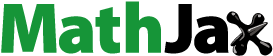
Abstract
This work demonstrates that Cd microadditions can enhance the precipitation of age-hardening precipitates in 2xxx and 6xxx alloys as well as the dispersoid precipitation in 3xxx alloys, but have a minimal effect on the precipitation in 7xxx alloys. Experimental and theoretical methods are utilised to investigate the nucleation and precipitation of precipitates/dispersoids in Cd-containing Al alloys. The enhanced precipitation of θ′ and α-dispersoids in 2xxx and 3xxx alloys, respectively, are proposed to result from the heterogeneous nucleation on earlier-formed Cd-rich nanoparticles, while the enhanced precipitation of β′′ in 6xxx alloys is attributed to the increased number density of effective Mg-Si co-clusters due to the Cd incorporation. This investigation provides theoretical basis for the design of precipitation-strengthened Al alloys via microalloying.
Introduction
Precipitation hardening is one of the most important strengthening mechanisms in aluminium alloys. In heat-treatable aluminium alloys, such as 2xxx, 6xxx and 7xxx series alloys, the strength can be substantially enhanced by fine, (semi-)coherent precipitates formed during artificial ageing (AA) treatments [Citation1]. Another type of secondary phase, dispersoids (e.g. α-Al(Mn,Fe)Si and Al3Zr) are commonly found in both heat-treatable and non-heat-treatable Al alloys. Dispersoids are generally formed during high-temperature heat treatments, and they have much better thermal stability than age-hardening precipitates [Citation2,Citation3], making them good candidates to replace precipitates for high-temperature applications. However, the nucleation of dispersoids is difficult due to the low number density of nucleation sites [Citation4–6] and the low diffusivities of solute elements in Al [Citation7–10]. As a consequence, the number density of dispersoids is generally not high enough to achieve a significant dispersion strengthening.
Driven by the huge commercial demand for high-strength Al alloys for both room-temperature and high-temperature applications, there is currently great interest to enhance the nucleation of precipitates and dispersoids in Al alloys. It has been discovered since the 1950s that the impurity elements Cd, In or Sn can significantly accelerate the age-hardening kinetics of 2xxx Al-Cu alloys [Citation11–15]. However, the mechanisms by which these elements aid the nucleation of θ′, especially for the Cd addition, have not been well understood. A recent study by authors demonstrated that the minor Cd addition could significantly enhance the precipitation of α-Al(Mn,Fe)Si dispersoids in a 3003 Al-Mn-Fe-Si alloy, which provides a promising approach to develop high-temperature Al alloys strengthened by dispersoids [Citation16]. Later, a similar enhanced precipitation strengthening effect with minor Cd additions was also reported in 6xxx Al-Mg-Si alloys [Citation17]. Although possible mechanisms related to Cd additions stimulating the nucleation of precipitates/dispersoids were proposed in these studies, no discussion about the differences/similarities of these mechanisms in different alloy systems has been made.
In this work, a revisit to the effects of minor Cd additions on the nucleation and precipitation of θ′ in Al-Cu alloys is carried out. Moreover, the influences of the Cd additions on the nucleation and precipitation of β′′ in 6xxx alloys and α-Al(Mn,Fe)Si dispersoids in 3xxx alloys during heat treatment are further investigated. Based on a comparison between the three different Cd-containing Al alloys, the mechanisms concerning the enhanced nucleation of precipitates/dispersoids by Cd additions can be better interpreted, which in turn provides a guide to the future work on enhancing the nucleation of specific precipitates and dispersoids in Al alloys. In addition, some novel precipitation behaviours introduced by Cd addition were studied to understand the effects of Cd on the later stages of precipitation.
Experimental
All the experimental alloys were prepared by melting in an induction furnace and casting into a copper mould with dimensions 100 × 70 × 30 mm3. For the Cd-containing alloys, the Al-5 wt-% Cd master alloy was added into the melt at ∼750°C. The chemical compositions of the alloys are measured by inductively coupled plasma optical emission spectroscopy (ICP-OES) and are listed in Table .
Table 1. Chemical compositions (wt-%) of the experimental alloys.
The precipitation-hardened alloys (e.g. Al-4.5Cu(-0.3Cd), 6082(Cd) and 7050(Cd) alloys) were conventionally solution heat-treated and artificial-aged. The aim of one-step aging for 7050(Cd) alloys is to evaluate the maximum hardness that both alloys can obtain, while the two-step aging is to achieve a better balance between strength and resistance to stress corrosion. The natural ageing time before artificial ageing is ∼1 h. In order to achieve dispersion strengthening effect, the 3003(Cd) alloys were continuously heated from room temperature (RT) up to 600°C at a rate of 50°C/h. The details of the heat treatment processes are given in Table . Vickers hardness measurements were carried out based on at least eight measurements with a Matsuzawa hardness tester under a 5 kg applied load.
