Abstract
The moisture resistance of friction-welded wood joints can be improved by applying bio-based bonding additives. Several biomolecules including tannic acid, organosolv lignin from hardwood, kraft lignin from softwood, and derivates thereof, were investigated regarding their applicability as bonding additives in the friction welding process. Welding with kraft lignin showed significantly increased moisture stability after 24 h water immersion. An average wet bond strength of 1.5 MPa compared to 0.38 MPa of untreated spruce was obtained. Modification of kraft lignin through succinylation, acetylation or depolymerisation led to no further improvement in moisture stability. Depolymerised kraft lignin resulted in an even higher delamination rate of the samples during water immersion than untreated samples. Structural analysis of the lignin variations by FTIR-ATR, GPC and 31P NMR in combination with thermal analysis by TGA and DSC showed the impact of various structural and chemical features on the thermal behaviour and intermolecular interactions of the applied lignin.
1. Introduction
In view of increasing depletion of fossil and mineral-based resources, high anthropological CO2 emissions and environmental pollution, a substitution of conventional fossil-based materials by renewable and biodegradable materials is an important step towards sustainable future societies [Citation1–5]. Wood, as a biodegradable material with high CO2 sequestering capability, is a resource with comparably low environmental impact, while exhibiting excellent mechanical properties [Citation6]. Through chemical modifications or combinations with other materials, it is possible to improve the inherent properties of wood and to introduce novel functionalities into wood and wood-based materials [Citation7–14]. For practical purposes, engineered wood products with more homogenised wood properties are of great importance to increase the utilisation of wood. Conventional adhesives used for engineered wood products are most often based on a small selection of synthetic resins. They impede the natural degradation of the product and are a serious obstacle to its recyclability. Moreover, adhesives play a non-negligible part in the generated CO2 (eq.) emissions during the production of engineered wood products [Citation15,Citation16].
While much research is conducted to reduce friction between two surfaces to avoid friction damage [Citation17–21], one may use friction for beneficial purposes. Linear friction welding of wood is a technique that allows bonding wood without synthetic adhesives through activation of its natural components (lignin, cellulose and hemicelluloses). By linear reciprocal movement of two wood surfaces, friction heat is generated at the interface. This plasticises the lignin and leads to defibrillation and entanglement of wood fibres. The plasticised lignin encases the entangled wood fibres upon cooling and solidification and results in a strong bond solely through the inherent components of wood [Citation22]. Longitudinally welded spruce has reached shear strengths of about 4.2 MPa [Citation23,Citation24] while bond strength of up to 9.3 MPa has been achieved using pine [Citation25]. Hardwood species allow for higher bond strength, with 13.4 MPa for beech wood [Citation26] and 13.3 MPa for ash wood [Citation27]. Most studies use a welding frequency range of 100–150 Hz, as pre-set by the welding equipment. However, even higher bond strengths of up to 15 MPa were reported for pine when increasing the welding frequency to up to 240 Hz [Citation28].
A limiting factor for the widespread application of friction-welded wood is its sensitivity to moisture. The hygroscopic behaviour of wood results in anisotropic swelling upon water uptake. It is assumed that there is a mismatch in the swelling behaviour between the bulk wood and the bondline. This leads to stresses at the interface of the welded components, resulting in failure and delamination of the bond [Citation28,Citation29]. Until yet, it has not been possible to obtain satisfyingly moisture-stable bonds, despite various efforts to optimise welding parameters of several wood species [Citation26,Citation27,Citation30–36]. Various treatments have already been studied to improve moisture stability in linear friction welding, such as citric acid [Citation37,Citation38], pine tree rosin [Citation39], sunflower oil, polybutylene adipate, pine tannin or furfural [Citation40]. Citric acid showed promising results for improving the moisture stability of butt-end welded spruce joints [Citation37]. However, no major effect was observed after citric acid treatment of longitudinally welded beech wood [Citation38]. Pine tree rosin led to an increase in moisture stability of linear welded joints through the protection of the bondline against moisture by its hydrophobic property, resulting in wet shear strength in welded beech of up to 5.2 MPa [Citation39]. Dowel welding was investigated with acetylated lignin. Pull-out tests of beech-dowels showed about 30% increase in the pull-out force after treatment [Citation41].
In this work, we investigated three different biomass-derived polyphenols, organosolv lignin extracted form hardwood, kraft lignin from softwood, and tannic acid, as potential bonding additives to increase the moisture stability of the welded wood. Lignin, as one of the most abundant hydrophobic biopolymers in the world and the main source of renewable aromatic structures [Citation42–45], may add to the protection of the bondline against moisture. We studied lignin from different sources and derivatives thereof to test their specific applicability in friction welding. Organosolv lignin is currently mostly produced on pilot-scale plants, but is of growing interest as a side product of bio-refineries. Organosolv lignin shows a high chemical purity and low water solubility [Citation46,Citation47]. Kraft lignin, as a side product of the most common pulping process, is of commercial interest as a phenolic source in adhesives due to its low cost and easy availability. Nowadays, the majority of the produced kraft lignin is still combusted for energy production. Even though it has been in the focus of research for the use as bio-adhesive for decades, it is mostly used only as a partial replacement of phenols in phenol-formaldehyde resins [Citation48], as a consequence of its relatively low reactivity towards crosslinking reactions [Citation44,Citation49,Citation50]. Besides the rather hydrophobic lignin, we used more hydrophilic tannic acid, a hydrolysable tannin, which is a low-cost product that has been researched for application in bio-adhesives [Citation51–54].
Only limited knowledge is available about how the physical and molecular features of bonding additives influence the bond strength and moisture resistance during friction welding. Therefore, we used carboxylation, acetylation and depolymerisation of kraft lignin to modify its functional groups and thereby vary its chemical reactivity. By using a variety of biomolecules and chemically altered derivatives thereof with selected chemical and physical properties, we aimed to obtain a deeper understanding of the relevance of chemical and structural features for the formation of the bondline as well as for an improved bond strength and moisture resistance of friction-welded wood joints.
2. Material & methods
2.1. Materials
A commercially available alkaline kraft lignin (#370959; Sigma-Aldrich, Buchs, Switzerland) was purchased. The alkaline kraft lignin was produced by kraft delignification of softwood, and contains a sulphur content of 1.3% according to the manufacturer.
Beechwood organosolv lignin was supplied by the Fraunhofer Center for Chemical-Biotechnological Processes CBP in Leuna.
