Abstract
Transient three-dimensional simulations are done for a phase-change material (PCM)-based heat sink subjected to constant heat flux of 1.59 kW/m2 with commercially available FLUENT software. Numerically obtained temperature–time histories are matched up with experimental results obtained earlier by our group to determine the overall heat transfer coefficient from the geometry that reconciles the differences between simulations and experiments. For a constant power level and fixed volumes of heat sink material (aluminum) and PCM (n-eicosane), simulations were done for 30 different geometric configurations to determine the time to reach complete melting. A feed-forward back-propagation neural network was then used in conjunction with a genetic algorithm to perform an exhaustive search and estimate the dimensions of the heat sink cavity for which the melt time and hence the thermal performance of the heat sink is maximum.
NOMENCLATURE
A | = | mushy zone constant, m2/s |
Abase | = | heater area, m2 |
ANN | = | Artificial neural networks |
b | = | breadth of the heat sink cavity, m |
C | = | effective specific heat, kJ/kg |
c | = | small number |
CFD | = | computational fluid dynamics |
CP | = | specific heat at constant pressure, kJ/kg-K |
D2 | = | total squared deviation, K2 |
DB2 | = | squared deviation of base temperature, K2 |
DP2 | = | squared deviation of PCM interior temperature, K2 |
DW2 | = | squared deviation of wall temperature, K2 |
f | = | liquid fraction |
G | = | generation count |
GA | = | genetic algorithm |
g | = | acceleration due to gravity, 9.81 m/s2 |
h | = | height of the heat sink cavity, m |
hAl | = | specific enthalpy of aluminum heat sink, kJ/kg |
hl | = | latent heat, kJ/kg |
hPCM | = | specific enthalpy of PCM, kJ/kg |
hs | = | sensible heat, kJ/kg |
i | = | iteration number |
k | = | thermal conductivity, W/m-K |
kAl | = | thermal conductivity of aluminum, W/m-K |
L | = | latent heat of fusion for PCM, kJ/kg |
l | = | length of the heat sink cavity, m |
MRE | = | mean relative error, s |
MSE | = | mean square error, s |
N | = | number of members in the population |
P | = | pressure, Pa |
PCM | = | phase-change material |
P–c | = | crossover probability |
P–m | = | mutation probability |
Q | = | power input, W |
q | = | heat flux, W/m2 |
R2 | = | absolute fraction of variance |
rand | = | random number between 0 and 1 |
Sb | = | buoyancy source term |
Smom | = | momentum source term |
T | = | temperature, K |
TB | = | base temperature of heat sink, K |
TBexp | = | experimentally measured base temperature, K |
TBnum | = | numerically observed base temperature, K |
Tm | = | melting temperature of PCM, K |
TP | = | PCM interior temperature, K |
TPexp | = | experimentally measured PCM interior temperature, K |
TPnum | = | numerically observed PCM interior temperature, K |
TW | = | average outer wall temperature of the heat sink, K |
TWexp | = | experimentally measured wall temperature, K |
TWnum | = | numerically observed wall temperature, K |
Tref | = | reference temperature, K |
t | = | time, s |
tANN | = | melting time derived from ANN modelling, s |
tmelt | = | time for complete melting, s |
tnum | = | melting time derived from numerical simulation, s |
U | = | overall heat transfer coefficient, W/m2 K |
u | = | velocity in x-direction, m/s |
V | = | velocity, m/s |
Vliquid | = | liquid velocity, m/s |
v | = | velocity in y-direction, m/s |
w | = | velocity in z-direction, m/s |
Greek Symbols
β | = | coefficient of thermal expansion, K−1 |
δ | = | half the temperature interval of the mushy zone, K |
λ | = | porosity |
μ | = | dynamic viscosity, kg/m = s |
ρ | = | density, kg/m3 |
Subscripts
ANN | = | artificial neural network |
Al | = | aluminum |
B | = | base |
Bexp | = | experimental base |
Bnum | = | numerical base |
b | = | buoyancy |
exp | = | experimental |
m | = | melting |
melt | = | melting |
mom | = | momentum |
num | = | numerical |
P | = | PCM interior |
Pexp | = | experimental PCM interior |
Pnum | = | numerical PCM interior |
ref | = | reference |
W | = | wall |
Wexp | = | experimental wall |
Wnum | = | numerical wall |
Additional information
Notes on contributors
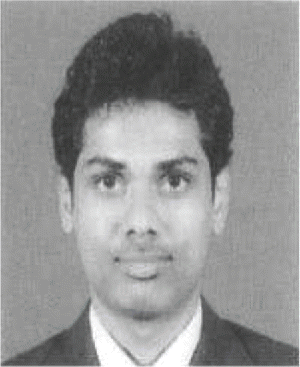
Ponnada Srivatsa
Ponnada Srivatsa is a thermal design engineer at General Electric Aviation, Bangalore, India. He graduated in mechanical engineering from National Institute of Technology, Warangal, India, in 2010, and obtained his M.Tech. from Indian Institute of Technology (IIT) Madras in 2013. His research interests include computational and experimental heat transfer, fluid dynamics, gas turbines, and optimization in thermal sciences.
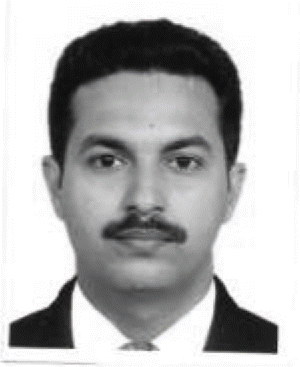
Rajesh Baby
Rajesh Baby is an associate professor in the Department of Mechanical Engineering at St. Joseph's College of Engineering and Technology, Palai, India. He graduated in mechanical engineering from M.A. College of Engineering, Kothamangalam, India in 2001. He obtained his M.Tech. in industrial refrigeration and cryogenic engineering from T.K.M College of Engineering, Kollam, India, in 2004 and his Ph.D. in mechanical engineering from Indian Institute of Technology Madras, Chennai, in 2013. His research interests include thermal management of electronic equipment, phase-change material-based composite heat sinks, cryocoolers, and heat transfer.
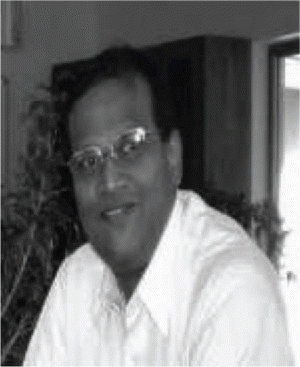
Chakravarthy Balaji
Chakravarthy Balaji is a professor in the Department of Mechanical Engineering at the Indian Institute of Technology (IIT) Madras. He graduated in mechanical engineering from Guindy Engineering College, Chennai (1990), India, and obtained his M.Tech. (1992) and Ph.D. (1995) both from IIT Madras. His research interests include computational and experimental heat transfer, optimization in thermal sciences, inverse heat transfer, satellite meteorology, and numerical weather prediction. He has around 140 journal publications to his credit and is an elected fellow of the Indian National Academy of Engineering.