The application of mini-environment and SMIF (standard mechanical interface) enclosure in the cleanroom can efficiently reduce airborne particles and isolate the personnel from the product. The purpose of this article is to analyze the airflow field and pressure distribution of SMIF enclosure and to investigate the air cleanliness inside the mini-environment. Based on the continuity, momentum and energy equations of airflow motion, the simulation code CFX will be used to study the flow field of air movement corresponding to the associated boundary conditions. The results show that proper drilling holes or slots can improve the circulation zones of SMIF enclosure. The positive pressure of SMIF enclosure is mainly affected by inlet air flux, area of outlets, and leakage area. The calculated results will provide the design rules for SMIF Robot inside the SMIF enclosure and reduce the particle accumulation during robot moving.
1. INTRODUCTION
As the semiconductor process technologies advance in leaps and bounds, the manufacturing operations take place at almost the molecular level. The requirement on the cleanliness of the process environments has increased as a result. However, conventional cleanrooms no longer meet the critical demand on air quality, thereby giving rise to the design concepts of mini-environments. As shown in , a mini-environment is defined as “the enclosure of an environment to isolate product manufacturing from major sources of pollution (e.g., operators) in order to create a new local environment with cleaner surroundings.” In addition to the mini-environment, CitationParikh and Kaempf (1984) from Hewlett-Packard Laboratories first proposed the concept of using SMIF wafer cassettes for transport in the manufacturing of very large integrated circuit in 1984. The SMIF enclosure in includes an environment that contains a local enclosure, a supply system of clean air inside the enclosure, a standard mechanical interface (SMIF) for control and transport and a robot arm for transporting the product in and out of the process equipment.
The main advantage of mini-environment and SMIF enclosure is the reduction of the area requiring high degree of cleanliness, which decreases the construction cost and operating cost of a cleanroom substantially. The effective isolation of the product from the major pollution source also stabilizes the control of cleanliness, significantly increases the product yield. Besides, it can also isolate special equipment or the equipment containing toxic chemicals, thereby reducing the health risks to personnel and providing operators with a more comfortable environment. The primary disadvantage is the greater complexity in fab design, which requires more equipment accessories and slows down the process. In addition, the multiple environment isolation design naturally adds to the inconvenience of product transport and easily causes cross contamination. To improve the flexibility and efficiency of the application of mini-environments, the application of self-cleanliess system to avoid cross contamination in SMIF enclosure now holds the key to the development of mini-environments.
Mini-environments have been installed in the cleanrooms of several semiconductor manufacturers. In early 1990, TSMC led the industry in applying SMIF and mini-environments in commercial manufacturing. After several years' operation, the product yield reached as high as 97%. Singapore's Chartered Semiconductor also increased the average yield of its 0.6 μ m logic products from 48% to 88% after incorporating SMIF and mini-environments. These examples indicate that the application of mini-environments and SMIF enclosure in the cleanroom of semiconductor fabs enhances product yield. However, except for relevant software and hardware systems in wafer isolation and automatic transport equipment, the environment inside the equipment must also be strictly controlled in order to maintain the cleanliness when feeding or extracting the wafer in and out of the process equipment. Thus, the distribution of internal airflow velocity, dissipation of pollutants and air pressure distribution inside the SMIF enclosure must also be considered during the design of wafer isolation and automatic transport equipment.
Many engineers and researchers have conducted numerical simulation and experimental measurement studies related to the control of cleanliness in mini-environments. Toshiaki CitationYamamoto et al. (1990) used a 2-D numerical model to investigate the optimization design of the equipment flow field inside the photography region. They found that by properly moving the position of process equipment and adjusting the position of ventilation opening and ventilation volume, they could eliminate the existing circulation zones. CitationScheler et al. (1995) used a numerical model to simulate the flow field in an ISE (Integrated SMIF Elevator). They simulated the flow field by both 2-D and 3-D numerical models, and concluded that the number of particles in the flow field could be effectively reduced and the cleanliness in the ISE ensured by means of a proper openning, decreasing the amount of turbulence in the flow field and maintaining the positive pressure in the process region. CitationQuarini and Chang (1996) analyzed and simulated the flow field of a wet bench in a cleanroom using experimental and numerical methods. Their research described the velocity, temperature, and turbulence strength of the flow field and found that the experimental results and the numerical simulation results were very consistent. CitationTannous (1996) used a CFD code (PHOENICS) to simulate the flow field and pressure field in mini-environments and SMIF. CitationMilberg et al. (1991) proposed the rules for designing mini-environments where wafers were located by experimental measurement method. CitationSchliesser (1994) also used experimental measurement method to propose the design rules of combining SMIF with mini-environments.