Tannic acid (#16201, Mw = 1701.2 g/mol), acetic anhydride, succinic anhydride, sodium hydroxide, citric acid monohydrate, tetrahydrofuran (THF, Chromasolv, inhibitor-free), chloroform-d1, pyridine, chromium(III) acetylacetonate, hydroxy-3a,4,7,7a-tetrahydro-1H-4,7-methanoisoindole-1,3(2H)-dione [eHNDI], and 2-chloro-4,4,5,5-tetramethyl-1,3,2-dioxaphospholane (Cl-TMDP, 95%) were purchased from Sigma-Aldrich (Buchs, Switzerland). Polystyrene standards (MW range: 0.16 − 3.00 × 106 g mol−1) were obtained from Polymer Laboratories (Church Stretton, United Kingdom).
Defect-free Norway spruce (Picea abies) specimens with dimensions of 160 × 100 × 10 mm3 (l × r × t) were prepared for welding. The density was between 418 and 530 kg/m3. The orientation of the annual rings was not determined. The wood was stored at 20 °C/65% r.h. before welding.
2.2. Lignin modifications & synthesis
2.2.1. Lignin acetylation
The acetylation of lignin was conducted based on a protocol by Monteil-Rivera and Paquet [Citation55]. Kraft lignin and acetic anhydride were mixed at a ratio of 1:10 by weight. The mixture was heated under constant stirring to 130 °C (heat-up time: ∼20 min) and left to react under reflux for 30 min. After cooling to room temperature, the acetylated lignin was precipitated by the addition of deionised water and separated by vacuum filtration. Following washing with water (until pH >4), the acetylated lignin was dried at room temperature overnight, followed by drying under vacuum (150 mbar, 40 °C) for 6 h.
2.2.2. Lignin succinylation
The succinylation of kraft lignin was conducted based on the protocol of Xiao et al. [Citation56] with some alterations. Kraft lignin was dispersed in deionised water at a ratio of 1:10 by weight. The pH of the solution was adjusted to 8.5–9 with a 0.5 M aqueous NaOH solution. Crystalline succinic anhydride (20 wt.% of lignin) was added stepwise to the mixture during 30 min at 28 °C. The pH of the solution was kept at 8.5–9 during the whole reaction with a 2% aqueous NaOH solution. After 1 h reaction time, the succinylated lignin was precipitated by adjusting the mixture to pH 2 with concentrated HCl, separated by centrifugation and washed multiple times with water until the pH of the supernatant was >4.
2.2.3. Lignin depolymerisation
Depolymerised kraft lignin was produced by dissolving 2 wt.% Na2CO3 in a 70% aqueous ethanol solution, followed by adding kraft lignin (5 wt.%). The mixture was heated to 180 °C for 1.5 h in a Parr® reactor. After cooling to room temperature, the solvent was evaporated under reduced pressure.
2.2.4. Lignin fractioning
Fractioning of kraft lignin was conducted by dissolving the kraft lignin in water-free acetone (0.1 g/ml), followed by filtration through two Whatman-filter #1. Thereby, two fractions were obtained. The dissolved lignin-fraction was named ASKL (acetone soluble kraft lignin) and the insoluble fraction AISKL (acetone insoluble kraft lignin).
2.3. Preparation of specimens for welding
2.3.1. Citric acid
For citric acid modification, the wood samples were placed in a basin filled with a 10 wt.% aqueous citric acid solution at room temperature. Care was taken that the sample was not fully immersed and that only one surface was covered with the solution. A vacuum of ∼50 mbar was applied for 10 min to aid the impregnation of the citric acid solution.
2.3.2. Tannic acid
For tannic acid treatment, a 16 wt.% aqueous tannic acid solution was applied by brush to both surfaces of the wood samples to be welded (235 g/m2).
2.3.3. Lignin
The different lignins were dispersed in an aqueous acetone solution (16 wt.%) with a concentration of 5 wt.% lignin. The mixtures were applied to both surfaces of the spruce samples by brush, obtaining a final concentration of 31.25 g lignin/m2.
2.4. Welding of specimens
The samples were welded with a linear vibration welding (LVW) machine LZM75 from Fischer Schweisstechnik (DE). All samples were conditioned at 20 °C and 65% r.h. for at least a week before welding.
2.4.1. Parameter study for the welding of native spruce
To analyse the influence of the welding parameters on the shear strength of unmodified spruce, different welding frequencies (80, 100 and 130 Hz) and welding pressures (0.5, 1, 1.5 and 2 MPa) were used. The welding time was set to 6 s. The applied cooling pressure was fixed at 0.5 MPa higher than the respective welding pressure and was held for 30 s after the end of the welding process. The welding amplitude (relative movement of the two surfaces to each other) was 1.5 mm.
2.4.2. Welding with kraft lignin
Samples treated with unmodified kraft lignin were investigated by using two lignin concentrations (31.25 and 62.5 g/m2), different welding frequencies (100 Hz and 130 Hz) and stopping criteria of 1 mm or 2 mm welding displacement (loss in thickness after welding due to compression of the cells and expulsed material). A welding and cooling pressure of 1.5 MPa and 2 MPa, respectively, was maintained. The cooling pressure was kept for 30 s.
2.4.3. Welding with different biomolecules
For comparing the differently modified bonding additives, the welding parameters were fixed at a welding frequency of 130 Hz and a welding pressure of 1.5 MPa. Furthermore, a welding displacement of 2 mm was used as stop criteria. The cooling time was 30 s at a pressure of 2 MPa.
An overview of the used welding parameters for the welding of the specimen with differently modified surfaces is given in .
Table 1. Overview of the welding parameters used in this study for the welding experiments with native spruce, kraft lignin modified spruce and spruce modified with different biomolecules (different lignins, tannic acid and citric acid).
2.5. Chemical and thermal characterisation
2.5.1. Thermogravimetric analysis (TGA)
The influence of the lignin modifications on the thermal stability was determined by using a TGA Q50 (TA Instruments). A 10–15 mg sample in powder form was placed in a Pt-pan and dried at 100 °C for 15 min before heating up to 1000 °C with a heating rate of 10 °C min−1 under nitrogen (60 ml min−1 sample purge flow and 40 ml min−1 balance purge flow). The weight after the pre-drying step was taken as starting weight (100%). The process was repeated with new samples by heating up to 500 °C for the visual characterisation of the formed char.