Table 2. Heat treatment processes of investigated alloys.
Thin foils for transmission electron microscopy (TEM) studies were prepared by using a Struers Tenupol-5 twin-jet electropolisher operated at ∼20 V. The electrolyte consisted of 1/3 HNO3 and 2/3 methanol cooled to ∼ −28°C. A JEOL 2100 operated at 200 kV was employed to acquire bright-field TEM images and the quantification of precipitates (the method was described in Ref. [Citation16,Citation18]). The thickness of all TEM foil was estimated by electron energy loss spectroscopy (EELS). A JEOL 2100F and a double aberration-corrected (image and probe Cs) cold-FEG JEOL ARM-200F were used for HAADF-STEM and corresponding EDS analyses.
Needle-shaped atom probe tomography (APT) samples for three-dimensional chemical composition measurements of precipitates/dispersoids were prepared by a two-step electropolishing procedure described in Ref. [Citation16]. APT characterisation was performed on a local electrode atom probe LEAP4000X SI under a high vacuum of 2 × 10−9 Pa, while the specimen was kept at a temperature of 20 K. A UV laser pulsing energy of 40 pJ, with a repetition rate of 250 kHz and a target evaporation rate of 0.5% was used. Atom probe data reconstruction and quantitative analyses were conducted by the Cameca IVAS 3.6.12 software.
First-principles calculations as implemented in the highly efficient Vienna ab initio simulation package (VASP) [Citation19,Citation20] were utilised to determine the equilibrium enthalpy of formation ΔH for the Q′ phase with and without Cd incorporation. The full potential frozen-core PAW method [Citation21,Citation22] was used to describe the electron–ion interactions and the exchange–correlation is treated within the generalised gradient approximation (GGA) of Perdew–Burke–Ernzerh of (PBE) [Citation23]. A cut-off energy of 400 eV was adopted, which was sufficient to insure a well-converged total energy. A Monkhorst–Pack [Citation24] k-mesh of 7 × 7 × 15 in combination with the linear tetrahedron method including Blöchl corrections [Citation25] is adopted for the Brillouin zone (BZ) integration. Fully relaxation with respect to the volume, shape, and atomic positions of the unit cell was carried out to obtain the equilibrium energy configurations. The convergence criteria for electronic self-consistency and ionic relaxation loop are 10-6 eV and 10-3 eV/Å, respectively.
The equilibrium formation enthalpy, for the Q′-phase with or without Cd incorporation was calculated in terms of the following [Citation26,Citation27]:
(1)
(1) where
,
,
,
,
, and
are the energies (per atom) of the compound
and the constituents, Al, Cu, Mg, Si and Cd, each in their equilibrium reference crystal structures. xA to xE are the corresponding concentrations of Al, Cu, Mg, Si and Cd, respectively.
Results and discussion
The effect of Cd on precipitation in 2xxx alloys
Figure presents bright-field TEM images of the precipitate microstructure in the Al-4.5Cu and Al-4.5Cu-0.3Cd alloys after ageing at 185°C for 120 min. It is worth noting that the chosen regions for TEM observations in both samples have similar thicknesses. As shown in Figure , the Cd-containing alloy has a much denser precipitate distribution than the alloy without Cd, which suggests that the minor addition of Cd can significantly enhance the age-hardening response of Al-Cu alloys. Such results are in agreement with previous works of Al-Cu alloys with trace Sn, Cd, and In additions [Citation11–13,Citation28–30].
Figure 1. HAADF-STEM image showing the precipitates in (a) Al-4.5Cu and (b) Al-4.5Cu-0.3Cd alloy aged at 185°C for 120 min. The microstructures are viewed along 〈100〉Al zone axes.
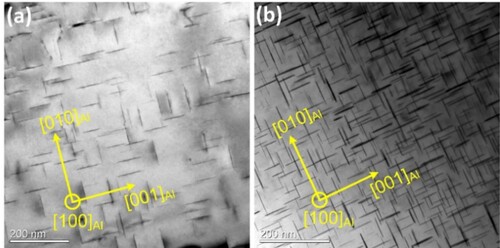
Figure (a) shows a HAADF-STEM image of precipitates in the Al-4.5Cu-0.3Cd alloy aged at 185°C for 120 min. As seen in Figure (a), some ultrafine nanoparticles (pointed out by white arrows) are attached to θ′ and θ′′ precipitates (indicated by yellow arrows), while others (pointed out by white arrows) are dispersed in the Al matrix. Figure (b) displays the corresponding distribution of Cd as determined by STEM-EDS. By comparing Figure (a,b), we can find that there is a clear Cd enrichment corresponding to the nanoparticles pointed out by white arrows in Figure (a).
