Abstract
CO2 is an environmentally friendly heat transfer fluid and has many advantages in thermal energy and power systems due to its peculiar thermal transport and physical properties. Supercritical CO2 (S-CO2) thermal energy conversion systems are promising for innovative technology in domestic and industrial applications including heat pump, air-conditioning, power generation, renewable energy systems, energy storage, thermal management, waste heat recovery and others. Both S-CO2 and transcritical CO2 thermodynamic cycles have been extensively investigated in order to improve the efficiencies of thermal and power systems and achieve net zero carbon emissions. This paper focuses on the progress and prospects for current research and technology development of S-CO2 thermal energy conversion systems and their applications including power generation, energy storage and waste heat recovery. First, the CO2 thermal transport and physical properties and benefits using CO2 as a heat transfer fluid in thermal energy and power systems are discussed. Then, classification of CO2 thermodynamic systems is presented. Next, S-CO2 for power generation, energy storage and waste heat recovery systems are presented. Finally, research needs of subcritical and supercritical CO2 heat transfer, fluid flow and heat exchangers for the development of various thermal energy and power systems are discussed.
Introduction
Due to global warming, climate change, waste pollution and energy consumption, developments and breakthroughs of scientific theories and innovative technologies for advanced and decarbonized thermal and energy conversion systems are urgently needed in order to achieve net zero emissions [Citation1]. Research and development of thermal management, heat transfer enhancement and process intensification technologies, novel thermal energy and power systems, energy storage and waste heat recovery technologies have been extensively conducted for the purpose of effective utilization of energy, decarbonization and environment protection over the past years [Citation2–4]. As an efficient and environmentally safe working fluid, CO2 has been considered an alternative to conventional heat transfer fluids in various thermal energy conversion systems such as power generation, thermal energy conversion and utilization, waste heat recovery, air conditioning, heat pump and refrigeration systems, thermal management for sustainable energy technologies, nuclear energy, high heat flux removal and so on [Citation5–13].
S-CO2 Brayton thermodynamic cycle is a promising thermal conversion system for power generation to replace the conventional steam Rankine cycle owing to its high thermal efficiency, simple cycle layout, compactness of components and wide operation range [Citation14–17]. S-CO2 Brayton systems can be used in thermal energy conversion systems using both no-renewable and renewable sources such as nuclear, geo-thermal, solar, thermal power plants, energy storage and waste heat recovery [Citation18–28].
In the heat pump, air-conditioning, and refrigeration systems, natural refrigerants which exist in nature’s biological or chemical cycles have been chosen to replace synthetic refrigerants [Citation29]. As a nature refrigerant, CO2 (also known as R744) has been receiving renewed interest as an efficient and environmentally safe working fluid in mobile air conditioning, heat pump systems and refrigeration systems at low temperatures [Citation30–32]. Due to its low critical temperature Tcrit of 31.1 °C and high critical pressure pcrit of 7.38 MPa, CO2 is utilized at much higher operating pressures in air-conditioning and heat pump systems. Supercritical CO2 gas cooling in gas coolers rather than condensation heat transfer in condensers operates in the high-pressure process. Furthermore, CO2 can be used in electronic cooling, two-phase thermosyphon loop and evaporative CO2 cooling system for the upgrade of the Compact Muon Solenoid pixel detector etc. [Citation4]. CO2 thermal systems can be used in geothermal energy utilization, combined heat, cooling and power systems, thermal management, solar energy utilization and recovery of waste heat [Citation33–51].
In order to develop advanced CO2 thermal and power systems, compressors, and heat exchangers such as evaporators, gas coolers, condensers, internal heat exchangers and recuperators should be properly designed [Citation6–11]. CO2 heat exchangers with microchannels and enhanced elements can enhance heat transfer and thus improve the thermal efficiencies of various thermal energy conversion systems [Citation7,Citation8]. Understanding subcritical and supercritical heat transfer and fluid flow is the key to design of various heat transfer components and needs to be specially investigated due to the peculiar heat transfer and fluid flow behaviors for both evaporation and supercritical heat transfer processes. The sharp variations of the thermal transport and physical properties at high reduced pressures result in quite different heat transfer and fluid flow phenomena in various channels and components [Citation7,Citation11]. Therefore, heat transfer calculation correlations and design methods of heat transfer components have been extensively studied over the past years and technical risks in the design of the components used for various thermal conversion systems are reduced. However, adaptation of the CO2 thermal and power systems to interface with various heat sources is imperative for its adoption as an industry manufactured technology. Further research on CO2 heat transfer and fluid flow in emerging enhanced heat transfer tubes and heat exchangers is still needed to provide robust and reliable design correlations and methods for various thermal energy conversion systems.
For understanding the current research and technology development of S-CO2 thermal and power systems and future research and technology development needs, this paper presents a review on S-CO2 thermal energy conversion systems and their applications focusing on power generation with conventional and renewable heat sources, energy storage and waste heat recovery. Research of CO2 heat transfer, fluid flow and heat transfer components and future research needs are also mentioned in this review.
CO2 thermal transport and physical properties and benefits of using CO2 as a heat transfer fluid in thermal energy conversion systems
CO2 is a nontoxic, environmentally friendly and non-flammable heat transfer fluid. It is stable at high temperature with a large operational temperature range from −73 to 1000 °C at both subcritical and supercritical conditions in thermal energy and power conversion systems [Citation33]. As shown in , the critical point of CO2 is at the pressure of 73.8 bar and the temperature of 31.1 °C [Citation52]. At the supercritical conditions, CO2 behaves like a gas but with the density of a liquid performing like a single-phase fluid. Due to its particular thermodynamic and physical properties, CO2 can work at subcritical and supercritical conditions in various thermal and energy conversion systems such as heat pump, air conditioning and refrigeration systems, power generation systems using both conventional and renewable energy sources, energy storage, cooling and heating, thermal management and waste heat recovery.
Figure 1. p-T diagram phases to carbon dioxide [Citation52].
![Figure 1. p-T diagram phases to carbon dioxide [Citation52].](/cms/asset/a37ecdf8-e374-4c4c-9eb7-51d32be7b38e/uhte_a_2282765_f0001_c.jpg)
The thermal transport and physical properties of CO2 may vary significantly near the critical point and thus can significantly affect the evaporation and supercritical heat transfer and fluid flow behaviors of CO2, the heat transfer components, and the thermal and energy systems. [Citation19] shows the thermal transport and physical properties of CO2 versus temperature at the pressures of 7.5, 8, 9, 10 and 12 MPa, which were obtained from REFPROP 7.0 [Citation53]. For a constant pressure larger than the critical pressure, an important characteristic is that the specific heat reaches a sharp maximum as shown in . This point is called the pseudocritical point as indicated by the dash line in for the pressure of 9 MPa and the corresponding pressure and temperature are the pseudocritical pressure (pps) and the pseudocritical temperature (Tps). Near the critical pressure, the thermal conductivity also reaches a maximum value. The thermal transport and physical properties of CO2 change drastically with temperature around the critical point in an isobaric process, especially near the pseudocritical and critical points. However, with increasing the pressure, these changes become less pronounced. The density and dynamic viscosity undergo a significant drop near the critical point, which is almost vertical within a very narrow temperature range while the enthalpy undergoes a sharp increase. The specific heat, thermal conductivity and Prandtl number have peak values near the critical points. The magnitude of these peaks decreases very quickly with increasing pressure.
Figure 2. Physical properties of supercritical CO2 at five different pressures versus temperatures [Citation19]. (a) Density; (b) Enthalpy; (c) Specific heat (the dash line indicates the pseudo-critical point at the pressure of 9 MPa); (d) Thermal conductivity; (e) Dynamic viscosity; and (f) Prandtl number.
![Figure 2. Physical properties of supercritical CO2 at five different pressures versus temperatures [Citation19]. (a) Density; (b) Enthalpy; (c) Specific heat (the dash line indicates the pseudo-critical point at the pressure of 9 MPa); (d) Thermal conductivity; (e) Dynamic viscosity; and (f) Prandtl number.](/cms/asset/cf3ad4d1-3c8b-432d-a33d-2c2deef78a3f/uhte_a_2282765_f0002_b.jpg)
Due to its high density, a relatively low fluid flow rate is needed for S-CO2 in thermal and power systems. This significantly reduces the compression work and lead to simple and compact turbines at high temperatures and improvement of the system efficiency [Citation34]. S-CO2 heat transfer and fluid flow processes are critical to reducing the temperature difference between the metal tubes and CO2. Furthermore, CO2 is used as a natural refrigerant for air-conditioning, heat pump and low temperature refrigeration systems. The physical and transport properties of CO2 are quite different from those of conventional refrigerants at high reduced pressures. In general, CO2 has much higher evaporation heat transfer than conventional refrigerants. Microchannels are needed for both evaporators, internal heat exchangers and gas coolers. Microchannel heat exchangers can increase the heat transfer and therefor increase the thermal system efficiencies and make the thermal systems compact.