2.5.2. Differential scanning calorimetry (DSC)
Glass transition temperature (Tg) was determined by Modulated Differential Scanning Calorimetry (MDSC) using a DSC Q2000 (TA Instrument) with Tzero® aluminium pans. A temperature ramp from 80 to 200 °C with a heating rate of 3 °C min−1 was applied. A temperature modulation (amplitude of 1 °C in a period of 60 s) was superimposed on the main heating ramp. The lignins were dried at 110 °C before measurement. Two heat cycles were run, and Tg was determined in the second run. The glass transition was analysed with the Universal Analysis 2000 (TA Instruments) software through the inflexion point method based on the change in the reversing heat flow signal [Citation57].
2.5.3. ATR-FTIR
Chemical characterisation of the used biomolecules was obtained with an attenuated total reflectance Fourier-transform-infrared (ATR-FTIR) spectrometer (Bruker Tensor 27) equipped with an ATR module over the scan range of 400–4000 cm−1 with a spectral resolution of 2 cm−1. The spectra were baseline corrected in the OPUS software using the concave rubber band method (20 iterations, 64 baseline points) and min-max normalised. Five normalised spectra were averaged and plotted in OriginPro 2021 (OriginLab Corporation).
2.5.4. 31P NMR
OH-group contents were analysed as previously described. In brief, an accurately weighed amount of lignin (approximately 30 mg) was dissolved in 425 µl of anhydrous CDCl3/pyridine solution (1:1.6 (v/v)). 100 µl of a standard solution of N-hydroxy-5-norbornene-2,3-dicarboxylic acid imide (eHNDI) (0.1225 M in anhydrous CDCl3/pyridine solution) containing Cr(III)-acetylacetonate as the relaxation agent was added. Finally, 75 µl of 2-chloro-4,4,5,5-tetramethyl-1,3,2-dioxaphospholane was added, and the mixture was stirred at room temperature for 2 h. The mixture was then transferred into 5 mm NMR tubes, and the spectra were measured on a Bruker AVANCE 400 MHz spectrometer equipped with a 5 mm double resonance broadband BBI inverse probe using the Bruker zgig pulse sequence (256 scans at 20 °C). All chemical shifts reported are relative to the reaction product of water with Cl-TMDP, which gives a sharp signal in pyridine/CDCl3 at 132.2 ppm. NMR data were processed with MestreNova (Version 9.0.1, Mestrelab Research), using standard ranges for integrals as established before for lignins and tannins [Citation58].
2.5.5. GPC-UV analyses
GPC analysis was used to determine the molecular weight distribution of lignin. Starting, lignin samples (ca. 50 mg) were acetylated using a 1:1 pyridine/acetic anhydride mixture (2 ml, 40 °C, 24 h) and recovered by stripping with EtOH, toluene and chloroform (three times each) before being subjected to GPC analysis.
GPC analyses were performed on an Agilent 1260 Infinity liquid chromatography system, equipped with an autosampler (Agilent 1260 Vialsampler, injection volume 25 µL) and connected in series to an Agilent 1260 DA VL detector (set at 280 nm) and an Agilent 1260 FL detector (λ excitation: 390 nm, λ emission: 550 nm for all samples). The GPC-column system was composed as follows (following the solvent flow direction): Agilent PLgel 5 µm (500 Å), Agilent PLgel 5 µm (1000 Å) and Agilent PLgel 5 µm (10,000 Å). Samples were dissolved in tetrahydrofuran (THF, accurately prepared at the concentration of 1 mg ml−1 starting from more concentrated stock solutions) and analysed using THF as eluent (Fluka 99.8%) at a flow rate of 1 ml min−1. Standards of polystyrene (MW range: 0.16 − 3.00 × 106 g mol−1) were used for calibration. The evaluation of the number-average molecular weight (Mn) and the weight-average molecular weight (Mw) of the samples was performed. Moreover, the ratio PDI = Mw/Mn, defined as polydispersity index was calculated. The Mn and Mw values reported are the average of three analyses (standard error Mw: 500 g mol−1; Mn: 100 g mol−1).
2.5.6. SEM
Bond failure and wood surface structure were analysed visually and by scanning electron microscopy (SEM) with a Jeol JSMF7100F. Samples were coated with a Pt/Pd (80/20) coating of ∼7 nm thickness using a sputter Coater (CCU-010, Safematic, Switzerland).
2.5.7. Tensile shear tests
Tensile shear tests were conducted according to DIN EN 302-1. Deviating from the standard, the sample thickness was increased from 10 to 20 mm. Four testing specimens were obtained per welded sample, whereof two were tested dry and two in wet state (cf. ). The specimen in dry state were conditioned at 20 °C, 65% r.h. prior measurement, the ones in wet state were tested after 24 h submersion in cold tap water. The tests were conducted with a Zwick/Roell Z010 universal testing machine, equipped with a 10 kN load cell and a testing speed of 0.4 mm/min. The strain was measured using a clip-on extensometer.
One-way ANOVA, followed by Fisher’s LSD posthoc test was performed with OriginPro 2021 to compare the measured shear strengths between different modifications.
3. Results & discussion
3.1. Welding of native spruce
The bond strength of friction-welded wood is highly dependent on anatomical parameters of the wood (species, grain direction, etc.), moisture content as well as on the welding parameters [Citation59]. To select a set of parameters for the initial investigations, we studied the influence of different welding frequencies and pressures on the shear strength of native spruce. shows the resulting tensile shear strengths of the bonded spruce in dry and wet state after 24 h water immersion.
Figure 1. Influence of welding pressure and welding frequency on the mean tensile shear strength of unmodified spruce after (A) conditioning at 65% r.h. and (B) after 24 h water immersion. The error bars denote the standard error of the mean (SE). Please note the different scaling of the axes.
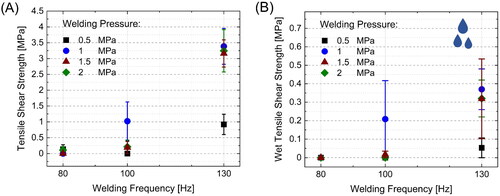
Increasing the welding frequency from 80 to 130 Hz led to increased bond strength, as has been shown previously for beech wood [Citation26]. The welding pressure appears to have only minor impact on the bond strength once a threshold of 1 MPa is reached. The welding pressure should be high enough to assure a maximal contact area of the wood pieces, but sufficiently low to avoid excessive cell collapse, which is a known phenomenon for spruce wood welding [Citation60,Citation61]. Based on these results for both, dry and wet conditions, a welding pressure of 1.5 MPa and 130 Hz welding frequency were selected for the subsequent studies on the modified wood material. Analysis of the bonded elements indicated that a welding displacement of roughly 1.75 to 2.25 mm showed the highest bond strengths in dry and wet conditions (Figure S1). Therefore, a stopping criteria of 2 mm welding displacement instead of a fixed welding time was chosen for the welding of the modified wood samples. Welding displacement as stop criteria is preferable over time to avoid an overly influence of different surface friction coefficients due to applied modifications and to obtain comparable amounts of decomposed cell structures. Furthermore, it allows controllable and homogenous sample thicknesses after the welding, which is beneficial for practical application.
