (Grönroos Citation2011). With this view, service improvements are based on the relationships and interactions between actors rather than on transactions and output, hence being a suitable approach for improvements in project-based organisations.
Deciding who benefits from improvements and thus should be involved in improvement work is challenging in multi-actor, construction projects. However, although it is difficult to assign the customer role (i.e. the primary beneficiary) to one specific actor in a construction project, it has been argued that customers “are the organizations with the motive, means and market opportunity to drive through innovation and improvement” (Smyth Citation2010, p. 260). Moreover, once benefits of improvements have been realised in one project, another challenge is how to transfer improvements and learning to other projects. One possibility of learning transfer is to focus improvement efforts on standardised modules that can be used in several projects, hence cross-cutting the challenges inherent in the lack of continuous processes but still allowing for customised solutions through a tailored bundling of modules.
Modularity, in general, can be defined as the extent to which components of a system are possible to separate and/or combine (de Mattos et al. Citation2019) and has for long been an established approach in product development. Focussing services, service modularity in specific is defined as “a way to develop services and manage heterogeneity (variability) in demand” (Pekkarinen and Ulkuniemi Citation2008, p. 85). Although service modularity is a multidisciplinary field with several current and potential application areas, recent literature has mainly focussed on three service sectors: healthcare, logistics and information, and communications technology (de Mattos et al. Citation2019), with limited insight into project-based sectors. So far, modularity in the construction sector has mainly focussed on modularity of the building elements per se, with categories such as modular buildings, volumetric preassembly, non-volumetric preassembly, and component manufacture and assembly (Peltokorpi et al. Citation2018). However, there is still limited understanding of the application of the concept of modularity to services in the construction sector.
Thus, the purpose is to support quality improvements in construction logistics services by using a service modularity approach for identifying the services to prioritise for improvement. To accomplish this the study uses a mixed-method approach encompassing key informant interviews, an illustrative case study, and a participatory concept mapping study involving 20 construction logistics practitioners. The focus is on construction logistics service providers and their quality improvement work.
Conceptual background
Construction logistics services and their quality are co-created, relational, and unique for each delivery. For efficient operations, this underlines the dilemma of balancing standardisation with customisation. One way to manage it is service modularity. In the multi-actor, project-based construction setting there are also challenges in learning from process-based improvement initiatives in manufacturing (Hoonakker et al. Citation2010). Consequently Landin (Citation2000, p. 509) argues that “the construction industry needs to blend quality concepts from both the service and manufacturing industries”. This contextualised way of working with quality is critical (Sousa and Voss Citation2002) but should still start from the three fundamental principles of quality: customer focus, continuous improvement, and teamwork (Dean and Bowen Citation1994). To address the purpose, this study draws on three key literature streams: construction logistics services, service modularity, and quality management and improvements.
Construction logistics services
Construction logistics is considered a complex service system, which includes not only several actors and touchpoints but also spreads across different companies and industries. Failure to manage such complexity is one of the major reasons to many construction projects suffering from low productivity and high production costs (Vrijhoef and Koskela Citation2000, Ekeskär and Rudberg Citation2016). Despite significant possibilities for creating added value in construction logistics services, previous research reports a lack of understanding and acceptance of the implementation of CLS (Sundquist et al. Citation2018). There is a strong dependency between the activities in the construction project and how the logistics is organised, mainly as the planning of the supply is dependent on the planning of the construction production (Thunberg and Fredriksson Citation2018). The main contractor is responsible for planning the construction production; hence it is also the main contractor that is responsible for the planning the supply process (Bäckstrand and Fredriksson Citation2020). Among few models that apply a logistics perspective to construction planning is the one developed by Friblick (Citation2000) and further elaborated by Thunberg (Citation2016) and Bäckstrand and Fredriksson (Citation2020). Based on this, models the relationship between the supply process and the construction production process and thereby the relation between the work on-site and off-site.
Figure 1. The relationship between a construction project, the construction process and the supply process, based on Friblick (Citation2000) and Thunberg (Citation2016).
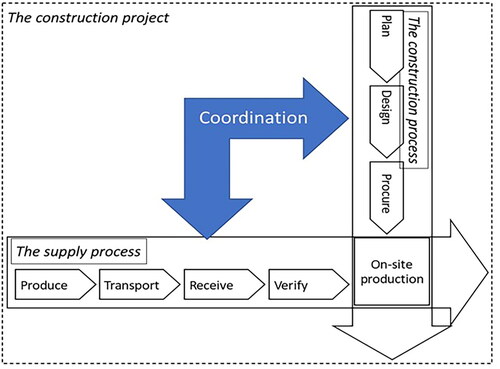
Service quality is essential in the choice of suppliers and subcontractors in the construction industry as these actors support the main contractor delivering value to the final customer, i.e. the developer (Hartmann and Caerteling Citation2010). Though, overall, there is a lack of clarity of the value a CLS creates and for whom, during a construction project. Moreover, to enhance value through improvements is challenging in a multi-actor setting, as improvements of construction logistics efficiency through CLS from one of the involved actors’ perspective might clash with other actors’ view on efficiency (Eriksson Citation2019). Thus, to support improvement work it is critical to define and describe the logistics services in terms of both content and actors involved.
Service modularity and service blueprinting
Although service modularity has foremost been addressed in healthcare, logistics and information, and communications technology (de Mattos et al. Citation2019), there are a few examples of studies applying modularity in construction (see ).
Table 1. Example of studies on modularity in construction.
Overall, the key focus of the selected studies on modularity in construction is physical building elements and less on service elements. An exception is Maxwell et al. (Citation2019), they, however, focus on the strategic level of construction logistics services, proposing modular solutions to be a way forward towards to pursue a re-usable and flexible logistic strategy in the industrial housebuilding setting. Hence, there is a gap in addressing modularity in construction services in conventional housebuilding projects and to propose operationalised and prescriptive solutions to balance efficiency and variety (da Rocha et al. Citation2021), which in this study is addressed through a service modularity approach operationalised through a service blueprint.
Modularity and logistics services
Logistics services operate in many different types of industries and, hence, needs, requirements, and drivers for modularisation differ (Brax et al. Citation2017). Rajahonka (Citation2013) studied 25 logistics service providers to define service modularity in a logistics context. The interviewees considered modularising their service offerings a fruitful and useful approach (Rajahonka Citation2013). Similarly, Bask et al. (Citation2011) suggest significant potential of modular services in logistics, but they hitherto had a low execution level. Both these studies argue that modularity might become more common in the future, given that the demand for customisation of logistics services increases (Bask et al. Citation2011, Rajahonka Citation2013).
Voss and Hsuan (Citation2009) define a service module as either standard or stand-alone services that can be mixed and matched based on the customers’ preferences. Examples in the logistics industry include order management, vendor-inventory management, and storage (de Mattos et al. Citation2019). Others define a service module as one or a set of service components or elements that offer one service function (Pekkarinen and Ulkuniemi Citation2008, Bask et al. Citation2011, Iman Citation2016, de Mattos et al. Citation2019).