There are many benefits in using CO2 as a heat transfer fluid in various thermal energy and power generation systems. For example, combined S-CO2 heating, cooling and power generation systems are crucial to achieving zero carbon emissions. S-CO2 thermal conversions systems can be used for energy storage, waste heat recovery and cooling for high heat flux, solar collectors, power generation, cooling for green hydrogen energy systems and so on. When S-CO2 is used as the heat transfer fluid for solar collectors and power systems, it eliminates a heat exchanger in the systems and thus results in more efficient and less complex units. Despite the benefits of using S-CO2, it also presents some challenges which need to be addressed here. Operating near the critical point means high working pressures, so reduced tube diameters are required leading in a reduction in the heat transfer rate in tubular receivers. As well as the possible leaks associated to moving parts and connections. Accordingly, the materials considered for various components of the system must have resistance to corrosion and thermal fatigue caused by high temperature, oxidation, and creep. In the aspects of subcritical and supercritical CO2 heat transfer, fluid flow and heat exchangers, proper calculations correlations and design methods should be verified and adopted [Citation54–56].
Classification of S-CO2 thermal energy conversion systems
A thermal energy conversion system generally consists of four basic processes, namely compression, heat addition at high pressure p2, expansion, and heat rejection at low pressure p1. Depending on if there is a phase change process in the thermal energy conversion systems, thermal power systems are classified as two types of systems as shown in . In the Joule–Brayton cycle, the thermal system remains in the vapor region and in the Rankine system, the heat transfer fluid undergoes phase change process in the heat addition and heat rejection processes [Citation11].
Figure 3. Classification of thermodynamic power cycles (for interpretation of the references to color in this figure legend, the reader is referred to the web version of this article) [Citation11].
![Figure 3. Classification of thermodynamic power cycles (for interpretation of the references to color in this figure legend, the reader is referred to the web version of this article) [Citation11].](/cms/asset/00e21612-c6e2-4862-8d4e-db06afa75fc7/uhte_a_2282765_f0003_c.jpg)
Thermal energy conversion systems are also classified according to their operating pressures below or above the critical pressure of the heat transfer fluid (pcrit). There are three classifications: subcritical thermal systems for p1 < pcrit and p2 < pcrit, supercritical thermal systems for p1 > pcrit and p2 > pcrit, and transcritical thermal systems for p1 < pcrit and p2 > pcrit) as shown in [Citation11]. In supercritical systems, the low pressure of the system is also above the critical pressure 73.8 bars, and there is no distinction between the fluid being in a liquid or a vapor state as shown in . In transcritical systems, the low pressure of the system is below the critical pressure 73.8 bars, and condensation heat transfer may occur in heat-rejection process. In transcritical systems, the lower the compressor inlet temperature and the closer the compression process is to the saturated liquid line, thus the lower the compression work. Therefore, transcritical systems can improve the thermal efficiencies of the thermal systems.
shows the thermal efficiencies of various thermal power conversion systems and heat sources with respect to the turbine inlet temperature. The heat sources include geothermal energy, solar thermal energy, nuclear energy, coal, waste heat recovery, and liquefied natural gas (LNG). The power conversion systems are organic Rankine cycle (ORC), steam Rankine cycle (steam turbine), air Brayton cycle (gas turbine), combined cycle gas turbine (CCGT), and S-CO2 direct and indirect cycles [Citation13]. As indicated in , the steam Rankine cycle can achieve high efficiency at low turbine inlet temperatures because liquid water is incompressible and requires less work for compression. However, the gas turbine utilizes air and a large amount of work is consumed in the compression process. Therefore, the thermal efficiencies of the systems with gas turbines are lower than that of the steam Rankine systems although the turbine inlet temperatures are much higher. This is because the compressors consume a large amount of work. Furthermore, there is a big issue with the materials at higher turbine inlet temperatures for the gas turbines.
Figure 4. Thermal efficiencies of power conversion systems and applications [Citation13].
![Figure 4. Thermal efficiencies of power conversion systems and applications [Citation13].](/cms/asset/d3229f19-c1b0-451a-a536-37b1688d0dd0/uhte_a_2282765_f0004_c.jpg)
S-CO2 thermal systems have higher efficiencies than other thermal systems and are promising systems to replace the existing systems. shows the principles of power conversion systems using steam and S-CO2. S-CO2 Brayton cycle is a power conversion system which combines the advantages of both steam Rankine systems and gas turbine systems. CO2 becomes more incompressible near the critical point [Citation13]. Therefore, S-CO2 is compressed in the incompressible region and the higher turbine inlet temperature can be utilized with less material issues as compared to the steam Rankine systems.
Figure 5. Principles of power conversion system [Citation13].
![Figure 5. Principles of power conversion system [Citation13].](/cms/asset/ffb7a5c7-b87a-425d-970b-1a19a3a8dfaa/uhte_a_2282765_f0005_c.jpg)
Progress and prospects for S-CO2 thermal and power conversion systems
S-CO2 Brayton systems for power generation
S-CO2 Brayton power generation systems have high thermal efficiency, simple cycle layout, compactness of component and wide operation range. shows the comparison of power conversion systems using water, air and CO2 as working fluids [Citation13]. The advantages of S-CO2 Brayton systems are due to the high density and low compressibility of CO2 near its critical point and the wide and rapid variation in the thermodynamic properties as shown in . SCO2 Brayton systems can be used in nuclear, geo-thermal, solar and thermal power plants and combined heat, cooling and power systems and others.
Figure 6. The comparison of steam, air, S-CO2 power conversion systems [Citation13].
![Figure 6. The comparison of steam, air, S-CO2 power conversion systems [Citation13].](/cms/asset/d70fb87a-f21f-4eb3-8ac7-088905415e10/uhte_a_2282765_f0006_c.jpg)
Various layouts of S-CO2 Brayton power generation systems have been investigated over the past years [Citation56–62]. A simple recuperated S-CO2 Brayton cycle is the basic layout because a recuperator is essential for the system. and illustrate a typical recompression cycle which consists of a main compressor, a recompression compressor, a turbine, a low temperature recuperator, a high-temperature recuperator, and a precooler [Citation18]. The thermodynamic processes occur at state points in the cycle in and . The recuperators minimize the heat which is wasted after the turbine stage. The precooler is set to achieve thermodynamic conditions of the main compressor inlet. This cycle uses a flow split in front of the precooler to allow some of the CO2 to bypass the cooling process and to be recompressed. The recompression cycle is a typical layout which significantly improves the thermal efficiency of the system by recovering the heat and solving the pinch-point problem in the recuperators. The reheating and intercooling cycles are typical layouts which improve the system performance by increasing the expansion work and reducing the compression work, respectively. Based on the basic S-CO2 Brayton cycle, research has been investigated to optimize the layouts in order to improving the thermal efficiencies of the thermal energy conversion systems [Citation15,Citation18,Citation26,Citation27,Citation42].
Figure 7. Layout of S-CO2 Brayton recompression cycle [Citation18].
![Figure 7. Layout of S-CO2 Brayton recompression cycle [Citation18].](/cms/asset/88e262a6-d2be-4884-8f76-b119e9fa8461/uhte_a_2282765_f0007_c.jpg)
Figure 8. T-s diagram of S-CO2 Brayton recompression cycle [Citation18].
![Figure 8. T-s diagram of S-CO2 Brayton recompression cycle [Citation18].](/cms/asset/fb137101-e998-4b95-85b8-b70560051aff/uhte_a_2282765_f0008_c.jpg)
One of the main advantages of the S-CO2 Brayton systems is the compact turbomachinery. This is mainly because the S-CO2 Brayton systems operate at the supercritical conditions, the minimum pressure is higher (up to 7.4 MPa) than any existing steam Rankine systems (a few kPa) or gas Brayton systems (up to 100 kPa). Furthermore, S-CO2 remains dense throughout the whole power generation systems. Therefore, the volumetric flow rate decreases as the S-CO2 density is higher than that of other working fluids. This results in up to 10 times smaller turbomachinery of the S-CO2 Brayton systems as compared to the turbomachinery of a steam Rankine cycle. However, the cycle pressure ratios of the S-CO2 Brayton systems are much smaller as compared to those of the steam Rankine systems, the turbine outlet temperatures are relatively high. Therefore, a large amount of heat must be recuperated in order to increase the thermal efficiencies of the systems. The recuperation process is needed in the S-CO2 Brayton systems. The most efficient layout of the S-CO2 systems is the recompressing layout. This is because the S-CO2 systems are similar to the steam Rankine systems in terms of the layout while the systems are similar to the gas turbine systems in the aspect of the design of main components. Various layouts are employed for the S-CO2 power systems depending on their applications [Citation42].
One key feature of the S-CO2 Brayton systems is that the specific heat of the cold side fluid is two to three times higher than that of the hot side fluid in the recuperators. It is especially important to explain why the recompressing layouts can improve the thermal efficiencies. As shown in and , CO2 flow is split to compensate for the specific heat difference in the low temperature recuperators and to maximize the heat recuperation in the recompressing layouts. Therefore, waste heat can be reduced, and thermal efficiencies can be improved in the recompressing layouts [Citation47].
The operating conditions in the S-CO2 heat exchangers play a crucial role in improving the thermal efficiencies of the systems. As a large amount of heat is recovered in the recuperators to increase the thermal efficiencies of the systems, high effectiveness is required and therefore the capital cost increases when conventional shell and tube heat exchangers are utilized. However, various compact heat exchangers with high compactness (up to 10 times compared as compared to shell and tube heat exchangers), such as printed circuit heat exchangers have been commercialized and can be applied to the S-CO2 cycle directly [Citation62].
