ABSTRACT
The influence of reducing dimensions to microscale on the performance parameters of parallel flow tubular micro heat exchanger is numerically analyzed considering the thermophysical property variation effect. Also, the improvement in convective heat transfer coefficient, at a given temperature, with the decrease in dimensions to microscale is investigated. In the micro heat exchanger, conventional method fails to give accurate performance analysis due to significant property variation. So, a new temperature difference, i.e. mean temperature difference correlation considering the property variation effect is derived. Operating conditions and geometric parameters are varied, keeping the inlet temperature of the both fluids and inlet velocity of the cold fluid fixed. The following performance parameters are evaluated: effectiveness, volumetric heat transfer coefficient, mean temperature difference, and log mean temperature difference. The reliability of the new mean temperature difference method is checked by calculating the percentage deviation between mean temperature difference and log mean temperature difference value for macroscale to microscale heat transfer. The results show that percentage deviation is maximum at microscale.
Nomenclature
A | = | surface area, m2 |
AMTD | = | arithmetic mean temperature difference, °C, K |
Bi | = | Biot number |
C | = | heat capacity rate, W/K |
Cp | = | specific heat at constant pressure, J/kg-K |
D | = | diameter, m |
dann | = | annular spacing between two coaxial cylinders in heat exchanger, m |
EMTD | = | effective mean temperature difference, °C, K |
F | = | LMTD correction factor, m2°C /W |
hcv | = | convective heat transfer coefficient, W/m2-K |
hv | = | volumetric heat transfer coefficient, W/m3-K |
k | = | thermal conductivity, W/m-K |
L | = | length of heat exchanger, m |
LMTD | = | log mean temperature difference, °C, K |
= | mass flow rate, kg/s | |
MTD | = | mean temperature difference, °C, K |
MWT | = | measuring wall temperature |
N | = | number of axial elements in which heat exchanger is discretized |
Nu | = | Nusselt number, dimensionless |
q | = | heat flow rate, W |
R | = | radius of pipe, m |
T | = | temperature, °C, K |
t | = | thickness of inner pipe (Equation1 |
T0 | = | stagnation temperature, °C, K |
u | = | axial flow velocity, m/s |
U | = | overall heat transfer coefficient, W/m2 K |
V | = | volume of heat exchanger, m3 |
z | = | axial flow direction |
Greek symbols
Δhcv | = | change in convective heat transfer coefficient, W/m2-K |
ΔT | = | temperature difference between hot and cold fluid, °C, K |
ΔTAM | = | arithmetic mean temperature difference (AMTD), °C, K |
ΔTlm | = | logarithmic mean temperature difference (LMTD), °C, K |
Δθ | = | change in temperature difference, °C, K |
Δz | = | width of discretized element, m |
%Δ(ΔTlm – θm) | = | percentage deviation between LMTD and MTD, dimensionless |
ρ | = | density, kg/m3 |
η | = | effectiveness |
θ | = | temperature difference between hot and cold fluid, °C, K |
θm | = | new mean temperature difference (MTD), °C, K |
Subscripts
c | = | cold fluid side |
cf | = | convected to fluid |
cv | = | convective |
ex | = | exit |
fm | = | bulk mean fluid value |
h | = | hot fluid side |
hyd | = | hydraulic diameter |
i | = | inner surface |
in | = | inlet |
k | = | kth element of discretized heat exchanger layout |
m | = | mean value over cross-section |
max | = | maximum value |
min | = | minimum value |
o | = | outer surface |
opt | = | optimum value |
true | = | true value considering the variation effect |
w | = | wall |
x | = | axial distance along the length of heat exchanger, m |
1 | = | inner pipe |
2 | = | outer pipe |
Superscript
− | = | average / mean data |
Acknowledgment
The authors would like to thank Dr. S. V. Prabhu, for proofreading of the manuscript.
Additional information
Notes on contributors
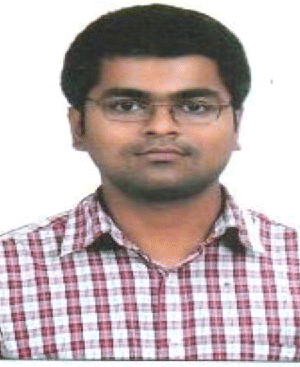
Ankush D. Tharkar
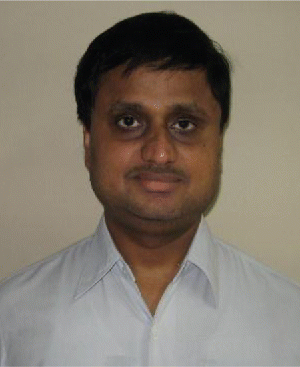
Shripad P. Mahulikar
Shripad P. Mahulikar is a professor in the Department of Aerospace Engineering, Indian Institute of Technology Bombay. He obtained his B.Tech. and integrated M.Tech. (by research) in Aerospace Engineering from IIT-B in 1990 and 1992, respectively, and earned his Ph.D. from Nanyang Technological University, Singapore, in 1999. He received the A. von Humboldt Fellowship in the Federal Republic of Germany (2003, 2007, 2009), Outstanding Reviewer Award from the ASME Journal of Heat Transfer in 2007, and DFG-Mercator chair Professorship in Hamburg University of Technology, Federal Republic of Germany (December 2011 onward).