Abstract
Heat transfer and pressure drop correlations for fully developed laminar Newtonian fluid flow in curved and coiled circular tubes are reviewed. Curved geometry is one of the passive heat transfer enhancement methods that fits several heat transfer applications, such as power production, chemical and food industries, electronics, environment engineering, and so on. Centrifugal force generates a pair or two pairs of cross-sectional secondary flow (based on the Dean number), which are known as the Dean vortices, and improves the overall heat transfer performance with an amplified peripheral Nusselt number variation. The main purpose of this review paper is to provide researchers with a comprehensive list of correlations and concepts that they may need during their research. The paper begins with an introduction to the governing equations and important dimensionless numbers for the flow in curved tubes. The correlations for developing flow in curved and coiled circular tubes are also presented. The main contribution of this study is reviewing the numerical and experimental correlations to calculate friction factor and Nusselt number in curved circular tubes. Nusselt number correlations are categorized based on the thermal boundary condition, as well as on the method. A Dean number range of 1 to 20,000 for the pressure drop correlations and 1 to 7000 for the heat transfer correlations and a Prandtl number range of 0.1 to 7,000 are covered with the reviewed correlations.
NOMENCLATURE
a | = | tube radius, m |
b | = | coil pitch, m |
Cp | = | specific heat capacity, J/kg-K |
Dh | = | hydraulic diameter, m |
De | = | Dean number |
Eu | = | Euler number |
f | = | Fanning friction factor |
Gz | = | Graetz number, |
Gr | = | Grashof number, |
He | = | helical coil number, |
h | = | convection heat transfer coefficient, W/m2-K |
k | = | thermal conductivity, W/m-K |
L | = | length of curved tubing, m |
L⋆ | = | dimensionless thermal length |
Nu | = | Nusselt number ≡ hDh/k |
P | = | tube perimeter m |
Pe | = | Peclet number ≡ UDh/α |
Pr | = | Prandtl number ≡ Cpμ/k |
q | = | heat flux, W/m2 |
R | = | radius of curvature, m |
Rc | = | effective radius of curvature, m |
1/R | = | curvature, 1/m |
Re | = | Reynolds number ≡ UDh/ν |
T | = | temperature, K |
U | = | average liquid velocity, m/s |
Greek Symbols
α | = | thermal diffusivity, m2/s |
β | = | volumetric thermal expansion coefficient, β = 1/T |
δ | = | boundary layer thickness, m |
η | = | torsion, |
μ | = | dynamic viscosity, N-s/m2 |
ρ | = | fluid density, kg/m3 |
φ | = | angle of tube curvature, rad, deg |
Subscripts
∞ | = | bulk |
ave | = | average |
bc | = | boundary condition |
c | = | curved |
crit | = | critical |
H1 | = | H1 boundary condition |
H2 | = | H2 boundary condition |
i | = | inlet |
m | = | mean |
o | = | outlet |
p | = | peripheral |
s | = | straight |
T | = | constant temperature |
th | = | thermal |
x | = | local |
w | = | wall |
Superscripts
⋆ | = | dimensionless |
= | mean value |
Additional information
Notes on contributors
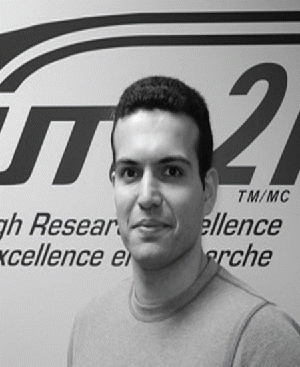
Mehdi Ghobadi
Mehdi Ghobadi is a postdoctoral researcher at C-CORE. He obtained his Ph.D. in mechanical engineering at Memorial University of Newfoundland (MUN) in 2014. In 2009, he completed his master of science at Iran University of Science and Technology. He investigated two-phase natural circulation systems in his master’s studies. He was involved with research related to passive techniques heat transfer enhancement with single-phase flow for his Ph.D. studies.
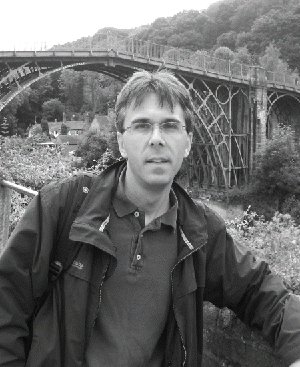
Yuri Stephan Muzychka
Yuri Stephan Muzychka is a professor in the Faculty of Engineering and Applied Science at Memorial University of Newfoundland, St. John’s, Newfoundland, Canada. He obtained his Ph.D. in mechanical engineering at the University of Waterloo. As a thermofluid analyst, his research is focused on the development of robust models for characterizing transport phenomena using fundamental theory. These models are validated using experimental and/or numerical results. He also undertakes fundamental research in microelectronics packaging, contact heat transfer, and thermal design/optimization of energy systems. He has published over 130 papers in refereed journals and international conference proceedings in these areas. He currently directs research in the Microfluidics and Multiphase Flow Research Laboratory at Memorial University of Newfoundland. This laboratory examines complex fluid dynamics and heat transfer problems in internal flows. These include transport in porous media, compact heat exchangers, two-phase flows, microchannel flows, noncontinuum flows, and non-Newtonian flows.