Interfaces between service modules are generally less distinct than those between product modules (Voss and Hsuan Citation2009, Bask et al. Citation2011). de Blok et al. (Citation2014, p. 186) define a service interface “as the set of rules and guidelines governing the flexible arrangement, interconnections, and interdependence of service components and service providers”. The standard interface between different service modules enables the mixing and matching of modules, which opens the possibility of customisation (Rajahonka Citation2013). Linked to interfaces is the decomposition of service modules, which refers to the possibility of breaking down the service module into individual functional elements that together deliver a complete service. In logistics, this includes delivery speed, time, and place of delivery, which are factors that the customer values (Bask et al. Citation2011). Hence, speed could, for example, have different offerings, such as overnight or regular delivery (3–5 days). The same goes for the place of delivery, which can vary from home to pick-up point delivery. Each service module should be represented by the smallest possible service unit that can be offered to the customer as a stand-alone one (Rahikka et al. Citation2011).
Service blueprinting
Service blueprinting is a useful tool to visualise and identify modules in complex systems (Geum and Park Citation2011, Chen and Cheng Citation2012), as it models a service system by visualising processes, timing, interactions, and infrastructure end-to-end and throughout the complete value chain (Shostack Citation1982, Fließ and Kleinaltenkamp Citation2004). Focussing the logistics area, Wehner et al. (Citation2021) use the concept of service modularity as a construct and service blueprint as a method to illustrate how not only to identify improvement potential of logistics services but also to explain the actor’s role herein.
Service blueprinting follows a structure in which the horizontal axis symbolises the chronology of processes, and the vertical axis divides the processes into distinctive service areas (Shostack Citation1982, Geum and Park Citation2011). A service process could, for instance, be exemplified by ordering or transporting, while a service area could be represented by customer action or on-stage visible action. The vertical axis is further divided into the lines of interaction, visibility, and internal interaction. The line of interaction separates the actions between the customer and supplier. The line of visibility distinguishes between front- and back-office operations. Finally, the line of internal interaction differentiates management from the support zone (Fließ and Kleinaltenkamp Citation2004). Thus, by using a service blueprint, each subsystem in the service system can easily be mapped out, from architecture to project planning at the same time, highlighting each actor’s responsibilities (Shostack Citation1982, Geum and Park Citation2011, Chen and Cheng Citation2012) and by that also defining the actors that need to be involved in improvement activities.
Quality management and improvements
Focussing the three fundamental principles of quality management; first, customer focus in service contexts is based on the emphasis on quality co-creation and understanding the customers’ perceived quality, which is in turn shaped by unique experiences and expectations (Grönroos Citation2011). For the construction sector, Loushine et al. (Citation2006) show that a poor understanding of customer expectations is a key barrier to successful quality improvement. The criticality of this issue is high, as customer satisfaction has been shown to influence customers’ willingness to repeatedly work with a contractor; in other words, customer satisfaction is important not only within existing projects but also to bridge new projects (Sunindijo et al. Citation2014). However, the customer concept is problematic per se in a multiple actor setting due to the various perspectives of, for example, owners, designers, and contractors (Loushine et al. Citation2006). This could be overcome by expanding the customer concept from the buyer role to anyone that creates value in the value creation process (Grönroos Citation2011). In other words, the customer role can be attributed to different actors, depending on which parts of the construction process are in focus.
Second, the criticality of continuous improvements is based on the idea that “consistent customer satisfaction can be attained only through the relentless improvement of processes that create products and services” (Dean and Bowen Citation1994, p. 305). Based on the study of a range of demonstration projects in the UK construction industry, Smyth (Citation2010) proposes various categories of improvement work that span the improvements before, during, and after a specific project from early involvement and contracts through build quality in construction and then, to the improvements related to environmental responsibility both during and after construction. Underlying all these categories is that improvements involve multiple actors, reflecting that the quality of services is inherently relational and based on interaction (Woo and Ennew Citation2005). Hence, continuous improvements need to be carried out in the relationships where services are co-created, which in a multi-actor setting such as construction (Loushine et al. Citation2006) means that teamwork for continuous improvement is critical.
Third, regarding the principle of teamwork, Hoonakker et al. (Citation2010) emphasise that partnering is a key concern in moving beyond conflicting relationships between actors and enabling joint efforts to improve quality. Traditionally, in quality management, teamwork is based on the quality circles implemented in Japan following WWII, an approach also argued to have been critical in the development of the Toyota production system (Womack et al. Citation2007). Subsequently, the teamwork approach has been expanded to focus not only on internal improvement teams but also on teams involving several actors in a supply chain: “customer focus and continuous improvement are best achieved by collaboration throughout an organisation as well as with customers and suppliers” (Dean and Bowen Citation1994, p. 395). In the construction sector, there is a focus on teams that “moves the process of continuous improvement some way from primarily relational contracting and points towards a more behavioural approach […] to proactively spreading and embedding these capabilities in the supplier organizations” (Smyth Citation2010, p. 263). Hence, teams working with continuous improvements are not restricted to one actor but should preferably involve multiple actors involved in the value-creation process.
Service modularity and quality improvements in construction logistics
It is argued in this paper that service modularity, operationalised in a service blueprint, can facilitate quality improvement of construction logistics services. By focussing on service modularity, this study addresses the gap in terms of support for identification of who benefits from, and who should drive improvements in a multi-actor construction setting. This requires a shared view among the involved actors on the need to improve as “the success of quality management is increased through the combined effort by all parties involved within a project” (Loushine et al. Citation2006, p. 1208). It further addresses the gap on how to sustain improvements between temporary projects (Smyth Citation2010, Backlund and Sundqvist Citation2018) by viewing service modules as knowledge and improvement carriers between projects.
In response to these gaps, a blueprint makes it possible to decompose construction logistics services into service modules, illustrating the relation between them and identifying the need for horizontal coordination. Compared with the common focus on vertical coordination in construction (Hedborg et al. Citation2020), service blueprint is more relational in nature in that it requires both information from several actors to get the “print” right, and collaborative effort as regards the actual improvement. As means of moving beyond pure descriptions of construction logistics services to the actual improvements thereof, the service blueprinting offers a way to approach quality improvements in a project-based setting. Additionally, the improvement of modules that can be reused in other projects creates a potential for the modules to become carriers of knowledge and learning between projects, supporting continuous improvement.
Methods
As this study focuses on a phenomenon in a specific context (i.e. logistics services in construction) it is based on a dominantly qualitative research approach (Voss et al. Citation2002). In addition, the combination of services, quality, and project context is of a nascent nature and hence an explorative design was used in the study (Edmondson and McManus Citation2007).
Sampling, data collection, and analysis
To operationalise the explorative approach and to capture the multi-actor nature of construction project, the research design of this study is based on a three-stage data collection (): key respondent interviews for overview and determining focus; concept mapping to get input from multiple actors; and analytical depth of improvement efforts through service modularity is provided through a service blueprint based on interviews, workshops, onsite observations, and company documents.