S-CO2 Brayton systems can be applied to various heat sources including conventional sources and renewable sources. They are considered as an alternative to the steam Rankine systems, nuclear energy ranging from pressurized water reactors (both large and small modular reactors) to the next generation nuclear reactors and fusion reactor applications as well [Citation42]. The S-CO2 systems can be utilized as topping systems for fossil fuel powered plants and bottoming systems of gas combined cycle plants. There are also promising heat sources including several renewable energy sources such as high temperature fuel cells, concentrated solar power and geothermal power which can be integrated with energy storage technology [Citation25,Citation44,Citation46,Citation56,Citation59].
S-CO2 thermal and power systems for energy storage
In recent years, research, and development of power generation from renewable resources are considerably increasing in order to achieve net zero carbon emission. Due to the stochastic and non-continuous nature of renewable resource availability (wind, solar and others), electrical energy storage is one of the main challenges for large-scale renewable power plants integration into the electric grid. Therefore, energy storage systems at different scales are needed to advance toward electrified systems with a high share of renewables. Depending on the amount of energy to be stored, there are different types of energy storage systems. Different integrations of S-CO2 systems in energy storage systems have been investigated [Citation28,Citation32,Citation34,Citation35,Citation37,Citation44].
Several options have been considered for storing electricity in thermal systems based on a combination of heat pumps and heat engines systems using CO2 as the working fluid. These are based on heat pumps, compression or incorporating underground reservoirs, thermal or geological storage [Citation35]. One promising energy storage technology is to use reversible heat pumps based on two closed cycles, indirectly connected by hot and cold thermal storage tanks. [Citation35] shows the conceptual system operation: in periods of excess energy, it is stored by a heat pump which compresses the working fluid. Sequence 1-2-3-4, transforming electrical energy into thermal energy and stores it, transferring/absorbing energy from the high and low-temperature (HT and LT) reservoirs. In periods with net electrical demand, the cycle follows the sequence 5-6-7-8, in which thermal energy is transformed into electrical energy by the operation of a heat engine. A functional heat transfer integration with heat storage tanks is required to obtain high efficiencies in the operation of the heat pump energy storage system. During charging, the working fluid temperature must be above the storage temperature during the whole heat transfer process. illustrates an example of poor integration in the temperature profile of LT storage, where the working fluid changes state (horizontal line denoting evolution at constant temperature) temperature change occurs in storage. illustrates an example of good thermal integration with the parallel evolution of the charge-discharge temperature profiles in the heat exchange with the thermal storage, where there is a sensible heat exchange in the HT reservoir and a latent exchange in the LT reservoir.
Figure 9. Reversible heat pump energy storage system with: (a) bad-integrated temperature profiles, and (b) well-integrated temperature profiles. QS: Sensible heat; QL: Latent heat; W: Work; cha: Charge; dis: Discharge [Citation35].
![Figure 9. Reversible heat pump energy storage system with: (a) bad-integrated temperature profiles, and (b) well-integrated temperature profiles. QS: Sensible heat; QL: Latent heat; W: Work; cha: Charge; dis: Discharge [Citation35].](/cms/asset/2efd94e0-073f-40f0-af1e-29bf53758946/uhte_a_2282765_f0009_c.jpg)
The integration of an energy storage system and geological storage of CO2 based on renewable energy within carbon capture and utilization applications is promising. The CO2 captured in a power plant or industrial facility is used as a working fluid in the proposed thermodynamic cycle to store renewable electrical energy underground. The storage of energy occurs in mechanical (work) and thermal (heat) forms [Citation35]. [Citation35] illustrates the conceptual scheme of a new energy storage system and storage of captured CO2 in a stationary source, consisting of two independent and open CO2 cycles, connected directly by geological storage and indirectly by thermal storage. As shown in , CO2 captured in a stationary source is used as a working fluid in a heat pump and injected into a geological formation (sequence 0-4-1-2-3-A), performing a charging cycle equivalent to that of the electrothermal system in the high (HT) and low (LT) temperature reservoirs. For the discharge, CO2 is extracted from the geological formation and used as the working fluid in the reverse cycle, ending with the re-injection of CO2 into the geological formation (sequence A-6-7-8-5-B).
Figure 10. Reversible heat pump energy storage system with well-integrated temperature profiles, including geological storage. QS: Sensible heat; QL: Latent heat; W: Work; cha: Charge; dis: Discharge; ST: Stationary CO2 source [Citation35].
![Figure 10. Reversible heat pump energy storage system with well-integrated temperature profiles, including geological storage. QS: Sensible heat; QL: Latent heat; W: Work; cha: Charge; dis: Discharge; ST: Stationary CO2 source [Citation35].](/cms/asset/0c3dcd88-b195-42e2-a3f3-ce8d024275fa/uhte_a_2282765_f0010_c.jpg)
To avoid the problem occurred in the traditional molten salt heat storage system, such as molten salt solidifying, heat transfer loss between the molten salt and working medium, and heat loss of stored heat, Liu et al. [Citation34] proposed a nonmolten salt heat storage scheme which uses compressed CO2 energy storage integrated with auxiliary combustion as shown in [Citation34]. In the cycle, under the energy storage conditions, the working fluid flows through the tower collector to absorb heat, some of the working fluid enters the main turbine to meet the power generation demand while other of the working fluid enters the turbine to drive the coaxial compressor to compress the CO2 near the critical point in the low-pressure tank and then stores it in the high-pressure tank. Under the energy release condition, supercritical CO2 flows out of the high-pressure tank, heated by a gas boiler, enters the turbine for work, and then passes through the heat exchanger to heat the bottom circulating working fluid. Then, CO2 is cooled to near the critical point and stored in a low-pressure tank without compression.
Figure 11. Schematic diagram of the integrated scheme of compressed CO2 energy storage and auxiliary combustion system [Citation34].
![Figure 11. Schematic diagram of the integrated scheme of compressed CO2 energy storage and auxiliary combustion system [Citation34].](/cms/asset/bd51ead6-999e-4164-9811-ab7b980f5069/uhte_a_2282765_f0011_c.jpg)
Geological storage in the concept of electrothermal energy storage has been studied in recent years. Carro et al. [Citation35] have proposed an energy storage system using transcritical CO2 cycles based on the concept of electrothermal energy storage and its integration with geological CO2 storage. [Citation35] illustrate the proposed conceptual layout of the basic electrothermal energy storage system based on a reversible heat pump. The thermodynamic charging cycle starts at the compressor inlet, where the fluid is compressed, reaching the highest temperature of the whole process. After transferring the heat to the hot water tank, the fluid expands in a hydraulic turbine, in whose output the lowest temperature of the process is reached. Similarly, the discharge cycle begins at the pump inlet, where the working fluid is compressed. After the evaporator, it expands in a gas turbine.
Figure 12. Conceptual layout of the basic electrothermal energy storage system. C: Compressor; HydT: Hydraulic turbine; P: Pump; T: Turbine; HXW: Heat exchange - Water; HXI: Heat exchange - Ice; HT: High temperature; LT: Low temperature [Citation35].
![Figure 12. Conceptual layout of the basic electrothermal energy storage system. C: Compressor; HydT: Hydraulic turbine; P: Pump; T: Turbine; HXW: Heat exchange - Water; HXI: Heat exchange - Ice; HT: High temperature; LT: Low temperature [Citation35].](/cms/asset/1c755bfa-8abb-417d-bc80-c87acefb0be8/uhte_a_2282765_f0012_c.jpg)
S-CO2 heat pump systems for heating and waste heat recovery
Due to the advantages of energy-saving, high-efficiency, and cost effectiveness, heat pump systems have been adopted in both residential and industrial sectors. The heat pumps based on the vapor-compression cycle consume a small amount of energy for a single-stage or multiple-stages compression, in order to generate the high-temperature and high-pressure vapor. Thus, the following heat-rejection process can be utilized for various purposes, including water heating, air heating, and steam production. Compared to electric or gas water heaters, the heat pump water heaters can contribute to a significant reduction in energy consumption and is able to provide high-temperature hot water with a relatively high coefficient of performance (normally around 3 to heat hot water up to 65 °C). Saikawa and Koyama [Citation56] developed a transcritical CO2 heat pump prototype as shown in and . The CO2-water heat exchanger of the prototype is a countercurrent type as shown in [Citation56]. Using capillary tubes for CO2 flow path could achieve high withstand pressure of the heat exchanger and high heat transfer coefficient of CO2. Also using plate with off-set inner fin for water flow path could achieve high heat transfer coefficient of water. Instead of a tube type, a plate type was selected for preventing the water path clogging. There is a case in which scale is generated when tap water is heated to over 60 °C. With these technologies, small and highly efficient heat exchanger with small temperature difference was developed.
Figure 13. Schematic of the heat pump prototype [Citation56].
![Figure 13. Schematic of the heat pump prototype [Citation56].](/cms/asset/cca1a540-3c96-4503-8ce8-89df305689a5/uhte_a_2282765_f0013_b.jpg)
Figure 14. Photograph of the heat pump prototype [Citation56].
![Figure 14. Photograph of the heat pump prototype [Citation56].](/cms/asset/b2c23e5a-6e87-437c-a324-a7b3ccd92ded/uhte_a_2282765_f0014_c.jpg)
Figure 15. The developed CO2-water heat exchanger [Citation56].
