Abstract
The third-generation heat transfer technologies, such as three-dimensional fin and dimple, are still important means of improving energy efficiency and will continue to be challenging issues. This paper presents condensation heat transfer performance of an edge-shaped finned tube fabricated by a ploughing–extruding process. The edge-shaped finned tube integrates more than one heat transfer enhancement technology and can enhance the heat transfer capacity greatly. It is seen that the overall heat transfer coefficient and heat flux increase with inlet velocity of cold water increasing, and decrease with inlet temperature of cold water increasing, whereas the shell-side heat transfer coefficient decreases with inlet velocity of cold water increasing and increases with inlet temperature of cold water increasing. At the same inlet velocity, the shell-side heat transfer coefficient for the edge-shaped finned tube is improved by 5–7 times compared to that of a smooth tube. At the same temperature difference between wall and vapor, the shell-side heat transfer coefficient is also higher than what had been reported in the literature. The shell-side heat transfer coefficient of the edge-shaped finned tube decreases with the increase of fabrication parameter feed at the same inlet velocity or inlet temperature of cold water.
NOMENCLATURE
Ai | = | inside surface area of tube, m2 |
Ao | = | heat transfer area based on outside nominal area of tube, m2 |
ap | = | ploughing–extruding depth of tool, mm |
Cpc | = | specific heat of cold water, J kg−1°C−1 |
ci | = | dimensionless constant |
di | = | inside diameter of tube, m |
do | = | outside diameter of tube, m |
f | = | feed of tool, mm/r |
kw | = | thermal conductivity of tube wall, W m−1 K−1 |
l | = | effective length of tube, m |
n | = | rotating velocity of tubes, r/min |
Pr | = | Prandtl number |
Qc | = | heat carried away by cold water, W |
q | = | heat flux, W m−2 |
qv | = | volumetric flow rate of cold water, m3 s−1 |
Re | = | tube-side Reynolds number |
Rw | = | thermal resistance of tube wall, K m2 W−1 |
Tic | = | inlet temperature of cold water, °C |
Toc | = | outlet temperature of cold water, °C |
Tsat | = | saturation temperature, °C |
Tw | = | temperature of wall, °C |
U | = | overall heat transfer coefficient, W m−2 K−1 |
V | = | inlet velocity of cold water, m s−1 |
Greek Symbols
ρc | = | density of cold water, kg m−3 |
αo | = | shell-side heat transfer coefficient, W m−2 K−1 |
αi | = | tube-side heat transfer coefficient, W m−2 K−1 |
ΔTm | = | log mean temperature difference, °C |
κr | = | primary cutting edge angle, deg |
κr′ | = | extruding angle, deg |
Additional information
Funding
Notes on contributors
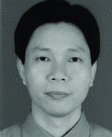
Zhen-Ping Wan
Zhen-Ping Wan is a professor of mechanical engineering at the South China University of Technology (SCUT), Guangzhou, China. He received his Ph.D. degree form SCUT. He has been teaching at SCUT since 2003 except for one year spent at the Wu Manufacturing Research Center, University of Michigan, as a visiting scholar. His research interests focus on functional surface structure manufacturing and its mechanism of action, electronics cooling, cutting tool development and precision engineering.
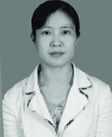
Xiao-Wu Wang
Xiao-Wu Wang is an associate professor at South China University of Technology. She received her Ph.D. from South China University of Technology in 2006. Her research interests include microscale heat transfer enhancement, energetic materials, thermodynamics model of thermal phenomenon, and renewable energy technology. She has co-authored 57 papers in journals and conference proceedings.
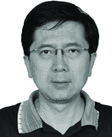
Yong Tang
Yong Tang is a professor of mechanical engineering at the South China University of Technology (SCUT). He received his Ph.D. degree form SCUT in 1994. He is the Associate Dean of the School of Mechanical and Automotive Engineering and the head of academic subject of Mechanical Manufacturing Engineering. His research interests include manufacturing process and advanced manufacturing of functional surface structures for thermal control and energy applications.