ABSTRACT
Triangular ducts fitted with various kinds of delta-winglet type vortex generators (VGs) are commonly used to achieve compactness and heat transfer enhancement in many industries. Successive locations of VGs on the inner surfaces of the ducts can be arranged in Common Flow Up (CFU) and Common Flow Down (CFD) orientations. In the present numerical study simultaneous effects of orientation and streamwise distance between VGs on triangular fin performance is carried out considering both global and local flow and heat transfer fields. With the configurations considered in this study, a CFD–CFU orientation and a nondimensional streamwise distance of 0.5 is determined as the best configuration. “RNG k-ϵ” turbulence model with “Enhanced wall treatment” option is determined as the best turbulence model to predict the flow fields inside the triangular duct with built-in VGs, for Reynolds number of 5000.
Acknowledgments
The present authors gratefully acknowledge the support of TUBITAK (Technological and Scientific Council of Turkey, Grant No: 111M726) and Office of Scientific Research Projects of Mersin University, (Grant No: BAP-FBE-MEB (ES) 2012-3YL) for funding this study.
Nomenclature
A | = | area (m2) |
Ac | = | cross-section area of triangular duct (m2) |
B | = | width of duct (m) |
cp | = | specific heat capacity (kJ kg−1 K−1) |
CFD | = | common flow down |
CFU | = | common flow up |
d | = | distance between VGs in z-direction (m) |
D | = | hydraulic diameter of triangular duct (m) |
f | = | friction factor |
h | = | convective heat transfer (W m−2 K−1) |
H | = | heigth of triangular duct (m) |
Hy | = | transverse distance between the duct base and the closest edge of the either VG (m) |
k | = | thermal conductivity (W m−1 K−1) |
L | = | length of triangular duct (m) |
Lw | = | maximum length of VG (m) |
Ly | = | length of VG in y-coordinate (m) |
Lz | = | length of VG in z-coordinate (m) |
= | mass flow rate (kg s−1) | |
Nu | = | Nusselt number |
p | = | perimeter of triangular duct (m) |
P | = | pressure (Pa) |
ΔP | = | pressure differences between inlet and outlet (Pa) |
PIV | = | particle image velocimeter |
Re | = | Reynolds number |
T | = | temperature (K) |
THP | = | thermohydraulic performance |
TKE | = | turbulence kinetic energy (J kg−1) |
u,v,w | = | X,Y,Z components of velocity (m s−1) |
y+ | = | nondimensional wall distance |
VGs | = | vortex generators |
W | = | inlet velocity (m s−1) |
X, Y, Z | = | Cartesian coordinates (m) |
Greek symbols
ρ | = | density (kg m−3) |
ϵ | = | turbulence dissipation (m2/s3) |
κ | = | turbulence kinetic energy (m2/s2) |
ω | = | specific turbulence dissipation rate (1/s) |
Subscripts
ave | = | average |
HT | = | heat transfer surfaces |
HW | = | hot walls |
in | = | inlet |
out | = | outlet |
s | = | smooth duct |
VG | = | vortex generators |
w | = | wall |
Additional information
Notes on contributors
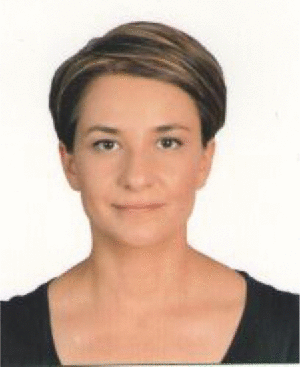
Azize Akcayoglu
Azize Akcayoglu is an associate professor in Automotive Engineering Department at Mersin University, Turkey. She is now with the School of Engineering at Penn State Behrend, as a lecturer. She received her B.Sc., M.Sc., and Ph.D. degrees in mechanical engineering. Her research focuses on experimental fluid mechanics, computational fluid dynamics and heat transfer specializing on laminar and turbulent steady and unsteady separated flows and convective heat transfer. Past research activities include greenhouse heating via geothermal energy, design and production of solar-powered race cars, numerical modeling of dispersion of dense gases in turbulent atmospheric boundary layer. Current research projects include performance improvement of heat exchangers and energy efficiency in gas turbines.
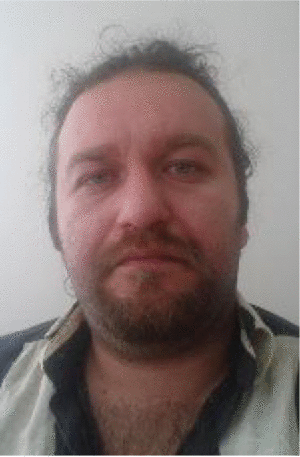
Celal Nazli
Celal Nazli is a research assistant in mechanical engineering, Kastamonu University, Turkey. He was previously working as a project engineer in Computational Fluid Dynamics Laboratory in Faculty of Technology, Mersin University. He received his B.Sc. in mechanical engineering from Gaziantep University, Turkey. He is currently working on computational fluid dynamics and heat transfer applications in gas turbines and heat exchangers.