![Figure 15. The developed CO2-water heat exchanger [Citation56].](/cms/asset/c7a994b1-2064-4d28-8c18-1741c08bb6a4/uhte_a_2282765_f0015_c.jpg)
Transcritical CO2 heat pumps can be used for waste heat recovery in domestic and industrial applications. Just for one typical example of waste of heat recovery of data centers (DCs) using CO2 heat pumps, the energy consumption of DCs has increased considerably with the rapid development of the information technology industry. DCs use about 3% of the global electricity supply, and the consumption is increasing at an annual rate of 15–20%. Around 40% of the power consumed by DCs is used for the cooling systems. The exergy loss of energy flow in DCs is huge due to the use of electrical energy for cooling DCs. A large amount of waste heat of the cooling is discharged to the external environment. Therefore, DCs may be considered energy producers if large amounts of low grade and medium-grade waste heat are effectively recovered and used for building heating, water heating, refrigeration, and air conditioning. Wang et al. [Citation62] have proposed a prosumer DC waste heat energy recovery system using a CO2 direct expansion ground source heat pump. Their proposed system is able to efficiently recycle the waste heat from DCs, including waste heat collection, building heating load matching, and non-heating period waste heat utilization. illustrates the model and components of the prosumer DC waste heat energy recovery system integrated with the CO2 direct expansion ground source heat pump [Citation62]. The system consists of an evaporator placed in the cabinet, air cooler, working fluid pump, compressor, throttle valve, borehole heat exchanger, and heat exchangers. If the outdoor temperature is lower than the initial operating temperature which is at least 5 °C below the temperature of the working fluid CO2, the air cooler will operate, and CO2 exchanges heat with outdoor air. To recycle the waste heat from the DC during the heating period, the temperature of CO2 from the DC is increased by the compressor, and CO2 exchanges heat with water that is used for building heating. In the non-heating period, CO2 is compressed and exchanges heat with the borehole heat exchanger. The heat generated by the DC is stored in the soil and later used for building heating. Different operation modes can be realized by applying different valve switching modes. The system can meet the cooling demands of the DC and recover waste heat for the purpose of building heating.
Figure 16. Model of the prosumer DC waste heat energy recovery system [Citation62].
![Figure 16. Model of the prosumer DC waste heat energy recovery system [Citation62].](/cms/asset/467c5c8d-24fd-4e70-9d87-c1abf9aeacc5/uhte_a_2282765_f0016_c.jpg)
Research of heat transfer, fluid flow and heat exchangers for CO2 thermal and power systems
The transport and physical properties of CO2 strongly affect the heat transfer and pressure drops at both subcritical supercritical conditions. Fundamentals and design correlations of evaporation, vapor liquid two phase flow, supercritical heat transfer and fluid flow are important in the design of various components such as evaporators, gas coolers, compressors, recuperators in the CO2 thermal and power systems. In particular, microchannel heat exchangers, compact heat exchangers and printed circuit heat exchangers rather than shell tube heat exchangers have been developed and used in S-CO2 systems as shown in [Citation56], [Citation63] and [Citation11]. Therefore, a good knowledge of the transport and physical properties and their effects on the calculation methods of CO2 heat transfer, and pressure drops, and the design methods of the components are needed.
Figure 17. The (a) one-pass and (b) two-pass internal configurations of the brazed plate heat exchangers [Citation63].
![Figure 17. The (a) one-pass and (b) two-pass internal configurations of the brazed plate heat exchangers [Citation63].](/cms/asset/641d31ab-7ace-41ff-9700-9c474a127efd/uhte_a_2282765_f0017_c.jpg)
Figure 18. (a) Typical printed circuit heat exchanger, (b) flow paths and details of the diffusion-bonded core, and (c) and of an etched plate [Citation11].
![Figure 18. (a) Typical printed circuit heat exchanger, (b) flow paths and details of the diffusion-bonded core, and (c) and of an etched plate [Citation11].](/cms/asset/7352167e-83e6-490b-9d9a-05413050cd13/uhte_a_2282765_f0018_c.jpg)
Studies of evaporation heat transfer, two phase flow, supercritical heat transfer and fluid flow behaviors in macro and microchannels, enhanced tubes and various heat exchanges have been extensively conducted over the past decades [Citation64–86]. The heat transfer mechanisms and design correlations have been proposed for the purpose of design of various heat exchangers of CO2 as well [Citation87–99].
For CO2 evaporation heat transfer and two-phase flow, the models developed by Cheng et al. [Citation87–90] are the proper methods which have been widely adopted in the design and simulations of CO2 evaporators [Citation7,Citation10,Citation54,Citation93]. For supercritical CO2 heat transfer and fluid flow, as most single-phase heat transfer correlations were not developed for supercritical fluids, they cannot necessarily be expected to give accurate results for CO2 at supercritical conditions. The main reason is that near the supercritical and subcritical regions, in the case of an isobaric change of state at subcritical pressures, all properties of a single-phase fluid change significantly continuously (sometimes very sharply) with temperature. If a supercritical fluid flow and heat transfer processes passe near the critical region, strong variations of fluid properties take place, and the heat transfer process is largely governed by local conditions [Citation100–102]. In a S-CO2 gas cooling and heating heat transfer process, the pressure of the heat exchangers during heat transfer is maintained above the critical pressure, so the physical and transport property variations can be severe as shown in . Consequently, heat transfer coefficients have to be calculated locally and heat exchangers with small increments [Citation102–108]. In addition, because of the large viscosity changes and gradients near the wall, pressure drop correlations need to be validated for S-CO2.
Concluding remarks
CO2 thermal energy conversion systems are promising technology in many applications in power generation with conventional and renewable energy sources, energy storage and waste heat recovery. Both supercritical and transcritical CO2 thermal systems are efficient energy conversion and utilization technology. The benefits of the S-CO2 thermal and power systems include (a) The thermal efficiency can be increased up to 5% as compared with the steam Rankine systems; (b) The turbomachinery can be much smaller and the overall system size can be reduced up to ten times as compared to the conventional steam Rankine systems; (c) The positive potential of the air-cooled S-CO2 cycle can be adopted if the system design becomes more sophisticated; (d) As the minimum pressure is higher than the CO2 critical pressure, the purification system requirements are lower than those of the steam Rankine systems; (e) CO2 is relatively cheaper and less harmful than other working fluids when an appropriate ventilation system is installed to prepare for a sudden large release of CO2 from the power conversion systems.
There are challenges of developing CO2 thermal systems and applications. Various layouts have been proposed for various applications. However, optimization of the systems is still needed. Development high performance components is needed. Various heat transfer enhancement and process intensification technologies are needed. Both subcritical and supercritical CO2 heat transfer and fluid flow research is still needed. In particular, for microchannels and printed heat exchangers and emerging structures heat transfer components.
Nomenclature | ||
C | = | compressor |
CCGT | = | combined cycle gas turbine |
DC | = | data center |
HE | = | heat engine |
HP | = | heat pump |
HT | = | high temperature |
HTR | = | high temperature regenerator |
HXI | = | heat exchange - ice |
HXW | = | heat exchange - water |
HydT | = | hydraulic turbine |
IHX | = | internal heat exchanger |
LNG | = | liquefied natural gas |
LT | = | low temperature |
LTR | = | low temperature regenerator |
MC | = | main compressor |
ORC | = | organic Rankine cycle |
P | = | pump |
p | = | pressure, Pa |
pps | = | psuedocritical pressure, Pa |
pcrit | = | critical pressure, Pa |
p1 | = | low pressure, Pa |
p2 | = | high pressure, Pa |
QL | = | latent heat |
QS | = | sensible heat |
RC | = | recompressing compressor |
s | = | entropy |
S-CO2 | = | supercritical CO2 |
ST | = | stationary CO2 source |
T | = | temperature, K, or turbine |
Tcrit | = | critical temperature, K |
Tps | = | pseudocritical temperature, K |
T-CO2 | = | transcritical CO2 |
W | = | work |
WHR | = | waste heat recovery |
Subscripts | ||
cha | = | charge |
crit | = | critical |
dis | = | discharge |
ps | = | pseudocritical |
1 | = | low |
2 | = | high |
Disclosure statement
No potential conflict of interest was reported by the author(s).
