ABSTRACT
Chemical-grade zirconium contains about 1–3 wt% hafnium, which is harmful for nuclear applications due to its high neutron-capture cross section. In the present paper, Zr-Hf separation in Sn-Cu-Zr-Hf and Cu-Zr-Hf alloy systems using molten salt containing CuCl2 or CuF2 was thermodynamically evaluated and lab-scale experiments on zirconium and hafnium separation in different molten salt systems were conducted. The best single-step Hf removal efficiency and Zr-Hf separation factor of about 95% and 9.0, respectively, were obtained with a NaCl-CaCl2-CuCl2 (3 wt%) molten salt system at 850°C and the CuCl2/Hf stoichiometric ratio of 1.5.
Introduction
Zirconium is ideal for nuclear energy applications as a cladding material (in the form of zircaloy) for fuel elements to form the fuel rod due to its very low absorption cross section for thermal neutrons and excellent corrosion-resistance properties. The thermal or slow neutrons are not absorbed and wasted during nuclear reactions, making the reactor work at a high efficiency.[Citation1, Citation2] Very pure Zr is needed to make the zircaloy, which contains about 98% Zr plus about 1.5% tin, also iron, chromium, and sometimes nickel to enhance its strength. Hafnium has a strong affinity for zirconium, so that in nature zirconium is always found in combination with 1–3 wt% of hafnium. The two elements can remain unseparated for all uses, except for nuclear applications due to their extremely opposite absorption characteristics for thermal neutrons. For its use as a nuclear material, zirconium is required to be free of hafnium, or at least the hafnium content should be less than 100 ppm. However, separating hafnium from zirconium is a challenging issue due to the great similarities in their physicochemical properties. Therefore, Zr-Hf separation has been a topic of investigation since the discovery of hafnium through the crystal bar process.[Citation3]
The annual global zirconium metal production/consumption is estimated to be around 7000 t/year, and about 85% of that, 5000–6000 t/year, goes into the nuclear industry. The demand for nuclear-quality zirconium is now rising rapidly due to the increased numbers of nuclear reactors worldwide. Hundreds of nuclear power plants are being or planning to be constructed in many countries. However, only a few companies (Wah Chang, Westinghouse, Cezus, etc.) in the USA, France, and Russia possess the nuclear-grade zirconium production technology.[Citation4]
A number of Zr-Hf separation technologies have been developed in the past decades, which can be roughly classified into hydro- and pyrometallurgical routes.[Citation4] However, there is still no dominant Zr-Hf separation method available so far. There are three established hydrometallurgical technologies for separating hafnium from zirconium: fractional crystallization, ion exchange, and solvent extraction. The fractional crystallization process is simple in operation and was applied in the nuclear industry for many years, but it was then substituted by solvent extraction and extractive distillation processes due to its multistep characteristics and low process efficiency.[Citation5] Ion exchange can effectively separate similar ions from each other in aqueous solutions.[Citation6] The selectivity of this process is determined by the type of ion exchange resins and the composition of solutions. It has been proved to be possible to obtain nuclear-grade zirconium by removing hafnium via the ion exchange process, but the high cost of the ion exchange resins is the main obstacle for industrial application. Solvent extraction with methyl isobutyl ketone (MIBK) and tributyl phosphate (TBP) as the solvents is the most commonly used hydrometallurgical method for Zr-Hf separation on industrial scale.[Citation7, Citation8] It has the advantages of high treatment capacity, low operating temperature, and simplicity in operation. However, it needs many stages of separation to approach the nuclear-quality product, and the hafnium-free zirconium compounds purified by this process always require some additional pyrometallurgical operations of calcination, chlorination, and the reduction with Kroll process to obtain the final zirconium metal product. The complex combination of the hydro- and pyrometallurgical operations makes the whole production process lengthy, and accordingly leads to the high production costs. In pyrometallurgy, the known separation methods were developed based on the following reaction features: redox characteristics,[Citation9, Citation10] volatility,[Citation11–Citation14] electrochemical properties,[Citation15–Citation17] and molten salt extraction.[Citation18, Citation19] Among all these methods, the extractive distillation process is a significant advance in Zr-Hf separation technology,[Citation14] which is the only industrialized pyrometallurgical Zr-Hf separation method. It achieves continuous operation at atmospheric pressure and a relatively low temperature (~500°C) and has a good compatibility for the Kroll process. However, the high process maintenance cost leads to expensive products as well. Megy made the first attempt to remove hafnium from zirconium with molten salt extraction.[Citation18] The molten salt system consisting of NaCl, KCl, and Na2ZrF6 comes into contact with the molten alloy of Zn-Zr-Hf at approximately 775°C. With this approach, the Hf in the molten metal phase is extracted into the molten salt phase. However, due to the low reaction rate between Zr4+ and Hf, an intensive agitation and relatively long reaction time are needed to decrease the Hf content to the nuclear-grade level. Xiao and Sandwijk developed a compact process for nuclear-grade zirconium production from crude zirconium ore.[Citation19] The flowsheet of the process is shown in . The purification compartment for Zr-Hf separation is the key of the whole process, which provides a higher thermodynamic separation potential at a similar temperature compared to Megy’s work. In the molten salt phase, CuCl2 is served as the oxidizer that could preferentially extract Hf into the salt phase and the reduced Cu is transferred into the low melting alloy. In both studies by Megy,[Citation18] and by Xiao and Sandwijk,[Citation19] producing nuclear-quality Zr alloy by one-step separation was proved to be technically feasible; however, the very low Zr solubility in the metal solvents results in limited process efficiency, which needs to be optimized.