3.2. Welding of kraft lignin modified specimens
Welding with kraft lignin increased the shear strengths in dry and wet state, as shown in . Furthermore, the influence of the selected welding parameters was reduced. Decreasing the welding frequency from 130 to 100 Hz showed no distinct change in shear strength of the welded samples, unlike for unmodified spruce (cf. ).
Figure 2. Tensile shear strength of kraft lignin treated spruce in (A) dry state and (B) after 24 h water immersion. Shown are welded spruce modified with different amounts of kraft lignin (1 or 2 g per specimen) and welded with a frequency of 100 or 130 Hz and a welding pressure of 1.5 MPa. The displacement (1 or 2 mm) was used as stop criteria. Please note the different scaling of the axes.
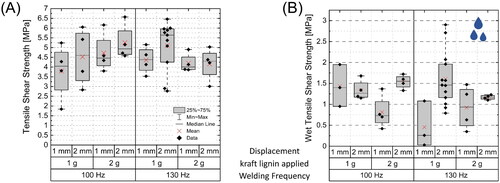
Classical adhesion theory can be used to gain a deeper understanding of the bonding mechanisms involved through the addition of technical lignins. Theories in wood adhesion postulate different mechanisms contributing to a successful bond formation, which can roughly be separated into mechanical adhesion (e.g. mechanical interlocking and diffusive chain entanglement) and specific adhesion (chemical interactions such as covalent or secondary chemical bonds) [Citation62,Citation63]. Even though friction welding differs from classical adhesive bonding in some regards, several principles are consistent.
3.3. Chemical & thermal characterisation of the biomolecules
To investigate possible mechanisms leading to the improvement in bond strength, lignin from different sources and different derivates of the kraft lignin were synthesised and used as bonding additives. Changes in the polarity of the kraft lignin was achieved by acetylation and succinylation, respectively. Additionally, the kraft lignin was depolymerised to reduce the molecular weight.
The introduction of novel functional groups into the modified kraft lignin was confirmed by FTIR-ATR () and hydroxyl groups were measured and quantified with 31P NMR to investigate the chemical and structural features of the different biomolecules, as summarised in . The individual NMR spectra are shown in Figure S2.
Figure 3. FTIR-ATR spectra of the modified lignins used as bonding additive for the welding, with proposed molecular structures of the modification of softwood kraft lignin. Exemplary shown is the β-aryl ether substructure of lignin. For depolymerisation, only some potential structures are depicted with no claim for completeness. A selection of characteristic absorption bands of the functional groups and their corresponding structural representations are denoted by the letters A–C.
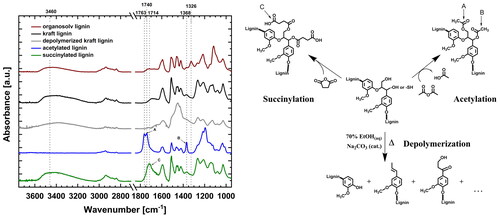
Table 2. Quantification of the hydroxyl groups of the modified lignins and tannic acid, determined by 31P NMR.
FTIR-ATR shows that acetylation of the lignin introduced new absorption bands at 1763 and 1740 cm−1 which indicates stretches of carbonyl groups (C=O) in aromatic and aliphatic alkoxy-groups, respectively [Citation55,Citation64]. The disappearance of the absorption band at around 3460 cm−1 (O–H stretch) [Citation65] indicates the complete esterification of the lignin hydroxyl groups. Additionally, the absorption band at 1368 cm−1 marks an increase in aliphatic C–H stretching in CH3 of the acetyl-group [Citation66,Citation67]. Successful acetylation could also be shown by quantitative 31P NMR analysis, indicating acetylation of around 95% of all OH-groups, with no discrimination between aliphatic or aromatic hydroxyl groups.
Succinylation of lignin is indicated by the appearance of unconjugated carboxyl groups at 1714 cm−1 (C=O stretch) [Citation66]. In the 31P NMR analysis, succinylation can be quantified to have proceeded at approx. 25% of the OH-groups. Acid content increases approx. by 40%, eventually indicating small residues of free succinic acid in the recovered material.
The absorption band at 1326 cm−1 for the beechwood organosolv lignin is characteristic of condensed syringyl- and guaiacyl-type lignin units [Citation67], which are absent in the kraft lignin from softwood. 31P NMR analysis confirms the typical high loading in S-type phenolics of ca. 2 mmol/g, next to only 0.8 mmol/g of G-type phenolics. The sample appears to be rather free from residual sugars (3 mmol/g aliphatic OH-groups) and displays only a small acid content.
FTIR-analysis of the depolymerised kraft lignin indicates a decrease in hydroxyl groups with a decreased absorption band at 3460 cm−1 (O–H deformation). These changes are confirmed by the 31P NMR analysis. Solubility under the standard analysis conditions was reduced. Relative quantitative analysis shows that aromatic OH-content is reduced over-proportionally compared to aliphatic OH-group content, hence indicating a drastic change in intrinsic reactivity of the material. The change in molecular weight after depolymerisation is shown in . The determination of the molecular weight distribution of the lignin was conducted by GPC. It is well known, that molecular weight plays an important role in the thermos-physical behaviour of the lignin, but varies strongly depending on the source and extraction methods.
Table 3. Molecular weight distribution of kraft and organosolv lignin measured by GPC.
Tannic acid revealed the highest absolute OH-group content with 9.61 mmol/g phenolic and 1.75 mmol/g aliphatic OH-groups. The ratio indicates a slight impurity of the sample that is additionally reflected by the detection of acid groups.
Thermal transitions of lignin are strongly affected by molecular weight, functional groups and degree of condensation and crosslinking [Citation68,Citation69]. To investigate the effect of the lignin modifications on their thermal properties, the glass transition temperature (Tg) of the different lignins and their derivatives was determined. As can be seen in , the source and modification of the lignins influences Tg.
Figure 4. (A) TGA data of the biopolymers used as welding modifications. (B) DSC thermogram with the glass-transition temperature of lignin. (C) Structures of the char after pyrolysis to 500 °C under N2.