Figure 2. (a) HAADF-STEM image of precipitates in the Al-4.5Cu-0.3Cd alloy aged at 185°C for 120 min. The nanoparticles are indicated by white arrows; the corresponding distributions of (b) Cd and (c) Cu as determined by STEM-EDS. Note that the microstructures are viewed along the 〈100〉Al direction.
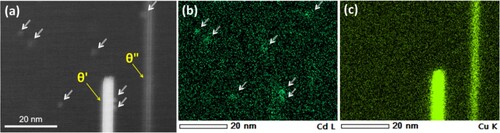
The effect of Cd on precipitation in 3xxx alloys
Bright-field TEM images of the 3003 and 3003Cd alloys as-heated to 450°C, where the maximum hardness of both alloys was achieved during continuous heating at a rate of 50°C/h, are shown in Figure . It is obvious from visual inspection that the 3003Cd alloy has a much higher number density of finer α-Al(Mn,Fe)Si dispersoids than the 3003 alloy. A quantitative analysis shows that the number density of dispersoids in the 3003Cd alloy as-heated to 450°C is almost twice of that in the 3003 alloy subjected to the same heat treatment [Citation16]. A closer examination reveals that most of the dispersoids in the 3003 alloy seem to be distributed along lines (Figure (a)), suggesting the preferential nucleation of dispersoids on dislocations. While the distribution of dispersoids in the 3003Cd alloy is much more homogeneous (Figure (b)).
Figure 3. Bright-field TEM images of dispersoids in the (a) 3003 and (b) 3003Cd alloys after continuous heating to 450°C. Noted that the chosen regions in both samples have similar thicknesses.
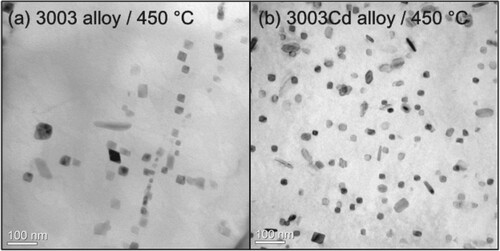
Figure (a) presents the bright-field TEM image of nanoparticles in the 3003Cd alloy as-heated to 300°C. When the alloy is heated to 300°C, in addition to some dark grey particles, a number of ‘composite’ particles (pointed out by blue boxes) which consist of a particle with dark grey contrast and a particle with dark contrast are found [Citation16]. The EDS analysis (Figure (b)) on one ‘composite’ particle reveals that the part with dark grey contrast in the ‘composite’ particle in Figure (a) is enriched in Mn, Fe and Si, while the part with dark contrast is enriched in Cd.
The effect of Cd on precipitation in 6xxx alloys
Figure shows bright-field TEM images of the 6082 and 6082Cd alloys aged at 185 °C for 30 min. In the 6082 alloy, black dots corresponding to the cross-sections of precipitates are sparsely distributed in the Al matrix (Figure (a)); while in the 6082Cd alloy, the number density of black dots is much higher (Figure (b)). According to the statistical analysis of the precipitate microstructure, the number density of the needle-shaped precipitates in the 6082Cd alloy aged for 30 min is 6.3 times higher than that in the 6082 alloy [Citation17].
Figure 5. Bright-field TEM images of the (a) 6082 and (b) 6082Cd alloys aged for 30 min. The regions for TEM observations in both samples have similar thicknesses. The images were taken along 〈100〉Al zone axes.