Figure 1. Flowsheet of the nuclear-grade zirconium production process developed by Xiao and Sandwijk.[Citation19]
![Figure 1. Flowsheet of the nuclear-grade zirconium production process developed by Xiao and Sandwijk.[Citation19]](/cms/asset/8078e052-3b02-4930-b191-fde3a9f8db1b/lsst_a_1170852_f0001_oc.jpg)
As summarized earlier, molten salt extraction was found to be a promising method for Zr-Hf separation even though it has the disadvantage of low process efficiency. Up to now, only Megy’s study and the study by Xiao and Sandwijk are found from open literature in this field, which means the scientific study on Zr-Hf separation with molten salt extraction is still very limited. In the present paper, a modified Zr-Hf separation process based on the concept of molten salt extraction was proposed with the aim of further improving the process efficiency of the study by Xiao and her co-workers.[Citation19, Citation20] The influence of various parameters was investigated, including Zr alloy composition, in particular, the Zr solubility in the molten alloy, salt composition, CuCl2 (CuF2) content, CuCl2 (CuF2)/Hf stoichiometric ratio, and operation temperature. As part of the total purification route, the purified Hf-free Zr alloy can be processed with molten salt electrolysis for pure Zr metal recovery from Cu- or Cu-Sn-based solvents utilizing their very different redox potentials. The produced Zr from molten salt electro-refining should be maintained as a dense deposit on the cathode by properly controlling the cell operating conditions to avoid the pyrophoricity of the Zr metal product. In case a sponge product is formed on the cathode, the cell will be protected or encapsulated in an inert gas chamber for Zr sponge compacting before further melting and casting.
Thermodynamic evaluation
The selective extraction of Hf from a molten Zr alloy is based on the fact that the hafnium reaction with CuCl2 (CuF2)-bearing molten salt is thermodynamically more in favor than the reaction of zirconium. The involved equilibrium reactions with CuCl2-bearing molten salt as the extractant and the equilibrium constants are shown in Eqs. (1) and (2), and the reactions using a CuF2-containing molten salt system and the equilibrium constants are described in Eqs. (3) and (4). According to Eqs. (2) and (4), the theoretical stoichiometric ratio of CuCl2 (CuF2) in the salt to Hf in the alloy is 2 mole of CuCl2 (CuF2) per 1 mole of Hf. (a) shows the equilibrium constant of the reactions of Hf with CuCl2 and CuF2 as a function of temperature, and (b) illustrates the equilibrium constant ratio of the reactions of Hf and Zr with CuCl2 and CuF2, respectively, within a temperature range from 600 to 1500°C.
Figure 2. Equilibrium constants of the Hf reactions with CuCl2 and CuF2 as function of temperature (a) and equilibrium constant ratio for the reactions of Zr and Hf with CuCl2 and CuF2 as a function of temperature (b), calculated with HSC chemistry.[Citation21]
![Figure 2. Equilibrium constants of the Hf reactions with CuCl2 and CuF2 as function of temperature (a) and equilibrium constant ratio for the reactions of Zr and Hf with CuCl2 and CuF2 as a function of temperature (b), calculated with HSC chemistry.[Citation21]](/cms/asset/ed8b5064-89a7-4c92-8a55-09e4a207f0d4/lsst_a_1170852_f0002_oc.jpg)
(a) demonstrates the significant higher Hf removal capacity of CuF2 than CuCl2 in the temperature range from 600 to 1500°C. It is obviously recognized from (b) that the driving force of the reaction between Hf and CuCl2 (CuF2) is thermodynamically several times larger than that between Zr and CuCl2 (CuF2). However, either with CuCl2 or CuF2, the driving force difference of the reactions of Hf and Zr shows a continuous downward trend with increasing temperature, which means that a higher temperature is not favourable for selective removal of Hf. It can also be observed that at a temperature lower than 1000°C, CuF2 is more effective for Zr-Hf separation than for CuCl2, and above 1100°C a CuCl2-containing molten salt system shows a better selectivity to Hf removal. It is well known that a chloride system is generally much more volatile than fluoride; therefore, in addition to the melting point of the alloy system, the chosen operation temperature will also be limited by the vapour pressure of the molten salts (chlorides and/or fluorides), and by the thermodynamic driving force and selectivity of Hf removal.