Additional information
Notes on contributors
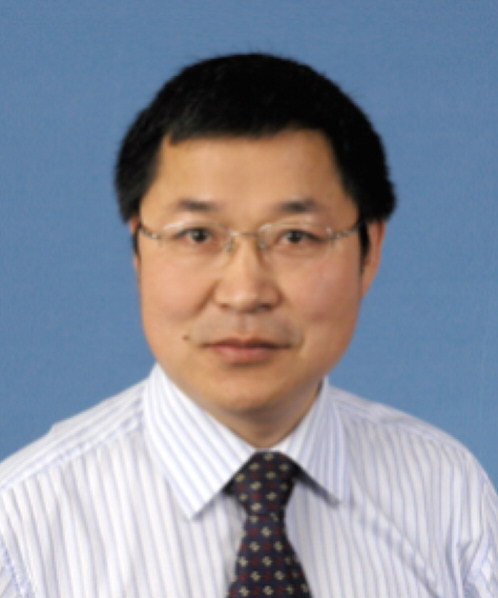
Lixin Cheng
Lixin Cheng obtained his Ph.D. in Thermal Energy Engineering at the State Key Laboratory of Multiphase Flow in Power Engineering at Xi’an Jiaotong University, China in 1998. He has extensive international working experience at several prestigious institutions. He has worked at Sheffield Hallam University, UK since 2016. He was associate professor at Aarhus University, Denmark in 2013–2015, senior lecturer at the University of Portsmouth in 2011–2013, lecturer at the University of Aberdeen, UK in 2009–2011. He was scientific collaborator at the Swiss Federal Institute of Technology in Lausanne (EPFL) in 2006–2009, Alexander von Humboldt fellow at the Leibniz University of Hanover, Germany in 2004–2006, senior research fellow at London South Bank University in 2001–2003 and research fellow at Eindhoven University of Technology, the Netherlands in 2000–2003. He has received several prestigious awards such as Alexander von Humboldt Fellowship in Germany in 2006, an ERCOFTAC Visitor Grant at EPFL, Switzerland in 2010 and a Distinguished Visiting Professorship of the City of Beijing, China in 2016–2021, and 2022–2025. His research interests include multiphase flow and heat transfer and thermal energy engineering, high heat flux thermal management, decarbonized heating and cooling technology, CO2 thermal, energy and power systems, renewable energy systems, hydrogen energy system, and new net zero energy technology. He has published more than 120 papers in journals and conferences, 9 book chapters and edited 10 books. He has delivered more than 60 keynote and invited lectures worldwide. He is the congress chair of the World Congress on Momentum, Heat and Mass Transfer (MHMT) since 2017. He is one of the founders and co-chair of the International Symposium of Thermal-Fluid Dynamics (ISTFD) series since 2019. He is associate editor of Heat Transfer Engineering, Heat Transfer Research and Journal of Fluid Flow, Heat and Mass Transfer, and international advisor of Thermal Power Generation (a Chinese journal).
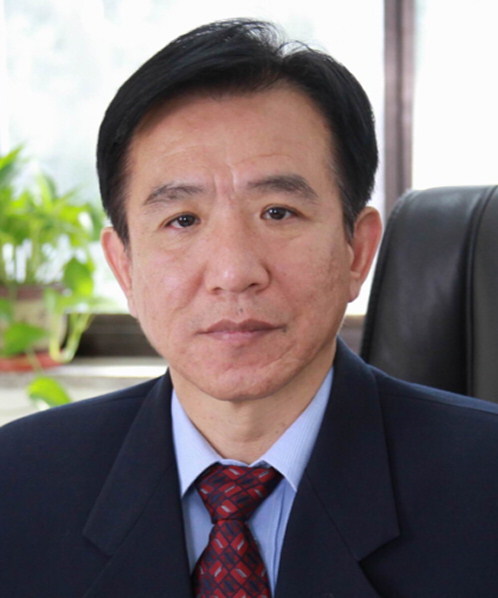
Guodong Xia
Guodong Xia is a leading professor in Thermal Energy Engineering at Beijing University of Technology, China. He received his Ph.D. in Thermal Energy Engineering at the State Key Laboratory of Multiphase Flow of Xi’an Jiaotong University, China in 1996. He was a visiting professor in the Institute of Process Engineering at the University of Hanover, Germany in 2000–2001. His research interests include fundamentals and applications of microscale heat transfer, multiphase flow and heat transfer, waste energy recovery, thermal energy system, heat exchanger design and enhanced heat transfer. He is a member of the multiphase flow committee of the Chinese Society of Engineering Thermophysics and a member of the multiphase flow committee of the Chinese Society of Theoretical and Applied Mechanics. He has published more than 150 papers in journals and conferences.
References
- L. Cheng, K. Wang, G. Xia and A. J. Ghajar, “Advanced heat transfer technologies: fundamentals and applications,” Heat Transfer. Eng., vol. 44, no. 21–22, pp. 1–3, 2023. DOI: 10.1080/01457632.2022.2164676.
- L. Cheng, Z. Guo and G. Xia, “A review on research and technology development of green hydrogen energy systems with thermal management and heat recovery,” Heat Transfer. Eng., pp. 1–23, 2023. DOI: 10.1080/01457632.2023.2191435.
- L. Cheng and G. Xia, “High heat flux cooling technologies using microchannel evaporators: fundamentals and challenges,” Heat Transfer. Eng., vol. 44, no. 16–18, pp. 1470–1497, 2023. DOI: 10.1080/01457632.2022.2140639.
- L. Cheng, L. Chai and Z. Guo, “Thermal energy, process, and transport intensification - a brief review of literature in 2021 and prospects,” Heat Trans. Res., vol. 53, no. 18, pp. 1–25, 2022. DOI: 10.1615/HeatTransRes.2022044585.
- M. Astolfi, D. Alfani, S. Lasala and E. Macchi, “Comparison between ORC and CO2 power systems for the exploitation of low-medium temperature heat sources,” Energy, vol. 161, pp. 1250–1261, Oct. 2018. DOI: 10.1016/j.energy.2018.07.099.
- M.-H. Kim, J. Pettersen and C. W. Bullard, “Fundamental process and system design issues in CO2 vapor compression systems,” Prog. Energy Combust. Sci., vol. 30, no. 2, pp. 119–174, 2004. DOI: 10.1016/j.pecs.2003.09.002.
- L. Cheng, G. Xia and J. R. Thome, “Flow boiling heat transfer and two phase flow phenomena of CO2 in macro- and micro-channel evaporators: fundamentals, applications and engineering design,” Appl. Therm. Eng., vol. 195, pp. 117070, Aug. 2021. DOI: 10.1016/j.applthermaleng.2021.117070.
- J. R. Thome and G. Ribatski, “State-of-the-art of two-phase flow and flow boiling heat transfer and pressure drop of CO2 in macro- and micro-channels,” Int. J. Refrig., vol. 28, no. 8, pp. 1149–1168, Dec. 2005. DOI: 10.1016/j.ijrefrig.2005.07.005.
- S. C. Kim, J. P. Won, Y. S. Park, T. W. Lim and M. S. Kim, “Performance evaluation of a stack cooling system using CO2 air conditioner in fuel cell vehicles,” Int. J. Refrig., vol. 32, no. 1, pp. 70–77, Jan. 2009. DOI: 10.1016/j.ijrefrig.2008.07.003.
- L. Cheng, G. Xia and Q. Li, “CO2 evaporation process modelling: fundamentals and engineering applications,” Heat Transfer. Eng., vol. 43, no. 8–10, pp. 658–678, 2022. DOI: 10.1080/01457632.2021.1905297.
- M. T. White, G. Bianchi, L. Chai, S. A. Tassou and A. I. Sayma, “Review of supercritical CO2 technologies and systems for power generation,” Appl. Therm. Eng, vol. 185, pp. 116447, Feb. 2021. DOI: 10.1016/j.applthermaleng.2020.116447.
- J. Wang, et al., “A comprehensive review and analysis on CO2 heat pump water heaters,” Energy Convs. Manag. X, vol. 15, pp. 100277, Aug. 2022. DOI: 10.1016/j.ecmx.2022.100277.
- Y. Ahn, et al., “Review of supercritical CO2 power cycle technology and current status of research and development,” Nucl. Eng. Technol., vol. 47, no. 6, pp. 647–661, Oct. 2015. DOI: 10.1016/j.net.2015.06.009.
- J. Han, et al., “Off-design analysis of a supercritical CO2 Brayton cycle with ambient air as the cold source driven by waste heat from gas turbine,” Heat Transfer. Eng., vol. 42, no. 16, pp. 1321–1331, 2021. DOI: 10.1080/01457632.2020.1794620.
- J. Yang, Z. Yang and Y. Duan, “Part-load performance analysis and comparison of supercritical CO2 Brayton cycles,” Energy Convs. Manag., vol. 214, pp. 112832, Jun. 2020. DOI: 10.1016/j.enconman.2020.112832.
- M. Chen, et al., “Supercritical CO2 Brayton cycle: intelligent construction method and case study,” Energy Convs. Manag., vol. 246, pp. 114662, Oct. 2021. DOI: 10.1016/j.enconman.2021.114662.
- H. Li, et al., “Preliminary conceptual exploration about performance improvement on supercritical CO2 power system via integrating with different absorption power generation systems,” Energy Convs. Manag, vol. 173, pp. 219–232, Oct. 2018. DOI: 10.1016/j.enconman.2018.07.075.
- J. H. Park, H. S. Park, J. G. Kwon, T. H. Kim and M. H. Kim, “Optimization and thermodynamic analysis of supercritical CO2 Brayton recompression cycle for various small modular reactors,” Energy, vol. 160, pp. 520–535, Oct. 2018. DOI: 10.1016/j.energy.2018.06.155.
- L. Cheng, G. Ribatski and J. R. Thome, “Analysis of supercritical CO2 cooling in macro- and micro-channels,” Int. J. Refrig., vol. 31, no. 8, pp. 1301–1316, Dec. 2008. DOI: 10.1016/j.ijrefrig.2008.01.010.
- L. Cheng, “Evaluation of correlations for supercritical CO2 cooling convective heat transfer and pressure drop in macro- and micro-scale tubes,” Int. J. Microscale Nanoscale Therm. Fluid Transp. Phenom., vol. 5, no. 2, pp. 113–126, 2014.
