ABSTRACT
The unsteady behavior of fluid flow such as pressure variation and fluctuation in a hydraulic turbine may lead to operational instability. Such dynamic behaviors effect the performance of rotating machines, which may reduce life span and even have impact on the overall safety of the turbine. The objectives of this study are to analyze the flow characteristics and to undertake a transient Fast Fourier Transform (FFT) analysis of a model turbine to investigate the stability of operational conditions. Flow analysis was conducted by changing the number of revolutions to 100, 200, 300, and 350 rpm. Reynolds-averaged Navier–Stokes equations were discretized by the finite volume method and a two equations shear stress transport model was used to account for the three dimensionality of unsteady flows. FFT analysis was performed by monitoring dynamic pressure fluctuation on the rotor and casing. Results revealed that as the number of revolutions increased, the flow gradually became more stable as it approached the rated rotation speed of 350 rpm. Also an experiment was conducted to verify the numerical performance and a good tendency of the results was achieved.
Nomenclature
CFD | = | Computational Fluid Dynamics |
FFT | = | Fast Fourier Transformation |
G | = | vibration amplitude, m/s2 |
g | = | acceleration due to gravity, m/s2 |
H | = | head, m |
k | = | turbulence kinetic energy, m2/s2 |
Ls | = | shaft power, kW |
Lw | = | water power, kW |
p | = | pressure, Pa |
Pk | = | production rate of turbulence |
Pkb, Pωb | = | shear production of turbulence |
Q | = | volume flow rate, m3/s |
S | = | source term |
SST | = | shear stress transport |
T | = | torque, N·m |
t | = | time, sec |
ui | = | velocity vector, m/s |
v | = | velocity of fluid, m/s |
x | = | component of position vector, m |
z | = | elevation of water level, m |
Greek symbols
ρ | = | density, kg/m3 |
η | = | efficiency |
ω | = | angular velocity, rad/s |
μ | = | viscosity, Pa·s |
μt | = | turbulent viscosity, Pa·s |
τij | = | stress tensor, N/m2 |
α, β, β′, σk, σω | = | Closure coefficients |
Subscripts
i,j,k | = | tensor indices |
1, 2 | = | inlet, outlet |
Acknowledgement
This research was supported by the Korea Institute of Energy Technology Evaluation and Planning (KETEP). The grant number is 20153030071530 for the Promotion of Science.
Additional information
Notes on contributors
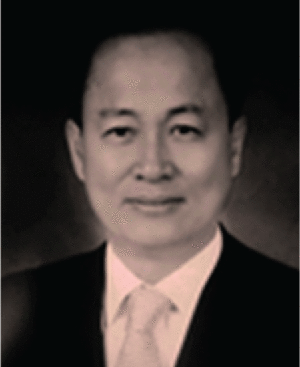
Nohyun Park
Nohyun Park is the Director of Kumsung E&C Co., Ltd. He is currently a Ph.D. student at Soongsil University, under the supervision of Prof. Sang-Ho Suh. He received his M.Sc degree in fluid mechanics in 2013 from Chungnam National University, Daejeon, South Korea. He is a member of Korean Society for new and renewable energy, member of hydraulic energy, and in-charge of hydraulic R&D, KETEP. He is currently working on turbo machinery design and development.
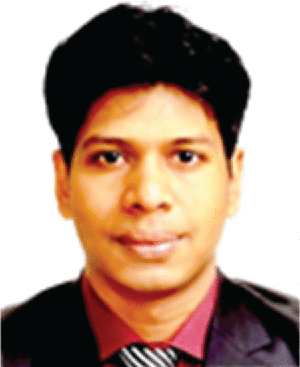
Md Rakibuzzaman
Md Rakibuzzaman is a research engineer at Soongsil University, Seoul, Korea. He received his B.Sc. degree in Mechanical Engineering in 2009 from Rajshahi University of Engineering and Technology, Bangladesh and M.Sc. degree in Mechanical Engineering in 2015 from Soongsil University, Seoul, South Korea. He is currently a Ph.D. Student at Soongsil University under the supervision of Prof. Sang-Ho Suh. His research interests include energy index, cavitation mechanism, and optimization in turbo machinery.
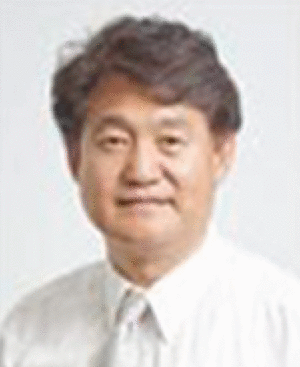
Sang-Ho Suh
Sang-Ho Suh is a Professor of Fluid Engineering at Soongsil University, Seoul, South Korea. He received his M.Sc. degree from Soongsil University in 1984 and his Ph.D. degree from Stuttgart University in 1989. He has been teaching at Soongsil University since 1990. He has been the head of the Mechanical Engineering Department of Soongsil University for three years and his research contributions were in the field of fluid machinery and bio-fluid engineering. He is currently working on biomedical engineering research which includes biofluid circulations (blood, urine and air flows in arteries, ureter, upper airway), development of biomedical devices, and industrial application research related to the performance evaluation of pumps and hydraulic turbines, development of automatic waste collecting system, and pneumatic capsule pipeline.