Figure 2. Research design; data collection stages and their focus. Arrows indicate how the different stages are linked and how their results feed into each other and combined contribute towards the purpose.
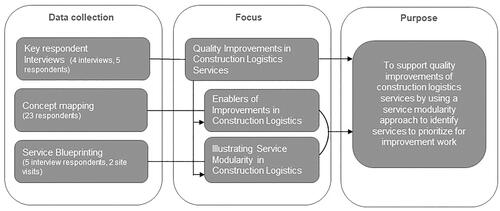
As outlined in , a staged data collection process based on multiple sources of evidence (Flick Citation2014) was applied for exploration. The three data collection stages contributed to both the overall research aim and the subsequent data collection activities. Overall, the key respondent interviews provide a basis for understanding improvement work in construction logistics, feeding into the other parts (concept mapping and service blueprinting) that later are combined into a priority matrix.
Key respondent interviews
The first data collection stage encompassed four semi-structured interviews. The sampling was based on both convenience (interviewees located in Sweden) and a purposive approach (Miles et al. 2014), focussing on high experience levels in a specific setting (van der Ven Citation2007). The sampling was further aligned with the multi-actor nature of construction as a network setting as such, the interviewees represented three types of actors: developers/clients (final customers), main contractors (first line customers/service buyers), and logistics service providers. Specifically, the interviewees were: one project manager from a client organisation (I1), one project developer and one regional manager from another client organisation interviewed jointly (I2), one logistics expert from a main contractor (I3), and one sales manager from a construction logistics service provider (I4). The interviews lasted 40–90 minutes; two interviews were recorded and transcribed, and during two interviews recording was not agreed on by the interviewees and thus detailed notes were taken by two participating researchers.
The interviews focussed on six themes: general viewpoints on construction logistics, improvement work, sustainability and efficiency, implementation, actors and governance, and examples of improvement initiatives. Examples of questions were: “Could you describe how you work with the quality improvement of construction logistics services?”, “How do you reason when designing a construction logistics setup? Do you have a standard solution, or do you customize?”, and “Could you provide an example of a construction logistic service that worked well and what you have done to improve that service? How do you work with improvements in that specific area?”. To analyse the interview data, the first step was to condense the data into individual interview write-ups. Second, a pattern-matching approach (Gibbert et al. Citation2008) was applied to thematically analyse the data vis-à-vis the three principles of quality (customer focus, continuous improvement, and teamwork) (Dean and Bowen Citation1994).
Concept mapping
The second data collection stage builds upon concept mapping (Vaughn and McLinden Citation2016) as a collaborative mixed method. Concept mapping was considered an appropriate methodology as it identifies and includes diverse perspectives and experiences from a particular community. In particular, not only are data collected iteratively, but participants also take an active part throughout the research process. A concept mapping study comprises the following main steps (Vaughn and McLinden Citation2016). (1) preparation (defining community and develop prompt), (2) idea generation (brainstorming), (3) sorting ideas, (4) representation (map and group ideas), (5) interpretation (review the process and discuss the results), and (6) utilisation (plan for future actions).
In this study, the use of concept mapping provides the basis for facilitating discussions and planning future actions for quality improvement. In the following paragraph, the steps of concept mapping are referred to by indicating the corresponding step number within brackets. Community was defined (step 1) as various types of actors with high levels of experience in developing and improving construction logistics services; thus, data collection was initiated at a meeting in June 2020 for a Swedish network around construction logistics services. Concept mapping is initiated by collecting multiple answers to a prompt from each respondent (step 1). In this study, the prompt was defined as: “In order to work with improvement of construction logistics services and their results, I need…”. The prompt takes the perspective of the individual and seeks to identify conditions beneficial for the improvement of construction logistics services.
Responses from idea generation (step 2), were collected using a structured questionnaire distributed digitally to the identified community including the three types of respondents (as described above). Twenty-three respondents generated 127 statements. All respondents were asked if they were willing to participate in the following phases of concept mapping. Those who answered yes (n = 20) were invited to sort the statements in step 3. This is in line with the guidelines of Trochim (Citation1989, p. 3) and Rosas and Kane (Citation2012). To prepare the data for sorting, these statements were preliminarily sorted into 17 categories by the authors, who analysed each category to identify and eliminate duplicates. To further reduce the number of statements before sorting, similar statements were rephrased into a single statement. Additionally, statements that did not answer the prompt were eliminated and each statement was checked for ambiguity (e.g. “time and resources are needed” were split into “time is needed” and “resources are needed”). The resulting 63 statements were also spell-checked and grammar modified before being uploaded to the “optimal sort” tool (OptimalSort Citation2018) and sent out for sorting (step 3), which was completed by 20 practitioners, resulting in 20 different ways of clustering the 63 statements. The practitioners in step 3 included clients (6), main contractors (9), and construction logistics providers (5). Further, the 20 practitioners held positions of logistics managers (8), development managers (4), project leaders (4), general managers (2), and quality managers/developers (2).
The combined data were analysed using the R software (R Citation2018) to identify clusters (step 4). Processing the raw data through hierarchical cluster analysis in R identified a range of 5–15 clusters. The clusters represent a group amongst the 63 statements that were often sorted into the same group by the respondents (Vaughn and McLinden Citation2016). By that, the overall clustering is generated by the quantitative analysis of the respondent’s own sorting. The determination of how many clusters in the range of 5–15 were to be used required analysis of the intersection and overlaps of clusters. This analysis is done both by reviewing the quantitative raw data depicting the distance between the statements as sorted by the 20 participants participating in the sorting stage, but also by assessing nine-cluster structure could be justified with respect to the similarity of the 63 statements grouped in each cluster. The final cluster solution was selected by examining all cluster solutions to determine whether the merging or splitting of statement groups was appropriate.
Note that the authors only affected the number of clusters used for further analysis; the underlying cluster structure was determined by statistical analysis and was not subject to authors’ judgement (Jackson and Trochim Citation2002, Vaughn and McLinden Citation2016). A higher number of clusters allows for a higher level of detail, whereas a lower number of clusters implies a higher level of generalisability. The clusters were then presented in a graphical form using cluster analysis and multidimensional scaling. The output from the concept mapping is used here to develop a list of enablers of improvement.
Service blueprinting
The case used as a basis for the service blueprint is a construction material supplier responsible for a construction logistics setup (CLS) for a housebuilding project in the centre of a medium-sized city in Sweden. The material supplier is a local branch of one of the major construction material trade chains in Sweden, part of a major European construction material trade actor. The main contractor and material supplier have worked together for a long period of time; however, this is the first time for both to utilise a CLS. The CLS was initiated by the main contractor due to experiencing a very confined area at the construction site. The terminal-based CLS includes several logistics services: materials flow planning, warehousing, transport, materials handling at the construction site, cleaning, waste management, and kitting of materials. The planning of deliveries was performed in two steps. First, the needs at the construction site are divided in relation to a production plan with a six-week horizon. Second, based on this, the material supplier orders materials to its warehouse and the call-offs to the site are planned with a one-week horizon. Express transport and short-term changes are offered at an extra cost.
