ABSTRACT
Flow boiling in microchannels promises high heat transfer due to the combined effect of latent heat of vaporization and forced convection in confined spaces. However, flow boiling based miniaturized thermal management devices are limited due to instability induced dryout. While several efforts have been made to delay instabilities via advanced surface modification techniques, there is a need to expand the scope of applications by developing low-cost and scalable fabrication technologies for commonly used heat exchanger materials. In this paper, we use a facile and self-limiting chemical oxidation technique for fabricating sharp needle-like superhydrophilic CuO nanostructures within six parallel 500 × 250 µm2 microchannels spread uniformly over a 1 × 1 cm2 area in a copper heat sink. We demonstrate heat transfer enhancement with nanostructured microchannels (NSM) without any appreciable change either in the average pressure drop or the fluctuations in comparison to baseline plain wall microchannels (PWM). Analysis of the high-speed images was performed to attribute the enhancement with NSM to the presence of a capillarity-fed thin-film evaporation regime, which otherwise was absent in PWM. We believe that these results are encouraging and suggest that the heat sink geometry can be optimized to investigate the true potential of nanostructured microchannels.
Nomenclature
A | = | Foot Print Area, cm2 |
CAS | = | Chemical Abstracts Service |
DI | = | Deionized |
FFT | = | Fast Fourier Transform |
f | = | Frequency, Hz |
H | = | Height of Microchannel, µm |
h | = | Heat Transfer Coefficient, W/m2K |
I | = | Current, A |
MAE | = | Mean Absolute Error |
NSM | = | Nanostructured Microchannel |
P | = | Pressure, kPa |
PWM | = | Plain Wall Microchannel |
ΔP | = | Pressure Drop, kPa |
= | Mass Flux, kg/m2s | |
Qin | = | Input Power, W |
Qloss | = | Heat Loss, W |
q″ | = | Effective Heat Flux, W/cm2 |
Re | = | Reynolds Number |
SEM | = | Scanning Electron Microscope |
T | = | Temperature, °C |
ΔT | = | Temperature Difference, °C |
t | = | Time, s |
V | = | Voltage, V |
W | = | Width of Microchannel, µm |
Greek symbols
σ | = | Standard Deviation |
ϵ | = | Characteristic Oxide Thickness, µm |
θ | = | Contact Angle, ° |
Subscripts
avg | = | Average |
f | = | Friction |
in | = | Inlet |
m | = | Momentum |
out | = | Outlet |
sim | = | Simulation |
sup | = | Superheat |
sur | = | Surface |
TC | = | Thermocouple |
w | = | Wetting |
Additional information
Funding
Notes on contributors
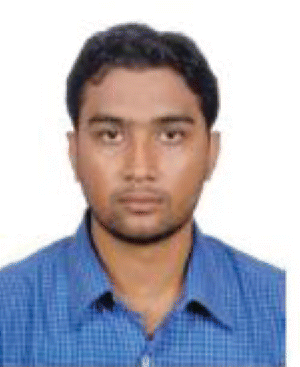
Durga Prasad Ghosh
Durga Prasad Ghosh is a Ph.D. student at the Indian Institute of Technology Patna, under the supervision of Dr. Rishi Raj. He graduated from Gandhi Institute of Engineering and Technology with a B.Tech. in Mechanical Engineering in 2011. He completed his M.Tech. in Thermal Engineering from KIIT University in 2014. His Ph.D. research is focused on fabrication of scalable and cost-effective nanostructures inside microchannels for high heat flux applications.
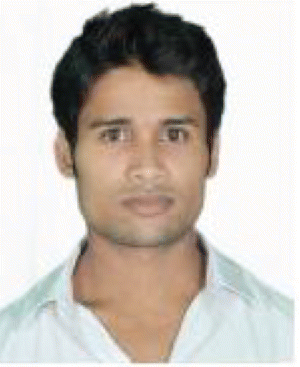
Deepak Sharma
Deepak Sharma is an M.Tech. student at the Indian Institute of Technology Patna, under the supervision of Dr. Rishi Raj. He received B.Tech. in Mechanical Engineering from Maharshi Dayanand University, Rohtak, Haryana. He is interested in thermal and fluid transport, surface engineering, and phase-change phenomena during heat transfer.
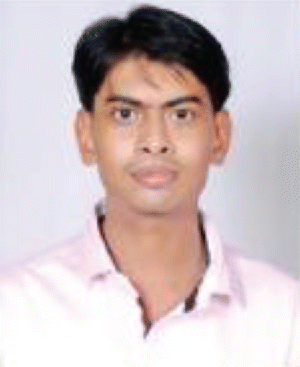
Diptimoy Mohanty
Diptimoy Mohanty is currently working as an Assistant Manager (MAT) in Dredging Corporation of India Limited. He completed B.Tech. in Mechanical Engineering from Indira Gandhi Institute of Technology, Sarang in 2014. He was on a Junior Research Fellowship at the Indian Institute of Technology Bombay under the guidance of Dr. Sandip Kumar Saha.
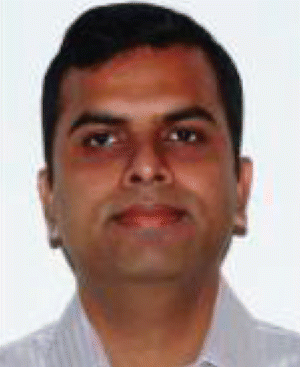
Sandip K. Saha
Sandip Kumar Saha is an Assistant Professor in the Department of Mechanical Engineering at the Indian Institute of Technology Bombay, India. He received Bachelors of Engineering degree in Mechanical Engineering from Jadavpur University, Kolkata, and his Masters and Ph.D. degrees in the same field from the Indian Institute of Science (IISc), Bangalore, India. His research interests include thermal management of electronics, thermal storage, heat transfer, and computational fluid dynamics.
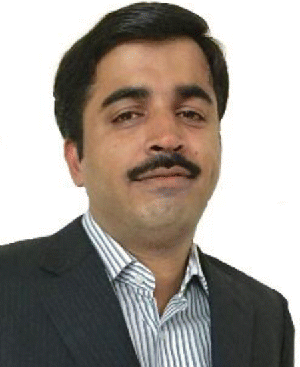
Rishi Raj
Rishi Raj is an Assistant Professor at Indian Institute of Technology Patna, India. He graduated from Indian Institute of Technology Guwahati with a B.Tech. in Mechanical Engineering in 2006. He received his Ph.D. in Mechanical Engineering from University of Maryland in 2010. Prior to joining Indian Institute of Technology Patna in 2013, he worked as Postdoctoral Associate at the Device Research Laboratory, Massachusetts Institute of Technology. His research interests include phase change heat transfer, micro-nano-scale transport, energy, surface science, and microgravity.