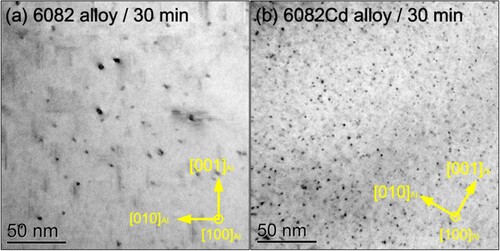
Figure (a) shows a HAADF-STEM image of the 6082Cd alloy aged at 185°C for 360 min. Finely dispersed precipitates with bright contrast (indicated by white arrows) can be seen in the Al matrix. Figure (b) shows an atomic resolution HAADF-STEM image of one precipitate cross-section. The precipitate cross-section in Figure (b) has two parts, one region marked by green exhibiting high intensity, and a second region which has a darker contrast. The darker part of the precipitate incorporates regions of highly disordered β′′ at the precipitate/matrix interfaces, and additionally, local triangular configurations (indicated by red dashed circles) are present. These configurations are similar to Q′/C-like sub-units. The corresponding EDS maps in Figure (c) demonstrate that the precipitate region with bright contrast is highly enriched with Cd, while the remaining precipitate region is enriched in Mg and Si. The columns exhibiting relatively high Z contrast (the central columns of Q′/C-like sub-units) inside the red circles could not be identified by EDS due to the limited resolution in this case. Generally, the central columns of Q′/C-like triangular sub-units are occupied by Cu. However, the Cu content of the 6082Cd alloy is only 0.01 wt-%. Since Ag was recently observed at the Cu sites in Q′/C-like sub-units [Citation31], it can be speculated that the columns with high Z contrast in the darker region of the precipitate shown in Figure (b) are occupied by Cu and/or Cd atoms.
Figure 6. (a) HAADF-STEM images of the precipitates in the 6082Cd alloy aged at 185°C for 360 min; (b) HAADF-STEM image of one typical precipitate cross-section and (c) its corresponding EDS maps. The formation enthalpies of various Q′ compounds (d) Al3Mg9Cu2-xCdxSi7 and (e) Al6Mg6Cu2-xCdxSi7 as a function of the number of Cd atoms (x) replacing Cu.
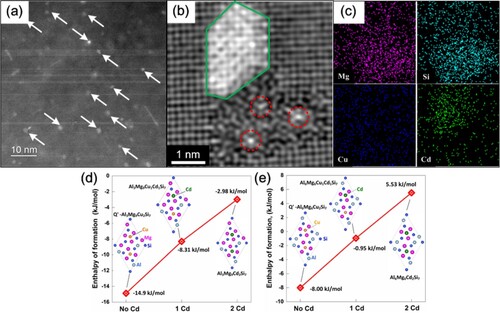
DFT simulations were used to further investigate the possible substitution of Cu by Cd in the Q′ phase. As shown in Figure (d), the formation enthalpy of the Q′ phase (assuming a composition as Al3Mg9Cu2Si7 [Citation32–34]) is calculated to be −14.9 kJ/mol. When one of the two Cu atoms is substituted by Cd, the formation enthalpy increases to −8.31 kJ/mol, and when both Cu atoms are substituted by Cd, the formation enthalpy further increases to −2.98 kJ/mol. Assuming the composition of Q′ is Al6Mg6Cu2Si7 [Citation31,Citation35], the formation enthalpy increases from −8.00 kJ/mol to −5.53 kJ/mol when the two Cu atoms are completely substituted by Cd (Figure (e)). Both results strongly indicate that Cd is not energetically favourable to occupy Cu sites in the Q′ phase.
The effect of Cd on precipitation hardening in 7xxx alloys
Figure presents the hardness evolution for the 7050 and 7050Cd alloys subjected to one-step ageing and two-step ageing. The 7050Cd alloy does not show evidently higher hardness than the 7050 alloy, which means that the Cd addition has a negligible effect on the precipitation hardening of 7xxx alloys. The reason for this phenomenon will be discussed in the precipitation mechanism part.
Atomic structure of Cd-rich nanoparticles
As shown above, both the precipitation of age-hardening precipitates and dispersoids in Cd- containing 2xxx, 3xxx and 6xxx alloys are closely associated with Cd-rich nanoparticles. In previous studies [Citation16,Citation36], Cd-rich nanoparticles in Al alloys were characterised to have a hcp structure. However, our studies suggest that most of the ultrafine Cd-rich nanoparticles formed during heating at 185–300°C may have a metastable structure different from hcp Cd phase. Figure displays atomic-resolution HAADF-STEM images of Cd-rich nanoparticles in the Al-4.5Cu-0.3Cd alloy as viewed along 〈100〉Al and 〈110〉Al zone axes. As indicated, these Cd-rich nanoparticles are ∼ 2 nm in diameter. The evident lattice contrast compared to the Al matrix is ascribed to the greater atomic mass of Cd atoms within the nanoparticles. A careful inspection reveals that the nanoparticles may have a fcc-based crystal structure, but with some atomic column positions slightly deviating from the perfect fcc lattice sites and exhibiting a near hcp crystal structure. Such offsets can be due to the lattice mismatch introduced by the incorporation of larger Cd atoms (compared to Al) in such nanoparticles. It also means that the Cd-rich nanoparticles are experiencing the phase transformation from Al-Cd phase with fcc structure to pure Cd phase with hcp structure during heating at 185∼300°C. Cd-rich nanoparticles with a similar crystal structure were also observed in the 6082Cd alloy (see Figure ).
