Abstract
A numerical simulation is conducted to investigate effects of dimple locations on the flow structure and heat transfer in a dimpled-pin finned channel. Pin fins are arranged with a staggered layout on the endwall surface. The dimple print diameter is the same as the pin fin diameter. Five different dimple locations are investigated in this study. All results are acquired at Reynolds numbers ranging from 8,500 to 60,000. The results show that the dimple locations have remarkable effects on the flow structure and heat transfer in a dimpled-pin finned channel. The Nusselt number of the dimpled-pin finned channel is only increased by 3.52%, while the friction factor is increased by 1.81% compared to the pure pin finned channel when the dimple is located in the wake region. The wake and reversed flow are responsible for this low heat transfer augmentation. When the dimple is located in between the two pin fins, the counter-rotating vortex and impingement within the dimple produce the highest Nusselt number and the lowest friction factor among the tested dimple locations. In this case, the Nusselt number is increased by 20.94% and the friction factor is decreased by 1.69% compared to the pure pin finned channel.
Additional information
Funding
Notes on contributors
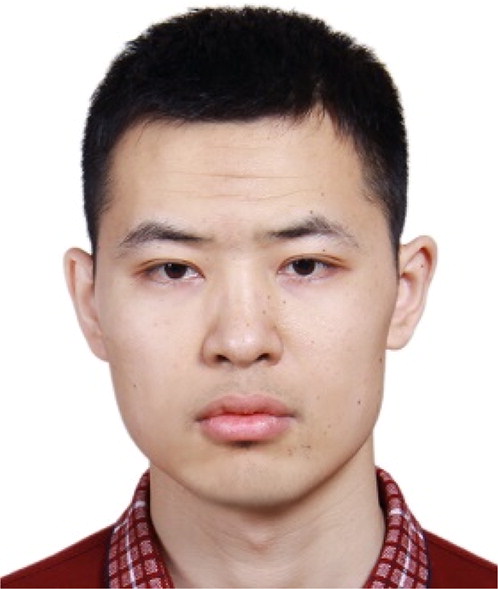
Wei Du
Wei Du is a Ph.D. student of Harbin Institute of Technology, Heilongjiang, China. He received his Bachelor of Engineering degree from Harbin Institute of Technology in 2015. His research interests are heat transfer and flow structure in the gas turbine trailing region.
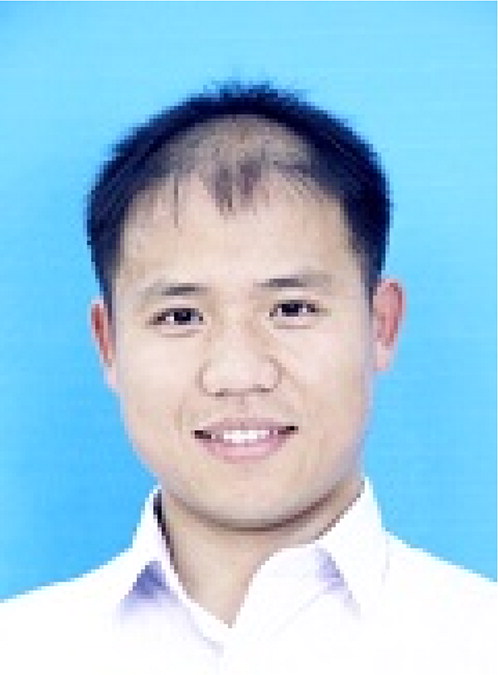
Lei Luo
Lei Luo is a lecturer in the School of Energy Science and Engineering, Harbin Institute of Technology, Heilongjiang, China. He received the Ph.D. degree from Harbin Institute of Technology in 2016. He received his Master's degree in 2014. His research interests are heat transfer and flow structure in the gas turbine and design methods for gas turbines.
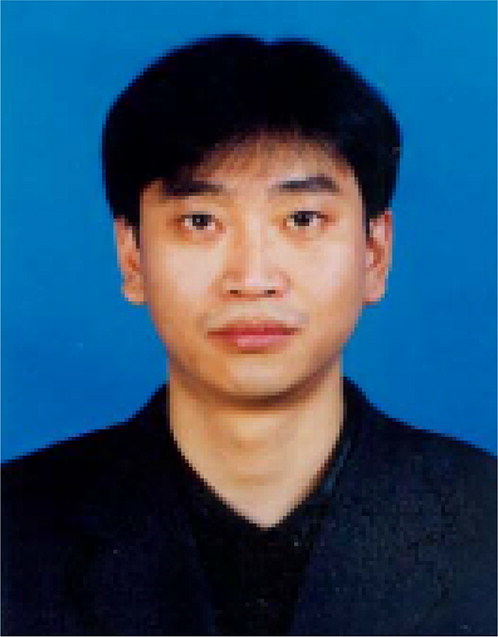
Songtao Wang
Songtao Wang is a Professor in the School of Energy Science and Engineering, Harbin Institute of Technology. He received the Ph.D. degree in 1999. He research interests are flow structure and heat transfer in the gas turbine, flow control in compressors and computational fluid dynamics.
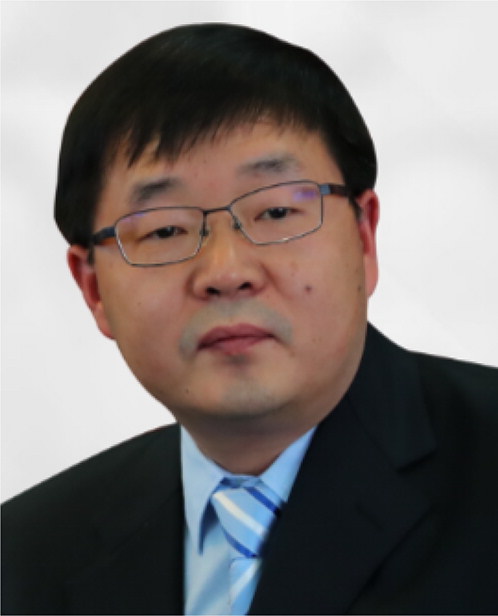
Xinghong Zhang
Xinghong Zhang is a Professor in the Center for Composite Materials and Structures, Harbin Institute of Technology. In 1997, he received the Master degree at Harbin Institute of Technology (HIT). In 1999, he received the Ph.D. degree at HIT. His research interests are ultra-high temperature ceramic composites and combustion synthesis technology of advanced materials.