ABSTRACT
A one-dimensional thermo-electrical mathematical model describing the heating and cooling of thin Ni-Cr20% wires is presented. The model is applied for wires in a free air environment and to wires placed in small circular cavities formed by expanded polystyrene material. The basis of the model is a semicoupled solution of the heat conduction equation and the electrical diffusion equation in a one-dimensional (1-D) control volume finite-difference framework. A study on the available natural convection correlations for thin metal wires for Rayleigh numbers in the range of 10−3–101 is carried out in order to select an appropriate heat transfer coefficient for the time-dependent heating and cooling of a wire. The model is tested against experimental data and is found to be in a good agreement with previous investigations. Based on the findings, expressions for the heat transfer coefficient of a hot wire inside a small circular cavity are suggested.
Nomenclature
Ac | = | area of wire circumference, m2 |
As | = | cross-sectional area, m2 |
ΔAci | = | outer surface area of cell with index I, m2 |
cp(T) | = | temperature dependent specific heat capacity at constant pressure, J/kg-K |
Dhole | = | diameter of circular hole, m |
Dw | = | diameter of wire, m |
E | = | electric field intensity, V/m |
EPS | = | expanded polystyrene |
Error | = | error, or numerical difference between experimental and simulated results |
g | = | gravitational acceleration, m/s2 |
Gr | = | Grashof number |
h | = | total heat transfer coefficient, W/m2-K |
hnc | = | natural convective heat transfer coefficient, W/m2-K |
hrad | = | radiation heat transfer coefficient, W/m2-K |
HTC | = | heat transfer coefficient |
IR | = | infrared |
k(T) | = | temperature-dependent thermal conductivity, W/m-K |
kf | = | thermal conductivity of air at the film temperature, W/m-K |
L | = | wire length, m |
Lo | = | Lorentz number, W-Ω/K2 |
N | = | number of discretization cells |
Nu | = | Nusselt number |
Num | = | Nusselt number mean value |
Pr | = | Prandtl number |
= | volumetric specific energy generated due to electric resistance heating, W/m3 | |
Qe | = | energy generated due to electric resistance heating, W |
= | volumetric specific energy lost to the surroundings, W/m3 | |
Qloss | = | energy lost to the surroundings, W |
R | = | electrical resistance, Ω |
Ra | = | Rayleigh number |
T | = | temperature of the wire, C |
t | = | time, s |
V | = | voltage, V |
V1 | = | applied voltage at left boundary, V |
Vm | = | wire volume, m3 |
Variation | = | percent coefficient of variation, or 100 times the standard deviation divided by the mean value |
x | = | coordinate, m |
Greek symbols
β | = | volumetric thermal expansion coefficient for air, 1/K |
Δ | = | difference for one cell |
ϵ | = | emissivity of wire |
νf | = | kinematic viscosity of the fluid evaluated at film temperature, m2/s |
ρ | = | density, kg/m3 |
σ(T) | = | temperature-dependent electrical conductivity, 1/Ω-m |
σNu | = | standard deviation |
Ω | = | Stefan–Boltzmann constant, W/m2-K4 |
Subscripts
air | = | property of the air |
exp | = | experimental |
i | = | cell number |
initial | = | initial condition |
f | = | evaluated at film temperature |
new | = | new time step |
old | = | old time step |
sim | = | simulated |
w | = | wire |
Superscripts | ||
t | = | current time |
t + Δt | = | time after one time step |
Funding
The authors thank Odico Formworks Robotics for the productive and long-term cooperation. Special thanks to Sønnik Clausen from the DTU Chemical Engineering, who helped us with the experimental sensors and data acquisition. This work was supported by Innovationsfonden project number 76421, which is highly acknowledged.
Additional information
Notes on contributors
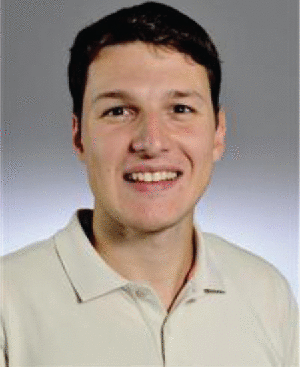
Kiril P. Petkov
Kiril P. Petkov is a Ph.D. candidate at the Technical University of Denmark. His research is in the field of numerical modeling of cutting processes and simulation of heat transfer in solids. He holds an M.Sc degree in mechatronics with a specialization in mathematical modeling from the University of Southern Denmark (2008).
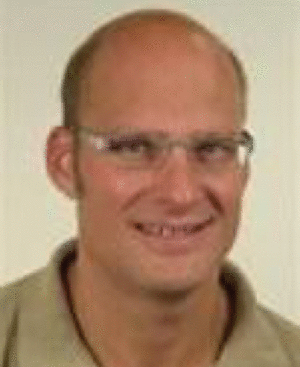
Jesper H. Hattel
Jesper H. Hattel is a professor at the Technical University of Denmark with expertise in process modelling of manufacturing processes, such as casting, molding, and welding, as well as modeling of cross-disciplinary and multiphysics CFD and finite-element method (FEM) problems. He is an author of more than 200 peer-reviewed publications, 100 article journals, and 19 books. He received his M.Sc. and Ph.D. from the Technical University of Denmark.