This article combines SMIF enclosure and mini-environment, as shown in , to simulate and analyze a flow field with the objective of providing the rules for the air purification design in wafer isolation and automatic transport equipment. Based on the continuity, momentum and energy equations of airflow motion, the simulation code CFX will be used to study the flow field of air movement corresponding to the associated boundary conditions.
2. THEORETICAL MODEL
The model of the actual equipment is divided into four blocks in this article. The cells in each of the blocks share the same size. The size and division details of the cells are shown in . shows the layout and dimensions of the model. In the 3D-model flow field, the following assumptions were made for this analysis: the flow is Newtonian and incompressible; all of the physical properties of liquid and solid material are constant; the flow is turbulence; and the thermal effect can be neglected.
TABLE 1 Grids for computing domains
Using the assumptions stated above, the governing equations for this study are
Continuity Equation
Momentum Equation
For turbulent closure the standard k-ϵ model is adopted:
Turbulent kinetic Energy Transport Equation
The five adjustable constants in standard k-ϵ model take the values obtained by comprehensive data fitting for a wide range of turbulent flows, which are C 1 = 1.44, C 2 = 1.92, C 3 = 0, σk = 1.0, and σϵ = 1.3. The shear production P and the body force production G are defined as,
The inlet boundary conditions at the airflow passing through the ULPA filters in the inlets of the mini-environment and SMIF enclosure assume to be uniform. The pressure in the mini-environments must be confined strictly to maintain the positive pressure state. Generally in clean room the internal pressure is 5 Pa larger than the outside pressure to ensure the cleanliness. For this reason the pressure setting in all outlets are 5 Pa in mini-environment and SMIF enclosure. It is also assumed that on the solid surfaces no-slip conditions are required.
3. NUMERICAL MODEL
The governing equations are solved using a commercial CFD code, CFX4, based on a finite volume discretization method. The CFD code utilizes the multi-block concept to establish a computational geometry. Within the code, the standard hybrid-differencing scheme and the SIMPLE (semi-implicit pressure linked equation) pressure correction algorithm are used in numerical analysis. In this algorithm an initial guessed pressure value is given to solve the momentum equations. Then a pressure correction equation derived from the continuity, is solved to obtain a pressure correction value, which is in turn used to update the velocity and pressure values. This procedure is iterated until convergence of the velocity and pressure values.
The CFD code checks convergence criteria by examining the residual of each solution and by the iteration times. The residual of the mass flow rate, for example, is defined as
4. RESULTS AND DISCUSSION
In this article, the major parameters affecting the flow field include the position and size of slot drilling at the bottom of the SMIF enclosure, inlet velocity of the SMIF enclosure, inlet velocity of the mini-environment, the leakage area on the contact face between the mini-environment and SMIF enclosure and the position of the robot arm and wafer in the SMIF enclosure. The effect of above parameters on the flow fields and pressure distributions are analyzed in the following sections.
4.1. Effect of the Slot Open at the Bottom of Smif Enclosure
To meet the requirement of cleanliness Class 1 or 0.1 inside the space of the SMIF enclosure, the circulation zones in the SMIF enclosure should be eliminated or reduced as much as possible, especially in the areas near the wafer cassette. To eliminate or reduce the presence of the circulation zones, the velocity gradient and pressure gradient in the flow field must be minimized as much as possible. That is, the flow field should approach uniformity. Thus, slotting at the bottom of the SMIF enclosure and changing the state of air flows inside the SMIF enclosure by increasing the number of rectangular slots can be adopted to obtain better flow field distribution and eliminate or reduce the presence of circulation zones.