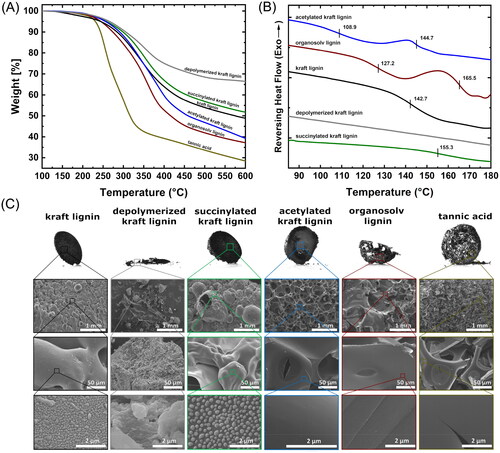
The lower molecular weight and degree of condensation of organosolv lignin compared to kraft lignin is reflected in its lower Tg. The effect of the functional groups on the Tg is visible in the differently modified kraft lignin samples. Contrary to the findings of Scarica et al. [Citation70], it appears that the introduction of aliphatic carboxylic acids into the lignin structure increased the Tg, presumably due to increased intermolecular interactions (hydrogen bonds) and partial polymerisation during heating [Citation68]. This may offset the effect of increased free volume gained by introducing succinic acid. This finding is supported by the low Tg of acetylated lignin, in which the introduced acetyl groups limit intermolecular hydrogen bonds and polymerisation reactions of the lignin.
Melting of the added lignin is necessary for wetting of the interface and intermixing with the native lignin of the adherends. This is assumed to result in chain entanglement and mechanical interlocking of the polymer chains and to improve adhesion through chemical interactions of the bonding additive with the lignocellulosic components of the adherent [Citation62].
Acetylated kraft lignin has previously been shown to exhibit a suitable melting temperature and viscosity for application in dowel welding, with a good interpenetration of the lignin at the welded interface [Citation41]. However, the required melt behaviour of the lignin is different in dowel welding compared to linear friction welding. A low Tg, as observed with acetylated lignin and organosolv lignin, indicates lower intermolecular forces of the lignin molecules and leads to a lower melt viscosity. This increases the chance of expulsion of the matrix from the bondline during the welding process. In contrast, an increased Tg of lignin indicates improved stabilisation by inter- and intramolecular interactions and potential self-condensation reactions of the lignin [Citation71], which are favourable properties to create a strong bond due to welding.
While the melt viscosity was not quantified, visual differences between the different modifications of the lignin regarding their melting behaviour were indicated in SEM studies after pyrolysis by TGA (). The lignins appeared to melt and aggregate into a smooth network during the melting process. Both succinylated and unmodified kraft lignin formed stable bubbles by trapped volatile products during thermal degradation [Citation72]. In contrast, acetylated kraft lignin, organosolv lignin and tannic acid form a more porous structure. Only the char of depolymerised kraft lignin showed no sign of melting and formation of a macroscopic network.
For the formation of a molecular network, the applied biopolymer should not undergo severe thermal degradation when exposed to temperatures that can be reached during the welding of spruce (maximum up to approx. 500 °C). shows the thermal decomposition of the applied bonding additives. The relevance of the thermal stability becomes obvious by comparing the weight loss of the pyrolyzed samples with the obtained shear strengths of the bonded assembly. As a trend, lower thermal degradation (higher char yield) results in higher shear strength under dry conditions (Figure S3). An exception was depolymerised kraft lignin, which showed lower thermal degradation, but had adverse effects on the shear strength.
3.4. Welding and characterisation of the surface-modified specimens
Bond strengths, both dry and wet, after welding with different bonding additives are shown in . The highest shear strengths in dry state were observed in samples treated with kraft lignin (5.1 ± 1.3 MPa) and succinylated kraft lignin (5.2 ± 1.4 MPa), with significantly increased bond strengths compared to the untreated samples (3.2 ± 1.4 MPa). Organosolv lignin showed no improvement in the shear strength.
Figure 5. (A) Sample preparation for tensile shear tests with: (1) surface modification, (2) welding, (3) cutting of the welded sample into shear tests specimen and (4) finished tensile shear test specimen. The tensile shear strengths of friction welded spruce with different modifications are shown in (B) dry state at a moisture content of ≈12% and (C) wet state after 24 h water immersion. Significant differences from the control samples (p < .05) are marked with an asterisk. Please note the different scaling of the axes.
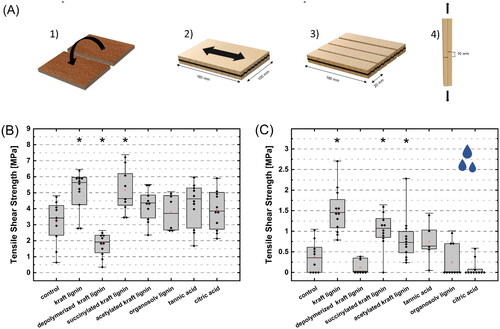
The wet shear strength after 24 h water immersion () indicated that treatments with kraft lignin and its derivatives led to significantly increased moisture resistance of the bond. The mean shear strength increased from 0.38 MPa of the untreated sample to 1.50 MPa after treatment with unmodified kraft lignin. Furthermore, a high proportion of delamination in the untreated spruce samples (40%) was observed during water immersion, while kraft lignin treated samples remained intact with no delaminated samples.
shows the fracture surfaces of the welded samples after tensile shear testing. The unmodified control sample possessed a kind of layered microstructure, which might have formed due to the reciprocal movement during the welding and could be explained by a higher melt viscosity and a less homogenous melting of the native lignin compared to the applied technical lignins. The same effect, but less pronounced, was observed for succinylated lignin, whereas unmodified kraft lignin and acetylated lignin led to a smooth microstructure. Furthermore, it was observed that samples treated with succinylated kraft lignin expulsed markedly less matrix material during the welding process than the other tested lignins, indicating reduced flowing of the viscous matrix due to the added modified lignin. Further investigations of the melt viscosity and its influence on the bond strength are necessary for optimising the melting behaviour of the lignin.
3.5. Bonding mechanisms
Besides chain entanglement and mechanical interlocking, chemical interactions can result in strong wood bonds. Studies on lignin-cellulose/starch films have shown that a higher carboxyl and aliphatic OH-group content in the lignin leads to increased tensile strength, presumably through hydrogen bonding of the cellulose with lignin [Citation73]. Stabilisation through secondary forces can increase the shear strength of lignin-treated welded spruce. Unmodified and succinylated kraft lignin are able to form more hydrogen bonds than acetylated lignin and therefore, showed superior bond strengths in dry conditions.
