ABSTRACT
The paper presents thermal and flow analyses of the boiling process of R507, R410 and R407 C refrigerants inside vertical tubes (21 mm) with coiled-wire inserts and various coil diameters (20; 20.5 mm), coil pitches (26; 44 mm) and wire diameters (1.5; 2 mm). The study differs from other publications as regards the conditions under which the experiment was conducted. It focuses on the boiling process in two long vertical tube sections (2 m), paired in an in-line arrangement. The study was conducted within a moderate range of mass flux densities 80–240 kgm−2s−1 and at low heat flux densities 5–11 kWm−2, corresponding to the operating conditions of air coolers. The study examined the influence of vapour quality, mass flux density, geometrical parameters of the inserts and the impact of temperature glide on heat transfer coefficient and flow resistance increases as compared with a plain tube. The obtained increase ratios of heat transfer coefficients amounted to 1.1-1.7 for an azeotropic agent and to 1.1-1.3 for zeotropic agents, with the relative increase in flow resistances amounting to 1.8-4.5. New equations are proposed in the paper for the calculation of heat transfer coefficient and flow resistance values for boiling inside vertical tubes with spiral inserts.
Acknowledgment
The study was performed as part of research project N N512 458040, funded by the Polish National Science Centre.
Nomenclature
A | = | heat transfer surface, m2 |
Ai | = | constants in Equationequation (11) |
AV | = | surface area limiting the volume V, m2 |
Aw | = | inner tube surface area (copper tube), m2 |
Bi | = | constants in Equationequation (13) |
Bo | = | boiling number, |
Cs | = | spring rigidity, Nm−1 |
d | = | diameter, m |
dh | = | hydraulic diameter, m |
do | = | outer diameter of the copper tube, inner diameter of the aluminium tube, m |
do1 | = | outer diameter of the aluminium tube, m |
dp | = | outer coil diameter, diameter of the full insert, m |
ds | = | diameter of the spring wire, m |
E | = | thermal power referred to discharge power |
f | = | friction factor |
fi | = | function in Equationequations (11) |
= | refrigerant mass flux density, kgm−2s−1 | |
h | = | heat transfer coefficient, Wm−2K−1 |
i | = | specific enthalpy, Jkg−1 |
k | = | thermal conductivity, Wm−1K−1 |
L | = | length of pipe, m |
Ls | = | length of spring wire, m |
Lt | = | length of the thermal measurement section, m |
= | mass flux, kgs−1 | |
Nu | = | Nusselt number, |
p | = | pressure, Pa |
r | = | specific evaporation heat, Jkg−1 |
Re | = | Reynolds number, |
= | heat flux density, kWm−2 | |
= | thermal efficiency, W | |
= | compressor engine power, W | |
s | = | coil pitch, m |
T | = | temperature, °C |
Twallo,i - | = | temperature of the outer, inner tube wall, °C |
V | = | volume of refrigerant in a tube with an insert, m3 |
= | volume flux, m3s−1 | |
w | = | velocity, ms−1 |
x | = | vapour quality, kgkg−1 |
xd | = | vapour quality downstream of the electronic expansion valve, kgkg−1 |
Xtt | = | Lockhart-Martinelli parameter, |
= | –temperature difference in the definition of the heat transfer coefficient for the refrigerant, K | |
ΔTR = TR, out − TR, in | = | –temperature glide of the refrigerant, K |
Greek symbols
δ | = | relative error (%) |
Δ | = | increment |
ϵh | = | heat transfer coefficient increase ratio |
ϵΔp | = | flow resistance increase ratio |
ϵh−Δp | = | product of the mean values of |
ϵNu−f | = | overall enhancement efficiency, ϵNu-f = (Nu/Nupt)/(f/fpt)1/3 |
μ | = | dynamic viscosity, Pas |
ρ | = | density, kgm−3 |
Subscripts
Al | = | aluminium |
Ch | = | Chisholm |
con1 | = | condenser |
con2 | = | subcooler |
Cu | = | copper |
evap | = | concerns the balance of heat absorbed by the refrigerant in the evaporator |
exp | = | measured value |
g | = | gas phase |
GW | = | Gungor-Winterton |
Heat | = | heater |
hg | = | after the compressor (hot gas) |
i | = | inner |
in | = | inlet |
l | = | liquid phase |
m | = | mean value |
max | = | maximum value |
o | = | concerns the evaporation process in the test section, external |
out | = | outlet |
pt | = | plain tube |
R | = | refrigerant (or water) |
sc | = | subcooling |
sv | = | superheating |
Superscript
─ | = | mean value |
Additional information
Funding
Notes on contributors
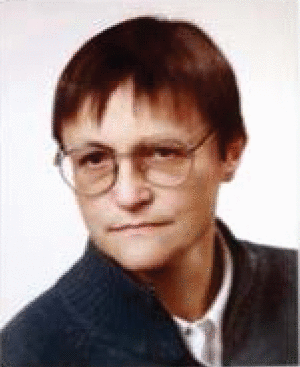
Beata Niezgoda-Żelasko
Beata Niezgoda-Żelasko obtai-ned her Ph.D. in technical sciences in 1994 and a post-doctoral degree in 2007 in the field of mechanics and mechanical engineering at the Cracow University of Technology. Currently she is an Associate Professor in the Institute for Thermal and Process Engineering, Cracow University of Technology. She has more than 30 years of academic experience and has published more than 80 journal papers. She is an author or co-author of five books in the field of heat pumps, heat exchangers design also flow and heat transfer of ice slurry. Her field of current research includes fluid flow and heat transfer of various coolants, design of heat pumps and atypical cooling devices.