Construction projects are expected to vary widely and are often seen as unique (Dubois and Gadde Citation2002). This means that their logistics are expected to be shaped by various sources, including site managers and their planning and contracting. Interestingly, Sezer and Fredriksson (Citation2021a) show that even if the projects are unique, the logistics flows follow a similar pattern throughout the different phases of a project. Furthermore, CLSs can be regarded as an established way to solve the issues of lack of space at the sites and its vicinity and demands on decreasing transport emissions (Sezer and Fredriksson Citation2021b). With construction transport counting for approximately 10% of the emissions during the construction project (Sezer and Fredriksson Citation2021b), CLSs are becoming an order qualifier, at least in large urban development projects in dense European cities (Brusselears et al. Citation2020). CLSs are typically developed and run by actors within the construction supply chain, such as third-party logistics providers or construction suppliers (Fredriksson et al. Citation2021). Recent research (Hedborg et al. Citation2020) shows that CLSs require more relational and collaborative project management approach, including horizontal collaboration. It can therefore be argued that the selected case in this study is illustrative of how construction logistics is organised today, and such collaborative emphasis is in line with the service approach taken in this study.
The case provided a rare opportunity as the studied actors were willing to provide in-depth insight and participate in developing a service blueprint. The blueprint was developed in three steps. Interviews were conducted with the material supplier (the key account manager [KAM], the logistics manager, the sales manager of the material supplier), and the main contractor (project manager and site manager), that is, the customer and service buyer in this case. At this stage, a total of five interviews (three interviews with the supplier and two with the main contractor) were conducted and two site visits (both the supplier warehouse and the construction site were visited) during a period of one year. The supplier also shared a presentation and description of the CLS. Thereafter, one of the authors developed a draft of the blueprint that was discussed with the KAM. Based on the input from the KAM, the authors identified the hotspots of the activities in the CLS, which were then verified in a workshop with the logistics manager and the KAM of the material supplier. The blueprint was also discussed in workshops with fellow researchers in the areas of logistics and purchasing.
The enablers of quality improvements derived from concept mapping were inserted into the columns of a priority matrix and analysed in terms of their relationship with the underlying principles of quality (customer focus, continuous improvements, and teamwork). The service blueprint was used to define and operationalise the CLS into service modules, which were included as the rows of a priority matrix. The use of improvement enablers to assess service modules and prioritise them for improvements was illustrated by the studied CLS. The assessment and prioritizations were performed in a workshop with four of the authors and as part of the validation process, an assessment was also performed by the KAM from the material supplier. The respondent was introduced to the prioritisation matrix and asked to make his own assessment of the relation between the enablers and the modules in the matrix. The respondent’s assessment was the same as the researcher in 80% of the cases and there were no diametrical differences. However, in terms of the validation based on the KAM’s use of the prioritisation matrix focus was not primarily to compare assessments but to observe his use of the matrix and to interview him about the perceived usefulness of the matrix. The validation revealed possible benefits of using the matrix in a multi-actor group, especially early in a project to support a structured and focussed discussion on construction logistics and improvements thereof.
Research quality
Based on quality criteria for a qualitative research design in general (Shenton Citation2004, Miles et al. Citation2014) and its adoption in a logistics and service context (Halldórsson and Aastrup Citation2003, Ellram and Tate Citation2015), provides a summary of the quality criteria that informed the research and the actions taken to accommodate these.
Table 2. Quality criteria applied to enhance validity and reliability.
Results
In this section, the first part focuses on what the key respondents view as critical aspects to enable quality improvements in construction logistics services. Second, the results from the concept-mapping in response to “what is needed to improve construction logistics services and their results” are shown. Third, an illustrative case of a service blueprint for a CLS is presented.
Improvement work in construction logistics
Interviewees from different types of actors have highlighted the need to continuously interact with customers. An example is the construction logistics service provider that sees the need to get involved early in the main contractor’s planning process to be able to “to become a more central supplier than just arms and feet, which anyone can supply” [I4]. Naturally, this would also create a foundation for a relationship throughout the project that is needed to support continuous updates and improvements.
Regarding continuous improvements, the key respondents share the view that quality improvements in construction in general are characterised by a shortage of structured and formalised approaches and methods. Lacking these standard approaches is viewed as resulting in person- and project-dependent improvement work, and one respondent added that this also influences the lack of early focus on improvements: “one should have a more structured way of working, raising some of these questions really early” [I1].
In addition to building a relationship between different actors early in a project, there is also the need for long-term relationships to provide a basis for fruitful improvement work. The relational aspect of well-functioning improvement is seen as internally critical in one of the organisations, as well as critical externally between actors. Examples of support for improvements through internal relationships are internal logistics networks “used to share experiences as well as spread information” [I3] and having the same staff responsible for setups and data analysis for every CLS to ensure learning between projects. Another example is the main contractor concurrently working on three projects with the same actors and viewing this continuity of actors and the geographical proximity between the sites as key to a joint workgroup focussing on logistics services and their improvements. However, moving into challenges, the project-dependent nature of improvement within each project decides what logistics solution to have, and thus makes it necessary for each project to access “concrete offerings and the possibility of buying very specific services and not complete solutions” [I3].
Therefore, the need for improvements in the relationships and interactions in the construction logistics service deliveries, continuous improvement approaches, and teamwork are agreed upon by the interviewees. The challenge is to make this happen in a project-based context, in other words, to determine what enablers are needed.
Enablers of improvement of construction logistics services
The concept mapping emanated from respondents’ views on what is needed to improve construction logistics services and their results. The analysis rendered nine clusters of aspects critical for improvement work (), referred to as enablers for improvement in construction logistics.
Figure 3. Nine clusters of aspects critical for improvement work.
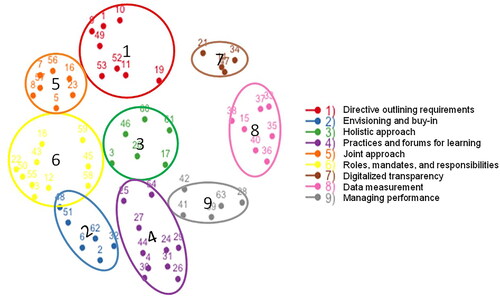
An enabler for improvements in construction logistics services is to create focus and priority around these services early in the project via inclusion in the directive outlining requirements. To get there, there are other enablers that contribute, such as envisioning and buy-in, which, if available, especially for the client, can lead to clear procurement requirements before the project starts. It can also mean that improvement work is still carried out, even if it may not have a positive effect on the short-term results but only in the longer term.