In this article, four different cases with regard to the position and area of slot open at the bottom of the SMIF enclosure are simulated to understand their impact on the flow field, as shown in . Except for differences in the position and area of slot, the rest of the boundary conditions are the same in all cases. The velocity at the SMIF air inlet is 0.5 m/s, and that at the mini-environment air inlet 0.3 m/s. The internal pressure of SMIF is 5 Pa in all cases, while the slot porosity at the air outlet of the mini-environment is 12%. Besides, in this article, the distribution of velocity and pressure of the flow field are recorded based on the flow channel (y = 0.322 plane) between the wafer cassette and transport robot mainly because the information obtained on the plane is more useful and easier to analyze.
FIG. 3 Cases for different positions and area of open slot at SMIF enclosure. (a) Area of open slot = 0 mm2; (b) Area of open slot = 8805 mm2; (c) Area of open slot = 2374 mm2; and (d) Area of open slot = 5743 mm2.
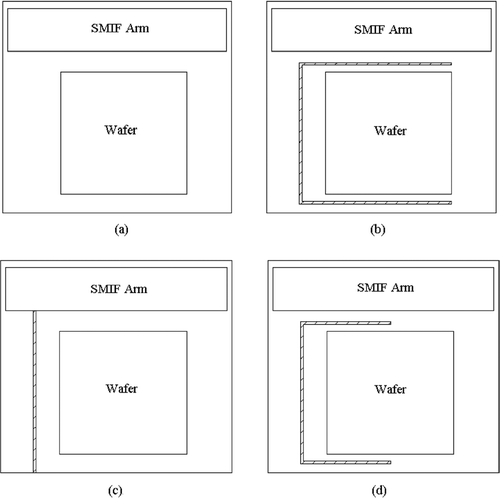
The velocity and pressure distributions of the simulation cases are shown in and , from case (a) to case (d) according to the arrangement in . Circulation zones are obviously present in all four cases, where case (a) and case (c) have the larger circulation zones while case (b) and case (d) have smaller zones. In addition, the pressure distribution also shows a greater variation in the pressure gradient and a smaller area of low pressure zone in the circulation zones where these two slot types are used. Thus, a better flow field can be obtained in case (b) and case (d). Besides, the circulation zone in these two cases shares similar sizes and positions. However, when the positive pressure requirement inside SMIF is considered, the pressure value of case (d), which has a smaller area of open slot, is larger than that of case (b). Given the considerations of the circulation size and the maintaining the positive pressure, case (d) will be a better design. Thus, the bottom slot open in all of the following numerical simulation cases is based on the design of case (d). Only the other design parameters vary.
4.2. Effect of the Air Inlet Velocity at the Smif Enclosure
The velocity difference between the influx airflow and zone airflow should be minimized to increase the cleanliness. Here, six different inlet velocities (v1) at SMIF enclosure are simulated to analyze the correlation between the above velocity and the circulation zones to serve as a reference for the optimization SMIF design. The inlet velocities (v1) of SMIF enclosures are chosen to be 0, 0.1, 0.3, and 0.5 m/s, and the inlet velocity at the mini-environment is set at 0.3 m/s. The velocity vector and pressure distribution of the cases numerical results are shown from to . Except the first case with zero velocity, which has a different flow field model, the flow fields of the other cases are all very similar, possessing a distinctive circulation zone. But the flow field of 0.1 m/s and 0.3 m/s is closer to the bottom of the SMIF enclosure and displays a better uniformity. In addition, the airflow obviously flows toward the slotting at the bottom. In , at v2 = 0.3 m/s, to meet the requirement of the positive pressure difference of 5 Pa–12 Pa, the value of v1 must reach at least 0.3 m/s, v1 = 0.3, and 0.5 m/s all meet this requirement.