Experimental
Materials
Chemical-grade reagents were used for all the experiments. Two different types of salts were used: chlorides and fluorides. Anhydrous sodium chloride (NaCl, 99.8% purity), magnesium chloride (MgCl2, 99% purity), lithium chloride (LiCl, 99% purity), calcium chloride (CaCl2, 99.99% purity), copper chloride (CuCl2, 98% purity), sodium fluoride (NaF, 99% purity), calcium fluoride (CaF2, 99.5% purity), and copper fluoride (CuF2, 99.5% purity) were used for preparing the molten salt. Metallic copper (Cu, 99.9% purity), zirconium (Zr, 99.8% metal basis with max. 4% Hf), and hafnium (Hf, 99.9% purity) were used for preparing the molten alloy. Argon gas (Ar, 99.999% purity) was used as protective atmosphere for all the experiments.
Experimental procedures
The salt powders with designed compositions were mechanically mixed at first and then placed in an alumina crucible (Alsint) for premelting in order to achieve homogeneous salt phase prior to the equilibrium experiments. The salt mixtures were fused at 750–900°C for 2 h and then naturally cooled to room temperature. Two types of master alloy containing minor hafnium were prepared based on the Sn-Cu-Zr ternary and Cu-Zr binary systems, respectively. The former contains about 55–60 wt% Sn, 40–45 wt% Cu, and 2 wt% Zr with low melting temperature (650–700°C), and the latter has a Cu/Zr weight ratio of approximately 1:1 with a relatively higher melting temperature (c.a. 920°C). The metallic Sn turnings, Cu powder, Zr lumps, and Hf turnings with the expected composition were put into an MgO crucible and a NaCl-KCl-Cryolite salt mixture was placed on the top covering the metal phase to avoid oxidation during the alloying process. The master alloy was prepared at 1200°C for 2 h. Both the master salt and master alloy were prepared in an EHS vertical electrical resistant tube furnace under a pure argon atmosphere. The well-prepared master alloy was cut into pieces of about 5 g each and the premelted salt mixtures were grounded into powders in a mortar. Then, the mixture of the alloy and salt was charged in an MgO crucible according to the designed CuCl2 (CuF2)/Hf stoichiometric ratio. Three crucibles were placed in a larger Alsint boat, which was put inside a Carbolite electrical-resistant horizontal tube furnace for the equilibrium reactions. With this approach, the same experimental conditions such as temperature, reaction time, and atmosphere can be guaranteed for investigating the influence of different CuCl2 (CuF2)/Hf ratios. The samples were heated to a certain operation temperature (850, 1000, or 1100°C, depending on different reaction systems) and kept constant for 2 h under an argon atmosphere, which was purified beforehand by potassium hydroxide, silica gel, phosphorus pentoxide, and hot titanium sponge (850°C) with a flow rate of 1 L/h. After the end of experiment, the furnace was allowed to cool down naturally to about 200°C and then the sample was taken out. The alloy sample was separated from the salt phase for analysis. The Sn-Cu-Zr-Hf alloy sample was analysed by ICP-OES in particular for the low concentration of hafnium, and the composition determination of the Cu-Zr-Hf alloy sample was performed with X-ray fluorescence spectrometry (XRF, PANalytical Axios). The schematic diagram of the experimental set-up is shown in .
Results and discussion
Hf removal efficiency and Zr-Hf separation factor
For the equilibrium experiments, the hafnium removal efficiency (α) and Zr-Hf separation factor (β) are the two most important indexes. The removal efficiency is determined as the relative difference of Hf content in the alloy before and after the reactions, as shown in Eq. (5), and the separation factor is referred to the change of hafnium to zirconium weight ratio before and after the reactions, which is defined in Eq. (6).
Zr-Hf separation in Sn-Cu-Zr-Hf alloy system
Equilibrium experiments on Zr-Hf separation were conducted initially in an Sn-Cu-Zr-Hf alloy system consisting of approximately 55–60 wt% Sn, 40–45 wt% Cu, and 2 wt% Zr containing Hf at the same level of crude ore (1–3 wt% Hf in Zr). The Sn-Cu binary system was chosen as the alloy basis in order to have a low alloy melting point of about 700°C and further to achieve a relatively low operation temperature. The equilibrium between the alloy and salt phases is preferred to be performed in both molten states because the species diffusion and mass transfer are much faster than that in the solid states. Three CuCl2-bearing all-chloride molten salt systems were used as the extractants with the basis of NaCl-MgCl2, NaCl-LiCl, and NaCl-CaCl2 respectively in their eutectic compositions.
