ABSTRACT
The present research is to develop a homogenous mathematical model to simulate capillary tube-suction line heat exchanger (CT-SL HX) based on the fundamentals of conservations of mass, momentum and energy with comprehensive experimental result validations. The computer model is fully validated by 72 experimental data with error bands of ±15%, ±2°C and ±35% on the mass flow rate prediction, the suction pipe outlet temperature, and the heat exchange estimation respectively. The results suggest that the internal diameter of the capillary tube, and the heat-transfer length of the CT-SL HX have demonstrated an apparent impact on the capillary tube outlet conditions and heat transfer across the segment.
Acknowledgements
The authors would like to acknowledge the financial assistance from the Ministry of Higher Education (MOHE), Malaysia, for providing the UMRG Fund RG030/15AET for research work to be conducted at the University of Malaya, Kuala Lumpur. Thanks are extended to the University of Malaya PPP Grants P0019-2009 C and PG111-2012B for the financial assistance to the co-author, Ms. H.H. Poh, for conducting the research work at HVAC&R Lab at the Department of Mechanical Engineering, University of Malaya. Special thanks are also extended to Dr. W.M. Chin, Senior R&D Manager of Daikin R&D (Malaysia), for providing technical help during the critical period of the research work.
Nomenclature | ||
A | = | cross section area, m2 |
a | = | acceleration, ms−2 |
Cc | = | coefficient of the contraction |
CV | = | control volume |
CT | = | capillary tube |
CT-SL HX | = | capillary tube suction line heat exchanger |
D | = | diameter, mm |
d | = | tube internal diameter, m |
dP | = | pressure difference, kPa or MPa |
dq | = | differential change in heat transfer, kW |
dt | = | time difference, s |
dV | = | velocity difference, ms−1 |
dz | = | step size for length |
Ė | = | energy, kJ/s |
f | = | friction factor |
F | = | force, N |
F1 | = | friction force on the wall, N |
F2 | = | force due to pressure difference, N |
F3 | = | force due to elevation, N |
G | = | mass flux, kgs−1m−2 |
g | = | gravity force, 9.81 ms−2 |
h | = | enthalpy, kJ/kg |
ID | = | internal diameter, m |
k | = | thermal conductivity, W/m.K |
L | = | length, mm or m |
m | = | mass, kg |
= | mass flow rate, kgs−1 or kg/hr | |
NACT | = | non-adiabatic capillary tube |
Nu | = | Nusselt number |
OD | = | outer diameter, m |
P | = | pressure, kPa or MPa |
ΔP | = | difference in pressure, kPa or MPa |
Pr | = | Prandtl number |
R1, R2, … | = | thermal resistance, kW−1 |
Re | = | Reynolds number |
s | = | Entropy, kJkg−1K−1 |
SC | = | sudden contraction |
T | = | temperature, °C |
U | = | overall heat transfer coefficient based on area, W/m2.K |
v | = | specific volume, m3kg−1 |
V | = | velocity, ms−1 |
w | = | width of solder joint, m |
x | = | vapor quality |
Greek Symbols | ||
θ | = | inclination angle of capillary tube suction line heat exchanger, degree |
φ | = | two phase friction factor multiplier |
ϵ | = | relative roughness of the tube |
µ | = | viscosity, Pa.s |
ρ | = | density, kgm−3 |
σ | = | ratio of A1 to A2 |
τ | = | shear stress, kPa |
δ | = | solder joint thickness, m |
Subscripts | ||
1 | = | inlet of control volume |
2 | = | exit of control volume |
1φ | = | single-phase |
2φ | = | two-phase |
brazed | = | brazing material |
c | = | capillary tube |
contract | = | contraction |
Concentric | = | concentric configuration of CT-SL HX |
des | = | design |
enlarge | = | enlargement |
en | = | entrance |
ext | = | exit |
f | = | fluid |
g | = | gas |
hx | = | heat exchange |
i | = | inner |
Lateral | = | lateral configuration of CT-SL HX |
lo | = | local |
m | = | average |
o | = | outer |
out | = | outlet |
s | = | suction pipe |
sat | = | saturated condition |
sp | = | single-phase |
tol | = | tolerance |
w | = | wall |
Additional information
Funding
Notes on contributors
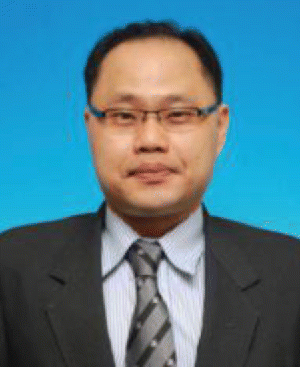
Yat Yau
Yat Huang Yau obtained his PhD in Mechanical Engineering in 2005 from the University of Canterbury, Christchurch, New Zealand. He is a Professor in Mechanical Engineering and Principal M&E consulting engineer at University of Malaya Consulting Unit (UPUM), University of Malaya, Kuala Lumpur, Malaysia. His major interest areas are: Air-Conditioning and Refrigeration, M&E Engineering; HVAC&R Engineering; Thermal Systems Simulation using TRNSYS; Energy Savings in Buildings; IEQ Engineering; Green Building Design, FEA, CAD & CAM Engineering.