Figure 8. Atomic-resolution image showing the microstructures of Cd-rich nanoparticles in the Al-4.5Cu-0.3Cd alloy aged at 185°C for 120 min. (a) Viewed along the 〈100〉Al zone axis, (b) viewed along the 〈110〉Al zone axis.
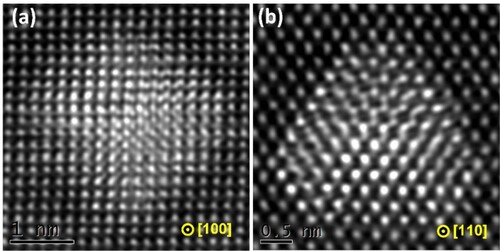
Figure 9. APT analyses: (a) Cd-rich nanoparticles defined by isosurfaces (green) for regions with higher than 4.6 at.-% Cd in the 3003Cd alloy as-heated to 250°C and the corresponding one-dimensional concentration profile; (b) co-clusters identified by target elements: Mg, Si and Cd in the 6082Cd alloy aged at 185°C for 5 min.
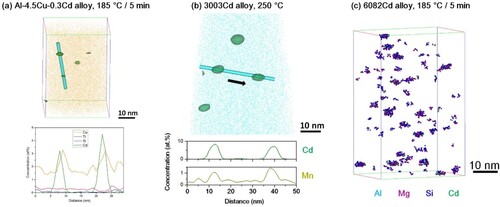
Precipitation mechanism in Cd-containing Al alloys
Since the STEM-EDS analyses (Figures , and ) have revealed that most of the strengthening precipitates/dispersoids in Cd-containing 2xxx, 3xxx and 6xxx alloys are associated with Cd-rich nanoparticles, APT was utilised to investigate the role of Cd-rich nanoparticles in the early stages of precipitation in these alloys. For the Al-4.5Cu-0.3Cd alloy, our APT analyses show a high density of Cd-rich nanoparticles, which are defined by an isoconcentration surface (green) at 3.0 at.-% Cd, formed in the early stages of AA (185°C/5 min), as shown in Figure (a). The corresponding one-dimensional concentration profiles of nanoparticles reveal that the maximum concentration of Cd within the nanoparticles is below 10 at.-%, confirming that Cd-rich nanoparticles are more likely to be metastable Al-Cd precipitates instead of a pure Cd equilibrium phase. It should be highlighted that Cu concentration peaks are detected within these Cd-rich nanoparticles. Similarly, a number of Cd-rich nanoparticles are formed in the 3003Cd alloy as-heated to 250°C [Citation16], and these nanoparticles are also enriched with Mn (Figure (b)). Moreover, the one-dimensional concentration profiles of Cd-rich nanoparticles in both Al-4.5Cu-0.3Cd and 3003Cd alloys further reveal that the enrichments of solute atoms (Cu and Mn, respectively) tend to be at the interface between Cd-rich nanoparticles and the Al matrix rather than in the centre of nanoparticles. It indicates that Cd-rich nanoparticles form first, which attract Cu atoms in the Al-4.5Cu-0.3Cd alloy and Mn atoms in the 3003Cd alloy, respectively. Based on our APT analyses, it is proposed that Cd-rich nanoparticles act as heterogeneous nuclei for θ′ and α-Al(Mn,Fe)Si in the two alloys.
In 2xxx alloys, the precipitation of θ′ during artificial ageing is usually very sluggish due to the relatively low diffusivity of Cu in the Al matrix at conventional artificial ageing temperatures (e.g. 2.4 × 10−16 cm2s−1 at 185°C [Citation37]). The dispersoid precipitation of α-Al(Mn,Fe)Si in 3xxx alloys is even slower due to the even lower diffusivity of Mn in Al (e.g. 1.0 × 10−22 cm2s−1 at 185°C and 7.2 × 10−18 cm2s−1 at 300°C [Citation37]). On the other hand, the diffusivity of Cd in Al is much faster than that of Cu and Mn: the diffusivity of Cd in Al are 7.0 × 10−15 cm2s−1 at 185°C and 4.9 × 10−12 cm2s−1 at 300°C [Citation37], respectively. The high diffusivity of Cd as well as the extremely low solubility enables it to have a high mobility in solid solution and precipitate more easily. Therefore, the precipitation of Cd-rich precipitates starts first in Al alloys during heating and acts as heterogeneous nuclei for θ′/α-Al(Mn,Fe)Si. In addition, it is well known that a high concentration of mobile vacancies in Al alloys is beneficial to solute clustering and precipitation [Citation38,Citation39]. Except rapid cooling to RT, adding alloying elements with high solute-vacancy binding energies, such as Cd (0.14 eV [Citation40]), can also stabilise vacancies in solid solution and thus accelerate the diffusion of solute atoms. Therefore, Cd additions are considered to thermodynamically and kinetically prompt the nucleation process of θ′/α-Al(Mn,Fe)Si.