(a) and (b) show the results of three series of Zr-Hf separation experiments at 850°C with the three different molten salt extractants. It can be clearly seen that the MgCl2-based salt system generally gives the highest Hf removal efficiency of over 99.5% in the three experiments. It seems that MgCl2 is the best option for Hf removal, when compared to LiCl and CaCl2. However, in addition to hafnium, the remaining zirconium in the alloy was determined to be very low when using MgCl2, resulting in very poor Zr-Hf separation factor of below 0.5, which means a large amount of zirconium got lost into the molten salt phase together with hafnium through the equilibrium reaction. Although thermodynamic evaluation indicates that MgCl2 reacts with neither Zr nor Hf in the molten alloy phase at the operation temperature, it could probably influence the activity of CuCl2 in the molten salt and degrade the selectivity between zirconium and hafnium. For the reaction systems based on NaCl-LiCl salt, the CuCl2/Hf stoichiometric ratio has a positive effect on Hf removal efficiency. The best hafnium removal was obtained at the stoichiometric ratio of 2; however, the corresponding separation factor was the lowest among the three experiments, which is mainly due to the over-charge of CuCl2 consuming also most of the zirconium. The best Zr-Hf separation factor was reached at the stoichiometric ratio of 1.5, as to be 7.9. Similarly, an NaCl-CaCl2 based salt system gives the highest separation factor of 8.9 at the stoichiometric ratio of 1.5, with the corresponding Hf removal efficiency to be 95%.
Figure 4. Hf removal efficiency (a) and Zr–Hf separation factor (b) as a function of CuCl2/Hf stoichiometric ratio at 850°C with NaCl–MgCl2–CuCl2, NaCl–LiCl–CuCl2, and NaCl–CaCl2–CuCl2.

The effect of CuCl2 concentration in the NaCl-CaCl2 salt system on Hf separation was further investigated at the CuCl2/Hf stoichiometric ratio of 1.5 and the operation temperature of 850°C, and the results are shown in (a) and (b). It can be seen that both Hf removal efficiency and Zr-Hf separation factor were improved significantly while increasing the CuCl2 content in the molten salt from 1.5 to 3 wt%. The increased copper chloride concentration in the salt can improve its activity and further enhance the Hf removal.
Zr-Hf separation in Cu-Zr-Hf alloy system
As illustrated in section titled “Zr-Hf Separation in Sn-Cu-Zr-Hf Alloy System”, in an Sn-Cu-Zr-Hf low melting alloy system, a very good Zr-Hf separation can be achieved with a single-step Hf removal efficiency of as high as 95% and Zr-Hf separation factor of about 9.0 at a relatively low operation temperature. However, it was also noticed that using Sn as the solvent metal, on the one hand, could effectively decrease the alloy melting point, on the other hand, it greatly reduces zirconium solubility,[Citation22] which results in a low process efficiency. Therefore, the selection of solvent metal needs to be reconsidered. According to the Cu-Zr binary phase diagram as shown in ,[Citation23] at a temperature of about 920°C, about 50–60 wt% zirconium can be dissolved into copper, which means by using Cu as the solvent metal, the Zr solubility could get more than a tenfold increase from below 5 wt% to approximately 50 wt%, compared to using the Sn-Cu binary system. Although the melting point of the alloy has an increase of approximately 200°C, which will in turn result in an increase in operation temperature, it will lead to a substantial enhancement in Zr solubility. shows the DSC curve of the well-prepared Cu-Zr-based alloy, which contains approximately 50 wt% Zr and 2 wt% Hf. An endothermic peak at 903°C can be clearly observed during the heating process, which is believed to be attributed by the phase change (melting) of the solid alloy into molten state. The experimentally determined alloy melting point is basically consistent with the reported binary Cu-Zr phase diagram. However, a much higher operating temperature is required, which is conversely limited by the high vapour pressure of the molten salt and the reduced thermodynamic driving force for Zr-Hf separation.
Figure 6. Cu–Zr binary phase diagram.[Citation23]
![Figure 6. Cu–Zr binary phase diagram.[Citation23]](/cms/asset/9987474e-1da3-49b4-b640-f531ec8e5afd/lsst_a_1170852_f0006_b.gif)
Zr-Hf separation with CuCl2-bearing molten salt systems
Representative results of the extraction experiments conducted at 1000°C with CuCl2-bearing molten salt systems are shown in (a) and (b). For the experiments using a full chloride salt system as the extractant, the molten salt mixture consisted of equimolar amount of NaCl-CaCl2 with 3 wt% CuCl2 and the CuCl2/Hf stoichiometric ratio varied from 0.75 to 5. As can be clearly seen from that the Zr-Hf separation efficiency of all these four experiments was generally poor and it was slightly influenced by the increase of CuCl2/Hf ratio. It is believed that the low reactivity/selectivity of CuCl2 in the molten salt to Hf is the reason for the low separation efficiency. One trial showed that the CuCl2 content was increased from 3 wt% to 10 wt% in order to have a higher CuCl2 activity in the salt phase. However, it was observed that about 40 wt% of the salt was evaporated during the 2-h reaction at 1000°C, and accordingly, serious salt evaporation resulted in an even worse Hf separation from Zr. From this experiment, it can be deduced that the operating temperature of 1000°C is too high for the chloride salt system, or if using chloride salt, the CuCl2 content should be controlled at a relative low level, leading to a narrow operation window. Therefore, in the following extraction experiments, as also shown in , the major components of the salt system, NaCl and CaCl2, were replaced by their corresponding fluorides, NaF and CaF2, respectively, and the concentration of the key component CuCl2 was kept unchanged at 10 wt%. In this way, the melting point of the salt mixture was increased and the vapour pressure at the operation temperature was lowered, and accordingly the influence of the salt evaporation (generally about 3 wt% weight loss) on Zr-Hf separation could be largely reduced.
