ABSTRACT
A comparative study with respect to the scaling of heat transfer of Newtonian titania nanofluid with concentrations of 5.0 vol.% and 10.0 vol.% is undertaken. For that purpose, experiments in circular flow pipe with inserted twisted tape having a pitch to diameter ratio of nearly 6 under constant heat flux are carried out in a Reynolds number range from 300 to 1300. The experimental data are ordered according to three different scaling approaches based on Reynolds number, on Reynolds and Prandtl numbers, and based on Reynolds and Prandtl numbers and nanoparticle concentration. It is found that, despite its relevance with respect to the flow dynamics, the first scaling is not sufficient to capture the heat transfer features properly. While the second approach is already based on the necessary and sufficient similarity numbers, the third approach does not provide deeper insight into the flow physics. It is concluded that description of laminar nanofluid pipe flow with inserted twisted tape based on a combination of Reynolds and Prandtl numbers is sufficient because two-phase flow effects like Brownian and thermophoretic diffusion are of minor importance. This finding is in agreement with most recent experimental results for the entrance region of laminar flow in empty pipes.
Funding
This work was done under grant MF090026. The author thanks Bernd Lange for support with the experiments. Special thanks go to one of my students, Marco Gruschka, who helped with the experiments.
Nomenclature | ||
cp | = | heat capacity, J kg−1 K−1 |
di | = | inner diameter of test pipe, m |
dtc | = | diameter at which the thermocouples are positioned, m |
Ec | = | Eckert number, Ec = ub2 cp−1ΔT−1 |
H | = | pitch of twisted tape, m |
h | = | heat transfer coefficient, W m−2 K−1 |
k | = | thermal conductivity, W m−1 K−1 |
l | = | length of pipe, m |
= | mass flux of working fluid, kg s−1 | |
= | mass flux of nanoparticles, kg s−1 | |
Nux | = | local Nusselt number, Nux = h di k−1 |
= | average Nusselt number, | |
Δp | = | pressure loss, Pa |
Pr | = | Prandtl number, Pr = μ cp k−1 |
qw | = | wall heat flux, W m−2 |
Q | = | heat transfer rate, W |
RHRe | = | ratio of heat transfer coefficient at constant Reynolds number |
RHRePr | = | ratio of heat transfer coefficient at constant product of Reynolds and Prandtl number |
RHRePrφ | = | ratio of heat transfer coefficient at constant product of Reynolds and Prandtl number and concentration |
Re | = | Reynolds number, Re = ρ ub di μ−1 |
RNRe | = | ratio of Nusselt numbers at constant Reynolds number |
RNRePr | = | ratio of Nusselt number at constant product of Reynolds and Prandtl number |
RNRePrφ | = | ratio of Nusselt number at constant product of Reynolds and Prandtl number and concentration |
T | = | temperature, K |
Tin | = | inlet temperature, K |
Tbi | = | bulk flow temperature at position i, K |
Twci | = | temperature measured with thermocouple at position i, K |
Twi | = | temperature at inner pipe wall at position i, K |
ub | = | bulk velocity, m s−1 |
x | = | streamwise/axial coordinate, m |
X | = | nondimensional streamwise coordinate, x/di |
Y | = | nondimensional pitch of twisted tape flow, y/di |
Z | = | nondimensional thickness of twisted tape, z/di |
Greek symbols | ||
δ | = | thickness of tape, mm |
Δ | = | indicates relative differences of compared pairs, % |
ζ | = | normalized pressure loss coefficient |
η1 | = | thermal performance parameter, (Nunf/Nuref)/(λref/λnf) |
η3 | = | thermal performance parameter, (Nunf/Nuref)/(λref/λnf)1/3 |
λ | = | friction factor, λ = 2Δp ρ−1 ub−2 |
μ | = | dynamic viscosity, kg m−1 s−1 |
ρ | = | density, kg m−3 |
φ | = | nondimensionalized mass concentration of nanoparticles, — |
φ | = | volumetric concentration of nanoparticles, % |
Subscripts | ||
b | = | bulk |
co | = | copper |
exp | = | experimental |
i | = | inlet |
nf | = | nanofluid |
np | = | nanoparticles |
ref | = | reference case (pipe without insert) |
w | = | wall |
x | = | local value |
00 | = | pure deionized water |
05 | = | TiO2/deionized water 5.0 vol.% |
10 | = | TiO2/deionized water 10.0 vol.% |
Superscripts | ||
αj | = | power of dimensions appearing in similarity numbers |
m, n | = | powers appearing in the RePr scaling |
p, q, r | = | powers appearing in the RePrφ scaling |
Additional information
Notes on contributors
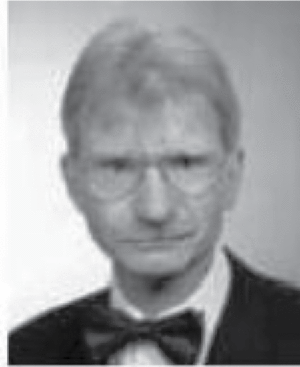
Matthias H. Buschmann
Matthias H. Buschmann is a senior researcher at the Institute für Luft- und Kältetechnik Dresden (ILK) and senior lecturer for vehicle aerodynamics at University of Dresden, Saxony, Germany. He is a theoretician in fluid mechanics but also highly interested in heat transfer experiments. He received his Ph.D. and habilitation at University of Dresden, where he worked as a research assistant before joining ILK about 11 years ago. He studied at the universities of Dresden (Germany), Karlsruhe (Germany), and Melbourne (Australia). His research interests include phase-change heat transfer, multiphase heat and mass transfer, nanofluid flow and heat transfer, and wall-bounded turbulence. He has contributed to more than 30 full papers and numerous conference papers. He is currently working on the influence of fractal turbulence on condensation and instantaneous phenomena occurring in thermosyphons operated with nanofluids.