In conventional 6xxx alloys, the Mg-Si co-clusters normally set the initial conditions for the precipitation of β′′ [Citation41]. While for the 6082Cd alloy, our APT analysis reveals that the clustering of Mg, Si as well as Cd has already started after ageing at 185°C for 5 min [Citation17]. Figure (c) displays the distribution of clusters by using Mg, Si and Cd as target elements. A close examination of individual clusters shows that a large fraction of Mg-Si co-clusters consist of Cd atoms, meaning that Cd atoms are incorporated into the initial co-clustering of Mg and Si. This is different from our APT analyses on the early precipitation stages in the Cd-containing 2xxx and 3xxx alloys, which reveals that a large number of Cd-rich nanoparticles form first. This is because the much higher diffusivity of Si and Mg (i.e. 5.4 × 10−15 cm2s−1 and 2.7 × 10−15 cm2s−1at 185°C [Citation37], respectively) than Cu and Mn in Al give rise to the formation of Mg-Si-Cd clusters in the 6xxx alloys instead of Cd-rich nanoparticles. The incorporation of Cd atoms in the initial Mg-Si co-clusters is believed to be thermodynamically beneficial to the precipitation of β′′ [Citation17,Citation42]. Moreover, the Cd addition can also preserve as many mobile vacancies as possible for the diffusion of Mg and Si atoms in solid solution. With a high concentration of vacancies, the formation of solute clusters during RT storage or pre-ageing for later precipitation can be significantly encouraged (Figure ).
It is worth noting that the mechanism for the enhanced precipitation of β′′ in Cd-containing 6xxx alloys is different from the heterogeneous nucleation in Cd-containing 2xxx and 3xxx alloys. Based on our systematic investigations, it is proposed that, for precipitates/dispersoids whose forming elements have relatively low diffusivities in Al (e.g. θ′ and α-Al(Mn,Fe)Si), the enhanced precipitation/dispersion strengthening via Cd additions is generally remarkable, and the dominant mechanism is the heterogeneous nucleation of precipitates/dispersoids on earlier-formed Cd-rich nanoparticles; for precipitates/dispersoids whose forming elements have higher diffusivities in Al (e.g. β′′), the enhanced precipitation strengthening with Cd additions is still remarkable but less significant [Citation12,Citation16,Citation17,Citation43], and the enhanced precipitation is more likely to be related to the increased number density of effective solute clusters for later precipitation and also the accelerated clustering process due to more vacancies; by analogy, for precipitates/dispersoids whose forming elements have even higher diffusivities (e.g. η′, the diffusivity of Zn in Al at 185°C is 6.9 × 10−15 cm2s−1 [Citation37]) as well as rather high solubilities in Al, the effects of Cd additions on the precipitation strengthening are even less significant (Figure ), and sometimes negligible.
In brief, the enhanced nucleation of θ′ and α-dispersoids in 2xxx and 3xxx alloys, respectively, are proposed to result from the heterogeneous nucleation on earlier-formed Cd-rich nanoparticles. This is because the forming elements of these strengthening precipitates/dispersoids (e.g. Cu in 2xxx alloys and Mn in 3xxx alloys) have relatively low diffusivities, while the Cd element has high diffusivity and extremely low solubility, which makes it precipitate first and thus act as heterogeneous nuclei. On the other hand, the enhanced nucleation of β′′ in 6xxx alloys is attributed to the increased number density of effective Mg-Si co-clusters (larger sizes and higher Mg/Si ratios) for precipitation of β′′ due to the Cd incorporation. This is because the diffusivities of the forming elements (e.g. Si and Mg) are comparable to that of Cd, therefore they participate in solute clustering simultaneously. The role of Cd is to assist the precipitation thermodynamically and kinetically via its high binding energies with solute elements and vacancies.