Figure 8. Hf removal efficiency (a) and Zr–Hf separation factor (b) as a function of CuCl2/Hf stoichiometric ratio at 1000°C with CuCl2–NaCl–CaCl2 and CuCl2–NaF–CaF2 salt systems.
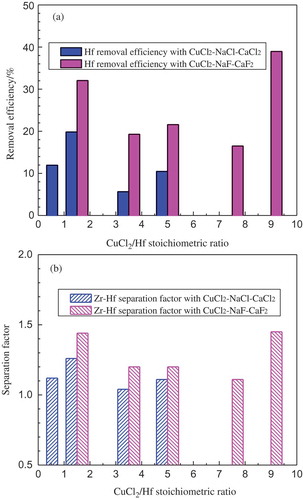
In the five experiments with a CuCl2-NaF-CaF2 salt system, the studied CuCl2/Hf stoichiometric ratio ranged from 1.5 to 9. A CuCl2/Hf stoichiometric ratio of as high as 9 was tried in the last case in order to guarantee an excessive amount of CuCl2 for the equilibrium reactions. In general, the change of CuCl2/Hf ratio shows no significant influence on Zr-Hf separation. Among the five experiments, the better Zr-Hf separation efficiency was obtained in the cases with the CuCl2/Hf stoichiometric ratio of 1.5 and 9 that the Hf removal efficiency and separation factor were approximately 35% and 1.5, respectively. In the case with the stoichiometric ratio of 9, the amount of CuCl2 in the salt is 9 times of the theoretical need of CuCl2 for the complete Hf removal. The excess CuCl2 will definitely react with Zr in the molten alloy also, leading to serious Zr loss into the salt phase, which is not desired. Therefore, conducting the extraction experiment with a lower CuCl2/Hf ratio is preferable. Moreover, looking at (a) and (b) generally, at the CuCl2/Hf stoichiometric ratios of 1.5, 3.5, and 5, the molten salt system of CuCl2-NaF-CaF2 delivers a better Zr-Hf separation efficiency than CuCl2-NaCl-CaCl2, which means that the enhancement in Zr-Hf separation was achieved by replacing NaCl-CaCl2 with the corresponding fluorides of NaF-CaF2 in the molten salt. However, the Zr-Hf separation is in general not efficient as compared to the previous studies using Sn-Cu–based low melting alloys.
Zr-Hf separation with CuF2-bearing molten salt systems
As thermodynamically evaluated in section titled “Thermodynamic evaluation”, CuF2 has a higher capacity of oxidizing Hf into the corresponding hafnium halide than that of CuCl2 within a temperature range of 600–1500°C (as seen in (a)), and a CuF2-containing molten salt system has a better selectivity to Hf than that containing CuCl2 as the extraction reagent to selectively extract Hf from a Cu-Zr-Hf molten alloy to the fused salt phase at a temperature below 1050°C (as seen in (b)). Therefore, separating Hf with a full fluoride salt system by replacing CuCl2 with CuF2 was systematically investigated. The separation experiments were conducted using a molten fluoride salt mixture containing 10 wt% CuF2 with the CuF2/Hf stoichiometric ratio changing from 1 to 4 at the operation temperatures of 1000 and 1100°C, respectively. Although 1100°C provides a lower extraction capacity of CuF2 to Hf than 1000°C and shows also a lower selectivity between Hf and Zr based on the thermodynamic evaluation, it could probably offer faster reactions to the equilibrium. Because generally a higher temperature could decrease the viscosities of both the molten phases, and the diffusion of the reactants and products is accordingly accelerated, which could be favourable to the extraction process.
As can be seen from (a) and (b), at the operation temperatures of 1000 and 1100°C, the variations of both Hf removal efficiency and separation factor showed a similar tendency, and their corresponding values do not show a big difference. Therefore, an operation temperature of 1000°C is believed to be more preferable for the present reaction system due to lower energy consumption. It can also be seen that at both operation temperatures the best Hf removal efficiency and Zr-Hf separation factor were obtained with a CuF2/Hf stoichiometric ratio of 2, which were 46.7% and 1.9 at 1000°C, and at 1100°C the corresponding values were 45.3% and 1.7, respectively. The lower stoichiometric ratio of 1 probably provides insufficient copper ions for the Hf removal reaction and the higher CuF2/Hf stoichiometric ratios of 3 and 4 make more Zr consumed than Hf, leading to a lower Zr-Hf separation efficiency.
Figure 9. Hf removal efficiency (a) and Zr–Hf separation factor (b) as a function of CuF2/Hf stoichiometric ratio with the salt containing 10 wt% CuF2 at 1000 and 1100°C.
