Abstract
The present study is concerned with the simulation of incompressible Newtonian fluid flow and heat transfer over a long semicircular bluff body in a channel at low Reynolds numbers. In particular, wall effects on the forced convection from a (heated) semicircular cylinder confined in a horizontal channel are investigated for Reynolds number = 1–40 and blockage ratio = 16.67–50% for air as the working fluid. Flow and thermal fields are found steady for the preceding range of settings. The onset of flow separation increases as the wall confinement increases. The size of the recirculation zone downstream of a semicircular cylinder is seen to increase almost linearly with Reynolds number for a fixed blockage ratio, but it decreases with increasing blockage ratio for a fixed Reynolds number. As expected, total drag coefficient and its components decrease with increasing value of Reynolds number. However, with increasing blockage ratio, the values of these drag coefficients increase. On the basis of equal projected area, the total drag coefficient for the present flow system is found to be greater than the corresponding drag in the case of the unconfined semicircular cylinder. Similarly, the overall drag in the case of a confined semicircular cylinder is found to be greater than that of a confined circular cylinder for the appropriate range of dimensionless control parameters. The maximum augmentation in heat transfer for blockage ratios of 25% and 50% is found to be approximately 16% and 51% with respect to the corresponding value at the blockage ratio of 16.67% at Reynolds number = 1. Finally, the correlations of wake length, drag coefficient, and average Nusselt number are obtained.
NOMENCLATURE
CD | = | total drag coefficient, CD = 2FD/(ρU2∞D), dimensionless |
CDF | = | friction drag coefficient, CDF = 2FDF/(ρU2∞D), dimensionless |
CDP | = | pressure drag coefficient, CDP = 2FDP/(ρU2∞D), dimensionless |
Cp | = | thermal heat capacity of the fluid, J kg−1 K−1 |
CV | = | control volume |
D | = | diameter of a semicircular cylinder, m |
Fr | = | Froude number, dimensionless |
FD | = | drag force per unit length of the cylinder, N m−1 |
FDF | = | friction drag force per unit length of the cylinder, N m−1 |
FDP | = | pressure drag force per unit length of the cylinder, N m−1 |
h | = | local heat transfer coefficient, W m−2 K−1 |
= | average heat transfer coefficient, W m−2 K−1 | |
H | = | height of the computational domain, m |
k | = | thermal conductivity of the fluid, W m−1 K−1 |
L | = | length of the computational domain, m |
Lr/D | = | recirculation or wake length, dimensionless |
n | = | power-law index, dimensionless |
NuL | = | local Nusselt number, NuL = hD/k, dimensionless |
Nu | = | average Nusselt number, |
p | = | pressure, Pa |
= | Prandtl number, | |
Re | = | Reynolds number, |
t | = | time, s |
T | = | temperature, K |
T∞ | = | temperature of the fluid at the channel inlet, K |
Tw | = | constant wall temperature at the surface of the cylinder, K |
U∞ | = | average velocity of the fluid at the inlet, m s−1 |
Ux, Uy | = | x- and y-components of the velocity, respectively, m s−1 |
x, y | = | streamwise and transverse coordinates, respectively, m |
Xd | = | downstream distance of a semicircular obstacle, m |
Xu | = | upstream distance of a semicircular obstacle, m |
Greek Symbols
α | = | thermal diffusivity, α = k/(ρCp) |
β | = | blockage ratio, β = D/H, dimensionless |
δ | = | size of the CV clustered around a semicircular obstacle, m |
ρ | = | density of the fluid, kg m−3 |
ν | = | kinematic viscosity, ν = μ/ρ, dimensionless |
μ | = | dynamic viscosity, Pa-s |
Subscripts
∞ | = | inlet condition |
w | = | surface of a semicircular obstacle |
c | = | critical value |
Additional information
Notes on contributors
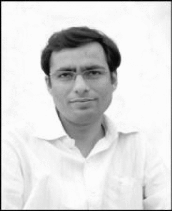
Anuj Kumar
Anuj Kumar did his M.Tech. in chemical engineering from the Department of Chemical Engineering at the Indian Institute of Technology Roorkee under the supervision of Dr. Dhiman. He received his B.Tech. degree in chemical engineering from HBTI Kanpur, India. His research interest includes CFD, fluid flow, and heat transfer phenomena around bluff bodies.
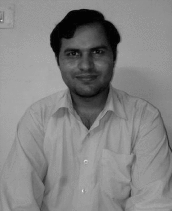
Amit Dhiman
Amit Dhiman holds B.Tech., M.Tech., and Ph.D. degrees in chemical engineering from the Institute of Engineering & Technology Lucknow, Indian Institute of Technology Roorkee, and Indian Institute of Technology Kanpur, respectively. He is currently an associate professor in the Department of Chemical Engineering at the Indian Institute of Technology Roorkee, India. He has also worked in Steel Authority of India Limited (SAIL) for about 6 months. He has published more than 50 research articles in scientific journals. His research interest includes CFD, non-Newtonian fluid flow and heat transfer, modeling and simulation, reaction engineering, and risk analysis. He is a member of the International Association of Engineers (IAENG).