Several identified enablers are based on an awareness of and consideration for construction logistics services being created and delivered in a context with multiple actors. Therefore, it is important to have a holistic approach under which it is possible, for example, to invest extra resources for one actor to enable improvements and opt for resource savings for another. In line with this holistic approach, it is also central to shift the view of construction logistics services from a necessary problem solver to productivity improvement. These improvements can be useful in more projects and for more actors. To support such continuous improvements, there is a need to have established practices and forums for learning within and across actors. Finally, a joint approach to construction logistics services and collaboration based on a long-term perspective and openness is a cornerstone in all improvement work, especially when many actors are involved. In parallel with this collaboration, it is important to create clarity in roles, mandates, and responsibilities, so that neither the construction logistics services themselves nor their improvements lack a clear owner who can drive the work forward.
As in several other industries, digitalisation is seen as an enabler for improvement work, with opportunities to support collaboration, measurement, follow-up, and control through digitalised transparency. Digitalisation can create transparency between actors and influence and facilitate collaboration via various digital platforms, as well as follow-up via simplicity in measurement and data analysis. Data measurement enables us to show the effects of construction logistics services via, for example, the measurement of key figures related to sustainability or results from improvement work, which might create an increased interest in these services. Finally, managing performance can support the improvement of construction logistics services by explicitly pointing out the effects and savings linked to various actors, thus creating interest in more work on this issue. All nine enablers are described in .
Table 3. Enablers of improvements of construction logistics services – description and examples.
Service blueprint of a construction logistics setup
The CLS studied is based on an existing concept, but it was jointly adopted by the material supplier and main contractor before implementation. For example, one project-specific adaptation is the possibility of the main contractor incorporating other suppliers’ deliveries in the material supplier’s terminal and computer system. The CLS was operationalised through a service blueprint (). According to Bitner et al. (Citation2008) there are five components of a typical service blueprint: (1) “Physical evidence” are all those tangibles that customers can see, (2) “Customer actions” include all the steps that customer take as part of the service delivery process. (3) “Onstage/visible contact employee actions” are those actions of frontline contact employees that occur as part of a face-to-face encounter. (4) “Backstage/invisible contact employee actions” refer to non-visible interaction with customers. (5) “Support processes” are activities carried out by individuals and units within the company who are not contact employees but that need to happen for the service to be delivered. The CLS encompasses four service modules (SM), which are clusters of interlinked activities that jointly enable other activities. If an individual activity within a cluster changes, this change will also affect other activities within the cluster. Therefore, if changed independently without considering interdependence in the cluster, the intended outcome might not be achieved.
Figure 4. Service blueprint of the studied CLS.
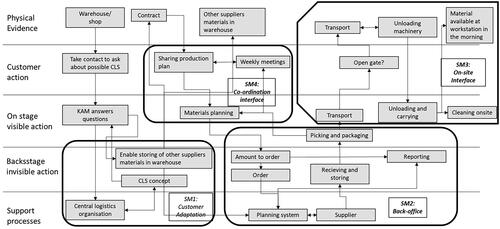
The first module, customer adaptation (SM1), concerns how the setup has been developed and adapted to fit a specific project and the main contractor customer. The concept is implemented locally; however, it is developed and maintained by the material supplier’s central logistics organisation. In this specific construction project, to be able to use a CLS, it was necessary to make main contractor adaptations enabling the storage of external suppliers’ materials in the warehouse, as well as the integration of this material in the material supplier’s planning system.
The second module, the back-office (SM2), includes activities that the material supplier has taken over from the main contractor and suppliers and that are no longer visible to the main contractor. These are traditional logistics activities, such as materials planning, ordering, receiving, storing, and delivering to the site, which ensures the availability of materials when needed. These activities must be carried out efficiently and safely; otherwise, the project will experience a lack of materials and quality issues.
The third module (SM3) is the on-site interface. These activities either take place with the material supplier with results that can be physically seen at the site, or they occur at the site but are carried out by the material supplier. Being visible at the site implies that the workers see the activities’ results, and, thus, crucially, these activities must not fail. Furthermore, as the activities and/or their results are visible at the site, the adaptation of activities needs to fit the specific physical site.
The fourth module (SM4) is the coordination interface with activities related to the continuous coordination between the production planning on site and the back-office activities at the material supplier. This module is central to the CLS and works like a pacemaker for other activities. It includes weekly meetings that enable capturing main contractor problems experienced at the on-site interface and feeding them back to the back office. Furthermore, it is also used for the long-term follow up of logistics performance, which can be fed back to customer adaptation.
Prioritising service modules for improvement
Several enablers for improvement work on construction logistics services have been identified based on the interviews and derived through concept mapping. These enablers reflect all three fundamental principles of quality management, as illustrated in . Further, the use of service blueprinting to identify modules in construction logistics services can be used to prioritise improvement work. In other words, the modules identified in the blueprint can be assessed against critical aspects enabling improvement in construction logistics services to identify the service modules to prioritise for improvement work. illustrates a matrix by which this prioritisation can be supported, using the CLS described in above as an example.
Table 4. Prioritisation matrix for the improvement of construction logistics services based on the CLS blueprinted in .
In , the enablers of quality improvements have been interpreted at the operational level, despite some of them being critical also at the strategic, or even industry level, for example, clear roles, mandates, and responsibilities for construction logistics. The process of using the prioritisation matrix is based on a group discussion, in which each enabler (column) is discussed in relation to each SM (row), leading up to an assessment of the extent to which the enabler is present in each SM in its current state (as-is). The assessment outcomes are labelled as low (L), medium (M), or high (H). Finally, each row is analysed to identify a SM for which the enablers indicate a high probability of a good outcome from the improvement work.
SM1: Customer adaptation scores high on envisioning and buy-in, directive outlining and requirements, practices and forum for learning, and joint approach. These high scores are given due to the material supplier’s early focus on a CLS based on a base-concept (directive outlining and requirements) adapted to the demands of the specific main contractor customer (joint approach). The importance of early involvement is underlined by the KAM from the material supplier, who in his validation scored high as well on all these. Furthermore, the CLS is organised to capture learning from this specific main contractor customer later to be used for the development of the base-concept CLS for long-term use in future projects (practices and forum for learning). The possibilities for development are enhanced by appointing two contact persons: one seller responsible for the commercial agreement and one material flow planner responsible for the weekly planning that works for the long term and at the operational level (envisioning and buy-in), respectively.
SM2: Back-office scored high on managing performance; directive outlining and requirements; and roles, mandates, and responsibilities. The back-office module provides the main contractor customer with reports regularly (managing performance) and helps with planning and ordering (directive outlining and requirements), which is enabled through the clear division of roles, mandates, and responsibilities between the material supplier and the main contractor. According to the KAM, the relevance of improvement work related to SM2 is primarily within the material supplier themselves, as this is connected to their general business development program.