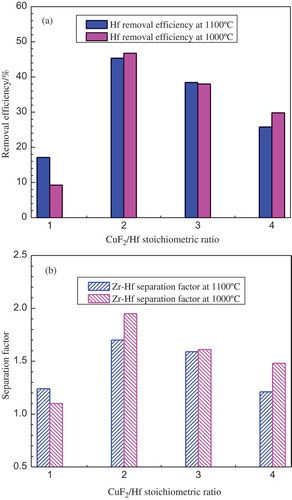
The influence of CuF2 content in the salt on Zr-Hf separation was studied and the results are shown in (a) and (b). All the experiments were conducted at 1000°C with a CuF2/Hf stoichiometric ratio of 2. It can be clearly seen from that the Zr-Hf separation efficiency shows an upward trend with the increase of CuF2 content in the salt and the best Hf removal efficiency and Zr-Hf separation factor were obtained with using the molten salt containing 10 wt% of CuF2. In the cases with the lower CuF2 contents of 3 wt% and 6 wt%, the results turned out to have very poor Zr-Hf separation that both the Hf removal efficiencies were below 6% and the values of separation factor were 0.89 and 1.00, respectively. In other words, the salt system that contains 6 wt% of CuF2 made no contribution to Zr-Hf separation at all, and when the CuF2 content was decreased to 3 wt%, even more percentage of Zr got lost into the fused salt phase than Hf removal after the equilibrium reactions. It is likely that the lowered CuF2 concentration in the salt decreased its activity, which subsequently degraded the driving force of the Hf removal reaction. A CuF2 content of higher than 10 wt% was not tested. If the initial stoichiometric ratio of CuF2/Hf is fixed to be 2, the higher CuF2 content will lead to a very low volume ratio of salt to metal, leading to an undesirable equilibrium condition that the molten salt phase could not fully cover the metal phase during the equilibrium process.
Figure 10. Hf removal efficiency (a) and Zr-Hf separation factor (b) as a function of CuF2 concentration at the CuF2/Hf stoichiometric ratio of 2 and 850°C.
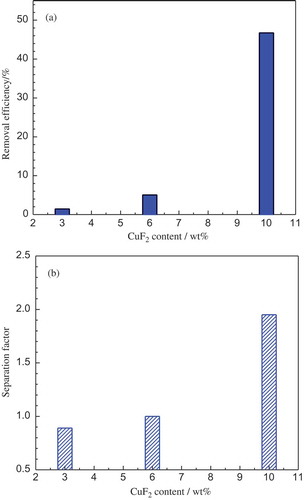
For using full fluoride salt system as the extractant, the equilibrium constant ratio of the CuF2 reaction with Hf to that with Zr can be described in Eq. (7), by combining Eq. (3) with Eq. (4).
Assuming that the activity coefficient of each species in the reaction system is unity, the value of activity is equal to the corresponding mole fraction, and Eq. (7) can be transformed into Eq. (8). As is a constant at a given temperature, thus in order to have a low Hf content in the alloy phase, the only way is to increase the ZrF4 content in the salt phase because the changes of Zr in the alloy can be ignored, and the HfF4 content in the salt is directly related to the extent of the Hf removal reaction.
Considering the whole reaction system, only the reaction of Zr in the alloy with CuF2 can generate ZrF4 into the molten salt phase, but this reaction is not desirable for Zr-Hf separation. The extent of the Zr reaction with CuF2 will be greatly limited by strictly controlling the initial content of CuF2 in the salt to be well sufficient for the thermodynamically more preferred Hf removal reaction. Therefore, the ZrF4 from the reaction between CuF2 and Zr is very limited and in order to have an influential ZrF4 content in the salt, the only way is to add extra the species externally.
Several attempts have been made with different amounts of additional ZrF4 in the molten salt system to improve Zr-Hf separation efficiency. However, generally, the addition of ZrF4 in the salt phase did not give an apparent enhancement in Zr-Hf separation as thermodynamically expected. This is likely due to the purity level of the ZrF4, which contains also HfF4 at the same level of the alloy phase. In this case, ZrF4 addition could not make contributions to Zr-Hf separation at all. The addition of pure ZrF4 is expected to be helpful for Hf removal, but it is in conflict with the purpose of the process of producing Hf-free zirconium, making the process self-defeating.
