Abstract
The fluid flow and heat transfer characteristics in a cross-corrugated triangular channel are studied under laminar forced flow and uniform wall temperature conditions. Both the local and the periodic mean values of friction factor and wall Nusselt numbers in the hydro and thermally developing entrance region are investigated. It is found that at higher Reynolds numbers, recirculations in the lower wall valleys are a dominant factor for flow and heat transfer, while at lower Reynolds numbers, parallel flows in the upper wall corrugation are the predominant factor. Compared with a parallel flat plates duct, the Nusselt numbers in a cross-corrugated triangular duct can be enhanced, and can be even higher at higher Reynolds numbers. The growth of steady recirculations and the concomitant periodic disruption and thinning of the boundary layer promote enhanced transport of heat as well as momentum. Effects of heat transfer enhancement are more obvious under higher Reynolds numbers. Two correlations are proposed to predict the periodic mean values of Nusselt numbers and friction factors for Reynolds numbers from 10 to 2000.
NOMENCLATURE
Aci | = | cross-sectional area at inlet or outlet of a cycle (m2) |
Acyc | = | surface area of the channel (m2) |
Bi | = | body force in the ith direction(Pa/m) |
cp | = | specific heat [J/(kg = K)] |
Dh | = | hydraulic diameter of the channel (m) |
f | = | friction factor |
fD | = | fully developed local or cyclic mean friction factor |
h | = | static enthalpy (kJ/kg) or heat transfer coefficient [W/(m2-K)] |
H | = | total enthalpy (J/kg) |
Lcyc | = | length of a cycle in flow direction (m) |
n | = | normal direction |
Nu | = | Nusselt number |
NuD | = | fully developed local or cyclic mean Nusselt number |
p | = | pressure (Pa) |
Pr | = | Prandtl number |
Re | = | Reynolds number |
t | = | time (s) |
T | = | temperature (K) |
ΔTm | = | logarithmic mean temperature difference between the wall and the fluid |
u | = | flow velocity (m/s) |
Uie | = | internal energy term (J/kg) |
Vcyc | = | volume of channel (m3) |
x, | = | y or z coordinates (m) |
y0 | = | pitch of the repeated segment of the duct (m) |
z0 | = | width of the repeated segment of the duct (m)</ul> |
Greek Symbols
β | = | included angle (º) |
ρ | = | fluid density (kg/m3) |
μ | = | molecular viscosity (N-s/m2) |
λ | = | thermal conductivity [W/(m-K)] |
σij | = | stress tensor (Pa) |
δij | = | Kroneker operator |
τ | = | aspect ratio (duct height/duct width) |
Subscripts
b | = | bulk |
i | = | inlet |
L | = | local |
m | = | mean |
o | = | outlet |
w | = | wall |
Superscript
* | = | dimensionless |
Additional information
Notes on contributors
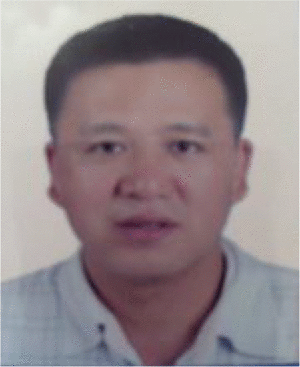
Zuoyi Chen
Zuoyi Chen is a senior research engineer and principal lecturer in the Chemistry Department, Guangdong University of Education, Guangzhou, China. Prior to joining the Chemistry Department, he received his Ph.D. in chemical engineering from the School of Chemistry and Chemical Engineering, South China University of Technology, China. His research interests include scientific computing and new materials processing. He has co-authored 21 papers in thermophysics journals and conference proceedings. He is currently working on mass and heat transfer on heat recovery ventilators.