Conclusions
Based on our investigations, we have demonstrated that a minor addition of Cd can enhance the precipitation of age-hardening precipitates in 2xxx and 6xxx alloys as well as the dispersoid precipitation in 3xxx alloys. It is found that most of the strengthening precipitates/dispersoids formed in Al alloys during heat treatment are associated with Cd-rich nanoparticles. These Cd-rich nanoparticles are characterised to be a metastable Al-Cd phase, having the same crystal structure and similar lattice parameters as the Al matrix and experiencing the phase transformation to pure Cd phase with hcp structure. For strengthening precipitates/dispersoids whose forming elements have relatively low diffusivities (e.g. Cu and Mn), the mechanism of enhanced precipitation/dispersion strengthening via Cd additions is the heterogeneous nucleation on earlier-formed Cd-rich nanoparticles. For precipitates/dispersoids whose forming elements have high diffusivities (e.g. Si and Mg), the enhanced precipitation is more likely to the increased number density of effective solute clusters for later precipitation and also the accelerated clustering process.
Acknowledgements
The authors are grateful to the BIT Research Fund Program for Young Scholars (grant number XSQD-201908009) and the National Natural Science Foundation of China (grant number 52201004). The Analysis & Testing Center at BIT, the Norwegian Centre of Transmission Electron Microscopy (NORTEM, Grant 197405) at NTNU, and the Materials Microstructural Characterization Centre at NJUST are greatly acknowledged.
Disclosure statement
No potential conflict of interest was reported by the author(s).
Additional information
Funding
References
- Andersen SJ, Marioara CD, Friis J, et al. Precipitates in aluminium alloys. Adv Phys X. 2018;3:791.
- Kaufman JG. Properties of aluminum alloys: tensile, creep, and fatigue data at high and low temperatures. Washington, D.C: ASM International; 1999.
- Liu K, Chen X-G. Development of Al–Mn–Mg 3004 alloy for applications at elevated temperature via dispersoid strengthening. Mater Des 2015;84:340–350.
- Hirasawa H. Precipitation process of Al-Mn and Al-Cr supersaturated solid solution in presence of age hardening phases. Scr Metall 1975;9:955–958.
- Lodgaard L, Ryum N. Precipitation of dispersoids containing Mn and/or Cr in Al–Mg–Si alloys. Mater Sci Eng A. 2000;283:144–152.
- Li YJ, Arnberg L. Quantitative study on the precipitation behavior of dispersoids in DC-cast AA3003 alloy during heating and homogenization. Acta Mater 2003;51:3415–3428.
- Fuller CB, Seidman DN, Dunand DC. Mechanical properties of Al(Sc. Zr) alloys at ambient and elevated temperatures. Acta Mater. 2003;51:4803–4814.
- Fuller C, Murray J, Seidman D. Temporal evolution of the nanostructure of Al(Sc,Zr) alloys: Part I – Chemical compositions of Al(ScZr) precipitates. Acta Mater 2005;53:5401–5413.
- Fuller C, Seidman D. Temporal evolution of the nanostructure of Al(Sc,Zr) alloys: Part II-coarsening of Al(ScZr) precipitates. Acta Mater 2005;53:5415–5428.
- Clouet E, Laé L, Épicier T, et al. Complex precipitation pathways in multicomponent alloys. Nat Mater 2006;5:482–488.
- Hardy HK. The ageing characteristics of ternary aluminium-copper alloys with cadmium, indium, or tin. J Inst Met 1951;80:483.
- Noble B. Theta-prime precipitation in aluminium-copper-cadmium alloys. Acta Metall 1968;16:393–401.
- Ringer SP, Hono K, Sakurai T. The effect of trace additions of sn on precipitation in Al-Cu alloys: an atom probe field ion microscopy study. Metall Mater Trans A. 1995;26:2207–2217.
- Silcock JM, Flower HM. Comments on a comparison of early and recent work on the effect of trace additions of Cd, In, or Sn on nucleation and growth of θ′ in Al–Cu alloys. Scr Mater 2002;46:389–394.
- Bourgeois L, Dwyer C, Weyland M, et al. The magic thicknesses of θ′ precipitates in Sn-microalloyed Al–Cu. Acta Mater 2012;60:633–644.
- Qian F, Jin S, Sha G, et al. Enhanced dispersoid precipitation and dispersion strengthening in an Al alloy by microalloying with Cd. Acta Mater 2018;157:114–125.
- Qian F, Zhao D, Mørtsell EA, et al. Enhanced nucleation and precipitation hardening in Al-Mg-Si(-Cu) alloys with minor Cd additions. Mater Sci Eng A. 2020;792:139698.