Comparing the Zr-Hf separation in Sn-Cu-Zr-Hf and Cu-Zr-Hf alloy systems in general, the Sn-Cu-Zr-Hf alloy system gives a very high single-step separation efficiency when using a NaCl-CaCl2-CuCl2 molten salt system as the extractive reagent, whereas the highest Hf removal efficiency obtained in the Cu-Zr-Hf system was just approximately 50% among the numerous attempts, which is much lower than that in the Sn-based alloy. Although the component of Sn is unfavourable for Zr solubility and results in relatively low process efficiency, it could substantially lower the alloy melting point and further decrease the operation temperature. As thermodynamically evaluated, a low operation temperature is always favourable for both Hf removal and Zr-Hf selectivity either with chlorides or with fluorides as the extractive reagent, which could probably be the main reason for the far higher Zr-Hf separation efficiency in Sn-Cu-Zr-Hf than that in Cu-Zr-Hf system. Moreover, from the species interaction point of view, the presence of Sn could possibly have varying degrees of impact on zirconium and hafnium activities in the molten state, enlarging the difference in their reactivity with the molten salt extractants. It seems, therefore, that the completely removal of Sn from the alloy system with the purpose of enhancing the Zr solubility is not an option for Zr-Hf separation. For future development, the composition of the alloy phase, in particular, the Sn concentration, should be optimized, aiming to achieve a balance between Zr solubility and melting temperature and further to achieve both good Zr-Hf separation and process efficiency.
Engineering perspectives
The present study aims to promote the molten salt extraction technology for the separation of hafnium from zirconium. The Zr-Hf separation reactor is designed to be followed by an electro-refining cell with the molten hafnium-free zirconium alloy as the anode to recover pure zirconium metal and the remaining Sn-Cu/Cu melt will be circulated back to the ZrO2 electrolysis for production of low melting Zr-Cu-Sn alloy. From engineering point of view, the process scaling-up could possibly encounter some challenges. For the electro-refining process after the Zr-Hf separation, the zirconium concentration of the molten alloy anode will be continuously changed as pure zirconium metal selectively deposits on the cathode. In order to avoid the co-deposition of Cu or Sn, the liquid anode composition, in particular the minimum Zr concentration, should be properly controlled. For the separation reactor, an inert mechanical stirrer could be installed for better mixing of the salt and alloy phases to promote faster reaction kinetics.
The transport and circulation of both liquid alloy and molten salts could be a challenge to synchronize. Properly positioning the reactors at different levels could be helpful by using the gravitational force for the melt flow from one reactor to another, instead of pumping the molten melts at high temperatures. Both Zr-Hf separation and Zr electro-refining are performed at high temperatures; the molten salt phase could be volatile and corrosive. The chloride salt system would be more advantageous than the fluoride salt system due to its lower operation temperature and less corrosive nature than fluoride salt. However, the chloride system is less favourable thermodynamically for Zr-Hf separation than the fluoride system. Lower temperature operation can also reduce energy consumption on a commercial scale. All these issues will be taken into account in the future during process upscaling phase.
Conclusions
In the present work, the separation of Hf from Zr by molten salt extraction with different molten salt systems in Sn-Cu-Zr-Hf and Cu-Zr-Hf alloy systems was comprehensively studied. The selectivity of CuCl2 and CuF2 to remove Hf from Zr was thermodynamically evaluated. Main findings of this work are listed as follows.
Thermodynamic evaluation shows that a lower temperature is favourable for separating Hf from Zr with both chloride/fluoride salts, and CuF2 has a better selectivity to Hf than CuCl2 below 1000°C.
In the Sn-Cu-Zr-Hf alloy system, the highest Hf removal efficiency and Zr-Hf separation factor were obtained to be about 95% and 9.0, respectively, using an NaCl-CaCl2-CuCl2 (3 wt%) molten salt system at 850°C and the CuCl2/Hf stoichiometric ratio of 1.5.
Sn in the alloy system was found to be effective on lowering the alloy melting point and subsequently decreasing the operation temperature, which is advantageous to Zr-Hf separation but unfavourable for Zr solubility.
In the Cu-Zr-Hf alloy system, with CuCl2-bearing salt systems, generally the Zr-Hf separation efficiency was slightly influenced by changing the CuCl2/Hf stoichiometric ratio and a CuCl2-NaF-CaF2 molten salt system delivered better separation efficiency than CuCl2-NaCl-CaCl2.
In the Cu-Zr-Hf alloy system, with CuF2-bearing salt systems, the experimental results obtained at the operation temperatures of 1000 and 1100°C did not show big difference, and the best Hf removal efficiency and Zr-Hf separation factor of approximately 47% and 2.0, respectively, were obtained at 1000°C with CuF2/Hf stoichiometric ratio of 2 using the salt system containing 10 wt% of CuF2.
Future research and development will focus on optimizing the alloy composition, in particular, the Sn content, in the alloy phase, in order to balance the Zr solubility and alloy melting point, targeting to enhance the selective Hf removal process and the process efficiency as well.
Funding
This work is conducted at Delft University of Technology (TU Delft). The financial support by the National Natural Science Foundation of China (NSFC) Grant No. 51274005 and 51174055 is acknowledged. The first author’s stay in the Netherlands is financially supported by the Chinese Scholarship Council (CSC). The authors thank Dr. Zhi Sun for his practical help in the experiments, Prof. Jilt Sietsma for his constructive discussions, and Mr. Sander van Asperen for his technical support during this work at TU Delft. Mr. Ruud Hendrikx at the Department of Materials Science and Engineering of TU Delft is acknowledged for the XRF analysis.