- Y. Yang, J. Wu, X. Song and Z. Gu, “Thermal management performance of Lithium-Ion battery using supercritical CO2 as cooling fluid,” Heat Transfer. Eng., vol. 44, no. 15, pp. 1452–1465, 2023. DOI: 10.1080/01457632.2022.2134082.
- L. Cheng and J. R. Thome, “Cooling of microprocessors using flow boiling of CO2 in micro-evaporators: preliminary analysis and performance comparison,” Appl. Therm. Eng, vol. 29, no. 11–12, pp. 2426–2432, 2009. DOI: 10.1016/j.applthermaleng.2008.12.019.
- X. Song, B. Yu, Y. Zhang, J. Shi and J. Chen, “An investigation into the thermodynamic improvement potential of a transcritical automotive CO2 refrigeration cycle,” Appl. Therm. Eng, vol. 216, pp. 119137, Nov. 2022. DOI: 10.1016/j.applthermaleng.2022.119137.
- J. Luo, T. Morosuk and G. Tsatsaronis, “Exergoeconomic investigation of a multi-generation system with CO2 as the working fluid using waste heat,” Energy Convs. Manag, vol. 197, pp. 111882, Oct. 2019. DOI: 10.1016/j.enconman.2019.111882.
- K. Wang, Z.-D. Zhang, M.-J. Li and C.-H. Min, “A coupled optical-thermal-fluid-mechanical analysis of parabolic trough solar receivers using supercritical CO2 as heat transfer fluid,” Appl. Therm. Eng, vol. 183part, no. 1, pp. 116154, Jan. 2021. DOI: 10.1016/j.applthermaleng.2020.116154.
- B. D. Iverson, T. M. Conboy, J. J. Pasch and A. M. Kruizenga, “Supercritical CO2 Brayton cycles for solar-thermal energy,” Appl. Energy, vol. 111, pp. 957–970, Nov. 2013. DOI: 10.1016/j.apenergy.2013.06.020.
- E. Guelpa and V. Verd, “Exergoeconomic analysis for the design improvement of supercritical CO2 cycle in concentrated solar plant,” Energy, vol. 206, pp. 118024, Sep. 2020. DOI: 10.1016/j.energy.2020.118024.
- F. G. Battisti, L. A. de Araujo Passos and A. K. da Silva, “Economic and environmental assessment of a CO2 solar-powered plant with packed-bed thermal energy storage,” Appl. Energy, vol. 314, pp. 118913, May 2022. DOI: 10.1016/j.apenergy.2022.118913.
- J. R. Thome, L. Cheng, G. Ribatski and L. F. Vales, “Flow boiling of ammonia and hydrocarbons: a state-of-the-art review,” Int. J. Refrig., vol. 31, no. 4, pp. 603–620, Jun. 2008. DOI: 10.1016/j.ijrefrig.2007.11.010.
- L. Cheng, G. Ribatski and J. R. Thome, “On the Prediction of Flow Boiling Heat Transfer of CO2,” in The 22nd IIR International Congress of Refrigeration, Beijing, 2007.
- L. Cheng and G. Xia, “Study of the effect of the reduced pressure on a mechanistic heat transfer model for flow boiling of CO2 in macroscale and microscale tubes,” Heat Transfer. Eng., vol. 44, no. 16–18, pp. 1657–1670, 2023. DOI: 10.1080/01457632.2022.2140631.
- D. Zhang, et al., “Performance study of transcritical CO2 heat pump integrated with ejector and latent thermal energy storage for space heating,” Energy Convs. Manag., vol. 268, pp. 115979, Sep. 2022. DOI: 10.1016/j.enconman.2022.115979.
- G. Carraro, P. Danieli, A. Lazzaretto and T. Boatto, “A common thread in the evolution of the configurations of supercritical CO2 power systems for waste heat recovery,” Energy Convs. Manag., vol. 237, pp. 114031, Jun. 2021. DOI: 10.1016/j.enconman.2021.114031.
- Y. Liu, Y. Wang, Y. Zhang and S. Hu, “Design and performance analysis of compressed CO2 energy storage of a solar power tower generation system based on the S-CO2 Brayton cycle,” Energy Convs. Manag., vol. 249, pp. 114856, Dec. 2021. DOI: 10.1016/j.enconman.2021.114856.
- A. Carro, R. Chacartegui, C. Ortiz, J. Carneiro and J. A. Becerra, “Integration of energy storage systems based on transcritical CO2: concept of CO2 based electrothermal energy and geological storage,” Energy, vol. 238, pp. 121665, Jan. 2022. DOI: 10.1016/j.energy.2021.121665.
- J. Du, et al., “A triple cascade gas turbine waste heat recovery system based on supercritical CO2 Brayton cycle: thermal analysis and optimization,” Energy Convs. Manag. X, vol. 16, pp. 100297, Dec. 2022. DOI: 10.1016/j.ecmx.2022.100297.
- H. Li, Y. Tao, Y. Zhang and H. Fu, “Two-objective optimization of a hybrid solar-geothermal system with thermal energy storage for power, hydrogen and freshwater production based on transcritical CO2 cycle,” Renew. Energy, vol. 183, pp. 51–66, Jan. 2022. DOI: 10.1016/j.renene.2021.10.080.
- M. Fallah, Z. Mohammadi and S. M. Seyed Mahmoudi, “Advanced exergy analysis of the combined S-CO2/ORC system,” Energy, vol. 241, pp. 122870, Feb. 2022. DOI: 10.1016/j.energy.2021.122870.
- J. He, et al., “Control strategy for a CO2-based combined cooling and power generation system based on heat source and cold sink fluctuations,” Energy, vol. 257, pp. 124716, Oct. 2022. DOI: 10.1016/j.energy.2022.124716.
- L. Sun, D. Wang and Y. Xie, “Energy, exergy and exergoeconomic analysis of two supercritical CO2 cycles for waste heat recovery of gas turbine,” Appl. Therm. Eng, vol. 196, pp. 117337, Sep. 2021. DOI: 10.1016/j.applthermaleng.2021.117337.
- S. Alharbi, M. L. Elsayed and L. C. Chow, “Exergoeconomic analysis and optimization of an integrated system of supercritical CO2 Brayton cycle and multi-effect desalination,” Energy, vol. 197, pp. 117225, Apr. 2020. DOI: 10.1016/j.energy.2020.117225.
- Z. Guo, Y. Zhao, Y. Zhu, F. Niu and D. Lu, “Optimal design of supercritical CO2 power cycle for next generation nuclear power conversion systems,” Prog. Nucl. Energy, vol. 108, pp. 111–121, Sep. 2018. DOI: 10.1016/j.pnucene.2018.04.023.
- O. Kizilkan, S. Khanmohammadi and M. Saadat-Targhi, “Solar based CO2 power cycle employing thermoelectric generator and absorption refrigeration: thermodynamic assessment and multi-objective optimization,” Energy Convs. Manag., vol. 200, pp. 112072, Nov. 2019. DOI: 10.1016/j.enconman.2019.112072.
- S. Trevisan, R. Gúedez and B. Laumert, “Thermo-economic optimization of an air driven supercritical CO2 Brayton power cycle for concentrating solar power plant with packed bed thermal energy storage,” Sol. Energy, vol. 211, pp. 1373–1391, Nov. 2020. DOI: 10.1016/j.solener.2020.10.069.
- Y. Ma, T. Morozyuk, M. Liu, J. Yan and J. Liu, “Optimal integration of recompression supercritical CO2 Brayton cycle with main compression intercooling in solar power tower system based on exergoeconomic approach,” Appl. Energy, vol. 242, pp. 1134–1154, May 2019. DOI: 10.1016/j.apenergy.2019.03.155.
- Y. Cao, H. Habibi, M. Zoghi and A. Raise, “Waste heat recovery of a combined regenerative gas turbine - recompression supercritical CO2 Brayton cycle driven by a hybrid solar-biomass heat source for multi-generation purpose: 4E analysis and parametric study,” Energy, vol. 236, pp. 121432, Dec. 2021. DOI: 10.1016/j.energy.2021.121432.
- M. Marchionni, G. Bianchi and S. A. Tassou, “Transient analysis and control of a heat to power conversion unit based on a simple regenerative supercritical CO2 Joule-Brayton cycle,” Appl. Therm. Eng., vol. 183, no. 2, pp. 116214, Jan. 2021. DOI: 10.1016/j.applthermaleng.2020.116214.
- G. Shu, L. Shi, H. Tian and L. Chang, “Comparison and selection research of CO2-based transcritical Rankine cycle using for gasoline and diesel engine’s waste heat recovery,” Heat Transfer. Eng., vol. 39, no. 7–8, pp. 672–686, 2018. DOI: 10.1080/01457632.2017.1325678.
- J. Liu, et al., “Thermo-economic analysis of a plasma-gasification-based waste-to-energy system integrated with a supercritical CO2 cycle and a combined heat and power plant,” Energy Tech., vol. 10, no. 8, pp. 2200101, Aug. 2022. DOI: 10.1002/ente.202200101.
- J. Song, Y. Wang, K. Wang, J. Wang and C. N. Markides, “Combined supercritical CO2 (SCO2) cycle and organic Rankine cycle (ORC) system for hybrid solar and geothermal power generation: thermoeconomic assessment of various configurations,” Renew. Energy, vol. 174, pp. 1020–1035, Aug. 2021. DOI: 10.1016/j.renene.2021.04.124.