SM3: On-site interface scored high on envisioning and buy-in; data measurement; and roles, mandates, and responsibilities. One concrete example of the well-functioning on-site interface is that the main contractor and the material supplier discovered together that the material supplier could do some of the materials planning based on drawings without consulting the contractor. This saves time and decreases the risk of mistakes during information exchanges (envisioning and buy-in). On-site personnel are also responsible for measuring time and reporting performance through pictures of, for example, deliveries placed at the agreed-upon location at night-time (data measurement). According to the KAM, SM3 is central in the relationship between the main contractor and the material supplier. This is due to the operational focus of this module and the present view on logistics among main contractor customers. The operational activities are carried out by the same actors and persons; for example, transportation is carried out by a local company. To the extent possible, the same driver is used to transport materials to the site, which enables learning. The driver can use earlier experiences to adapt deliveries and capture feedback from employees at the site. Additionally, to make the work as efficient as possible, the material supplier has one dedicated person working with the CLS at the warehouse (roles, mandates, and responsibilities).
SM4: The co-ordination interface scored high on managing performance, data measurement, and joint approach by the authors. The KAM also considered digitalised transparency, joint approach and roles, mandates, and responsibilities to be scored high as the importance of who to do what and why is central to ensure the value of the CLS. The material flow planner meets with the main contractor once a week to plan deliveries and discuss possible improvements (joint approach). The seller is only attending meetings once a month to avoid sending signals that improvements are the only ways to sell more services, and, when present, the seller’s role is to present statistics and capture feedback (managing performance and data measurement).
The low (L) levels of certain enablers in are generally due to a lack of long-term focus because of the project-based context and the lack of digital data gathering and analysis. There are digitalised measurements from the CLS, but the data are mainly used for invoicing. Further, the purpose of the data collection is unclear, leading to data not being suited to support quality improvements. There is also a lack of long-term agreement between the material supplier and the main contractor, which means there is a risk that the improvements made in this single project will not be further developed in upcoming projects; thus, continuous improvement is hindered.
To ensure sustained improvements, improvement work should focus on a module that can be reused in new projects in a relatively standardised form, with the potential for well-functioning teamwork. As such, shows that the co-ordination interface should be prioritised for quality improvement, as it does not have a low presence of any enabler, has a high level of managing performance and, thus, the potential to show clear effects of improvement, a high level of holistic approach, and collaboration between actors; and finally, it affects several other modules, such as customer adaptation based on an increased customer understanding from the interactions in the co-ordination interface.
Discussion
A key challenge for quality improvements in a construction context has long been argued to be the temporary project-based nature (Dubois and Gadde Citation2002), due to which improvements are difficult to sustain from one project to another (Smyth Citation2010, Backlund and Sundqvist Citation2018). To support sustained quality improvements of construction logistics services this study focuses four areas: enablers of quality improvements in construction logistics services, service modularity to balance customisation and standardisation, service blueprinting as a means of modelling services, and sustaining improvements.
First, learning from quality improvements in contexts with continuous processes has been viewed as challenging, owing to the project-based setting (Smyth Citation2010, Backlund and Sundqvist Citation2018), as well as the challenges in a multi-actor setting with unclear responsibilities for improvement work and an unclear customer role (developer as final customer, and main contractor as first line customer) (Loushine et al. Citation2006). Also, the unclarity of how costs, benefits and responsibilities are shifted between actors as a CLS is introduced in a project have created resistance to work with construction logistics between main contractor customers and construction logistics service providers (Thunberg and Fredriksson Citation2022). To overcome these challenges, there is a need to look beyond the traditional product-based views on quality to a service-based one, where quality is co-created between actors (Grönroos Citation2011). This is supported by the inductively derived enablers for quality improvements, which include several enablers related to the interactions between actors (e.g. joint approach and clear roles, mandates, and responsibilities). These enablers are even more critical in a situation characterised by the uncertainty in roles, mandate and responsibilities following the shift of activities between actors coming with the introduction of a CLS (Thunberg and Fredriksson Citation2022). Overall, this study contributes with defining a set of enablers that are specifically adapted to construction logistics services, and that relate to all three fundamental principles of quality management ().
Second, the enablers in point to the necessity of conducting both measurements and analyses customised to a specific project (managing performance) and the need for standardised practices and processes supporting improvements across projects (practices and forum for learning). Therefore, balancing customisation and standardisation is required, which in other settings is often approached using a modularity approach (Bask et al. Citation2011, Gremyr et al. Citation2019). Modularisation of the service design opens for continuous improvement possibilities even in a context characterised by a lack of continuous processes. To this end, modules act as carriers of knowledge and experiences, ensuring that improvements from one project will be sustained in the upcoming ones.
Third, service blueprinting has been chosen as a tool to operationalise service modularity, which, in this setting, makes it possible to create a joint image across the CLS actors. By the blueprint’s inherent horizontal, relational focus, it does somewhat challenge, and is challenged by, the conventional approach to contracting in construction that has a foremost transactional approach to contracting in construction, in which contractor is selected through competitive bidding (Hedborg et al. Citation2020). Moreover, in a context where the uniqueness of a certain project is often positioned as a challenge (Dubois and Gadde Citation2002), blueprinting can aid in decomposition and operationalisation (Geum and Park Citation2011, Shostack Citation1982) into standard modules. Additionally, the blueprint can be used to identify actors critical in the improvement work, as the vertical axis displays the lines of interaction, visibility, and internal interaction. Therefore, it can be a practical tool to identify actors to involve in improvement work and also be a response to da Rocha et al.’s (Citation2021) call for more operationalised and prescriptive solutions to balance efficiency and variety.
Fourth, by combining the empirically derived enablers of quality improvement and service blueprinting, a priority matrix () has been developed to support quality improvement. The blueprint is used to visualise and manage priorities for quality improvement, where priority is given to the improvement of a module with most prerequisites in place and, thus, the highest chances for a good result by providing added value. This is of high relevance as the construction industry is presently struggling with adoption of CLS due to the lack of ability from the construction logistics service provider to show value to the cost-focussed industry (Thunberg and Fredriksson Citation2022). Additionally, the blueprint visualises the connections between modules and can create buy-in in the improvement work for actors not seeing an immediate improvement need. For example, improvements in the coordination interface may not directly involve back-office actors, but the blueprint shows the connection between improved precision in the interface and ordering in the back-office.
Due to the lack of data regarding construction logistics performance, the understanding of present quality delivery is low, among suppliers as well as main contractor customers. As indicated in the validation interview the prioritisation matrix can provide value in supporting discussions on what enablers are present to support improvement work and what enablers that need to be developed. Main contractors prefer stable and continuous relationships and the delivery of high-quality services by suppliers and subcontractors build trust and thus enable long-term relationships (Hartmann and Caerteling Citation2010). To facilitate a continuous improvement and focus efforts where main contractor customers gain the most value of service quality improvements, the priority matrix can be used to facilitate a discussion between main contractors and suppliers and support teamwork. Within construction logistics services, providers can use the matrix as a tool to identify a roadmap from “as-is” to “to-be” and by this support long-term continuous development in main contractor – supplier relationships. The blueprint as such can also create visibility of the service content, an important managerial contribution in the construction industry where construction logistics knowledge so far is relatively low. Thus, service-blueprinting can work as a tool to balance standardisation and customisation and by this increase the value of the construction logistics service.