Additional information
Funding
References
- Banda, R.; Lee, H.Y.; Lee, M.S. (2012) Separation of Zr from Hf in hydrochloric acid solution using amine-based extractants. Industrial & Engineering Chemistry Research, 51: 9652–9660.
- Li, H.; Nersisyan, H.; Park, K.; Park, S.; Kim, J.; Lee, J. (2011) Nuclear-grade zirconium prepared by combining combustion synthesis with molten-salt electrorefining technique. Journal of Nuclear Materials, 413: 107–113.
- van Arkel, A.E.; de Boer, J.H. (1925) Darstellung von reinem Titanium-, Zirkonium-, Hafnium- und Thoriummetall. Zeitschrift Für Anorganische Und Allgemeine Chemie, 148: 345–350.
- Xu, L.; Xiao, Y.; van Sandwijk, A.; Xu, Q.; Yang, Y. (2015) Production of nuclear grade zirconium: a review. Journal of Nuclear Materials, 466: 21–28.
- Vinarov, I.V. (1967) Modern methods of separating zirconium and hafnium. Russian Chemical Reviews, 36: 522–536.
- Yang, X.J.; Pin, C.; Fane, A.G. (1999) Separation of hafnium from zirconium by extraction chromatography with liquid anionic exchangers. Journal of Chromatographic Science, 37: 171–179.
- Levitt, E.H.; Freund, A. (1956) Extraction of zirconium by TBP. Journal of the American Chemical Society, 78: 1545–1549.
- Voit, D.O. (1980) Equilibrium distribution behavior of zircony-hafnyl thiocyanates between methyl-isobutyl-ketone and aqueous phases. ISEC’80 proceedings, Belgium: 59–80.
- Mallikarjunan, R.; Sehra, J.C. (1989) Pyrometallurgical processes for the separation of hafnium from zirconium. Bulletin of Materials Science, 12: 407–434.
- Flengas, S.N.; Dutrizac, J.E. (1977) A new process for the separation of hafnium from zirconium. Metallurgical Transactions B, 8B: 377–385.
- Besson, P.; Guerin, J.; Brun, P.; Bakes, M. Process for the separation of zirconium and hafnium tetrachlorides from mixtures thereof. U.S. Patent 4021531, May 3, 1977.
- McLaughlin, D.F.; Stoltz, R.A. Zirconium and hafnium tetrachloride separation by extractive distillation with molten zinc chloride lead chloride solvent. U.S. Patent 4737244, April 12, 1988.
- Sathiyamoorthy, D.; Shetty, S.M.; Bose, D.K.; Gupta, C.K. (1999) Pyrochemical separation of zirconium and hafnium tetra-chlorides using fused salt extractive distillation process. High Temperature Materials and Processes, 18: 213–226.
- Niselson, L.A.; Egorov, E.A.; Chuvilina, E.L.; Arzhatkina, O.A.; Fedorov, V.D. (2009) Solid-liquid and liquid-vapor equilibria in the Zr(Hf)Cl4-KAlCl4 systems: A basis for the extractive distillation separation of zirconium and hafnium tetrachlorides. Journal of Chemical & Engineering Data, 54: 726–729.
- Kirihara, T.; Nakagawa, I.; Seki, Y.; Honda, Y. Process of separation of hafnium from zirconium by molten salt electrolysis. U.S. Patent 4857155, August 15, 1989.
- Kirihara, T.; Nakagawa, I.; Seki, Y.; Honda, Y.; Ichihara, Y. Process for separation of hafnium tetrachloride from zirconium tetrachloride. U.S. Patent 5009751, April 23, 1991.
- Salylev, A.B.; Kudyakov, V.Y.; Smirnov, M.V.; Moskalenko, N.I. (1985) Separation of hafnium and zirconium in solution of their tetrchlorides in molten alkali-metal chlorides. Journal of Applied Chemistry of the USSR, 57: 1710.
- Megy, J.A.; Freund, H. (1979) The separation of zirconium and hafnium in a molten salt-molten zinc system. Metallurgical Transactions B, 10B: 413–421.
- Xiao, Y.; van Sandwijk, A. Process for separating hafnium and zirconium. European Patent 20090160442, November 18, 2010.
- Xiao, Y.; van Sandwijk, A.; Yang, Y.; Laging, V. (2014) New routes for the production of reactor grade zirconium. Molten Salt Chemistry and Technology, 1st ed.; John Wiley & Sons, Ltd., pp. 391–401.
- Roine, A. (2007) HSC Chemistry, Version 6.1, Outotec Research Oy, Pori, Finland.
- Pi, C.; Li, G.; Xiao, Y.; Zhang, Z.; Zhao, Z.; Yang, Y. (2014) An experimental investigation on the solubility of Zr in Cu-Sn alloys. Advanced Materials Research, 887–888:324–328.
- Okamoto, H. (2012) Cu-Zr (Copper-Zirconium). The Journal of Phase Equilibria and Diffusion, 33: 417–418.