- Y. Khan and R. S. Mishra, “Performance analysis of solar driven combined recompression main compressor intercooling supercritical CO2 cycle and organic Rankine cycle using low GWP fluids,” Energy, Built Environ., vol. 3, no. 4, pp. 496–507, Oct. 2022. DOI: 10.1016/j.enbenv.2021.05.004.
- X. Yang, et al., “Environmentally friendly techniques for high gas content thick coal seam stimulation - multi-discharge CO2 fracturing system,” J. Nat. Gas Sci. Eng., vol. 61, pp. 71–82, Jan. 2019. DOI: 10.1016/j.jngse.2018.11.006.
- REFPROP. NIST Refrigerant Properties Database 23, Version 7.0, Gaithersburg, MD, 2002.
- L. Cheng and G. Xia, “Flow boiling heat transfer and two-phase flow of carbon dioxide: fundamentals, mechanistic models and applications,” Proc. of the 4th World Congr. on Momentum, and Heat Mass Transfer (MHMT'19), 2019. Rome, Italy, April 10–12. DOI: 10.11159/icmfht19.2.
- S. Yamaguchi, D. Kato, K. Saito and S. Kawai, “Development and validation of static simulation model for CO2 heat pump,” Int. J. Heat Mass Transfer., vol. 54, no. 9–10, pp. 1896–1906, Apr. 2011. DOI: 10.1016/j.ijheatmasstransfer.2011.01.013.
- M. Saikawa and S. Koyama, “Thermodynamic analysis of vapor compression heat pump cycle for tap water heating and development of CO2 heat pump water heater for residential use,” Appl. Therm. Eng., vol. 106, pp. 1236–1243, Aug. 2016. DOI: 10.1016/j.applthermaleng.2016.06.105.
- S. Alshahrani, L. Vesely, J. Kapat, C. Ahamed Saleel and A. Engeda, “Performance investigation of supercritical CO2 Brayton cycles in combination with solar power and waste heat recovery system,” ASME J. Sol. Energy Eng., vol. 144, no. 6, pp. 061004, Dec. 2022. DOI: 10.1115/1.4054663.
- S. Hou, et al., “Optimization of a combined cooling, heating and power system using CO2 as main working fluid driven by gas turbine waste heat,” Energy Convs. Manag, vol. 178, pp. 235–249, Dec. 2018. DOI: 10.1016/j.enconman.2018.09.072.
- X. Ma, P. Jiang and Y. Zhu, “Performance analysis and dynamic optimization of integrated cooling and power generation system based on supercritical CO2 cycle for turbine-based combined cycle engine,” Appl. Therm. Eng., vol. 215, pp. 118867, Oct. 2022. DOI: 10.1016/j.applthermaleng.2022.118867.
- E. K. Levy, X. Wang, C. Pan, C. E. Romero and C. R. Maya, “Use of hot supercritical CO2 produced from a geothermal reservoir to generate electric power in a gas turbine power generation system,” J. CO2 Util., vol. 23, pp. 20–28, Jan. 2018. DOI: 10.1016/j.jcou.2017.11.001.
- C. Zhang, B. Hao, L. Cheng, J. Xu and Q. Wang, “Heat transfer characteristics of CO2 in a horizontal tube under subcritical and supercritical pressures,” Heat Transfer. Eng., vol. 45, no. 4–5, pp. 1–18, 2023. DOI: 10.1080/01457632.2023.2191440.
- X. Wang, et al., “Energy, exergy, and economic analysis of a data center energy system driven by the CO2 ground source heat pump: prosumer perspective,” Energy Convs. Manag., vol. 232, pp. 113877, Mar. 2021. DOI: 10.1016/j.enconman.2021.113877.
- A. Zendehboudi, Z. Ye, A. Hafner, T. Andresenc and G. Skaugen, “Heat transfer and pressure drop of supercritical CO2 in brazed plate heat exchangers of the tri-partite gas cooler,” Int. J. Heat Mass Transfer., vol. 178, pp. 121641, Oct. 2021. DOI: 10.1016/j.ijheatmasstransfer.2021.121641.
- S. Jeong and D. Park, “Evaporative heat transfer of CO2 in a smooth and a micro-grooved miniature channel tube,” Heat Transfer. Eng., vol. 30, no. 7, pp. 582–589, 2009. DOI: 10.1080/01457630802595025.
- L. Cheng and D. Mewes, “Review of two-phase flow and flow boiling of mixtures in small and mini channels,” Int. J. Multiphase Flow, vol. 32, no. 2, pp. 183–207, Feb. 2006. DOI: 10.1016/j.ijmultiphaseflow.2005.10.001.
- L. Cheng and T. Chen, “Comparison of six typical correlations for upward flow boiling heat transfer with kerosene in a vertical smooth tube,” Heat Transfer. Eng., vol. 21, no. 5, pp. 27–34, 2000. DOI: 10.1080/01457630050127928.
- L. Cheng and G. Xia, “Fundamental issues, mechanisms and models of flow boiling heat transfer in microscale channels,” Int. J. Heat Mass Transfer., vol. 108, no. Part A, pp. 97–127, May 2017. DOI: 10.1016/j.ijheatmasstransfer.2016.12.003.
- L. Cheng, “Flow patterns and bubble growth in microchannels,” in Microchannel Phase Change Heat Transfer, editor S. K. Saha, Elsevier Publisher, pp. 91–140, 2016. DOI: 10.1016/B978-0-12-804318-9.00003-0.
- L. Cheng, “Flow boiling heat transfer with models in microchannels,” in Microchannel Phase Change Heat Transfer, editor S. K. Saha, Elsevier Publisher, pp. 141–191, 2016. DOI: 10.1016/B978-0-12-804318-9.00004-2.
- Y. Lv, G. Xia, L. Cheng and D. Ma, “Experimental study on the pressure drop oscillation characteristics of the flow boiling instability with FC-72 in parallel rectangle microchannels,” Int. Comm. Heat Mass Transfer., vol. 108, pp. 104289, Nov. 2019. DOI: 10.1016/j.icheatmasstransfer.2019.104289.
- Y. Lv, G. Xia, L. Cheng and D. Ma, “Experimental investigation into unstable two-phase flow phenomena during flow boiling in multi-microchannels,” Int. J. Therm. Sci., vol. 166, pp. 106985, Aug. 2021. DOI: 10.1016/j.ijthermalsci.2021.106985.
- G. Xia, Y. Lv, L. Cheng, D. Ma and Y. Jia, “Experimental study and dynamic simulation of the continuous two phase instable boiling in multiple parallel microchannels,” Int. J. Heath Mass Transfer., vol. 138, pp. 961–984, 2019. Aug DOI: 10.1016/j.ijheatmasstransfer.2019.04.124.
- G. Xia, Y. Cheng, L. Cheng and Y. Li, “Heat transfer characteristics and flow visualization during flow boiling of acetone in semi-open multi-microchannels,” Heat Transfer. Eng., vol. 40, no. 16, pp. 1349–1362, 2019. DOI: 10.1080/01457632.2018.1470296.
- Z. Guo, et al., “Heat transfer enhancement − A brief review of literature in 2020 and prospects,” Heat Trans Res., vol. 52, no. 10, pp. 65–92, Jun. 2021. DOI: 10.1615/HeatTransRes.2021038770.
- Z. Guo, “Heat transfer enhancement − a brief review of 2018 literature,” J. Enh Heat Transf., vol. 26, no. 5, pp. 429–449, Sep. 2019. DOI: 10.1615/JEnhHeatTransf.2019031660.
- G. Xia, B. Cai, L. Cheng, Z. Wang and Y. Jia, “Experimental study and modeling of average void fraction of gas-liquid two-phase flow in a horizontal helically coiled rectangular channel,” Exp. Therm. Fluid Sci., vol. 94, pp. 9–22, Jun. 2018. DOI: 10.1016/j.expthermflusci.2018.01.027.
- B. Cai, G. Xia, L. Cheng and Z. Wang, “Flow regime visualization and identification of air–water two-phase flow in a horizontal helically coiled rectangular channel,” Heat Transfer. Eng., vol. 43, no. 8–10, pp. 720–736, 2022. DOI: 10.1080/01457632.2021.1905313.
- H. Wei, T. Cong, C. Jiang, W. Zhou and B. Bai, “Heat transfer enhancement of a partially serrated twisted finned tube with non-grooving on the leeward side,” J Enh Heat Transf, vol. 29, no. 4, pp. 41–61, 2022. DOI: 10.1615/JEnhHeatTransf.2022040235.
- T. G. Karayiannis and M. M. Mahmoud, “Flow boiling in microchannels: fundamentals and applications,” Appl. Therm. Eng., vol. 115, pp. 1372–1397, Mar. 2017. DOI: 10.1016/j.applthermaleng.2016.08.063.
- L. Cheng, “Fundamental issues of critical heat flux phenomena during flow boiling in microscale-channels and nucleate pool boiling in confined spaces,” Heat Transfer. Eng., vol. 34, no. 13, pp. 1016–1043, 2013. DOI: 10.1080/01457632.2013.763538.