Conclusions
Quality management and improvements have long been argued to be problematic in a project-based context due to the challenge of making improvements transferable across projects. This study shows that the principles of quality management (customer focus, continuous improvements, and teamwork) are relevant in a construction logistics setting and can be supported by a modularity approach. Further, a service blueprint is used to decompose construction logistics services into modules that can be targeted for improvements. To prioritise and start improvement work, this study proposes nine empirically derived enablers of the quality improvement of construction logistics services: envisioning and buy-in; managing performance; directive outlining requirements; data measurement; practices and forums for learning; digitalised transparency; holistic approach; joint approach; and roles, mandates, and responsibilities. Using these prerequisites as a basis for the improvement prioritisation of certain modules, the modules per se can become carriers of knowledge and improvement between projects. Hence, even in a project-based context, support for continuous improvement is created.
This study is not without limitations. One limitation is the use of an illustrative case, as opposed to one where the priority matrix has been applied in practice and connected to actual improvement efforts. Therefore, an area of future research would be to first to apply the priority matrix to other cases, and second to use the matrix as a starting point for improvement projects for which the actual improvement outcomes could be evaluated. It could also be of interest to apply analytical hierarchy process (AHP) in addition to the service blueprint as a part of the prioritisation of what service modules to target for improvement work. Moreover, while studying improvement projects it would be of interest to further study how tools and practices from the quality management area could be developed to better support improvements in construction logistics services. Another area for future research would be to elaborate and develop the use of service blueprinting by moving from a provider to a main contractor customer perspective as well as a developer customer perspective. This entails exploring questions such as what happens when a main contractor wants to buy modules that do not fit together from the provider’s perspective, when selling only a few modules does not make sense in terms of provider efficiency, or when a developer orders a CLS without the consent of the main contractor (e.g. Janné and Fredriksson Citation2019).
Disclosure statement
The authors report that there are no competing interests to declare.
Data availability statement
The data that support the findings of this study are available from the first author, upon reasonable request.
References
- Agapiou, A., et al., 1998. The role of logistics in the materials flow control process. Construction management and economics, 16, 131–137.
- Akintoye, A., Mcintosh, G., and Fitzgerald, E., 2000. A survey of supply chain collaboration and management in the UK construction industry. European journal of purchasing and supply management, 6, 159–168.
- Backlund, F., and Sundqvist, E., 2018. Continuous improvement: challenges for the project-based organization. International journal of quality and reliability management, 35, 1306–1320.
- Bäckstrand, J., and Fredriksson, A., 2020. The role of supplier information availability for construction supply chain performance. Production planning and control. 33 (9-10), 863–874.
- Bask, A., et al., 2011. Modularity in logistics services: a business model and process view. International journal of services and operations management, 10 (4), 379–399.
- Bitner, M. J., Ostrom, A. L., and Morgan, F. N. 2008. Service blueprinting: a practical technique for service innovation. California management review, 50(3), 66–94.
- Brax, S.A., et al., 2017. Service modularity and architecture–an overview and research agenda. International journal of operations & production management, 37 (6), 686–702.
- Brusselears, N., et al., 2020. Economic, social and environmental impact assessment for off-site construction logistics: the data availability issue. Bristol: IoP Publishing LtD.
- Chen, H.R., and Cheng, B.W., 2012. Applying the ISO 9001 process approach and service blueprint to hospital management systems. The TQM journal, 25 (5), 418–432.
- da Rocha, C.G., Korb, S., and Sacks, R., 2022. Work structuring and product design for customized repetitive projects. Construction management and economics, 40 (7-8), 526–547.
- de Blok, C., et al., 2014. Interfaces in service modularity: a typology developed in modular health care provision. Journal of operations management, 32 (4), 175–189.
- de Mattos, C.S., Fettermann, D.C., and Cauchick-Miguel, P.A., 2021. Service modularity: literature overview of concepts, effects, enablers, and methods. The service industries journal, 41 (15-16), 1007–1028.
- Dean, J. W., and Bowen, D. E., 1994. Management theory and total quality: improving research and practice through theory development. In: R.E. Cole and W.R. Scott, eds. The quality movement and organization theory. Thousand Oaks, CA: Sage Publications, 3–21.
- Dubois, A., and Gadde, L.-E., 2002. The construction industry as a loosely coupled system: implications for productivity and innovation. Construction management and economics, 20, 621–631.
- Edmondson, A.C., and McManus, S.E., 2007. Methodological fit in management field research. Academy of management review, 32 (4), 1246–1264.
- Ekeskär, A., and Rudberg, M., 2016. Third-party logistics in construction: the case of a large hospital project. Construction management and economics, 34, 174–191.
- Ellram, L., and Tate, W.L., 2015. Redefining supply management’s contribution in services sourcing. Journal of purchasing and supply management, 21 (1), 64–78.
- Eriksson, V., 2019, Transport efficiency: analysing the transport service triad. Licentiate thesis report no. L2019:107. Chalmers University of Technology, Gothenburg, Sweden.
- Flick, U., 2014. Mapping the field. In: U. Flick, ed. The SAGE handbook of qualitative data analysis. Thousand Oaks, CA: SAGE Publications, 3–18.
- Fließ, S., and Kleinaltenkamp, M., 2004. Blueprinting the service company: managing service processes efficiently. Journal of business research, 57 (4), 392–404.
- Friblick, F., 2000. Supply chain management in the construction industry – opportunity or Utopia? Degree licentiate in engineering. Lund University.
- Fredriksson, A., Janné, M., and Rudberg, M., 2021. Characterizing third-party logistics setups in the context of construction. International journal of physical distribution and logistics management, 51 (4), 325–349.
- Geum, Y., and Park, Y., 2011. Designing the sustainable product-service integration: a product-service blueprint approach. Journal of cleaner production, 19 (14), 1601–1614.
- Gibbert, M., Ruigrok, W., and Wicki, B., 2008. What passes as a rigorous case study? Strategic management journal, 29 (13), 1465–1474.
- Gosling, J., et al., 2015. Principles for the design and operation of engineer-to-order supply chains in the construction sector. Production planning and control, 26, 203–218.
- Gravina da Rocha, C., Korb, S., and Sacks, R. 2022. Work structuring and product design for customized repetitive projects. Construction Management and Economics, 40(7–8), 526–547.
- Gremyr, I., Valtakoski, A., and Witell, L., 2019. Two routes of service modularization: advancing standardization and customization. Journal of services marketing, 33 (1), 73–87.
- Grönroos, C., 2011. Value co-creation in service logic: a critical analysis. Marketing theory, 11 (3), 279–301.
- Halldórsson, Á., and Aastrup, J., 2003. Quality criteria for qualitative inquiries in logistics. European journal of operational research, 144 (2), 321–332.
- Hamzeh, F.R., Tommelein, I.D., Ballard, G., and Kaminsky, P.M. 2007. Logistics centers to support project-based production in the construction industry. In: C.L. Pasquire and P. Tzortzopoulos, eds. 15th annual conference of the International Group for Lean Construction. East Lansing, MI: IGLC.
