Abstract
An experimental investigation has been carried out to study the heat transfer and friction factor characteristics of a V-down-perforated baffled roughened solar air heater duct. The roughened wall was uniformly heated and the rest three walls of the duct were kept insulated. Measurements have been carried out for the duct aspect ratio of 10, Reynolds number range of 3800–19,000, relative hole position range of 0.429–0.571, relative roughness pitch range of 2–4, and open area ratio range of 12–44%. The relative roughness height of 0.4 and angle of attack of 60° are kept constant during the entire experimentation. The heat transfer and friction factor data obtained were compared with the data obtained from a smooth duct under similar operating conditions. In comparison to the smooth duct the V-shaped perforated baffle roughened duct enhanced the Nusselt number and friction factor by 2.57 and 5.96 times, respectively. The thermohydraulic performance parameter is found superior for the open area ratio of 24% and relative roughness pitch of 2.5.
NOMENCLATURE
AR | = | duct aspect ratio |
Ap | = | surface area of absorber plate, m2 |
Ao | = | area of orifice meter, m2 |
b | = | baffle length, m |
Cd | = | coefficient of discharge |
Cp | = | specific heat of air, J/kg-K |
d | = | hole diameter, m |
Dh | = | hydraulic diameter of duct, m |
e | = | height of the baffle, m |
e/H | = | relative roughness height |
f | = | friction factor |
Gair | = | mass velocity of air, kg/s-m2 |
H | = | height of the duct, m |
h | = | heat transfer coefficient, W/m2-K |
kair | = | thermal conductivity of air, W/m-K |
L | = | length of test section, m |
l | = | hole position from base of baffle, m |
l/e | = | relative hole position |
= | mass flow rate of air, kg/s | |
Nu | = | Nusselt number |
n | = | number of drilled holes in the baffle |
P | = | baffle pitch, m |
P/e | = | relative roughness pitch |
ΔPo | = | pressure drop across orifice plate, Pa |
ΔP | = | pressure drop across test section, Pa |
Pr | = | Prandtl number |
Qu | = | useful heat gain, W |
Re | = | Reynolds number |
Ti | = | temperature of fluid at inlet, K |
To | = | temperature of fluid at outlet, K |
Tp | = | mean temperature of absorber plate, K |
Tf | = | bulk mean temperature of flowing fluid, K |
W | = | width of the duct, m |
Greek Symbols
α | = | angle of angle, o |
β | = | open area ratio |
η | = | thermohydraulic performance parameter |
ρair | = | density of air at bulk mean air temperature, kg/m3 |
ψ | = | ratio of orifice diameter to pipe diameter |
Subscript
s | = | smooth duct |
Additional information
Notes on contributors
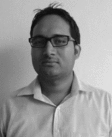
Sunil Chamoli
Sunil Chamoli is an assistant professor in the Department of Mechanical Engineering, DIT University, Dehradun, India. His doctoral research was focused on heat transfer enhancement in rectangular duct using perforated turbulators. He has published seven research articles in the referred journals.
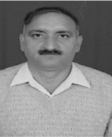
Narender Singh Thakur
Narender Singh Thakur is a professor in the Centre for Energy and Environment at NIT Hamirpur, India. His research interests include heat transfer enhancement, refrigeration and air conditioning systems, and solar energy. He has guided many research scholars, both M.Tech and Ph.D., and co-authored more than 30 papers in refereed journals.