Covalent crosslinking of the lignocellulosic material of the native spruce could improve the bond strength and resistance against moisture. However, citric acid-treated samples showed no improvement in bond strengths, even though esterification of carboxylic acids with lignocellulosic OH-groups might be possible [Citation74,Citation75]. Hence, most likely cross-linking reactions did not take place to the extent necessary for improving the bond strength.
The mechanisms leading to increased moisture resistance are not elucidated in detail, yet. Nonetheless, based on the superior moisture resistance of kraft lignin and succinylated kraft lignin, it is assumed that an interplay of chain entanglement, mechanical interlocking and chemical interactions is responsible for the improved moisture resistance.
The chain entanglement and mechanical interlocking are influenced by the melting behaviour of the lignin, which in turn is affected by molecular weight, degree of internal condensation and branching as well as by chemical functionalities present along the lignin chains [Citation76–78]. This is in line with the lower shear strength of samples treated with organosolv lignin compared to kraft lignin. Presumably, this is due to the lower molecular weight of the lignin chains in organosolv lignin resulting in less chain entanglement, and the peculiarities of the different structural features of oligomeric organosolv lignin molecules that are supposed to be rather linear and significantly less condensed. The organosolv lignin sample displays nearly the same amount of OH-groups compared to the kraft lignin; hence, the sheer number of functional groups capable of undergoing hydrogen bonding appears to be of less importance. The detrimental effect on the moisture resistance observed in samples treated with tannic acid, which shows the overall highest amount of OH-groups per gram substance, supports this assumption. Non-linear tannic acid, as well as the rather linear smaller organosolv lignin, lead most probably to a coverage of the surface that exhibits less ‘pending’ moieties suitable for sufficient entanglement, besides interaction via hydrogen bonding and electronic interactions between aromatic moieties.
Welding with acetone-fractioned kraft lignin showed that even though the acetone-insoluble kraft lignin (AISKL) fraction improves the wet strength slightly better than the acetone-soluble kraft lignin (ASKL) fraction, the resulting bond strength of welded samples treated with either fraction is lower than after treatment with unmodified kraft lignin (see Figure S4). The AISKL fraction consists of branched polymeric material with higher molecular weight compared to the ASKL fraction, which contains a higher proportion of condensed lignin with less polymeric material [Citation79]. The superior bond strength after treatment with unmodified kraft lignin suggests a layered structure of the assembled lignin in the bondline, with an entanglement of the high molecular weight lignin chains, while the condensed, lower molecular weight fraction stabilises the entangled network and creates a hydrophobic environment that partially protects the bondline from moisture.
4. Conclusion
Wood-based biopolymers can improve the bond strength and moisture resistance of friction-welded spruce wood. The molecular structure and thermal behaviour of the applied bonding additive play an important role in the formation of a strong and moisture-resistant bond. Kraft lignin and derivates thereof that maintained their polymeric nature and did not fully compromise hydrogen bonding and/or intrinsic stacking propensities, resulted in improved bond strength and increased moisture resistance of linear friction welded spruce.
Further improvement of lignin-based bonding additives relies on an understanding of the bonding mechanisms involved. Chain entanglement, mechanical interlocking and chemical interactions have been identified as potentially important mechanisms that seem to work in a hierarchical manner, starting with physical entanglement enabling intermolecular interactions and chemical bonding. In the conducted study, chemical cross-linking seems to have played only a minor role.
Kraft lignin and derivatives thereof have high potential as biopolymer-based bonding additives for application in friction welding. Characterising the melt viscosity of the lignin as influenced by chemical functionality and structural characteristics could help further improving the bond strength and moisture resistance. A deeper understanding of the melting behaviour of lignin and the interaction with the lignocellulosic material from the adherend will allow for controlled lignin functionalisation to achieve an optimal distribution of the lignin across the welded bondline.
Acknowledgements
The authors would like to thank Thomas Schnider for the wood sample preparation and technical support. The Scientific Center for Optical and Electron Microscopy (ScopeM) of ETH is gratefully acknowledged for its technical support in electron microscopy. HL would like to thank the Italian Ministry of University Education and Research (MIUR) for the Grant ‘Dipartimento di Eccellenza 2018-2022’ to the Department of Earth and Environmental Sciences of the University of Milano-Bicocca.
Disclosure statement
No potential conflict of interest was reported by the author(s).
References
- Hong H, Gao L, Zheng Y, et al. A path of Multi-Energy hybrids of concentrating solar energy and carbon fuels for low CO2 emission. ES Energy Environ. 2021;13:1–7.
- Xu J, Zhu P, El Azab IH, et al. An efficient bifunctional Ni-Nb2O5 nanocatalysts for the hydrodeoxygenation of anisole. Chin J Chem Eng. 2022;49:187–197.
- Wei D, Weng M, Mahmoud MHH, et al. Development of novel biomass hybrid aerogel supported composite phase change materials with improved light-thermal conversion and thermal energy storage capacity. Adv Compos Hybrid Mater. 2022;5(3):1910–1921.
- Cao Y, Weng M, Mahmoud MHH, et al. Flame-retardant and leakage-proof phase change composites based on MXene/polyimide aerogels toward solar thermal energy harvesting. Adv Compos Hybrid Mater. 2022;5(2):1253–1267.
- Cheng H, Xing L, Zuo Y, et al. Constructing nickel chain/MXene networks in melamine foam towards phase change materials for thermal energy management and absorption-dominated electromagnetic interference shielding. Adv Compos Hybrid Mater. 2022;5(2):755–765.
- Churkina G, Organschi A, Reyer CPO, et al. Buildings as a global carbon sink. Nat Sustain. 2020;3(4):269–276.
- Liang C, Du Y, Wang Y, et al. Intumescent fire-retardant coatings for ancient wooden architectures with ideal electromagnetic interference shielding. Adv Compos Hybrid Mater. 2021;4(4):979–988.
- Yuan B, Wang Y, Elnaggar AY, et al. Physical vapor deposition of graphitic carbon nitride (g-C3N4) films on biomass substrate: optoelectronic performance evaluation and life cycle assessment. Adv Compos Hybrid Mater. 2022;5(2):813–822.
- Yuan B, Guo M, Murugadoss V, et al. Immobilization of graphitic carbon nitride on wood surface via chemical crosslinking method for UV resistance and self-cleaning. Adv Compos Hybrid Mater. 2021;4(2):286–293.