- Hartmann, A., and Caerteling, J., 2010. Subcontractor procurement in construction: the interplay of price and trust. Supply chain management. An international journal, 15 (5), 354–362.
- Hedborg, S., Eriksson, P.-E., and Karrbom-Gustavsson, T., 2020. Organisational routines in multi-project contexts: coordinating in an urban development project ecology. International journal of project management, 38 (7), 394–404.
- Hoonakker, P., Carayon, P., and Loushine, T., 2010. Barriers and benefits of quality management in the construction industry: an empirical study. Total quality management, 21 (9), 953–969.
- Iman, N., 2016. Modularity matters: a critical review and synthesis of service modularity. International journal of quality and service sciences, 8 (1), 38–52.
- Jackson, K.M., and Trochim, W.M., 2002. Concept mapping as an alternative approach for the analysis of open-ended survey responses. Organizational research methods, 5 (4), 307–336.
- Janné, M., and Fredriksson, A., 2019. Construction logistics governing guidelines in urban development projects. Construction innovation, 19, 89–109.
- Landin, A., 2000. ISO 9001 within the Swedish construction sector. Construction management and economics, 18, 509–518.
- Loushine, T.W., et al., 2006. Quality and safety management in construction. Total quality management and business excellence, 17 (9), 1171–1212.
- Lundesjö, G., 2011. Using Construction Consolidation Centres to reduce construction waste and carbon emissions. Banbury, Oxon: Waste & Resources Action Programme.
- Maxwell, D., et al., 2019. Logistics strategy for industrialised house building. In: Modular and offsite construction (MOC) summit proceedings, 259–267.
- Miles, M. B., Huberman, A. M., and Saldana, J., 2014. Qualitative data analysis: a methods sourcebook. Thousand Oaks, CA: SAGE Publications.
- OptimalSort, 2018. Card sorting platform that supports remote sorting. Available from: https://www.optimalworkshop.com [Accessed 31 May 2018].
- Pekkarinen, S., and Ulkuniemi, P., 2008. Modularity in developing business services by platform approach. The international journal of logistics management, 19 (1), 84–103.
- Peltokorpi, A., et al., 2018. Categorizing modularization strategies to achieve various objectives of building investments. Construction management and economics, 36 (1), 32–48.
- Pero, M., Stößlein, M., and Cigolini, R., 2015. Linking product modularity to supply chain integration in the construction and shipbuilding industries. International journal of production economics, 170, 602–615.
- R, 2018. R is a free software environment for statistical computing and graphics. Available from: https://cran.r-project.org/ [Accessed 31 May 2018].
- Rahikka, E., Ulkuniemi, P., and Pekkarinen, S., 2011. Developing the value perception of the business customer through service modularity. Journal of business & industrial marketing, 26 (5), 357–367.
- Rajahonka, M., 2013. Views of logistics service providers on modularity in logistics services. International journal of logistics research and applications, 16 (1), 34–50.
- Rosas, S.R., and Kane, M., 2012. Quality and rigor of the concept mapping methodology: a pooled study analysis. Evaluation and program planning, 35 (2), 236–245.
- Sezer, A.A., and Fredriksson, A., 2021a. Paving the path towards efficient construction logistics by revealing the current practice and issues. Logistics, 5 (3), 53.
- Sezer, A.A., and Fredriksson, A., 2021b. Environmental impact of construction transport and the effects of building certification schemes. Resources, conservation & recycling, 172, 105688.
- Shenton, A.K., 2004. Strategies for ensuring trustworthiness in qualitative research projects. Education for information, 22 (2), 63–75.
- Shostack, G.L., 1982. How to design a service. European journal of marketing, 16 (1), 49–63.
- Smyth, H., 2010. Construction industry performance improvement programmes: the UK case of demonstration projects in the Continuous Improvement programme. Construction management and economics, 28 (3), 255–270.
- Sousa, R., and Voss, C.A., 2002. Quality management re-visited: a reflective review and agenda for future research. Journal of operations management, 20, 91–109.
- Sundquist, V., Gadde, L.-E., and Hulthén, K., 2018. Reorganizing construction logistics for improved performance. Construction management and economics, 36 (1), 49–65.
- Sunindijo, R.Y., Hadikusumo, B.H., and Phangchunun, T., 2014. Modelling service quality in the construction industry. International journal of business performance management, 15 (3), 262–276.
- Thunberg, M., 2016. Developing a framework for supply chain planning in construction. Doctoral thesis. Linköping University.
- Thunberg, M., and Fredriksson, A. 2018. Bringing planning back into the picture–How can supply chain planning aid in dealing with supply chain-related problems in construction?. Construction management and economics, 36(8), 425–442.
- Thunberg, M., and Fredriksson, A., 2022. A model for visualizing costs shifts when introducing construction logistics setups. Construction innovation.
- Transport for London, 2013. Construction logistics plan guidance for developers. Windsor House, London: Transport for London.
- Trochim, W.M., 1989. An introduction to concept mapping for planning and evaluation. Evaluation and program planning, 12, 1–16.
- van der Ven, A. H., 2007. Engaged scholarship: a guide for organizational and social research. New York, NY: Oxford University Press.
- Vaughn, L. M., and McLinden, D., 2016. Concept mapping: Visualizing what the community thinks. In: L.A. Jason and D.S. Glenwick, eds. Handbook of methodological approaches to community-based research: qualitative, quantitative, and mixed methods. New York: Oxford University Press, 305–314.
- Voordijk, H., Meijboom, B., and de Haan, J., 2006. Modularity in supply chains: a multiple case study in the construction industry. International journal of operations & production management, 26 (6), 600–618.
- Voss, C.A., and Hsuan, J., 2009. Service architecture and modularity. Decision sciences, 40 (3), 541–569.
- Voss, C., Tsikriktsis, N., and Frohlich, M., 2002. Case research in operations management. International journal of operations & production management, 22 (2), 195–219.
- Vrijhoef, R., 2020. Extended roles of construction supply chain management for improved logistics and environmental performance. In: P. Tzortzopoulos, M. Kagioglou, and L. Koskela, eds. Lean construction – core concepts and new frontiers. Boca Raton, FL: Routledge, 2000.
- Vrijhoef, R., and Koskela, L., 2000. The four roles of supply chain management in construction. European journal of purchasing & supply management, 6, 169–178.
- Wehner, J., Altuntas Vural, C., and Halldórsson, Á., 2021. Energy efficiency in logistics through service modularity: the case of household waste. International journal of physical distribution & logistics management, 51 (1), 76–94.
- Womack, J. P., Jones, D. T., and Roos, D., 2007. The machine that changed the world: the story of lean production – Toyota’s secret weapon in the global car wars that is now revolutionizing world industry. New York: Simon and Schuster.
- Woo, K., and Ennew, C.T., 2005. Measuring business-to-business professional service quality and its consequences. Journal of business research, 58, 1178–1185.