- Marioara CD, Andersen SJ, Zandbergen HW, et al. The influence of alloy composition on precipitates of the Al-Mg-Si system. Metall Mater Trans A. 2005;36:691–702.
- Kresse G, Furthmüller J. Efficiency of ab-initio total energy calculations for metals and semiconductors using a plane-wave basis set. Comput Mater Sci 1996;6:15–50.
- Kresse G, Furthmüller J. Efficient iterative schemes for ab initio total-energy calculations using a plane-wave basis set. Phys Rev B. 1996;54:11169–11186.
- Blöchl PE. Projector augmented-wave method. Phys Rev B. 1994;50:17953–17979.
- Kresse G, Joubert D. From ultrasoft pseudopotentials to the projector augmented-wave method. Phys Rev B. 1999;59:1758–1775.
- Perdew JP, Burke K, Ernzerhof M. Generalized gradient approximation made simple. Phys Rev Lett 1996;77:3865–3868.
- Monkhorst HJ, Pack JD. Special points for Brillouin-zone integrations. Phys Rev B. 1976;13:5188–5192.
- Blöchl PE, Jepsen O, Andersen OK. Improved tetrahedron method for Brillouin-zone integrations. Phys Rev B. 1994;49:16223–16233.
- Zhao D, Zhou L, Kong Y, et al. Structure and thermodynamics of the key precipitated phases in the Al–Mg–Si alloys from first-principles calculations. J Mater Sci 2011;46:7839.
- Zhao D, Zhou L, Du Y, et al. Structure, elastic and thermodynamic properties of the Ni–P system from first-principles calculations. Calphad. 2011;35:284–291.
- Silcock JM, Heal TJ, Hardy HK. The structural ageing characteristics of ternary aluminium-copper alloys wih cadimium, indium, or tin. J Inst Met 1955;84:23.
- Bourgeois L, Nie JF, Muddle BC. Assisted nucleation of θ′ phase in Al–Cu–Sn: the modified crystallography of tin precipitates. Philos Mag 2005;85:3487–3509.
- Homma T, Moody MP, Saxey DW, et al. Effect of Sn addition in preprecipitation stage in Al-Cu alloys: a correlative transmission electron microscopy and atom probe tomography study. Metall Mater Trans A. 2012;43:2192–2202.
- Mørtsell EA, Andersen SJ, Friis J, et al. Atomistic details of precipitates in lean Al–Mg–Si alloys with trace additions of Ag and Ge studied by HAADF-STEM and DFT. Philos Mag 2017;97:851–866.
- Matsuda K, Ikeno S, Uetani Y, et al. Metastable phases in an Al-Mg-Si alloy containing copper. Metall Mater Trans A. 2001;32:1293–1299.
- Chakrabarti DJ, Laughlin DE. Phase relations and precipitation in Al–Mg–Si alloys with Cu additions. Prog Mater Sci 2004;49:389–410.
- Marioara CD, Andersen SJ, Stene TN, et al. The effect of Cu on precipitation in Al–Mg–Si alloys. Philos Mag 2007;87:3385–3413.
- Takeshi S, et al. Atomic structures of precipitates in Al–Mg–Si alloys with small additions of other elements. Adv Eng Mater 2018;20(7):1800125.
- Silcock JM. Intermediate precipitates in aged binary alloys of aluminium with cadmium, indium and tin. J Inst Met 1955;84:19–22.
- Du Y, Chang YA, Huang B, et al. Diffusion coefficients of some solutes in fcc and liquid Al: critical evaluation and correlation. Mater Sci Eng A. 2003;363:140–151.
- Bourgeois L, Zhang Y, Zhang Z, et al. Transforming solid-state precipitates via excess vacancies. Nat Commun 2020;11:1248.
- Peng J, Bahl S, Shyam A, et al. Solute-vacancy clustering in aluminum. Acta Mater 2020;196:747–758.
- Wolverton C. Solute–vacancy binding in aluminum. Acta Mater 2007;55:5867–5872.
- Fallah V, Langelier B, Ofori-Opoku N, et al. Cluster evolution mechanisms during aging in Al–Mg–Si alloys. Acta Mater 2016;103:290–300.
- Zandbergen MW, Cerezo A, Smith GDW. Study of precipitation in Al–Mg–Si alloys by atom probe tomography II. Influence of Cu additions. Acta Mater 2015;101:149–158.
- Qian F, Mørtsell EA, Marioara CD, et al. Improving ageing kinetics and precipitation hardening in an Al-Mg-Si alloy by minor Cd addition. Materialia. 2018;4:33–37.