- Maddodi BS, Lu A, Devesh S, et al. Repurposing plastic wastes in non-conventional engineered wood building bricks for constructional application – a mechanical characterization using experimental and statistical analysis. Eng Sci. 2022;18:329–336.
- Lian M, Huang Y, Liu Y, et al. An overview of regenerable wood-based composites: preparation and applications for flame retardancy, enhanced mechanical properties, biomimicry, and transparency energy saving. Adv Compos Hybrid Mater. 2022;5(3):1612–1657.
- Culebras M, Collins GA, Beaucamp A, et al. Lignin/Si hybrid carbon nanofibers towards highly efficient sustainable Li-ion anode materials. Eng Sci. 2022;17:195–203.
- Wu Q, Gao L, Huang M, et al. Aminated lignin by ultrasonic method with enhanced arsenic (V) adsorption from polluted water. Adv Compos Hybrid Mater. 2022;5(2):1044–1053.
- Mu L, Dong Y, Li L, et al. Achieving high value utilization of bio-oil from lignin targeting for advanced lubrication. ES Mater Manuf. 2021;11:72–80.
- Ferdosian F, Pan Z, Gao G, et al. Bio-based adhesives and evaluation for wood composites application. Polymers. 2017;9(12):70.
- Puettmann M, Wilson J. Life-cycle analysis of wood products: cradle-to-gate LCI of residential wood building materials. Wood Fiber Sci. 2005;37:18–29.
- Zhao S, Niu M, Peng P, et al. Edge oleylaminated graphene as ultra-stable lubricant additive for friction and wear reduction. Eng. Sci. 2020;9:77–83.
- Li W, Chen Q, Zhang W, et al. Boron oxide/alumina nanocomposites as lubricant oil additives to save friction-induced energy waste. ES Mater Manuf. 2022;18:10–17.
- Li W, Wang M, Chen Q, et al. A new preparation method of copper oxide/aluminium oxide nanocomposites with enhanced anti-friction properties. ES Mater Manuf. 2023;19:692.
- Hua J, Björling M, Larsson R, et al. Friction control of chitosan-Ag hydrogel by silver ion. ES Mater Manuf. 2022;16:30–36.
- He Y, Duan R, Zhang Q, et al. Reinforce the mechanical toughness, heat resistance, and friction and wear resistance of phenolic resin via constructing self-assembled hybrid particles of graphite oxide and zirconia as nano-fillers. Adv Compos Hybrid Mater. 2021;4(2):317–323.
- Gfeller B, Zanetti M, Properzi M, et al. Wood bonding by vibrational welding. J Adhes Sci Technol. 2003;17(11):1573–1589.
- Hahn B, Stamm B, Weinand Y. Linear friction welding of spruce boards: experimental investigations on scale effects due to humidity evaporation. Wood Sci Technol. 2014;48(4):855–871.
- Leban JM, Pizzi A, Wieland S, et al. X-ray microdensitometry analysis of vibration-welded wood. J Adhes Sci Technol. 2004;18(6):673–685.
- Vaziri M, Lindgren O, Pizzi A. Optimization of tensile-shear strength for linear welded scots pine. J Adhes Sci Technol. 2012;26(1-3):109–119.
- Mansouri HR, Omrani P, Pizzi A. Improving the water resistance of linear vibration-welded wood joints. J Adhes Sci Technol. 2009;23(1):63–70.
- Amirou S, Pizzi A, Delmotte L. Investigations of mechanical properties and chemical changes occurring during welding of thermally modified ash wood. J Adhes Sci Technol. 2020;34(1):13–24.
- Vaziri M, Sandberg D. Welding of thermally modified wood and thermal modification of the welded wood: effects on the shear strength under climatic conditions [CT scanning; digital microscopy; shear strength; thermal modification; ThermoWood]. BioResources. 2021;16(2):3224–3234.
- Vaziri M, Karlsson O, Abrahamsson L, et al. Wettability of welded wood-joints investigated by the Wilhelmy method: part 1. Determination of apparent contact angles, swelling, and water sorption. Holzforschung. 2021;75(1):65–74.
- Omrani P, Pizzi A, Mansouri HR, et al. Physico-chemical causes of the extent of water resistance of linearly welded wood joints. J Adhes Sci Technol. 2009;23(6):827–837.
- Rhême M, Botsis J, Cugnoni J, et al. Influence of the moisture content on the fracture characteristics of welded wood joint. Part 2: mode II fracture. Holzforschung. 2013;67(7):755–761.
- Rhême M, Botsis J, Cugnoni J, et al. Influence of the moisture content on the fracture characteristics of welded wood joint. Part 1: mode I fracture. Holzforschung. 2013;67(7):747–754.
- Ruponen J, Čermák P, Rhême M, et al. Reducing the moisture sensitivity of linear friction welded birch (Betula pendula L.) wood through thermal modification. J Adhes Sci Technol. 2015;29(22):2461–2474.
- Vaziri M, Lindgren O, Pizzi A, et al. Moisture sensitivity of scots pine joints produced by linear frictional welding. J Adhes Sci Technol. 2010;24(8-10):1515–1527.
- Zor M, Vaziri M, Sandberg D. Water resistance of welded birch wood produced by linear friction. Kastamonu Univ J For Fac. 2020;20(3):266–271.
- Amirou S, Pizzi A, Belleville B, et al. Water resistance of natural joint of spruce produced by linear friction welding without any treatment. Int Wood Prod J. 2017;8(4):201–207.
- Amirou S, Pizzi A, Delmotte L. Citric acid as waterproofing additive in butt joints linear wood welding. Eur J Wood Prod. 2017;75(4):651–654.
- Zigon J, Pizzi A, Zhang H, et al. The influence of heat and chemical treatments of beech wood on the shear strength of welded and UF bonded specimens. Eur J Wood Prod. 2015;73(5):685–687.
- Pizzi A, Mansouri HR, Leban JM, et al. Enhancing the exterior performance of wood joined by linear and rotational welding. J Adhes Sci Technol. 2011;25(19):2717–2730.
- Wieland S, Shi B, Pizzi A, et al. Vibration welding of wood: X-ray tomography, additives, radical concentration. For Prod J. 2005;55(1):84–87.
- Pizzi A, Zhou X, Navarrete P, et al. Enhancing water resistance of welded dowel wood joints by acetylated lignin. J Adhes Sci Technol. 2013;27(3):252–262.
- Boerjan W, Ralph J, Baucher M. Lignin biosynthesis. Annu Rev Plant Biol. 2003;54(1):519–546.