4.3. Effect of the Inlet Velocity at the Mini-Environment
To explore the effect of the inlet velocity (v2) of the mini-environment on the flow field and pressure field, six simulation cases which chosen to be 0, 0.1, 0.3, and 0.5 m/s are provided here. Since the maximum supply of airflow velocity by the FFU (fan filter unit) cannot exceed 0.5 m/s, the maximum velocity of the simulations cases must be 0.5 m/s. The inlet velocity (v1) of SMIF enclosures is set at 0.3 m/s. The velocity vector and pressure distribution of the cases are shown in , , . Simulation results of these cases indicate the presence of a distinct circulation zone. As v2 decreases, the circulation zone tends to increase. This trend is even more pronounced when examined by the pressure. In fact, the change of velocity of the mini-environment does not have a significant impact on the flow field in SMIF. As shown in , the effect of the changes in inlet velocity falls mainly on the pressure field. The reason is that the inlet cross-section of the mini-environment is around 4.58 times of the SMIF enclosure inlet, producing a greater impact on the pressure field. Besides, since the airflow of SMIF enclosure comes primarily from the enclosure inlet, the flow pattern should naturally sustain a greater impact. In addition, to meet the requirement of the positive pressure different between 5 Pa and 12 Pa, when v1 = 0.5 /s, the v2 value ranges between 0.25 m/s and 0.42 m/s.
5. CONCLUSIONS
To achieve the requirement of cleanliness in the mini-environment and SMIF enclosure, the present CFD simulation results for flow field and pressure distribution are shown for different parameters. The effects of major parameter are summarized below.
1. | Slotting at the bottom of the SMIF enclosure strongly influences the flow pattern and pressure distribution. Position and area of slot are appropriately set to reduce the circulation zone and to solve the requirement of positive pressure effectively. | ||||
2. | As the air inlet velocity of the SMIF enclosure reaches 0.3 m/s to meet the requirement of the positive pressure, the value of the inlet velocity of the mini-environment must maintain at least 0.3 m/s. Additionally, when inlet velocity of the SMIF enclosure equals 0.5 m/s, the inlet velocity of the mini-environment ranges between 0.25 m/s and 0.42 m/s. | ||||
3. | The air inlet velocity of the SMIF enclosure affects the flow pattern more than that of the mini-environment. | ||||
4. | As the wafer cassette and robot arm moves into the mini-environment, the overall internal pressure value tends to increase. |
NOMENCLATURE
B | = |
gravity force |
C μ, C 1, C 2, C 3 | = |
turbulent model constant |
G | = |
body force |
P | = |
total pressure |
U | = |
Velocity vector |
x,y,z | = |
coordinate |
ρ | = |
density |
ϵ | = |
turbulent dissipation |
κ | = |
turbulent kinetic energy |
μ | = |
dynamic fluid viscosity |
ξ | = |
mass flow rate |
σ | = |
stress tensor |
= |
Superscript | |
T | = |
transport maxtrix |
= |
Subscripts | |
T | = |
turbulent |
buoy | = |
buoyancy force |
eff | = |
effective |
rot | = |
rotation force |
res | = |
resistance force |
REFERENCES
- Milberg , J. , Fischbacher , J. and Engel , A. 1991 . Fluidic Integration of Equipment in Cleanrooms . Solid State Technology , : 43 – 45 . [CSA]
- Parikh , M. and Kaempf . 1984 . SMIF: A Technology for Wafer Cassette Transfer in VLSI Manufacturing . Solid State Technol. , : 110 – 115 . [CSA]
- Quarini , G. L. and Chang , Y. C. 1996 . Experimental Measurements and Theoretical Predictions of the Thermo Hydraulic Performance of Clean Rooms for the Semi-Conductor Industry . J. Process Mechan. Engineer. , 210 : 9 – 18 . [CSA]
- Scheler , W. , Vorberg , P. , Schneider , H. and Fabian , P. 1995 . SMIF Integration of a Wafer Prober by Components of Jenoptik GmbH . Proc. Inst. Environ. Sci. , : 211 – 217 . [CSA]
- Schliesser , J. 1994 . Designing Methods to Obtain a Less Contaminated Air-Flow at the Product Level . Proc. Inst. Environ. Sci , : 406 – 412 . [CSA]
- Tannous , A. G. 1996 . Air Flow Simulation in a Mini Environment . Solid State Technol. , : 201 – 209 . [CSA]
- Yamamoto , T. , Viner , A. S. , Donovan , R. P. and Ensor , D. S. 1990 . Model Study of Contaminant Flow in the Vicinity of Semiconductor Processing Equipment . J. IES , 30 : 19 – 24 . [CSA]