- L. Cheng, G. Ribatski and J. R. Thome, “Two-phase flow patterns and flow pattern maps: fundamentals and applications,” ASME Appl. Mech. Rev., vol. 61, no. 5, pp. 50802, Sep. 2008. DOI: 10.1115/1.2955990.
- M. R. Özdemir, M. M. Mahmoud and T. G. Karayiannis, “Flow Boiling of water in a rectangular metallic microchannel,” Heat Transfer. Eng., vol. 42, no. 6, pp. 492–516, 2021., DOI: 10.1080/01457632.2019.1707390.
- R. Diaz and Z. Guo, “Enhanced conduction and pool boiling heat transfer on single-layer graphene-coated substrates,” J. Enh. Heat Transf., vol. 26, no. 2, pp. 127–143, 2019. DOI: 10.1615/JEnhHeatTransf.2018028488.
- M. Piasecka and K. Strąk, “Influence of the surface enhancement on the flow boiling heat transfer in a minichannel,” Heat Transfer. Eng., vol. 40, no. 13–14, pp. 1162–1175, 2019. DOI: 10.1080/01457632.2018.1457264.
- L. Cheng, G. Xia, Q. Li and J. R. Thome, “Fundamental issues, technology development, and challenges of boiling heat transfer, critical heat flux, and two-phase flow phenomena with nanofluids,” Heat Transfer. Eng., vol. 40, no. 16, pp. 1301–1336, 2019. DOI: 10.1080/01457632.2018.1470285.
- G. Xia, M. Du, L. Cheng and W. Wang, “Experimental study on the nucleate boiling heat transfer characteristics of a water-based multi-walled carbon nanotubes nanofluid in a confined space,” Int. J. Heat Mass Transfer., vol. 113, pp. 59–69, 2017. Oct DOI: 10.1016/j.ijheatmasstransfer.2017.05.021.
- L. Cheng, G. Ribatski, L. Wojtan and J. R. Thome, “New flow boiling heat transfer model and flow pattern map for carbon dioxide evaporating inside horizontal tubes,” Int. J. Heat Mass Transfer., vol. 49, no. 21–22, pp. 4082–4094, 2006. Oct DOI: 10.1016/j.ijheatmasstransfer.2006.04.003.
- L. Cheng, G. Ribatski, L. Wojtan and J. R. Thome, “Erratum to: new flow boiling heat transfer model and flow pattern map for carbon dioxide evaporating inside tubes, [Heat Mass Transfer 49 (21-22) (2006) 4082-4094],” Int. J. Heat Mass Transfer., vol. 50, no. 1–2, pp. 391, 2007. DOI: 10.1016/j.ijheatmasstransfer.2006.07.033.
- L. Cheng, G. Ribatski, J. Moreno Quibén and J. R. Thome, “New prediction methods for CO2 evaporation inside tubes: part I - A general two-phase flow pattern map and development of a phenomenological model of two-phase flow frictional pressure drop,” Int. J. Heat Mass Transfer., vol. 51, no. 1–2, pp. 111–124, 2008. Jan DOI: 10.1016/j.ijheatmasstransfer.2012.05.044.
- L. Cheng, G. Ribatski and J. R. Thome, “New prediction methods for CO2 evaporation inside tubes: part II - A general flow boiling heat transfer model based on flow patterns,” Int. J. Heat Mass Transfer., vol. 51, no. 1–2, pp. 125–135, Jan. 2008. DOI: 10.1016/j.ijheatmasstransfer.2007.04.001.
- J. Moreno Quibén, L. Cheng, R. J. da Silva Lima and J. R. Thome, “Flow boiling in horizontal flattened tubes: part I—Two-phase frictional pressure drop results and model,” Int. J. Heat Mass Transfer., vol. 52, no. 15–16, pp. 3634–3644, Jul. 2009. DOI: 10.1016/j.ijheatmasstransfer.2008.12.032.
- J. Moreno Quibén, L. Cheng, R. J. da Silva Lima and J. R. Thome, “Flow boiling in horizontal flattened tubes: part II—Flow boiling heat transfer results and model,” Int. J. Heat Mass Transfer., vol. 52, no. 15–16, pp. 3645–3653, Jul. 2009. DOI: 10.1016/j.ijheatmasstransfer.2008.12.033.
- J. Patiño, et al., “A comparative analysis of a CO2 evaporator model using experimental heat transfer correlations and a flow pattern map,” Int. J. Heat Mass Transfer., vol. 71, pp. 361–375, Apr. 2014. DOI: 10.1016/j.ijheatmasstransfer.2013.12.027.
- Q. Wang, J. Xu, C. Zhang, B. Hao and L. Cheng, “A critical review on heat transfer of supercritical fluids,” Heat Transfer. Eng., vol. 44, pp. 1–26, 2023. DOI: 10.1080/01457632.2022.2164684.
- B. Liu, M. Lu, B. Shui, Y. Sun and W. Wei, “Thermal-hydraulic performance analysis of printed circuit heat exchanger precooler in the Brayton cycle for supercritical CO2 waste heat recovery,” Appl. Energy, vol. 305, pp. 117923, Jan. 2022. DOI: 10.1016/j.apenergy.2021.117923.
- L. Chai and S. A. Tassou, “Performance analysis of heat exchangers and integrated CO2 supercritical Brayton cycle for varying heat carrier, cooling and working fluid flow rates,” Heat Transfer. Eng., vol. 44, no. 16–18, pp. 1498–1518, 2023. DOI: 10.1080/01457632.2022.2140640.
- H. Zhang, J. Guo, X. Huai, K. Cheng and X. Cui, “Studies on the thermal-hydraulic performance of zigzag channel with supercritical pressure CO2,” J. Supercrit. Fluids, vol. 148, pp. 104–115, Jun. 2019. DOI: 10.1016/j.supflu.2019.03.003.
- Y. Guo, Z. Luo and L. Zhao, “Enhanced flow boiling of open mini-channel and jet impingement cooling scheme by separating liquid-vapor pathways,” J. Enh. Heat Transf., vol. 29, no. 5, pp. 19–36, 2022. DOI: 10.1615/JEnhHeatTransf.2022040822.
- W. Zheng, T. Chen, P. Sen and B. Bai, “Jet impingement boiling on monocrystalline silicon surfaces with open microchannels,” Heat Transfer. Eng., vol. 44, no. 16–18, pp. 1554–1562, 2023. DOI: 10.1080/01457632.2022.2140636.
- L. Chai and S. A. Tassou, “Recent progress on high temperature and high-pressure heat exchangers for supercritical CO2 power generation and conversion systems,” Heat Transfer. Eng., vol. 44, pp. 1–19, 2023. DOI: 10.1080/01457632.2022.2164683.
- Z. Ren, L. Zhang, C.-R. Zhao, P.-X. Jiang and H.-L. Bo, “Local flow and heat transfer of supercritical CO2 in semicircular zigzag channels of printed circuit heat exchanger during cooling,” Heat Transfer. Eng., vol. 42, no. 22, pp. 1889–1913, 2021. DOI: 10.1080/01457632.2020.1834205.
- Z.-Y. Liu, L. Cheng and H. Chen, “Molecular dynamics study of CO2 phase change transport in the near-critical region: model parameter optimization,” Heat Transfer. Eng., vol. 44, no. 16–18, pp. 1544–1553, 2023. DOI: 10.1080/01457632.2022.2140635.
- Q. Wang, X. Huang, B. Xu, Q. Chen and H. Wang, “Numerical study on heat transfer and flow characteristics of supercritical CO2 in printed circuit heat exchangers with zigzag channels,” Heat Transfer. Eng., vol. 44, pp. 1–17, 2023. DOI: 10.1080/01457632.2022.2164679.
- W.-X. Chu, K. Bennett, J. Cheng, Y.-T. Chen and Q.-W. Wang, “Thermo-hydraulic performance of printed circuit heat exchanger with different cambered airfoil fins,” Heat Transfer. Eng., vol. 41, no. 8, pp. 708–722, 2020. DOI: 10.1080/01457632.2018.1564203.
- L. Chai and S. A. Tassou, “Modeling and evaluation of the thermohydraulic performance of compact recuperative heat exchangers in supercritical carbon dioxide waste heat to power conversion systems,” Heat Transfer. Eng., vol. 43, no. 13, pp. 1067–1082, 2022. DOI: 10.1080/01457632.2021.1943833.
- M. Saeed, A. S. Berrouk, M. S. AlShehhi and Y. F. AlWahedi, “Numerical investigation of the thermohydraulic characteristics of microchannel heat sinks using supercritical CO2 as a coolant,” J. Supercrit. Fluids, vol. 176, pp. 105306, Oct. 2021. DOI: 10.1016/j.supflu.2021.105306.
- Y. Lei and Z. Chen, “Cooling heat transfer and pressure drop of supercritical CO2 in wavy microchannels with consistent and opposite crests and troughs,” Int. J. Refrig., vol. 109, pp. 64–81, Jan. 2020. DOI: 10.1016/j.ijrefrig.2019.07.015.
- D. Wang, Y. Wang, B. Yua, J. Shi and J. Chen, “Numerical study on heat transfer performance of micro-channel gas coolers for automobile CO2 heat pump systems,” Int. J. Refrig., vol. 106, pp. 639–649, Oct. 2019. DOI: 10.1016/j.ijrefrig.2019.02.023.