- Chio C, Sain M, Qin W. Lignin utilization: a review of lignin depolymerization from various aspects. Renew Sustain Energy Rev. 2019;107:232–249.
- Glasser WG. About making lignin great again—some lessons from the Past. Front Chem. 2019;7:565.
- Ragauskas AJ, Beckham GT, Biddy MJ, et al. Lignin valorization: improving lignin processing in the biorefinery. Science. 2014;344(6185):1246843.
- Lora JH, Glasser WG. Recent industrial applications of lignin: a sustainable alternative to nonrenewable materials. J Polym Environ. 2002;10(1/2):39–48.
- Vishtal A, Kraslawski A. Challenges in industrial applications of technical lignins. BioResources. 2011;6(3):3547–3568.
- Xu C, Ferdosian F. Conversion of lignin into bio-based chemicals and materials. In: He L-N, Rogers RD, Su D, editors. Green chemistry and sustainable technology. Berlin: Springer; 2017. p. 91–109.
- Lewis NG, Lantzy TR. Lignin in adhesives. In: Hemingway RH, Conner AJ, editors. Adhesives from renewable resources. Washington, DC: American Chemical Society; 1989. p. 13–26.
- Pizzi A. Recent developments in eco-efficient bio-based adhesives for wood bonding: opportunities and issues. J Adhes Sci Technol. 2006;20(8):829–846.
- Ghahri S, Pizzi A. Improving soy-based adhesives for wood particleboard by tannins addition. Wood Sci Technol. 2018;52(1):261–279.
- Spina S, Zhou X, Segovia C, et al. Phenolic resin adhesives based on chestnut (Castanea sativa) hydrolysable tannins. J Adhes Sci Technol. 2013;27(18-19):2103–2111.
- Ghahri S, Chen X, Pizzi A, et al. Natural tannins as new cross-linking materials for soy-based adhesives. Polymers. 2021;13(4):595.
- Zhou X, Du G. Applications of tannin resin adhesives in the wood industry. In: Aires A, editor. Tannins - structural properties, biological properties and current knowledge. London: IntechOpen; 2020. p. 97–103
- Monteil-Rivera F, Paquet L. Solvent-free catalyst-free microwave-assisted acylation of lignin. Ind Crops Prod. 2015;65:446–453.
- Xiao B, Sun XF, Sun R. The chemical modification of lignins with succinic anhydride in aqueous systems. Polym Degrad Stab. 2001;71(2):223–231.
- DIN EN ISO 11357-2. Plastics – differential scanning calorimetry (DSC) – part 2: determination of glass transition temperature and step height. Berlin: Beuth Verlag GmbH; 2020.
- Meng X, Crestini C, Ben H, et al. Determination of hydroxyl groups in biorefinery resources via quantitative 31P NMR spectroscopy. Nat Protoc. 2019;14(9):2627–2647.
- Hahn B, Vallée T, Stamm B, et al. Moment resisting connections composed of friction-welded spruce boards: experimental investigations and numerical strength prediction. Eur J Wood Prod. 2014;72(2):229–241.
- Gfeller B, Pizzi AP, Zanetti M, et al. Solid wood joints by in situ welding of structural wood constituents. Holzforschung. 2004;58(1):45–52.
- Rautkari L, Properzi M, Pichelin F, et al. Surface modification of wood using friction. Wood Sci Technol. 2009;43(3-4):291–299.
- Frihart CR. Wood adhesion and adhesives. In: Rowell RM, editor. Handbook of wood chemistry and wood composites. New York (NY): CRC Press; 2005. p. 215–278.
- Schultz J, Nardin M. Theories and mechanisms of adhesion. In: Pizzi A, Mittal KL, editors. Handbook of adhesive technology. 2nd ed. Boca Raton (FL): CRC Press; 2003. p. 53–68.
- Glasser WG, Jain RK. Lignin derivatives. I. Alkanoates. 1993;47(3):225–233.
- Stark NM, Yelle DJ, Agarwal UP. Techniques for characterizing lignin. In: Faruk O, Sain M, editors. Lignin in polymer composites. Norwich (NY): William Andrew Publishing; 2016. p. 49–66.
- Chen Y, Stark NM, Cai Z, et al. Chemical modification of kraft lignin: effect on chemical and thermal properties. BioResources. 2014;9(3):5488–5500.
- Faix O. Classification of lignins from different botanical origins by FT-IR spectroscopy. Holzforschung. 1991;45(s1):21–28.
- Zhou S, Brown RC, Bai X. The use of calcium hydroxide pretreatment to overcome agglomeration of technical lignin during fast pyrolysis. Green Chem. 2015;17(10):4748–4759.
- Han T, Sophonrat N, Tagami A, et al. Characterization of lignin at pre-pyrolysis temperature to investigate its melting problem. Fuel. 2019;235:1061–1069.
- Scarica C, Suriano R, Levi M, et al. Lignin functionalized with succinic anhydride as building block for biobased thermosetting polyester coatings. ACS Sustain Chem Eng. 2018;6(3):3392–3401. 2018/03/05
- Wang C, Kelley SS, Venditti RA. Lignin-Based thermoplastic materials. ChemSusChem. 2016;9(8):770–783.
- Sharma RK, Wooten JB, Baliga VL, et al. Characterization of chars from pyrolysis of lignin. Fuel. 2004;83(11-12):1469–1482.
- Zhao Y, Tagami A, Dobele G, et al. The impact of lignin structural diversity on performance of cellulose nanofiber (CNF)-starch composite films. Polymers. 2019;11(3):538.
- Bischof-Vukusic S, Katovic D, Schramm C, et al. Polycarboxylic acids as non-formaldehyde anti-swelling agents for wood. Holzforschung. 2006;60(4):439–444.
- Lee SH, Md Tahir P, Lum WC, et al. A review on citric acid as green modifying agent and binder for wood. Polymers. 2020;12(8):1692.
- Akpan EI. Melt-processing of lignin. In: Akpan EI, Adeosun SO, editors. Sustainable lignin for carbon fibers: principles, techniques, and applications. Cham: Springer Nature Switzerland AG; 2019. p. 281–324.
- Olsson A-M, Salmén L. The effect of lignin composition on the viscoelastic properties of wood. Nord Pulp Pap Res J. 1997;12(3):140–144.
- Sun Q, Khunsupat R, Akato K, et al. A study of poplar organosolv lignin after melt rheology treatment as carbon fiber precursors. Green Chem. 2016;18(18):5015–5024.
- Crestini C, Lange H, Sette M, et al. On the structure of softwood kraft lignin. Green Chem. 2017;19(17):4104–4121.